连铸教材
《连续铸钢操作与控制》课程标准

《连续铸钢操作与控制》课程标准一、课程性质和任务本课程是钢铁智能冶金技术专业的专业核心课程。
《连续铸钢操作与控制》是培养冶金行业从事连铸技术工作的必修课。
课程以连续铸钢生产的全过程为工作对象,面向的主要岗位包括大包浇注、中包浇注、连铸主控、连铸切割、铸坯质检等,主要培养学生在充分掌握连铸理论的前提下,能对主要岗位进行正确操作,运用所学理论知识解决连铸生产复杂问题,能够进行连铸坯质量控制、产品设计、工艺设计,以及具有连铸技术创新与应用等专业能力,同时注重培养学生的社会能力和职业素养,使学生成长为有能力的连铸人才。
二、课程教学目标本课程是为培养和提高学生具备专业能力、方法能力、社会能力。
(一)知识教学目标:(1)掌握连续铸钢生产技术的国内外发展概况与特点;(2)掌握连续铸钢的基本概念、基本原理、工艺过程;(3)掌握主要设备的结构与原理等,能画出设备简图;(4)掌握主要设备的性能,并能说明主要设备的特点;(5)掌握连续铸钢生产技术的主要技术经济指标;(6)掌握连铸机分类的有关知识,具有选择机型能力;(7)掌握铸坯的形成过程和影响因素;(8)掌握和计算浇铸温度、拉坯速度、冷却制度等参数;(9)掌握连铸生产时各参数对铸坯质量影响;(10)掌握和总结影响铸坯质量的因素;(11)掌握连续铸钢生产技术新技术、新工艺。
(二)能力培养目标:(1)具有识别和选用连铸常用耐火材料能力;(2)具有识别和选用连铸常用功能材料能力;(3)具有连铸计算机仿真操作能力;(4)具有检查和使用连铸设备和使用工器具能力;(5)具有连铸开浇前的准备工作能力;(6)能进行连铸开浇能力;(7)具有控制二冷强度、拉坯矫直以及脱锭工作能力;(8)具有连铸坯切割以及停浇操作能力;(9)具有铸坯精整能力;(10)具有分析铸坯缺陷的特征,并根据缺陷分析原因能力;(11)具有分析生产事故的特征,分析原因并解决能力;(12)具有根据生产要求对工艺过程进行调整,并能分析相关工艺规程能力。
连铸原理与工艺 教学大纲

连铸原理与工艺一、课程说明课程编号:050122Z10课程名称:连铸原理与工艺/ The Principle and Technology of Continuous Casting课程类别:专业选修课学时/学分:32 /2先修课程:冶金原理;冶金设备;钢铁冶金学适用专业:冶金工程教材、教学参考书:1. 蔡开科. 连续铸钢原理与工艺. 北京: 冶金工业出版社, 20022.史宸兴主编. 实用连铸冶金技术. 北京: 冶金工业出版社, 19983.蔡开科主编. 连铸坯质量控制. 北京: 冶金工业出版社, 20104.熊毅刚主编. 现代钢铁工业技术-板坯连铸. 北京: 冶金工业出版社, 1994 5.朱苗勇主编. 现代冶金学(钢铁冶金卷). 北京: 冶金工业出版社, 2005 6.黄希祜编. 钢铁冶金原理. 北京: 冶金工业出版社, 2002二、课程设置的目的意义连铸原理与工艺是建立在冶金原理、传输原理和冶金设备基础之上,是针对钢铁冶金最关的键环节-连铸过程的相关理论和工艺的全面阐述,是培养冶金工程专业高级技术人员的核心专业课程。
通过本课程的学习,使学生了解国内外连续铸钢的发展,连铸机型和结构特征,连铸工艺参数的设计原理,连铸钢水质量控制,连铸操作工艺,中间包冶金,连铸保护浇注,结晶器冶金,连铸坯凝固与传热,连铸二次冷却控制,连铸坯质量控制,连铸保护渣和覆盖剂等,为从事炼钢和连铸生产、设计、科研打下基础。
三、课程的基本要求知识要求:了解国内外连续铸钢的发展概况;连续铸钢的优越性;传统连铸技术的发展与新的连铸技术的开发;连铸机机型分类;各种连铸机的特点;小方坯、板坯、圆坯、大方坯连铸机的结构特征;连铸机机型选择原则;以及连铸机型的确定等。
