SPC八大判异原则及图形
SPC_8种判异准则

SPC_8种判异准则SPC(统计过程控制)是一种结合统计和数据分析的质量管理方法,用于监控过程的稳定性和控制产品的质量。
为了有效地判断一个过程是否发生了变化,并且有助于及时采取纠正措施,SPC中有八种常用的判异准则。
1. 极差判异准则(Range Test):极差是指一组数据中最大值和最小值之间的差异,当一些样本的极差超过了设定的极差上限或下限时,就发生了极差异常。
极差过大可能是因为操作方法改变、设备故障或材料变异导致。
2. 一致性判异准则(Run Test):一致性是指一组数据连续出现的相同结果,当同一个符号连续出现的次数超过设定的限制时,就发生了一致性异常。
一致性的出现可能是由于操作员的错误或机器的固有问题导致。
3. 均值判异准则(Mean Test):均值是指一组数据的平均值,在SPC中常常用于判断处理过程中是否存在平均偏移。
当一个样本的均值超过设定的均值上限或下限时,就发生了均值异常。
均值异常可能是由于原材料的变化、机器调整不当、操作员技术水平等问题引起。
4. 均值差异判异准则(Mean Difference Test):均值差异是指两组数据的均值之间的差异,在SPC中常常用于不同运营条件或不同设备之间的比较。
当两组数据的均值差异超过设定的差异上限或下限时,就发生了均值差异异常。
均值差异异常可能是由于不同设备或运营条件导致的。
5. 中位数判异准则(Median Test):中位数是指一组有序数据中处于中间位置的数值,中位数判异准则用于判断一组数据是否存在异常,当一个样本的中位数超过设定的中位数上限或下限时,就发生了中位数异常。
中位数异常可能是由于样本中存在极端值或其他偏倚导致。
6. 偏度判异准则(Skewness Test):偏度是指一组数据分布的不对称程度,正偏表示分布右侧比左侧更重,负偏表示分布左侧比右侧更重。
偏度判异准则用于判断一组数据的偏度是否超过设定的阈值,一旦发生偏度异常,可能是由于采样偏差或数据收集错误导致。
SPC_8种判异准则

