电子元器件插件工艺检验标准
电子元器件贴片及接插件焊接检验标准

矩形元件 异形元件 元件引脚长度—双面有元件插件元件引脚弯度焊锡量—单面板焊锡量—双面板电路板对应丝印识别:电路板焊接一、焊接流程1、焊接开始前,整理好桌面及周边环境,为电路焊接工作准备一个有条理、整洁的环境。
2、仓库领料,并依据元件明细表核对物料,确保物料正确无误,遇到生疏元件及时向相关负责人询问。
3、依据元件明细表进行电路板焊接。
4、电路板焊接完成后,依据元件明细表核对元件,以保证无错焊、虚焊、漏焊、假焊、桥接。
特别是确认多引脚元件和有极性元件焊接正确。
同样重要的是检查和优化焊点,一块合格的电路板是焊点光滑、过渡均匀、无毛刺、元件排列整齐美观。
二、对焊接点的基本要求1、焊点要有足够的机械强度,保证被焊件在受振动或冲击时不致脱落、松动。
不能用过多焊料堆积,这样容易造成虚焊、焊点与焊点的短路。
2、焊接可靠,具有良好导电性,必须防止虚焊。
虚焊是指焊料与被焊件表面没有形成合金结构。
只是简单地依附在被焊金属表面上。
3、焊点表面要光滑、清洁, 焊点表面应有良好光泽,不应有毛刺、空隙,无污垢,尤其是焊剂的有害残留物质,要选择合适的焊料与焊剂。
三、焊接技术1、手工焊接的基本操作方法①焊前准备,准备好电烙铁以及镊子、剪刀、斜口钳、尖嘴钳、焊料、焊剂(我们这里是指焊锡丝,以下通指焊锡丝)等工具,将电烙铁及焊件搪锡,左手握焊料,右手握电烙铁,保持随时可焊状态。
②用烙铁加热备焊件。
③送入焊料,熔化适量焊料。
④移开焊料,当焊料流动覆盖焊接点,迅速移开电烙铁。
2、电子元器件焊接的顺序是由小到大,由低到高3、元器件焊接注意事项:1)批量将同侧的一端焊盘镀上适量焊锡(仅适用于贴装元器件)。
2)依据文件规定的元器件方向,正确焊接在镀锡焊盘上。
3)批量焊接元件另一端。
4)修复优化焊点,并做清理工作。
5)上述元器件,单个引脚焊接时间在保证焊接质量的前提下,一般1.5-4秒,以避免烫坏焊盘和元器件(对于比较大的元器件如:保险铜件、片形插头等焊接时间4-6秒)。
电子元器件检验标准
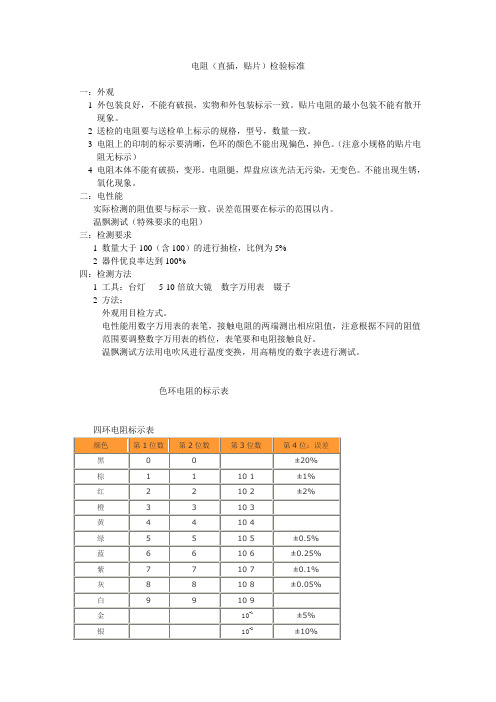
电阻(直插,贴片)检验标准一:外观1 外包装良好,不能有破损,实物和外包装标示一致。
贴片电阻的最小包装不能有散开现象。
2 送检的电阻要与送检单上标示的规格,型号,数量一致。
3 电阻上的印制的标示要清晰,色环的颜色不能出现偏色,掉色。
(注意小规格的贴片电阻无标示)4 电阻本体不能有破损,变形。
电阻腿,焊盘应该光洁无污染,无变色。
不能出现生锈,氧化现象。
二:电性能实际检测的阻值要与标示一致。
误差范围要在标示的范围以内。
温飘测试(特殊要求的电阻)三:检测要求1 数量大于100(含100)的进行抽检,比例为5%2 器件优良率达到100%四:检测方法1 工具:台灯5-10倍放大镜数字万用表镊子2 方法:外观用目检方式。
电性能用数字万用表的表笔,接触电阻的两端测出相应阻值,注意根据不同的阻值范围要调整数字万用表的档位,表笔要和电阻接触良好。
温飘测试方法用电吹风进行温度变换,用高精度的数字表进行测试。
色环电阻的标示表四环电阻标示表四环电阻读取方法五环电阻标示表五环电阻读取方法贴片电阻标示和封装贴片电阻的封装有0402,0603,0805,1206贴片电阻的标示从左往右第一位,第二位是数字位,第三位是表示有多少个0数。
小数点用R表示。
高精度贴片电阻一般是指1%的。
这类电阻用4位表示。
从左往右第一位,第二位,第三位是数字位,第四位是表示有多少个0数。
小数点用R表示。
电容(直插,贴片)检验标准一:外观1 外包装良好,不能有破损,实物和外包装标示一致。
贴片电容的最小包装不能有散开现象。
2 送检的电容要与送检单上标示的规格,型号,数量一致。
3 电容上的印制的标示要清晰,极性标示要准确。
