板料成型工艺 思考题
生产实习思考题及参考答案
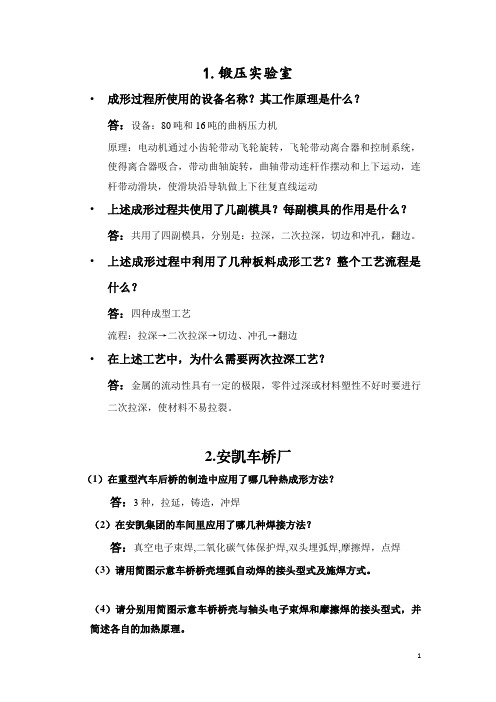
1.锻压实验室•成形过程所使用的设备名称?其工作原理是什么?答:设备:80吨和16吨的曲柄压力机原理:电动机通过小齿轮带动飞轮旋转,飞轮带动离合器和控制系统,使得离合器吸合,带动曲轴旋转,曲轴带动连杆作摆动和上下运动,连杆带动滑块,使滑块沿导轨做上下往复直线运动•上述成形过程共使用了几副模具?每副模具的作用是什么?答:共用了四副模具,分别是:拉深,二次拉深,切边和冲孔,翻边。
•上述成形过程中利用了几种板料成形工艺?整个工艺流程是什么?答:四种成型工艺流程:拉深→二次拉深→切边、冲孔→翻边•在上述工艺中,为什么需要两次拉深工艺?答:金属的流动性具有一定的极限,零件过深或材料塑性不好时要进行二次拉深,使材料不易拉裂。
2.安凯车桥厂(1)在重型汽车后桥的制造中应用了哪几种热成形方法?答:3种,拉延,铸造,冲焊(2)在安凯集团的车间里应用了哪几种焊接方法?答:真空电子束焊,二氧化碳气体保护焊,双头埋弧焊,摩擦焊,点焊(3)请用简图示意车桥桥壳埋弧自动焊的接头型式及施焊方式。
(4)请分别用简图示意车桥桥壳与轴头电子束焊和摩擦焊的接头型式,并简述各自的加热原理。
答:电子束焊:以集中的高速电子束轰击工作表面是产生的热能进行焊接,与电弧焊相比.主要特点是焊缝熔深大,熔宽小,焊接金属纯度高.摩擦焊:机械能转换成热能----材料塑形变形---热塑下的锻压力----分子间扩散再结晶摩擦焊与传统的熔焊最大的不同在于整个焊接过程中,带焊接金属获得能量升高到的温度并没有达到其熔点,即金属是在热塑性状态下实现的类锻态固相焊接.相比较传统熔焊,摩擦焊具有焊接接头质量高,能达到焊缝强度与基本材料等强度,焊接效率高,质量稳定,一致性好,可实现异种材料焊接.3.合力叉车试述铸造成形的实质及其优缺点。
答:实质:利用熔融金属的流动性能实现成型。
优点:铸造的适应性强,可铸各种形状的工件,原材料来源广泛,成本低。
缺点:铸件组织性能差,废品率高,铸造工序较多,劳动条件差。
材料成型复习题思考及答案
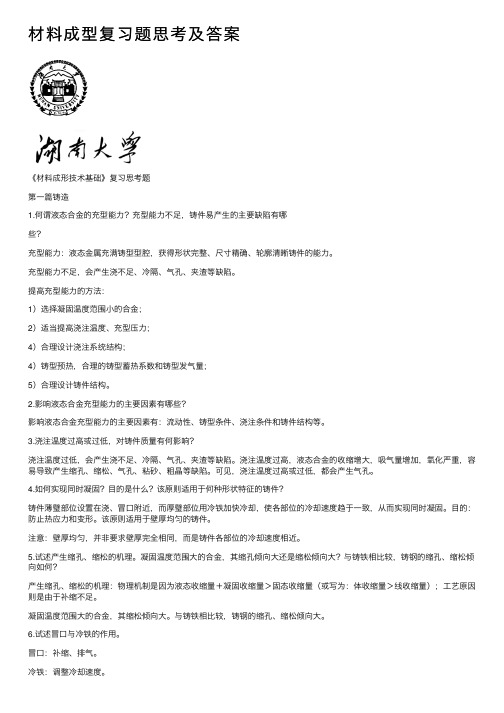
材料成型复习题思考及答案《材料成形技术基础》复习思考题第⼀篇铸造1.何谓液态合⾦的充型能⼒?充型能⼒不⾜,铸件易产⽣的主要缺陷有哪些?充型能⼒:液态⾦属充满铸型型腔,获得形状完整、尺⼨精确、轮廓清晰铸件的能⼒。
充型能⼒不⾜,会产⽣浇不⾜、冷隔、⽓孔、夹渣等缺陷。
提⾼充型能⼒的⽅法:1)选择凝固温度范围⼩的合⾦;2)适当提⾼浇注温度、充型压⼒;4)合理设计浇注系统结构;4)铸型预热,合理的铸型蓄热系数和铸型发⽓量;5)合理设计铸件结构。
2.影响液态合⾦充型能⼒的主要因素有哪些?影响液态合⾦充型能⼒的主要因素有:流动性、铸型条件、浇注条件和铸件结构等。
