典型液压传动系统实例分析
液压系统设计计算实例

12.13,液压缸的工况图如图12.8所示。
➢ 设计内容与方法
4.拟定液压系统原理图
➢ 设计内容与方法 5.液压元件选择
(1)选择液压泵 ①液压泵最高工作压力 管路总压力损失ΣΔp初步按
0.6MPa估算,有Pp≥pmax+ΣΔp=(4.5+0.6)MPa=5.1MPa ②液压泵最大供油量 取K=1.1,有
➢ 设计内容与方法
3.液压缸参数确定
(5) 采最用低无稳杆定腔速进度油验,算单向最行低程速调度速为阀工调进速时,vm查in=得5最0m小m稳/m定in流,量工进时,
qmin=0.1×10-3m3/min,则
A1≥ qmin 0.1106
vm in
ቤተ መጻሕፍቲ ባይዱ
50
mm2=2 000mm2 满足最低速度要求。
(6) 绘制液压缸工况图 计算各工况下的压力、流量和功率汇总于表
液压与气动控制
F 33667 p 4.5106
4A 4 7482106
3.14
➢ 设计内容与方法
3.液压缸参数确定
( (12) )选 确4 定 定工 液作 压4压 缸力 有效p 工根作据面表积1A2.3和表12.4,初选工作压力p=4.5MPa。
4
4
A= 4 m24=7 482×10-6m2
(3)确定缸筒内径D、活塞杆直径d
➢ 设计内容与方法 5.液压元件选择
①油管 初步选取v=4m/s,则d=m=14.5×103m=14.5mm 查手册确定采用φ18×1.5的紫铜管。 ②滤油器 采用XU-J40×80型过滤器。 ③油箱容积的确定 V=(5~7)qP=(5~7)×20L=(100~140)L
➢ 设计内容与方法
液压传动系统实例及液压系统的组成
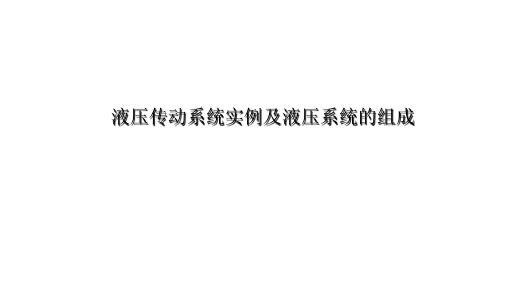
5、由于一般采用油作为传动介质,因此 液压元件有自我润滑作用,有较长的使用寿命。
6、液压元件都是标准化、系列化的产品,便于设计、制造和推广应用。
缺点:
1、损失大、效率低、发热大。
2、不能得到定比传动。
3、当采用油作为传动介质时还需要注意防火问题。
Байду номын сангаас
4、液压元件加工精度要求高,造价高。
5、液压系统的故障比较难查找,对操作人员的技术水平要求高。
液压传动系统实例及液压系统的组成
一、液压千斤顶 二、液压图形符号
三、液压系统的组成
一、液压千斤顶
液压千斤顶原理见下图。当向下压杠杆1时,小活塞3使缸2内的液体经管道6、阀7进 入大缸9,并使活塞8上升,顶起重物W。适当地选择大、小活塞面积和杠杆比,就可以人 力升起很重的负载W。
图1-2
液压千斤顶原理图
其作用是将液压能重新转化成机
如各种阀。其中有方向阀和压力 阀两种。
械能,克服负载,带动机器完成所需的运动。
如油箱、油管、滤油器等。 即液体。
液压传动的优缺点
优点: 1、可以在运行过程中实现大范围的无机调速。 2、在同等输出功率下,液压传动装置的体积小、重量轻、运动惯量小、动态性能好。
3、采用液压传动可实现无间隙传动,运动平稳。 4、便于实现自动工作循环和自动过载保护。
二、液压图形符号
下图为机床工作台液压系统的图形符号图
机床工作台液压系统的图形符号图
-油箱 -滤油器 -液压泵 -溢 流阀 -开停阀 -换向阀 -活塞 液压缸 -工作台
三、液压系统的组成
1、动力元件 2、执行元件 3、控制元件 4、辅助元件 5、传动介质
即液压泵,它可将机械能转化成液压能,是一个能量转化装置。
液压基本回路及系统应用实例

采用二位四通电磁换向阀的换向回路
采用三位四通手动换向阀的换向回路
2.锁紧回路
采用O型中位机能三位四通电磁换向阀的锁紧回路
