精炼工艺流程图
炼钢生产过程以及流程图详解(全)
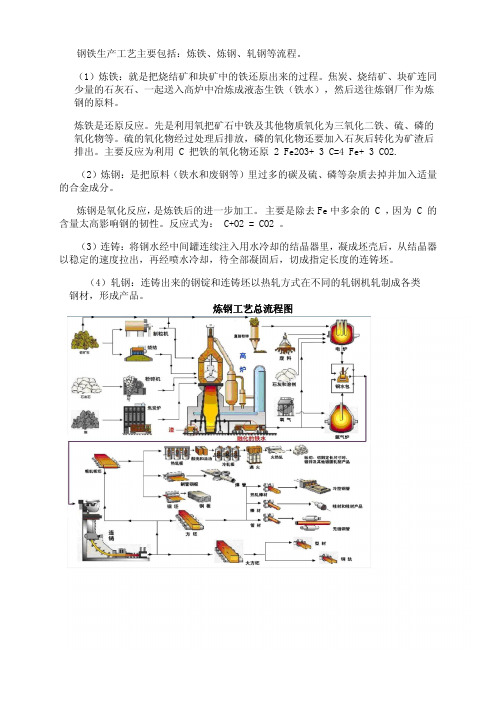
钢铁生产工艺主要包括:炼铁、炼钢、轧钢等流程。
(1)炼铁:就是把烧结矿和块矿中的铁还原出来的过程。
焦炭、烧结矿、块矿连同少量的石灰石、一起送入高炉中冶炼成液态生铁(铁水),然后送往炼钢厂作为炼钢的原料。
炼铁是还原反应。
先是利用氧把矿石中铁及其他物质氧化为三氧化二铁、硫、磷的氧化物等。
硫的氧化物经过处理后排放,磷的氧化物还要加入石灰后转化为矿渣后排出。
主要反应为利用 C 把铁的氧化物还原 2 Fe2O3+ 3 C=4 Fe+ 3 CO2.(2)炼钢:是把原料(铁水和废钢等)里过多的碳及硫、磷等杂质去掉并加入适量的合金成分。
炼钢是氧化反应,是炼铁后的进一步加工。
主要是除去Fe中多余的 C ,因为 C 的含量太高影响钢的韧性。
反应式为: C+O2 = CO2 。
(3)连铸:将钢水经中间罐连续注入用水冷却的结晶器里,凝成坯壳后,从结晶器以稳定的速度拉出,再经喷水冷却,待全部凝固后,切成指定长度的连铸坯。
(4)轧钢:连铸出来的钢锭和连铸坯以热轧方式在不同的轧钢机轧制成各类 钢材,形成产品。
炼钢工艺总流程图炼焦生产流程:炼焦作业是将焦煤经混合,破碎后加入炼焦炉内经干馏后产生热焦碳及粗焦炉气之制程。
烧结生产流程:烧结作业系将粉铁矿,各类助熔剂及细焦炭经由混拌、造粒后,经由布料系统加入烧结机,由点火炉点燃细焦炭,经由抽气风车抽风完成烧结反应,高热之烧结矿经破碎冷却、筛选后,送往高炉作为冶炼铁水之主要原料。
还原气体,还原铁矿石,产生熔融铁水与熔渣之炼铁制程。
转炉生产流程:炼钢厂先将熔铣送前处理站作脱硫脱磷处理,经转炉吹炼后,再依订单钢种特性及品质需求,送二次精炼处理站(RH真空脱气处理站、Ladle Injection盛桶吹射处理站、VOD真空吹氧脱碳处理站、STN搅拌站等)进行各种处理,调整钢液成份,最后送大钢胚及扁钢胚连续铸造机,浇铸成红热钢胚半成品,经检验、研磨或烧除表面缺陷,或直接送下游轧制成条钢、线材、钢板、钢卷及钢片等成品。
铁合金车间工艺流程图

硅铁车间工艺流程图煅烧车间工艺流程图↓↓ ↓↓ ↓原料车间压球工艺流程图↓↓↓↘↓↙↓↓↓↓还原车间工艺流程图↓↓↑↓↓↓↓精炼车间工艺流程图↓↓↓↓↓↓↓↓↓附录F5硅铁车间工艺条件及技术指标1.硅石1.1SiO2含量:≥97%。
1.2硅石中有害杂质含量:Al2O3≤0.8% P2O5≤0.02% MgO+CaO≤1%1.3硅石应有较好的机械强度和抗爆性。
1.4硅石加工粒度:60-120mm。
2.焦粉2.1固定碳含量:≥84%2.2灰分:≤6%2.3挥发份:≤22.4入炉粒度:5-15mm(其中5mm以下的不得大于5%)2.5要求高电阻,不得有粉沫。
3.钢屑3.1含铁量:≥97%3.2应是普通炭钢屑,不得混有合金钢屑、有色金属屑和生铁屑等。