(注意小规格的贴片电容无标示)4 电容腿,焊盘应该光洁无污染,无变色。
不能出现生锈,氧化现象。
5 电容本体不能有破损,变形,电解电容不能有破损,变形,漏液现象。
二:电性能实际检测不能有短路击穿现象,不能有较大的漏电现象。
容值要与标示一致。
电子元器件贴片及接插件焊接检验标准

偏移
矩 形 元 件
异 形 元 件
1
审核: 审核 批准: 批准 XXXX 电子有限公司 发布时间: 发布时间 编 制
编号: 编号 页号: 页号 2 / 8 版本号: 版本号
电子元器件贴片及插件焊接检验标准 电子元器件贴片及插件焊接检验标准
翘起
立起
矩 形 元 件
异 形 元 件
2
1
2
审核: 审核 批准: 批准 XXXX 电子有限公司 发布时间: 发布时间 编 制
电子元器件贴片及插件焊接检验标准 电子元器件贴片及插件焊接检验标准
电容
电阻、电感、 电阻、电感、二极管
5
审核: 审核 批准: 批准 XXXX 电子有限公司 发布时间: 发布时间 编 制
编号: 编号 页号: 页号 6 / 8 版本号: 版本号
电子元器件贴片及插件焊接检验标准 电子元器件贴片及插件焊接检验标准
有 有 有
插 件 焊 接
有 有
有 有 间 有 有
8
元件引脚长度— 元件引脚长度—双面有元件
插件元件引脚弯度
焊锡量— 焊锡量—单面板
焊锡量— 焊锡量—双面板
7
审核: 审核 批准: 批准 XXXX 电子有限公司 发布时间: 发布时间 编 制
编号: 编号 页号: 页号 8 / 8 版本号: 版本号
电子元器件贴片及插件焊接检验标准 电子元器件贴片及插件焊接检验标准
三极管、三端集成块 三极管、
连接器
集成块
6
审核: 审核 批准: 批准 XXXX 电子有限公司 发布时间: 发布时间 编 制
编号: 编号 页号: 页号 7 / 8 版本号: 版本号
电子元器件贴片及插件焊接检验标准 电子元器件贴片及插件焊接检验标准
完整word版)电子元器件检验标准

完整word版)电子元器件检验标准目测、量测、比对、实物装配验证等。
三、差异检验项目差异检验项目清单中列出的部件,需按照规定的检验方法进行检验。
未列出的部件,按照通用检验项目执行。
四、不合格品处理4.1不合格品分类不合格品分为三类:重要不合格品、一般不合格品和提示不合格品。
4.2不合格品处理措施4.2.1重要不合格品重要不合格品指会影响产品的功能、可靠性、安全性的不合格品,必须全部退回或报废。
4.2.2一般不合格品一般不合格品指不会影响产品的功能、可靠性、安全性的不合格品,可由供应商改正后再次送检,或由本公司处理后再使用。
4.2.3提示不合格品提示不合格品指不符合技术规范或标准要求,但不影响产品的功能、可靠性、安全性的不合格品,可由供应商改正后再次送检,或在不影响产品质量的前提下使用。
改写:电子元器件来料检验标准文件编号:SW/QC-2015-2015-11-30A/0生效日期:2015年11月30日版本/版次:0页码/页数:第1页/共6页一、适用范围及检验方案1、适用范围本检验标准适用于PCBA上的贴片件或接插件。
具体下表清单列出了电子元器件的名称和序号。
2、检验方案2.1每批来料的抽检量(n)为5只,接收质量限(AQL)为:CR与MA=0,MI=(1,2)。
当来料少于5只时,则全检,且接收质量限CR、MA与MI=0.2.2来料检验项目=通用检验项目+差异检验项目。
差异检验项目清单中未列出的部件,按通用检验项目执行。
二、通用检验项目序号检验项目规格型号标准要求1 检查型号规格是否符合要求(送货单、实物、BOM表三者上的信息必须一致)2 包装检查包装是否符合要求(有防静电要求的必须有防静电袋/盒等包装,易碎易损的必须用专用包装或气泡棉包装等)3 外观外包装必须有清晰、准确的标识,明确标明产品名称、规格/型号、数量等。
或内有分包装则其上必须有型号与数量等标识。
4 贴片件盘料或带盘包装时,不应有少料、翻面、反向等。
