大容量注射剂生产工艺流程图
大容量注射剂生产工艺流程图

目录1.大容量注射剂生产区概况2.需要验证的关键工序及工艺验证3.工艺流程的实施4.操作过程及工艺条件5.技术安全、工艺卫生及劳动保护6.物料平衡及技经指标7.设备一览表8.岗位定员9.附件(含设备操作、清洁规程)10.变更记录1.大容量注射剂生产区概况本生产区面积904㎡,其中1万级净化区域167㎡,10万级净化区域174㎡。
大容量注射剂车间采用10万级和1万级(局部百级)空气净化洁净级别,10万级区域设置缓冲、更衣、洗涤、洁具、称量、配碳、浓配、洗瓶等,1万级区域设置缓冲、更衣更鞋、稀配、化验、灌装、加塞、轧盖、洗涤、存放、洁具等功能间,所有隔断采用无粉尘产生的静电喷涂彩钢板,结合处采用圆角处理,不易产生积灰;人员经过三次更衣和二次更鞋后进入洁净区操作,物料进入洁净区均采用传递窗或气闸进行传递,人流、物流的进入相对分开,保证了洁净区空气洁净度要求;生产设备均采用优质不锈钢材料制造,采用洗瓶、灌装、压塞、轧盖联动线生产,其中洗瓶出口、灌装、加塞采用百级层流保护,灭菌器采用水浴式灭菌器。
1.1 大容量注射剂生产工艺流程图(见后页)1.2 大容量注射剂生产区工艺布局布置图(见后页)1.3 大容量注射剂生产区工艺设备布置图(见后页)1.4 大容量注射剂生产区送回风口平面布置图(见后页)以上项目按验证文件规定,均已在规定周期内进行相关的验证,验证方案及报告见相应文件。
大容量注射剂生产工艺流程图3.工艺流程的实施3.1 批生产指令的签发3.1.1 批生产指令由车间技术负责人根据生产计划表起草,并依据产品工艺规程于生产前一个工作日制定。
3.1.2 批生产指令应经QA质监员审核并签字,由车间主任签字批准后生效。
3.2 生产批记录的发放3.2.1 除配制工序和包装工序外,工序相应的生产批记录于生产当日由车间工艺质监员发放给各工序负责人,并于工序结束当日填写完整返回车间工艺质监员处汇总。
3.2.2 配制工序和包装工序的生产批记录于生产前一天由车间工艺质监员随同批生产指令或批包装指令一同发放,并于工序结束当日填写完整返回车间工艺质监员处汇总。
注射液生产流程图及关键控制点

批号外观质量数量灭菌温度、时间可见异物检查包装质量检查成品质量检验装量、外观质量检查原料安瓿清洁除尘拆外包装称量配制清洁除尘拆外包装灭菌、检漏灯检包装注射用水清洗可见异物检查外包装材料进厂质量检验质量检验检查流程物料库房一般生产区D级中间产品检验药液检查干燥灭菌温度、时间安瓿清洁度加 工QC检验过程控制供应商审计进厂验收质量检查工序监控点监控内容监控频次监控标准配液备料物料物料信息、外观、异物每次1、所领物料与生产所用物料一致;2、外观无破损;3、物料无异物称量衡具,量具校验合格证、校准每批1、有检验合格证并在有效期内2、经过校准且有记录原辅料环境、数量、复核每次1、环境:温度:18℃-26℃,湿度:45%-65%;2、称量数量与批生产指令一致;3、双人独立复核配制原辅料标识每批1、标识与生产所需一致除菌过滤器规格、起泡点每批1、除菌过滤器所用规格与生产要求一致;2、起泡点合格药液澄明度、数量、pH值、含量每批1、澄明度:无浑浊;2、药液数量与批生产指令一致;3、pH值:3.2-3.8;4、含量:4.85mg/ml~5.50mg/ml 过滤过滤器压力每次1、过滤压力0.1-11 