SPC_8种判异准则SPC(Statistical Process Control,统计过程控制)是一种通过统计分析来监控和控制过程稳定性的方法。
在SPC中,判异准则用来判断过程是否处于控制状态,即过程是否稳定。
下面介绍SPC中常用的8种判异准则:1.点在控制界限之外:该判异准则是最常用的准则之一、该准则要求观察点的数值超出了控制限范围,即超出了正常的变异范围。
2.达到连续规则:该准则要求连续9个点落在同一侧的控制线上,即在过程的一侧出现异常。
这种异常模式可能显示出其中一种迁移或持续的趋势。
3.前后规则:该准则要求连续6个点在同一侧的控制线上,在随后的6个点中至少有4个点处于另一侧的控制线上。
这种模式可能显示出不稳定的变异。
4.背靠背规则:该准则要求连续6个点在同一侧的控制线上,并且其中至少有3个点与前面的连续6个点在同一侧。
这种模式可能表明过程正发生变化。
5.平均值规则:该准则要求连续两个样本的平均值落在中心线的同一侧,并且超出了控制限的2个标准差。
这种模式可能表示过程均值的变化。
6.趋势规则:该准则要求观察点有连续的5个点递增或递减。
这种模式可能表示着其中一种持续的变化趋势。
7.群体间隔规则:该准则要求同一样本的两个连续点间隔超过2个标准差。
这种模式可能表示出样本的变异与正常变异模式不同。
8.确认规则:当其他判异准则发出异常信号时,可以使用该准则进行确认。
该准则要求出现连续超过10个点都没有异常信号时,可以认为其他判异准则出现异常是真实的。
这些判异准则提供了一种可靠的方法来检测和判断过程是否处于控制状态。
通过使用这些准则,可以及时识别并纠正过程中的异常,保证产品质量的稳定性和一致性。
同时,SPC中还可以根据不同的需求和情况,灵活调整和应用这些判异准则,以适应不同的生产环境和过程变异特点。
SPC判异准则及异常处理方法
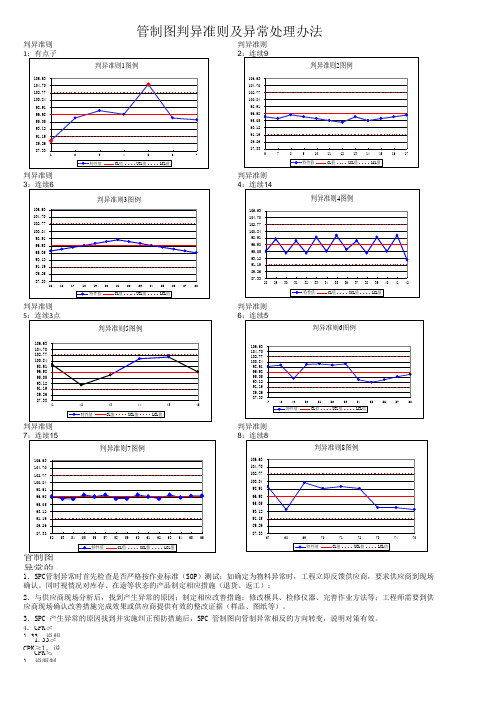
判异准则1:有点子落在界外。
判异准则2:连续9点落在中心线同一侧。
判异准则3:连续6点递增或递减。
判异准则4:连续14点相邻点上下交替。
判异准则5:连续3点中有2点落在中心线同一侧的B 区以外。
判异准则6:连续5点中有4点在中心线同一侧的C 区以外。
判异准则7:连续15点在C 区中心线上下。
判异准则8:连续8点在中心线两侧。
但无一在C 区中。
管制图异常的处理:
4. CPK≥1.33,说明制程能力较好,需继续保持; 1.33≥CPK≥1,说明制程能力一般,须改进加强; CPK≤1,说明制程能力较差,急需改进。
管制图判异准则及异常处理办法
1.SPC管制异常时首先检查是否严格按作业标准(SOP)测试;如确定为物料异常时,工程立即反馈供应商,要求供应商到现场确认。
同时视情况对库存、在途等状态的产品制定相应措施(退货、返工);
2.与供应商现场分析后,找到产生异常的原因;制定相应改善措施:修改模具、检修仪器、完善作业方法等;工程师需要到供应商现场确认改善措施完成效果或供应商提供有效的整改证据(样品、图纸等)。
3.SPC 产生异常的原因找到并实施纠正预防措施后,SPC 管制图向管制异常相反的方向转变,说明对策有效。
SPC-8种判异准则
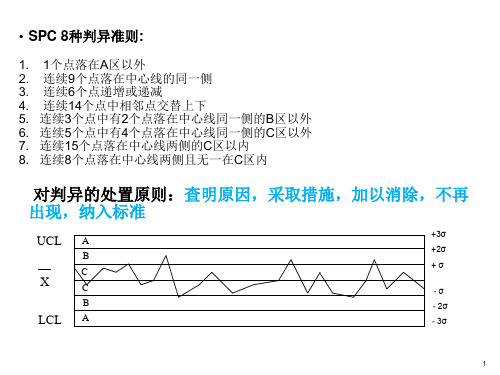
对判异的处置原则:查明原因,采取措施,加以消除,不再 出现,纳入标准
UCL A
+3σ
+2σ
B
C
+σ
X
C
-σ
B
- 2σ
LCL A
- 3σ
1
判异准则1
任何 1个点落在A区以外
x
UCL A
B C
C B A
LCL
x
Test 1. One Point Beyond Zone A
异常原因一般为: • 新操作人员,方法不对,机器故障,原料不合格 • 检验方法或标准变化 • 计算错误,测量误差
2
判异准则2,5, 6:
Test 2. Nine Points in a Row on One Side of the Center Line
2: 连续9个点落在中心线的同一侧;
UCL
A
5: 连续3个点中有2个点落在中心线同一侧的B 区以外;
B
6: 连续5个点中有4个点落在中心线同一侧的C
C
区以外
B
x
A
LCL
3
判异准则3 连续6个点递增或递减
Test 3. 6 Points in a Row Steadily Increasing or Decreasing
UCL
A
x
B
C
C
B A
LCL
x
异常原因一般为:
• 工具逐渐磨损,维护水平逐渐降低,操作人员技能逐渐提高
4
判异准则4
连续14个点中相邻点交替上下
异常原因一般为:
• 数据有假,计算错误;分层不够
6
判异准则8
连续8个点落在中心线两侧且无一在C区内
SPC判异规则

GB/T4091-2001《常规控制图》规定了八个判异准则:
准则1:一个点子落在A区以外。
A B C C B A
UCL
CL
LCL
P=0.0027
准
则 ②
连续9点落在中心线同一侧。
A B C C B A 表明均值可能产生偏移。
P=2(0.9973/2)9= 0.0038
准 则 ③
连续6点递增或递减。
八条判异规则的原理
在3σ界限控制图中,正常条件下,点子越出界限
的概率只有0.27%,这是一个小概率事件,若不是
异常状态,点子是不会超出控制界限以外的。另外, 即使所有点子落在界限内,但如果有下列排列异常的 情况发生,仍有可能判断处于失控状态。同理可以计 算下列情况的发生概率,它们也是小概率事件。
①过程控制异常的判断
准 则 ⑦ 连续15点落在中心线两侧的C区之内
A B C
C B A
数据分组不当,控制规格太宽和数据不准确所造成。 或应重新计算控制线。 P=(1-0.15886x2)15=0.00326
准
则 ⑧
ቤተ መጻሕፍቲ ባይዱ
连续8点落在中心线两侧,但无一点在C区中
A B C
C B A
标准差太大
P=(0.15886x2)8=0.000103
P=0.004
准 则 ⑤
连续3点中有2点落在中心线同一侧的B区以外
A
B
C C B
A
说明标准差可能已经变大
P=6X0.0228X0.0228X0.9772=0.003
准 则 ⑥
连续5点中有4点落在中心线同一侧的C区以外
A B
C C
B A 可能均值发生了变化 P=2X5X0.158664X(1-0.15886)=0.005331
SPC判稳、判异准则