3.浇注温度过⾼或过低,对铸件质量有何影响?浇注温度过低,会产⽣浇不⾜、冷隔、⽓孔、夹渣等缺陷。
浇注温度过⾼,液态合⾦的收缩增⼤,吸⽓量增加,氧化严重,容易导致产⽣缩孔、缩松、⽓孔、粘砂、粗晶等缺陷。
可见,浇注温度过⾼或过低,都会产⽣⽓孔。
4.如何实现同时凝固?⽬的是什么?该原则适⽤于何种形状特征的铸件?铸件薄璧部位设置在浇、冒⼝附近,⽽厚璧部位⽤冷铁加快冷却,使各部位的冷却速度趋于⼀致,从⽽实现同时凝固。
⽬的:防⽌热应⼒和变形。
该原则适⽤于壁厚均匀的铸件。
注意:壁厚均匀,并⾮要求壁厚完全相同,⽽是铸件各部位的冷却速度相近。
5.试述产⽣缩孔、缩松的机理。
凝固温度范围⼤的合⾦,其缩孔倾向⼤还是缩松倾向⼤?与铸铁相⽐较,铸钢的缩孔、缩松倾向如何?产⽣缩孔、缩松的机理:物理机制是因为液态收缩量+凝固收缩量>固态收缩量(或写为:体收缩量>线收缩量);⼯艺原因则是由于补缩不⾜。
凝固温度范围⼤的合⾦,其缩松倾向⼤。
与铸铁相⽐较,铸钢的缩孔、缩松倾向⼤。
6.试述冒⼝与冷铁的作⽤。
冒⼝:补缩、排⽓。
冷铁:调整冷却速度。
7.⼀批铸钢棒料(Φ200×L mm )加⼯:(1)沿其轴线,在⼼部钻Φ80mm 棒料长度为L 1; (2)将其车为Φ80mm L2。
试分析L 、L1、L2是否相等。
高分子加工思考题解答

第一章绪论1.高分子材料分为哪几类?(高分子材料是一定配合的高分子化合物(由主要成分树脂或橡胶和次要成分添加剂组成)在成型设备中,受一定温度和压力的作用熔融塑化,然后通过模塑制成一定形状,冷却后在常温下能保持既定形状的材料制品。
分为塑料、橡胶、纤维三类)2.塑料、橡胶、纤维分类?3.名词解释:工程塑料通用塑料特种塑料化学纤维合成纤维4.生产塑料制品的完整工序有哪五个?原料准备、成型、机械加工、修饰和装配5. 热塑性高分子材料和热固性高分子材料得物理性质及加工性能比较(见讲义)。
第二章高分子材料成型原理1.高分子材料的熔融性能热传递三种方式:热传导、对流、辐射聚合物的加热与冷却都不易由于聚合物的表观粘度随摩擦升温而降低,使物料熔体烧焦的可能性不大2.聚合物的流动和流变性能拉伸流动和剪切流动,各类型流体的流动曲线,影响高聚物熔体粘度的因素,粘度、流动稠度、流动指数、流动性的关系,熔体流动速率熔体流动速率——在规定的温度、压力(2160×9.81×10-3N)下,每10min内通过国标指定尺寸(书P76装料筒直径φ9.55±0.025mm, 出料口直径φ2.095±0.005mm)毛细管的试样总质量(克数)单位:克/10分钟3.聚合物熔体的弹性流动缺陷:管壁上的滑移,端末效应,离模膨胀,弹性对层流的干扰,熔体破裂,鲨鱼皮,产生原因熔体破裂——当挤出速率逐渐增加,挤出物表面将出现不规则现象(畸变、支离和断裂),甚至使内在质量受到破坏。