质量监控0.2Mpa洗瓶安瓶物料信息、外观每批1、所领物料与生产所用物料一致;2、外观无破损注射用水超声频率、注射用水澄明度、水温、水压、清洁度每小时1、超声波频率:70Hz;2、注射用水澄明度:无浑浊;3、水压:0.35-0.45Mpa;4、清洁度:无颗粒物压缩空气清洁度、压力每小时1、清洁度:无颗粒物,无油;2、压力:0.30-0.60Mpa洗后安瓶清洁度随时/批1、清洁度:无颗粒物,无浑浊;2、瓶内无积水灭菌干燥隧道烘箱温度、网带频率每小时1、温度:290±10℃;2、网带频率:≤25Hz灌封药液装量、中间体检验报告单每批1、装量:2.10ml ~2.30ml/支;2、有中间体检验合格报告熔封封口长度、封口质量、装量、灌封时间随时/班1、封口高度:6.5cm;2、封口质量:不合格品(无尖头、泡头、凹头等)≤5‰;3、灌封时间≤8h灭菌检漏灭菌柜温度,时间每柜1、温度:100℃;2、时间:20min半成品标识、存放区、无菌检查每柜1、每批灭菌半成品存放按柜次存放并有状态标识;2、无菌检查:合格灯检待检品装量、可见异物、外观随时/班1、装量:2.10ml ~2.30ml/支;2、可见异物:抽检20支不得有可见异物;3、外观:抽检20支不得有外观不合格品(无尖头、泡头、凹头等)不合格品数量,标识,处理每批1、不合格品统计数量,每批分区存放并有状态标识;2、在QA监督下每批销毁工序监控点监控内容监控频次监控标准纸盒内容、字迹、位置、数量随时/班1、内容、数量与批包装指令一致;2、字迹清晰,与样张相符;1、内容、数量与包装标签内容、字迹、位置、数量随时/班批包装指令一致;2、字迹清晰,与样张相符;装盒包装内容物、装盒数量、装盒质量随时/批1、包装内容物与批包装指令一致;2、装盒数量:2ml*5支/盒;3、装盒质量:无少装内容物,无多装或少装说明书装箱装箱内容物、装盒数量、装盒质量随时/批1、装箱内容物与批包装指令一致;2、装箱数量:2ml*100盒/件;3、装箱质量:无少装内容物入(寄)库成品标识、存放区、无菌检查每批1、成品统计数量,每批分区存放并有状态标识;。
大容量注射液生产工艺规程

制药有限公司大容量注射液生产工艺规程颁发单位:GMP办公室工艺规程批准程序目录1. 剂型、规格 (3)2. 生产工艺流程 (3)3. 操作过程及工艺条件 (4)4.质量控制要点 (6)5.设备一览表、主要设备生产能力 (7)6.工艺过程中的SOP (7)7.中间产品的控制 (8)8.验证工作要点 (8)9.工艺卫生和环境卫生 (10)10.劳动组织及岗位定员 (10)一、制剂类型:最终灭菌大容量注射液,100ml规格,西林瓶包装。
二、流程图:大容量注射剂工艺流程图三、操作过程及工艺条件1 生产前的检查与确认1.1 是否还留有前批生产的产品或物料,是否已清洁并取得“清场合格证”。
1.2 检查确认生产现场的机器设备和器具是否已清洁并准备完毕挂上“合格”标示。
1.3 所使用原辅料是否准备齐全。
是否有质量检验报告单,合格品才能使用。
1.4 检查工艺用水是否新鲜制备,贮存不得超过24小时。
1.5 检查确认与生产品种相适应的批生产指令、配套文件及有关记录是否已准备齐全。
1.6 检查确认生产场所的温度是否在规定范围内(18-26℃,相对湿度在30%-65%)。