能力要求:熟练掌握连铸工艺参数的设计原理,包括连铸机生产能力,连铸机产量计算,铸坯断面,连铸机流数,浇注时间,准备时间,准备时间,铸机的弧形半径,冶金长度,拉速设计,中间包容积,中间包内腔主要尺寸,中间包内腔主要尺寸,结晶器的结构,结晶器主要尺寸计算,结晶器冷却水量,二冷区水量及各段水量分配,水口设计等的定义、设计原理和优化标准。
连铸理论与工艺板坯连铸资料课件

拉坯速度的不稳定可能导致连铸坯质量波动。为确保拉坯速度稳定,应定期对拉坯设备进行维护,优化 连铸工艺参数,以减小速度波动范围,提高连铸过程势与展 望
连铸技术的前沿研究动态
高效连铸技术
提高连铸机的生产效率,减少能源消耗和环境污染是当前研究的重点。例如, 开发新型结晶器、优化二冷制度等都能有效提高连铸效率。
连铸工艺优点
与传统模铸相比,连铸具有高效、节能、提高金属收得率和产品质量等 优点。
03
连铸工艺类型
根据连铸机的结构和铸坯的运出方式,连铸工艺主要分为立式、立弯式
、弧形和水平连铸等。
连铸过程中的传热与凝固
传热机制
连铸过程中的传热主要包括钢水与结晶器壁之间的对流换热、结 晶器壁的导热以及坯壳与冷却水之间的对流换热。
连铸理论与工艺板坯连铸资料课 件
contents
目录
• 连铸理论基础 • 板坯连铸工艺与技术 • 连铸过程中的问题与解决方案 • 连铸工艺的未来发展趋势与展望
01
连铸理论基础
连铸工艺概述
01 02
连铸工艺定义
连铸工艺是将钢水直接连续倒入特定形状的结晶器中,通过强制冷却使 钢水在结晶器中快速凝固成具有一定形状、尺寸和内部质量的连铸坯的 工艺过程。
在保证产品质量和生产效率的前提下,降 低原料、能源、人力等方面的成本,提高 企业经济效益。
03
连铸过程中的问题与解决方案
连铸坯表面质量缺陷及预防措施
裂纹
连铸坯表面裂纹是常见的缺陷,主要源于铸坯在凝固过程中的内部应力。预防措施包括优 化连铸工艺参数,如浇注温度、拉坯速度,以及改善二冷区冷却制度等。
凝固前沿与坯壳生长
随着热量的传递,钢水在结晶器内逐渐形成凝固前沿,坯壳从凝固 前沿向外生长,直至完全凝固。
连铸工艺部分讲义 ppt课件

第一部分:
二、中间包
连铸耐材
14
第一部分:
二、中间包
连铸耐材
15
第一部分: 连铸耐材
二、中间包
4、中间包的准备 :
4.1 快换机件、上水口、座砖安装 4.1.1 喷涂:用石墨粉喷涂上水口座圈外圆和快换机构的加紧环内壁。 4.1.2 吻合:下装上水口并使其下表面露出加紧环1~2mm,调整上水口吹氩 进气口,必须使其与快换机构的吹氩喷嘴吻合。 4.1.3 检测压力:检查快换机构里的空气弹簧,其压力在1200~1600N。 4.1.4 清理:清理干净盖板下表面、上水口下表面和中包座圈上表面。 4.1.5 确认垂直:在中间包上方目测上水口是否垂直于水平面,否则重装。 4.1.6 捣打紧密:座砖、上水口座圈、定位板之间的缝隙必须使用已拌匀的 捣打料捣打紧密。 4.1.7 涂抹结合面:上水口与座砖结合面泥浆饱满,泥浆用玻璃水混成。 4.1.8 座砖就位:座砖底面与定位板上表面在安装前必须干净,就位后用木 锤打结实。 4.1.9 测试:安装完毕后用浸入式水口测试快换机构2次,观察快换机构是 否灵活,观察上水口与浸入式水口之间有无缝隙。
25
第一部分: 连铸耐材
二、中间包
8、关于长寿命中间包:
26
第一部分: 连铸耐材
二、浸入式水口
1、作用: 隔绝空气,防止
钢水二次氧化。
2、材质:
大多为镁碳或铝碳 加锆质材料组成, 也有石英材料制成 的。
结晶器卷渣示意图
保护渣层
结晶器卷渣示意图
A,B,C为卷渣处
27
第一部分: 连铸耐材
二、浸入式水口
一、连铸耐材
连铸耐材
8
第一部分:
二、中间包
连铸耐材
连铸工教程1
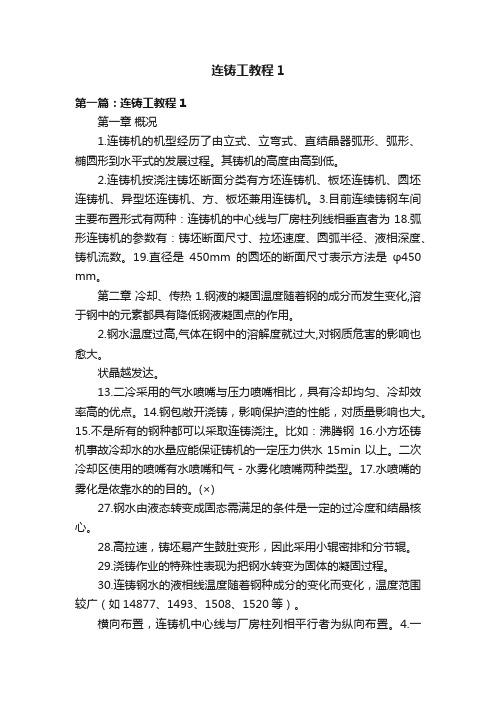
连铸工教程1第一篇:连铸工教程1第一章概况1.连铸机的机型经历了由立式、立弯式、直结晶器弧形、弧形、椭圆形到水平式的发展过程。
其铸机的高度由高到低。
