连铸
连铸生产工艺流程
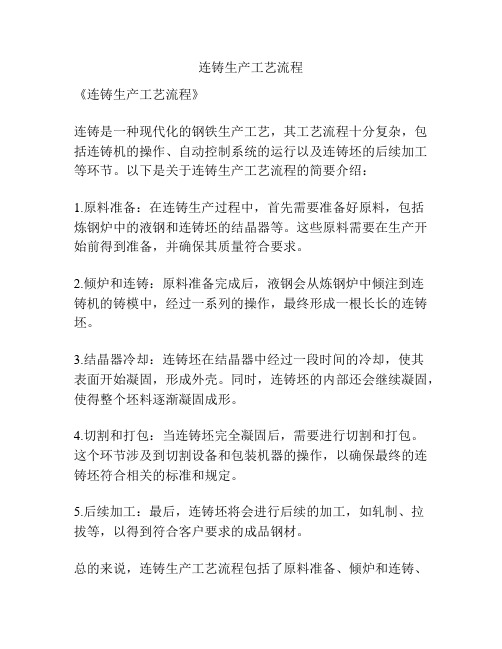
连铸生产工艺流程
《连铸生产工艺流程》
连铸是一种现代化的钢铁生产工艺,其工艺流程十分复杂,包括连铸机的操作、自动控制系统的运行以及连铸坯的后续加工等环节。
以下是关于连铸生产工艺流程的简要介绍:
1.原料准备:在连铸生产过程中,首先需要准备好原料,包括
炼钢炉中的液钢和连铸坯的结晶器等。
这些原料需要在生产开始前得到准备,并确保其质量符合要求。
2.倾炉和连铸:原料准备完成后,液钢会从炼钢炉中倾注到连
铸机的铸模中,经过一系列的操作,最终形成一根长长的连铸坯。
3.结晶器冷却:连铸坯在结晶器中经过一段时间的冷却,使其
表面开始凝固,形成外壳。
同时,连铸坯的内部还会继续凝固,使得整个坯料逐渐凝固成形。
4.切割和打包:当连铸坯完全凝固后,需要进行切割和打包。
这个环节涉及到切割设备和包装机器的操作,以确保最终的连铸坯符合相关的标准和规定。
5.后续加工:最后,连铸坯将会进行后续的加工,如轧制、拉
拔等,以得到符合客户要求的成品钢材。
总的来说,连铸生产工艺流程包括了原料准备、倾炉和连铸、
结晶器冷却、切割和打包以及后续加工等几个主要环节。
通过这些操作,连铸生产工艺可以实现高效、自动化的生产,为钢铁行业的发展做出了重要贡献。
连铸的原理

连铸的原理
连铸是一种先进的铸造工艺,它通过在同一设备上连续进行浇铸和凝固,实现了铸坯的一次成型,大大提高了生产效率和产品质量。
连铸的原理主要包括连续浇铸、连续凝固和连续切割三个方面。
首先,连续浇铸是指在连铸设备上通过连续浇注熔融金属,使金属液不间断地流入结晶器中。
这样可以避免浇注过程中的温度变化和氧化,保证了金属液的纯净度和温度稳定性。
同时,连续浇铸还可以减少浇注过程中的气体夹杂和金属液的氧化,提高了产品的内部质量。
其次,连续凝固是指在结晶器中,熔融金属通过连续往复的凝固过程,逐渐形成固态铸坯。
在这个过程中,结晶器内部的冷却系统不断地将热量带走,使金属液逐渐凝固成固态金属。
通过控制结晶器的温度和冷却速度,可以实现对铸坯组织和性能的精确控制,从而获得更高质量的产品。
最后,连续切割是指在连铸设备的出口处,通过连续的切割装置将凝固成型的铸坯切割成所需长度的产品。
这样可以避免传统浇铸中的冷却等待时间,提高了生产效率。
同时,连续切割还可以减少铸坯表面的氧化和变形,保证了产品的表面质量和尺寸精度。
总的来说,连铸的原理是通过连续浇铸、连续凝固和连续切割,实现了铸坯的一次成型,大大提高了生产效率和产品质量。
这种先进的铸造工艺在现代工业生产中得到了广泛应用,为各种金属制品的生产提供了可靠的技术保障。
连铸过程原理及数值模拟

连铸过程原理及数值模拟连铸是一种重要的金属成形工艺,广泛应用于钢铁、铝合金等金属材料的生产和加工中。
连铸过程原理及数值模拟是研究连铸工艺的关键内容,通过对连铸过程的原理分析和数值模拟,可以优化连铸工艺参数,提高产品质量和生产效率。
连铸过程是将熔融金属直接注入到连续运动的铸坯中,通过冷却和凝固过程,将熔融金属转化为固态铸坯。
连铸的基本原理是利用连续运动的铸坯带走热量,使熔融金属迅速凝固,形成连续的固态铸坯。