电子元器件贴片及插件焊接检验规范

6.7
锡珠、锡渣
直径大于0.2mm或长度大于0.2mm的锡渣黏在底板的表面上,或焊锡球违反最小电气间隙(图11),
即锡渣在引脚、焊点0805及以下贴片元件上均不可接受;每600mm多于5个直径小于0.2mm的焊锡珠、锡
2
渣不可接受。
a)元件两脚间有锡渣
b)贴片元件上有锡渣
6
c)底板上锡渣大于0.2mm
d)锡渣示意图
图11锡珠锡渣-不可接受状态
6.8
少锡、薄锡
引脚、孔壁和可焊区域焊点润湿小于270º(图12),或焊角未形成弯月形的焊缝角,润湿角小
于15º(图14),或焊料未完全润湿双面板的金属孔,焊锡的金属化孔内填充量小于50%(图13、15),
均不可接受。
图12焊点润湿小于270º
图13金属化孔内填充量小
的润湿角大于90º(图4);不润湿(图5),导致焊料在表面上形成小球或小珠,就象蜡面上的水珠。
焊缝会凸起并且没有羽状边缘呈现,出现缩锡现象。以上三种情况均不可接受。图6所示为焊接质量判
定标准。
图3引脚与焊料润湿角大于90º
图4焊盘与焊料润湿角大于90º
4
图5焊点不润湿
图6焊接质量判定标准
6.3
空焊
基材元器件插入孔全部露出,元器件引脚及焊盘未被焊料润湿(图7)。不可接受。
Q/FVFM
厦门誉信实业有限公司企业标准
Q/FVFM2002.17-2015
电子元器件贴片及插件焊接
检验规范
2015-02-10发布
2015-06-01实施
发布
厦门誉信实业有限公司
前
言
本标准按照GB/T1.1-2009《标准化工作导则第1部分:标准的结构和编写规则》制定。
PCB插件、焊接检验标准

PCB插件、焊接检验标准一、目的规范本公司生产的半成品检验,确保产品质量要求,防止不良品流出。
二、范围适用于本公司内所有半成品板的外观检验和特性检验。
三、检验要求3.1 安装元器件准位要求3.1.1 元器件引线成形元器件引线成形要求同类元件保持高度一致,成形元器件两端余量一致。
元器件引脚同焊盘引脚对应整齐,无明显倾斜。
元器件引线不允许出现超过引线截面积10%的缺口或变形。
外露基体金属不超过引线可焊表面面积的5%。
(GBT19247.1-2003;6.4)引线从元器件本体或弯曲半径前的容焊点的伸出长度,至少应为引线直径或厚度,不能小于0.8mm。
(GBT19247.3-2003;4.2.3)如图1:最大引线直径/mm 最小弯曲半径R<0.8 直径/厚度0.8~1.2 1.5倍直径/厚度>1.2 2倍直径/厚度图1 引线弯曲引线成形要求应使元器件衬底表面与印制板表面的不平行度(即元器件斜面)最大间距≤2.0mm。
(GBT19247.2-2003/IEC61191-2:1998;4.2.1)如图23.1.2 元器件引线的弯曲元器件弯曲要求不允许延伸到密封部分内。
引线弯曲半径(R)必须大于引线标称厚度。
上、下弯曲的引线部分和安装的连接盘之间的夹角最小45°,最大为90°。
(GBT19247.2-2003/IEC61191-2:1998;4.2.2)如图2:图2双引线元器件独立垂直安装时,较大的侧面应垂直于印制板表面,最多倾斜15°。
(GBT19247.3-2003;A.4.2)3.1.3 晶体管、二极管等极性元器件的安装元器件要求按极性正确安装保持元器件极性标识同电路板上极性标识一致。
元器件比较密集的地方要求各引脚分别套上不同彩色的塑料套管,防止碰极短路。
对于一些大功率晶体管,要求固定散热片。
3.1.4 集成电路的安装集成电路方向正确安装,插到低,保持两边余量一致。
不允许插错、插反。
电子元器件贴片及其接插件焊接检验规范标准
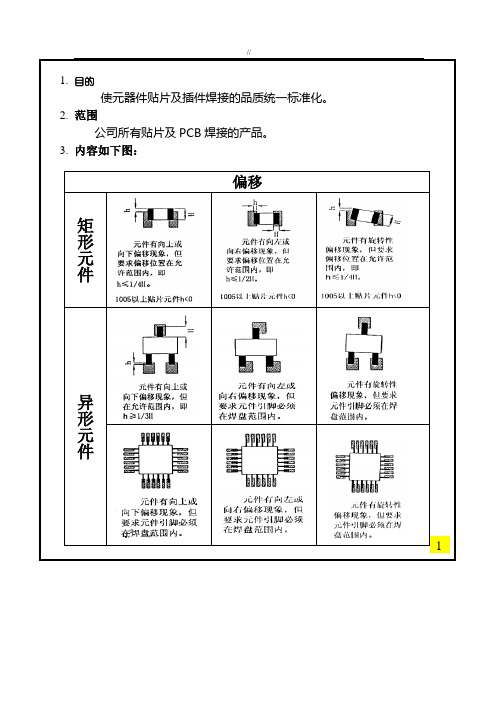
2 1贴片焊接包焊拉尖沾胶焊锡量明显太多,超出焊盘范围,且高出元件焊端。
焊接有拉尖现象。
