轴承的失效形式和解决方--电蚀
滚动轴承常见的失效形式和原因分析范文

滚动轴承常见的失效形式及原因分析+浪逐风尖2008-11-05 10:55滚动轴承在使用过程中,由于很多原因造成其性能指标达不到使用要求时就产生了失效或损坏.常见的失效形式有疲劳剥落、磨损、塑性变形、腐蚀、烧伤、电腐蚀、保持架损坏等。
一,疲劳剥落疲劳有许多类型,对于滚动轴承来说主要是指接触疲劳。
滚动轴承套圈各滚动体表面在接触应力的反复作用下,其滚动表面金属从金属基体呈点状或片状剥落下来的现象称为疲劳剥落。
点蚀也是由于材料疲劳引起一种疲劳现象,但形状尺寸很小,点蚀扩展后将形成疲劳剥落。
疲劳剥落的形态特征一般具有一定的深度和面积,使滚动表面呈凹凸不平的鳞状,有尖锐的沟角.通常呈显疲劳扩展特征的海滩装纹路.产生部位主要出现在套圈和滚动体的滚动表面.轴承疲劳失效的机理很复杂,也出现了多种分析理论,如最大静态剪应力理论、最大动态剪应力理论、切向力理论、表面微小裂纹理论、油膜剥落理论、沟道表面弯曲理论、热应力理论等。
这些理论中没有一个理论能够全面解释疲劳的各种现象,只能对其中的部分现象作出解释。
目前对疲劳失效机理比较统一的观点有:1、次表面起源型次表面起源型认为轴承在滚动接触部位形成油膜的条件下运转时,滚动表面是以内部(次表面)为起源产生的疲劳剥落。
2、表面起源型表面起源型认为轴承在滚动接触部位未形成油膜或在边界润滑状态下运转时,滚动表面是以表面为起源产生的疲劳剥落。
3、工程模型工程模型认为在一般工作条件下,轴承的疲劳是次表面起源型和表面起源型共同作用的结果。
疲劳产生的原因错综复杂,影响因素也很多,有与轴承制造有关的因素,如产品设计、材料选用、制造工艺和制造质量等;也有与轴承使用有关的因素,如轴承选型、安装、配合、润滑、密封、维护等。
具体因素如下:A、制造因素1、产品结构设计的影响产品的结构设计是根据使用性能目标值来确定的,这些目标值如载荷容量、寿命、精度、可靠性、振动、磨损、摩擦力矩等。
在设计时,由于各种原因,会造成产品设计与使用的不适用或脱节,甚至偏离了目标值,这种情况很容易造成产品的早期失效。
浅谈轴承失效原因分析

轴承失效原因分析滚动轴承在使用过程中,由于很多原因造成其性能指标达不到使用要求时就产生了失效或损坏.常见的失效形式有疲劳剥落、磨损、塑性变形、腐蚀、烧伤、电腐蚀、保持架损坏等。
一,疲劳剥落疲劳有许多类型,对于滚动轴承来说主要是指接触疲劳。
滚动轴承套圈各滚动体表面在接触应力的反复作用下,其滚动表面金属从金属基体呈点状或片状剥落下来的现象称为疲劳剥落。
点蚀也是由于材料疲劳引起一种疲劳现象,但形状尺寸很小,点蚀扩展后将形成疲劳剥落。