在连铸过程中,主要包括液相区、液固两相区和固相区三个区域。
在液相区,熔融金属通过连续浇注,填充到铸坯的空腔中。
熔融金属的温度高于固相线,处于液态状态。
随着熔融金属的注入,液相区的长度逐渐增加。
在液固两相区,熔融金属和正在凝固的铸坯同时存在。
由于熔融金属的温度高于固相线,所以熔融金属仍然保持液态。
而铸坯由于受到液相的热量传递,开始逐渐凝固。
在这个区域中,液相区的长度逐渐减小,凝固铸坯的长度逐渐增加。
在固相区,整个铸坯都已经完全凝固。
熔融金属已经完全转化为固态,形成连续的固态铸坯。
在这个区域中,液相区的长度为零,凝固铸坯的长度为整个连铸过程的长度。
为了研究连铸过程的细节和优化连铸工艺参数,数值模拟成为一种重要的方法。
数值模拟是通过数学模型和计算机仿真技术,对连铸过程进行模拟和分析。
数值模拟可以准确地计算连铸过程中的温度场、流场和凝固结构等关键参数,为工艺优化提供科学依据。
在连铸过程的数值模拟中,需要考虑多个物理过程的相互作用。
首先是流体力学过程,包括熔融金属的流动和铸坯带走热量的过程。
其次是热传导过程,包括熔融金属的冷却和凝固过程。
最后是凝固结构演化过程,包括铸坯的晶粒生长和偏析等现象。
为了建立连铸过程的数值模型,需要考虑材料的物理性质、流体力学和热传导方程等方面的参数。
同时,还需要考虑边界条件和初始条件等参数。
通过数值模拟,可以预测连铸过程中的温度分布、流速分布和凝固结构等重要参数,为工艺优化提供指导。
连铸技术的基本原理
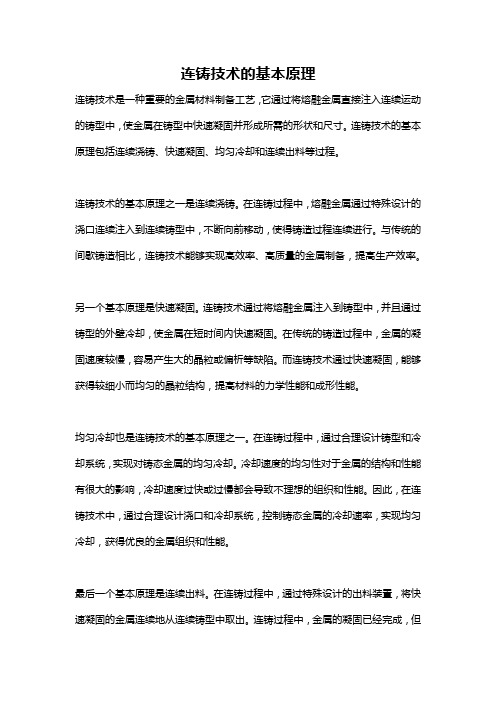
连铸技术的基本原理连铸技术是一种重要的金属材料制备工艺,它通过将熔融金属直接注入连续运动的铸型中,使金属在铸型中快速凝固并形成所需的形状和尺寸。
连铸技术的基本原理包括连续浇铸、快速凝固、均匀冷却和连续出料等过程。
连铸技术的基本原理之一是连续浇铸。
在连铸过程中,熔融金属通过特殊设计的浇口连续注入到连续铸型中,不断向前移动,使得铸造过程连续进行。
与传统的间歇铸造相比,连铸技术能够实现高效率、高质量的金属制备,提高生产效率。
另一个基本原理是快速凝固。
连铸技术通过将熔融金属注入到铸型中,并且通过铸型的外壁冷却,使金属在短时间内快速凝固。
在传统的铸造过程中,金属的凝固速度较慢,容易产生大的晶粒或偏析等缺陷。
而连铸技术通过快速凝固,能够获得较细小而均匀的晶粒结构,提高材料的力学性能和成形性能。
均匀冷却也是连铸技术的基本原理之一。
在连铸过程中,通过合理设计铸型和冷却系统,实现对铸态金属的均匀冷却。
冷却速度的均匀性对于金属的结构和性能有很大的影响,冷却速度过快或过慢都会导致不理想的组织和性能。
因此,在连铸技术中,通过合理设计浇口和冷却系统,控制铸态金属的冷却速率,实现均匀冷却,获得优良的金属组织和性能。
最后一个基本原理是连续出料。
在连铸过程中,通过特殊设计的出料装置,将快速凝固的金属连续地从连续铸型中取出。
连铸过程中,金属的凝固已经完成,但温度较高,通过连续出料并进行后续的热处理,可以获得所需的金属材料。
总的来说,连铸技术的基本原理包括连续浇铸、快速凝固、均匀冷却和连续出料。
这些原理相互作用,使得连铸技术成为一种高效、高质量的金属材料制备方法。