利用压力控制阀来调节系统或系统某一部分的压力 的回路。压力控制回路可以实现调压、减压、增压、卸 荷等功能。 1.调压回路 2.减压回路 3.增压回路 4.卸荷回路
二、数控车床液压系统
图14-77 -
本章小结
1.液压系统的基本原理和液压传动系统的组成。 2.液压系统的流量和压力的有关概念和相关计算。 3.液压泵的类型及工作原理。 4.液压缸的常见类型及特点,运动速度及输出推力的 计算,结构上的特点。 5.液压控制阀的功用、种类、工作原理及特点。 6.液压辅助元件的种类及其工作原理、特点。 7.方向控制回路中换向回路和锁紧回路的应用,简单 的方向控制回路。 8.压力控制回路中调压、减压、增压、卸荷等功能的 应用,简单的方向控制回路。
进油节流调速回路
将节流阀串联在液压泵与液压缸之间。 泵输出的油液一部分经 节流阀进入液压缸的工作腔, 泵多余的油液经溢流阀流回 油箱。由于溢流阀有溢流, 泵的出口压力pB保持恒定。 调节节流阀通流截面积,即 可改变通过节流阀的流量, 从而调节液压缸的运动速度。
回油节流调速回路
将节流阀串接在液压缸与油箱之间。 调节节流阀流通面积, 可以改变从液压缸流回油箱 的流量,从而调节液压缸运 动速度。
液压缸差动连接速度换接回路
利用液压缸差动连接获得快速运动的回路。
液压缸差动连接时,当相同流量 进入液压缸时,其速度提高。图示用 一个二位三通电磁换向阀来控制快慢 速度的转换。
短接流量阀速度换接回路
采用短接流量阀获得快慢速运动的回路 。 图示为二位二通电磁换向阀 左位工作,回路回油节流,液压 缸慢速向左运动。当二位二通电 磁 换向阀右位工作时(电磁铁通 电),流量阀(调速阀)被短接, 回油直接流回油箱,速度由慢速 转换为快速。二位四通电磁换向 阀用于实现液压缸运动方向的转 换。
8典型的液压与气压传动系统

北京科技大学
(5)原位停
止
上滑块返回, 碰到挡块压下行程 开关后,行程开关 发出信号,电磁铁 2YA失电,先导阀和 上、下换向阀都处 于中位,上滑块原 位停止不动。液压 泵处于卸荷状态。 油路:
液压泵 顺 序阀10 上缸换 向阀7中位 下缸 换向阀2中位 油 箱。
北京科技大学
2、下滑块工作循环
回油路: 液压缸7右腔 液动换向阀12左位 液控顺序阀2 背压阀1 油箱。 特点: 系统压力升高,限压式变量泵流量减小, 直到与调速阀4设定的流量相等;进入液 压缸无杆腔的流量由调速阀决定;液控顺 序阀2被打开,液压缸右腔的油液经液控 顺序阀2 背压阀1流回油箱。
北京科技大学
3、二工进
行程挡铁压下行程开关,发出电信号, 电磁铁3YA 得电。 进油路: 过滤器 变量泵14 单向阀13 液动换向阀12左位 调速阀4 调速 阀10 液压缸7左腔。 回油路: 液压缸7右腔 液动换向阀12左位 液控顺序阀2 背压阀1 油箱。 特点
北京科技大学
(2)慢速
加压
液控单向阀I1 关闭,液压缸 上腔压力升高, 实现慢速加压。 主油路走向与 上一阶段相同。
北京科技大学
(3)保压延时
液压缸上腔压力继 续升高,压力继电 器8动作,发出电 信号,电磁铁1YA 失电,先导阀3和 换向阀7换到中位, 保压开始。保压时 间由时间继电器 (图中未画出)控 制。 特点:
北京科技大学
四、液压系统工作原理 北京科技大学
五、液压系统的工作过程如下:
1、快进 电磁铁1YA得电 进油路: 过滤器 液压泵14 单向阀13 液动换向阀12左位 行程阀(机动换 向阀)8(接通) 液压缸7左腔。 回油路: 液压缸7右腔 液动换向阀12左位 单向阀3 行程阀8 液压缸7左腔。
液压与气动技术——液压系统实例分析

• • ①进油路:液压泵→精滤油器→先导阀7、
9→ • ②回油路:右抖动缸→先导阀8、14→油箱。