疲劳剥落的形态特征一般具有一定的深度和面积,使滚动表面呈凹凸不平的鳞状,有尖锐的沟角.通常呈显疲劳扩展特征的海滩装纹路.产生部位主要出现在套圈和滚动体的滚动表面.轴承疲劳失效的机理很复杂,也出现了多种分析理论,如最大静态剪应力理论、最大动态剪应力理论、切向力理论、表面微小裂纹理论、油膜剥落理论、沟道表面弯曲理论、热应力理论等。
这些理论中没有一个理论能够全面解释疲劳的各种现象,只能对其中的部分现象作出解释。
目前对疲劳失效机理比较统一的观点有:1、次表面起源型次表面起源型认为轴承在滚动接触部位形成油膜的条件下运转时,滚动表面是以内部(次表面)为起源产生的疲劳剥落。
2、表面起源型表面起源型认为轴承在滚动接触部位未形成油膜或在边界润滑状态下运转时,滚动表面是以表面为起源产生的疲劳剥落。
3、工程模型工程模型认为在一般工作条件下,轴承的疲劳是次表面起源型和表面起源型共同作用的结果。
疲劳产生的原因错综复杂,影响因素也很多,有与轴承制造有关的因素,如产品设计、材料选用、制造工艺和制造质量等;也有与轴承使用有关的因素,如轴承选型、安装、配合、润滑、密封、维护等。
具体因素如下:A、制造因素1、产品结构设计的影响产品的结构设计是根据使用性能目标值来确定的,这些目标值如载荷容量、寿命、精度、可靠性、振动、磨损、摩擦力矩等。
在设计时,由于各种原因,会造成产品设计与使用的不适用或脱节,甚至偏离了目标值,这种情况很容易造成产品的早期失效。
滚动轴承失效的四种形式
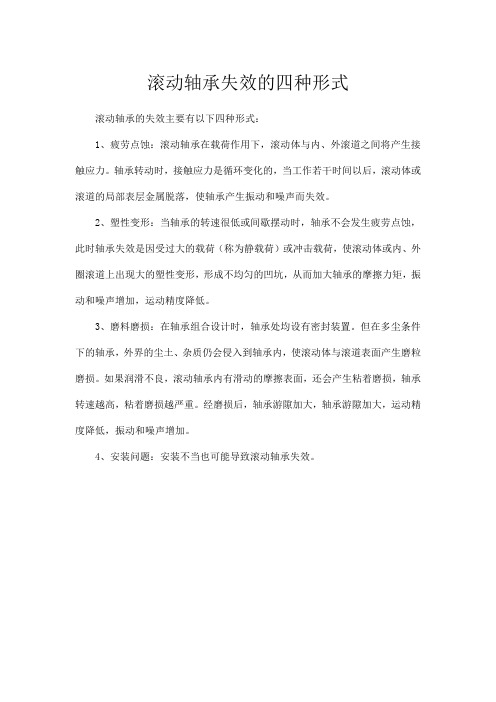
滚动轴承失效的四种形式
滚动轴承的失效主要有以下四种形式:
1、疲劳点蚀:滚动轴承在载荷作用下,滚动体与内、外滚道之间将产生接触应力。
轴承转动时,接触应力是循环变化的,当工作若干时间以后,滚动体或滚道的局部表层金属脱落,使轴承产生振动和噪声而失效。
2、塑性变形:当轴承的转速很低或间歇摆动时,轴承不会发生疲劳点蚀,此时轴承失效是因受过大的载荷(称为静载荷)或冲击载荷,使滚动体或内、外圈滚道上出现大的塑性变形,形成不均匀的凹坑,从而加大轴承的摩擦力矩,振动和噪声增加,运动精度降低。
3、磨料磨损:在轴承组合设计时,轴承处均设有密封装置。
但在多尘条件下的轴承,外界的尘土、杂质仍会侵入到轴承内,使滚动体与滚道表面产生磨粒磨损。
如果润滑不良,滚动轴承内有滑动的摩擦表面,还会产生粘着磨损,轴承转速越高,粘着磨损越严重。
经磨损后,轴承游隙加大,轴承游隙加大,运动精度降低,振动和噪声增加。
4、安装问题:安装不当也可能导致滚动轴承失效。