2 洗瓶、塞、铝盖2.1理瓶:根据“批生产指令”准备所需的清洁盘、领取必须的西林瓶。
在理瓶室将西林瓶的合格品摆满瓶盘。
2.2清洗:把西林瓶放在不锈钢传送链条上,开动洗瓶机,定时检查安瓿的清洁度:目检1000ml注射用水无可见异物,抽50支,毛、块≤2%。
洗瓶岗位按清场SOP进行清场,并填写生产记录。
2.3 理塞、铝盖:根据《生产指令》准备所需的丁基胶塞和铝盖,分别、依次放入多功能胶塞漂洗机。
2.4清洗:将丁基胶塞放入多功能漂洗机后,加入纯化水,开动机器进行清洗,清洗后捞出、沥干。
排除纯化水后再加入注射用水清洗,捞出、沥干。
将铝盖放入多功能漂洗机后,加入纯化水,开动机器清洗,清洗后捞出、沥干。
排除纯化水后再加入注射用水清洗,捞出、沥干。
清洗过后,按岗位清场操作规程进行清场,填写清场合格证,并填写生产记录。
注射剂制备工艺流程
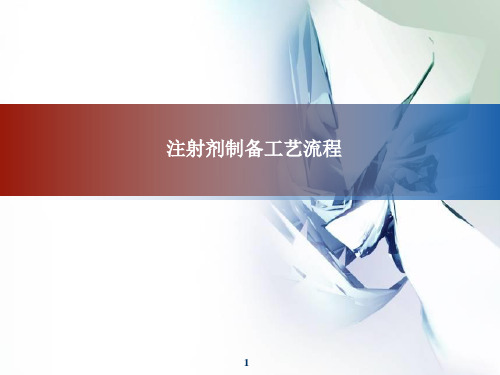
灌封的生产工艺管理要点 1、灌封操作室洁净度按1万级要求,灌封部位局 部达到100级;室内相对室外呈正压,温度18℃~ 26℃,相对湿度45%~65%; 2、灌封时要经常抽查装量及封口质量,封口不得 炭化、封口不严等;QA定时抽查澄明度; 3、收集灌封后安瓿的容器应有标签,标签上应标 明品名、规格、批号、生产日期、灌封人、灌封 序号,防止发生混药、混批。
注射剂洗灌封联动机
33
灌封的生产操作 生产前的准备 1、检查操作间是否有清场合格标志,并在有效期 内,否则按清场标准操作规程进行清场并经QA人 员检查合格后,填写清场合格证,才能进行下一 步操作; 2、检查设备是否有“合格”标牌及“已清洁”标 牌,且在有效期内; 3、领取校正后的注射器; 4、按灌封机标准操作规程检查设备是否正常,并 安装活塞和灌注器;
16
注射剂配液和质量检查 注射剂配液是指将符合注射液要求的原料药、营 养素、电解质、血浆及附加剂溶解于注射用水或 其他非水溶剂中,经过滤过制成专供注射用的溶 液、混悬液或乳浊液状制剂。 注射液质量检查系指从事注射液配制全过程的各 工序质量控制点的现场监督和对规定的质量标进 行检查、判定的操作。
34
灌封的生产操作 5、按《灌封设备消毒规程》对设备、所用容器进 行消毒; 6、挂运行状态标志,进入灌封操作。 生产操作 1、开启控制箱的主开关,显示主电源接通的绿信 号灯亮; 2、根据人机界面的提示逐步操作; 3、根据每分钟的产量调节走瓶速度。
35
灌封的生产操作 生产结束 1、按下主机停机按钮,主机驱动信号灯灭,主机 停止运转; 2、停机后将机器外表的水渍、污渍擦拭干净; 3、收集中间产品挂上标签,标明状态,交中间站, 做好交接工作; 4、按《灌封设备清洁操作规程》清洗消毒设备, 按《灌封间清场标准操作规程》进行清场,经QA 人员检查合格,发清场合格证。 记录 按照要求如实填写各类生产记录。
磺胺间甲氧嘧啶钠注射液生产工艺规程-大容量

磺胺间甲氧嘧啶钠注射液生产工艺规程(大容量)目录1 产品概述2 处方和依据3 工艺流程图4 制剂工艺过程及工艺条件5 原辅材料质量标准和检查方法6 中间产品质量标准和检查方法7 成品质量标准和检查方法8 包装规格、包装材料质量标准9 说明书、产品文字说明和标志10 工艺要求11 设备一览表和主要设备生产能力12 技术安全与劳动保护13 劳动组织14 技术经济指标计算15 原辅料消耗定额16 包装材料消耗定额17 动力消耗定额18 综合利用与环境保护目的:制定本标准的目的是规范磺胺间甲氧嘧啶钠注射液生产过程,对一定数量的成品所需的起始原辅料和包装材料,以及工艺、加工说明、技术参数、注意事项等进一步标准化。