连铸技术的广泛应用,不仅能够提高金属材料的生产效率,提高材料的力学性能和成形性能,还能够减少金属材料的能源消耗和环境污染。
随着现代工业的发展,连铸技术在制造业中的地位和作用将越来越重要,对于推动金属材料制造业的发展具有重要的意义。
连铸絮流的原因

连铸絮流的原因
连铸絮流的原因可以归结为以下几个方面:
1. 液态金属流动不稳定:在连铸过程中,液态金属在急速凝固的条件下流动,容易受到外界因素的干扰,如震动、气泡等,导致流动不稳定,产生絮状流动。
2. 浇注速度过快:如果浇注速度过快,液态金属在流动过程中容易形成涡流或涡旋,从而形成絮状流动。
3. 浇注过程中的气体和杂质:连铸过程中,液态金属中可能存在气体和杂质,这些气体和杂质在流动过程中容易聚集在一起,形成絮状流动。
4. 浇注温度不均匀:连铸过程中,由于温度分布不均匀,液态金属在流动过程中可能出现冷凝现象,导致絮状流动的产生。
5. 浇注模具设计不合理:连铸模具的设计不合理,如出口形状不当、流道设计不合理等,会导致液态金属流动不稳定,形成絮状流动。
连铸絮流的原因主要包括液态金属流动不稳定、浇注速度过快、存在气体和杂质、浇注温度不均匀以及浇注模具设计不合理等因素。
连铸的名词解释
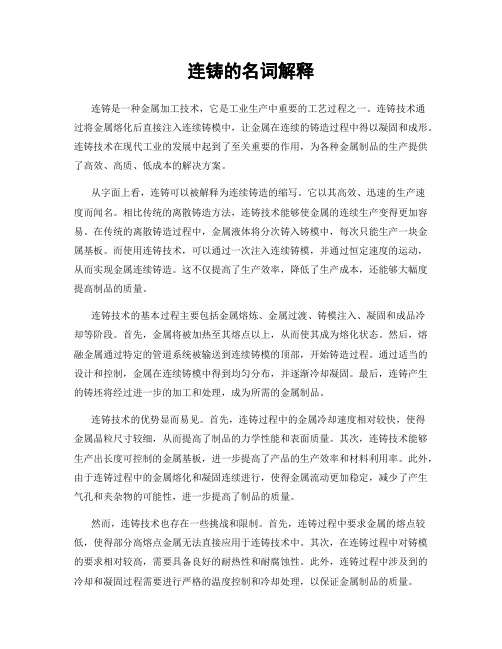
连铸的名词解释连铸是一种金属加工技术,它是工业生产中重要的工艺过程之一。
连铸技术通过将金属熔化后直接注入连续铸模中,让金属在连续的铸造过程中得以凝固和成形。
连铸技术在现代工业的发展中起到了至关重要的作用,为各种金属制品的生产提供了高效、高质、低成本的解决方案。
从字面上看,连铸可以被解释为连续铸造的缩写。
它以其高效、迅速的生产速度而闻名。
相比传统的离散铸造方法,连铸技术能够使金属的连续生产变得更加容易。
在传统的离散铸造过程中,金属液体将分次铸入铸模中,每次只能生产一块金属基板。
而使用连铸技术,可以通过一次注入连续铸模,并通过恒定速度的运动,从而实现金属连续铸造。
这不仅提高了生产效率,降低了生产成本,还能够大幅度提高制品的质量。
连铸技术的基本过程主要包括金属熔炼、金属过渡、铸模注入、凝固和成品冷却等阶段。
首先,金属将被加热至其熔点以上,从而使其成为熔化状态。
然后,熔融金属通过特定的管道系统被输送到连续铸模的顶部,开始铸造过程。
通过适当的设计和控制,金属在连续铸模中得到均匀分布,并逐渐冷却凝固。
最后,连铸产生的铸坯将经过进一步的加工和处理,成为所需的金属制品。
连铸技术的优势显而易见。
首先,连铸过程中的金属冷却速度相对较快,使得金属晶粒尺寸较细,从而提高了制品的力学性能和表面质量。
其次,连铸技术能够生产出长度可控制的金属基板,进一步提高了产品的生产效率和材料利用率。
此外,由于连铸过程中的金属熔化和凝固连续进行,使得金属流动更加稳定,减少了产生气孔和夹杂物的可能性,进一步提高了制品的质量。
然而,连铸技术也存在一些挑战和限制。
首先,连铸过程中要求金属的熔点较低,使得部分高熔点金属无法直接应用于连铸技术中。
其次,在连铸过程中对铸模的要求相对较高,需要具备良好的耐热性和耐腐蚀性。
此外,连铸过程中涉及到的冷却和凝固过程需要进行严格的温度控制和冷却处理,以保证金属制品的质量。
尽管如此,连铸技术在如今的工业生产中扮演了重要的角色。
