在切削过程中建模与仿真刀具的磨损
CNC机床加工中的切削刃角优化与磨损
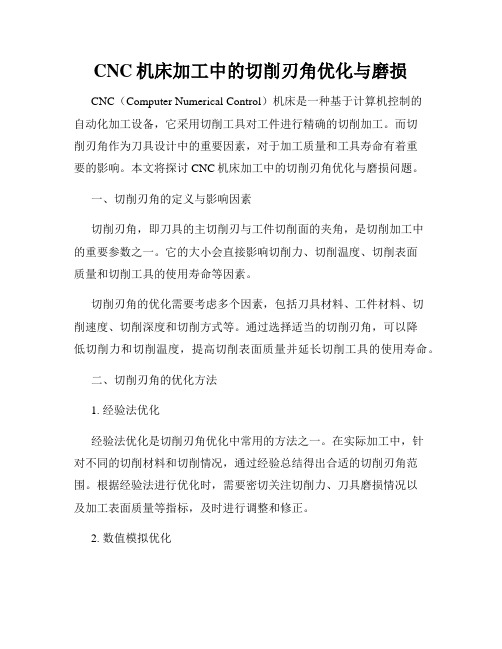
CNC机床加工中的切削刃角优化与磨损CNC(Computer Numerical Control)机床是一种基于计算机控制的自动化加工设备,它采用切削工具对工件进行精确的切削加工。
而切削刃角作为刀具设计中的重要因素,对于加工质量和工具寿命有着重要的影响。
本文将探讨CNC机床加工中的切削刃角优化与磨损问题。
一、切削刃角的定义与影响因素切削刃角,即刀具的主切削刃与工件切削面的夹角,是切削加工中的重要参数之一。
它的大小会直接影响切削力、切削温度、切削表面质量和切削工具的使用寿命等因素。
切削刃角的优化需要考虑多个因素,包括刀具材料、工件材料、切削速度、切削深度和切削方式等。
通过选择适当的切削刃角,可以降低切削力和切削温度,提高切削表面质量并延长切削工具的使用寿命。
二、切削刃角的优化方法1. 经验法优化经验法优化是切削刃角优化中常用的方法之一。
在实际加工中,针对不同的切削材料和切削情况,通过经验总结得出合适的切削刃角范围。
根据经验法进行优化时,需要密切关注切削力、刀具磨损情况以及加工表面质量等指标,及时进行调整和修正。
2. 数值模拟优化数值模拟方法是近年来逐渐应用于切削刃角优化的一种方法。
通过建立切削过程的数学模型,结合计算机仿真技术,可以对不同切削刃角的影响进行模拟分析。
通过模拟分析的结果,可以找到在给定切削条件下最优的切削刃角。
3. 实验优化实验优化方法是基于实际试验数据进行分析和优化的方法。
通过在实际加工中采集切削力、刀具磨损情况和表面质量等数据,并进行统计和分析,可以得到不同切削刃角下的性能指标。
根据实验结果,选择性能指标最优的切削刃角。
三、切削刃角的磨损与修复切削刃角的磨损是切削加工中不可避免的问题之一,它会导致切削力增加、切削温度升高,同时降低切削表面质量和刀具的使用寿命。
为解决这一问题,可以采取以下措施进行切削刃角的修复:1. 刀具重研磨当刀具的切削刃角磨损到一定程度时,可以将刀具进行研磨修复。
数控加工中的刀具磨损与寿命预测
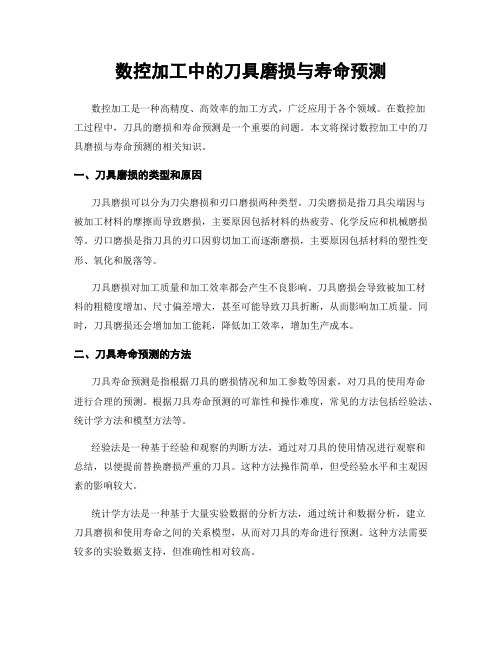
数控加工中的刀具磨损与寿命预测数控加工是一种高精度、高效率的加工方式,广泛应用于各个领域。
在数控加工过程中,刀具的磨损和寿命预测是一个重要的问题。
本文将探讨数控加工中的刀具磨损与寿命预测的相关知识。
一、刀具磨损的类型和原因刀具磨损可以分为刀尖磨损和刃口磨损两种类型。
刀尖磨损是指刀具尖端因与被加工材料的摩擦而导致磨损,主要原因包括材料的热疲劳、化学反应和机械磨损等。
刃口磨损是指刀具的刃口因剪切加工而逐渐磨损,主要原因包括材料的塑性变形、氧化和脱落等。
刀具磨损对加工质量和加工效率都会产生不良影响。
刀具磨损会导致被加工材料的粗糙度增加、尺寸偏差增大,甚至可能导致刀具折断,从而影响加工质量。
同时,刀具磨损还会增加加工能耗,降低加工效率,增加生产成本。
二、刀具寿命预测的方法刀具寿命预测是指根据刀具的磨损情况和加工参数等因素,对刀具的使用寿命进行合理的预测。
根据刀具寿命预测的可靠性和操作难度,常见的方法包括经验法、统计学方法和模型方法等。
经验法是一种基于经验和观察的判断方法,通过对刀具的使用情况进行观察和总结,以便提前替换磨损严重的刀具。
这种方法操作简单,但受经验水平和主观因素的影响较大。
统计学方法是一种基于大量实验数据的分析方法,通过统计和数据分析,建立刀具磨损和使用寿命之间的关系模型,从而对刀具的寿命进行预测。
这种方法需要较多的实验数据支持,但准确性相对较高。
模型方法是一种基于理论模型和计算机仿真的方法,通过对切削力、摩擦力等因素进行建模和模拟,预测刀具磨损和寿命。
这种方法需要较高的专业知识和计算机辅助工具,但预测结果较为准确。
三、刀具磨损与寿命预测的优化策略为了提高刀具的使用寿命,延长刀具更换周期,可以采取一些优化策略。
首先,选择合适的刀具材料和涂层技术。
刀具材料的选择应根据被加工材料的性质和加工工艺的要求,具有较高的硬度、耐磨性和热稳定性。
涂层技术可以有效减少刀尖的磨损,提高刀具的寿命。
其次,合理选择和设计加工参数。
切削过程刀具磨损状态决策模型构建

切削过程刀具磨损状态决策模型构建下载提示:该文档是本店铺精心编制而成的,希望大家下载后,能够帮助大家解决实际问题。
文档下载后可定制修改,请根据实际需要进行调整和使用,谢谢!本店铺为大家提供各种类型的实用资料,如教育随笔、日记赏析、句子摘抄、古诗大全、经典美文、话题作文、工作总结、词语解析、文案摘录、其他资料等等,想了解不同资料格式和写法,敬请关注!Download tips: This document is carefully compiled by this editor. I hope that after you download it, it can help you solve practical problems. The document can be customized and modified after downloading, please adjust and use it according to actual needs, thank you! In addition, this shop provides you with various types of practical materials, such as educational essays, diary appreciation, sentence excerpts, ancient poems, classic articles, topic composition, work summary, word parsing, copy excerpts, other materials and so on, want to know different data formats and writing methods, please pay attention!随着传统制造业的发展,切削加工技术在各个领域得到了广泛的应用。
三维金属切削过程刀具磨损的有限元模拟仿真
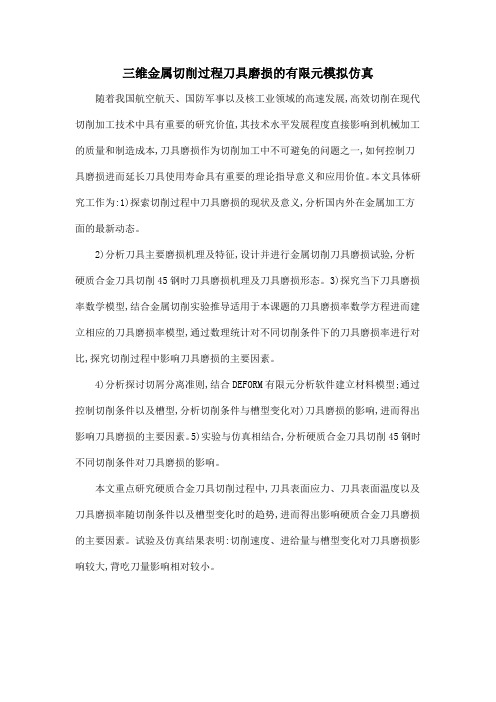
三维金属切削过程刀具磨损的有限元模拟仿真随着我国航空航天、国防军事以及核工业领域的高速发展,高效切削在现代切削加工技术中具有重要的研究价值,其技术水平发展程度直接影响到机械加工的质量和制造成本,刀具磨损作为切削加工中不可避免的问题之一,如何控制刀具磨损进而延长刀具使用寿命具有重要的理论指导意义和应用价值。
本文具体研究工作为:1)探索切削过程中刀具磨损的现状及意义,分析国内外在金属加工方面的最新动态。
2)分析刀具主要磨损机理及特征,设计并进行金属切削刀具磨损试验,分析硬质合金刀具切削45钢时刀具磨损机理及刀具磨损形态。
3)探究当下刀具磨损率数学模型,结合金属切削实验推导适用于本课题的刀具磨损率数学方程进而建立相应的刀具磨损率模型,通过数理统计对不同切削条件下的刀具磨损率进行对比,探究切削过程中影响刀具磨损的主要因素。
4)分析探讨切屑分离准则,结合DEFORM有限元分析软件建立材料模型;通过控制切削条件以及槽型,分析切削条件与槽型变化对)刀具磨损的影响,进而得出影响刀具磨损的主要因素。
5)实验与仿真相结合,分析硬质合金刀具切削45钢时不同切削条件对刀具磨损的影响。
本文重点研究硬质合金刀具切削过程中,刀具表面应力、刀具表面温度以及刀具磨损率随切削条件以及槽型变化时的趋势,进而得出影响硬质合金刀具磨损的主要因素。
试验及仿真结果表明:切削速度、进给量与槽型变化对刀具磨损影响较大,背吃刀量影响相对较小。
基于金属切削原理的刀具磨损机理及预测模型
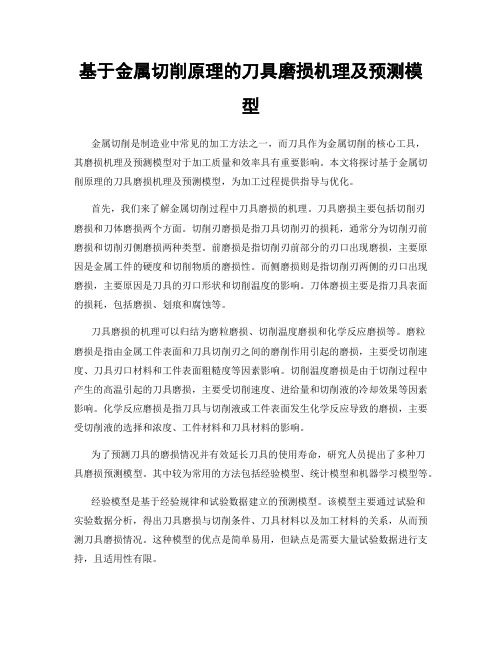
