浅谈动车组轮对制造工艺要点
动车组制造工艺4

A’
A
板条中间受拉两侧受压,
板条端面的位移就是残余变形。
焊接后的应力
23/122
第四章 动车组车体装配焊接工艺
4. 结论:
• 板条焊接时,在温度超过600℃的焊缝区域产生了压缩
塑性变形,焊接后,板条焊缝区域的长度将比原来有 所缩短,根据平面假设,此时,板条焊缝区域受有拉
应力,远离焊缝区域受有压应力,形成一个新的平衡
12/122
第四章 动车组车体装配焊接工艺
(3)电阻焊的应用
电阻焊适用于薄板的搭接和型材的对接,在航 空、汽车、地铁车辆、锅炉、自行车、量具刃具以 及无线电器件等工业领域中都得到了广泛应用。 如国外某些铝制高速地铁车辆的制造,每台车 辆约有10000个焊点,一辆轿车至少有5000个焊点。 电阻焊还可用于客车侧墙板与侧立柱的连接,底架 侧梁等纵向梁的拼接等。
15/122
第四章 动车组车体装配焊接工艺
3. 钨极氩弧焊(TIG焊)
钨极氩弧焊是钨极气体保护焊(TIG)的一种。它是在 氩气保护层下,以燃烧于非熔化电极(钨极)与焊件间的电 弧作为热源,熔化铝合金填充焊丝及基体金属而实现焊接 的一种方法。
16/122
第四章 动车组车体装配焊接工艺
(1)钨极氩弧焊的优点
(1) 材料的线膨胀系数。线膨胀系数大的材料,焊后收 缩量也大。不锈钢和铝合金的线膨胀系数比低碳钢 大。所以焊接变形也比低碳钢大。 (2) 焊缝的纵向收缩随焊缝长度的增加而增加。 (3) 焊缝的横向收缩则随焊缝宽度的增加而增加。如前 所述,一条焊缝的横向收缩量约相当于2~4m长焊 缝的纵向收缩量,所以焊缝的横向收缩不可忽视。
– 熔化极氩弧焊(MIG焊)
钨极氩弧焊(TIG焊)
3/122
CRH2动车组轮对检修流程及改进设计
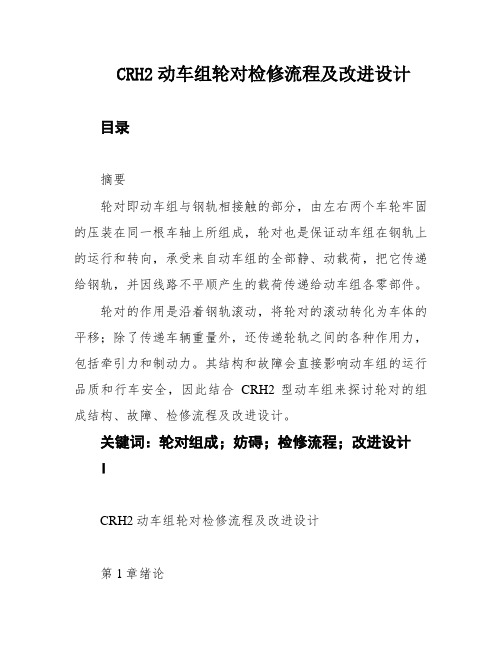
CRH2动车组轮对检修流程及改进设计目录摘要轮对即动车组与钢轨相接触的部分,由左右两个车轮牢固的压装在同一根车轴上所组成,轮对也是保证动车组在钢轨上的运行和转向,承受来自动车组的全部静、动载荷,把它传递给钢轨,并因线路不平顺产生的载荷传递给动车组各零部件。
轮对的作用是沿着钢轨滚动,将轮对的滚动转化为车体的平移;除了传递车辆重量外,还传递轮轨之间的各种作用力,包括牵引力和制动力。
其结构和故障会直接影响动车组的运行品质和行车安全,因此结合CRH2型动车组来探讨轮对的组成结构、故障、检修流程及改进设计。
关键词:轮对组成;妨碍;检修流程;改进设计ICRH2动车组轮对检修流程及改进设计第1章绪论1.1研究背景近几年,跟着高速动车组的迅速发展,高铁已经我国大多数人出行选择的交通体式格局,而轮对是高速动车在轨道上运行必不可少的元件之一。
动车的全部重量通过轮对支持在钢轨上;通过轮对与钢轨的黏着发生牵引力或制动力;通过轮对滚动使动车前进。
另外,轮对在动车运行中的承载情形比较繁重,当车轮经钢轨接头、道岔等线路不屈顺处时,轮对直接蒙受全部垂向和侧向的冲击。