3.3生锈严重的钢屑不得使用。
3.4钢屑的卷曲长度为30-50mm。
3.5要纯净,不得混有泥土等杂质。
4.冶金焦4.1粒度:5—10mm4.2固定碳≥84%4.3灰分≤6%4.4挥发份≤10%4.5不得有粉尘粉沫5.球团矿5.1含铁≤60%5.2粉沫≤5%5.3有较好的机械强度6.硅铁指标6.1硬75#硅铁占90%。
6.2软75#硅铁占10%。
6.370#硅以下的产品不生产。
6.4硅的偏析-不大于4%,小于20×20mm的数量,不得超过8%。
7.硅铁生产技术条件7.1矿热炉容量7.1.1炉膛底部直径5.8m。
7.1.2炉子直径7.32m。
7.1.3炉膛深度2.15m。
7.1.4极心圆直径2.5m。
7.1.5电极直径1.00m。
7.2二次侧电压:118-160A7.3运行电流:13档7.4出铁时间:5-15分钟7.5出铁次数:3-4次/班(特殊情况除外)7.6配料比:硅石200kg 焦粉108-140kg 钢屑10kg7.7 球团矿:36kg(根据硅铁含硅量调整)煅烧工艺条件及技术指标1.工艺条件1.2 要求白云石成分稳定,粒度20~35mm,不含泥土及杂质。
120t区域精炼工艺3-16详解PPT课件

7/30/2024
.
16
适当的Al2O3含量:在渣中的Al2O3含量低于30% 时,增加其含量,可以增加渣的流动性,改善动力 学2.0条低%件氧以,势下但:,是(以FAe保Ol2O证+M3脱含n氧O量+、过C脱高r2O硫,3效)不含果利量。于一夹般杂应物控的制吸在附。 因此Ca应F2尽:量萤减石少有其利用于量化。渣,但是对包衬的侵蚀严重,
5.由于Al2O3比硅化合物更容易通过碰撞、聚合长大,因此更易去除。 6.在精炼处理过程中,钢水被渣中的FeO、MnO以及大气中的氧二次 氧化。
7/30/2024
.
21
4.Ca处理
对 不于易A去l脱除氧。镇通静过钢向,钢钢液中中夹加杂入物钙主合要金是或固高态CaAOl2O渣3料夹,杂将物钢,中熔点固高态, 的 的 的夹夹Al2杂杂O3物物转对中变钢S为的材液平性态衡能的浓的铝度影酸很响钙高也球,比形可固夹以态杂吸A,l附2O易大3小于量。从的同钢S时,液,中当含排其C除温a。度O残降很余低高 时,CaS析出,生成复合夹杂物,该夹杂物为球形,熔点高,轧制 时状态不变形。
搅拌作为一种炉外精炼手段,搅拌强度、持续时间应当可以按精炼要求 控制。
较早出现的搅拌方法,是利用钢液本身的位能,依靠钢液的冲击,促使 钢水搅动。
真空碳氧反应产生的CO气泡产生熔池搅拌,但搅拌强度较弱,持续的时 间也不可能太长,精确控制也比较困难。
RH、DH等方法利用压差造成部分钢水位能差异,利用钢液回流搅动熔 池,是一种简便可行的办法。
扩散脱氧 Al+O2- →Al2O3 Al2O3+CaO→(CaO)x(Al2O3)y
7/30/2024
.