2.连铸机按浇注铸坯断面分类有方坯连铸机、板坯连铸机、圆坯连铸机、异型坯连铸机、方、板坯兼用连铸机。
3.目前连续铸钢车间主要布置形式有两种:连铸机的中心线与厂房柱列线相垂直者为18.弧形连铸机的参数有:铸坯断面尺寸、拉坯速度、圆弧半径、液相深度、铸机流数。
19.直径是450mm的圆坯的断面尺寸表示方法是φ450 mm。
第二章冷却、传热 1.钢液的凝固温度随着钢的成分而发生变化,溶于钢中的元素都具有降低钢液凝固点的作用。
2.钢水温度过高,气体在钢中的溶解度就过大,对钢质危害的影响也愈大。
状晶越发达。
13.二冷采用的气水喷嘴与压力喷嘴相比,具有冷却均匀、冷却效率高的优点。
14.钢包敞开浇铸,影响保护渣的性能,对质量影响也大。
15.不是所有的钢种都可以采取连铸浇注。
比如:沸腾钢16.小方坯铸机事故冷却水的水量应能保证铸机的一定压力供水15min以上。
二次冷却区使用的喷嘴有水喷嘴和气-水雾化喷嘴两种类型。
17.水喷嘴的雾化是依靠水的的目的。
(×)27.钢水由液态转变成固态需满足的条件是一定的过冷度和结晶核心。
28.高拉速,铸坯易产生鼓肚变形,因此采用小辊密排和分节辊。
29.浇铸作业的特殊性表现为把钢水转变为固体的凝固过程。
30.连铸钢水的液相线温度随着钢种成分的变化而变化,温度范围较广(如14877、1493、1508、1520等)。
横向布置,连铸机中心线与厂房柱列相平行者为纵向布置。
4.一台连铸机具有独立传动系统的机组数目,称为连铸机的机数。
5.一台连铸机能同时浇注的铸坯根数称为连铸机的流数。
6.影响铸机拉速因素有钢种、断面、钢水温度等。
7.弧形连铸机的铸机半径与铸坯厚度有关。
8.立弯式连铸机比弧形连铸机,结晶器内夹杂易上浮。
9.连铸机的机型对铸坯内夹杂物的数量和分布有着重要影响。
某钢厂CSP 连铸理论培训教材
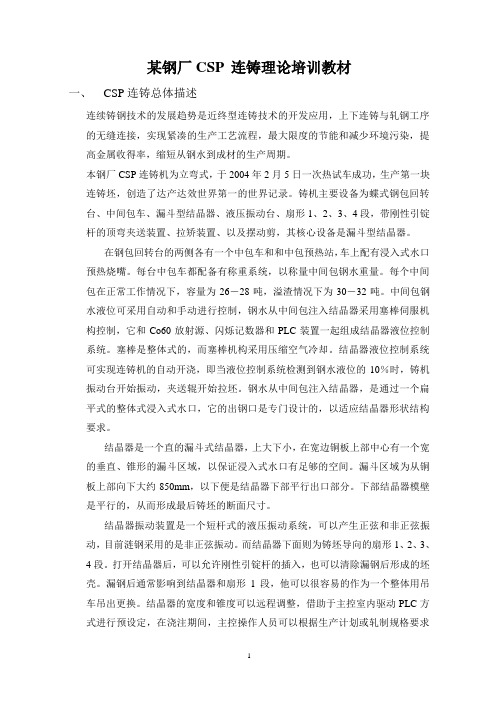
某钢厂CSP 连铸理论培训教材一、CSP连铸总体描述连续铸钢技术的发展趋势是近终型连铸技术的开发应用,上下连铸与轧钢工序的无缝连接,实现紧凑的生产工艺流程,最大限度的节能和减少环境污染,提高金属收得率,缩短从钢水到成材的生产周期。
本钢厂CSP连铸机为立弯式,于2004年2月5日一次热试车成功,生产第一块连铸坯,创造了达产达效世界第一的世界记录。
铸机主要设备为蝶式钢包回转台、中间包车、漏斗型结晶器、液压振动台、扇形1、2、3、4段,带刚性引锭杆的顶弯夹送装置、拉矫装置、以及摆动剪,其核心设备是漏斗型结晶器。
在钢包回转台的两侧各有一个中包车和和中包预热站,车上配有浸入式水口预热烧嘴。
每台中包车都配备有称重系统,以称量中间包钢水重量。
每个中间包在正常工作情况下,容量为26-28吨,溢渣情况下为30-32吨。
中间包钢水液位可采用自动和手动进行控制,钢水从中间包注入结晶器采用塞棒伺服机构控制,它和Co60放射源、闪烁记数器和PLC装置一起组成结晶器液位控制系统。
塞棒是整体式的,而塞棒机构采用压缩空气冷却。
结晶器液位控制系统可实现连铸机的自动开浇,即当液位控制系统检测到钢水液位的10%时,铸机振动台开始振动,夹送辊开始拉坯。
钢水从中间包注入结晶器,是通过一个扁平式的整体式浸入式水口,它的出钢口是专门设计的,以适应结晶器形状结构要求。
结晶器是一个直的漏斗式结晶器,上大下小,在宽边铜板上部中心有一个宽的垂直、锥形的漏斗区域,以保证浸入式水口有足够的空间。
漏斗区域为从铜板上部向下大约850mm,以下便是结晶器下部平行出口部分。
下部结晶器模壁是平行的,从而形成最后铸坯的断面尺寸。
结晶器振动装置是一个短杆式的液压振动系统,可以产生正弦和非正弦振动,目前涟钢采用的是非正弦振动。
而结晶器下面则为铸坯导向的扇形1、2、3、4段。
打开结晶器后,可以允许刚性引锭杆的插入,也可以清除漏钢后形成的坯壳。
