强度与刚度设计分解
机械设计中的结构强度与刚度分析
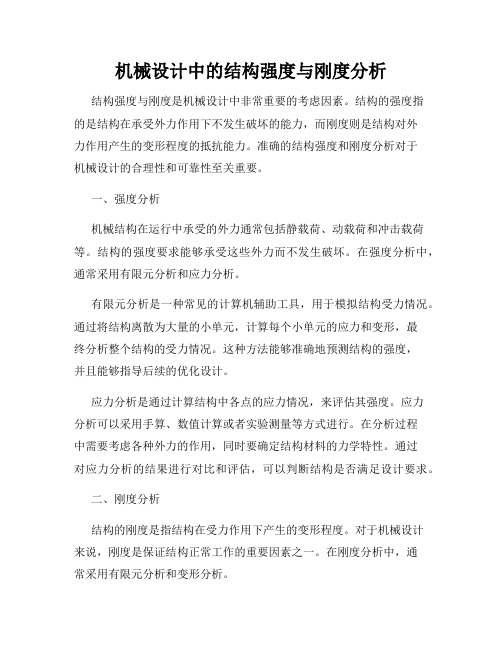
机械设计中的结构强度与刚度分析结构强度与刚度是机械设计中非常重要的考虑因素。
结构的强度指的是结构在承受外力作用下不发生破坏的能力,而刚度则是结构对外力作用产生的变形程度的抵抗能力。
准确的结构强度和刚度分析对于机械设计的合理性和可靠性至关重要。
一、强度分析机械结构在运行中承受的外力通常包括静载荷、动载荷和冲击载荷等。
结构的强度要求能够承受这些外力而不发生破坏。
在强度分析中,通常采用有限元分析和应力分析。
有限元分析是一种常见的计算机辅助工具,用于模拟结构受力情况。
通过将结构离散为大量的小单元,计算每个小单元的应力和变形,最终分析整个结构的受力情况。
这种方法能够准确地预测结构的强度,并且能够指导后续的优化设计。
应力分析是通过计算结构中各点的应力情况,来评估其强度。
应力分析可以采用手算、数值计算或者实验测量等方式进行。
在分析过程中需要考虑各种外力的作用,同时要确定结构材料的力学特性。
通过对应力分析的结果进行对比和评估,可以判断结构是否满足设计要求。
二、刚度分析结构的刚度是指结构在受力作用下产生的变形程度。
对于机械设计来说,刚度是保证结构正常工作的重要因素之一。
在刚度分析中,通常采用有限元分析和变形分析。
有限元分析可以用于计算结构的刚度。
通过将结构离散为小单元,计算每个小单元的变形,并进一步计算整个结构的变形情况。
通过对变形情况的分析,可以确定结构的刚度是否满足设计要求,并指导后续的优化设计。
变形分析是利用力学原理计算结构在受力作用下的变形情况。
变形分析可以通过数学建模、力学方程求解或者实验测量等方式进行。
在分析过程中需要考虑各种外力的作用和结构材料的力学特性。
通过对变形分析的结果进行评估,可以判断结构的刚度是否满足设计要求。
三、结构强度和刚度的优化设计结构强度和刚度的优化设计是机械设计中的重要任务之一。
通过分析结构的强度和刚度,可以确定结构的不足之处,并进行相应的优化改进。
在结构强度方面,可以通过增加材料的强度、增加结构的截面积或者改变结构的形状等方式来增强结构的强度。
机械设计基础机械结构的强度与刚度分析

机械设计基础机械结构的强度与刚度分析在机械设计中,结构的强度和刚度是两个非常重要的指标。
强度决定了机械结构在受力情况下的承载能力,刚度则关系到机械结构的变形和稳定性。
本文将探讨机械结构的强度和刚度分析的基本原理和方法。
一、强度分析1. 强度设计基本原理在进行结构的强度设计时,需要考虑机械结构受力情况下的应力和变形情况。
强度设计的基本原则是保证机械结构在各种负载情况下都不会出现破坏。
常用的强度设计方法有极限强度设计法和工作强度设计法。
极限强度设计法是基于材料的强度极限进行设计,通过比较应力和材料强度之间的关系来判断结构是否安全。
工作强度设计法则是根据材料的工作强度进行设计,将应力与工作应力进行比较来判断结构的安全性。
2. 强度分析方法在进行强度分析时,首先需要确定机械结构受力情况下的应力分布。
常见的受力情况包括拉力、压力、弯矩等。
根据受力情况,可以通过解析法、有限元法等方法计算结构的应力分布。
解析法是基于力学原理和材料力学性质的计算方法,通过数学公式和材料力学公式计算出结构的应力。