焊盘有沾胶现象,但必须在规定范围内:h1≤0.2mm h ≤1/4H焊锡量明显太多,超出焊盘范围,且高出元件焊端。
焊接有拉尖现象。
少锡0805以下贴片矩形元件h<1/3H 判定为少锡. 1005贴片矩形元件h <1/4H 判定为少锡.H >2mm 以上贴片矩形元件 .h <0.5mm 判定为少锡.45678 电路板对应丝印识别:电路板焊接一、焊接流程1、焊接开始前,整理好桌面及周边环境,为电路焊接工作准备一个有条理、整洁的环境。
2、仓库领料,并依据元件明细表核对物料,确保物料正确无误,遇到生疏元件及时向相关负责人询问。
3、依据元件明细表进行电路板焊接。
4、电路板焊接完成后,依据元件明细表核对元件,以保证无错焊、虚焊、漏焊、假焊、桥接。
特别是确认多引脚元件和有极性元件焊接正确。
同样重要的是检查和优化焊点,一块合格的电路板是焊点光滑、过渡均匀、无毛刺、元件排列整齐美观。
二、对焊接点的基本要求1、焊点要有足够的机械强度,保证被焊件在受振动或冲击时不致脱落、松动。
不能用过多焊料堆积,这样容易造成虚焊、焊点与焊点的短路。
2、焊接可靠,具有良好导电性,必须防止虚焊。
虚焊是指焊料与被焊件表面没有形成合金结构。
只是简单地依附在被焊金属表面上。
3、焊点表面要光滑、清洁,焊点表面应有良好光泽,不应有毛刺、空隙,无污垢,尤其是焊剂的有害残留物质,要选择合适的焊料与焊剂。
三、焊接技术1、手工焊接的基本操作方法①焊前准备,准备好电烙铁以及镊子、剪刀、斜口钳、尖嘴钳、焊料、焊剂(我们这里是指焊锡丝,以下通指焊锡丝)等工具,将电烙铁及焊件搪锡,左手握焊料,右手握电烙铁,保持随时可焊状态。
②用烙铁加热备焊件。
③送入焊料,熔化适量焊料。
④移开焊料,当焊料流动覆盖焊接点,迅速移开电烙铁。
2、电子元器件焊接的顺序是由小到大,由低到高3、元器件焊接注意事项:1)批量将同侧的一端焊盘镀上适量焊锡(仅适用于贴装元器件)。
PCB插件、焊接检验标准
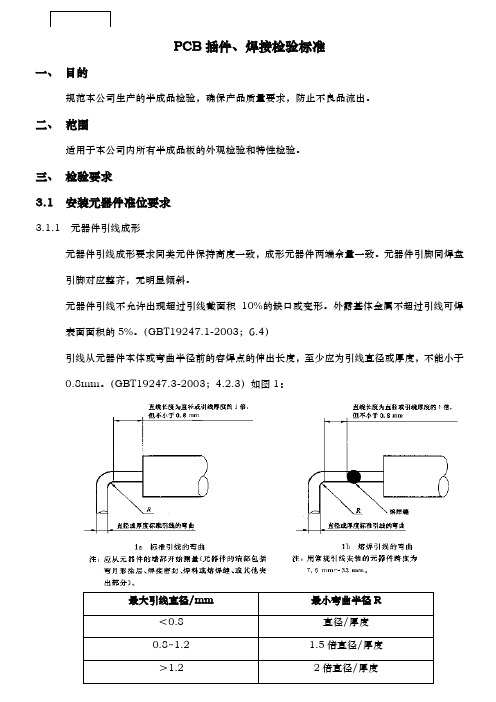
PCB插件、焊接检验标准一、目的规范本公司生产的半成品检验,确保产品质量要求,防止不良品流出。
二、范围适用于本公司内所有半成品板的外观检验和特性检验。
三、检验要求3.1 安装元器件准位要求3.1.1 元器件引线成形元器件引线成形要求同类元件保持高度一致,成形元器件两端余量一致。
元器件引脚同焊盘引脚对应整齐,无明显倾斜。
元器件引线不允许出现超过引线截面积10%的缺口或变形。
外露基体金属不超过引线可焊表面面积的5%。
(GBT19247.1-2003;6.4)引线从元器件本体或弯曲半径前的容焊点的伸出长度,至少应为引线直径或厚度,不能小于0.8mm。
(GBT19247.3-2003;4.2.3)如图1:最大引线直径/mm 最小弯曲半径R<0.8 直径/厚度0.8~1.2 1.5倍直径/厚度>1.2 2倍直径/厚度图1 引线弯曲引线成形要求应使元器件衬底表面与印制板表面的不平行度(即元器件斜面)最大间距≤2.0mm。
(GBT19247.2-2003/IEC61191-2:1998;4.2.1)如图23.1.2 元器件引线的弯曲元器件弯曲要求不允许延伸到密封部分内。
引线弯曲半径(R)必须大于引线标称厚度。
上、下弯曲的引线部分和安装的连接盘之间的夹角最小45°,最大为90°。
(GBT19247.2-2003/IEC61191-2:1998;4.2.2)如图2:图2双引线元器件独立垂直安装时,较大的侧面应垂直于印制板表面,最多倾斜15°。
(GBT19247.3-2003;A.4.2)3.1.3 晶体管、二极管等极性元器件的安装元器件要求按极性正确安装保持元器件极性标识同电路板上极性标识一致。
元器件比较密集的地方要求各引脚分别套上不同彩色的塑料套管,防止碰极短路。
对于一些大功率晶体管,要求固定散热片。
3.1.4 集成电路的安装集成电路方向正确安装,插到低,保持两边余量一致。