连铸工艺流程

连铸工艺流程连铸是一种常用的铸造工艺,适用于生产长条状或板状金属材料。
它是通过将熔化的金属直接倒入连续流动的水冷铜板中,使其冷却并形成连续的长条状或板状产品。
连铸工艺具有高效率、低能耗、高品质等优点,广泛应用于钢铁、铝合金等行业。
连铸工艺流程主要包括准备工作、连续浇铸、冷却和切割四个阶段。
首先是准备工作。
这个阶段包括准备熔炉、铜板、铸模、流动水和其他所需设备和材料。
熔炉中加入合适的金属原料,加热使其熔化。
同时,准备好冷却水,并确保其具有足够的流动性和温度适宜。
铜板和铸模是制造连铸机的主要部件,需要进行充分的清洗和检查,以确保表面平整和无缺陷。
接下来是连续浇铸。
将熔化的金属倒入连铸机的铜板中,通过喷头将金属喷向铸模,并使其连续地流动。
连铸机的喷头是一个关键部件,可以调整金属流动的速度和方向,以保证产品的质量。
同时,需要控制好浇注速度和温度,以避免金属过热或过冷,影响产品的性能。
然后是冷却。
在连铸过程中,金属材料与铜板接触,通过快速传热,使金属迅速冷却并凝固。
冷却水通过铜板流过,吸收金属的热量,并保持适宜的温度。
冷却水的流量和温度需要根据不同金属材料进行调整,以确保产品的结晶组织和力学性能。
最后是切割。
冷却后的连铸坯可以根据需要进行切割成适当的长度,以便进一步加工。
切割可以通过割断或切削进行。
割断是指使用切割设备将连铸坯切成所需长度,并去除不良部分。
切削是指使用机械切割工具将连铸坯切割成规定的尺寸和形状。
总之,连铸工艺是一种高效、高品质的铸造工艺,适用于生产长条状或板状金属材料。
其主要流程包括准备工作、连续浇铸、冷却和切割。
通过合理调整浇注速度、温度和冷却设备,可以制造出具有良好结晶组织和优异性能的产品。
连铸工艺的应用范围广泛,为钢铁、铝合金等行业的发展提供了重要的支撑。
炼钢厂连铸工艺流程

炼钢厂连铸工艺流程1.钢水准备:从炼钢炉中输出得到熔化的钢水,然后通过脱氧、温度调节和脱气等工艺处理,得到适合连铸工艺的钢水。
2.连铸结晶器:将处理后的钢水通过倾转、倾倒和挤压等技术,直接浇注到连铸机结晶器中。
结晶器内部有一组多孔结晶器衬套,通过冷却水的循环,将钢水快速冷却并结晶。
3.凝固:钢水在结晶器中快速冷却,开始凝固成为连续铸坯。
凝固过程中,还会通过控制结晶器内的冷却水温度和流量,来调节钢坯的凝固速度和结晶器壁的温度。
4.伸展:连续铸坯凝固后,通过拉伸机构将钢坯从结晶器中拉出,使其变长,同时也能控制钢坯的截面形状。
这个过程中,还会进行坯底冷却,以控制坯底凝固的厚度。
5.切割:钢坯经过拉伸后,通过切割机构将其切断成合适的长度,以供后续工序使用。
6.冷却:切割成合适长度的连续铸坯通过冷却水箱,进行冷却。
冷却的目的是使钢坯的内部和外部温度均匀降低,以便后续的轧制工艺。
7.钢坯调整:冷却后的连续铸坯,根据需要可能需要进行尺寸调整。
这个过程中通常使用钢坯矫直机、切割坯边机等设备,对钢坯进行校直和修边,使其符合轧制工艺要求。
8.轧制:经过调整后的钢坯将被送入炼钢厂的轧机进行轧制。
根据需要,钢坯可能还会经过多道次的轧制和调整。
9.检测:轧制后的产品将进入质检环节,通过各种非破坏性和破坏性检测手段,对产品进行检测,以确保其质量符合要求。