基于金属切削原理的刀具磨损机理及预测模型金属切削是制造业中常见的加工方法之一,而刀具作为金属切削的核心工具,其磨损机理及预测模型对于加工质量和效率具有重要影响。
本文将探讨基于金属切削原理的刀具磨损机理及预测模型,为加工过程提供指导与优化。
首先,我们来了解金属切削过程中刀具磨损的机理。
刀具磨损主要包括切削刃磨损和刀体磨损两个方面。
切削刃磨损是指刀具切削刃的损耗,通常分为切削刃前磨损和切削刃侧磨损两种类型。
前磨损是指切削刃前部分的刃口出现磨损,主要原因是金属工件的硬度和切削物质的磨损性。
而侧磨损则是指切削刃两侧的刃口出现磨损,主要原因是刀具的刃口形状和切削温度的影响。
刀体磨损主要是指刀具表面的损耗,包括磨损、划痕和腐蚀等。
刀具磨损的机理可以归结为磨粒磨损、切削温度磨损和化学反应磨损等。
磨粒磨损是指由金属工件表面和刀具切削刃之间的磨削作用引起的磨损,主要受切削速度、刀具刃口材料和工件表面粗糙度等因素影响。
切削温度磨损是由于切削过程中产生的高温引起的刀具磨损,主要受切削速度、进给量和切削液的冷却效果等因素影响。
化学反应磨损是指刀具与切削液或工件表面发生化学反应导致的磨损,主要受切削液的选择和浓度、工件材料和刀具材料的影响。
为了预测刀具的磨损情况并有效延长刀具的使用寿命,研究人员提出了多种刀具磨损预测模型。
其中较为常用的方法包括经验模型、统计模型和机器学习模型等。
经验模型是基于经验规律和试验数据建立的预测模型。
该模型主要通过试验和实验数据分析,得出刀具磨损与切削条件、刀具材料以及加工材料的关系,从而预测刀具磨损情况。
这种模型的优点是简单易用,但缺点是需要大量试验数据进行支持,且适用性有限。
统计模型是基于统计方法建立的预测模型。
该模型主要通过统计分析历史数据,得出刀具磨损与切削参数的关系,从而预测刀具磨损情况。
这种模型的优点是能够在一定范围内预测刀具磨损,但缺点是对于新的切削条件和材料可能预测误差较大。
机器学习模型是基于机器学习算法建立的预测模型。
金属难加工材料切削及刀具磨损虚拟仿真报告(一)
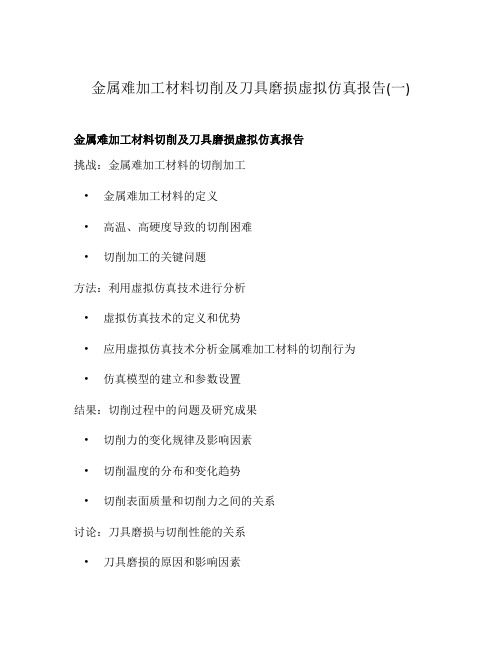
金属难加工材料切削及刀具磨损虚拟仿真报告(一)金属难加工材料切削及刀具磨损虚拟仿真报告挑战:金属难加工材料的切削加工•金属难加工材料的定义•高温、高硬度导致的切削困难•切削加工的关键问题方法:利用虚拟仿真技术进行分析•虚拟仿真技术的定义和优势•应用虚拟仿真技术分析金属难加工材料的切削行为•仿真模型的建立和参数设置结果:切削过程中的问题及研究成果•切削力的变化规律及影响因素•切削温度的分布和变化趋势•切削表面质量和切削力之间的关系讨论:刀具磨损与切削性能的关系•刀具磨损的原因和影响因素•切削力和刀具磨损的关系•如何通过优化切削参数延缓刀具磨损总结:虚拟仿真技术在切削加工中的应用前景•虚拟仿真技术的优势和局限性•未来发展方向和研究重点•为实际切削加工提供参考和决策依据金属难加工材料切削及刀具磨损虚拟仿真报告挑战:金属难加工材料的切削加工•金属难加工材料的定义–金属难加工材料是指具有高硬度、高强度和高耐磨性的金属材料,如钛合金、高速钢等。
•高温、高硬度导致的切削困难–由于金属难加工材料的硬度较高,切削时需要更大的切削力。
–高温会导致材料软化和脆性增加,使刀具损耗加剧。
•切削加工的关键问题–如何降低切削力和温度,提高切削效率和加工质量。
方法:利用虚拟仿真技术进行分析•虚拟仿真技术的定义和优势–虚拟仿真技术利用计算机模拟真实物理过程,可以减少实验成本、提高研究效率。
–通过虚拟仿真可以提前预测切削加工过程中的各种参数和结果。
•应用虚拟仿真技术分析金属难加工材料的切削行为–通过建立切削仿真模型,可以模拟金属难加工材料在切削过程中的变形、热力分布等行为。
–利用仿真结果可以分析切削力、切削温度和切削表面质量等参数的变化趋势。
•仿真模型的建立和参数设置–建立金属难加工材料的切削仿真模型。
–设置切削参数,如切削速度、进给速度和切削用量。
–调整模型和参数以获得准确的仿真结果。
结果:切削过程中的问题及研究成果•切削力的变化规律及影响因素–切削力随着切削速度的增加而增加,随着进给速度的增加先增加后减小。
磨损问题的仿真求解研究
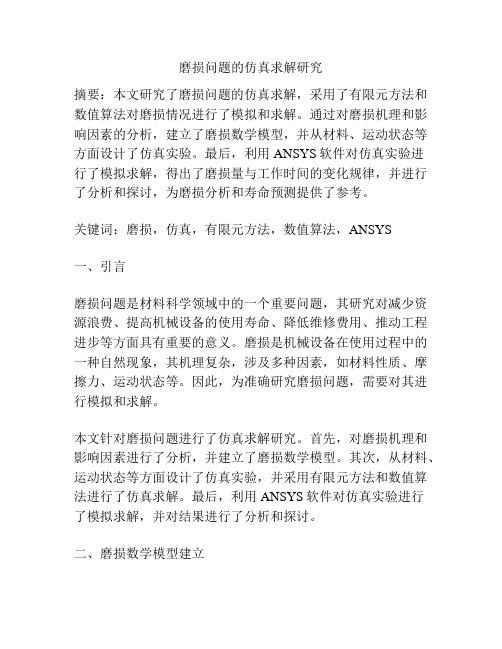
磨损问题的仿真求解研究摘要:本文研究了磨损问题的仿真求解,采用了有限元方法和数值算法对磨损情况进行了模拟和求解。
通过对磨损机理和影响因素的分析,建立了磨损数学模型,并从材料、运动状态等方面设计了仿真实验。
最后,利用ANSYS软件对仿真实验进行了模拟求解,得出了磨损量与工作时间的变化规律,并进行了分析和探讨,为磨损分析和寿命预测提供了参考。
关键词:磨损,仿真,有限元方法,数值算法,ANSYS一、引言磨损问题是材料科学领域中的一个重要问题,其研究对减少资源浪费、提高机械设备的使用寿命、降低维修费用、推动工程进步等方面具有重要的意义。
磨损是机械设备在使用过程中的一种自然现象,其机理复杂,涉及多种因素,如材料性质、摩擦力、运动状态等。
因此,为准确研究磨损问题,需要对其进行模拟和求解。
本文针对磨损问题进行了仿真求解研究。
首先,对磨损机理和影响因素进行了分析,并建立了磨损数学模型。
其次,从材料、运动状态等方面设计了仿真实验,并采用有限元方法和数值算法进行了仿真求解。
最后,利用ANSYS软件对仿真实验进行了模拟求解,并对结果进行了分析和探讨。
二、磨损数学模型建立磨损数学模型是研究磨损问题的重要基础。
在建立磨损数学模型时,需要考虑材料性质、运动状态、受力情况等多种因素。
本文基于磨损机理和影响因素的分析,建立了如下的磨损数学模型:$$W = kHd$$其中,$W$表示磨损量,$H$表示受力情况,$d$表示工作时间,$k$为比例系数。
该数学模型考虑了磨损与受力情况、工作时间、材料性质等因素的关系。
其中,受力情况是决定磨损量的重要因素,其受力情况的大小和方向都会对磨损量产生影响。
三、仿真实验设计为了验证磨损数学模型的有效性,本文利用有限元方法和数值算法对磨损情况进行了模拟和求解。
具体的仿真实验设计如下:1. 材料选择:本文选择了工程塑料作为材料,其具有良好的韧性和抗磨损性能。
2. 运动状态:本文采用了滑动摩擦运动状态,其运动状态为水平滑动,速度恒定,摩擦力为定值。
solidworks刃边切入力仿真
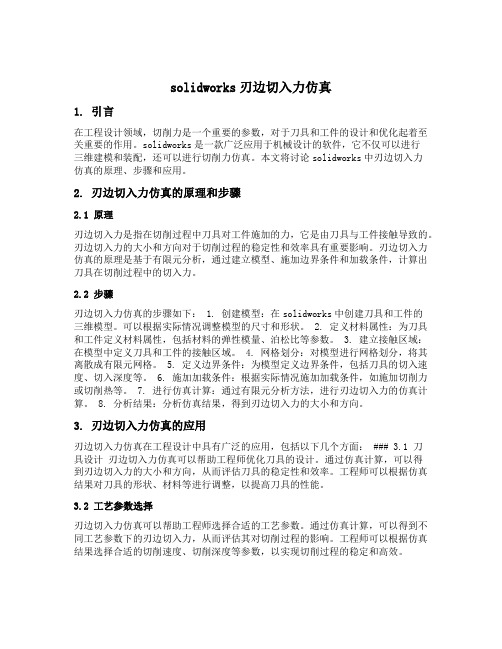
solidworks刃边切入力仿真1. 引言在工程设计领域,切削力是一个重要的参数,对于刀具和工件的设计和优化起着至关重要的作用。
solidworks是一款广泛应用于机械设计的软件,它不仅可以进行三维建模和装配,还可以进行切削力仿真。
本文将讨论solidworks中刃边切入力仿真的原理、步骤和应用。
2. 刃边切入力仿真的原理和步骤2.1 原理刃边切入力是指在切削过程中刀具对工件施加的力,它是由刀具与工件接触导致的。
刃边切入力的大小和方向对于切削过程的稳定性和效率具有重要影响。
刃边切入力仿真的原理是基于有限元分析,通过建立模型、施加边界条件和加载条件,计算出刀具在切削过程中的切入力。
2.2 步骤刃边切入力仿真的步骤如下: 1. 创建模型:在solidworks中创建刀具和工件的三维模型。
可以根据实际情况调整模型的尺寸和形状。
2. 定义材料属性:为刀具和工件定义材料属性,包括材料的弹性模量、泊松比等参数。
3. 建立接触区域:在模型中定义刀具和工件的接触区域。
4. 网格划分:对模型进行网格划分,将其离散成有限元网格。
5. 定义边界条件:为模型定义边界条件,包括刀具的切入速度、切入深度等。
6. 施加加载条件:根据实际情况施加加载条件,如施加切削力或切削热等。
7. 进行仿真计算:通过有限元分析方法,进行刃边切入力的仿真计算。
8. 分析结果:分析仿真结果,得到刃边切入力的大小和方向。
3. 刃边切入力仿真的应用刃边切入力仿真在工程设计中具有广泛的应用,包括以下几个方面: ### 3.1 刀具设计刃边切入力仿真可以帮助工程师优化刀具的设计。