离模膨胀——被挤出的聚合物熔体断面积远比口模断面积大,称为离模膨胀鲨鱼皮——挤出物周边具有周期性的皱褶波纹。
4.高分子材料的成型性能聚合物的聚集态:结晶态、玻璃态、高弹态、粘流态等聚集态可挤压性、可模塑性、可纺性、可延性概念5.成型过程中的取向作用拉伸取向(薄膜双向拉伸后,拉伸后的薄膜在拉伸方向上的拉伸强度和抗蠕变性能会提高。
6.高分子材料的降解与交联交联、交联度熟化降解——高分子材料化学键的断链、交联、主链化学结构改变、侧基改变以及上述四种作用的综合交联——线性大分子链之间以新的化学键连接、形成三维网状或体型结构的反应。
材料成型基础复习试题(含答案)

材料成型基础复习试题(含答案)试卷1⼀、思考题1.什么是机械性能?(材料受⼒作⽤时反映出来的性能)它包含哪些指标?(弹性、强度、塑性、韧性、硬度等)各指标的含意是什么?如何测得?2.硬度和强度有没有⼀定的关系?为什么? (有,强度越⾼,硬度越⾼)为什么?(都反映材料抵抗变形及断裂的能⼒)3.名词解释:过冷度,晶格,晶胞,晶粒与晶界,同素异晶转变,固溶体,⾦属化合物,机械混合物。
4.过冷度与冷却速度有什么关系?对晶粒⼤⼩有什么影响? (冷却速度越⼤过冷度越⼤,晶粒越细。
)5.晶粒⼤⼩对⾦属机械性能有何影响?常见的细化晶粒的⽅法有哪些? (晶粒越细,⾦属的强度硬度越⾼,塑韧性越好。
孕育处理、提⾼液体⾦属结晶时的冷却速度、压⼒加⼯、热处理等)6.说明铁素体、奥⽒体、渗碳体和珠光体的合⾦结构和机械性能。
7.默绘出简化的铁碳合⾦状态图,并填⼈各区域内的结晶组织。
8.含碳量对钢的机械性能有何影响?⼆、填表说明下列符号所代表的机械性能指标三、填空1. 碳溶解在体⼼⽴⽅的α-Fe中形成的固溶体称铁素体,其符号为F ,晶格类型是体⼼⽴⽅,性能特点是强度低,塑性好。
2. 碳溶解在⾯⼼⽴⽅的γ-Fe中形成的固溶体称奥⽒体,其符号为 A ,晶格类型是⾯⼼⽴⽅,性能特点是强度低,塑性⾼。
3. 渗碳体是铁与碳的⾦属化合物,含碳量为6.69%,性能特点是硬度⾼,脆性⼤。
4. ECF称共晶线线,所发⽣的反应称共晶反应,其反应式是得到的组织为 L(4.3%1148℃)=A(2.11%)+Fe3C 。
5. PSK称共析线线,所发⽣的反应称共析反应,其反应式是A(0.77%727 ℃)=F(0.0218%)+ Fe3C 得到的组织为珠光体。
6. E是碳在γ-Fe中的最⼤溶解度点,P是碳在α-Fe中的最⼤溶解度点, A l线即 PSK ,A3线即 GS , A cm线即 ES 。
7. 45钢在退⽕状态下,其组织中珠光体的含碳量是 0.77% 。
《模具设计与制造》第2版(李奇 朱江峰) 课后习题答案 (10)
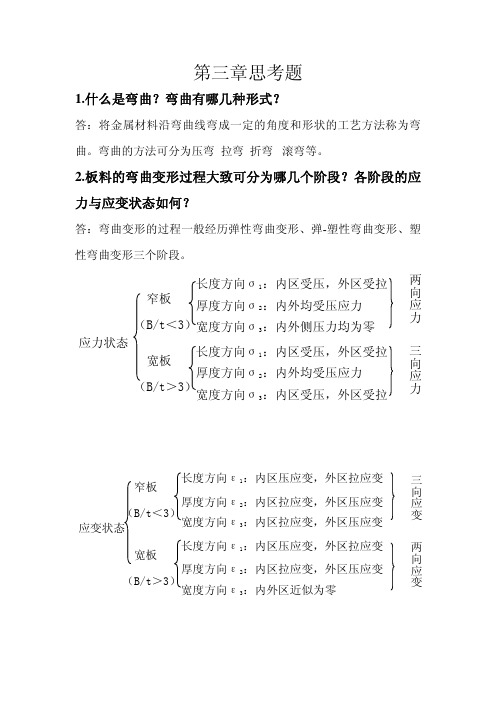
1.什么是弯曲?弯曲有哪几种形式?