10.成品:经过检测合格后,轧制后的产品成品将根据需求进行打包、标记和存储,以便销售和运输。
综上所述,炼钢厂连铸工艺流程是将熔化的钢水通过连续铸造技术直接浇注到连铸机结晶器中,经过凝固、伸展、切割、冷却、调整、轧制、检测等一系列工艺处理,最终得到质检合格的连续铸坯。
这种工艺流程具有工艺连续、设备高效、产品质量稳定等优点,已被广泛应用于炼钢厂的生产中。
- 1、下载文档前请自行甄别文档内容的完整性,平台不提供额外的编辑、内容补充、找答案等附加服务。
- 2、"仅部分预览"的文档,不可在线预览部分如存在完整性等问题,可反馈申请退款(可完整预览的文档不适用该条件!)。
- 3、如文档侵犯您的权益,请联系客服反馈,我们会尽快为您处理(人工客服工作时间:9:00-18:30)。
实验测定:
实验研究指出,树枝晶间距 l 与凝固速度 R 和温度梯度有关。
l CR m G n
雅可比试验不同温度梯度和凝固速度对树枝形态的影响,并测定 了 l 和 l 与 R 和 G 关系,如图4-13所示。由图可得出: 上述两经验式中,对一次晶间距,指数m、n值相差较大;对二次 晶间距,m、n值近似相等。不同作者得到的m、n值相差较大。 试验指出,二次枝晶间距与区域凝固时间 们的经验关系式:
(2) 成分过冷条件,由平衡相图可知:
dT dC m dx dx
dT dC 式中: 为凝固前沿液相线温度梯度; dx dx 固前沿浓度梯度; m为液相线斜率。
为凝
当液体中实际温度低于液相线温度时就产生了成分过冷 区。那么不产生过冷的条件应该是实际温度梯度大于或 等于液相线温度梯度。即: dT dC 或 ( 4-11) G m G dx x 0 dx x 0 式中:G为液体中实际温度梯度,它决定于向外界的传 热。
O O
O O
O O
钢 坯 清 理 O
加 热
轧 制
轧 钢 燃 料 消 耗 ×109J/t
2.01 0.92
O
O O
3 4 5
O O O
O O O
O
O O O
O O O
1.34 0.878 0.334
6
连铸坯直接轧 制CC-DR
O
O
角 部 补 热
O
4 连铸技术的发展历史
(1)19世纪中叶H.Bessemer提出了连续浇注金属的构想; (2)1933年,现代连铸的奠基人S.Junghans提出并发展 了结晶器振动装置,奠定了连铸的工业应用的基础; (3)本世纪30年代,连铸成功应用于有色金属; (4)1950年, S.Junghans和Mannesmann公司合作,建成 世界上第一台工业连铸机; (5)50年代,工业应用时期; 到50年代末,有连铸机30台,产量110t,连铸比0.34%. (6)60年代,稳步发展时期; 到60年代末,有连铸机200余台,产量4000万t. (7)70年代,迅猛发展时期; 1981年连铸比33.8%. (8)80年代,完全成熟时期; 1990年连铸比64.1%; (9)90年代,近终型连铸技术时代
(4)求 G 和
1 3 G (2 3 cos cos )( r G r 2 lc ) 3
3
r
:
( G ) 0 r
而
2 3 cos cos 0,
3
(2 3cos cos3 ) 2r lc r 2 G 0