轮对还蒙受很大的静载荷、动作用力和组装应力,闸瓦制动时还发生热应力,因此要求它有足够的强度。
为了保证动车的运行安全,适当选择轮对的部件材料,坚持轮对的正确组装和良好的运行状态以及定期及时检测与修理是相当紧张的。
1.2研究思路在动车组轮对的优化研讨进程中,以动车组轮对的组成开始介绍,然后了解动车组轮对的常见妨碍以及其检修办法,再对动车组轮对的检修流程进行研讨,联合了CRH2型动车组轮对,再通过自己的想法与意见提出动车组轮对的检修流程改进设计。
1第2章轮对的组成2.1轮对组成的内容轮对普通由车轴、轮心和轮箍组成,高速动车组普通采用整体车轮,以是不再有轮心和轮箍之分。
另外,高速动车组轮对还有动力轮对组成和非动力轮对组成的区分,其中动力轮对上通常装有齿轮箱,如图1所示。
图1轮对组成图动力轮对组成装置在动力转向架上,包含一个动力轮对轴箱装置和一个非动力轮对轴箱装置;非动力轮对组成装置在非动力转向架上,包括两个非动力轮对轴箱装置。
CRH3动车轮对压装选配
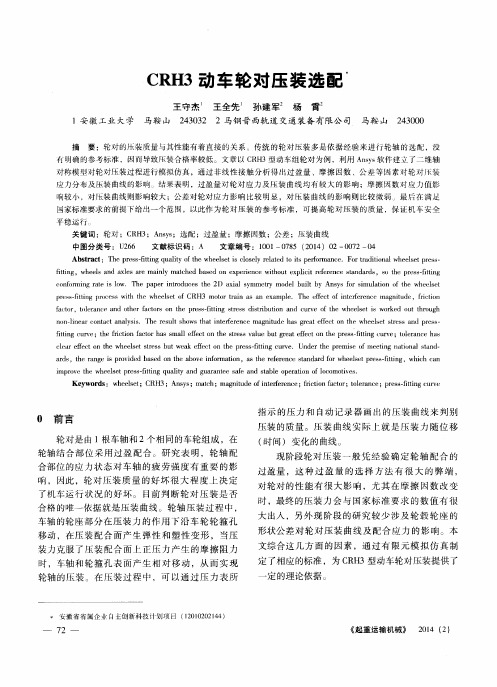
有明确的参考标 准 ,因而导致压装合格率较低 。文章 以 C R H 3型动车组轮对为例 ,利用 A n s y s 软件 建立 了二 维轴 对称模 型对轮 对压装过程进行模拟仿真 ,通过 非线性接 触分析 得 f I J 过盈 量 、摩擦 因数 、公差 等 素 对轮对 装
应 力 分 布及 压 装 曲线 的影 响 结 果 表 明 ,过 盈 量 对 轮 对 应 力 及 装 曲 线 均 有 较 大 的 影 响 ;摩 擦 因 数 对 应 力值 影 响较 小 ,对 装 曲线 则 影 响较 大 ;公 差 对 轮 对 应 力 影 响 比 较 明显 ,对 压 装 曲 线 的影 响 则 比较 微 弱 。最 后 孑 F 满 足
f a c t o r ,t o l e r a n c e a n d o t h e r f a e t o r s o n t h e p r e s s — i f t t i n g s t r e s s d i s t r i b u t i o n a n d c u r v e o f t h e w h e e l s e t i s w o r k e d o u t t h r o u g h mm— l i n e a r c o n t a c t a n a l y s i s .T h e r e s u l t s h o ws t h a t i n t e f r e r e n c e ma g n i t u d e h a s g r e a t e f f e c t o n t h e w h e e l s e t s t r e s s a n d p r e s s — i f t t i n g C H I V e ;t h e f r i c t i o n f a c t o r h a s s ma l l e f f e c t o n t h e s t r e s s v a l u e b u t g r e a t e f e c t o n t h e p r e s s — i f t t i n g c u l w e ;t o l e r a n c e h a s (  ̄ l e a r e f f e c t o n t h e w h e e l s e t s t r e s s b u t we a k e f f e c t o n t h e p r e s s — i f t t i n g c u r v e .U n d e r t h e p r e mi s e o f me e t i n g n a t i o n a l s t a n d —
动车组轮对多边形危害及预防措施分析

动车组轮对多边形危害及预防措施分析一、危害分析:动车组的轮对多边形问题是指轮对在使用过程中由于摩擦力的作用,在车轮的外圈上出现断面不规则的多边形磨损问题。
这种磨损如果得不到及时有效的处理,将对列车的运行安全和车辆的使用寿命产生严重的危害。
1. 影响列车安全运行:轮对多边形磨损导致车轮的外圈不平整,当车轮与钢轨接触时,容易产生动态不平衡力,造成列车的横向振动,进一步影响车体的稳定性,甚至使列车出轨。
2. 增加列车运行噪音:多边形磨损使车轮与钢轨之间的接触状态不规则,从而增加列车在运行过程中的噪音。
这不仅对列车乘客的舒适度产生负面影响,也对周围环境造成噪音污染。
3. 加剧车轮与轨道的磨损: 多边形磨损引起轮对与轨道的接触力分布不均匀,使得车辆在行驶过程中对轨道的磨损加剧,形成恶性循环,降低轨道使用寿命。
4. 轮轴和承载构件的损坏:多边形磨损增加了轮轴和承载构件的受力情况,容易导致轮轴断裂、承载构件的疲劳裂纹和变形等严重故障。
二、预防措施:为了有效预防和解决动车组轮对多边形问题,需要采取以下措施:1. 均衡受力:通过定期对车轮进行动平衡校正,保障车轮在高速运行中的动态平衡,减小多边形磨损的产生。
2. 加强轮对磨损检测:建立完善的轮对检测机制,及时发现轮对多边形磨损现象,并采取相应的维修和更换措施。
3. 提高轮对加工质量:加强轮对的制造工艺控制,提高轮对的制造质量,减小多边形磨损的风险。
4. 进行轮对磨损监测:采用先进的监测技术,对轮对磨损情况进行实时监测,并及时采取维修和更换措施。
如采用超声波或激光检测技术对轮对的磨损情况进行在线监测。
5. 定期维护保养:建立健全的轮对维护保养制度,定期对轮对进行检查、清洗、润滑和调整,及时发现和处理问题。
6. 加强人员培训:对相关人员进行轮对多边形问题的认识和解决方法的培训,提高运维人员的技术水平和维护能力。
动车组轮对多边形问题是一个需要高度重视的安全隐患,通过加强预防措施,可有效降低多边形磨损的产生,确保列车的安全运行和车辆的使用寿命。