• 主换向阀的控制油路为: • ①进油路:液压泵→精滤油器→先导阀7、
9→单向阀I2→主换向阀右端;
• ②回油路:主换向阀左端→先导阀8、14→ 油箱。
• 2)端点停留阶段 • • • ②回油路:换向阀左端→节流阀L1→先导阀
• ②回油路:液压缸右腔→液控换向阀(左 位)→液控顺序阀6→背压阀5→
• (3)第二次工作进给
• ①进油路:变量泵1→单向阀2→液控换向 阀3(左位)→调速阀8→调速阀→9液压缸 左腔;
•② • (4 • 当滑台第二次工作进给终了碰到死挡铁时,
滑台停止前进。这时,液压缸左腔油压力 进一步升高,使压力继电器12动作,发出 电信号给时间继电器,其停留时间由时间 继电器控制。设置死挡铁,可以提高滑台 停留时的位置精度。
如发现导轨润滑油过多会使工作台产生浮动而影响运动精度或过少会使工作台产生低速爬行现象一般油量过多则首先检查润滑油压力是否过高必要时可降低压力再调节节流阀l油量过少则应考虑润滑油压力是否过低可先升高压力再调节流将砂轮架底座前端的定位螺钉旋出使砂轮架快速前进至最前端千分表磁性表座固定在工作台上表头触及砂轮架得出某一读数
图8.1 1—泵;2—单向阀;3、4—电磁换向阀;5—背压阀;6— 7、13—单向阀;8、9—调速阀;10—电磁换向阀;11—行程阀;12—压力继电器
• 8.2.2 动力滑台液压系统工作原理
• (1)快进 •1 • ①进油路:变量泵1→电磁换向阀4(左位)
→单向阀I1 →液控换向阀3(左端); • ②回油路:液控换向阀3(右端)→节流阀
• (2
•
液压传动案例
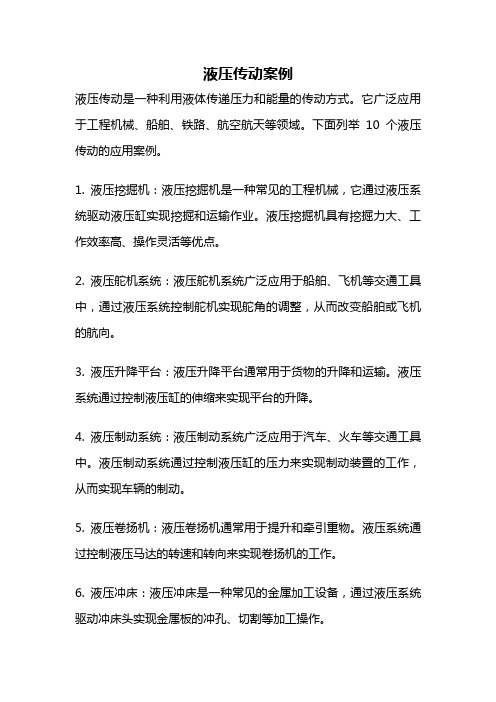
液压传动案例液压传动是一种利用液体传递压力和能量的传动方式。
它广泛应用于工程机械、船舶、铁路、航空航天等领域。
下面列举10个液压传动的应用案例。
1. 液压挖掘机:液压挖掘机是一种常见的工程机械,它通过液压系统驱动液压缸实现挖掘和运输作业。
液压挖掘机具有挖掘力大、工作效率高、操作灵活等优点。
2. 液压舵机系统:液压舵机系统广泛应用于船舶、飞机等交通工具中,通过液压系统控制舵机实现舵角的调整,从而改变船舶或飞机的航向。
3. 液压升降平台:液压升降平台通常用于货物的升降和运输。
液压系统通过控制液压缸的伸缩来实现平台的升降。
4. 液压制动系统:液压制动系统广泛应用于汽车、火车等交通工具中。
液压制动系统通过控制液压缸的压力来实现制动装置的工作,从而实现车辆的制动。
5. 液压卷扬机:液压卷扬机通常用于提升和牵引重物。
液压系统通过控制液压马达的转速和转向来实现卷扬机的工作。
6. 液压冲床:液压冲床是一种常见的金属加工设备,通过液压系统驱动冲床头实现金属板的冲孔、切割等加工操作。
7. 液压起重机:液压起重机是一种常见的起重设备,通过液压系统驱动液压缸实现起重和运输作业。
液压起重机具有起重力大、操作灵活等优点。
8. 液压剪切机:液压剪切机通常用于对金属板材进行剪切和切割。
液压系统通过控制液压缸的压力和位置来实现剪切机的工作。
9. 液压输送机:液压输送机是一种用于输送散状物料的设备,通过液压系统驱动输送带或滚筒实现物料的输送。
10. 液压缸:液压缸是液压传动的核心部件,广泛应用于各种机械设备中。
液压缸通过液压系统提供的压力驱动活塞运动,实现机械设备的工作。
以上是液压传动的一些应用案例,涵盖了工程机械、船舶、交通工具等各个领域。
液压传动具有传动力大、速度可调、操作灵活等优点,因此在工程装备和机械设备中得到了广泛应用。
液压与气压传动液压系统设计实例
根据系统的工作环境和要求,选择合适的液压介质,如矿 物油、合成油、水等,并确定其清洁度和粘度等参数。