505.7 605.7 931.7 1356 1493 1803 1725 1736
1.1.2 非均质形核
上图为一个平面的夹杂物上形成一个半球缺的固体晶核,晶核与液 体、固体有三个界面。处于平衡时:
式中:
为界面张力; 表示晶体在夹杂物表面的润湿倾向。
ls cs cos lc
参考书目
(1) 炼钢学原理 冶金工业出版社,曲英主编。 (2) 浇注与凝固 冶金工业出版社,蔡开科主编。 (3) 连续铸钢 科学出版社,蔡开科主编。
(4) 钢铁冶金学(炼钢部分)
冶金工业出版社, 陈家祥主编。
前 言
1 现代炼钢技术的发展(连铸技术的作用)
( 1)
1947年-1974年:
技术特点:转炉、高炉的大型化;以模铸-初轧 为核心,生产外延扩大。
1 凝固理论
1 凝固理论
1.1 钢液结晶与凝固结构
1.1.1 均质形核
(1)新核的形成引起系统的自由能的变化: · 体积自由能的下降: ΔGv=-(4/3)(πγ3 (GA-GB)) 式中:γ:球形晶核的半径;GA:A相体积自由能; GB:A相体积自由能 · 表面自由能的增加: ΔGF=4πγ2σ 式中:σ:A、B两相界面自由能 (2) 均质形核的条件: ΔGΣ=ΔGv+ΔGF=-(4/3)(πγ3 (GA-GB))+4πγ2σ
(2)产生新相界表面自由能
GF lc 2r 2 (1 cos ) ( cs ls )r 2 (1 cos2 ) r 2 lc (2 3 cos cos3 )
(3)总自由能变化 G :
Gr
:
1 G r 3 (2 3 cos cos 2 )G r 2 lc (2 3 cos cos 3 ) 3
由图4-1可知,当ΔGΣ达到最大值时的晶核大小叫临界半径,在 r r 时,求:
由(4-4)式可知,临界晶核半径是与过冷度成反比。由图(4-1)可知: — 晶核长大导致系统自由能增加,新相不稳定; — 晶核长大导致系统自由能减少,新相能稳定生长; — 形核和晶核溶解处于平衡。 结论是:在一定温度下,任何大于临界半径的晶核趋向于长大,
1.1.3 晶体的长大
1.1.3.1 晶体的长大的能量消耗
- 原子的扩散
- 晶体的缺陷
- 原子的粘附
- 结晶潜热的导出
1.1.3.2 晶核长大的驱动力-成分过冷理论
(1)成分过冷的产生 ·纯金属凝固:过冷是靠模壁向外传热控制 ·合金凝固:
选分结晶
溶质元素在固相和液相的再分配 溶质浓度的不同使液相线温度不同Fra bibliotek钢的凝固与连续铸造
•教学目的:
本部分课程从钢的凝固原理出发, 结 合钢的连铸工艺,使学生从理论上和实践上 掌握浇注和凝固过程中发生的主要的物理化 学现象,初步掌握连铸工艺与设备及其最新 发展,为将来从事冶金工程领域的工作,为 生产高质量的连铸坯,以及解决连铸生产中 的实际问题奠定理论基础。
课程大纲
1.1.4.4 凝固结构对产品性能的影响
(1)柱状晶的枝干较纯,而枝晶间偏析
故: 2r lc r 2 G 0
r
2 lc G
以
r 代入
G 得:
4 lc 3 G 2 3 cos cos 2 3(G)
2
(4-10)
非均质形核功与均质形核功相差
— 180 , cos180 0 ,晶体独立于液体中,形核功与均质形核相同;
小于临界半径晶核趋向消失。
表4-1纯液体金属结晶过冷度
金属