不允许插错、插反。
- 1、下载文档前请自行甄别文档内容的完整性,平台不提供额外的编辑、内容补充、找答案等附加服务。
- 2、"仅部分预览"的文档,不可在线预览部分如存在完整性等问题,可反馈申请退款(可完整预览的文档不适用该条件!)。
- 3、如文档侵犯您的权益,请联系客服反馈,我们会尽快为您处理(人工客服工作时间:9:00-18:30)。
元件插件工艺及检测标准一、目的:使LED电源PCB板组装(PCBA)工作人员掌握基本的电子元件操作工艺;规范电子元件在PCBA上的插件/焊锡等操作要求, 并为PCBA检验提供检查标准二、范围:适用于本公司PCBA(LED电源PCB的插件/焊锡)的工艺操作和检查。
三、参考文件:工艺要求参照:IPC-A-610B (Class Ⅱ)四、定义:PCBA: Printed CircuitBoard Assembly (印刷线路板组装)AX: (轴向)RD: Radial (径向)HT: Horizontal (卧式)VT: Vertical (立式)SMT: Surface Mount Technology (表面安装技术)SMD: Surface Mount Device(表面安装元件)SMC:Surface Mounting Components(表面安装零件)SIP: Simplein-line package 单列直插式封装SOJ:Small Outline J-leadpackage (具有J型引线的小外形封装) SOP: Small Outline package (小外形封装)SOT: Small Outline Transistor (小外形晶体管)IC:IntegratedCircuit (集成电路)PR: Preferred (最佳)AC: Acceptable (可接受的)RE:Reject (拒收)五、元件类别:电阻,电容, 电感, 二极管, 三极管, IC, ICSocket,晶体,整流器, 蜂鸣器, 插头,插针, PCB,磁珠等, 在此文件中, 根据本公司情况暂时定义电阻, 电容,电感, 二极管, 三极管,MOS管工艺标准六、元件插件工艺及检测标准1. 卧式(HT) 插元件卧式插元件主要是小功率,低容量, 低电压的电阻,电容,电感, Jumpe r(跳线),二极管, IC等,PCBA上的组装工艺要求和接收标准如下: 1.1元件在基板上的高度和斜度1.1.1轴向(AX)元件1.1.1.1功率小于1W的电阻, 电容(低电压,小容量的陶瓷材料),电感, 二极管,IC等元件PR:元件体平行于PCB板面且紧贴PCB板面, 如图示:AC:元件体与PCB表面之间最大倾斜距离(D)不大于3mm, 元件体与PCB表面最低距离(d)不大于0.7mm,如图示:RE: 元件体与PCB板面距离D>3mm, 或d>0.7mm1.1.1.2耗散功率大于或等于1W的元件PR: 元件体平行于PCB板面且与PCB板面之间的距离D≥1.5mm,如图示:AC:元件体与PCB板面之间的距离D≥1.5mm, 元件体与PCB板面的平行不作要求RE: 元件体与PCB板面之间的距离D≤1.5mm1.1.1.3ICPR: 元件体平行于PCB, IC引脚全部插入焊盘中, 引脚突出PCB面1.mm,倾斜度=0, 如图示:AC:IC引脚全部插入焊盘中, 引脚突出PCB面大于0.5mm, 如图:RE: IC引脚突出PCB面小于0.5mm, 或看不见元件引脚, 如图:1.1.2径向(RD)元件(电容, 晶振)PR: 元件体平贴于PCB板面,如图示:AC:元件脚最少有一边贴紧PCB板面,如图示:RE:元件体未接触PCB板面,如图示:1.2元件的方向性与基板对应符号的关系:1.2.1 轴向(AX)无极性元件(电阻,电感, 小陶瓷电容等)PR: 元件插在基板中心标记且元件标记清晰可见,元件标记方向一致(从左到右,从上到下), 如图:AC: 元件标记要求清晰,但方向可不一致, 