答:将金属材料沿弯曲线弯成一定的角度和形状的工艺方法称为弯
曲。弯曲的方法可分为压弯 拉弯 折弯 滚弯等。
2.板料的弯曲变形过程大致可分为哪几个阶段?各阶段的应 力与应变状态如何?
答:弯曲变形的过程一般经历弹性弯曲变形、弹-塑性弯曲变形、塑
性弯曲变形三个阶段。
两
窄板
长度方向σ1:内区受压,外区受拉 厚度方向σ2:内外均受压应力
向 应 力
(B/t<3)宽度方向σ3:内外侧压力均为零
应力状态
三
宽板
长度方向σ1:内区受压,外区受拉 厚度方向σ2:内外均受压应力
向 应 力
(B/t>3)宽度方向σ3:内区受压,外区受拉
三
窄板 长度方向ε1:内区压应变,外区拉应变
向 应
厚度方向ε2:内区拉应变,外区压应变
变
(B/t<3)
应变状态
宽度方向ε3:内区拉应变,外区压应变
两
宽板 长度方向ε1:内区压应变,外区拉应变
向 应
厚度方向ε2:内区拉应变,外区压应变
变
(B/t>3)
宽度方向ε3:内外区近似为零
3.什么是最小弯曲半径?影响最小弯曲半径的因素有哪些?
答:在材料不发生破坏的情况下所能弯曲半径的最小值。 最小弯曲半径受材料的力学性能、弯曲方向、板料厚度等因素的
影响。
4.什么是回弹?在生产中掌握回弹规律有何实际意义?
答:在板料弯曲变形结束、工件不受外力作用时,由于弹性恢 复,使弯曲件的角度、弯曲半径与模具的形状尺寸不一致,这种现 象称为回弹。
回弹是用来说明当去除成型工具的压力时,成型的部件所产生 的尺寸变化。在生产中掌握回弹规律可准确的计算出凸、凹模的刃种?各有何意义?
哈工程--材料成型习题

哈⼯程--材料成型习题习题《材料成形》部分第1章铸造填空题:1、铸造⽅法从总体上可分为普通铸造和特种铸造两⼤类,普通铸造是指砂型铸造⽅法,不同于砂型铸造的其他铸造⽅法统称为特种铸造,常⽤的特种铸造⽅法有:()、()、()、()、()等。
2、凝固过程中所造成的体积缩减如得不到液态⾦属的补充,将产⽣()或()。
3、对砂型铸件进⾏结构设计时,必须考虑合⾦的()和铸造()对铸件结构提出的要求。
4、()是铸造合⾦本⾝的物理性质,是铸件许多缺陷()产⽣的基本原因。
5、浇注位置是指造型时()在铸型中所处的位置,它影响铸件的质量。
6、铸造应⼒按产⽣的原因不同,主要可分为()和()两种。
7、铸件上各部分壁厚相差较⼤,冷却到室温,厚壁部分的残余应⼒为()应⼒,⽽薄壁部分的残余应⼒为()应⼒。
8、任何⼀种液态⾦属注⼊铸型以后,从浇注温度冷却⾄室温都要经过三个联系的收缩阶段,即()、()和()。
9、在低压铸造、压⼒铸造和离⼼铸造时,因⼈为加⼤了充型压⼒,故()较强。
提⾼浇铸温度是改善合⾦()的重要措施。
10、铸件浇铸位置的选择必须正确,如重要加⼯⾯、⼤平⾯和薄壁部分在浇铸时应尽量(),⽽厚⼤部位应尽量(),以便安放冒⼝进⾏()。
单项选择题:1、下列合⾦流动性最好的是:()①普通灰铸铁;②球墨铸铁;③可锻铸铁;④蠕墨铸铁。
2、摩托车活塞应具有良好的耐热性、热膨胀系数⼩,导热性好、耐磨、耐蚀、重量轻等性能。
在下列材料中,⼀般选⽤:()①铸造黄铜;②合⾦结构钢;③铸造铝硅合⾦;④铸造碳钢。