通过仿真计算,可以得到刃边切入力的大小和方向,从而评估刀具的稳定性和效率。
工程师可以根据仿真结果对刀具的形状、材料等进行调整,以提高刀具的性能。
3.2 工艺参数选择刃边切入力仿真可以帮助工程师选择合适的工艺参数。
通过仿真计算,可以得到不同工艺参数下的刃边切入力,从而评估其对切削过程的影响。
- 1、下载文档前请自行甄别文档内容的完整性,平台不提供额外的编辑、内容补充、找答案等附加服务。
- 2、"仅部分预览"的文档,不可在线预览部分如存在完整性等问题,可反馈申请退款(可完整预览的文档不适用该条件!)。
- 3、如文档侵犯您的权益,请联系客服反馈,我们会尽快为您处理(人工客服工作时间:9:00-18:30)。
在切割过程中建模与仿真刀具的磨损摘要对于研究了不同刀具的磨损类型实验和分析方法仍然是主要方式。
数值方法和模拟的快速进步,联系到越来越强大的计算机的存在可能会使用有限元法研究刀具磨损。
这项工作的主要目的是提出一种新的方法来预测在切割过程中刀具磨损的操作。
特别是,能源的消耗,连接刀具磨损量与摩擦消耗所使用的能量。
另外,在诱导切削残余应力和由于磨损的机理使工具几何形状变化之间的相互作用做调查。
为了进行这项研究中,它被提交到刀具磨损的测量实验中,特别是在失量切割中。
正交切削操作使用商用有限元软件ABAQUS/ Explicit的数值模拟。
©2013的作者。
由Elsevier B.V. 发布。
根据第14届CIRP大会上的国际科学委员会负责选择和同行审查在会议的人的加工操作。
关键词:刀具磨损;数值模拟;切割;切屑形成;1.介绍、刀具磨损在加工操作中对经济有很大的影响同时也影响表面加工完整性。
事实上,刀具磨损影响刀具寿命和最终产物中的残余应力的质量。
对于这些raisons对刀具的磨损很多调查都能在文献[1-2-3]中找到。
刀具在正交切削下的磨损模拟的开发要么是验证磨损的机理。
要么是在这些模拟中,研究人员往往会更好地理解刀具磨损的残余应力对最终产物的影响[4]。
在一些研究[5-6]的在一个子程序实现刀具磨损模型,是相对的像磨损和扩散特定的磨损机理磨损。
因此,在本次调查中,具体机制被认为在很大程度上影响了磨损现象。
事实上,刀具的磨损受几个不同类材料的附着力、侵蚀、腐蚀、磨料和断裂。
在切割过程中,刀具几何形状的改变受刀具磨损的影响。
此更新的刀具几何形状主要是参照,在数值仿真,通过该工具面节点的运动[7]。
这个方法是使用一个特定的子程序的评估切削变量,如温度,正常压力,并且在正交切削模拟中每个节点工具滑动的距离。
在这之后,其他子程序启动征收节点的运动。
现有磨损模型可分为两个类型:第一种是切削参数、刀具寿命型,这样的泰勒公式,第二个是切割过程中的变量通常是基于一个或若干磨损机制[8]。
这个模型无力的,因为,一方面,磨损现象被建模为不连续的现象的时间而不是真实的情况。
在另一方面,它是在实施的的限制磨损机理,即磨损问题降低到1或2的磨损机制。
磨损接触的现象说明了通过形成之间的关系微动系统碎片和摩擦中消耗的能量。
这个耗能是更加可控制在接触区中使用量方面[9]。
这种方法是实验性的,一个摩擦磨损试验机,用于量化接触力的值,然后将能量耗散因摩擦以及与它链接遗失的能量耗散在这个区域[10]。
由于这些原因,本文提出了一种新的的方法,它提供了不仅是一个全球性的建模磨损现象,而且还是两个组合方面,正交的切割的配置中工具的磨损和在最终产物中的残余应力的影响。
为了带领这项研究中,提出的方法有三个不同的部分。
在第一部分中,一个工磨损由测量呈现。
此后,能量办法提出修改后用于在应用程序中正交切削。
一种数值模拟正交切割操作正在开发,使用了商用的有限元软件ABAQUS/ Explicit。
最后一部分,包括刀具磨损演变的数值结果在仿真和结论。
2.实验测试在实验测试中,进行验证有限元模型,并测量渐进刀具磨损,包括转制成42CD4与操作盘为70毫米的最初直径。
所使用的工具是未涂覆的用碳化钨(WC)作为TPKN1603参考PPR。
(图1)。
图一实验配置磨损测量完成使用显微镜和有列于表1,根据图2Vc是切割速度,f为进给量。
图2刀具几何形状测量位置3.数值模型3.1建模工具用于切削工具的材料是钨碳化物。
这种选择是由在实验测试中刀具的类型所影响。
因此,要比较经验和那些由数值模拟的问题的结果,需要使用同一类型的材料。
关于用于材料流动模型的方法是选择使用曲线约束塑性应变的功能。
因此,具有弹性塑料的工具建模材料的性能如图2[11]所示。
在能计算实施的损伤模型研究的软件ABAQUS/ Explicit中进行约翰逊和库克的[12-13]模型建模刀具的损伤。
所用的参数列于下表3[9]。
切削工具被定义为可变形、易损的。
切割速度是相当于施加一个刚性体。
这个想法来自于一个事实,即我们必须避免施加在可变形的速度或位移体上。
因此,要避免一切纯粹的数字问题,我们选择使用一个刚性体支撑可变形的刀具。
这两者之间的连接是功能领带。
该刀具具有10°的切削刃半径,以及一个侧翼11°的角。
几何建模是用在实验测试中对切削的插入。
因为接触问题,它确保了工具切削的部分刃口半径是无损伤(D 区)如图3所示。
此解决方案是重要的的,以保持接触在分离区和所有节点的外之间在D 区的表面上。
刀区域D刚性支撑图3几何形状和刀具网断裂能的Emax (在ABAQUS 中)开始实施是为了在相当低的正交切削中找到一个快速的刀具磨损,持续一个数值模拟几毫秒。
3.2工件建模在非常高的应变、应变率和温度的金属切割过程中,对材料的流动有很大影响。
为了得到更好的切屑形成分析结果,它结合了所有这些方面的材料模型必要的。
在该模拟中,它被选择了约翰逊和库克的行为和本构关系[14-15-16]。
3.3接触问题面临的最重要的问题正交切削数值模式中考虑到刀具的磨损是接触管理的发展。
目前,经典模拟和它生长在的情况下接触是动态的这方面是非常敏感的,即两组节点之间,分别为节点工件和刀具的节点。
需要注意的是在ABAQUS 软件中,如何数值模型是开发的,不能处理之间的接触区域两个节点。
因此,它仅仅允许一个表面之间的接触和一组节点。
商业软件是有限的在2D 方面的联系人管理方面建模。
如图4所示。
工作表面节点刀具节点刀具表面节点图4接触问题该解决方案可以管理所有将生成的接刀具与切屑的内表面的节点。
这种方法是可能通过利用正交切削与分离模型的行定义的字段和分离,三个地方选择芯片的内表面上的能力。
如图5所示。
内表面切屑图5刀具和切屑之间的接触问题在刀具/切屑与刀具/工作接触和摩擦决定了切削功率和刀具磨损。
在这种提出了一种库仑摩擦模型被用于以恒定的0.2的摩擦系数。
4.数值模拟4.1仿真持续几秒钟的发展正交切削最后的数值模拟大多数情况下几毫秒。
这些模拟大大减少模拟时间方面有相当大的计算时间可能需要几天的时间。
所以,关于数值模拟,其中仿真时间是为了一分钟后,预期一个相当高的计算时间可能达到几个星期。
计算时间可达到几个星期。
为了开发一个数值模拟这需要几秒钟,我们必须找到减少计算时间的解决方案。
在下面,我们介绍了发达国家提供创新的解决方案来解决这个问题的模式。
在数值模拟计算时间主要需要计算之间划分的在材料内的变形和需要管理该联系人。
这取决于这个时间是可变的配方中使用。
它是已知的计算时间甚至不太重要的在下面的顺序配方,拉格朗日,欧拉和ALE。
由于接触约束的开始可以得出结论,的拉格朗日选择配方已经完成,我们不能改变它。
这要追溯到二次调查的途径是负责增加计算相对的接触管理。
因此可以推断,接触的时间更重要而不是在接触节点的数目。
下面的图,(图6),显示的情况下相对长的数值模拟50毫米,计算时间在接触节点的增加是越来越重要。
这些节点相关的切屑。
在某些情况下,有过多的扭曲,创造一个停止计算。
扭曲的网格是位于切屑。
这是由于弯曲的切屑本身。
切屑加工表面图6。
由接触引起的节点的计算时间增加现在是集中在所造成的问题是在模拟的发展中逐步产生切屑。
的解决方案是在从事实上切屑产生用于管理大量的计算时间接触的节点。
