现代石油加工技术--催化裂解
催化裂化技术

催化裂化原料 催化裂化原料分为馏分油和渣油两大类。
1、Distillate Oil(馏分油)
(1)直馏重馏分油(350~500℃)
大多数直馏重馏分含芳烃较少,容易裂化,轻油收率较高, 是理想的催化裂化原料。
(2)热加工产物:焦化蜡油、减粘裂化馏出油等。
其中烯烃、芳烃含量较多,转化率低、生焦率高。不单独
• 5.正碳离子将H+ 还给催化剂,本身变成烯烃,反应中止。
催化裂化催化剂
一、催化裂化剂的种类、组成和结构
工业上使用的裂化催化剂归纳起来有三大类:
1、天然白土催化剂
催化裂化装置最初使用的经处理的天然白土,其主要活性 组分是硅酸铝。
2、无定型硅酸铝催化剂
天然白土被人工合成硅酸铝所取代。
• 无定型硅酸铝催化剂 • 硅酸铝的主要成分是氧化硅和氧化铝,合成硅酸铝依铝含量的不同又分 为低铝(含Al2O310%~13%)和高铝(含Al2O3约25%)二种。其催化剂 按颗粒大小又分为小球状(直径在3~6mm)和微球状(直径在40~80)。 • Al2O3、SiO2及少量水分是必要的活性组分,而其它组分是在催化剂的制 备过程中残留下来的极少量的杂质。合成硅酸铝是由Na2SiO3和Al2(SO4)3 溶液按一定的比例配合而成凝胶,再经水洗、过滤、成型、干燥、活化 而制成的。硅酸铝催化剂的表面具有酸性,并形成许多酸性中心,催化 剂的活性就来源于这些酸性中心,即催化剂的活性中心。
在全世界催化裂化装置的总加工能力中,提升管催化
裂化已占绝大多数。
流程图画面
催化裂化化学反应原理
• 一、单体烃催化裂化的化学反应 • (一)烷烃 • 烷烃主要发生分解反应,分解成较小分子的烷烃和烯烃, 烷烃分解时多从中间的C—C键处断裂,分子越大越容易 断裂
石油化工催化裂化装置工艺流程图

炼油生产安全技术-催化裂化的装置简介类型及工艺流程催化裂化技术的发展密切依赖于催化剂的发展。
有了微球催化剂,才出现了流化床催化裂化装置;分子筛催化剂的出现,才发展了提升管催化裂化.选用适宜的催化剂对于催化裂化过程的产品产率、产品质量以及经济效益具有重大影响。
催化裂化装置通常由三大部分组成,即反应¾再生系统、分馏系统和吸收稳定系统。
其中反应––再生系统是全装置的核心,现以高低并列式提升管催化裂化为例,对几大系统分述如下:㈠反应––再生系统新鲜原料(减压馏分油)经过一系列换热后与回炼油混合,进入加热炉预热到370℃左右,由原料油喷嘴以雾化状态喷入提升管反应器下部,油浆不经加热直接进入提升管,与来自再生器的高温(约650℃~700℃)催化剂接触并立即汽化,油气与雾化蒸汽及预提升蒸汽一起携带着催化剂以7米/秒~8米/秒的高线速通过提升管,经快速分离器分离后,大部分催化剂被分出落入沉降器下部,油气携带少量催化剂经两级旋风分离器分出夹带的催化剂后进入分馏系统。
积有焦炭的待生催化剂由沉降器进入其下面的汽提段,用过热蒸气进行汽提以脱除吸附在催化剂表面上的少量油气。
待生催化剂经待生斜管、待生单动滑阀进入再生器,与来自再生器底部的空气(由主风机提供)接触形成流化床层,进行再生反应,同时放出大量燃烧热,以维持再生器足够高的床层温度(密相段温度约650℃~68 0℃)。
再生器维持0.15MPa~0。
25MPa (表)的顶部压力,床层线速约0。
7米/秒~1。
0米/秒。
再生后的催化剂经淹流管,再生斜管及再生单动滑阀返回提升管反应器循环使用。
烧焦产生的再生烟气,经再生器稀相段进入旋风分离器,经两级旋风分离器分出携带的大部分催化剂,烟气经集气室和双动滑阀排入烟囱。
再生烟气温度很高而且含有约5%~10% CO,为了利用其热量,不少装置设有CO 锅炉,利用再生烟气产生水蒸汽。
对于操作压力较高的装置,常设有烟气能量回收系统,利用再生烟气的热能和压力作功,驱动主风机以节约电能。
石油炼制名词解释

名词解释:1.催化裂化:催化裂化是在0.1~0.3MPa、500℃左右的温度及催化剂作用下,重质原料油发生以裂解为主的一系列化学反应,转化为气体、汽油、柴油、油浆及焦炭的工艺过程。
2.催化剂活性:催化剂的活性就是能加快反应速度的性能。
3.二次燃烧:由过剩O2含量太高,再生器密相床烧焦产生的CO在稀相段或集气室燃烧,放出大量热量而烧坏设备。
4氢转移反应:某烃分子上的氢脱下来立即加到另一烯烃分子上使之饱和的反应。
5碳堆积:再生器烧焦能力低或供氧不足,反应生成的焦炭烧为完全,使催化剂活性及选择性下降,又至使反应时生焦量增大,再生器烧焦更不完全,这样造成恶性循环,使催化剂上焦炭迅速增大,这就是碳堆积。
简答题1.简述催化裂化的化学反应分解反应、异构化反应,氢转移反应,烷基化反应,芳构化反应,烷基化反应、生焦反应2.列出芳烃转化的催化剂种类有酸性催化剂和固体酸,固体酸又分为浸附在适当载体上的质子酸;浸附在适当酸性卤化物,混合氧化物催化剂,贵金属-氧化硅-氧化铝催化剂;分子筛催化剂3.C8芳烃异构化反应所用的催化剂无定型SiO2-Al2O3催化剂,负载型铂催化剂。
ZSM催化剂,HF-BF3催化剂4.简述目前工业上分离对二甲苯的方法?答:深冷结晶法,络合分离法,吸附分离法5.简述开发芳烃转化工艺的原因不同来源的各种芳烃馏分组成是不同的,能得到各种芳烃的产量也不同,因此如果仅从这里取得芳烃,必然导致供需矛盾,所以用该工艺调节芳烃产量为什么催化裂化产物中少C1、C2,多C3、C4?正碳离子分解时不生成<C3、C4的更小正碳离子。
为什么催化裂化产物中多异构烃?伯、仲正碳离子稳定性差,易转化为叔正碳离子。
为什么催化裂化产物中多β烯烃?伯正碳离子易转为仲正碳离子,放出H+形成β烯烃。
催化裂化的原料和产品有什么特点?答:主要原料有:直馏馏分油、常压渣油、脱沥青油、焦化蜡油、减压渣油等。
主要产品有液化气、汽油、柴油、油浆等。
催化裂化是目前石油炼制工业中最重要的二次加工过程,也是

(1)环境空气 根据建设项目可能对大气环境造成的影响程度和范围以及项目所在地区的 环境敏感程度,确定评价工作等级如下: 拟建项目装置产生的主要大气污染物为烟尘、SO2、NOx,根据《环境影响 评价技术导则—大气环境》(HJ/T2.2-2008)中的估算模式对项目的大气环境评价 工作进行分级。根据项目的工程分析结果,选择 TSP 和 SO2 来确定评价工作等 级,计算最大地面浓度占标率 Pi,及第 i 个污染物的地面浓度达标准限值 10%时 所对应的最远距离 D10%。 根据估算模式的计算结果,Pmax=4.308%<10%,最大浓度出现的距离(1.9km)
(3)声环境
根据《兰州市饮用水源保护区、大气、噪声功能区划图》,声环境兰新铁路 以南为一类区,兰新铁路以北,化工街、生产街、广河路、合水北路、西固东路 以南地区及兰州石化分公司东区专用铁路以东,环行东路以西,西固东路以北的 三角地带为二类区,其余地区为三类区,主要交通干线两侧为四类区。
1.3.2 环境质量标准
西固路以北的工业区(西起西柳沟,东至水上公园,北至黄河,南至西固路)为大 气三类区,其余部分均为二类区。根据《国务院关于酸雨控制区和二氧化硫污染 控制区有关问题的批复》(国函(1998)5 号),兰州市区为 SO2 控制区。
(2)地表水环境
根据《兰州市城市生活饮用水的保护区区划方案》,地表水在一水厂排泥口 以上为Ⅱ类水域,以下为Ⅲ类水域。
厂界外声环境功能区类别
昼间夜间Biblioteka 36555
表 1.6-9
施工阶段
土石方 打桩 结构 装修
建筑施工场界噪声限值(GB12523-1990) 单位:dB(A)
主要噪声源
噪声限值
昼间
夜间
推土机、挖掘机、装载机
催化裂解和催化裂化的不同点

催化裂解就是在催化剂存在的条件下,对石油烃类进行高温裂解来生产乙烯、丙烯、丁烯等低碳烯烃,并同时兼产轻质芳烃的过程。
由于催化剂的存在,催化裂解可以降低反应温度,增加低碳烯烃产率与轻质芳香烃产率,提高裂解产品分布的灵活性。
(1) 催化裂解的一般特点①催化裂解就是碳正离子反应机理与自由基反应机理共同作用的结果,其裂解气体产物中乙烯所占的比例要大于催化裂化气体产物中乙烯的比例。
②在一定程度上,催化裂解可以瞧作就是高深度的催化裂化,其气体产率远大于催化裂化,液体产物中芳烃含量很高。
③催化裂解的反应温度很高,分子量较大的气体产物会发生二次裂解反应,另外,低碳烯烃会发生氢转移反应生成烷烃,也会发生聚合反应或者芳构化反应生成汽柴油。
(2) 催化裂解的反应机理一般来说,催化裂解过程既发生催化裂化反应,也发生热裂化反应,就是碳正离子与自由基两种反应机理共同作用的结果,但就是具体的裂解反应机理随催化剂的不同与裂解工艺的不同而有所差别。
在Ca-Al系列催化剂上的高温裂解过程中,自由基反应机理占主导地位;在酸性沸石分子筛裂解催化剂上的低温裂解过程中,碳正离子反应机理占主导地位;而在具有双酸性中心的沸石催化剂上的中温裂解过程中,碳正离子机理与自由基机理均发挥着重要的作用。
(3) 催化裂解的影响因素同催化裂化类似,影响催化裂解的因素也主要包括以下四个方面:原料组成、催化剂性质、操作条件与反应装置。
①原料油性质的影响。
一般来说,原料油的H/C比与特性因数K越大,饱与分含量越高,BMCI值越低,则裂化得到的低碳烯烃(乙烯、丙烯、丁烯等)产率越高;原料的残炭值越大,硫、氮以及重金属含量越高,则低碳烯烃产率越低。
各族烃类作裂解原料时,低碳烯烃产率的大小次序一般就是:烷烃>环烷烃>异构烷烃>芳香烃。
②催化剂的性质。
催化裂解催化剂分为金属氧化物型裂解催化剂与沸石分子筛型裂解催化剂两种。
催化剂就是影响催化裂解工艺中产品分布的重要因素。
催化裂解原理与机理

催化裂解催化裂解,是在催化剂存在的条件下,对石油烃类进行高温裂解来生产乙烯、丙烯、丁烯等低碳烯烃,并同时兼产轻质芳烃的过程。
由于催化剂的存在,催化裂解可以降低反应温度,增加低碳烯烃产率和轻质芳香烃产率,提高裂解产品分布的灵活性。
一、催化裂解的一般特点1、催化裂解是碳正离子反应机理和自由基反应机理共同作用的结果,其裂解气体产物中乙烯所占的比例要大于催化裂化气体产物中乙烯的比例。
2 、在一定程度上,催化裂解可以看作是高深度的催化裂化,其气体产率远大于催化裂化,液体产物中芳烃含量很高。
3 、催化裂解的反应温度很高,分子量较大的气体产物会发生二次裂解反应,另外,低碳烯烃会发生氢转移反应生成烷烃,也会发生聚合反应或者芳构化反应生成汽柴油。
二、催化裂解的反应机理一般来说,催化裂解过程既发生催化裂化反应,也发生热裂化反应,是碳正离子和自由基两种反应机理共同作用的结果,但是具体的裂解反应机理随催化剂的不同和裂解工艺的不同而有所差别。
在Ca-Al系列催化剂上的高温裂解过程中,自由基反应机理占主导地位;在酸性沸石分子筛裂解催化剂上的低温裂解过程中,碳正离子反应机理占主导地位;而在具有双酸性中心的沸石催化剂上的中温裂解过程中,碳正离子机理和自由基机理均发挥着重要的作用。
三、催化裂解的影响因素同催化裂化类似,影响催化裂解的因素也主要包括以下四个方面:原料组成、催化剂性质、操作条件和反应装置。
3.1 原料油性质的影响一般来说,原料油的H/C比和特性因数K越大,催化裂解法处理焦油方案[1]饱和分含量越高,BMCI值越低,则裂化得到的低碳烯烃(乙烯、丙烯、丁烯等)产率越高;原料的残炭值越大,硫、氮以及重金属含量越高,则低碳烯烃产率越低。
各族烃类作裂解原料时,低碳烯烃产率的大小次序一般是:烷烃>环烷烃>异构烷烃>芳香烃。
3.2催化剂的性质催化裂解催化剂分为金属氧化物型裂解催化剂和沸石分子筛型裂解催化剂两种。
催化剂是影响催化裂解工艺中产品分布的重要因素。
石油加工中的催化裂化工艺技术

石油加工中的催化裂化工艺技术石油加工是将原油转化为各种石油产品的过程,其中催化裂化是一种重要的加工工艺技术。
本文将对石油加工中的催化裂化工艺技术进行介绍,旨在帮助读者更好地了解该过程的原理和应用。
一、催化裂化的概述催化裂化是将长链烃分子在催化剂的作用下裂解为短链烃分子的过程。
它通过破坏长链分子的结构,使原油中的重质烃分子转化为轻质烃分子,从而提高汽油产量。
催化裂化工艺技术在炼油行业中有着广泛的应用,并成为提高汽油产量和改善燃料质量的重要手段。
二、催化裂化的原理催化裂化过程中,催化剂起到了关键的作用。
一般采用酸性固体催化剂,如二氧化硅、氧化铝和硼砂等。
这些催化剂表面具有一定的酸性,能够吸附原油中的长链分子并发生脱氢和脱碳反应,从而裂解为短链烃分子。
此外,催化剂还能够催化裂解产物的再重组反应,生成较高辛烷值的汽油。
三、催化裂化过程催化裂化过程主要包括以下几个步骤:料油预热、加热和蒸汽气化;进料油在催化剂床层中与催化剂接触发生裂化反应;裂解产物经过分离和处理,得到目标产品;再生催化剂,使其恢复活性。
整个过程需要严格控制反应温度、压力和催化剂的质量和活性。
四、催化裂化的应用催化裂化工艺技术在炼油工业中有着广泛的应用。
通过调整反应条件和催化剂的配方,可以实现不同的生产目标,如提高汽油产量、改善燃料质量、减少环境污染等。
此外,催化裂化还可以生产出其他石化产品,如乙烯和丙烯等。
五、催化裂化的发展趋势催化裂化工艺技术在过去几十年取得了较大的进展,但仍存在一些问题和挑战。
例如,催化剂的寿命较短,需要经常更换和再生;催化裂化过程中产生的废热和废气对环境造成污染。
为了解决这些问题,近年来研发了一系列新型催化剂和工艺技术,如热解裂化和催化裂解结合等,以提高催化裂化的效率和环境友好性。
六、结论石油加工中的催化裂化工艺技术是一项重要的炼油工艺,能够将原油转化为汽油等石化产品。
催化裂化过程中,催化剂起到了关键的作用,通过裂解和重组反应实现原油的转化。
先进炼油化工技术催化裂解技术(DCC)
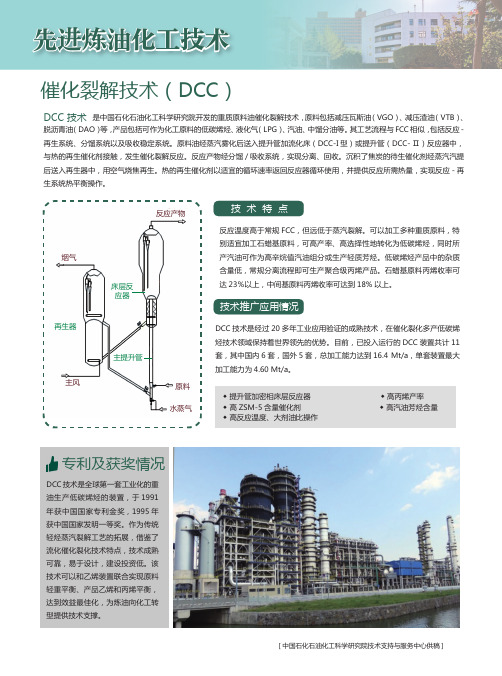
催化裂解技术(DCC)
DCC 技术 是中国石化石油化工科学研究院开发的重质原料油催化裂解技术,原料包括减压瓦斯油(VGO)、减压渣油(VTB)、脱沥青油(DAO)等,产品包括可作为化工原料的低碳烯烃、液化气(LPG)、汽油、中馏分油等。
其工艺流程与FCC 相似,包括反应-再生系统、分馏系统以及吸收稳定系统。
原料油经蒸汽雾化后送入提升管加流化床(DCC-I 型)或提升管(DCC-Ⅱ)反应器中,与热的再生催化剂接触,发生催化裂解反应。
反应产物经分馏/吸收系统,实现分离、回收。
沉积了焦炭的待生催化剂经蒸汽汽提后送入再生器中,用空气烧焦再生。
热的再生催化剂以适宜的循环速率返回反应器循环使用,并提供反应所需热量,实现反应-再生系统热平衡操作。
DCC 油生产低碳烯烃的装置,于[中国石化石油化工科学研究院技术支持与服务中心供稿]反应产物烟气原料
水蒸气主风再生器床层反应器主提升管
先进炼油化工技术。
- 1、下载文档前请自行甄别文档内容的完整性,平台不提供额外的编辑、内容补充、找答案等附加服务。
- 2、"仅部分预览"的文档,不可在线预览部分如存在完整性等问题,可反馈申请退款(可完整预览的文档不适用该条件!)。
- 3、如文档侵犯您的权益,请联系客服反馈,我们会尽快为您处理(人工客服工作时间:9:00-18:30)。
36
20
15
CH
10
24
5
450
500
550
600
650
反应温度,℃
➢C4烃在上海石化院开发的催化剂上表现出很好的裂解性能 ➢乙丙烯产率很高, 650℃时接近50 wt%
25
6. 汽柴油二次裂解反应规律
• 研究意义
➢ 汽柴油-重要产品-中间产物
➢ 反映出芳香烃的催化裂解性能
➢ 反应历程的探讨和动力学研究
7
二、催化裂解催化剂及工艺技术
• 金属氧化物型
➢ 一般是在氧化铝等载体上负载碱金属、碱土金属或稀土金 属的氧化物,或者是几种氧化物的复合物
➢ 此类催化剂的裂解温度一般较高
• 沸石分子筛型
➢ 一般用金属交换沸石分子筛作为裂解催化剂的活性组分, 如丝光沸石、HASM-5沸石分子筛、HZSM-5沸石分子筛 、ZRP沸石分子筛和ZSM-5沸石分子筛
630 11.39 9.00 41.80 19.11 15.12 39.09 25.15
660 15.10 8.25 39.58 17.58 15.69 42.84 24.37
680 16.21 7.46 39.08 17.56 16.10 43.36 24.44
700 19.75 6.43 36.97 16.39 16.90 46.64 21.88
油气停留时间2.8s,剂油比18,水油比1.10
27
汽柴油二次裂解反应规律
➢丁烷:17.7 wt%,丁烯:81.5 wt%
23
C4烃催化裂解转化率随反应温度的变化
温度,℃
450 480
异丁烷 -58.67 -41.89
转化率,wt% 正丁烷 1-丁烯 t-2-丁烯 -6.92 92.47 66.41 -4.54 91.49 65.07
c-2-丁烯 61.69 58.92
2002-2007 乙烯年均增长率 5.0% 丙烯年均增长率 5.2%
3
➢目的产品:汽油和柴油 ➢改变工艺条件可以提高乙丙烯产 率 ➢增幅有限
技术背景
乙烯
95%
丙烯
66%
32%