3、在下列铸造合⾦中,⾃由收缩率最⼩的是:()①铸钢;②灰铸铁;③铸造铝合⾦;④⽩⼝铸铁4、图⽰圆锥齿轮铸件,齿⾯质量要求较⾼。
材料HT350,⼩批⽣产。
最佳浇注位置及分型⾯的⽅案是:( )①⽅案Ⅰ;5)③提⾼浇注温度④采⽤颗粒⼤⽽均匀的原砂以改善填充条件多项选择题:1、液态合⾦浇注温度冷却到室温所经历的收缩阶段有:()①⾼温收缩;②液态收缩;③凝固收缩④低温收缩;⑤固态收缩2、挖沙或假箱造型时候,分型⾯:()①⼀定是曲⾯;②⼀定是圆锥⾯;③可以是平;④⼀定是平⾯;⑤可以是曲⾯3、影响液态合⾦充型能⼒的主要因素是:()①合⾦的结晶特性;②浇注温度;③合⾦的收缩率;④铸造⼯艺凝固原则;⑤铸件壁厚和铸型条件4、产⽣缩孔、缩松的基本原因:()①液态收缩;②固态收缩;③凝固收缩;④线收缩;⑤等温收缩结构改错题:1、如右图所⽰,浇铸位置是否合理?若不合理请改为合理。
塑料成型工艺与模具设计课后习题.doc
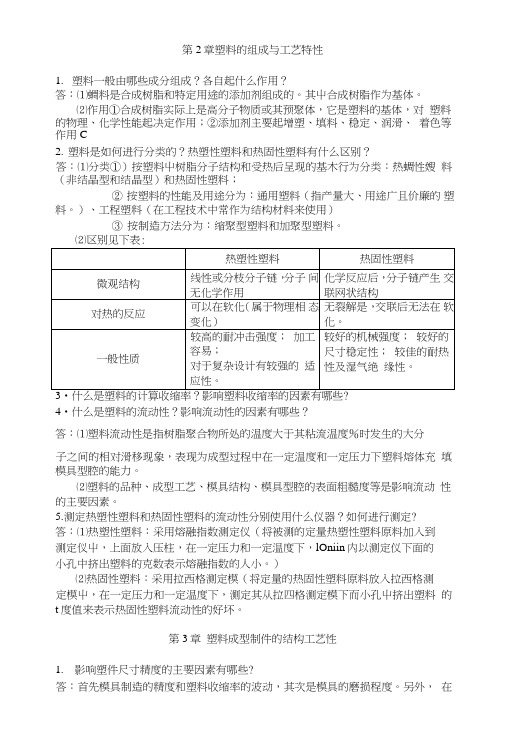
第2章塑料的组成与工艺特性1.塑料一般由哪些成分组成?各自起什么作用?答:⑴蜩料是合成树脂和特定用途的添加剂组成的。
其屮合成树脂作为基体。
⑵作用①合成树脂实际上是高分子物质或其预聚体,它是塑料的基体,对塑料的物理、化学性能起决定作用;②添加剂主要起增塑、填料、稳定、润滑、着色等作用C2.塑料是如何进行分类的?热塑性塑料和热固性塑料有什么区别?答:⑴分类①)按塑料屮树脂分子结构和受热后呈现的基木行为分类:热蜩性嫂料(非结晶型和结晶型)和热固性塑料;②按塑料的性能及用途分为:通用塑料(指产量大、用途广且价廉的塑料。
)、工程塑料(在工程技术中常作为结构材料来使用)③按制造方法分为:缩聚型塑料和加聚型塑料。
⑵区别见下表:•什么是塑料的计算收缩率?影响塑料收缩率的因素有哪些?4•什么是塑料的流动性?影响流动性的因素有哪些?答:⑴塑料流动性是指树脂聚合物所处的温度大于其粘流温度%时发生的大分子之间的相对滑移现象,表现为成型过程中在一定温度和一定压力下塑料熔体充填模具型腔的能力。
⑵塑料的品种、成型工艺、模具结构、模具型腔的表面粗糙度等是影响流动性的主要因素。
5.测定热塑性塑料和热固性塑料的流动性分别使用什么仪器?如何进行测定?答:⑴热塑性塑料:采用熔融指数测定仪(将被测的定量热塑性塑料原料加入到测定仪屮,上面放入压柱,在一定压力和一定温度下,lOniin内以测定仪下面的小孔中挤出塑料的克数表示熔融指数的人小。
)⑵热固性塑料:采用拉西格测定模(将定量的热固性塑料原料放入拉西格测定模屮,在一定压力和一定温度下,测定其从拉四格测定模下而小孔屮挤出塑料的t度值来表示热固性塑料流动性的好坏。
第3章塑料成型制件的结构工艺性1.影响塑件尺寸精度的主要因素有哪些?答:首先模具制造的精度和塑料收缩率的波动,其次是模具的磨损程度。
另外,在成型吋工艺条件的变化、然件成型后的吋效变化、嫂件的飞边等都会影响蜩件的楮度。
2•什么是塑件的脱模斜度?脱模斜度选取应遵循哪些原则?答:⑴为了便于从成型零件上顺利脱出塑件,必须在塑件内外表面沿脱模方向设计足够的斜度,称为脱模斜度。