Sn Pb Al Cu Mn Fe Ni Co
熔点
f ( K )
过冷度
ΔT(k)
103 80 130 130 308 295 319 330
T T f
0.208 0.133 0.110 0.174 0.206 0.161 0.186 0.181
前言
1
凝固理论
·钢液的结晶
·晶体的长大 ·凝固结构
1.1 钢液结晶与凝固结构
·凝固结构控制
1.2 凝固偏析 ·凝固显微偏析
·凝固宏观偏析
1.3 凝固收缩 1.4 钢的高温力学性能 1.5 凝固过程中气体和非金属夹杂物
2
连铸工艺与设备
2.1 连铸机机型及特点 2.2 连铸工艺与设备
-钢包
-中间包 -结晶器 -二次冷却区 -拉坯矫直机 -切割机 2.3 连铸新技术
1.1.4 凝固结构
1.1.4.1 钢水凝固过程的冶金特点
(1)δ -γ相的转变 · 稳定的δ相(或γ相)凝固 例如: 铁素体的Cr钢 · δ相凝固后转变为奥氏体 例如:Ni-Cr奥氏体不锈钢 · δ相凝固后转变为γ,再转变为α相 例如:低碳钢
(2)钢液的流动 (3)凝固收缩 (4)裂纹敏感性 (5)凝固结构
2 2
晶核与夹杂物接触面积:
r (1 cos )
球缺体积:
1 3 r (2 3 cos cos 3 ) 3
球缺表面积:
2rh 2r 2 (1 cos )
形成晶核时系统自由能变化: (1)体积自由能 Gv: Gv
1 3 r (2 3 cos cos 3 )G 3
4-15表示了不同凝固方法的冷却速度与树枝晶间距关系。由 于冷却速度的差异,故连铸坯的树枝晶结构比钢锭的要细。加 大冷却速度,可以得到较细的树枝晶结构。 文献中对二次枝晶间距与冷却速度还有不同的经验式。铃木等 人提出 C 0.88% 的炭钢中:
l 709 0.395 ( : C 分,l : )
0.5
t c 关系如图4-14。它
l 0.00716 tc (1.5%C,1.1%Mn)
l 0.0518 tc
0.44
(0.6%C,1.1%Mn)
树枝晶间距对钢锭结构、显微偏析有重要影响。实际钢锭凝固时 凝固速度与温度梯度不可能彼此独立变化,而通过凝固时放出热 量来影响整个凝固过程。这样就可用冷却速度来控制树枝晶间距 ,以得到细的树枝结构。而影响冷却速度最重要的因素是凝固方 法。图
1 (2 3 cos cos 3 ) 。由(4-10)式可知 4
—
0 , cos0 1 液体中质点已是一个晶核,不需任何过冷度就可形核;
,依附于外来质点形成晶核。
— 0 180
结论是非均质形核有效性决定于润湿角 。越小 ,形核功就越小,就易形核 ,形核速率比较如图4-4。非均质形核的过冷度比均质形核大为减少。在实际生 产中主要是非均质形核,除模壁表面作为“依托”形成晶核外,液体金属中需含 有两类小质点:一类叫活性质点,如金属氧化物(Al2O3),其晶体结构与金属 晶体结构相似,它们之间界面张力小,可作为“依托”而形成核心。另一类是难 熔物质的质点,它们的结构虽然与金属晶体结构相差较远,但这些难熔质点表面 往往存在细微凹坑和裂纹,其中尚未熔化的金属,可作为“依托”而形成晶体核 心。因此,可以在钢液中加入形核剂以细化晶粒。
( 2)
1974年-1989年:
技术特点:全连铸工艺,以连铸机为核心。