选择合适元件和连接方式
01
选择液压泵和液压马达
根据系统的负载和运动参数,选择合适的液压泵和液压马达,确保其能
够提供足够的流量和压力,并满足系统的效率和精度要求。
02
选择液压缸和阀门
其他常见问题及相应解决方案
气穴现象
产生原因是油液中溶解的气体在低压区析出并形成气泡。解决方案 是减小吸油管路的阻力,避免产生局部低压区。
压力冲击
产生原因是液压阀突然关闭或换向,导致系统内压力急剧变化。解 决方案是在液压阀前设置蓄能器或缓冲装置,吸收压力冲击。
爬行现象
产生原因是液压缸或马达摩擦阻力不均、油液污染等。解决方案是改 善液压缸或马达的润滑条件,使用干净的油液。
关键技术应用
节能环保措施
采用负载敏感技术、电液比例控制技术等 ,提高挖掘机液压系统的控制精度和响应 速度。
通过优化系统设计和选用高效节能元件,降 低挖掘机液压系统的能耗和排放,提高环保 性能。
压力机液压系统性能评估方法论述
评估方法介绍
采用实验测试、仿真分析等方法对压力机 液压系统进行性能评估,获取系统在不同
明确系统的设计目标和约束条件
根据实际需求,明确系统的设计目标,如高效率、 低能耗、高精度等,并考虑成本、空间、重量等 约束条件。
确定系统方案和布局
制定系统原理图
根据设计要求和目标,制定液压系统的原理图,包括液压 缸、液压马达、液压泵、油箱、阀门等元件的连接方式和 控制逻辑。
确定系统布局和安装方式
根据机械设备的结构和空间要求,确定液压系统的布局和 安装方式,包括元件的布置、管路的走向和固定方式等。
典型液压传动系统应用实例
根据工作循环和动作要求,参照电磁铁动作顺序表弄清液流路线,读懂液压系统图。
进油路:泵1-阀6中位 3Y得电,阀21 处于左位。
综合归纳以上的分析,总结系统在性能、操作、环境、安全等方面的要求和特点,达到对系统工作原理和性能的全面清晰的理解
-阀21左位-下缸下腔。 下缸上腔则经阀21中位从油箱补油。
主缸滑块在自重作用下 迅速下降,泵1 虽处于 最大流量状态,仍不能 满足其需要,因此主缸 上腔形成负压,上位油 箱15 的油液经充液阀14 进入主缸上腔。
3) 主缸慢速接近工件、加压
当主缸滑块降至一定位置触 动行程开关2S 后,5Y 失电, 阀9 关闭,主缸下腔油液经 背压阀10、阀6 右位、阀21 中位回油箱。这时,主缸上 腔压力升高,阀14 关闭,主 缸在泵1 供给的压力油作用 下慢速接近工件。接触工件 后阻力急剧增加,压力进一 步提高,泵1 的输出流量自过程 飞机轮部的液压系统
目的和任务
目的
通过对典型液压系统的分析,进一步加深对各种液压 元件和基本回路综合运用的认识。
任务
了解设备的功用和液压系统工作循环、动作要求。 根据工作循环和动作要求,参照电磁铁动作顺序表弄 清液流路线,读懂液压系统图。 了解系统由哪几种基本回路组成,各液压元件的功用 和相互的关系,液压系统的特点。
飞机轮部的液压系统
一 液压系统工作原理
1) 启动 电磁铁全部不得电,主泵输出油
液通过阀6、21中位卸载。 2)主缸快速下行 电磁铁1Y、5Y 得电,阀6 处于右
位,控制油经阀8 使液控单向阀9 开启
进油路:泵1-阀6右位-阀13 -主缸上腔。
回油路:主缸下腔-阀9- 阀6右位-阀21中位-油箱
分析系统对各分系统之间动作的顺序、联动、互锁、同步、抗干扰 等方面的要求和实现方法,理解各分系统是如何组成整个系统的。
液压与气压传动8-2 典型液压系统实例
一、概述
液压机是用来对金属、木材、塑料等进行压力加工的机械,也是最 早应用液压传动的机械之一。目前液压传动己成为压力加工机械的主 要传动形式。液压机传动系统是以压力变换为主的系统由于用在主传 动,系统压力高,流量大,功率大,因此特别要注意提高原动机功率利用率, 须防止泄压时产生冲击。