有限元法则是将结构分割为小块,然后通过数值计算方法求解每个小块上的应力,最终得到整个结构的应力分布。
二、刚度分析1. 刚度设计基本原理刚度是指机械结构受力情况下的变形程度。
在机械设计中,需要保证机械结构在受力情况下变形不超过允许范围,以确保机械结构的工作效果和稳定性。
刚度设计的基本原理是通过设计结构的几何形状和材料来控制结构的变形程度。
2. 刚度分析方法刚度分析的方法主要包括解析法和有限元法。
解析法是通过力学公式和材料力学公式计算结构的刚度。
有限元法是将结构离散化,并使用数值计算方法求解每个小块上的位移,最终得到整个结构在受力情况下的变形程度。
综上所述,机械结构的强度和刚度分析是机械设计中非常重要的一部分。
通过合理地进行强度和刚度设计,可以保证机械结构在工作时的安全性和稳定性。
强度和刚度分析的方法主要包括解析法和有限元法,设计工程师可以根据实际情况选择合适的方法进行分析。
机械设计基础机械结构的刚度与强度分析
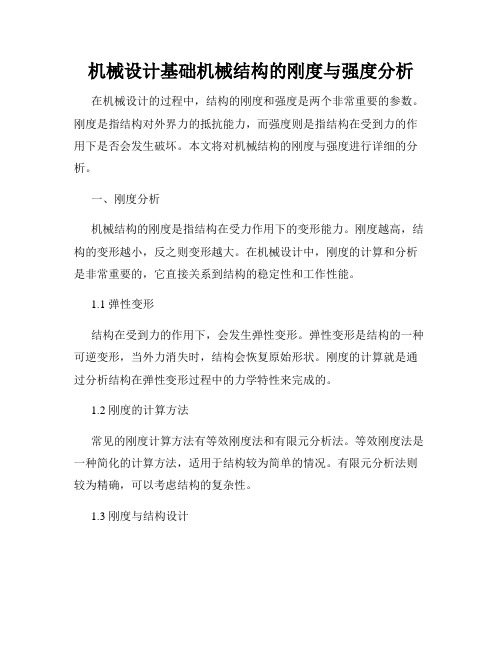
机械设计基础机械结构的刚度与强度分析在机械设计的过程中,结构的刚度和强度是两个非常重要的参数。
刚度是指结构对外界力的抵抗能力,而强度则是指结构在受到力的作用下是否会发生破坏。
本文将对机械结构的刚度与强度进行详细的分析。
一、刚度分析机械结构的刚度是指结构在受力作用下的变形能力。
刚度越高,结构的变形越小,反之则变形越大。
在机械设计中,刚度的计算和分析是非常重要的,它直接关系到结构的稳定性和工作性能。
1.1 弹性变形结构在受到力的作用下,会发生弹性变形。
弹性变形是结构的一种可逆变形,当外力消失时,结构会恢复原始形状。
刚度的计算就是通过分析结构在弹性变形过程中的力学特性来完成的。
1.2 刚度的计算方法常见的刚度计算方法有等效刚度法和有限元分析法。
等效刚度法是一种简化的计算方法,适用于结构较为简单的情况。
有限元分析法则较为精确,可以考虑结构的复杂性。
1.3 刚度与结构设计在机械结构设计中,刚度的要求会根据具体应用来确定。
一般来说,对于需要保持形状和位置不变的结构,刚度要求较高;而对于需要发生变形的结构,刚度要求可以适度降低。
二、强度分析机械结构的强度是指结构在受到力作用下不会发生破坏的能力。
强度分析是机械设计中必不可少的一步,它可以保证结构在正常工作条件下的安全性。
2.1 强度与材料特性结构的强度与所采用的材料有直接关系。
不同类型的材料具有不同的强度特性,例如金属材料的强度主要依赖于其抗拉强度和屈服强度。
在强度分析中,需要考虑结构所受到的最大力和所能承受的最大应力之间的关系。
2.2 强度计算方法常用的强度计算方法有等效应力法和有限元分析法。
等效应力法通过将结构的应力状态转化为等效应力的形式,然后与材料的强度特性进行比较来判断结构的安全性。
有限元分析法则可以更加精确地分析结构的应力和变形情况。
2.3 安全系数在强度分析中,通常会引入安全系数来保证结构的可靠性和安全性。
安全系数是指结构所能承受的最大力与实际所受力之间的比值。
机械结构设计中的刚度与强度分析

机械结构设计中的刚度与强度分析在机械工程和制造领域中,机械结构设计的刚度与强度分析是至关重要的一环。
刚度和强度是机械结构的两个基本性能指标,它们直接影响着机械设备的可靠性、稳定性和安全性。