适用范围:适用于磺胺间甲氧嘧啶钠注射液生产全过程。
责任人:质量部部长、生产部部长、车间主任。
内容:1产品概述:本品为磺胺间甲氧嘧啶钠的灭菌水溶液。
含磺胺间甲氧嘧啶钠(C11H11N4NaO3S)应为标示量的96.0%~104.0%1.1产品特点:1.1.1性状:本品为无色至微黄色的澄明液体。
1.1.2作用与用途:磺胺类药。
用于各种敏感菌引起的呼吸道、消化道、泌尿道感染及球虫病、猪弓形虫病等。
局部灌注可治疗乳腺炎和子宫内膜炎。
1.1.3用法用量:静脉注射一次量每1Kg体重家畜0.5ml,一日1~2次,连用2-3日。
1.1.4规格:100ml:10g(磺胺间甲氧嘧啶钠)1.1.5贮藏:遮光、密闭保存。
1.1.6停药期:28日1.1.7有效期:二年1.1.8批准文号:2 处方和依据:2.1处方:(1000ml)磺胺间甲氧嘧啶钠100g 硫代硫酸钠 1 g注射用水 至1000ml10000级区100000级区4 制剂工艺过程及工艺条件: 4.1总述:4.1.1按生产指令单领取磺胺间甲氧嘧啶钠原料,在浓配灌中加入计算量70%的注射用水, 再加入计算量的硫代硫酸钠搅拌使溶解;然后加磺胺间甲氧嘧啶钠原料搅拌至完全溶解,粗滤至稀配灌中,加注射用水近全量,调节PH在规定范围内(9.7-10.8),补加注射用水至足量;用孔径为0.45um、0.22um的过滤器(使用前后经过完整性测试合格)精滤,检查澄明度、含量合格后,将药液输送到至灌封岗位,灌装压盖,100℃30分钟灭菌,灯检、贴签包装成规定规格即可。
注射剂的制备课件PPT
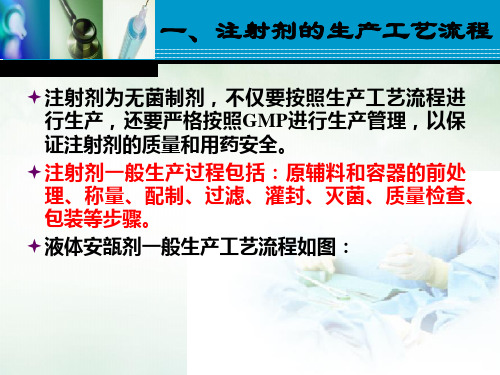
围的水溶液等;
④ 聚四氟乙烯膜:热稳定性和化学稳定性均好,可耐260
℃高温,适用于强酸、强碱及各种有机溶剂;
⑤ 聚酰胺膜、聚砜膜和聚氯乙烯膜等。
3.钛滤器
是用粉末冶金工艺将钛粉加工制成的过滤材料, 包括钛滤棒和钛滤片。
常用于注射液的预滤。
4.板框压滤机
以油为溶剂的注射剂,选用干热灭菌。
后要在烘箱内120~140℃温度下进行干燥,若用于无菌 由多个滤板和滤框交替排列组成,滤过面积大,截留固体多,经济耐用,适于大生产,常用于滤过黏性、微粒较大的浸出液,也可用
于注射液的粗滤。 配液的所有用具和容器在使用前均应用硫酸重铬酸钾清洗或其他适宜洗涤剂清洗,然后用纯化水反复冲洗,最后用新鲜的注射用水荡
注意可能对主药产生吸附而使含量下降。活性炭在 酸性条件下吸附能力强,一般均在酸性环境中使用。
配制所用注射用水,其储存时间不得超过12小时。
配 制 的 药 液 , 需 经 过 pH 、 含 量 等 项 检 查 , 合 格 后 进入下一工序。
四、注射液的滤过
滤过是保证注射液澄明的关键工序。由于不同滤
✓ 垂熔玻璃滤器 洗涤方法:甩水洗涤法、加压气水喷射洗涤法和超声洗涤法。
罐封室是注射液制备的关键区域,洁净度要求达到100级。 高位静压滤过装置利用液位产生的静压力进行滤过,其特点是压力稳定,滤过质量好,但流速稍慢;