19
一般情况下,脱氧结束后Mn/Si要>3,保证 生成的硅化物在钢水中以液态存在。
金银精炼工作流程图及工作标准

金银精炼工作流程图及工作标准
(一)金银精炼工作流程图
单位名称
精炼分厂
层次
3
单位
值班领导
工段长
节点
A
B
流程名称 概要
精炼班长 C
金银精炼工作流程
技术员 D
精炼工 E
1
开始
熔炼班 F
2
金泥
签收排产
粉化金
3
安排
加料
4
指标控制
设定参数
5
采样送检
收料
6
烘干
班长签收
7
结束
8
(二)金银精炼工作标准
任务 名称
精炼 准备
金银 精炼
节点
任务程序、重点及标准
程序
☆ 工段长从熔炼班接收粉化金,从值班领导处签收金泥,安排 A2 生产 F2 ☆ 精炼班班长具体安排本班生产 B2 重点 C3 ☆ 工作安排
标准
☆ 及时合理
程序
☆ 精炼工进行加料,精炼班班长对各项指标进行控制,技术员 E3 设定各项参数 C4
☆ 精炼工进行收料并烘干 D4
☆ 精炼班长采样送检 E5
☆ 熔炼班班长签收 C5
重点 E6
☆ 精炼过程控制 F6
标准
☆ 严格执行工艺控制标准
时限
依情况 即时
依情况 按规定 即时 即时
相关资料
《岗位职责与工 作标准》
《岗位操作规 程》
《岗位职责与工 作标准》
《岗位操作规 程》
。
植物油、浸出油、精炼工艺及设备

1.6.1.2工艺流程1.6.1.2.1植物油生产工艺流程及说明该项目把本地及周边地区农民种植的优质原料集中起来,采取先进的脱壳、除尘、去杂技术处理后通过物理压榨生产的毛油,经过精制后以植物油商品销售。
物理压榨后的饼以浸出方式生产的毛油,再经过精炼工序就可以得到精炼植物油,做为商品在市场上销售。
粕作为饲料生产的原料销售。
(1)工艺技术说明:清理:与普通二级油所用设备相同分级:用分级筛分离出花生中的未成熟粒、霉变粒、破碎粒等不完善粒,这部分可用于生产二级油,单独销售。
烘干/冷却:烘干设备可用热风气流干燥机。
花生烘干后水分控制在5%~6%。
然后迅速用冷空气把油粒温度降至40℃以下。
破碎/脱皮:破碎机可用齿辊式破碎机,目的是把红外衣扒掉,破碎后用风力风选器或吸风平筛将红外衣吸出,分离出的花生红皮可用作医药化工原料。
热风烘炒:将总量25%~30%的花生瓣送至燃油热风烘炒炉,在此烘炒炉内油料被加热到180℃~200℃。
烘炒温度是浓香花生油产生香味的关键因素,温度太低,香味较淡;温度太高,油料易湖化。
降温与轧糁:为防止油料糊化和自燃,烘炒后应迅速散热降温,降温后用齿辊式破碎机轧成碎粒状。
蒸炒:"用五层立式蒸炒锅对生坯进行蒸炒。
1层~2层装料要满,起到蒸的作用;3层~5层装料要浅,起到排除水分的作用;出料温度108℃~112℃,水分5%~7%,为保证花生油有浓郁的香味,蒸炒锅炉的间接蒸汽压力应不小于0.6mpa。
榨油:本工艺使用的榨油机考虑到浓香花生油生产工艺的特殊性,对榨油机主轴转速作了适当调整,主轴转速由原来的8rpm提高到10rpm,并适当放厚饼的厚度,一般控制在10mm左右。