塑料成型思考题答案

1、塑料添加剂的种类和用途(1)增塑剂改善树脂成型时的流动性和提高塑料柔顺性的添加剂。
(2)稳定剂阻缓塑料变质的物质。
(3)固化剂促使树脂固化、硬化的添加剂。
(4)填充剂又称填料,减少贵重树脂含量,降低成本;同时还起到增强作用,改善塑料性能,扩大使用范围。
(5)着色剂使塑料制品件获得美丽的色泽,美观宜人,提高塑料的使用品质。
2、塑料分类(1)热塑性塑料是指在特定的温度范围内,能反复加热软化和冷却变硬的塑料。
(2)热固性塑料是指受热后成为不熔的物质,再次受热不再具有可塑性且不能再回收利用的塑料。
3、常用塑料(1)热塑性塑料:聚乙烯PE、聚丙烯PP、聚氯乙烯PVC、聚苯乙烯PS、ABS塑料、聚甲基丙烯酸甲酯PMMA、聚酰胺PA、聚碳酸酯PC(2)热固性塑料:酚醛树脂PF、氨基塑料、环氧树脂EP、不饱和聚酯树脂UP(3)发泡塑料4、塑料成型的工艺性能(1)热塑性塑料成型的工艺性能:流动性、收缩率、热稳定性、吸湿性、相容性(2)热固性塑料成型的工艺性能:收缩率、流动性、水分及挥发物含量、硬化速度5、注塑机的分类(1)按注射机注射方向和模具开合方向的分类:卧式注射机、立式注射机、角式注射机(2)按注射机装置分类:螺杆式、柱塞式、螺杆预塑化型(3)按锁模装置分类:直压式、肘拐式6、注射机基本参数和选择(1)最大注射量的校核(2)注射压力的校核(3)锁模力的校核(4)安装部分的尺寸校核(5)开模行程和顶出机构的校核7、热塑性塑料注射成型过程主要包含哪些环节,(1)成型前的准备(2)注射工艺过程:加料、塑化、注射○1充模○2保压○3倒流○4浇口冻结后的冷却○5脱模(3)制品的后处理其主要工艺参数是什么?(1)温度:机筒温度、喷嘴温度、模具温度(2)压力:塑化压力、注射压力(3)时间:完成一次注射成型过程所需的时间称为成型周期充模时间(螺杆前进时间)注射时间保压时间(螺杆停留在前进位置的时间)成型周期冷却时间闭模冷却时间(螺杆后退时间也包括这段时间)其他时间(开模、脱模、涂脱模剂、安装嵌件和合模等)8、热固性塑料注射成型过程基本与热塑性塑料相仿,其主要工艺参数是什么?(1)温度:料温、模具温度(2)压力:注射压力和注射速度、保压压力和保压时间、背压和螺杆转速(3)成型周期(4)其他工艺条件:物料在机筒的存留时间及其注射量、排气、热固性注射物料的典型工艺条件9、压缩成型工艺过程包含哪几个阶段?每阶段包含哪些工作?其艺原理是将松散的固态成型物料直接加入到模具中,通过加压方法使其熔融塑化,然后根据型腔形状进行流动成型,最终经过固化转变成为塑件。
- 1、下载文档前请自行甄别文档内容的完整性,平台不提供额外的编辑、内容补充、找答案等附加服务。
- 2、"仅部分预览"的文档,不可在线预览部分如存在完整性等问题,可反馈申请退款(可完整预览的文档不适用该条件!)。
- 3、如文档侵犯您的权益,请联系客服反馈,我们会尽快为您处理(人工客服工作时间:9:00-18:30)。
第二章板料成型工工艺
1.板料冲裁过程分为哪几个阶段,各阶段的变形特点是什么?