灌液部分装有自动止灌装置,当灌注针头降下无安瓿时,药液不再输出,避免污染机器与浪费。
实验表明,用100℃流通蒸汽30分钟灭菌,含量降低3%;
安瓿熔封方法分为拉封和顶封两种,由于拉封封 配制所用注射用水,其储存时间不得超过12小时。
曲颈易折安瓿使用方便,可避免折断后玻璃屑和微粒对药液的污染,故SFDA已强制推行使用该种安瓿。
大输液生产工艺规程

大输液生产工艺规程
大输液生产工艺规程
大输液生产工艺规程
输液工序关键质控要点
输液工序关键质检要点
十、半成品质量标准(指标)、成品及原辅料质量标准依据
输液半成品质量标准(指标)
原辅料及成品质量标准依据品名质量标准依据
葡萄糖中国药典95年版二部Р。
845 氯化钠中国药典95年版二部Р。
945 氯化钾中国药典95年版二部Р.947 氯化钙中国药典95年版二部Р.943 甘露醇中国药典95年版二部Р。
85 甲硝唑中国药典95年版二部Р。
152 各种氨基酸日本味之素质量标准(92版)
大输液生产工艺规程
大输液生产工艺规程
大输液生产工艺规程
大输液生产工艺规程。
大容量注射剂生产工艺流程图

更衣和二次更鞋后进入洁净区操作,物料进入洁净区均采用传递窗或气闸进行传递,人
流、物流的进入相对分开,保证了洁净区空气洁净度要求;生产设备均采用优质不锈钢
4.操作过程及工艺条件
4.1工艺用水
4.1.1操作过程
4.1.1.1原水为符合国家饮用水的标准自来水。
4.1.1.2纯化水由原水经机械过滤t活性炭过滤t精滤(保安)t一级反渗透t二级
反渗透t脱气塔t进入贮罐t紫外灯灭菌t膜过滤t各使用点。
4.1.1.3注射用水由纯化水经多效蒸馏水机经过蒸馏而得。
4.1.2工艺条件
全自动胶塞清洗机验证
VP-ZJ-dz003
大容量注射剂配料罐及管路系统验证
VP-ZJ-dz004
大容量注射剂过滤系统验证
VP-ZJ-dz005
PSMD200冰浴式灭菌器验证
VP-ZJ-dz006
大容量注射剂生产工艺验证
VP-ZJ-dz007
大容量注射剂在线清洗验证方案
VP-ZJ-dz008
以上项目按验证文件规定,均已在规定周期内进行相关的验证,验证方案及报告见相应
4.2.1操作过程
4.2.1.1按批生产指令,开领料单由车间主任签字后,凭领料单领取原辅料。
4.2.1.2根据原辅料检验报告书,对原辅料的品名、批号、生产厂家规程及数量核
对,并分别称(量)取所需原辅料,各不同品种的具体操作按“工艺规程各论”执行。
4.2.1.3原辅料的计算、称量、投料必须进行复核,操作人、复核人均应在原始记
题目:大容量注射剂生产工艺规程通则
- 1、下载文档前请自行甄别文档内容的完整性,平台不提供额外的编辑、内容补充、找答案等附加服务。
- 2、"仅部分预览"的文档,不可在线预览部分如存在完整性等问题,可反馈申请退款(可完整预览的文档不适用该条件!)。
- 3、如文档侵犯您的权益,请联系客服反馈,我们会尽快为您处理(人工客服工作时间:9:00-18:30)。
目录1.大容量注射剂生产区概况2.需要验证的关键工序及工艺验证3.工艺流程的实施4.操作过程及工艺条件5.技术安全、工艺卫生及劳动保护6.物料平衡及技经指标7.设备一览表8.岗位定员9.附件(含设备操作、清洁规程)10.变更记录1.大容量注射剂生产区概况本生产区面积904㎡,其中1万级净化区域167㎡,10万级净化区域174㎡。