此解决方案还依赖于这一事实,切屑是一种浪费,即使它允许我们对有丰富的关于行为的信息剪切的操作。
因此,选择了消除该切屑。
因此,它不会引起在仿真中落实到计算时间管理芯片本身和原料之间的联系表面的难题。
下面的图7给出了模型使用不连续的切屑的形成,经过一段时间后切屑弹出从切削区域的时间,在切削面积的弹射节省的时间,可以大幅度减少接触表面,然后由此所得的方程。
当前部分的切屑切屑间隔工作图7减少计算时间的解决方案,e=80μm切削移动图8 从切削面积中消切屑4.2磨损数值模拟开发的模型,提供了第一个相当满意结果。
结果表明,月牙洼磨损逐渐发展为模拟研究进展。
从下面的图9,结果表明选择的解决方案来管理切屑和刀具之间的接触使刀具工作良好。
这给了令人满意的结果,在这里我们看到在该切屑包括刀具磨损和保持接触表面的月牙洼和之间的所有形成芯片的节点。
刀具切屑区域D图9数控刀具磨损仿真据观察,这种方法提供了在后刀面磨损比较差结果,因为忽视在前面的发生侧面刀具的回弹现象。
后者产生加工表面和刀具的前刀面之间的联系。
这接触效应提高摩擦系数是造成该地区高温[ 17 ]。
但在研究了进给速度和切削之间的比率刃口半径(F / R),它是可以忽略的后刀面磨损。
结论在本文中,刀具磨损建模开发从能量耗散接触区作为一个结果。
这种做法导致的实现在工具材料的损伤规律。
方法刀具的节点消除时使用后者达到的最大能量值的定义域。
该工具的第一个结果表达有限元法充满精力的方法似乎是有趣的。
当然,这是必要的使用的刀具磨损断裂能量设置完成研究。
后来,一部分是致力于发展一种新的方法,使我们能够显著降低计算所需的时间完成模拟。
方法高光的事实计算时间复杂性产生的管理切屑和刀具之间的接触。
该方法提出了保持历史加工完成的部分,因此,它是可能得到诱导的残余应力部分。
这最后一个方面将在未来的论文。
文献[1] Kgnay, Tchadj M.. 2009, Contribution àl’identification des mécanismes d’usure en usinage d’un WC-6%Co par une approche tribologique etthermique. ENSMP 2009. Thèse de doctorat. ED n°.432.[2] Nouari M., Molinari A. 2002, Modeling of tool wear by diffusion inmetal cutting, Wear 252-1, p. 135–149.[3] Poulachon G., Moisan A. et Jawahir I. S. 2001, Tool-wear mechanisms inhard turn-ing with polycrystalline cubic boron nitride tools, Wear,250(1-12) p. 576–586.[4] Muñoz-Sánchez A., Canteli J.A.,. Cantero J.L, Miguélez M.H. 2011,Numerical analysis of the tool wear effect in the machining inducedresidual stresses, 19-2 p. 872–886.[5] Yen Y. C., Söhner J., Lilly B., and Altan T., 2004, Estimation of tool wearin orthogonal cutting using the finite element analysis. Journal ofMaterials Processing Technology, 262 p. 82-91.[6] Filice L., Micari F., Settineri L., Umbrello D. 2007, Wear modelling inmild steel orthogonal cutting when using uncoated carbide tools, Wear,262, p. 545–554.[7] Attanasio A., Ceretti E., Fiorentino A., Cappellini C., Giardini C. 2010,Investigation and FEM-based simulation of tool wear in turningoperations with uncoated carbide tools, Simulation Modelling Practiceand Theory, 269, p. 344-350.[8] Xie L.-J., Schmidt, Schmidt C., Biesinger F. 2004, 2D FEM estimate oftool wear in turning operation, Wear, 258-10, p. 1479-1490.[9] Ramalho A., Miranda J.C. 2006, The relationship between wear anddissipated energy in sliding systems, Wear 260, p. 361-376.[10] Huq M.Z., Celis J.-P., 2002 Expressing wear rate in sliding contactsbased on dissipated energy, Wear 252, p. 375–383.[11] Moxnes J. F., Teland J. A., Skriudalen S., Bergsrud S. M., Sundem-Eriksen L. and Fykse H. 2010, Development of material models forsemi-brittle materials like, Norwegian Defence ResearchEstablishment (FFI), ISBN 978-82-464-1830-8.[12] Johnson R. and Cook W.K., 1983, A constitutive model and data formetals subjected to large strains, high strain rates and hightemperatures, 7th International Symposium on Balistics p. 541-547.[13] Johnson W.H. and Cook G.R. 1985, Fracture Characteristics of ThreeMetals Subjected to Various Strains, Strain Rates, Temperature andPressures, 21 p. 31-48.[14] Barge M., Hamdi H., Rech J. and Bergheau J. M., 2005, Numericalmodelling of orthogonal cutting: influence of numerical parameters,Journal of Materials Processing Technology, 164-165, p. 1148-1153.[15] Mabrouki T., Girardin F., Asad M., and Rigal J.-F. 2008, Numerical andexperimental study of dry cutting for an aluminium alloy 48, p. 1187 -1197.