漏钢后通常影响到结晶器和扇形1段,他可以很容易的作为一个整体用吊车吊出更换。
钢的连铸讲义
世界上第一台工业连铸机; 50年代,工业应用时期; 到50年代末,有连铸机30台,产量110t,连铸比0.34% 60年代,稳步发展时期; 到60年代末,有连铸机200余台,产量4000万t. 70年代,迅猛发展时期; 1981年连铸比33.8%. 80年代,完全成熟时期; 1990年连铸比64.1%;
炼钢生产的大炉容量、高浇铸温度和钢本身 比热低,这些在有色金属生产中未曾遇到过。 一项最重要的开拓性工作是如何提高一台连铸 机的浇铸能力,最关键的是浇铸速度。 1913年,瑞典人皮尔逊提出结晶器以可变的频 率和振幅做往复振动的想法。 1933年德国人容汉斯(S.Junghans)真正将 这一想法付诸实施。
宽板坯铸机于1959年建在原苏联的新列别茨克 厂。日本住友和罗西为新日铁光厂提供的世界上 第一台不锈钢宽板坯连铸机在1960年12月投产, 宽度为1050mm。
在整个50年代,连续铸钢技术尽管开始步入工 业生产,但产量很少,1960年的产量仅为115万 吨,连铸比仅为0.34﹪。
1.3.4 60年代弧形铸机引发的一场革命
❖ 连铸产品的均一性好,质量好; ❖ 易于实现机械化和自动化。
表:炼钢-轧钢不同生产流程的轧钢能耗比较
工艺过程
炼铸均初
连钢
加
轧 轧钢燃
钢锭热轧
铸坯
热
制 料消耗
开
清
×109J/t
坯
理
1 模铸钢锭冷装 O O O O 轧制IC-CCR
O
O
O 2.01
2 模铸钢锭开坯 O O O O 后 直 接 轧 制 IC -DR
连铸安全培训教材
连铸安全培训教材一、背景介绍连铸工艺是一种重要的钢铁生产工艺,在现代钢铁企业中得到广泛应用。
然而,由于连铸过程中存在一定的安全风险,为了确保工作人员的安全和生产的顺利进行,连铸安全培训显得尤为重要。
本教材旨在通过详细的安全培训内容,为连铸作业人员提供全面的安全知识和技能,帮助他们提高安全意识,预防事故的发生。
二、连铸作业环境和风险分析1. 连铸作业环境连铸作业环境复杂,涉及高温、高压、有毒、有害等因素,操作人员需要穿戴特定的工作服、手套、安全帽等个人防护设备。
2. 连铸作业风险(1)高温风险:液态钢水温度高,作业人员易烫伤或中暑,需注意保持适宜的室温和通风条件。
(2)机械风险:涉及到铸机设备、辊道、链条等机械部件,操作人员需熟悉相关设备的结构和安全操作规程,避免夹伤和碰撞事故。
(3)化学风险:液态钢水的成分中含有一定的有害物质,例如铅、砷等,作业人员应佩戴防护面罩、手套等个人防护装备,避免直接接触。
(4)高压风险:连铸作业中,液态钢水通过高压喷嘴喷射,操作人员需保持安全的距离,并严格遵守相关操作规程。
三、连铸安全操作规程1. 过程准备(1)检查设备:连铸作业前要对设备进行检查,确保设备运行正常。
(2)个人防护:作业人员需穿戴好个人防护装备,并确保其完好。
(3)作业区域准备:清理作业现场,确保无杂物。
2. 连铸操作流程(1)液态钢水准备:按照工艺要求,浇注适量的钢水到连铸机中。
(2)连铸机设备操作:根据操作规程,启动设备,控制液态钢水的流动。
(3)监控与调整:对连铸过程进行监控,调整液态钢水喷射的角度和压力,确保连铸坯的质量。
(4)连铸结束:停止设备运行,清理作业区域,存储连铸坯。
四、连铸安全事故案例分析本章节将通过分析连铸作业过程中的典型事故案例,总结事故原因和处理方法,以引导作业人员在工作中避免类似事故的发生。
五、连铸安全应急处理连铸作业过程中,可能会出现突发状况,例如火灾、爆炸等。
作业人员需要掌握应急处理知识和技能,迅速采取正确的措施,保障人员的安全。
(太钢不锈钢培训教材)连铸设备分册65页-BD
- 1 -
太钢二钢厂不锈钢培训教材-连铸设备分册