本文将深入探讨机械结构设计中的刚度与强度分析,以及其在实际应用中的重要性。
刚度是指机械结构在受到外力作用时产生的变形程度。
一个刚度较高的结构在受力后会产生较小的变形,从而保证机械设备的稳定性和精度。
刚度的分析主要包括静态刚度和动态刚度两个方面。
静态刚度是指结构在静态条件下的刚度表现,可以通过有限元分析等方法进行计算和优化。
动态刚度则是指结构在动态条件下的刚度表现,例如在振动环境下的刚度特性。
动态刚度的分析可以帮助工程师预测和解决机械结构在振动工况下可能出现的问题,确保机械设备的可靠性和耐久性。
与刚度相比,强度是指机械结构在受到外力作用时能够承受的最大应力。
一个强度较高的结构可以保证机械设备在工作过程中不会发生破坏或失效。
强度的分析主要包括静态强度和疲劳强度两个方面。
静态强度是指结构在静态条件下的强度表现,可以通过应力分析和材料力学等方法进行计算和评估。
疲劳强度则是指结构在循环载荷下的强度表现,例如机械设备在长时间运行过程中可能受到的循环载荷。
疲劳强度的分析可以帮助工程师预测和解决机械结构在长期使用过程中可能出现的疲劳破坏问题,确保机械设备的寿命和可靠性。
在机械结构设计中,刚度和强度的分析是紧密相关的。
一方面,刚度的优化可以提高结构的强度,因为刚度较高的结构在受力时会产生较小的应力。
另一方面,强度的保证可以提高结构的刚度,因为强度较高的结构在受力时会产生较小的变形。
因此,机械工程师在设计机械结构时需要综合考虑刚度和强度的要求,进行合理的优化和权衡。
在实际应用中,刚度与强度分析在机械工程和制造领域中具有广泛的应用。
例如,在航空航天领域,飞机结构的刚度与强度分析是确保飞机安全飞行的关键。
在汽车工业中,车身结构的刚度与强度分析可以提高汽车的操控性和安全性。
制造工艺中的强度与刚度分析
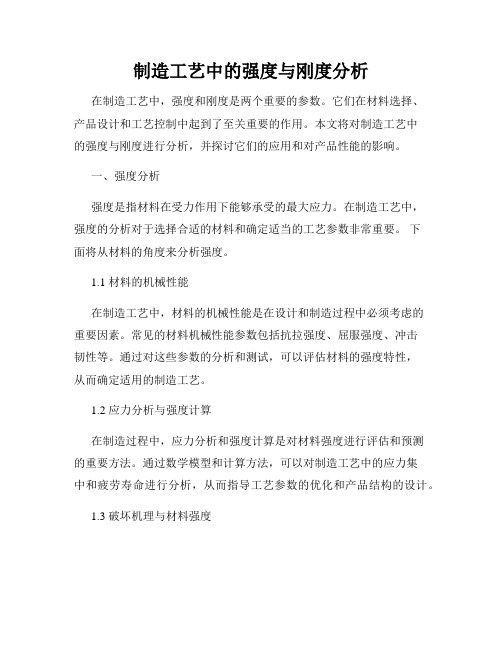
制造工艺中的强度与刚度分析在制造工艺中,强度和刚度是两个重要的参数。
它们在材料选择、产品设计和工艺控制中起到了至关重要的作用。
本文将对制造工艺中的强度与刚度进行分析,并探讨它们的应用和对产品性能的影响。
一、强度分析强度是指材料在受力作用下能够承受的最大应力。
在制造工艺中,强度的分析对于选择合适的材料和确定适当的工艺参数非常重要。
下面将从材料的角度来分析强度。
1.1 材料的机械性能在制造工艺中,材料的机械性能是在设计和制造过程中必须考虑的重要因素。
常见的材料机械性能参数包括抗拉强度、屈服强度、冲击韧性等。
通过对这些参数的分析和测试,可以评估材料的强度特性,从而确定适用的制造工艺。
1.2 应力分析与强度计算在制造过程中,应力分析和强度计算是对材料强度进行评估和预测的重要方法。
通过数学模型和计算方法,可以对制造工艺中的应力集中和疲劳寿命进行分析,从而指导工艺参数的优化和产品结构的设计。
1.3 破坏机理与材料强度破坏机理是指材料在外力作用下发生破坏的方式和原因。
对于不同的材料,破坏机理可能存在差异。
了解和分析破坏机理可以帮助制造过程中选择合适的材料和技术,并提高产品的强度。
二、刚度分析刚度是指材料或结构在受力作用下抵抗形变的能力。
在制造工艺中,刚度的分析对于产品的设计和性能评估起着关键作用。
下面将从结构的角度来分析刚度。