[16] Salvatore F., Mabrouki T., Hamdi H., 2012, Numerical andexperimental study of residual stresses induced by machiningprocesses, Int. Journal of Surface Science and Engineering, 6-1/2, p.136-147.[17] Salvatore F., Mabrouki T., Hamdi H., 2011, Numerical simulation andanalytical model-ling of ploughing and elastic phenomena duringmachining processes, Int. Journal of Surface Science and Engineering,6-3, p. 185-200.Modeling and simulation of tool wear during the cutting process AbstractExperimental and analytic methods are still the main ways to investigate different cutting tool wear types. Numerous developmentsof numerical methods and simulations, associated to the existence of more and more powerful computer make possible tool wearstudies using FEM. The main purpose of this work is to present a new approach to predict tool wear progression during cuttingoperation. In particular, an energy approach, linking the tool wear volume with the energy dissipated by friction is used. In addition,the interaction between residual stresses induced by cutting and the variation of tool geometry due to wear's mechanisms is investigated.In order to carry out this study, it is presented the experimental measurements of the wear of the tool, in particular the lost volumeduring the cut. Numerical simulation of orthogonal cutting operation using the commercial FEM code ABAQUS/Explicit is employed.1. IntroductionThe tool wear has a large influence on the economicsof machining operation and the influence in the surfaceintegrity. In fact, tool wear affect the tool life and thequality of the final product in terms of residual stress.For these raisons many investigations on tool wear arefound in the literature [1-2-3]. The simulation of wear ofthe cutting tool in orthogonal cutting is developed toeither validate a mechanism of wear. Either in thesesimulations, researchers tend to better understand theinfluence of tool wear in the impact of the residual stressin the final product [4]. In some investigations [5-6] thetool wear model implemented in a subroutine, is relativeto a specific wear mechanism like abrasion and diffusivewear. So in this investigation, a specific mechanism isconsidered as largely influencing the wear phenomena.In fact, tool wear is affected by several and differentmechanisms like material adhesion, erosion, corrosion,abrasive, and fracture. During cutting, tool geometry ischanging due the tool wear effect. This updating in thetool geometry is largely modeled, in numericalsimulation, by a movement of the tool face node [7].This method is used with a specific subroutine whichevaluates the cutting variables like, temperature, normalpressure and sliding distance from every tool nodes thatexist in the simulation of orthogonal cutting. After that,other subroutine is launched to impose node movement.The existing wear model can be classified into twotypes: the first one is cutting parameter-tool life type,such Taylor’s equation, the second one is cutting processvariable often based on one or several wear mechanisms[8]. This modeling is weak because, on one hand, thewear phenomena are modeled as discontinuousphenomena in time which is not the case in reality. Onthe other hand, it is limited in terms of the implementedwear mechanism, i.e. the problem of wear is reduced toone or two wear mechanism.The phenomenon of wear in contact is illustrated infretting system by a relationship between the formationof debris