3.4 中间罐车 3.4.1 中间罐车的型式 3.4.2 中间罐车的总体结构 4. 结晶器及其振动机构 4.1 结晶器 4.1.1 结晶器内坯壳的形成 4..2 结晶器的型式和构造 4. 2.1 结晶器振动的目的 4. 2.2 结晶器振动方式 4. 2.3 结晶器振动机构的类型 4.2.4 结晶器振动机构介绍 4.2.5 结晶器振动的运动参数 5. 二冷区铸坯导向装置 5.1 二冷装置的作用与工艺要求 5.2 二次冷却区的传热 5.2.1 二冷区热平衡 5.3 二冷区铸坯导向装置的结构 5.3.1 小方坯连铸机二冷装置 5.3.2 大方坯连铸机二冷装置 5.3.3 板坯连铸机二冷装置 5.3.4 二冷区扇形段更换方法 5.3.5 二冷区支承导向部件结构 6. 拉矫机 6.1 拉矫机的技术要求 6.2 拉矫机的型式与结构 6.3 矫直的基本原理和矫直力的确定 6.4 拉坯力的计算与确定 7. 引锭杆及其存放装置
图 1-1
- 5 -
太钢二钢厂不锈钢培训教材-连铸设备分册
至今已形成完整的机型型谱。通常称为传统连铸机,主要有立 式、立弯式、弧形式和水平连铸机等。在其大发展的同时,广 大连铸工作者为获得更高质量的铸坯,进一步提高连铸机的拉 坯速度,相继开发出多种形式的连铸机,这里称其为新型连铸 机。下面仅对其中几种主要新型机作简要叙述,详见图 1-1。 1.2.1 立式连铸机 如图 1-1(1)所示,其基本特征是:连铸机的各主体设备: 结晶器及其振动装置、二次冷却支承导向装置、拉坯设备及切 割装置等均从上到下配置在同一铅垂生产线,且在浇铸过程中 铸坯没有受到任何强制变形过程。因而具有如下优点: (1)由于钢水铅垂注入结晶器内,四周冷却条件相同,易 于调节控制,因而钢水结晶固易达到最佳状态。且钢水中各种 非金属夹杂物易于上浮,铸坯内夹杂物最少,横断面结晶组织 对称。 (2)连铸机的主体设备结构均简单,且可省去一套矫直装 置。 (3)铸坯在结晶凝因过程中,不受任何机械外力作用。为 获得高质量铸坯创造更有利的条件。 其主要缺点是: (1)铸机机身很高,由此带来一系列问题:钢水的静压大, 极易产生鼓肚变形。机械设备的维护检修很不方便。施工工作 量都很大(不论是向空中还是往地下) ,因而投资较多。 (2)铸坯定尺长度受到限制,发展困难。 随着生产率进一步提高,铸坯尺寸要增大,拉速需加快, 都迫使立式连铸机还要加高,其缺点会更加突出,发展受到严 重限制。
连铸操作课程标准(最终版)
连铸操作课程标准课程名称:连铸操作课程代码:适用专业:冶金技术学时:56 学分:4开课学期:第四学期第一部分前言1、课程性质与地位连铸在钢铁生产企业中有着举足轻重的地位,它前接炼铁-炼钢,后续轧钢,连铸生产的质量和产量直接影响到其它生产环节的正常运行,因此《连铸操作》是冶金技术专业的一门核心学习领域。
学生在学完公共学习领域,《冶金基础化学》、《冶金制图》、《金属学及热处理》等学习领域的基础上,并通过认识实习后学习本课程,为学生进行工学结合实习、顶岗实习及将来的工作奠定基础。
本学习领域主要让学生学会连铸生产的基本理论和主要工艺操作技能,铸坯质量控制方法与常见生产事故处理方法,并对连铸生产的主要工艺设备和机械设备能够正确使用与维护。
同时注重培养学生的社会能力和方法能力。
2、课程的基本理念参照《冶金行业职业技能标准》,与行业、企业的工程技术人员共同研讨,以培养学生连铸生产的岗位能力为目标,以真实的工作任务为载体,按所需的岗位技能设实训项目,配备专业知识,将“教、学、做”三个要素固化到课程内容中,使学生通过本课程的学习,掌握连铸生产主要岗位的操作技能,学到相关的专业知识,了解常见的生产事故、问题及处理方法,以适应职业岗位的任职要求。
3、课程的设计思路(1)针对工作岗位需求选取教学内容,步骤如下:①在专业建设指导委员会指导下,与兼职教师、企业的工程技术人员共同研讨,确定学生在连铸生产区域的就业岗位为大包工、拉钢工、火切工、主控室操作工、精整工等;②分析各个工种的岗位能力要求,找出典型的工作任务,并由典型工作任务确定出连铸工的三个行动领域,即设备维护、生产工艺操作、连铸坯质量控制和生产事故处理四个行动领域,在此基础上确定出认识连铸、连铸操作工艺、连铸坯质量控制、常见事故处理四个工作项目。