二、工况特点及对液压系统的要求
主机动作要求:液压机根据其工作循环要求有快进、减速接近工件、加压、 保压延时、泄压、快速回程及保持(即活塞)停留在行程的任意位置等基 本动作,图8-3为液压机典型工作塞前进、停止和退回等动作。
《液压与气压传动》第8章 典型液压传动系统
四、液压系统的特点 1. 液压系统中各部分相互独立,可根据需要使任一部分单独动作,也可 在执行元件不满载时,各串联的执行元件任意组合地同时动作。 2. 支腿回路中采用双向液压锁6,将前后支腿锁定在一定位置,防止出 现“软腿”现象或支腿自由下落现象。 3. 起升回路、吊臂伸缩、变幅回路均设置平衡阀,以防止重物在自重 作用下下滑。 4.为了防止由于马达泄漏而产生的“溜车”现象,起升液压马达上设有 制动阀,并且松阀用液压力,上阀用弹簧力,以保持在突然失去动力时液压 马达仍能锁住,确保安全。
《液压与气压传动》第8章 典型液压传动系统
四、 YA32-315型四柱万能液压机液压系统特点 1. 采用高压大流量恒功率变量泵供油,既符合工艺要求,又节省能量,这是
压机液压系统的一个特点; 2.本压机利用活塞滑块自重的作用实现快速下行,并用充液阀对主缸充液。
这一系统结构简单,液压元件少,在中、小型液压机是一种常用的方 案;
《液压与气压传动》第8章 典型液压传动系统
4DT
10 9
7
1DT
液压传动原理及几种典型应用
液压传动原理及⼏种典型应⽤简单机床液压传动系统的⼯作过程,就是液压传动系统传动⼯作原理的真实写照。
下⾯以机床液压传动系统和液压千⽄顶为例来说明液压传动的⼯作原理实例1液压千⽄顶的⼯作原理1-杠杆⼿柄2-⼩缸体3-⼩活塞4、7-单向阀5-吸油管6、10-管道8-⼤活塞9-⼤缸体11-截⽌阀12-通⼤⽓式油箱如图1.2-1所⽰,⼤缸体9和⼤活塞8组成举升液压缸。
杠杆⼿柄1、⼩缸体2、⼩活塞3、单向阀4和7组成⼿动液压泵⼯作原理:(1)如提起⼿柄使⼩活塞向上移动,⼩活塞下端油腔容积增⼤,形成局部真空,这是单向阀4打开,通过吸油管5从油箱12中吸油;(2)⽤⼒压下⼿柄,⼩活塞下移,⼩缸体下腔的压⼒升⾼,单向阀4关闭,单向阀7打开,⼩缸体下腔的油液经管道6输⼊⼤缸体9的下腔,迫使⼤活塞8向上移动,顶起重物。
(3)再次提起⼿柄吸油时,举升缸的下腔的压⼒油将⼒图倒流⼊⼿动泵内,但此时单向阀7⾃动关闭,使油液不能倒流,从⽽保证了重物不会⾃⾏下落。
不断地往复扳动⼿柄,就能不断地把油液压⼊举升缸的下腔,使重物逐渐地升起。
机械公社(4)如果打开截⽌阀11,举升缸的下腔的油液通过管道10、截⽌阀11流回油箱,⼤活塞在重物和⾃重作⽤下向下移动,回到原始位置。
对液压传动⼯作过程的分析结论:» ⼒的传递遵循帕斯卡原理» 运动的传递遵照容积变化相等的原则» 压⼒和流量是液压传动中的两个最基本的参数» 液压传动系统的⼯作压⼒取决于负载;液压缸的运动速度取决于流量» 传动必须在密封容器内进⾏,⽽且容积要发⽣变化» 传动过程中必须经过两次能量转换实例2磨床⼯作台⼯作原理1-油箱 2-过滤器 3、12、14-回油管 4-液压泵 5-弹簧 6-钢球 7-溢流阀 8-压⼒⽀管 9-开停阀 10-压⼒管 11-开停⼿柄 13-节流阀 15-换向阀 16-换向阀⼿柄 17-活塞 18-液压缸 19-⼯作台⼯作原理:(1)如图1.2-2,液压泵4在电动机(图中未画出)的带动下旋转,油液由油箱1经过滤器2被吸⼊液压泵,⼜液压泵输⼊的压⼒油通过⼿动换向阀11,节流阀13、换向阀15进⼊液压缸18的左腔,推动活塞17和⼯作台19向右移动,液压缸18右腔的油液经换向阀15排回油箱。