如图:RE: 元件标记不清楚或插错孔位, 如图:1.2.2轴向(AX)有极性元件, 如二几管, 电解电容等PR: 元件的引脚插在对应的极性脚位, 元件标记清晰可看见,如图:AC:元件的引脚必须插在相应的极性脚位上,元件标记可看见, 如图:RE: 元件的引脚未按照极性方向插在相应的脚位上, 如图:1.3元件引脚成形与曲脚1.3.1引脚成形PR: 元件体或引脚保护层到弯曲处之间的距离L>0.8mm, 或元件脚直径弯曲处无损伤,如图:A元件脚直径或厚度( D半径( R )/T )≤0.8mm 1 X D0.8~1.2mm 1.5X D≥1.2mm 2 X DRE: ( 1) 元件体与引脚保护弯曲处之间L<0.8mm,且弯曲处有损伤, 如图:( 2) 或元件脚弯曲内径R小于元件直径, 如图:1.3.2屈脚PR: 元件屈脚平行于相连接的导体,如图:AC:屈脚与相间的裸露导体之间距离(H)大于两条非共通导体间的最小电气间距, 如图:RE: 屈脚与相间的裸露导体之间距离(H)大于两条非共通导体间的最小电气间距,如图:1.4元件损伤程度1.4.1元件引脚的损伤PR: 元件引脚无任何损伤, 弯脚处光滑完好, 元件表面标记清晰可见, 如图:AC: 元件引脚不规则弯曲或引脚露铜,但元件或部品引脚损伤程度小于该引脚直径的10%,如图:RE:( 1 )元件引脚受损大于元件引脚直径的10%,如图:(2)严重凹痕锯齿痕,导致元件脚缩小超过元件的10%,如图:1.4.2 IC元件的损伤PR: IC 元件无任何损伤, 如图:AC: 元件表面受损, 但未露密封的玻璃,如图:RE:元件表面受损并露出密封的玻璃, 如图:1.4.3轴向(AX)元件损伤PR: 元件表面无任何损伤,如图:AC:元件表面无明显损伤,元件金属成份无暴露,如图:RE:(1 )元件面有明显损伤且绝缘封装破裂露出金属成份或元件严重变形,如图:(2 )对于玻璃封装元件,不允许出现小块玻璃脱落或损伤.1.5元件体斜度PR:元件体与其在基板上两插孔位组成的连线或元件体在基板上的边框线完全平行,无斜度,如图:AC:元件体与其在基板上两插孔位组成的连线或元件体在基板上的边框线斜度≤1.0mm,如图:RE: 元件体与其在基板上两插孔位组成的连线或元件体在基上的边框线斜度>1.0mm,如图:2.立式(VT)插元件2.1.1轴向(AX)元件PR: 元件体与PCB板面之间的高度H在0.4mm-1.5mm之间, 且元件体垂直于PCB板面, 如图:AC: H在0.4-3mm之间, 倾斜Q<15°,如图:RE: 元件体与PCB板面倾斜, 且间距H<0.4mm或H>3mm或Q>15°.2.1.2径向(RD)元件2.1.2.1引脚无封装元件PR: 元件体引脚面平行于PCB板面, 元件引脚垂直于PCB板面,且元件体与PCB板面间距离为0.25-2.0mm, 如图:AC: 元件体与PCB板面斜倾度Q小于15°, 元件体与PCB板面之间的间隙H在0.20-2.0mm之间,三极管离板面高度最高大于4.0mm,如图:RE: 元件与PCB板面斜倾角Q>15°或元件体与PCB板面的间隙H>2.0mm或三极管>4.0mm.2.1.2.2:引脚有封装元件PR: 元件垂直PCB板面,能明显看到封装与元件面焊点间有距离,如图:AC:元件质量小于10g且引脚封装刚好触及焊孔且在焊孔中不受力,而焊点面的引脚焊锡良好(单面板), 且该元件在电路中的受电压<240VAC或DC,如图:RE: 引脚封装完全插入焊孔中,且焊点面焊锡不好,可看见引脚封装料, 如图:2.2元件的方向性与基板符号的对应关系2.2.1轴向(AX)元件PR: 元件引脚插入基板时,引脚极性与基板符号极性完全吻合一致,且正极一般在元件插入基板时的上部,负极在下部,如图:AC:元件引脚插入基板时,引脚极性与基板符号极性吻合一致,但元件在插入基板时,正极在上和负极在下不作要求,如图:RE: 