探讨滚动轴承失效的原因以及维护方法
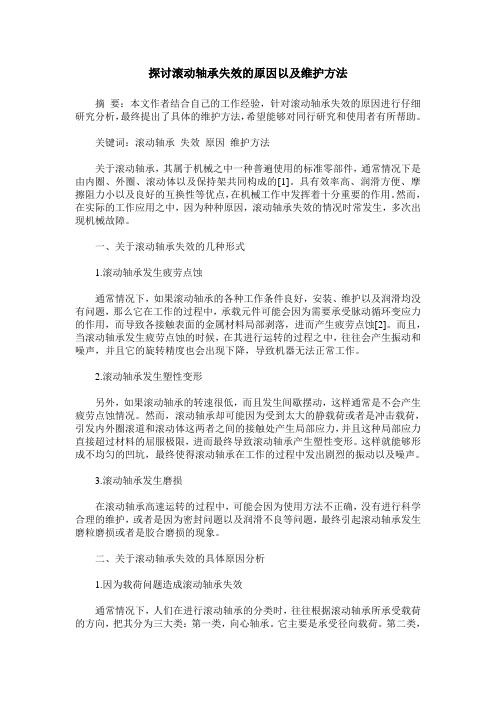
探讨滚动轴承失效的原因以及维护方法摘要:本文作者结合自己的工作经验,针对滚动轴承失效的原因进行仔细研究分析,最终提出了具体的维护方法,希望能够对同行研究和使用者有所帮助。
关键词:滚动轴承失效原因维护方法关于滚动轴承,其属于机械之中一种普遍使用的标准零部件,通常情况下是由内圈、外圈、滚动体以及保持架共同构成的[1]。
具有效率高、润滑方便、摩擦阻力小以及良好的互换性等优点,在机械工作中发挥着十分重要的作用。
然而,在实际的工作应用之中,因为种种原因,滚动轴承失效的情况时常发生,多次出现机械故障。
一、关于滚动轴承失效的几种形式1.滚动轴承发生疲劳点蚀通常情况下,如果滚动轴承的各种工作条件良好,安装、维护以及润滑均没有问题,那么它在工作的过程中,承载元件可能会因为需要承受脉动循环变应力的作用,而导致各接触表面的金属材料局部剥落,进而产生疲劳点蚀[2]。
而且,当滚动轴承发生疲劳点蚀的时候,在其进行运转的过程之中,往往会产生振动和噪声,并且它的旋转精度也会出现下降,导致机器无法正常工作。
2.滚动轴承发生塑性变形另外,如果滚动轴承的转速很低,而且发生间歇摆动,这样通常是不会产生疲劳点蚀情况。
然而,滚动轴承却可能因为受到太大的静载荷或者是冲击载荷,引发内外圈滚道和滚动体这两者之间的接触处产生局部应力,并且这种局部应力直接超过材料的屈服极限,进而最终导致滚动轴承产生塑性变形。
这样就能够形成不均匀的凹坑,最终使得滚动轴承在工作的过程中发出剧烈的振动以及噪声。
3.滚动轴承发生磨损在滚动轴承高速运转的过程中,可能会因为使用方法不正确,没有进行科学合理的维护,或者是因为密封问题以及润滑不良等问题,最终引起滚动轴承发生磨粒磨损或者是胶合磨损的现象。
二、关于滚动轴承失效的具体原因分析1.因为载荷问题造成滚动轴承失效通常情况下,人们在进行滚动轴承的分类时,往往根据滚动轴承所承受载荷的方向,把其分为三大类:第一类,向心轴承。
它主要是承受径向载荷。
滚动轴承常见失效形式及原因分析
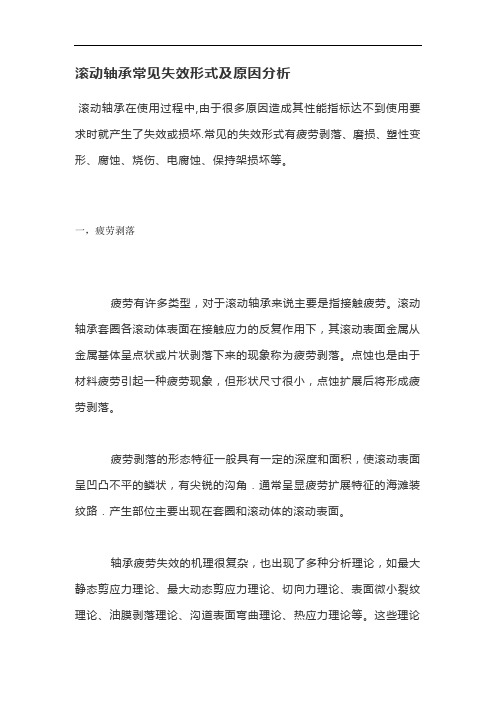
滚动轴承常见失效形式及原因分析滚动轴承在使用过程中,由于很多原因造成其性能指标达不到使用要求时就产生了失效或损坏.常见的失效形式有疲劳剥落、磨损、塑性变形、腐蚀、烧伤、电腐蚀、保持架损坏等。
一,疲劳剥落疲劳有许多类型,对于滚动轴承来说主要是指接触疲劳。
滚动轴承套圈各滚动体表面在接触应力的反复作用下,其滚动表面金属从金属基体呈点状或片状剥落下来的现象称为疲劳剥落。