- 1、下载文档前请自行甄别文档内容的完整性,平台不提供额外的编辑、内容补充、找答案等附加服务。
- 2、"仅部分预览"的文档,不可在线预览部分如存在完整性等问题,可反馈申请退款(可完整预览的文档不适用该条件!)。
- 3、如文档侵犯您的权益,请联系客服反馈,我们会尽快为您处理(人工客服工作时间:9:00-18:30)。
第四章典型液压传动系统实例分析第一节液压系统的型式及其评价一、液压系统的型式通常可以把液压系统分成以下几种不同的型式。
1.按油液循环方式的不同分按油液循环方式的不同,可将液压系统分为开式系统和闭式系统。
(1)开式系统如图4.1所示,开式系统是指液压泵1从油箱5吸油,通过换向阀2给液压缸3(或液压马达)供油以驱动工作机构,液压缸3(或液压马达)的回油再经换向阀回油箱。
在泵出口处装溢流阀4。
这种系统结构较为简单。
由于系统工作完的油液回油箱,因此可以发挥油箱的散热、沉淀杂质的作用。
但因油液常与空气接触,使空气易于渗入系统,导致工作机构运动的不平稳及其它不良后果。
为了保证工作机构运动的平稳性,在系统的回油路上可设置背压阀,这将引起附加的能量损失,使油温升高。
在开式系统中,采用的液压泵为定量泵或单向变量泵,考虑到泵的自吸能力和避免产生吸空现象,对自吸能力差的液压泵,通常将其工作转速限制在额定转速的75%以内,或增设一个辅助泵进行灌注。
工作机构的换向则借助于换向阀。
换向阀换向时,除了产生液压冲击外,运动部件的惯性能将转变为热能,而使液压油的温度升高。
图4.1 开式系统但由于开式系统结构简单,因此仍为大多数工程机械所采用。
(2)闭式系统如图4.2所示。
在闭式系统中,液压泵的进油管直接与执行元件的回油管相联,工作液体在系统的管路中进行封闭循环。
闭式直系统结构较为紧凑,和空气接触机会较少,空气不易渗入系统,故传动的平稳性好。
工作机构的变速和换向靠调节泵或马达的变量机构实现,避免了在开式系统换向过程中所出现的液压冲击和能量损失。
但闭式系统较开式系统复杂,由于闭式系统工作完的油液不回油箱,油液的散热和过滤的条件较开式系统差。
为了补偿系统中的泄漏,通常需要一个小容量的补油泵进行补油和散热,因此这种系统实际上是一个半闭式系统。
一般情况下,闭式系统中的执行元件若采用双作用单活塞杆液压缸时,由于大小腔流量不等,在工作过程中,会使功率利用率下降。
所以闭式系统中的执行元件一般为液压马达。
如大型液压挖掘机、液压起重机中的回转系统,全液压压路机的行走系统与振动系统中的执行元件均为液压马达。
闭式系统中执行元件为液压马达的另一优点是在起动和制动时,其最大起动力矩和制动力矩值相等。
2.按系统中液压泵的数目分按系统中液压泵的数目可将其分为单泵系统、双泵系统和多泵系统。
(1)单泵系统由一个液压泵向一个或一组执行元件供油的液压系统,即为单泵液压系统,如图4.3所示。
单泵系统适用于不需要进行多种复合动作的工程机械,如推土机、铲运机等铲土运输机械的液压系统。
对某些工程机械如液压挖掘机、液压起重机的工作循环中,既需要实现复合动图4.2 闭式系统1-液压泵;2-液压马达;3-单向阀,4-补油泵;5-油箱作,又需要对这些动作能够进行单独调节,采用单泵系统显然是不够理想的。
为了更有效地利用发动机功率和提高工作性能,就必须采用双泵系统或多泵系统。
(2)双泵系统图4.4为双泵液压系统图。
双泵液压系统实际上是两个单泵液压系统的组合。
每台泵可以分别向各自回路中的执行元件供油。
每台泵的功率是根据各自回路中所需的功率而定,这样可以保证进行复合动作。