2.1 结构刚度的影响因素在制造工艺中,结构的刚度受到多种因素的影响,包括材料的刚性、结构的几何形式、连接方式等。
通过对这些因素的分析,可以了解结构的变形特性,进而优化工艺参数和设计结构。
2.2 建模与分析方法在制造工艺中,建模与分析方法可以帮助我们预测和评估产品的刚度性能。
常用的建模方法包括有限元分析和力学模型,可以通过这些方法模拟和计算结构在受力作用下的形变和应力分布,从而指导工艺选择和设计改进。
2.3 优化设计与刚度控制优化设计和刚度控制可以在制造工艺中提高产品的刚度性能。
通过结构参数和材料的选择,可以达到一定的刚度要求。
强度与刚度相互关系的深入解析

强度与刚度相互关系的深入解析在物理学和工程学中,强度和刚度是两个重要的概念。
它们在材料的性能和结构设计中起着关键的作用。
强度通常指的是材料的抗拉、抗压或抗剪能力,而刚度则是指材料在受力下的变形程度。
强度和刚度之间存在着密切的相互关系,它们互相影响,并在材料的选择和设计中需要进行综合考虑。
首先,我们来看一下强度和刚度的定义和计算方法。
强度通常用于描述材料在受力下的破坏能力。
常见的强度指标有抗拉强度、抗压强度和剪切强度。
抗拉强度是指材料在拉伸载荷下断裂前的最大承受能力。
抗压强度是指材料在受到压缩载荷时的最大承受能力。
剪切强度是指材料在受到剪切载荷时的最大承受能力。
这些强度指标可以通过实验测试或理论计算得到。
刚度则是指材料在受力下的变形程度。
常见的刚度指标有弹性模量和剪切模量。
弹性模量是指材料在受力下的弹性变形程度,它反映了材料的刚度。
剪切模量则是指材料在受到剪切力时的变形程度。
刚度指标可以通过实验测试或理论计算得到。
强度和刚度之间存在着密切的相互关系。
一般来说,材料的强度越高,其刚度也会相应增加。
这是因为强度和刚度都与材料的分子结构和原子间的相互作用力有关。
例如,金属材料通常具有较高的强度和刚度,这是因为金属原子之间的金属键强度较高。
相反,塑料材料通常具有较低的强度和刚度,这是因为塑料分子之间的相互作用力较弱。
然而,并不是所有情况下强度和刚度都呈正相关。
在某些情况下,材料的强度可能很高,但其刚度较低。
这是因为材料的强度主要取决于其原子间的结合能力,而刚度则主要取决于材料的分子结构和排列方式。
例如,玻璃材料具有较高的强度,但其刚度较低。
这是因为玻璃的分子结构是无序的,没有明确的晶体结构。
此外,强度和刚度还受到其他因素的影响,如温度、湿度和加载速率等。
在高温下,材料的强度和刚度通常会下降,这是因为高温会破坏材料的分子结构。
湿度也会对材料的强度和刚度产生影响,特别是对于纤维材料和木材等吸湿性材料来说。
此外,加载速率也会影响材料的强度和刚度。
机械结构的刚度与强度分析

机械结构的刚度与强度分析在机械结构设计中,刚度和强度是两个非常重要的指标。
刚度可以理解为结构在受力时的变形程度,而强度则表示结构在受力时的承载能力。
在进行机械结构设计时,合理地进行刚度和强度分析对于确保结构的性能和安全至关重要。
首先,我们来讨论机械结构的刚度分析。
刚度是描述结构受力变形的能力,是指结构对外界施加的力的抵抗能力。
合理地分析机械结构的刚度,有助于避免因结构刚度不足导致的变形过大、功能失效等问题。
在进行刚度分析时,常用的方法有有限元方法和基于经验公式的分析。