高铁车轮锻造工艺研究

doi:10.3969/j.issn.1006-4311.2021.19.056
0 引言 高铁车轮作为承载机车的重要行驶部分,在工作过 程中承受着来自高铁的全部静、动载荷,加之运行过程中 的频繁减速制动等,使得车轮的工况相当复杂。随着高速 铁路技术的飞速发展,对高铁车轮的质量要求越来越高, 而当前国产的车轮存在制造设备精度不够、生产工艺不 熟练、废品率较高等诸多问题,不能满足高铁车轮的使用 要求。 目前,高铁车轮大多是用模锻—轧制的方法制造[1]。这 种制造方法相对复杂,其热成形工艺更是决定高铁车轮整 体组织性能的关键。国内外学者对车轮锻造工艺进行了大 量分析。武胜飞[2]分析了坯料和模具的装配位置以及模具 倾斜对车轮成形造成的影响,得出了最优的模具型腔。宋 光鑫[3]通过数值模拟的方法得到了工艺参数对车轮成形时 金属填充情况的影响及成形过程中力的变化。郑仰利[4]通 过建立镦粗和预成形工艺的数学模型分析了不同工艺参 数对火车车轮预成形效果的影响。Kushnarev 等[5]对车轮模 锻预成形中预锻和终锻进行了三维模拟,初步分析了影响 预成形坯形状和尺寸的因素。 本文采用数值模拟技术开展不同预锻模具型腔、摩擦 系数及压弯工艺对车轮成形质量的影响研究,以期为提高 车轮锻造质量提供理论指导。 1 高铁车轮成形工艺分析 目前,高铁车轮成形工艺的第一步是锻造成形,锻造 过程分为预锻和终锻两部分,预锻工艺主要负责对毛坯进 行镦粗以及分配金属,终锻则是在预锻坯的基础上进行约 束墩挤。第二步是轧制,对成形车轮的轮辋部位及辐板部
时刻的模具轴向反力随摩擦系数的增大而增大。因此,摩 擦系数 f=0.3 时得到的结果是最理想的。
1.1.3 高铁车轮锻造成形金属流动规律 为进一步研究高铁车轮的锻造工艺,运用 ABAQUS, 在满足最优的模具以及合适参数的条件下,模拟了车轮的 终锻过程,模拟结果如图 8 所示。 结果表明,在成形初始时刻,模具刚开始下压,坯料处 于镦粗状态,金属在水平方向上有向外流动的趋势,在竖 直方向上整体呈向下流动的趋势;模具继续下压,由于轮 毂部位和轮辋部位的模具压入轮坯的距离较小,辐板下方 的金属受压向两侧流动,分别流入轮毂和轮辋部位;模具 再继续下压,当轮坯外侧面与模具型腔侧面接触时,模具 上冲头已压入轮坯一定距离,金属流动受到轮毂和轮辋部 位型腔侧面的阻力影响,辐板处的金属向内外分流减小, 挤压过来的金属向下流动,填充轮毂部位的下半型腔;在 模具下腔充填到一定程度时,金属向下流动受到型腔侧壁
轮对压装关键因素浅析

轮对压装关键因素浅析作者:曹振山宋宇晗李钊来源:《山东工业技术》2018年第07期摘要:轮对是转向架的重要组成部分。
通过了解轮对压装的基本工艺的基础上,并进一步分析圆柱度,过盈量,压入速度和润滑剂等关键因素对轮对压装质量的影响。