and the energy dissipated by friction in thecontact. This dissipated energy is the more controllablein terms of quantity used in the contact zone [9]. Thismethod is experimental, a tribometer is used to quantifythe value of efforts in the contact and then the energydissipated by friction and links it with the lost volume inthis zone [10].For these reasons, it is presented in this paper a newapproach, which provides not only a global modeling ofthe wear phenomena but also the combination of twoaspects, the progression of tool wear and his impact onthe residual stress of the final product in the orthogonalcutting configuration.In order to lead this study, the methodology proposedhas three different parts. In the first part, a tool wearmeasurements are presented. Afterwards, the energyapproach is presented and modified for the application inthe orthogonal cutting. A numerical simulation of theorthogonal cutting operation is developed, using thecommercial FEM code ABAQUS/Explicit. The last partincludes the numerical results of the tool wear evolutionduring simulation and the conclusion.2. Experimental testsThe experimental tests, conducted to validate theFEM model and measure the progressive tool wear,consisted of turning operation discs made of 42CD4 withan initial diameter of 70 mm. the used tool is uncoatedwith a tungsten carbide (WC) referenced as TPKN 1603PPR. (Fig. 1).Fig. 1. Experimental configurationWear measurements are done using microscope andthere are presented in table 1, according to figure 2. Vc isthe cutting speed, f the feed rate.Table 1. Experimental wear measure in case of tungsten carbide toolCutting conditions TimeFig. 2. Location of measured geometries of the tool3. Numerical model3.1. Tool modelingThe material used for the cutting tool is tungstencarbide. This choice is influenced by the type of toolused in experimental tests, which are tools made oftungsten carbide. So, to compare the results issued bythe experience and those issued by the numericalsimulation, the choice of using the same type ofmaterials is required. In regard to the law used to modelthe flow of material was chosen to use the curveconstraints functions of plastic strain. Therefore, thematerial used to model the tool has an elastic-plasticbehavior like it is acted in table 2 [11].Table 2.Carbide tungsten material modelThe damage model implemented on the calculationsoftware ABAQUS/Explicit to model the damage of thetool is the model of Johnson and Cook [12-13]. Theparameters used are given in the following table 3 [9].Table 3. Carbide tungsten material modelThe cutting tool is defined as deformable anddamageable. The cutting speed is rather imposed a rigidbody. This idea comes from the fact that we must avoidapplying a velocity or displacement on a deformablebody. So to avoid all purely numerical problems, wechose to use a rigid body that supports the deformabletool. The connection between the two is done with thefunction Tie.The tool has a cutting edge radius of 10 , and a flankangle of 11 °. The geometric modeling is on the cuttinginsert used in experimental tests. Because of contactproblems, it is ensured that a portion of the tool cuttingedge radius is without damage (Zone D) like it is showedin figure 3. This solution is necessary to maintain contactbetween all nodes in the separation zone and the outersurface of the D zone.Fig. 3. Geometry and mesh