入榨温度135℃,入榨水分1.5%~2%,机榨饼残油9%~10%。
所得毛油经沉淀后用立式叶片过滤机过滤后送到精炼车间,机榨饼经破碎后送至浸出车间进行二次浸出。
浸出毛油经精炼后作普通油单独销售。
(2)植物油生产工艺流程植物油生产工艺流程图1.6.1.2.2浸出油工艺流程萃取溶剂饼浸出油工艺流程图1.6.1.2.3精炼工艺流程及说明(1)精炼工艺流程说明毛油精炼,通常是指对毛油进行精制。
大豆油精炼加工工艺
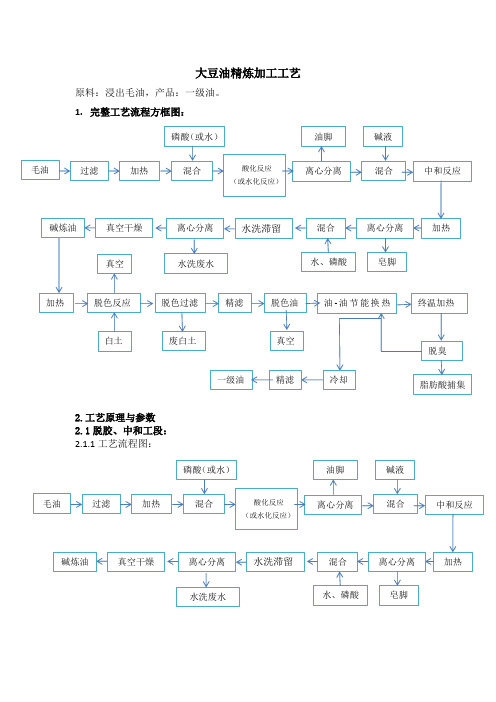
大豆油精炼加工工艺原料:浸出毛油,产品:一级油。
1. 完整工艺流程方框图:2.工艺原理与参数2.1脱胶、中和工段:2.1.1工艺流程图:油脚 碱液 磷酸(或水) 毛油 过滤 混合 加热 离心分离 酸化反应 (或水化反应) 混合 中和反应 加热离心分离 混合 水洗滞留 离心分离 真空干燥碱炼油 皂脚水洗废水 水、磷酸 油脚 碱液 磷酸(或水) 毛油 过滤混合 加热 离心分离 酸化反应 (或水化反应) 混合 中和反应加热 离心分离 混合 水洗滞留 离心分离 真空干燥 碱炼油 皂脚 水洗废水 水、磷酸 真空白土 加热 脱色反应 脱色过滤 精滤 脱色油 废白土 真空 油-油节能换热终温加热 脱臭 脂肪酸捕集冷却 精滤 一级油2.1.2工艺设备及原理大豆毛油经过滤、除杂后由泵送入生产线,经加热器加热至一定温度后进入混合器。
在混和器中,毛油与一定比例的磷酸溶液(或水)充分混合,随后进入延时罐进一步调质,油中的非水化磷脂转化为水化磷脂,然后进入脱胶离心机中进行分离,分离出油脚进入暂存罐中暂存。
酸化后的油(或脱胶油)进入混和器,与一定比例的碱液混合,使游离脂肪酸与碱发生中和反应生成钠皂,再进入延时反应罐充分反应,随后经泵送至加热器加热至一定温度,然后进入脱皂离心机中进行油皂分离,分离出皂脚进入皂脚罐中暂存。
脱皂后的油进入混和器中与一定比例的热水混合,同时添加少量的磷酸溶液(或柠檬酸水溶液),用于鳌和金属离子,利于去除残皂等杂质。
随后进入延时反应罐充分反应,再进入水洗离心机进行水洗分离,以去除残留皂脚等杂质。
水洗后的油最后进入真空干燥器中去除水分及其它挥发性物质,由泵输送至脱色工段。
2.1.3工艺参数●酸法脱胶工艺:100%磷酸(浓度75~85%)加入油量0.05~0.2 %100%柠檬酸(浓度~50%)加入油量0.05~0.2 %酸脱胶不仅对除去非水化磷脂,降低金属离子含量有利,而且对碱炼水洗除去油脂中含皂含量也有很大的益处。
精炼车间工艺流程 PPT

6、开启加热器蒸汽管阀门,使蒸汽加热器预热,蒸汽压力不大于0.5MPa。 7、将毛油泵入毛油罐待用。 8、这时脱胶脱酸工段已处于待机状态。 二、开机 1、开启进油泵、离心混合器以及酸、碱延时器,根据生产量调节进油流 量。 2、观察经蒸汽加热器加热后的出口油温,并调节蒸汽阀门,使出口油温 在60-75度之间。 3、开启酸定量泵。 4、油-酸混合液经过离心混合器,进入酸延时器,并注意酸延时器搅拌 轴的转速,以及罐内液位的变化。