有限元方法通常能够提供更为准确的结果,但其计算较为复杂。
而基于经验公式的分析则更为简便,适用于一些简单结构或者进行初步估算。
其次,我们来探讨机械结构的强度分析。
强度是描述结构对外界施加的力的承载能力,是结构在受力时不发生破坏的能力。
合理地进行强度分析可以保证结构在使用过程中不会出现材料的破坏或失效。
在进行强度分析时,需要考虑材料强度、应力分布、载荷大小等因素。
常用的强度分析方法有静力学分析、模态分析等。
静力学分析可分析结构在静态载荷下的响应情况,而模态分析则可用于分析结构在动态载荷下的响应情况。
针对机械结构的刚度和强度分析,我们还需考虑结构的材料选择、设计优化等因素。
材料的选择应根据结构的性能要求,选择合适的材料以确保结构的刚度和强度。
而在进行结构设计优化时,需要结合刚度和强度的要求,寻找最佳设计方案,以提高结构的性能和安全性。
此外,在进行刚度和强度分析时,也需考虑结构的固有频率及共振等问题。
固有频率是指结构在受力后自身固有振动的频率,共振是指结构在外界激励作用下与其固有频率相吻合时发生的振动现象。
合理地考虑固有频率和共振问题,能够避免结构的振动导致失稳、疲劳等问题。
综上所述,机械结构的刚度与强度分析在设计过程中具有重要的地位。
通过合理地进行刚度和强度分析,可确保结构在使用过程中具有较好的性能和安全性。
同时,还需考虑结构的固有频率和共振问题,以避免振动导致的不稳定及疲劳等问题。
机械设计中的强度与刚度分析

机械设计中的强度与刚度分析在机械设计中,强度和刚度是两个重要的概念。
强度指的是材料或结构在承受外部力作用下不发生破坏的能力,而刚度则是指材料或结构在受力时的变形程度。
强度和刚度分析是机械设计中不可或缺的步骤,它们对于确保产品的可靠性和安全性起着至关重要的作用。
一、强度分析强度分析主要是对材料或结构在受力情况下的承载能力进行评估。
在机械设计中,强度分析常常涉及到材料的抗拉、抗压、抗弯等性能。
通过对材料的强度进行分析,可以确定产品是否满足设计要求,是否能够承受预期的工作载荷。
在强度分析中,常用的方法包括理论计算和有限元分析。
理论计算是通过应力和变形的理论公式进行计算,可以快速得到初步的结果。
而有限元分析则是通过将结构离散为有限个小单元,利用计算机进行数值模拟,得到更加精确的结果。
无论采用哪种方法,都需要根据具体的受力情况和材料性能进行合理的假设和参数选择。
强度分析还需要考虑到材料的疲劳寿命。
在实际使用中,材料会受到循环载荷的作用,长时间的循环载荷会导致材料的疲劳破坏。
因此,在强度分析中需要考虑到材料的疲劳寿命,以确保产品在使用寿命内不会发生疲劳破坏。
二、刚度分析刚度分析主要是对材料或结构在受力情况下的变形程度进行评估。
在机械设计中,刚度分析常常涉及到材料或结构的弹性变形。
通过对材料或结构的刚度进行分析,可以确定产品在受力情况下的变形程度,从而保证产品的工作性能和精度。
刚度分析需要考虑到材料的弹性模量和几何形状等因素。
弹性模量是描述材料抵抗变形的能力的物理量,不同材料具有不同的弹性模量。
几何形状则决定了材料或结构在受力时的变形程度,不同形状的结构会有不同的刚度。
刚度分析还需要考虑到材料或结构的稳定性。
在受到外部力作用时,材料或结构可能会发生失稳现象,导致变形超过可接受范围。