大容量注射剂车间采用10万级和1万级(局部百级)空气净化洁净级别,10万级区域设置缓冲、更衣、洗涤、洁具、称量、配碳、浓配、洗瓶等,1万级区域设置缓冲、更衣更鞋、稀配、化验、灌装、加塞、轧盖、洗涤、存放、洁具等功能间,所有隔断采用无粉尘产生的静电喷涂彩钢板,结合处采用圆角处理,不易产生积灰;人员经过三次更衣和二次更鞋后进入洁净区操作,物料进入洁净区均采用传递窗或气闸进行传递,人流、物流的进入相对分开,保证了洁净区空气洁净度要求;生产设备均采用优质不锈钢材料制造,采用洗瓶、灌装、压塞、轧盖联动线生产,其中洗瓶出口、灌装、加塞采用百级层流保护,灭菌器采用水浴式灭菌器。
1.1 大容量注射剂生产工艺流程图(见后页)1.2 大容量注射剂生产区工艺布局布置图(见后页)1.3 大容量注射剂生产区工艺设备布置图(见后页)1.4 大容量注射剂生产区送回风口平面布置图(见后页)以上项目按验证文件规定,均已在规定周期内进行相关的验证,验证方案及报告见相应文件。
大容量注射剂生产工艺流程图3.工艺流程的实施3.1 批生产指令的签发3.1.1 批生产指令由车间技术负责人根据生产计划表起草,并依据产品工艺规程于生产前一个工作日制定。
3.1.2 批生产指令应经QA质监员审核并签字,由车间主任签字批准后生效。
3.2 生产批记录的发放3.2.1 除配制工序和包装工序外,工序相应的生产批记录于生产当日由车间工艺质监员发放给各工序负责人,并于工序结束当日填写完整返回车间工艺质监员处汇总。
3.2.2 配制工序和包装工序的生产批记录于生产前一天由车间工艺质监员随同批生产指令或批包装指令一同发放,并于工序结束当日填写完整返回车间工艺质监员处汇总。
3.2.3 所有生产工序必须按批生产(包装)指令执行。
3.3 工艺用水的管理使用3.3.1 纯化水、注射用水系统由工程设备科管理,制水工序制备而得。
3.3.2 按照SMP-ZL-qa024,纯化水每周生产第一个工作日由QA质监员取样送QC 检验,注射用水在生产期间每天下午三点由QA质监员取样送QC检验,QC检验合格后出具报告单由QA质监员交至车间工艺质监员。
3.3.3 车间配料岗位投料前,确认所用注射用水经检验符合规定,记录使用注射用水的批号检验报告单附批生产记录中。
3.3.4 车间在没有收到工艺用水检验报告单的情况下,不得进行生产操作。
3.5 批包装指令的签发3.5.1 车间技术负责人在灭菌工序完成后对半成品数量、质量等方面进行审核并对照生产工艺检查已完成的工作是否按工艺执行。
3.5.2 车间技术负责人计算理论成品率和预计成品率后根据SMP-JS-016判定生产是否异常,如有异常按SMP-JS-012调查分析原因。
3.5.3 批审查通过后车间技术负责人依据产品工艺规程于包装前一个工作日签发批包装指令。
批包装指令应经QA质监员审核并签字,由车间主任签字批准后生效。
3.6 批生产记录在交由车间工艺质监员汇总后,车间技术负责人审核并签名,要求在包装完成的两个工作日内送质监科。
4.操作过程及工艺条件4.1 工艺用水4.1.1 操作过程4.1.1.1 原水为符合国家饮用水的标准自来水。
4.1.1.2 纯化水由原水经机械过滤→活性炭过滤→精滤(保安)→一级反渗透→二级反渗透→脱气塔→进入贮罐→紫外灯灭菌→膜过滤→各使用点。
4.1.1.3 注射用水由纯化水经多效蒸馏水机经过蒸馏而得。