of the toolFracture energy Emax (in ABAQUS) was implementedin the tool quite low in order to found a fast tool wear innumerical simulations of orthogonal cutting that lasts afew ms.3.2. .Work piece modelingVery high strain, strain rate and temperature in metalcutting process, have strong influence on materiel’s flow. To get better chip formation analysis results, amaterial model that combines all these aspects isnecessary. In this simulation, it is opted for the Johnsonand Cook behaviour and constitutive law [14-15-16].3.3. .Contact problemThe most important problem faced in thedevelopment of a numerical model of orthogonal cuttingthat takes into account the tool wear is contactmanagement. Already, this aspect is very sensitive in theclassical simulation and it grows in the case where thecontact is dynamic, i.e. between two sets of nodes,respectively node of work piece and tool node. Note thatthe ABAQUS software, on how the numerical model isdeveloped, cannot handle the contact regions betweentwo nodes. So, it just allows a contact between a surfaceand a set of nodes. The commercial software is limitedin terms of contact management regarding 2Dmodelling. (Fig. 4).Fig. 4. Contact problemThis solution can manage the contact between allnodes of the tool and the inner surface of the chip thatwill be generated. This method is possible through theuse of a model of orthogonal cutting with a separationline defined fields and three areas of separation, wherethe ability to select the inner surface of the chip (Fig. 5).Fig. 5. Contact problem between the tool and the chipThe contact and friction at tool/chip and tool/workdetermines the cutting power and the tool wear. In this paper a Coulomb’s frictio n model is used with a constantfrictional coefficient of 0.2.4. Numerical simulations4.1. Development of a simulation lasting several secondsNumerical simulations of orthogonal cutting last inmost cases a few milliseconds. These simulations greatlyreduced in terms of simulation time have a fairly largecomputational time and can take several days. So,regarding the numerical simulations where thesimulation time is in order of one minute, it is expectedthat a fairly high computational time which may meetseveral weeks. In order to develop a numericalsimulation which takes several seconds, we must findsolutions to reduce the computation time. In thefollowing, it is presented the developed model whichprovides innovative solutions to address this problem.The computation time in a numerical simulation ismainly divided between the need to calculate thedeformations within the material and the need to managethe contact. This time is variable depending on theformulation used. It is known that the computation timeis even less important in the order of the followingformulations,Lagrangian, Eulerian and ALE.It can be concluded that the choice of the Lagrangianformulation is already done and we cannot change it,because of contact constraints imposed from thebeginning. This goes back to investigate the secondchannel which is responsible for increasing thecomputing relative to management of the contact. So it ispossible to deduce that the contact time is moreimportant than the number of nodes in contact is high.The following figure, (Fig. 6), shows the case ofnumerical simulation of relatively long pieces of about50 mm, the calculation time isincreasingly importantgiven the