冲裁变形过程三阶段
(1)弹性变形阶段
在凸模压力下,材料产生弹性压缩、拉伸和弯曲变形,凹模上的板料则向上翘曲,间隙越大,弯
曲和上翘越严重。
同时,凸模稍许挤入板料上部,板料的下部则略挤入凹模洞口,但材料的内应力未
超过材料的弹性极限。
(2)塑性变形阶段
凸模继续压入,材料内的应力达到屈服极限时,便开始产生塑性变形。
随凸
模挤入板料深度的增大,塑性变形程度增大,变形区材料硬化加剧,冲裁变形力
不断增大,直到刃口附近侧面的材料由于拉应力的作用出现微裂纹时,塑性变形
阶段结束。
(3)断裂分离阶段
已形成的上下微裂纹,随凸模继续压入沿最大剪应力方向不断向材料内部扩展,当上下裂纹重合时,
板料被剪断分离。
2. 冲裁件的切断面具有明显的区域性特征.通常由塌角、光面、毛面、毛刺四部分组成。
这
四个部分是怎样形成的?
塌角a:它是在冲裁过程中刃口附近的材料被牵连拉入变形(弯曲和拉伸)的结果。
光面b:它是在塑性变形过程中凸模(或凹模)挤压切入材料,使其受到剪切应力τ和挤压应
力σ的作用而形成的。
毛面c:它是由于刃口处的微裂纹在拉应力σ作用下不断扩展断裂而形成的。
毛刺d:冲裁毛刺是在刃口附近的侧面上材料出现微裂纹时形成的。
当凸模继续下行时,
便使已形成的毛刺拉长并残留在冲裁件上。
3.影响冲裁件质量的主要因素有哪些?
冲裁件断面质量主要与凸凹模间隙、刃口锋利程度有关。
同时也受模具结构,材料性能及板厚等因素的影响。
4.什么是精密冲裁?它与普通冲裁有何区别?
精密冲裁法是改变冲裁条件,以增大变形区的静水压作用,抑制材料的断裂,使塑性剪切变形延续到剪切的全过程,在材料不出现剪裂纹的冲裁条件下实现材料的分离,从而得到断面光滑而垂直的精密零件。
区别;生产中采用精密冲裁工艺,可以直接从板料中获得公差等级高(可达IT6~IT8级)、粗糙度小(可达O.8~O.4μm)的精密零件。
生产率高。
可以满足精密零件批量生产的要求。
5.凸凹模间歇过大或过小对冲裁过程有何影响?
当间隙过大时,
(1)上、下裂纹向内错开。
材料的弯曲与拉伸增大,拉应力增大,易产生剪裂纹,塑性变形阶
段较早结束,致使断面光面减小,塌角与斜度增大,形成厚而大的拉长毛刺,且难以去除。
(2)冲裁的翘曲现象严重。
(3)由于材料在冲裁时受拉伸变形较大,所以零件从材料中分离出来后,因弹性回复使外形尺
寸缩小(受拉后,弹性恢复),内腔尺寸增大。
(4)推件力与卸料力大为减小,甚至为零,材料对凸、凹模的摩擦作用大大减弱,所以模具寿
命较高。
间隙小,光面宽度增加,塌角、毛刺、斜度等都有所减小,工件质量较高当工件公差要求较严时,需要使用较小的间隙。
凸凹模受到金属的挤压作用增大,从而增加了材料与凸凹模
之间的摩擦力。
这不仅增大了冲裁力、卸料力和推件力,还加剧了凸、凹模的磨损,降低了模具寿命(冲硬质材料更为突出)。
当工件公差要求较严时,仍然需要使用较小的间隙。
6.什么是板料的弯曲变形?