图4.4 双泵液压系统1-双联液压泵;2-换向阀;3-多路换向阀;4-变速阀;5-先导阀;6-行走马达;7-缓冲制动阀;8-回转马达;9-回转马达换向阀当系统中只需要进行单个动作而又要充分利用发动机功率时,可采用合流供油方式,即将两台液压泵的流量同时供给一个执行元件。
这样可使工作机构的运动速度加快。
这种双泵液压系统在中小型液压挖掘机和起重机中已被广泛采用。
(3)多泵系统为了进一步改进液压挖掘机和液压起重机的性能,近年来在大型液压挖掘机和液压起重机中,开始采用三泵系统。
图4.5为三泵液压系统原理图。
这种三泵液压系统的特点是回转机构采用独立的闭式系统,而其它两个回路为开式系统。
这样,可以按照主机的工作情况,把不同的回路组合在一起,以获得主机最佳的工作性能。
3.按所用液压泵型式的不同分按所用液压泵型式的不同,可将液压系统分为定量系统和变量系统。
(1)定量系统。
采用定量泵的液压系统,称为定量系统,如图4.3,图4.4所示。
定量系统中所用的液压泵为齿轮泵、叶片泵或柱塞泵。
液压泵的功率是按理论功率η450maxQpN=选取的。
对定量泵,当发动机转速一定时,流量Q也一定。
而压力是根据工作循环中需要克服的最大阻力确定的,因此液压系统工作时,液压泵功率是随工作阻力变化而改变的。
在一个工作循环中液压泵达到满功率的情况是非常少的。
据统计,在挖掘机中定量泵功率的平均利用率约为54~60%(图4.6)。
液压系统中液压泵的理论功率与发动机有效功率之比约为0.8~1.2。
对定量泵,其功率比值可取在l以上,但应小于发动机的功率储备,以免突然过载时造成发动机熄火而影响正常工作。
(2)变量系统变量系统中所用的液压泵为恒功率控制的轴向柱塞泵,泵的功率特性曲线如图4.7所示。
从图中可以看出,功率调节器中,控制活塞右面有压力油作用,控制活塞左面有弹簧力的作图4.5 三泵液压系统原理图图4.6 定量系统与变量系统功率利用率比较图4.7 恒功率控制变量泵的功率特性曲线用,当泵的出口压力低于弹簧装置预紧压力时,弹簧装置未被压缩,液压泵的摆角处于最大角度,此时泵的排量也为最大。
随着液压泵出口压力的增高弹簧被压缩,液压泵的摆角也就随着减小,排量也就随之减少。
液压泵在出口压力和弹簧装置预压紧力相平衡时的位置,称为调节起始位置。
调节起始位置时,作用在功率调节器中控制活塞上的液压力称为起调压力。
当液压泵的出口压力大于起调压力时,由于调节器中弹簧压缩力与其行程有近似于双曲线的变化关系,因而在转速恒定时,液压泵出口压力与流量也呈近似于双曲线的变化。
这样液压泵在调节范围之内始终保持恒功率的工作特性。
由于液压泵的工作压力是随外载荷的大小而变化的,因此,可使工作机构的速度随外载荷的增大而减小,或随外载荷的减小而增大,使发动机功率在液压泵调节范围之内得到充分利用。
变量泵的起调压力p 0是由弹簧装置的刚度和液压系统的要求决定的。
调节终了压力p max 是由液压系统决定、由安全阀调定。
相应于起调压力时的摆角为最大,相应于调节终了时的摆角为最小。
变量泵的优点是在调节范围之内,可以充分利用发动机的功率,缺点是结构和制造工艺复杂,成本高。
为了防止发动机因过载而突然熄火,一般将液压泵的理论功率与发动机有效功率之比限于0.8~l.0之间。
4.按向执行元件供油方式的不同分按向执行元件供油方式的不同,可将液压系统分为串联系统和并联系统。
(1)串联系统在系统中,当一台液压泵向一组执行元件供油时,上一个执行元件的回油即为下一个执行元件进油的液压系统称为串联系统,如图4.8。
在串联系统中,若液压泵输出的压力油以压力p l ,流量Q l 进入第一个执行元件,以压力p 2、流量Q 2进入第二个执行元件。
那么,在不考虑损失的情况下,对双作用单活塞杆液压缸,Q l ≠Q 2。