元件引脚插入基板时,引脚极性与基板符号极性刚好相反,如图:2.2.2径向(RD)元件AC: 元件引脚极性与基板符号极性一致,如图:RE: 元件体引脚极性与基板符号极性相反,如图:2.3元件引脚的紧张度PR:元件引脚与元件体主轴之间夹角为0°(即引脚与元件主轴平行, 垂直于PCB板面), 如图:AC: 元件引脚与元件体主轴袒闪角Q<15°,如图:RE: 元件引脚与元件体主轴之间夹角Q>15°.2.4元件引脚的电气保护在PCBA板上有些元件要有特殊的电气保护,则通常使用胶套,管或热缩管来保护电路PR:元件引脚弯曲部分有保护套,垂直或水平部分如跨过导体需有保护套且保护套距离插孔之间距离A为1.0mm-2.0mm,如图:AC: 保护套可起到防止短路作用, 引脚上无保护套时, 引脚所跨过的导体之间的距离B≥0.5mm, 如图:RE: 保护套损坏或A>2.0mm时, 不能起到防止短路作用或引脚上无保护套时,或引脚所跨过的导体之间距离B<0.5mm,如图:2.5元件间的距离PR: 在PCBA板上,两个或以上踝露金属元件间的距离要D≥2.0mm,如图:AC: 在PCBA板上, 两个或以上踝露金属元件的距离最小D≥1.6mm, 如图:RE: 在PCBA板上, 两个或以上踝露金属元件间的距离D<1.6mm,如图:2.6元件的损伤PR:元件表面无任何损伤,且标记清晰可见,如图:AC: 元件表面有轻微的抓、擦、刮伤等,但未露出元件基本面或有效面,如图:RE: 元件面受损并露出元件基本面或有效面积,如图:3. 插式元件焊锡点工艺及检查标准3.1单面板焊锡点单面板焊锡点对于插式元件有两种情形:a.元件插入基板后需曲脚的焊锡点b.元件插入基板后无需曲脚(直脚)的焊锡点3.1.1标准焊锡点之外观特点A.焊锡与铜片, 焊接面, 元件引脚完全融洽在一起, 且可明显看见元件脚B. 锡点表面光滑,细腻, 发亮C. 焊锡将整个铜片焊接面完全覆盖,焊锡与基板面角度Q<90°, 标准焊锡点如图示:3.1.2可接受标准A. 多锡焊接时由于焊锡量使用太多,使零件脚及铜片焊接面均被焊锡覆盖着,使整个锡点象球型,元件脚不能看到.AC:焊锡点虽然肥大Q>90°,但焊锡与元件脚,铜片焊接面焊接良好,焊锡与元件脚,铜片焊接面完全融洽在一起,如图:RE:焊锡与元件引脚, 铜片焊接状况差,焊锡与元件脚/铜片焊接面不能完全融洽在一起,且中间有极小的间隙, 元件引脚不能看到, 且Q>90°,如图:B. 上锡不足(少锡)焊锡、元件引脚、铜片焊接面在上锡过程中,由于焊锡量太少,或焊锡温度及其它方面原因等造成的少锡.AC: 整个焊锡点,焊锡覆盖铜片焊接面≥75%, 元件脚四周完全上锡,且上锡良好,如图:RE: 整个焊锡点, 焊锡不能完全覆盖铜片焊接面<75%,元件四周亦不能完全上锡,锡与元件脚接面有极小的间隙, 如图:C. 锡尖AC: 焊锡点锡尖, 只要该锡尖的高度或长度h<1.0mm,而焊锡本身与元件脚、铜片焊接面焊接良好,如图:RE: 焊锡点锡尖高度或长度h≥1.0mm,且焊锡与元件脚、铜片焊接面焊接不好, 如图:D. 气孔AC: 焊锡与元件脚、铜片焊接面焊接良好, 锡点面仅有一个气孔且气孔要小于该元件脚的一半, 或孔深<0.2mm,且不是通孔, 只是焊锡点面上有气孔, 该气孔没有通到焊接面上, 如图:RE:焊锡点有两个或以上气孔,或气孔是通孔, 或气孔大于该元件脚半径,如图:D. 起铜皮AC: 焊锡与元件脚、铜片焊接面焊接良好,但铜皮有翻起h<0.1mm,且铜皮翻起小于整个Pad位的30%, 如图:RE:焊锡与元件脚、铜片焊接面焊接一般, 但铜皮翻起h>0.1mm,且翻起面占整个Pad位的的30%以上, 如图:E. 