弯曲是将坯料弯成一定角度、一定曲率,形成一定形状零件的工序
7.影响弯曲件回弹的因素和减少回弹量的措施是什么?
影响回弹量的因素
(1) 材料的机械性能材料屈服极限愈高,弹性模量愈小,则弯曲后回弹角Δα=α-α0愈大。
(2)相对弯曲半径r/t值相对弯曲半径越小,弯曲回弹值越小。
(3)弯曲角中心角α值中心角α越大,则变形区域的r·α越大,回弹积累值越大,弯曲后回弹角Δα也愈大。
(4)零件形状形状复杂的弯曲件,弯曲后回弹角Δα较小。
(5)弯曲方式校正弯曲的回弹较自由弯曲的小。
减少回弹量的措施
(1)改进弯曲件设计和合理选材改进弯曲件结构,如在弯曲件变形处压制加强筋,可使回弹角减小,并提高弯曲
件的刚度。
对于一些硬材料,弯曲前采用退火处理,也可减少回弹。
(2)校正法在弯曲行程结束时,对板料施加亠定的校正压力,迫使变形处内层纤维产生切向拉伸应变,那么板料经
校正以后,内、外层纤维都要伸长,结果卸载后都要缩短,内、外层回弹趋势相反,因此回弹量将会减小,达到克服或减少回弹的目的。
采用校正法单角弯曲时,所使用的凸模几何形状和尺寸。
一般认为弯曲金属的校正压缩量为料厚2%~5%。
(3)补偿法根据弯曲件的回弹趋势和回弹量大小,修正凸模或凹模工作部分形状和尺寸,使零件的回弹量得到补偿。
(4)拉弯法板料在拉力作用下进行弯曲,使整个板料剖面上都作用有拉应力。
卸载后,因内、外层纤维的回弹趋势
相互抵消,从而可减少回弹。
8.什么是板料的拉深变形?板料拉深时各部分变形的特点是什么?
拉深是利用拉深模使平面坯料(工序件)变成开口空心件的冲压工序。
变形的特点①拉深件的底部一般不变形,只起传递拉力的作用,厚度基本不变。
②零件直壁由毛坯的环形部分(即毛坯外径与凹模洞口直径间的一圈)转化而成的,主要受拉力作用,厚度有所减小。
③直壁与底之间的过渡圆角部被拉薄最严重。
④拉深件的法兰部分,切向受压应力作用,厚度有所增大。
拉深时,金属材料产生很大的塑性流动,坯料直径越大,拉深后筒形直径越小,变形程度越大,其变形程度有一定限度。
9.拉深件常见缺陷及预防措施是什么?
1)起皱拉深时,法兰处受压应力作用而增厚。
当拉深变形程度较大,压应力增大,板料又
比较薄时,则可使法兰部分材料失稳而拱起,产生起皱现象。
预防措施可采用设置压边圈
的方法解决(图2-2-20),也可以通过增加毛坯的相对厚度(t/D)或拉深系数的途径来解决。
2)拉裂
预防措施(1)正确选择拉深系数。
拉深系数越小,表明拉深件直径越小,变形程度越大,坯料
被拉入凹模越困难,因此越容易产生拉裂废品。
一般情况下,拉深系数不小于0.5~0.8。
坯
料的塑性差取上限值,塑性好取下限值。
如果拉深系数过小,不能一次拉深成形时,则可采
用多次拉深工艺。
多次拉深过程中,必然产生加工硬化现象。
为了保证坯料具有足够的塑性,生产中坯料经过
一两次拉深后,应安排工序间的退火处理。
其次,在多次拉深中,拉深系数应一次比一次略
大些,确保拉深件质量和生产顺利进行。
(2)合理设计拉深模结构①凸凹模的圆角半径。
材料为钢的拉深件,取r凹=10t,而r凸=(0.6~1)r凹。
这两个圆角半径过小,产品易拉裂。
②凸凹模间隙。
一般取Z=(1.1~1.2)t,比冲裁模的间隙大。
间隙过小,模具与拉深件间的摩擦力增大,容易拉裂工件,擦伤工作表面,降低模具寿命。
间隙过大,又容易使拉深件起皱,影响拉深件的精度。
(3)注意润滑。
为了减小摩擦,以降低拉深件壁部的拉应力,减少模具的磨损,拉深时通常要加润滑剂。