节蒸汽阀门,使蒸汽加热器的出口油温在105-115度之间。 4、当真空干燥器内的油位达到一定高度时,开启真空干燥器抽出泵,
将油抽到一级油罐内(碱炼油罐)。 5、进行取样化验,直至合格。
二、停机: 1、关闭进油阀门。 2、关闭蒸汽加热器的蒸汽阀门。 3、待油抽空后,关闭脱水油抽出泵和真空管道阀门。 4、关闭所有阀门,下次开机待用。
精炼车间工艺流程
第三章 精炼车间工艺及原理
第一节、油脂精炼的目的和方法 第二节、脱胶脱酸工段 第三节、脱色工段 第四节、脱蜡工段 第五节、脱臭工段 第六节、综合注意事项 第七节、锅炉房(蒸汽锅炉与导热油炉) 第八节、操作规程及岗位职责
第一节、油脂产品精炼的意义
油脂精炼属于油脂加工的范畴,油脂加工就是把不同种类、不同制油方法 得到的毛油,加工成各种品种和各种规格的油脂产品的过程,除了油脂精炼, 还包括油脂的改性、调制、水解聚合等。用压榨、浸出、水代法制取的未经精 炼的油脂称为毛油,毛油的主要成份是甘油三酸酯及其混合物。毛油中存在非 甘油三酸酯的成份,统称为“杂质”。
例:毛油流量1m³/h,AV(酸价)1mgKOH/g,碱液浓度20Be`,碱定量泵100L/h, 求冲程?
已知:20Be`=14.36% d=1.2(碱的比重) 解: G理 = 0.713*AV*W
大豆油精炼加工工艺
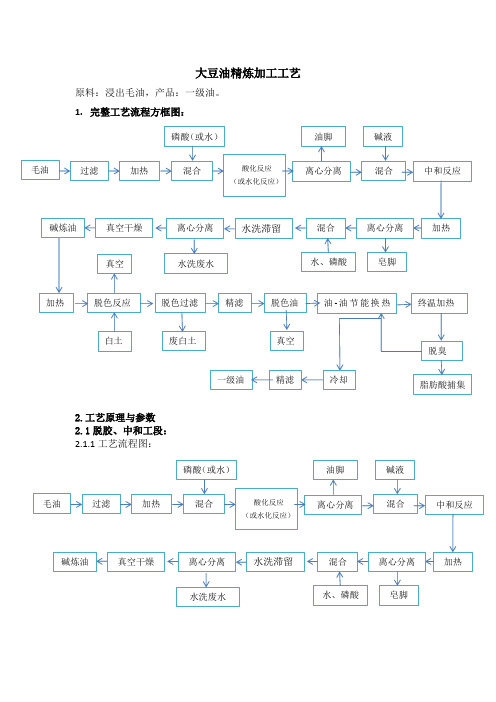
大豆油精炼加工工艺原料:浸出毛油,产品:一级油。
1. 完整工艺流程方框图:2.工艺原理与参数2.1脱胶、中和工段:2.1.1工艺流程图:油脚 碱液 磷酸(或水) 毛油 过滤 混合 加热 离心分离 酸化反应 (或水化反应) 混合 中和反应 加热离心分离 混合 水洗滞留 离心分离 真空干燥碱炼油 皂脚水洗废水 水、磷酸 油脚 碱液 磷酸(或水) 毛油 过滤混合 加热 离心分离 酸化反应 (或水化反应) 混合 中和反应加热 离心分离 混合 水洗滞留 离心分离 真空干燥 碱炼油 皂脚 水洗废水 水、磷酸 真空白土 加热 脱色反应 脱色过滤 精滤 脱色油 废白土 真空 油-油节能换热终温加热 脱臭 脂肪酸捕集冷却 精滤 一级油2.1.2工艺设备及原理大豆毛油经过滤、除杂后由泵送入生产线,经加热器加热至一定温度后进入混合器。
在混和器中,毛油与一定比例的磷酸溶液(或水)充分混合,随后进入延时罐进一步调质,油中的非水化磷脂转化为水化磷脂,然后进入脱胶离心机中进行分离,分离出油脚进入暂存罐中暂存。
酸化后的油(或脱胶油)进入混和器,与一定比例的碱液混合,使游离脂肪酸与碱发生中和反应生成钠皂,再进入延时反应罐充分反应,随后经泵送至加热器加热至一定温度,然后进入脱皂离心机中进行油皂分离,分离出皂脚进入皂脚罐中暂存。
脱皂后的油进入混和器中与一定比例的热水混合,同时添加少量的磷酸溶液(或柠檬酸水溶液),用于鳌和金属离子,利于去除残皂等杂质。