焊锡点高度对焊锡点元件脚在基板上的高度要求以保证焊接点有足够的机械强度AC: 元件脚在基板上高度0.5<h≤2.0mm, 焊锡与元件脚,铜片焊接面焊接良好,元件脚在焊点中可明显看见, 如图:RE: 元件脚在基板上的高度h<0.5mm或h>2.0mm,造成整个锡点为少锡, 不露元件脚, 多锡或大锡点等不良现象,如图:注:对用于固定零件之插脚如变压器或接线端子之插脚高度可接受2.5mm为限.3.1.3不可接受的缺陷焊锡点在基板焊锡点中有些不良锡点绝对不可接收, 现列举部分如下RE: ( 1)冷焊(假焊/虚焊)如图:(2 )焊桥(短路),锡桥,连焊,如图:( 3 )溅锡, 如图:( 4 )锡球, 锡渣,脚碎,如图:(5) 豆腐渣,焊锡点粗糙, 如图:( 6 ) 多层锡, 如图:( 7)开孔(针孔),如图:3.2双面板焊锡点双面板焊锡点同单面板焊锡点相比有许多的不同点:a.双面板之PAD位面积较小(即外露铜片焊接面积)b.双面板每一个焊点PAD位都是镀铜通孔鉴于此两点, 双面板焊锡点在插元件焊接过程及维修过程就会有更高要求, 其焊锡点工艺检查标准就更高, 下面将分别详细讨论双面板之焊锡点收货标准3.2.1标准焊锡点之外观特点A.焊锡与元件脚,通孔铜片焊接面完全融洽在一起, 且焊点面元件脚明显可见.B.元件面和焊点面的焊锡点表面光滑, 细腻, 发亮.C.焊锡将两面的Pad位及通孔内面100%覆盖, 且锡点与板面角度Q<90°, 如图:3.2.2可接收标准A.多锡焊接时由于焊锡量过多,使元件脚,通孔, 铜片焊接面完全覆盖,不是使焊接时的两面元件脚焊点肥大, 焊锡过高AC:焊锡点元件面引脚焊锡虽然过多,但焊锡与元件脚,通孔铜片焊接面两面均焊接良好, 且Q<90°,如图:RE:焊锡点元件面引脚肥大, 锡点面引脚锡点肥大,不能看见元件脚且焊锡与元件脚, 铜片焊接面焊接不良, 如图:B.上锡不良AC: 焊锡与元件脚,通孔铜片焊接面焊接良好, 且焊接锡在通孔铜片内的上锡量高度h>75%·T(T: 基板厚度),从焊点面看上锡程度大于覆盖元件脚四周(360°)铜片的270°, 或从元件面能清楚的看到通孔铜片中的焊锡, 如图:RE:从焊点面看, 不能清晰的看到元件引脚和通孔铜片焊接面中的焊锡或在通孔铜片焊接面完全无焊锡或元件引脚到Pad位无焊锡或h<75%·T或上锡角度Q<270°(针对SolderPad360°而言),如左图:C. 锡尖在焊接过程中由于焊锡温度过低或焊接时间过长等原因造成的锡尖AC: 焊锡点的锡尖高度或长度h<1.0mm,而焊锡本身与元件引脚及通孔铜片焊接面焊接良好,Q<90°,如图:RE:焊锡点锡尖高度或长度h≥1.0mm,且焊锡与元件引脚, 通孔铜片焊接面焊接不良, 如图:D.气孔AC:焊锡与元件脚,铜片焊接面焊接良好, 锡点面仅有一个气孔且气孔要小于该元件脚的1/2, 且不是通孔(只是焊锡点表面有气孔,未通到焊接面上), 如图:RE:焊锡点上有两个或以上气孔, 或气孔是通孔, 或气孔大于该元件脚直径的1/2,焊点面亦粗糙,如图:E.起铜皮AC: 焊锡点与元件脚, 通孔铜片焊接面焊接良好, 但铜皮翘起高度h<0.1mm,翘起面积S<30%·F (F为整个焊盘的面积)RE: 焊锡与元件脚, 通孔铜片焊接面焊接质量一般,但铜皮翘起h>0.1mm, 且翘起面积S>30%·F(F为整个焊盘的面积),如图:F.焊接点高度PR:元件脚在焊锡点中明显可见, 引脚露出高度h=0.1mm,且焊锡与元件脚,通孔铜片焊接面焊接良好,如图:AC: 元件脚露出基板的高度0.5mm<h≤2.0mm,元件脚在焊锡点中可明显看见, 且焊锡与元件脚,通孔铜片焊接面焊接良好. (但对于通孔铜片焊接面的双面PCB板, 基板厚度T>2.3mm, 则元件脚露出基板高度可接收0<h≤0.5mm),如图:RE:元件脚露出基板高度h<0.5mm或h>2.0mm (仅对于厚度T≤2.3mm的双面板), 造成整个锡点为少锡, 不露元件脚, 多锡或大锡点等不良现象,且焊接不良,如图:3.2.3 不可接收的缺陷焊锡点:在双面板(镀铜通孔铜片焊接面)焊锡点中,有些不良焊点绝对不可接收, 其不可接收程度完全同于单面板,详细请参考3.1.3。