通过分析关键因素的影响,有助于提高轮对压装质量,从而为转向架安全工作提供重要保障。
关键词:转向架;轮对压装;关键因素DOI:10.16640/ki.37-1222/t.2018.07.023轮对本身的结构并不复杂,但是由于它承担的任务多且重要,因此它的加工制造以及组装要求都非常高。
尤其是轮对的组装对于转向架的运行表现起到关键性的作用,组装稍有差错容易引发列车停车,甚至脱轨等重大事故。
通过对轮对组装过程的分析,可以更好地保证轮对正常使用,保障列车行驶安全。
1 轮对压装工艺简介轮对本身结构较为简单,但是其对压装的要求却十分严格。
目前常见压装根据压装方式不同可以分为普通压装和注油压装两种方式。
其中普通压装根据压装温度不同可以分为热压装和冷压装。
热压装是将车轮内孔进行加热使其膨胀后再进行压装,其主要是针对过盈量较大的情况下使用。
热压装工艺设备一般较为复杂,一次投入成本较高,压装合格率较高,可提高车轴的使用寿命,止推试验效率低。
冷压装是直接通过压装机将车轮压到车轴上的方式,其主要是针对过盈量较小的情况下使用。
冷压装设备较为简单,一次性投入成本较低,但压装合格率一般,对操作要求较高,操作不当容易“戗轴”,对车轴寿命有一定影响,止推试验效率高。
而注油压装是在车轮上开注油孔,在压装过程中通过注入高压油,在车轮和车轴接触面之间形成一层油膜进行压装,其主要是针对车轴表面要求较高时使用。
注油压装设备较为复杂,操作难度较大,加工难度大,但压装过程允许停顿且不限时间,可以在一定范围内自由调整车轮位置。
这三种压装工艺目前都在使用,都有各个的优缺点。
这三种压装工艺的选择主要根据车轮和轮轴的结构以及压装的具体要求来决定的。
动车组车轮的制造工艺与质量控制
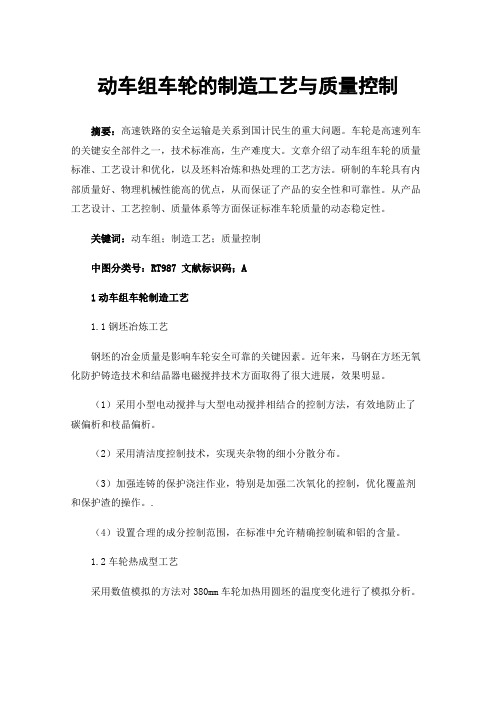
动车组车轮的制造工艺与质量控制摘要:高速铁路的安全运输是关系到国计民生的重大问题。
车轮是高速列车的关键安全部件之一,技术标准高,生产难度大。
文章介绍了动车组车轮的质量标准、工艺设计和优化,以及坯料冶炼和热处理的工艺方法。
研制的车轮具有内部质量好、物理机械性能高的优点,从而保证了产品的安全性和可靠性。
从产品工艺设计、工艺控制、质量体系等方面保证标准车轮质量的动态稳定性。
关键词:动车组;制造工艺;质量控制中图分类号:RT987文献标识码;A1动车组车轮制造工艺1.1钢坯冶炼工艺钢坯的冶金质量是影响车轮安全可靠的关键因素。
近年来,马钢在方坯无氧化防护铸造技术和结晶器电磁搅拌技术方面取得了很大进展,效果明显。
(1)采用小型电动搅拌与大型电动搅拌相结合的控制方法,有效地防止了碳偏析和枝晶偏析。
(2)采用清洁度控制技术,实现夹杂物的细小分散分布。
(3)加强连铸的保护浇注作业,特别是加强二次氧化的控制,优化覆盖剂和保护渣的操作。
.(4)设置合理的成分控制范围,在标准中允许精确控制硫和铝的含量。
1.2车轮热成型工艺采用数值模拟的方法对380mm车轮加热用圆坯的温度变化进行了模拟分析。
图1钢坯加热过程温度分布由图1可见,当加热时间达到5h时,钢坯温度总体较均匀。
图2车轮用Φ380mm圆坯加热过程数值模拟与实测结果对比1.3热处理工艺热处理工艺的关键是如何有效地发挥v的强化作用和晶粒细化作用,从而提高车轮的强韧性匹配,提高车轮的质量。
用formastor热模拟试验机测定了d2和er8的cct曲线,用金相显微镜观察了显微组织,并测定了5kg维氏硬度。
为热处理工艺参数的设计提供了参考。
Cct曲线如图3所示。
图3D2/ER8的CCT曲线3质量控制3.1标准动车组质量管理体系的构建针对标准动车组认证后的大批量生产,根据零缺陷管理体系和产品实现过程中的要求,以iris和iso9001标准体系为依据,从标准车轮的技术条件入手,根据目前的生产条件、管理水平和员工的业务素质,提出了一种基于iso9001标准体系的车轮零缺陷管理系统,针对高速高风险的特点,注重预防,准确识别产品安全特征,全面识别产品和工艺生产模式,明确工艺参数和产品特征值控制要求,明确设备精度参数要求,加强工艺控制,实施生产过程各要素跟踪,加强工艺监督,明确工作责任,实施严格的质量追溯制度。
新一代动车组轮对提吊组成加工工艺优化
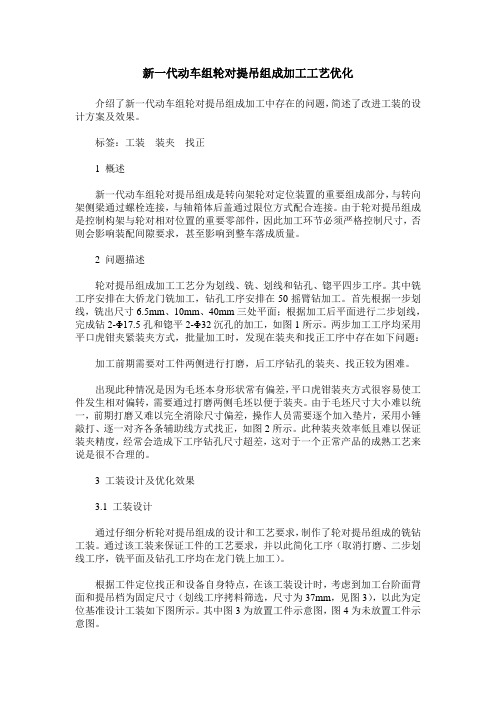
新一代动车组轮对提吊组成加工工艺优化介绍了新一代动车组轮对提吊组成加工中存在的问题,简述了改进工装的设计方案及效果。
标签:工装装夹找正1 概述新一代动车组轮对提吊组成是转向架轮对定位装置的重要组成部分,与转向架侧梁通过螺栓连接,与轴箱体后盖通过限位方式配合连接。
由于轮对提吊组成是控制构架与轮对相对位置的重要零部件,因此加工环节必须严格控制尺寸,否则会影响装配间隙要求,甚至影响到整车落成质量。
2 问题描述轮对提吊组成加工工艺分为划线、铣、划线和钻孔、锪平四步工序。
其中铣工序安排在大侨龙门铣加工,钻孔工序安排在50摇臂钻加工。
首先根据一步划线,铣出尺寸6.5mm、10mm、40mm三处平面;根据加工后平面进行二步划线,完成钻2-Φ17.5孔和锪平2-Φ32沉孔的加工,如图1所示。
两步加工工序均采用平口虎钳夹紧装夹方式,批量加工时,发现在装夹和找正工序中存在如下问题:加工前期需要对工件两侧进行打磨,后工序钻孔的装夹、找正较为困难。
出现此种情况是因为毛坯本身形状常有偏差,平口虎钳装夹方式很容易使工件发生相对偏转,需要通过打磨两侧毛坯以便于装夹。
由于毛坯尺寸大小难以统一,前期打磨又难以完全消除尺寸偏差,操作人员需要逐个加入垫片,采用小锤敲打、逐一对齐各条辅助线方式找正,如图2所示。
此种装夹效率低且难以保证装夹精度,经常会造成下工序钻孔尺寸超差,这对于一个正常产品的成熟工艺来说是很不合理的。
3 工装设计及优化效果3.1 工装设计通过仔细分析轮对提吊组成的设计和工艺要求,制作了轮对提吊组成的铣钻工装。
通过该工装来保证工件的工艺要求,并以此简化工序(取消打磨、二步划线工序,铣平面及钻孔工序均在龙门铣上加工)。
根据工件定位找正和设备自身特点,在该工装设计时,考虑到加工台阶面背面和提吊档为固定尺寸(划线工序拷料筛选,尺寸为37mm,见图3),以此为定位基准设计工装如下图所示。
其中图3为放置工件示意图,图4为未放置工件示意图。
- 1、下载文档前请自行甄别文档内容的完整性,平台不提供额外的编辑、内容补充、找答案等附加服务。
- 2、"仅部分预览"的文档,不可在线预览部分如存在完整性等问题,可反馈申请退款(可完整预览的文档不适用该条件!)。
- 3、如文档侵犯您的权益,请联系客服反馈,我们会尽快为您处理(人工客服工作时间:9:00-18:30)。
浅谈动车组轮对制造工艺要点
【摘要】通过对某型动车组轮对设计要求及结构特点,对某型动车组轮对制造工序进行工艺分析,并根据生产实际情况,设计了合理的轮对制造工艺方法及关键质量控制措施。
【关键词】动车组;轮对制造;工艺要点
1前言
某型动车组是根据目前铁路发展趋势和动车组系列产品的特点,为进一步提高快速应对市场需求的能力,降低研发、制造以及售后成本,结合和谐号动车组样车研制的研究成果,研制的既能满足持续高速运营、又能满足站站停运营模式动车组。
某型动车组转向架在高速动车组转向架基础上,结合实际情况,进一步提高零部件国产化率,降低制造成本而研发出来的新型动车组转向架。
2轮对轴箱主要结构特点
某型动车组轮对轴箱组成主要分为动车轮对和拖车轮对两种;动车轮对主要包括车轴、车轮组成、齿轮箱等,拖车轮对主要包括车轴、车轮、轴装制动盘等,如图1和图2。
3轮对制造工艺分析及设计
为保证某型动车组轮对制造质量及工艺步骤合理性,制造过程中将轮对划分为若干个制造单元,对各单元进行分零件加工、组装,最后对单元零部件进行总组装,具体工艺流程如图3。
4轮对制造工艺要点
1、车轮加工:
车轮采购半成品,内孔留量加工,工艺要点如下:
1)粗车轮毂内孔;
2)根据注油孔实际位置车出周向浅槽;
3)精车轮毂内孔;
4)用成型车刀加工注油沟,休整倒角R2;
5)用砂纸将内孔圆弧过渡处均匀打磨,去毛刺。
2、车轴加工:
车轴采购半成品,车轴总长、轴端中心孔和三螺孔加工到位,车轴入厂后需进行外圆精加工,工艺要点如下:
1)精车轴颈、轮座、齿轮箱座(动车车轴)、制动盘座(拖车车轴)、防尘板座和各圆弧尺寸;
2)滚压轴颈卸荷槽圆弧;
3)磨削轴颈和防尘板座;
4)磨削轮座、齿轮箱座(动车车轴)和制动盘座(拖车车轴);
5)对车轴各圆弧进行抛光,去除棱角毛刺,过渡处打磨圆滑。
3、轮装制动盘组装
动车车轮加工后需进行轮装制动盘的组装,制动盘组装与城际160公里相同,工艺要点如下:
1)车轮、制动盘整备:检查车轮、制动盘外观,车轮、制动盘不平衡位置及数值标识清晰,对制动盘与车轮的螺栓孔、定位销孔、制动盘上的定位销槽安装面用软布进行擦拭,在车轮及制动盘接触表面均匀涂抹一层摩擦剂;