因此,在刚度分析中需要考虑到稳定性的影响,以确保产品在受力情况下不会失去稳定性。
三、强度与刚度的关系强度和刚度在机械设计中是密切相关的。
- 1、下载文档前请自行甄别文档内容的完整性,平台不提供额外的编辑、内容补充、找答案等附加服务。
- 2、"仅部分预览"的文档,不可在线预览部分如存在完整性等问题,可反馈申请退款(可完整预览的文档不适用该条件!)。
- 3、如文档侵犯您的权益,请联系客服反馈,我们会尽快为您处理(人工客服工作时间:9:00-18:30)。
一、常规机械强度设计 设计四个螺栓的直径
一、常规机械强度设计
1.受力分析
一、常规机械强度设计
2.计算内力: 由 Q=QP+KCF 及下图得总拉力Q=3962N
一、常规机械强度设计
3.确定尺寸:
根据许用应力和安全系数可的危险剖面的 直径d≥9.054mm 因此,选用M12的螺栓。
一、常规机械强度设计
2.弹塑性强度理论
变形分析
应力状态分析 (弹性极限状态、弹塑性状 态、塑形极限状态)
各状态的 极限载荷
2.弹塑性强度理论
特点:
1)基本假设:除理想弹性这一点外, 其余同弹性力学。即平衡方程、几 何方程均相同 2)应力应变之间的关系是非线性的, 其非线性性质与具体材料有关
2.弹塑性强度理论
特点:
二、现代机械强度设计
设计步骤: 1.根据常规设计方法,初步确定结构形状及 尺寸; 2.应用有限元法分析应力、应变分布; 3.用声、光、电等检测手段,确定零构件缺 陷尺寸和位置; 4.对于无缺陷材料,计算服役寿命=裂纹形成 寿命+裂纹扩展寿命; 5.对于有缺陷材料,用断裂力学方法计算裂 纹扩展寿命。
案例分析——装载机前车架 前车架
案例分析——装载机前车架
1.受力分析 (1)扭转工况:车架上的载荷作用点离对称轴有偏 距,相当于加以极限扭矩,使车架产生扭转。 (2)弯曲工况:最大载荷作用在对称轴上,沿铅垂 方向产生偏载,使车架处于弯曲工况状态。 (3)弯扭联合工况:将弯曲工况和扭转工况组合在 一起即为弯扭工况。车架受载最为严重的工况 是弯曲工况和弯扭联合工况,与车架结构强度 及刚度直接有关的亦主要是这2种工况。在车 架的载荷计算工况中,车架所受的最大载荷是 最大牵引力,为158kN,最大掘起力为 210.9kN。
1.应力强度因子是裂纹尖端应力应变场强 度的度量; 2.应力强度因子是裂纹尖端应力应变场具 有奇异性的度量; 3.应力强度因子的临界值是材料本身的固 有属性。
4.疲劳强度理论
设计准则: 1.无限寿命设计:对疲劳强度要求高。钢轨、桥梁、 车轴等的设计。
1
有限寿命区
应力只要不超过 1 ,则N可无限增 大
一、常规机械强度设计
存在的问题: 1.应力的多轴性和变形的弹塑性; 2.疲劳破坏的普遍性; 3.疲劳与蠕变的交互作用; 4.强度中的寿命计算; 5.疲劳强度可靠性; 6.局部应力应变分析; 7.断裂力学
二、现代机械强度设计
理论:
1.应力应变分析方法及线弹性强度理论 2.弹塑性强度理论 3.含裂纹体的强度理论 4.疲劳强度理论
1.应力应变分析方法及线弹性强度理论
弹性力学 基本方程
一点处的 应力应变
方程求解: 解析法、 有限元法
主应力 主平面
坐标变换 强度准则
设计计算
1.应力应变分析方法及线弹性强度理论
特点:
考虑了材料的线弹性变形,即应力应变是 线性关系,运用弹性力学、形变能理论、 最大剪应力理论等确定主应力和主平面, 能较好的解决复杂应力的问题。
强度与刚度设计
定义
强度:材料或零构件抵抗外力而不发生失效 的能力。
定义ቤተ መጻሕፍቲ ባይዱ
刚度:材料在受力时抵抗弹性变形的能力。
强度设计
常规 强度设计
现代 强度设计
一、常规机械强度设计
理论:
一、常规机械强度设计
设计步骤: (1)由理论力学确定零构件所受外力; (2)由材料力学(有时采用弹性力学或塑性力学)计算其 内力; (3)由机械原理和机械零件确定其结构尺寸和形状; (4)计算该零构件的工作应力或安全系数。
4.校核 (1)联接结合面下端的挤压应力 σpmax=1.267MPa<[σp] 联接结合面下端不致压溃。 (2)联接结合面上端的残余应力 σpmin=0.114MPa>0 即联接结合面上端受压处不会产生缝隙
一、常规机械强度设计
特点:
1.假设制造机械零构件的材料性能是均匀的、 各向同性的、连续的实体; 2.承受较为简单的载荷作用; 3.应用弹性变形理论。
案例分析——装载机前车架
案例分析——装载机前车架
轮式装载机的车架由前车架和后车架组成。前 车架是装载机的基础承载构件,是车架的主要承 载体;后车架为箱形结构,受力较小。因此,这 里只计算前车架的强度及刚度。 前车架是由薄钢板焊接而成的三维空间结构, 形状较为复杂,用常规的力学方法无法对其进行 精确计算。为此,这里采用现代强度及刚度设计 方法。该车架采用四板组焊的焊接工艺。车架为 左右对称结构,有一纵向对称轴。其上作用有掘 起力、铲入力。由结构的对称性,可取结构的一 半进行强度及刚度的计算与分析。
案例分析——装载机前车架
2.有限元法:对结构进行网格划分
案例分析——装载机前车架
3.约束条件
在上述3种载荷计算工况下,约束部位为车 架内各铰孔及车架底部与前桥的联接部位, 各铰孔内结点的x方向、y方向、z方向位 移均被限制为零。底部联接部位沿纵向 (z方向)位移及横向(y方向)位移为零。
3)应力与应变之间没有一一对应的关系,它 与加载历史有关——不惟一性; 4)在变形体中存在弹性变形区和塑性变形区, 因而在求解问题时,需要找出弹性区和塑 性区的分界线(屈服准则);
2.弹塑性强度理论
特点:
5)在分析问题时,需要区分是加载过程还是 卸载过程。在加载过程中,使用塑性的应 力应变关系方程;在卸载过程中,使用广 义胡克定律。
无限寿命区
4.疲劳强度理论
设计准则: 2.安全寿命设计(有限寿命设计):要求零部件或结 构在给定的使用周期内不能产生任何疲劳缺陷。 常用于飞机、汽车、压力容器等的设计中。
1N
有限寿命区
无限寿命区
4.疲劳强度理论
设计准则: 3.破损-安全设计:承认裂纹可以出现,但在被检测 和维修之前,不会导致整个结构的破坏。(避免 因安全系数造成重量过大,例如在航空工业) 4.损伤-容限设计:假设裂纹预先存在,用断裂力学 方法分析其寿命。是3的进一步改进。
3.含裂纹体的强度理论
确定结构及受力 应力强度因子K 判断是否处于裂纹 的稳定扩展阶段 G准则 K准则 确定Paris公式中 的各项系数 由最大应力求出临 界裂纹尺寸a
求裂纹扩展寿命
Paris公式用于研究裂纹扩展速率,作为设计选材时的 参考,以及计算裂纹体的剩余寿命。
3.含裂纹体的强度理论
应力强度因子的特性: