新型络合剂的合成及其络合铁脱硫工艺研究
络合铁脱硫成套技术
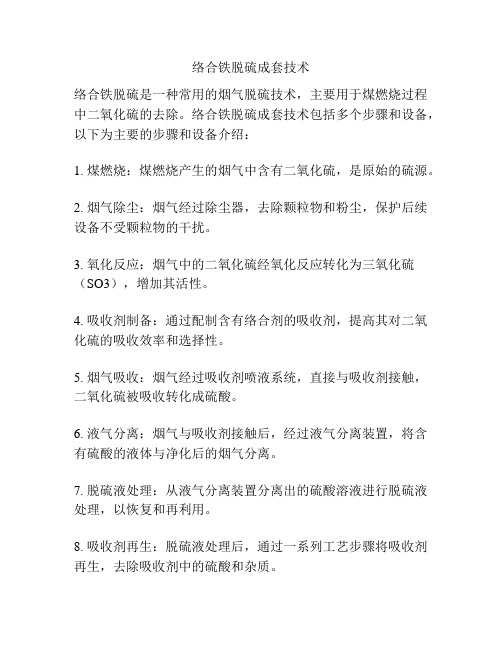
络合铁脱硫成套技术
络合铁脱硫是一种常用的烟气脱硫技术,主要用于煤燃烧过程中二氧化硫的去除。
络合铁脱硫成套技术包括多个步骤和设备,以下为主要的步骤和设备介绍:
1. 煤燃烧:煤燃烧产生的烟气中含有二氧化硫,是原始的硫源。
2. 烟气除尘:烟气经过除尘器,去除颗粒物和粉尘,保护后续设备不受颗粒物的干扰。
3. 氧化反应:烟气中的二氧化硫经氧化反应转化为三氧化硫(SO3),增加其活性。
4. 吸收剂制备:通过配制含有络合剂的吸收剂,提高其对二氧化硫的吸收效率和选择性。
5. 烟气吸收:烟气经过吸收剂喷液系统,直接与吸收剂接触,二氧化硫被吸收转化成硫酸。
6. 液气分离:烟气与吸收剂接触后,经过液气分离装置,将含有硫酸的液体与净化后的烟气分离。
7. 脱硫液处理:从液气分离装置分离出的硫酸溶液进行脱硫液处理,以恢复和再利用。
8. 吸收剂再生:脱硫液处理后,通过一系列工艺步骤将吸收剂再生,去除吸收剂中的硫酸和杂质。
9. 产生石膏:脱硫液处理后的硫酸溶液通过蒸发和结晶等工艺,产生固体硫酸盐(一般为石膏或石膏浆)。
10. 排放净化烟气:经过络合铁脱硫处理后的烟气,其中的二
氧化硫含量大大降低,符合环境排放标准。
这些步骤和设备组成了络合铁脱硫成套技术,可以高效地去除燃煤产生的二氧化硫,减少烟气对环境的污染。
络合铁脱硫工艺再生反应机理研究及现场应用
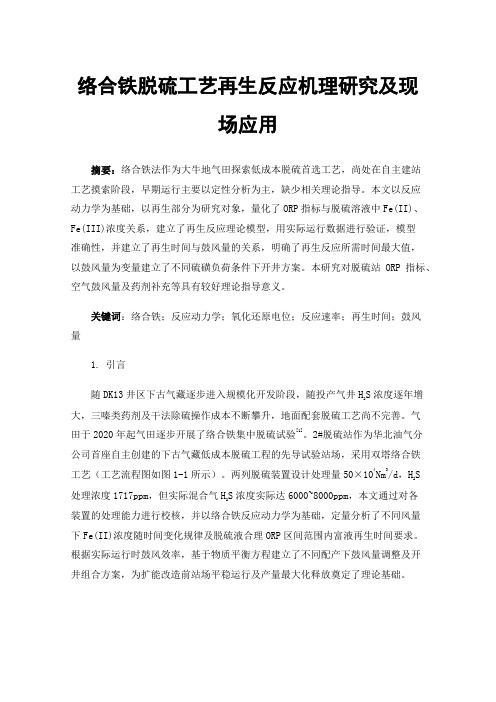
络合铁脱硫工艺再生反应机理研究及现场应用摘要:络合铁法作为大牛地气田探索低成本脱硫首选工艺,尚处在自主建站工艺摸索阶段,早期运行主要以定性分析为主,缺少相关理论指导。
本文以反应动力学为基础,以再生部分为研究对象,量化了ORP指标与脱硫溶液中Fe(II)、Fe(III)浓度关系,建立了再生反应理论模型,用实际运行数据进行验证,模型准确性,并建立了再生时间与鼓风量的关系,明确了再生反应所需时间最大值,以鼓风量为变量建立了不同硫磺负荷条件下开井方案。
本研究对脱硫站ORP指标、空气鼓风量及药剂补充等具有较好理论指导意义。
关键词:络合铁;反应动力学;氧化还原电位;反应速率;再生时间;鼓风量1. 引言S浓度逐年增随DK13井区下古气藏逐步进入规模化开发阶段,随投产气井H2大,三嗪类药剂及干法除硫操作成本不断攀升,地面配套脱硫工艺尚不完善。
气田于2020年起气田逐步开展了络合铁集中脱硫试验[1]。
2#脱硫站作为华北油气分公司首座自主创建的下古气藏低成本脱硫工程的先导试验站场,采用双塔络合铁S工艺(工艺流程图如图1-1所示)。
两列脱硫装置设计处理量50×104Nm3/d,H2S浓度实际达6000~8000ppm,本文通过对各处理浓度1717ppm,但实际混合气H2装置的处理能力进行校核,并以络合铁反应动力学为基础,定量分析了不同风量下Fe(II)浓度随时间变化规律及脱硫液合理ORP区间范围内富液再生时间要求。
根据实际运行时鼓风效率,基于物质平衡方程建立了不同配产下鼓风量调整及开井组合方案,为扩能改造前站场平稳运行及产量最大化释放奠定了理论基础。
图1-1 络合铁脱硫工艺流程示意图2. 装置处理能力分析络合铁脱硫工艺处理单元主要可划分为“吸收-再生-压滤”三部分。
吸收能力主要由药剂硫容量(铁离子浓度)及循环量决定,铁离子控制范围在4500~5500mg/L,对应硫容量1.2~1.5g/L,循环量最大运行32m3/h时,对应硫磺负荷为2304kg/d。
焦化脱硫工艺应用络合铁催化剂的探讨
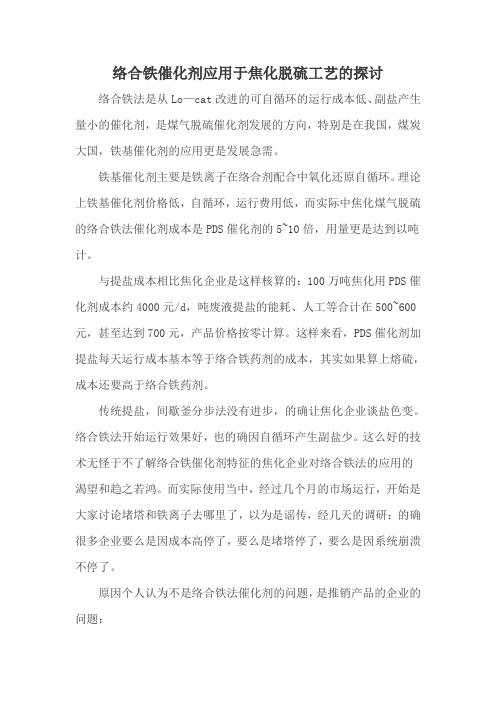
络合铁催化剂应用于焦化脱硫工艺的探讨络合铁法是从Lo—cat改进的可自循环的运行成本低、副盐产生量小的催化剂,是煤气脱硫催化剂发展的方向,特别是在我国,煤炭大国,铁基催化剂的应用更是发展急需。
铁基催化剂主要是铁离子在络合剂配合中氧化还原自循环。
理论上铁基催化剂价格低,自循环,运行费用低,而实际中焦化煤气脱硫的络合铁法催化剂成本是PDS催化剂的5~10倍,用量更是达到以吨计。
与提盐成本相比焦化企业是这样核算的:100万吨焦化用PDS催化剂成本约4000元/d,吨废液提盐的能耗、人工等合计在500~600元,甚至达到700元,产品价格按零计算。
这样来看,PDS催化剂加提盐每天运行成本基本等于络合铁药剂的成本,其实如果算上熔硫,成本还要高于络合铁药剂。
传统提盐,间歇釜分步法没有进步,的确让焦化企业谈盐色变。
络合铁法开始运行效果好,也的确因自循环产生副盐少。
这么好的技术无怪于不了解络合铁催化剂特征的焦化企业对络合铁法的应用的渴望和趋之若鸿。
而实际使用当中,经过几个月的市场运行,开始是大家讨论堵塔和铁离子去哪里了,以为是谣传,经几天的调研:的确很多企业要么是因成本高停了,要么是堵塔停了,要么是因系统崩溃不停了。
原因个人认为不是络合铁法催化剂的问题,是推销产品的企业的问题:第一、号称不改原有设备,试用调配药剂就可以,这个说法误导了焦化企业。
络合铁法产生副盐少,硫增加了1/4多,除非原设计脱硫处理量大于实际约30%,原系统是不可能适应突然增加的硫产生量,悬浮硫高,堵塔和冒液必然。
第二、络合铁法是靠铁离子氧化H2S直接生成硫,是在脱硫塔内就进行反应的,依靠原适合PDS工艺的塔盘来保证适合络合铁法在塔内产生大量硫泡沫是不可能的,堵塔也是必然要发生的。
第三、推销络合铁催化剂的讲不产生盐,对副作用闭口不提,也不提为什么要加入那么多的络合铁催化剂。
实际上铁离子是靠配比的络合剂自循环于脱硫液中,产生的硫泡沫就是副产品,是脱硫废液,如果压滤,损失在硫膏内;如果用熔硫釜,多余水分蒸发,催化剂损失在硫渣中。
GLT络合铁脱硫技术及应用发展

GLT络合铁脱硫技术及应用发展潘威;刘印东;魏哲峰;王杨【摘要】GLT络合铁脱硫技术由于硫化氢转化为硫磺选择性99%以上、脱硫过程无三废产生且催化剂环境友好得到广泛应用.介绍了GLT络合铁法脱硫化学原理、在石油石化行业天然气、酸气硫回收及克劳斯尾气深度脱硫中的应用、在化学粘胶纤维尾气硫化氢治理中的应用、在焦炉煤气脱硫中的应用以及其它化工尾气硫化氢治理中的应用.GLT络合铁技术非常适用于潜硫量小、硫化氢浓度波动大、气量波动大的尾气治理.GLT络合铁技术解决了焦炉煤气脱硫领域络合铁催化剂长期使用过程中稳定性不高、带来设备腐蚀、结晶堵塔、补充量大、硫泡沫浮选困难等问题.【期刊名称】《江西化工》【年(卷),期】2019(000)004【总页数】4页(P105-108)【关键词】硫化氢;脱硫;GLT络合铁;工业应用【作者】潘威;刘印东;魏哲峰;王杨【作者单位】武汉国力通能源环保股份有限公司,湖北武汉430206;唐山市汇丰炼焦制气有限公司,河北唐山063100;唐山市汇丰炼焦制气有限公司,河北唐山063100;唐山市汇丰炼焦制气有限公司,河北唐山063100【正文语种】中文络合铁脱硫技术是一种采用络合铁作为催化剂的湿式氧化还原脱除硫化氢的技术,其特点是直接将H2S转化成单质硫,H2S的脱除率可达99%以上[1-2],是一种工艺简单、脱硫效果高、工作硫容高、副反应少且环保无毒的新型脱硫技术,克服了传统脱硫工艺复杂、工作硫容量低、环境污染严重等弊端,符合当前节能减排,经济高效的工业化指导思想。
GLT络合铁脱硫技术是由武汉国力通能源环保股份有限公司开发。
针对潜硫量小于30吨/天的硫化氢治理及硫磺回收,该公司开发了具有自主知识产权的GLT络合铁脱硫成套技术,经10余年对络合铁脱硫化氢技术的研发与推广,在中石化、中石油、中海油、地方炼油企业、化纤企业、大型煤化工企业、冶金企业等均有工业化脱硫装置在稳定运行,净化后气体中硫化氢含量低于10ppm。
络合铁脱硫剂稳定性研究
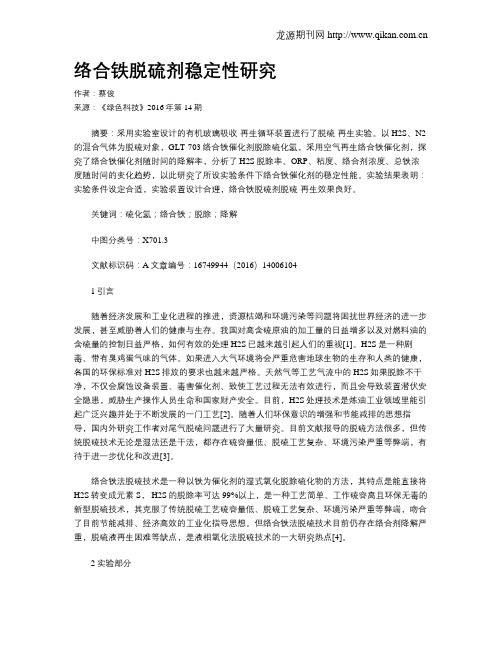
络合铁脱硫剂稳定性研究作者:蔡俊来源:《绿色科技》2016年第14期摘要:采用实验室设计的有机玻璃吸收-再生循环装置进行了脱硫-再生实验。
以H2S、N2的混合气体为脱硫对象,GLT-703络合铁催化剂脱除硫化氢,采用空气再生络合铁催化剂,探究了络合铁催化剂随时间的降解率,分析了H2S脱除率、ORP、粘度、络合剂浓度、总铁浓度随时间的变化趋势,以此研究了所设实验条件下络合铁催化剂的稳定性能。
实验结果表明:实验条件设定合适,实验装置设计合理,络合铁脱硫剂脱硫-再生效果良好。
关键词:硫化氢;络合铁;脱除;降解中图分类号:X701.3文献标识码:A文章编号:16749944(2016)140061041引言随着经济发展和工业化进程的推进,资源枯竭和环境污染等问题将困扰世界经济的进一步发展,甚至威胁着人们的健康与生存。
我国对高含硫原油的加工量的日益增多以及对燃料油的含硫量的控制日益严格,如何有效的处理H2S已越来越引起人们的重视[1]。
H2S是一种剧毒、带有臭鸡蛋气味的气体。
如果进入大气环境将会严重危害地球生物的生存和人类的健康,各国的环保标准对H2S排放的要求也越来越严格。
天然气等工艺气流中的H2S如果脱除不干净,不仅会腐蚀设备装置、毒害催化剂、致使工艺过程无法有效进行,而且会导致装置潜伏安全隐患,威胁生产操作人员生命和国家财产安全。
目前,H2S处理技术是炼油工业领域里能引起广泛兴趣并处于不断发展的一门工艺[2]。
随着人们环保意识的增强和节能减排的思想指导,国内外研究工作者对尾气脱硫问题进行了大量研究。
目前文献报导的脱硫方法很多,但传统脱硫技术无论是湿法还是干法,都存在硫容量低、脱硫工艺复杂、环境污染严重等弊端,有待于进一步优化和改进[3]。
络合铁法脱硫技术是一种以铁为催化剂的湿式氧化脱除硫化物的方法,其特点是能直接将H2S转变成元素S, H2S的脱除率可达99%以上,是一种工艺简单、工作硫容高且环保无毒的新型脱硫技术,其克服了传统脱硫工艺硫容量低、脱硫工艺复杂、环境污染严重等弊端,吻合了目前节能减排、经济高效的工业化指导思想。
络合铁法脱硫技术

络合铁法脱硫技术陶骏200809101107(化学与环境工程学院B08091011 武汉430056)摘要简要介绍络合铁脱硫技术原理、流程以及应用范围,归纳了国内外的应用现状和前景,提出了需要解决的技术难题。
关键词脱硫络合铁法工艺流程1.引言工业原料气和工业废气中的H2S 能引起设备腐蚀和催化剂中毒,导致生产成本增加和产品质量下降;如不经处理排放到大气中,会带来严重的环境问题, 直接威胁人类的生存与发展。
研究开发H2S的高效脱除技术已成为世界各国关注的热点。
2.1概述在各种脱H2S气体的方法中,采用络合铁液相氧化法的工业化装置越来越多。
20世纪60年代以来不断有专利发布, 目前仍然是十分活跃的研究方向。
络合铁脱硫技术是一种以铁为催化剂的湿式氧化还原脱除硫化物的方法,它的特点是吸收剂无毒、能一步将H2S 转变成元素S, H2S的脱除率可达99%以上。
络合铁脱硫技术适用于H2S 浓度较低或H2S浓度较高但气体流量不大的场合。
在硫产量< 20 td时,该工艺的设备投资和操作费用具有明显优势, 更重要的优点是该工艺在脱除硫化物过程中,几乎不受气源中CO2含量的影响而能达到非常高的净化度。
络合铁法处理H2S含量低的气体还有其它显著的优点:集脱硫与硫磺回收为一体,吸收与再生均可在常温下进行;H2S 转化为硫氧化物的副反应少。
2.2应用范围络合铁脱硫工艺, 可广泛应用于如下含硫气体的脱硫: ( 1) 各种含硫化氢废气。
( 2)炼厂气、天然气。
( 3)胺法、低温甲醇洗、 Selexol 尾气和克劳斯尾气。
( 4)煤气化装置及合成氨厂工艺气体。
2.3基本原理络合铁法脱硫的基本原理是, H2S 在碱性溶液中被 Fe3+的络合物Fe3+L n 氧化成单质硫,而本身被H2S 还原成Fe2+Ln ,然后用空气氧化再生,生成Fe3+Ln, 循环使用,其反应为:总反应是:根据络合铁法的反应原理,由于配体的存在, 不但增加了铁离子的溶解性,而且提高了铁离子的稳定性。
乌海沼气络合铁脱硫催化剂

乌海沼气络合铁脱硫催化剂
乌海沼气络合铁脱硫催化剂是一种新型的催化剂,它可以有效地去除沼气中的硫化氢,从而提高沼气的质量和利用价值。
本文将从催化剂的制备、工作原理和应用前景三个方面进行介绍。
一、催化剂的制备
乌海沼气络合铁脱硫催化剂是由铁离子和络合剂组成的。
制备过程中,首先需要将铁离子和络合剂混合,然后加入载体材料,最后进行干燥和煅烧处理。
制备好的催化剂具有高的比表面积和良好的热稳定性,可以在高温高压的条件下进行反应。
二、工作原理
乌海沼气络合铁脱硫催化剂的工作原理是通过络合剂与硫化氢发生反应,生成络合物,从而将硫化氢转化为不易挥发的硫化铁。
这种催化剂具有高的催化活性和选择性,可以在较低的温度下实现高效的脱硫效果。
同时,催化剂的再生性能也很好,可以多次使用。
三、应用前景
乌海沼气络合铁脱硫催化剂具有广泛的应用前景。
首先,它可以用于沼气的净化和提纯,提高沼气的质量和利用价值。
其次,它还可以用于工业废气的处理和环境保护。
此外,随着新能源的发展和应用,乌海沼气络合铁脱硫催化剂也将在能源领域发挥重要作用。
乌海沼气络合铁脱硫催化剂是一种具有良好催化性能和应用前景的新型催化剂。
它可以有效地去除沼气中的硫化氢,提高沼气的质量和利用价值,同时也可以用于工业废气的处理和环境保护。
相信在未来的发展中,它将会得到更广泛的应用和推广。
络合铁法脱硫工艺研究进展
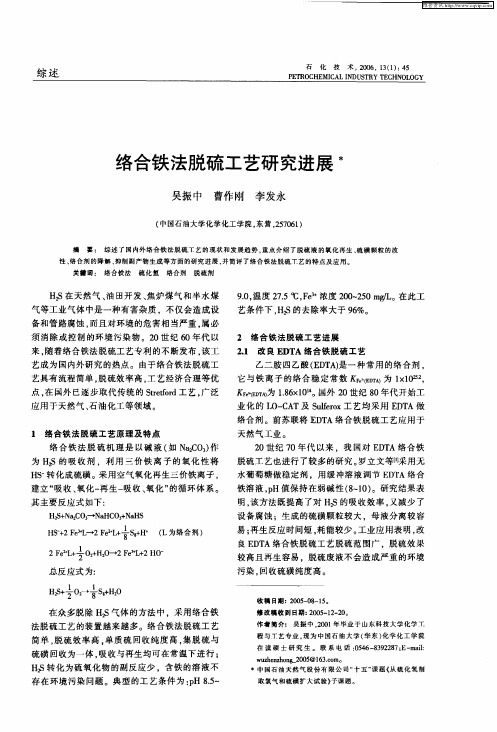
石化技术 20 第 1 0 6年 3卷第 l 期
22 磺基水杨 酸(D) . F 络合 铁脱硫 工艺 F D络合 铁脱硫 工艺 的特点 是硫容 量高 、 格 价
低 廉 。工艺所 用络 合剂 F 与铁 离子形 成带 双键 D,
体来 源 和 净化 度 要 求 的 不 同 ,O— A L C T工 艺有 常
简单 , 脱硫效率高 , 单质硫 回收纯度高, 集脱硫与
硫磺 回收为一体 , 吸收与再 生均可在 常温下进 行 ; H S转化 为硫 氧化物 的副反 应少 ,含铁 的溶液 不 2 存 在环境 污染 问题 。典 型的工艺 条件 为 :H 8 ~ p . 5
在 读 硕 士 研 究 生 。 联 系 电话 :5 6 89 2 7 E— i 0 4 — 32 8 ; mal :
明 , 方法既提 高 了对 H S的吸收 效率 , 该 2 又减少 了 设 备腐蚀 ;生成 的硫磺颗粒 较大 。母液分 离较容
H一 -2 eL古s H (为络 s 2 eL + B ; 生反应 时间短 , 再 耗能较少 。 工业应 用表 明 , 改
良E T D A络合铁脱 硫工艺脱 硫范 围广 ,脱硫 效果
2F2 + 0+ 2-2 eL2H 一 eL ÷ 2H0 +  ̄ + O + F
厶
较 高且再生容 易 ,脱硫废 液不会造 成严重 的环境 污染 , 回收硫磺纯 度高 。
总反 应式 为:
1 1
HS÷0 专S H0 2 + 厂 8 2 +
业化的 L —A O C T及 S l rx工艺 均 采用 E T uf o e D A做
艺具有 流程简单 , 硫效率 高 , 脱 工艺 经济合理等 优
点 , 国外 已逐步取 代传统 的 Srt r 工 艺 , 泛 在 t fd eo 广
- 1、下载文档前请自行甄别文档内容的完整性,平台不提供额外的编辑、内容补充、找答案等附加服务。
- 2、"仅部分预览"的文档,不可在线预览部分如存在完整性等问题,可反馈申请退款(可完整预览的文档不适用该条件!)。
- 3、如文档侵犯您的权益,请联系客服反馈,我们会尽快为您处理(人工客服工作时间:9:00-18:30)。
新型络合剂的合成及其络合铁脱硫工艺研究严思明;廖咏梅;王柏云;王富辉【摘要】采用氯磺酸磺化法合成了一种含有磺酸基和羧基的新型络合剂磺化戊二酸(SG),用 SG与乙二胺四乙酸、柠檬酸、FeCl3配制出一种三元络合铁脱硫体系。
在连续脱硫装置中考察脱硫液与硫化氢气体体积比、装置运行时间、填料高度等脱硫工艺条件对复配脱硫体系脱硫效率的影响,在再生装置中考察空气流量、再生时间、再生温度等再生工艺条件对复配脱硫体系再生率的影响。
结果表明:在脱硫液与含硫化氢原料气体积比为0.134、填料高度为0.4 m、脱硫温度为40℃、初始 pH为8.0的条件下,原料气中的 H2 S质量浓度可由227.679 g?m3降到0.011 g?m3,脱除率达99.99%;在空气流量为125 L?h、再生时间为30 min、温度为30℃、初始 pH为8.0的条件下,脱硫剂的再生率达93.24%。
%A new complexing agent SG containing sulfonic group and carboxylic group is synthesized using chlorosulfonic acid and glutaric acid.The ternary complex iron desulfurization system is prepared with SG,EDTA,citric acid and Fe3+.In a continuous desulfurization device,the effect of liquid to feed gas ratio,running time and filler height on the desulfurization efficiency of the ternary system is stud-ied.The effect of air flow rate,regeneration time and temperature on the regeneration for the ternary system is also investigated.The optimum desulfurization conditions are approached as follows:the liq-uid?feed gas ratio of 0.134,the packing height of 0.4 m,the temperature of 40 ℃ and pH of 8.0.In this case,the H2S content of the feed gas is reduced from 227.679 g?m3 to 0.011 g?m3,the removal rate is up to 99.99%.The regeneration rate is up to 93.24% at the optimum regenerationconditions:the air flow of 125 L?h,the regeneration time of 30 min,the regeneration temperature of 30 ℃ and pH of 8.0.【期刊名称】《石油炼制与化工》【年(卷),期】2015(000)002【总页数】6页(P27-32)【关键词】络合剂;络合铁;脱硫;再生;硫化氢【作者】严思明;廖咏梅;王柏云;王富辉【作者单位】西南石油大学化学化工学院,成都 610500;西南石油大学化学化工学院,成都 610500;西南石油大学化学化工学院,成都 610500;西南石油大学化学化工学院,成都 610500【正文语种】中文硫化氢是一种有毒气体。
天然气、焦化气、合成气、炼厂气等气体中都含有一定量的H2S,这些气体在被使用和进一步加工前都必须经过净化处理脱除其中的H2S。