点蚀也是由于材料疲劳引起一种疲劳现象,但形状尺寸很小,点蚀扩展后将形成疲劳剥落。
疲劳剥落的形态特征一般具有一定的深度和面积,使滚动表面呈凹凸不平的鳞状,有尖锐的沟角.通常呈显疲劳扩展特征的海滩装纹路.产生部位主要出现在套圈和滚动体的滚动表面。
轴承疲劳失效的机理很复杂,也出现了多种分析理论,如最大静态剪应力理论、最大动态剪应力理论、切向力理论、表面微小裂纹理论、油膜剥落理论、沟道表面弯曲理论、热应力理论等。
这些理论中没有一个理论能够全面解释疲劳的各种现象,只能对其中的部分现象作出解释。
目前对疲劳失效机理比较统一的观点有:>>>>1、次表面起源型次表面起源型认为轴承在滚动接触部位形成油膜的条件下运转时,滚动表面是以内部(次表面)为起源产生的疲劳剥落。
>>>>2、表面起源型表面起源型认为轴承在滚动接触部位未形成油膜或在边界润滑状态下运转时,滚动表面是以表面为起源产生的疲劳剥落。
>>>>3、工程模型工程模型认为在一般工作条件下,轴承的疲劳是次表面起源型和表面起源型共同作用的结果。
疲劳产生的原因错综复杂,影响因素也很多,有与轴承制造有关的因素,如产品设计、材料选用、制造工艺和制造质量等;也有与轴承使用有关的因素,如轴承选型、安装、配合、润滑、密封、维护等。
具体因素如下:(1)制造因素a.产品结构设计的影响产品的结构设计是根据使用性能目标值来确定的,这些目标值如载荷容量、寿命、精度、可靠性、振动、磨损、摩擦力矩等。
常见滚动轴承的失效形式及原因分析
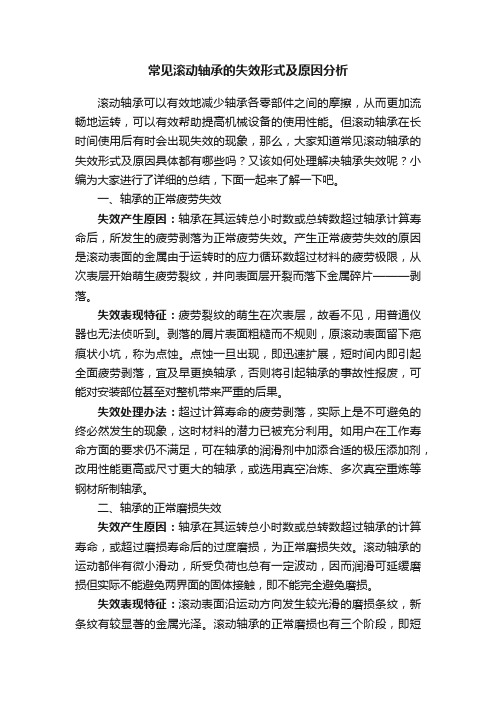
常见滚动轴承的失效形式及原因分析滚动轴承可以有效地减少轴承各零部件之间的摩擦,从而更加流畅地运转,可以有效帮助提高机械设备的使用性能。
但滚动轴承在长时间使用后有时会出现失效的现象,那么,大家知道常见滚动轴承的失效形式及原因具体都有哪些吗?又该如何处理解决轴承失效呢?小编为大家进行了详细的总结,下面一起来了解一下吧。
一、轴承的正常疲劳失效失效产生原因:轴承在其运转总小时数或总转数超过轴承计算寿命后,所发生的疲劳剥落为正常疲劳失效。
产生正常疲劳失效的原因是滚动表面的金属由于运转时的应力循环数超过材料的疲劳极限,从次表层开始萌生疲劳裂纹,并向表面层开裂而落下金属碎片———剥落。
失效表现特征:疲劳裂纹的萌生在次表层,故看不见,用普通仪器也无法侦听到。
剥落的屑片表面粗糙而不规则,原滚动表面留下疤痕状小坑,称为点蚀。
点蚀一旦出现,即迅速扩展,短时间内即引起全面疲劳剥落,宜及早更换轴承,否则将引起轴承的事故性报废,可能对安装部位甚至对整机带来严重的后果。