③以连铸生产相关设备及连铸生产工艺流程(浇注一个钢种)为载体,以连铸生产工艺操作任务为驱动,对学生进行岗位技能的训练;④分析一个钢种浇铸过程中的操作步骤、所需完成的任务,把完成每项任务所需的操作技能设为实训项目,并配置相关的专业知识、经验案例和设备知识。
- 1、下载文档前请自行甄别文档内容的完整性,平台不提供额外的编辑、内容补充、找答案等附加服务。
- 2、"仅部分预览"的文档,不可在线预览部分如存在完整性等问题,可反馈申请退款(可完整预览的文档不适用该条件!)。
- 3、如文档侵犯您的权益,请联系客服反馈,我们会尽快为您处理(人工客服工作时间:9:00-18:30)。
8. 连铸机8.1 CONCAST——SBQ连铸的领先者Concast 提供的连续铸钢设备比业界中任何别的公司都多。
50多年来,Concast公司通过致力于连续铸钢的钢凝固工艺,向用户提供服务。
今天,采用Conc ast公司的设备已经成为电弧炉、二次冶炼设备和连铸的工业性能基准。
Concast公司致力于炼钢过程的开发,不管这种炼钢过程是使用废钢还是用铁矿石。
我们为长材产品部门的用户专门研究和开发冶炼、精炼和连铸工艺和技术,这是一个本公司竞争者都不能涉足的工作。
8.2 中间罐设计CONCAST中间罐设计有助于清除杂质,保证钢水流量稳定,并能使铸流之间的温度场均匀化。
通过模拟钢水流,可以优化中间罐的大小与形状以及挡板和挡墙的设计。
中间罐设计成能提供足够长的钢水停留时间(平均10分钟),这有助于清除杂质,使杂质有时间漂浮在表面,并被覆盖的粉末所吸收。
设计中间罐时考虑到了挡板、挡墙或紊流抑制剂,以使钢水流动分配最佳化,在钢水到达中间罐水口前消除冲击流产生的紊流。
这种设计有助于对结晶器钢水液面进行更好的控制,并使所有铸流中的钢水入口温度均匀化。
根据钢种、浇注时间和主要操作条件,针对各个工程项目选择分隔墙或紊流抑制剂的设计。
中间罐设计模型8.3 浸没式浇铸技术提供Conc ast 塞棒控制系统,用于浸没式浇铸。
Concast塞棒控制的特点:- 塞棒位置极其精确,控制迅速。
- 电机械系统可靠,维护需求低。
- 铸流启动顺序完成自动化。
使用Conc ast塞棒系统,使得对结晶器内钢水液面控制极佳,这对于有效润滑和实现良好表面质量极其重要。
用耐火材料管子进行浸没式浇铸,将钢水倒进结晶器中。
耐火材料管子能防止钢水流与环境(氧气和氮气)接触,并防止重新氧化造成杂质的形成。
在进行浸没式浇铸时,使用两种类型的耐火材料罩:- 浸没式入口水口(SEN)- 浸没式入口长水口(SES)采用SEN,防止钢流再次氧化的效果更好,因为喷嘴实际上布置做在中间罐的底部。
采用SES,能通过陶瓷密封防止空气渗透进水口和中间罐喷嘴之间的联轴器。
总存在某种再氧化的危险,因为如果SES被移动,则密封可能损坏。
选择这些系统中的哪一个,取决于钢的清洁度要求以及现场操作条件。
筒型结晶器是预装配的可快速移动的装置。
自对中设计以及冷却水入口的自密封接头能保证对准最佳和安全操作。
在更换某一段或开展维护工作时,可以快速更换结晶器组件(在5到10分钟内),这使得停工时间最短,机器利用率和生产率最大化。
水套是一种精确机加工部件,它能保证排热和铸坯外壳增大均匀。
结晶器管支架系统上端使用键形夹,在受热的情况下这些键形夹能沿纵轴自由膨胀。
筒式结晶器设计能容纳用于浇铸断面范围内的共用结晶器电磁搅拌器。
在更换断面期间,无需拆除或重新安装电磁搅拌器。
这样就降低了设备损坏的危险,并排除了污物进入水系统的危险。
8.4.1 CONVEX结晶器管CONCAST已经开发了一种称为CONVEX的高速连铸技术,并申请了这种技术的专利。