工业上的脱硫方法很多,按脱硫剂的物理形态不同,可分为固体脱硫法(干法)和液体脱硫法(湿法)。
络合铁法脱硫技术是一种以铁为催化剂的湿式氧化脱硫方法,能直接将H2S转变成单质硫,H2S脱除率较高,装置规模小,处理量大,是一种工艺流程简单、脱硫剂可循环利用、对环境友好的脱硫技术。
进一步提高络合铁的稳定性和脱硫效果是络合铁法脱硫技术的主要研究方向[1-4]。
本课题根据络合剂性能及结构要求,采用氯磺酸磺化法合成了一种含有磺酸基和羧基的新型络合剂磺化戊二酸(SG),用SG与乙二胺四乙酸(EDTA)、柠檬酸、FeCl3配制出一种三元络合铁脱硫体系。
在连续脱硫装置中考察脱硫液与含硫化氢原料气体积比(简称液气体积比)、装置运行时间、填料高度等脱硫工艺条件对复配脱硫体系脱硫效率的影响,在再生装置中考察空气流量、再生时间、再生温度、初始pH等再生工艺条件对复配脱硫体系再生率的影响。
1.1 试剂与仪器H2S标准气体(H2S 15%+N2 85%),9.8 MPa,成都浩云气体有限责任公司生产;戊二酸、氯磺酸、柠檬酸、乙二胺四乙酸二钠、三氯化铁,均为化学纯,成都科龙化工试剂厂生产。
电子天平,JD200-4型,沈阳龙腾电子有限公司生产;间歇脱硫装置,自制;连续脱硫装置,自制;再生装置,自制。
1.2 实验装置与流程间歇脱硫装置流程示意见图1。
将一定量原料气通入脱硫装置净化,净化气通入尾气处理槽。
分别测定原料气和净化气中的H2S含量,计算脱硫率。
该装置主要用于脱硫剂配方初步评选的脱硫实验。
连续脱硫装置流程示意见图2。
吸收塔高100 cm,直径6 cm,填料为25mm×25 mm×1.2 mm的塑料环,分别测定原料气和净化气中H2S含量,计算脱硫率。
该装置主要用于考察脱硫工艺条件对络合铁脱硫液脱硫效果的影响。
再生装置流程示意见图3。
络合铁脱硫液的再生是脱硫液中的Fe2+L(L为络合剂)在氧气(空气)作用下生成Fe3+L的过程[5]。
取连续脱硫装置吸收H2S后所得富液1 L置于再生器中,通入设定流量的空气,每隔一定时间,取一定量的脱硫液测定其中Fe2+浓度,计算再生率。
该装置主要用于脱硫液的再生实验,考察再生工艺条件对脱硫液再生率的影响。
1.3 分析方法SG对Fe3+的螯合值采用络合滴定法[6]测定;原料气和净化气中H2S含量采用碘量法[7]测定;脱硫液中的铁离子含量采用重铬酸钾法[8]测定。
1.4 SG的合成羧酸的α-氢原子较活泼,易发生取代反应。
在一定温度下,磺酸基可以取代羧酸的α-氢原子,生成磺化羧酸。
参考文献[9]用氯磺酸对戊二酸进行磺化。
准确称取一定量的戊二酸,加入干燥的三颈瓶中,并用一定量的三氯甲烷溶解。
将用三氯甲烷稀释3倍的氯磺酸逐滴加入三颈瓶中,控制滴加速率,使溶液温度保持在一定范围内。
氯磺酸逐滴加完后加热使溶液温度升高至反应温度。
反应一定时间后,得到含目标产物的混合物,用氨水将其中和至pH为7.0,再用旋转蒸发仪蒸出溶剂,重结晶2次,得到较纯净的产物SG,SG收率约为54%。
脱硫液中Fe3+总含量越高,理论硫容越大。
脱硫液中Fe3+L越多,游离Fe3+越少,Fe3+生成Fe(OH)3沉淀引起Fe3+的损失越小,有利于高效脱除H2S[10]。
通过三因素四水平正交试验,以SG的铁螯合值为评价依据,考察反应温度(a)、戊二酸与氯磺酸摩尔比(b)、反应时间(c)对SG合成反应的影响。