失效处理办法:超过计算寿命的疲劳剥落,实际上是不可避免的终必然发生的现象,这时材料的潜力已被充分利用。
如用户在工作寿命方面的要求仍不满足,可在轴承的润滑剂中加添合适的极压添加剂,改用性能更高或尺寸更大的轴承,或选用真空冶炼、多次真空重炼等钢材所制轴承。
二、轴承的正常磨损失效失效产生原因:轴承在其运转总小时数或总转数超过轴承的计算寿命,或超过磨损寿命后的过度磨损,为正常磨损失效。
滚动轴承的运动都伴有微小滑动,所受负荷也总有一定波动,因而润滑可延缓磨损但实际不能避免两界面的固体接触,即不能完全避免磨损。
失效表现特征:滚动表面沿运动方向发生较光滑的磨损条纹,新条纹有较显著的金属光泽。
滚动轴承的正常磨损也有三个阶段,即短期的“跑合”磨损,很长时间的平缓磨损,以及短期的剧烈磨损,终使轴承的精度丧失,或引起振动和噪声而不能继续使用。
失效处理办法:超过额定寿命或磨损寿命的磨损失效,在现有技术水平条件下实际上也是不可避免的。
滚动轴承常见的失效形式及原因
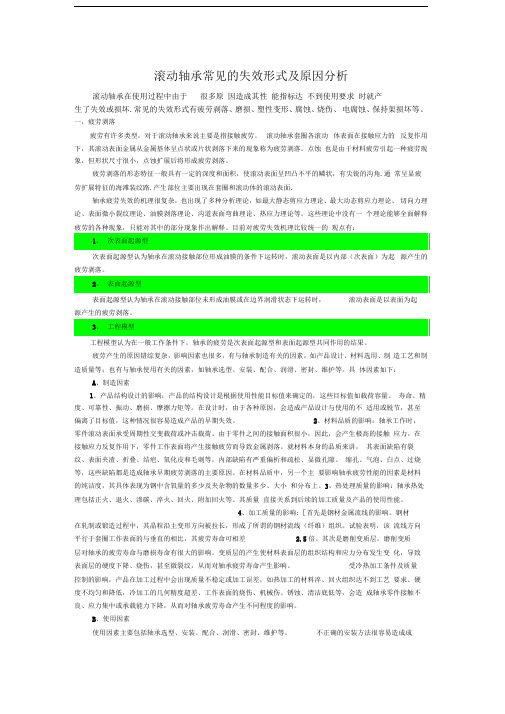
滚动轴承常见的失效形式及原因分析滚动轴承在使用过程中由于很多原因造成其性能指标达不到使用要求时就产生了失效或损坏.常见的失效形式有疲劳剥落、磨损、塑性变形、腐蚀、烧伤、电腐蚀、保持架损坏等。
一,疲劳剥落疲劳有许多类型,对于滚动轴承来说主要是指接触疲劳。
滚动轴承套圈各滚动体表面在接触应力的反复作用下,其滚动表面金属从金属基体呈点状或片状剥落下来的现象称为疲劳剥落。
点蚀也是由于材料疲劳引起一种疲劳现象,但形状尺寸很小,点蚀扩展后将形成疲劳剥落。
疲劳剥落的形态特征一般具有一定的深度和面积,使滚动表面呈凹凸不平的鳞状,有尖锐的沟角.通常呈显疲劳扩展特征的海滩装纹路.产生部位主要出现在套圈和滚动体的滚动表面.轴承疲劳失效的机理很复杂,也出现了多种分析理论,如最大静态剪应力理论、最大动态剪应力理论、切向力理论、表面微小裂纹理论、油膜剥落理论、沟道表面弯曲理论、热应力理论等。
这些理论中没有一个理论能够全面解释疲劳的各种现象,只能对其中的部分现象作出解释。
目前对疲劳失效机理比较统一的观点有:次表面起源型认为轴承在滚动接触部位形成油膜的条件下运转时,滚动表面是以内部(次表面)为起源产生的疲劳剥落。
表面起源型认为轴承在滚动接触部位未形成油膜或在边界润滑状态下运转时,滚动表面是以表面为起源产生的疲劳剥落。
工程模型认为在一般工作条件下,轴承的疲劳是次表面起源型和表面起源型共同作用的结果。