随后进入延时反应罐充分反应,再进入水洗离心机进行水洗分离,以去除残留皂脚等杂质。
水洗后的油最后进入真空干燥器中去除水分及其它挥发性物质,由泵输送至脱色工段。
2.1.3工艺参数●酸法脱胶工艺:100%磷酸(浓度75~85%)加入油量0.05~0.2 %100%柠檬酸(浓度~50%)加入油量0.05~0.2 %酸脱胶不仅对除去非水化磷脂,降低金属离子含量有利,而且对碱炼水洗除去油脂中含皂含量也有很大的益处。
- 1、下载文档前请自行甄别文档内容的完整性,平台不提供额外的编辑、内容补充、找答案等附加服务。
- 2、"仅部分预览"的文档,不可在线预览部分如存在完整性等问题,可反馈申请退款(可完整预览的文档不适用该条件!)。
- 3、如文档侵犯您的权益,请联系客服反馈,我们会尽快为您处理(人工客服工作时间:9:00-18:30)。
精炼车间工艺流程图
400T/D酶法脱胶工段:
柠檬酸
↓
毛油→过滤(过滤器)→换热☆(换热器,70-95℃)→酸混合→酸反应(酸反应罐)
液碱水,PLC酶
↓↓
→碱混合→碱反应(碱反应罐)→换热☆(换热器,50-55℃)→酶混合器→酶反应→换热☆(换热器,75-90℃)→离心分离(离心机)→换热☆(换热器,85—95℃)→水混合→
↓
油脚
→水洗延时罐
↓
洗涤水
↑
→离心分离(离心机)→换热☆(换热器,105-125℃)→干燥☆(干燥罐,真空≤200mbar)→干燥油→冷却☆(换热器,65℃以下)→过滤→三级油
1200T/D水化脱胶工段:
热软水油脚→储存(暂存罐)→蒸发☆(蒸发器,100-135℃)→冷却☆(冷却器,30-65℃)
↓↑↓毛油→过滤(过滤器)→换热☆(换热器,70-95℃)→水化(水化反应罐)→离心分离(离心机)磷脂
→换热☆(换热器,90-125℃)→干燥☆(干燥罐,真空≤300mbar)→脱胶油
900T/D深度脱胶工段:
柠檬酸
↓
毛油→过滤(过滤器)→换热☆(换热器,70-95℃)→酸混合→酸反应(酸反应罐)→换热☆(换热器,40-45℃)
液碱
↓
→碱混合→碱反应(碱反应罐)→换热☆(换热器,70-95℃)→离心分离(离心机)→
↓
油脚
换热☆(换热器,105-125℃)→干燥☆(干燥罐,真空≤200mbar)→干燥油→冷却☆(换热器,75℃以下)
↓
过滤→四级油
1000T/D精炼工艺流程图:
磷酸液碱
↓↓
毛油→过滤(过滤器)→换热☆(换热器70-95℃)→酸混合→酸反应→碱混合→碱反应
→离心分离(离心机)→水洗混合→离心分离(离心机)→干燥(干燥罐)→干燥油→换热☆(换热器,88-125℃)
↓↓
皂脚洗涤水
白土
↓
→预混(预混罐)→脱色☆(脱色塔,真空≤400mbar)→混合油→过滤(过滤器)
↓
废白土
→脱色油→换热(换热器)→脱臭☆(脱臭塔,真空≤5mbar,温度230-250℃)→脱臭油→换热☆(换热器,75℃以下)
↓
脂肪酸,维E
→过滤→一级油→油罐→灌装封盖→装箱→入库
注:☆为关键控制点。