2)制动盘组装:组装时应保证车轮和制动盘不平衡点成150°~210°之间,车轮定位销孔与制动盘定位销槽对中,螺栓及螺母的螺纹用润滑油润滑,制动盘预组后先用70±5N.m的扭矩按照1、5、9、2、6、10、3、7、11、4、8、12的顺序交叉紧固所有螺栓,如图4,然后用140±5N.m的扭矩仍按照1、5、9、2、6、10、3、7、11、4、8、12的顺序交叉紧固所有螺栓;
4、轮对、轴制动盘压装
车轮、轴制动盘与车轴采用冷压方式组装,压装须符合轮对压装技术条件要求,工艺要点如下:
1)尺寸测量:在被测量表面三个测量截面(S1~S3或S4~S6)的相互垂直方向上,测得两个直径值,并取6个测量平均值作为被测表面的直径值,通过它来选配过盈量。
轮(盘)座、轮(盘)毂孔的圆柱度对过盈量影响较大,因此要求轮毂孔圆柱度小于0.02mm,车轴轮座小于0.015mm,各测量部位不允许出现倒锥,如图5所示。
图5轮座、盘座各部尺寸测量示意图
2)工件选配
车轮压装过盈量应在(0.212~0.296)mm,,制动盘压装过盈量在(0.229~0.304)mm之间;车轮须满足如下配台要求:
a. 同一车轴上组装的两个车轮轮辋宽度差应≤2mm;
b. 同一轮对两车轮直径差≤0.3mm;同一转向架两车轮直径差≤0.5mm;同一车辆两车轮直径差≤1mm。
3)打磨、清洗
为增大压装配合面摩擦力,且车轮(制动盘)压装不合格注油退卸时液压油需有渗出间隙,因此需对车轮轮座(制动盘座)及车轮(制动盘)进行打磨处理具体操作如下:
用120至200目棕刚玉砂纸打磨轮座倒角部位,使其圆滑过渡。
使用80至120目棕刚玉砂纸沿与纵向轴线成45°方向交叉打磨轮座(制动盘座)表面,见图2所示,往复打磨动作时要求单程均匀用力打磨。
打磨后纹理尽量均匀。
4)轮对压装
a.压装准备。
压装前在轴颈上涂抹少量变压器油,用压装保护套对轴颈进行防护。
为降低压装过程中对接触表面划伤程度,用毛刷蘸取适量润滑剂均匀涂抹在轮座(盘座)及轮毂孔(盘毂孔)表面及倒角部位。
b.压装。
将预组后的轮对上料后使用液压数控压力机进行压装。
c.压装效果。
通过压力曲线图作为判断压装后配合面是否完好的参考,压力曲线应均匀平稳上升,不得有配合面呛伤导致的陡升,且压力曲线应全部在曲线起点与终点处压力的连线以上(注油沟处曲线除外),车轮最大压装力应满足831kN~1229kN,制动盘最大压装力应满足263kN~450kN。
c.尺寸检测。
轮对组装后,检查轮对各部尺寸,各部尺寸要求见表2.
6结论
通过对上述某型动车组轮对制造工艺措施的实施,保证了生产过程中轮对设计性能的实现,也保证了该类型轮对的制造质量,弥补了在此速度等级动车组转向架研发制造上的空白,提高了国内在该速度等级动车组转向架研制上的竞争力。
参考文献:
[1] EN 13260:2009,铁路应用轮对和转向架轮对生产要求[S].
[2] TB/T 1718-2003,。