正交试验设计方案及试验结果见表1~表3。
从表3可以看出,极差的大小顺序为Ra>Rb>Rc,即合成条件对螯合值影响由大到小的顺序为:反应温度>戊二酸与氯磺酸摩尔比>反应时间。
对于反应温度,k3>k1>k2>k4;对于戊二酸与氯磺酸摩尔比,k3>k1>k2>k4;对于反应时间,k2>k4>k1>k3。
故SG合成的较佳试验条件为a3,b3,c2,即反应温度为45 ℃、戊二酸与氯磺酸摩尔比为1∶2.6、反应时间为8 h。
1.5 络合铁脱硫液的复配一般情况,单一络合铁脱硫体系的脱硫率随脱硫时间延长而降低较快,脱硫率也不高,通常引入多种配体来提高络合铁脱硫液的稳定性和脱硫效率,本课题采用SG 与常用络合剂复配制备复合脱硫剂。
初步试验结果表明[11],SG+EDTA+柠檬酸+FeCl3复配络合铁脱硫液具有较好的脱硫效果。
采用间歇脱硫装置进行脱硫实验,参考文献[12-14],考虑到能耗和腐蚀,确定脱硫液中总铁离子浓度为0.15 mol/L、脱硫温度为40 ℃、pH为8.0、脱硫液用量为500 mL、原料气H2S质量浓度为227.679 g/m3、进气量为25 mL/min,固定络合剂总浓度,改变各络合剂摩尔浓度,以脱硫时间为4 min时的脱硫率为评价依据,优化脱硫体系配方,实验结果见表4。
由表4可见,5号复配体系的脱硫率最高,达99.21%,且溶液底部无黑色FeS沉淀物。
2.1 络合铁脱硫工艺的研究为了考察复配络合铁脱硫体系的实际应用效果、长期有效性,模拟实际工业过程设计了中试实验装置,即连续脱硫装置,分别考察液气体积比、装置运行时间、填料高度对络合铁脱硫体系脱硫率的影响。
原料气中H2S质量浓度为227.679 g/m3,脱硫液的配方为:0.15 mol/L Fe3+,0.033 mol/L SG,0.052 mol/L EDTA,0.025 mol/L柠檬酸。
再生条件为空气流量100 L/h、温度40 ℃、pH 8.0。
2.1.1 液气体积比对脱硫率的影响脱硫塔的进液量与进气量之比称为液气体积比。
液气体积比越小,能耗和成本越小;但液气体积比太小,净化气中H2S含量可能不达标。
在温度为40 ℃、初始pH为8.0、脱硫时间为0.5 h的条件下,液气体积比对脱硫率的影响见图4。
由图4可见,脱硫率随液气比增大而增大,在液气体积比大于0.134后,脱硫率趋于稳定,此时净化气的硫质量浓度约为0.019 g/m3,能够达到国家标准对硫含量的要求(低于20 mg/m3)。
考虑到脱硫效果及运行成本,最佳液气体积比为0.134。
2.1.2 填料高度对脱硫率的影响在温度为40 ℃、初始pH为8.0、液气体积比为0.134的条件下,填料高度对脱硫率的影响见图5。
由图5可见:脱硫率随填料高度的增加而增大,填料高度在0.4 m以下时,脱硫率与填料高度基本呈线性关系;填料高度大于0.4 m时,脱硫率增加缓慢,因此最优填料高度为0.4 m。
2.1.3 脱硫装置运行时间对脱硫率的影响在温度为40 ℃、初始pH为8.0、液气体积比为0.134的条件下,脱硫时间对脱硫率的影响见图6。
由图6可知,脱硫率随脱硫时间延长而略有减小,脱硫6 h后脱硫率仍能达到99.8%以上,说明脱硫液的脱硫性能稳定。