1991年在德国的THYSSEN OBERHAUSEN对此技术进行了第一次试运转,从此以后此技术实现了工业化操作。
之后CONVEX技术被应用于世界各地的许多装置上,用于生产特种型材(SBQ)产品。
现在有几家制钢厂(包括德国的SAARSTAHL,意大利的LUCCHINI Group和瑞士的VON MOOS)完全采用CONVEX技术,铸造汽车工业中使用的SBQ等级的钢坯。
所有这些工厂都采用了非调质工艺,在轧制之前无需对钢坯进行检验或磨光。
CONVEX技术设计能够满足以下要求:- 改善传热- 在结晶器周围及沿着结晶器均匀分配热传递。
与其他结晶器设计技术相比,这种技术热效率高,使得其浇注速度显著提高,可靠性和钢坯质量也有所改善。
钢水在老式的方形结晶器中凝固时,会导致不均匀冷却以及拐角处形成气隙,而CONVEX 结晶器能通过逐渐改变交叉形状(crossshape),补偿拐角处的收缩。
这样,沿着钢坯周长和沿着结晶器铜管全部长度方向能始终保持均匀接触。
这种效果的一个概念示例见下图。
(图)Conventional technology: 常规技术Convex technology: Convex 技术其结果凝固壳厚度均匀,从而降低了形状缺陷和产生裂纹的可能性。
根据浇铸的钢种,优化结晶器的几何形状(长度,锥度,CONVEX 形状和转角半径)。
Concast 积累了用于各种SBQ 钢(包括不锈钢)的CONVEX 结晶器铜的设计方面的广泛经验。
8.5 结晶器钢水液面控制结晶器钢水液面控制系统的功能是测量结晶器上部中的实际钢液面,并将此数据传送至塞棒的控制PLC ,最终在技术许可的范围内,使结晶器内的钢液面保持不变和稳定,从而保证浇铸产品的表面质量。
(图) Measuring Range 测量范围 Source 来源Mould 结晶器Det ector 检测器Signal processing unit 信号处理装置to level cont rolling PLC 去液面控制PL C在一个以铅为保护衬里的钢罩中安装放射源Co60。
此放射源以稳定速率放射出γ粒子,γ放射出的粒子穿过保护罩中的一个窄缝以及结晶器,射向安装在结晶器另一侧的检测器。
检测器接收的与γ粒子数成比例的信号通过屏蔽电缆送到液面控制处理器。
常规技术 Convex 技术 测量范围放射源 结晶器 检测器 信号处 理装置 到液面控制PLC放射源本身的辐射强度极低,可以不考虑。
这种辐射测量的传感器装置用于所有操作活动(自动启动、防止溢流和破裂,检测等),是一种相当的可靠系统,安装于结晶器区域内部和耐火材料覆盖层以下位置。
世界范围内大多数连铸机都使用这种系统。
8.6 底辊(FOOT ROLLERS)结晶器上安装了底辊,以防止钢坯鼓出,并使铸流保持在中心位置。
这种配置改善了结晶器的性能以及结晶器铜管和外壳之间的均匀接触,降低了结晶器铜管的磨损。
建议在底辊之后另设一个支撑铸流的支撑段。
此支撑段在第2段的下面,精确地调整至底辊处。
8.7 振荡器8.7.1 液压结晶器振荡结晶器振荡有许多特征。
它用于防止铸流粘结晶器,并保证良好传热。
另外,它也被用于防止或处理固态外壳的开裂。
要满足达到所有这些功能的要求,同时要保证形成的振荡划痕浅,并且无缺陷。
液压振荡与标准电动机械振荡相比有某些优势。
采用液压振荡,可以在连铸期间改变振荡行程的长度和振荡曲线形状。
这就提高了振荡系统的灵活性,并可以根据钢种对振荡参数进行连续优化。
利用液压振荡时可以使用非正弦振荡曲线。
使用非正弦振荡曲线,是为了延长铸流的恢复时间,或在钢坯撕裂阶段减少结晶器向上拉。
标准正弦振荡曲线和非正弦曲线的示例见下图。