管式炉蒸汽裂解
催化裂化
•对原料要求苛刻-轻烃、石脑油、柴油 •我国轻油资源匮乏,热裂解原料短缺
4
技术背景
乙丙烯产率高
原料范围宽
630 -8.39 10.29 85.35 88.51 86.62 84.07
660 17.31 29.55 82.46 85.35 84.25 81.41
680 27.60 42.54 88.19 90.16 89.51 87.14
700 54.43 63.65 88.91 90.52 90.24 87.90
➢ 此类催化剂的裂解温度一般较低
8
催化裂解工艺技术
• 国外
➢ 催化-蒸汽裂解工艺——俄罗斯、欧美
➢ THR工艺 ——日本
➢ QC裂解技术——Stone & Webster
➢ Superflex工艺——KBR公司
• 国内
➢ DCC工艺 ➢ CPP工艺
石油化工科学研究院
➢ HCC工艺
洛阳石油化工工程公司
➢300kt/a乙烯能力的HCC装置的总投资与同等规模的轻油蒸汽热裂解制乙 烯装置的总投资相当,但其裂解原料费用远小于蒸汽裂解原料费用。 ➢用中等质量的常压渣油为原料时,HCC工艺的乙烯生产成本仅为同等规模 的石脑油热裂解制乙烯的76%;内部收益率为21.2%,远高于蒸汽裂解。
称香生.炼油设计,2000,30(6): 1-4
8.87 15.2 88.34 64.95
650 18.72 22.01 88.87 67.56
55.58 56.77 59.93 63.02
➢ 丁烯的转化率远大于丁烷的转化率 ➢ 1-丁烯的转化率大于2-丁烯的转化率
24
乙烯和丙烯收率,wt%
50
45
C H +C H 24 36
40
35
30
CH
25
5
600 620 640 660 680 700 720
反应温度,℃
➢总烯烃产率可达45 wt% ➢烯烃分布跟CPP催化剂差别很大
15
大庆常渣催化裂解/热裂解对比
Байду номын сангаас
烯烃产率, m%
50
乙烯 丙烯 丁烯
40
30
20
10
0 CPP
HCC
热裂解
反应温度660 ℃
16
3. 加拿大HVGO在CPP上的裂解规律
500
-33.4 -3.11 90.89 64.44
530 -25.12 -2.1 89.82 62.89
550 -19.92 -0.65 89.14 62.21
57.65 55.94 55.59
580 -11.98 2.5 88.33 61.64
600
-5.15 6.36 88.13 62.32
630
第4章 催化裂解
1
本章主要内容
• 催化裂解技术背景及特点 • 催化裂解催化剂及工艺技术 • 催化裂解反应规律 • 烃类裂解性能的特征化研究 • 催化裂解反应历程和机理 • 催化裂解反应动力学
2
一、催化裂解技术背景及特点
• 低碳烯烃的市场需求
1996-2001 乙烯年均增长率 4.0% 丙烯年均增长率 5.1%
i-戊烷 n-戊烷 C5烯烃 C6及以上
含量,wt% 10.23 0.09 3.95 0.10 3.01 0.20
➢丁烷:26.2 wt% 丁烯:65.9 wt%
20
C4烃催化裂解转化率随反应温度的变化
温度,℃ i-丁烷 n-丁烷
t-2-丁烯 n-丁烯-1
i-丁烯 c-2-丁烯
600 -15.16 2.32 80.39 85.79 81.56 79.82