increase of nodes in contact. These nodes arerelated to chips. In some cases, there were excessivedistortions that create a stop calculation. The distortedmeshes are particularly located in the chip. This is due tothe winding of chip on itself.Fig. 6.Increase in computation time caused by the nodes in contactIt is now focused on the problem created by thegradually chip generated as the simulation evolves. Thesolution is in place from the fact that the chip generatessignificant computational time for the management ofnodes in contact. This solution also relies on the fact thatthe chip is something of a waste, even if it allows us tohave a wealth of information concerning the conduct ofthe cut operation. Consequently it is opted for theelimination of this chip. So that it does not causecomplications in the simulation which would bereflected in the computation time implemented tomanage the contact between the chip itself and the rawsurface. The following figure 7 presents the modeldeveloped with the discontinuous chip. After a period oftime the chip is ejected from the cutting area. Theejection of the cutting area saves time thanks to thesizeable reduction of the contact surfaces and then theresulting equations.Fig. 7. Solution to reduce the calculation time, e=80 mFig. 8. Elimination of the chip from the cutting area4.2. Numerical wear simulationsThe developed model, delivers first fairly satisfactoryresults. It shows that the crater wear develops graduallyas the simulation advances. From the following figure 9,it is showed that the solutions chosen to manage thecontact between the chip and all nodes of the tool workwell. These give satisfying results, where we see that theinside of the chip follows the tool wear and keeps acontact surface between the crater and all nodes of theformed chip.Fig. 9. Numerical tool wear simulationsIt is observed that this approach gives rather poorresults in terms of flank wear because of the neglectedthe spring back phenomenon that happening in front offlank tool. The latter generates a contact between themachined surface and the rake face of the tool. Thiscontact effect as raising the coefficient of friction that iscausing high temperatures in this area [17]. But in thepresented study the ratio between feed rate and cuttingedge radius (f/R) is high and it is possible to neglectflank wear.ConclusionIn the presented paper, tool wear modeling hasdeveloped as a result from the energy dissipation on thecontact zone. This approach leads to implementing adamage law in the tool material. The method ofelimination of nodes of the tool is used when the latterreaches the value of a defined maximum energy fields.The first results of the tool wear delivered by FEMenergetic approach seems like interesting. For sure, it isnecessary to complete the study with the setting of thetool wear using fracture energy.Afterwards, a section is devoted to the developmentof a new method that allows us to significantly reducethe computation time required to complete thesimulation. The approach high-lights the fact that thecomputation time is generated by the complexity ofmanaging the contact between the chip and work piece.This method presented in this paper keeps the historyof machining in the finished part and as a result, it ispossible to derive the residual stresses induced in thepart. This last aspect will be presented in a future paper.。