4.1.2 工艺条件4.1.2.1 原水应符合国家饮用水标准。
4.1.2.2 原水的预处理的进水流量应≤8.6m3/h。
4.1.2.3 纯化水的电导率应≤2us/cm,离子检查符合«中国药典»2000版二部“纯化水”的标准。
注射用水的电导率≤2us/cm,离子检查符合«中国药典»2000版二部“注射用水”的标准。
4.2 配制工序4.2.1 操作过程4.2.1.1 按批生产指令,开领料单由车间主任签字后,凭领料单领取原辅料。
4.2.1.2 根据原辅料检验报告书,对原辅料的品名、批号、生产厂家规程及数量核对,并分别称(量)取所需原辅料,各不同品种的具体操作按“工艺规程各论”执行。
4.2.1.3 原辅料的计算、称量、投料必须进行复核,操作人、复核人均应在原始记录上签名。
4.2.1.4 过滤前及本批生产结束,滤芯均需要做气泡点测试,应符合SOP-ZJ-dz022规定。
4.2.1.5 配料过程中,凡接触药液的配制容器、管道、用具等均需做特别处理。
4.2.1.6 称量时使用经计量检定合格,标有在有效期内的合格证的衡器,每次使用前应检查核对。
4.2.2 工艺条件4.2.2.1 配制用注射用水应符合«中国药典»2000年版二部“注射用水标准”。
4.2.2.2 其余工艺条件按“工艺规程各论”执行。
4.2.2.3 药液从稀配到灌装结束应不超过4小时(特殊品种另定)。
4.3 理瓶外洗工序4.3.1 操作过程按批生产指令领取输液瓶并除去外包装,在理瓶间经理瓶转盘送入外洗机,瓶身外表面清洗干净后进入洁净区,具体操作见SOP-ZJ-dz002。
4.3.2 工艺条件4.3.2.1 外洗机采用纯化水进行清洗,毛刷无断裂、脱毛。
4.4 洗瓶工序4.4.1 操作过程输送带将外洗好的输液瓶送至超声波洗瓶机内进行清洗,具体操作见SOP-ZJ-dz006。
4.4.2 工艺条件4.4.2.1 纯化水应符合«中国药典»2000年版二部标准注射用水应符合«中国药典»2000年版二部标准4.4.2.2 超声波槽水温应控制在40~50℃;检查超声波强度2kw×2组(折合电流约9A/组),大于额定电流的80%属正常,在线操作须每小时记录一次。
4.4.2.3 注射用水压力0.15~0.20Mpa,流量4m3/h。
喷射管路压力,表压为0.10~0.15Mpa。
4.4.2.4 超声波洗瓶出口处取洁净输液瓶用过滤注射用水荡洗后进行不溶性微粒监测,要求10μm以上的微粒不得过20粒/ml,25μm以上的微粒不得过2粒/ml。
4.5 胶塞清洗工序4.5.1 操作过程将已脱包的胶塞通过全自动胶塞清洗机吸料装置送入清洗机内腔,设定清程序后开始清洗、硅化、灭菌及干燥。
出料在百级层流罩下进行。
4.5.2 工艺条件4.5.2.1 注射用水应符合«中国药典»2000年版二部标准。
终端使用0.22μm的聚醚砜滤芯过滤。
4.5.2.2 对硅化前最后冲洗水和清洁胶塞分别进行不溶性微粒监测,要求10μm 以上的微粒不得过20粒/ml,25μm以上的微粒不得过2粒/ml。
4.6 灌装、压塞工序4.6.1 操作过程4.6.1.1 将已处理的灌装机、阀门等安装好,用0.22µm滤芯过滤的新鲜注射用水清洗,调试灌装机,并校正装量,并抽干注射用水。