Q 1、Q 2与液压缸活塞的有效面积S l 、S 2成正比,即1212S S Q Q(4—1) 在不考虑管路和执行元件中的能量损失时,第一个执行元件中的工作压力p 1,取决于克服该执行元件上载荷所需的压力p ′和第二个执行元件的工作压力p 2,即:p 1=p ′+p 2 (4—2)这说明在串联系统中,每通过一个执行元件工作压力就要降低一次。
因此串联系统的特点是:当主泵向多路阀控制的各执行元件供油时,只要液压泵出口压力足够,便可实现各执行元件的运动的复合。
但由于执行元件的压力是叠加的,所以克服外载荷的能力图4.8 串联系统将随执行元件数量的增加而降低。
(2)并联系统并联系统是指在系统中,当一台液压泵同时向一组执行元件供油时,进入各执行元件的流量只是液压泵输出流量的一部分,如图4.9所示。
并联系统的特点是:当主泵向多路阀所控制的各执行元件供油时,流量的分配是随各执行元件上外载荷的不同而变化,压力油首先进入外载荷较小的执行元件。
只有当各执行元件上外载荷相等时,才能实现同时动作。
液压泵的出口压力取决于外载荷小的执行元件上的压力与该油路上的压力损失之和。
由于并联系统在工作过程中只需克服一次外载荷,因此克服外载荷的能力较大。
除了上述的分类以外,按调速方法图 4.9并联系统的不同,液压系统又有节流调速系统和容积调速系统之分。
这部分已在速度调节基本回路中介绍过,这里不再赘述。
二、液压系统的评价随着液压技术的发展,液压传动在国内外工程机械、机床等方面应用越来越广泛。
任何一种机械的液压传动系统都应满足重量轻、体积小、结构简单、使用方便、效率高和质量好的要求。
其中尤应强调质量好和效率高,并在保证质量好、效率高的基础上应尽可能地采用先进技术。
液压机械性能的优劣,主要是取决于液压系统性能的好坏。
而液压系统性能的好坏则又以系统中所用元件的质量好坏和所选择的基本回路恰当与否为前提。
对一个液压系统的评价,应该从液压系统的效率、功率利用、调速范围和微调特性、振动和噪声等几个方面加以分析对比。
1.液压系统的效率在保证主机性能要求的前提下,应该使液压系统具有尽可能高的效率。
液压系统效率的高低反映了液压系统中能量损失的多少。
这种能量损失最终是以热的形式出现,使系统的油温升高。
系统中引起能量损失的因素很多,主要有以下几个方面:(1)换向阀在换向制动过程中出现的能量损失在开式系统中工作机构的换向只能借助于换向阀封闭执行元件的回油路,先制动后换向。
当执行元件及其外载荷的惯性很大时,在制动过程中压力油和运动机构的惯性都迫使执行元件继续运动,同时压入回油腔的液体,使回油腔的压力增高,严重时可达几倍的工作压力。
液体在此高压作用下,将从换向阀或制动阀的开口缝隙中挤出,从而使运动机构的惯性能变为热耗,使系统的油温升高。
在一些换向频繁,载荷惯性很大的系统中,如挖掘机的回转系统,由于换向制动而产生的热耗是十分可观的,有可能成为系统发热的主要因素。
(2)元件本身的能量损失元件的能量损失包括液压泵、液压马达、液压缸和控制元件等的能量损失,其中以泵和液压马达的损失为最大。
液压泵和液压马达中能量损失的多少,可用效率来表示。
液压泵和液压马达效率的高低,是作为其质量好坏的主要指标之一。
液压泵和液压马达的效率等于机械效率和容积效率的乘积,机械效率和容积效率是与多种因素有关的,如工作压力、转速和工作油液的粘度等。
一般,每一台液压泵和液压马达在一个额定的工作点,即在一定的压力和一定的转速下,具有最高的效率,当增加或降低转速和工作压力时,都会使效率下降。
管路和控制元件的结构,同样也可以影响能量损失的大小。
因为油液流动时的阻力与其流动状态有关,为了减少流动时的能量损失,可在结构上采取改进措施:对于管件,可增大截面积以降低流动速度;对于控制元件,可增大结构尺寸,以增大通流量。