(图)Hydraulic osc illation single sinus c urve si mulation w ith:液压振荡单下凹曲线模拟 Graph w idth is 1 sec. 图形宽度为1秒 Standard Sinusoidal Osc illation Curve 标准正弦振荡曲线Nonsinusoidal Osc illation Curve 非正弦振荡曲线8.7.2 可伸缩振荡 当某一个支撑段需要布置在结晶器下时,使用可伸缩振荡台迅速地更换筒式结晶器断面。
液压振荡单正弦曲线模拟:图形宽度为1秒标准正弦振荡曲线 液压振荡单正弦曲线模拟:图形宽度为1秒非正弦振荡曲线用可伸缩振荡器在连铸机顶部进行的、旨在更换所有规格的操作:- 缩回振荡器(见下图)——此时高架起重机可以直接接近支撑段。
- 提起支撑段,并更换之。
- 对于新断面,更换新筒。
- 将振荡器移动至连铸位置。
在提升时,结晶器外罩和结晶器搅拌器都无需拆开。
所有辅助系统(冷却水,电)都保持连接。
采用常用的振荡装置(不可伸缩)时,包括搅拌器在内的结晶器外罩必须拆除,以接近支撑段。
在这种情况下,要从振荡台上拆除这一部分(见下图中最右的铸流)。
由于要求的起重机移动和电气连接/切断次数增多,操作时间明显延长。
8.8 电磁搅拌采用电磁搅拌,以改进铸流质量。
采用能使钢水旋转的旋转电磁场,以实现上述目的。
8.8.1 结晶器电磁搅拌器采用结晶器搅拌器(M-EMS),对各种SBQ钢和普通钢都有好处。
用塞棒和浸没式入口长水口/浸没式入口水口来浇铸SBQ钢,使用结晶器搅拌器的金相效果包括:- 液面以下非金属杂质减少。
- 碳偏析和孔隙度降低。
- 等轴区域增大。
对于敞口式浇铸,采用结晶器电磁搅拌器的好处为:- 液面以下非金属杂质减少。
- 形成的表面针孔减少。
- 等轴区域增大。
(图)Equiaxed zone 等轴区Equiazed zone w idth 等轴区宽度 Tundish superheat 中间罐过热(图)采用浸没浇铸时,电磁搅拌器必须位于结晶器的中下部,以防止夹带结晶器粉末,以及浸没式入口水口/浸没式入口长水口因搅拌作用而受到侵蚀。
可以很方便地在对面将搅拌器靠近弯月面作敞口式浇铸。
这样钢坯表面就能收到最明显的效果。
Concast 筒式结晶器的设计,对于这两种相反的必要条件,都提供了成本少、效益高的解决方案。
结晶器电磁搅拌器很容易从浇注平台快速地从低位移至高位。
8.8.2 末端电磁搅拌器结晶器电磁搅拌器造成的碳偏析的减少不足以满足高碳钢应用的最为严格的要求。
当生产计划中有这种要求的钢时,建议在连铸机中采用一个末端搅拌器(F-EMS ),对结晶器电磁搅拌器的作用进行补充。
末端电磁搅拌器只能用于以下SBQ 级钢:- 用于生产线材,如PC 线和轮胎线(tyre c ord )(中心偏析减少)的高碳钢。
- 轴承钢(中心偏析减少)- 高合金含量的中碳钢(中心质量改善)高碳钢线材(方坯连铸生产路径)的大多数合格生产商的经验证明,末端电磁搅拌器配合硬冷却,可以进一步减少中心偏析。
以下两图显示了采用不同技术所能达到的偏析控制的范围。
以下图表显示了在钢坯上测量的偏析指数S.I.=C/C0(参考:Convex 连铸机,钢坯),用等轴区 等轴区宽度 中间罐过热连铸技术对偏析指数的影响(图) Effect of Casting Technology on Segregation Index 连铸技术对析出指数的影响 segregation index C/C0 析出指数C/C0(图)以下图表表示用连铸坯(参考:Convex 连铸机)轧制的高碳钢线材(直径11mm )的平均偏析程度。
显示的指数是AFNOR 标准NFA 04-114规定的线材额定值,水平轴显示渗碳铁网络的额定值(A=无,B=痕量),垂直轴显示中心偏析点强度(2=辉度对比偏析)。
(图)Hard cooling 硬冷却 MEMS and hard c ooling MEMS 和硬冷却 M+F EMS and hard cooling M+F EMS 和硬冷却8.9 二次冷却在结晶器除去铸流的热量大约为20%。