4.6.1.2 接通药液管道,将开始打出的适量药液回入配制,重新过滤,并检查澄明度合格后,开始灌装;灌装时每半小时抽检装量一次,灌装容量可通过灌装机上的药液调节阀进行流量调节达到要求装量,并填写在原始记录上。
4.6.1.3 将清洁无菌的胶塞倒入理塞斗,开振荡器调节旋钮使胶塞充满送塞轨道。
4.6.2 工艺条件4.6.2.1 量筒检测装量,100ml产品理论装量为102.0ml,在线控制在100.0~103.0ml。
4.6.2.2 灌装压塞间内的风速,换气次数,尘埃粒子,菌落数,温度湿度按百级层流洁净环境监控制度执行。
4.6.2.3 从传送带上取已轧盖产品,进行澄明度检查(20瓶/次)和不容性微粒(1瓶/次)监测,要求10μm以上的微粒不得过20粒/ml,25μm以上的微粒不得过2粒/ml。
4.6.2.4 已灌装的半成品,应在6小时内灭菌。
4.7 轧盖工序4.7.1 操作过程筛选好盖子装入理盖斗内。
检查瓶口瓶盖高度与轧盖位置。
开理盖振荡器调节旋钮至所需要的量充满送盖轨道。
运行中应时刻注意绞龙与拨轮及轧头轧刀运转情况。
每半小时抽查一次轧盖是否完好。
4.7.2 工艺条件每半小时检查轧盖质量,用三指拧法检查轧盖严密性,不能有歪盖、松盖及皱纹。
4.8 灭菌工序4.8.1 操作过程4.8.1.1 按批生产记录,设定好温度、时间等数据。
4.8.1.2 将轧盖后的输液产品根据产品流转卡,核对品名、规格、批号、数量正确后,送入灭菌柜中进行灭菌,具体操作见SOP-ZJ-dz034。
4.8.1.3 同一批号需要多个灭菌柜次灭菌时,需由车间技术负责人编制亚批号,灭菌负责人填写产品流转卡对灭菌产品和未灭菌产品以及不同亚批号产品加以区分,并严格控制操作间的人员进入。
4.8.2 工艺条件4.8.2.1 按产品“工艺规程各论”执行。
4.9 灯检4.9.1 操作过程产品由卸瓶机输送至工作台面,并由转盘将产品送上输送带,上灯检台灯检。
按卫生部《澄明度检查细则和判断标准》进行灯检,并灯检合格产品由输送带送到下道工序。
不同亚批号要分别灯检,不得混淆。
具体操作见SOP-ZJ-dz036。
4.9.2 工艺条件4.9.2.1 按产品“工艺规程各论”执行。
4.10 贴签、装箱工序4.10.1 操作过程4.10.1.1 由灯检输送带输出的成品进入到贴签工段。
并由质监员检查该产品名称、规格以及批号有效期的瓶贴,放置其设备上。
再由气缸用正负压缩空气将瓶贴贴在输液瓶上。
4.10.1.2 根据批包装指令领取包装材料,由质监员核对装箱单、拼箱单等内容。
在无误的情况下进行封箱入库。
4.10.1.3 不同亚批号要分别贴签和包装,拼箱要有拼箱单。
4.10.2 工艺条件4.10.2.1 按产品“工艺规程各论”执行。
5.技术安全、工艺卫生及劳动保护5.1 技术安全5.1.1 操作人员操作时应按规定穿戴好劳保用品,并严格按设备操作规程进行操作,做到人离、关机、关水、关电。
5.1.2 灌装应严格控制氮气的压力,操作完及时关闭氮气开关及一切电源开关。
5.1.3 包装材料严格防火措施。
5.1.4 相关岗位应防酸、碱等化学试剂损伤。
5.2 工艺卫生5.2.1 洗瓶、浓配、稀配、灌装压塞区域的风速、换气次数、尘埃粒子、菌落数、温湿度按“洁净环境监控制度”执行。
5.2.2 各工序执行厂房、设备的清洁规程和清场管理制度。
5.2.3 操作人员按规定穿戴好工作衣、帽,一万级、局部百级区域需戴好口罩。