疲劳产生的原因错综复杂,影响因素也很多,有与轴承制造有关的因素,如产品设计、材料选用、制造工艺和制造质量等;也有与轴承使用有关的因素,如轴承选型、安装、配合、润滑、密封、维护等。
具体因素如下:A、制造因素1、产品结构设计的影响:产品的结构设计是根据使用性能目标值来确定的,这些目标值如载荷容量、寿命、精度、可靠性、振动、磨损、摩擦力矩等。
在设计时,由于各种原因,会造成产品设计与使用的不适用或脱节,甚至偏离了目标值,这种情况很容易造成产品的早期失效。
滚动轴承常见的失效形式与原因分析
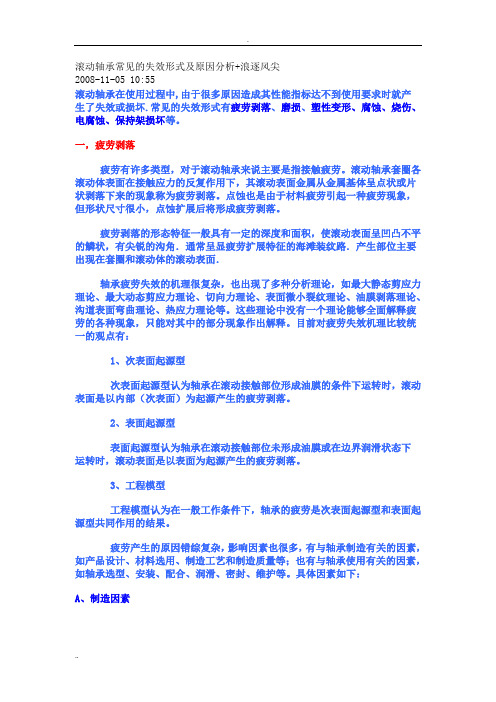
滚动轴承常见的失效形式及原因分析+浪逐风尖2008-11-05 10:55滚动轴承在使用过程中,由于很多原因造成其性能指标达不到使用要求时就产生了失效或损坏.常见的失效形式有疲劳剥落、磨损、塑性变形、腐蚀、烧伤、电腐蚀、保持架损坏等。
一,疲劳剥落疲劳有许多类型,对于滚动轴承来说主要是指接触疲劳。
滚动轴承套圈各滚动体表面在接触应力的反复作用下,其滚动表面金属从金属基体呈点状或片状剥落下来的现象称为疲劳剥落。
点蚀也是由于材料疲劳引起一种疲劳现象,但形状尺寸很小,点蚀扩展后将形成疲劳剥落。
疲劳剥落的形态特征一般具有一定的深度和面积,使滚动表面呈凹凸不平的鳞状,有尖锐的沟角.通常呈显疲劳扩展特征的海滩装纹路.产生部位主要出现在套圈和滚动体的滚动表面.轴承疲劳失效的机理很复杂,也出现了多种分析理论,如最大静态剪应力理论、最大动态剪应力理论、切向力理论、表面微小裂纹理论、油膜剥落理论、沟道表面弯曲理论、热应力理论等。
这些理论中没有一个理论能够全面解释疲劳的各种现象,只能对其中的部分现象作出解释。
目前对疲劳失效机理比较统一的观点有:1、次表面起源型次表面起源型认为轴承在滚动接触部位形成油膜的条件下运转时,滚动表面是以内部(次表面)为起源产生的疲劳剥落。
2、表面起源型表面起源型认为轴承在滚动接触部位未形成油膜或在边界润滑状态下运转时,滚动表面是以表面为起源产生的疲劳剥落。
3、工程模型工程模型认为在一般工作条件下,轴承的疲劳是次表面起源型和表面起源型共同作用的结果。
疲劳产生的原因错综复杂,影响因素也很多,有与轴承制造有关的因素,如产品设计、材料选用、制造工艺和制造质量等;也有与轴承使用有关的因素,如轴承选型、安装、配合、润滑、密封、维护等。
具体因素如下:A、制造因素1、产品结构设计的影响产品的结构设计是根据使用性能目标值来确定的,这些目标值如载荷容量、寿命、精度、可靠性、振动、磨损、摩擦力矩等。
在设计时,由于各种原因,会造成产品设计与使用的不适用或脱节,甚至偏离了目标值,这种情况很容易造成产品的早期失效。