➢丁烯的转化率远大于丁烷的转化率 ➢随反应温度的升高,丁烷与丁烯转化率的差距逐渐缩小
21
低碳烯烃产率,wt%
40 36 32 28 24 20 16 12
8 600
乙烯 丙烯 乙烯+丙烯
620 640 660 680 700
反应温度,℃
➢C4烃在CPP催化剂上表现出良好的裂解性能 ➢乙丙烯产率较高,660℃时接近36 wt%
• 汽柴油原料
➢ 烷基苯-43.74%
➢ 烷基萘-20.86%
82%
➢ 其它芳烃-17.64%
➢ 饱和烃+烯烃-17.76%
26
汽柴油二次裂解反应规律
• 产品分布
温度 ℃
产品产率,wt%
干气 液化气 汽油 柴油
焦炭
转化率
总烯烃选 择性
600 9.25 9.99 42.30 19.92 15.23 37.79 25.31
22
5. C4烃在上海石化院催化剂上的裂解规律
组分 乙烯 丙烷 环丙烷 丙烯 丙二烯 异丁烷 正丁烷
含量,wt% 0.02 0.04 0.02 0.23 0.04 4.05 13.61
组分 t-2-丁烯 1-丁烯 异丁烯 c-2-丁烯 1,3-丁二烯
C5烃 C6烃
含量,wt% 18.36 51.06 0.08 11.85 0.13 0.09 0.42
11
1. 大庆常渣在CPP上的裂解规律
产物分布随反应温度的变化
温度,℃ 干气
600 12.77 620 16.07 640 19.64 660 23.06 680 27.68 700 32.37 716 35.61
产品产率,wt% 液化气 汽油 柴油 45.69 24.24 5.71 46.55 20.04 5.85 45.78 18.27 4.90 43.17 16.86 4.31 39.28 15.10 4.58 33.93 15.49 4.64 30.10 14.13 4.24
组分 甲烷 乙烷 乙烯 乙炔 丙烷 环丙烷 丙烯
含量,wt% 0.02 0.01 0.04 0.01 0.03 0.01 0.18
组分 丙二烯
丙炔 i-丁烷 n-丁烷 t-2-丁烯 n-丁烯-1 i-丁烯
含量,wt% 0.01 0.30 18.39 7.84 14.83 13.26 27.50
组分 c-2-丁烯 1,3-丁二烯
转化率 wt%
93.78 95.34 95.21 98.77 98.60 98.86
低碳烯烃 选择性 %
29.78 36.54 43.20 45.33 43.98 42.74
油气停留时间1.8 s,剂油比16,水油比0.67
14
低碳烯烃产率,wt%
45
40
35
乙烯 丙烯
30
丁烯
25
总烯烃
20
15
10
焦炭 13.70 14.59 14.49 15.40 16.72 18.76
转化率 低碳烯烃 wt% 选择性 % 78.62 29.25 78.87 30.14 79.30 29.98 80.17 29.05 82.05 27.53 82.69 25.56
油气停留时间2.5 s,剂油比15.4,水油比0.55
➢ RSCC工艺
中国石油集团公司
9
催化裂解工艺技术
• DCC-- Deep Catalytic Cracking
➢ DCC-Ⅰ:最大量生产以丙烯为主的气体烯烃 ➢ DCC-Ⅱ :最大量生产丙烯和异丁烯、异戊烯等气体烯
烃,并同时兼产高辛烷值优质汽油
• CPP-- Catalytic Pyrolysis Process
17
35
30
C =+C =+C =