准则依据图示特点发生原因
准则11点再A区外可对均值或标准差的变化给
出信号;也可对过程中的单
个失控做出反应
计算错误;
测量误差;
原料不合格;
设备故障
准则2连续9点分布于中
心线同侧
补充准则1而设计,以改进
控制图的灵敏度
过程平均值变大或是变小(人员或
是工具变化)
准则3连续6点递增或递
减
针对过程平均值的趋势设
计,比准则2更灵敏
工具磨损、维修逐渐变坏;
作业者技能提高
判异准则(GB/T4091-2001《常规控制图》)SPC控制图判稳、判异准则
判稳准则(满足一条即可)
①连续25个点,界外点数d=0 ②连续35个点,界外点数d≤1 ③连续100个点,界外点数d≤2
准则4连续14个相邻点上
下交替
由于两台设备轮流使用或是
两个作业人员轮流操作而引
起的系统效应
两个设备轮流使用或是两个作业人
员轮流作业
准则5连续3点中有2个点
落在中心线同一侧
的B区以外
对于变异的增加也比较灵
敏,第三点甚至可以不存在
平均值发生变化
准则6连续5点中有4点落
在中心线同一侧的
C区以外
与准则5相似平均值发生变化
准则7连续15点在C区中
心线上下
不要被美好的“外貌”所迷
惑
数据虚假;
分层不够;
准则8连续8点在中心线
两侧,当无一在C
区中
分层不够。
SPC控制图8种不良模式

4
潘帅杰 <常规控制图>
国家标准GB/T4091-2001
5
异常4:连续14点中相邻点交替上下
例1:
A B C C B A
异常5:连续3点有2点落在中心线同一侧的B区外(2σ外)
例1:
A B C C B A A B C C B A
异常6:连续5点中有4点落在中心线同一侧的C区外(1σ 外) 例1:
异常1:点落在控制限外
例1:
A B C C B A A B C C B A
异常2:连续9点落在中心线同一侧
例1:
A B C C B A
异常3:连续6点递增或递减
例1:
例2:
A B C C B A A B C C B A
例2:
A B C C B A
例2:
潘帅杰 <常规控制图>
国家标准GB/T4091-2001
例1:
A B C C B A A B C C B A
异常8:连续8点落在中心线两侧且无1点在C区内
例1:
例2:
A B C C B A A B C C B A
例2:
潘帅杰 <常规控制图>
国家标准GB/T4091-2001
9
潘帅杰 <常规控制图>
国家标准GB/T4091-2001
10
例2:
A B C C B A A B C C B A
例2:
A B C C B A
例2:
潘帅杰 <常规控制图>
国家标准GB/T4091-2001
6
潘帅杰 <常规控制图>
国家标准GB/T4091-2001
spc控制图判异标准

连续8点在中心线两侧,
中心线上下
准则 Criteria 7 UCL
A B
A B
X
C C B A
X
C C B
LCL
LCL
A
控制图在贯彻预防原则中的作用
第一:应用控制图对生产过程进行监控,
如出现前述的8种情形之一,应及时采取 措施加以消除,这就是预防。 第二:控制图上点子突然出界,显示异 常。这时必须查出异因,采取措施,加 以消除。 控制图的作用:及时告警。必须强调现 场第一线的生产管理人员来推行SPC,把 它作为日常工作的一部分。
X
C C B
LCL
A
LCL
A
准则3
连续6点递增或递减
准则 Criteria 3 UCL UCL
准则4
连续14点相邻点上
下交替
准则B
X
C C B
LCL
A
LCL
A
天马行空官方博客:/tmxk_docin ;QQ:1318241189;QQ群:175569632
- 8种准则
天马行空官方博客:/tmxk_docin ;QQ:1318241189;QQ群:175569632
判异的定义
国标GB/T 4091-2001《常规控制图》中
规定了8种判异准则。 为了应用这些准则,将控制图等分为6个 区域,每个区域宽1σ,分别标识为A、B、 C、C、B、A。 需要指明:这些判异准则主要适用于X 图和单值X图,且假定质量特性X服从正 态分布。
天马行空官方博客:/tmxk_docin ;QQ:1318241189;QQ群:175569632
准则1
一点落在A区以外。 点出界就判异