四轴加工
轮模四轴加工工艺流程

轮模四轴加工工艺流程一、加工前的准备。
轮模四轴加工之前,那可得好好准备准备。
就像咱们出门旅行得收拾行李一样。
首先得把要加工的轮模材料选好,这材料的质量可是关键哦。
要是材料不好,后面加工得再精细都白搭。
就像盖房子,地基没打好,上面的建筑再漂亮也不稳当。
这材料得有合适的硬度、韧性啥的,得符合轮模的使用要求。
然后呢,咱们得看看加工设备。
四轴加工设备得调试好,各种参数都得检查检查。
就像给汽车做保养,每个零件都得看看有没有问题。
刀具也很重要呀,要选择合适的刀具,就像厨师做菜得选对厨具一样。
刀具的材质、形状都得考虑到,不同的加工部位可能需要不同的刀具呢。
二、粗加工。
准备工作做好了,就开始粗加工啦。
粗加工就像是给轮模打个大致的形状。
这时候呢,不用太讲究精细度,主要是把多余的材料去掉。
就像雕刻一个塑像,先把大的石块凿掉。
四轴加工的优势在这时候就有点体现出来了,它可以从不同的角度去加工,比普通的加工方式效率高不少呢。
不过在粗加工的时候,也要注意控制加工的量,别一下子去掉太多材料,要是不小心把该留下的部分也去掉了,那就麻烦啦。
三、半精加工。
粗加工完了,轮模有个大概样子了,就到半精加工啦。
这时候就像是给轮模做初步的修饰。
半精加工要把粗加工留下的一些不平整的地方弄得更光滑一些,尺寸也得更接近最终的要求。
这个过程就像是给塑像初步打磨一样,要让它看起来更精致一点。
在半精加工的时候,对加工精度的要求就提高了不少呢。
而且要考虑到后续精加工的余量,不能留太多也不能留太少,留太多精加工的时候工作量大,留太少又怕加工不到位。
四、精加工。
精加工那可是轮模加工的重头戏。
这时候就像是给轮模穿上漂亮的衣服,要让它变得完美无缺。
精加工的时候,加工的精度要求特别高。
每一个细节都得处理好,尺寸必须精确到很小的范围。
四轴加工在精加工的时候就特别厉害,可以通过不同轴的联动,把轮模的复杂形状加工得特别精细。
这时候操作人员就得特别小心啦,就像艺术家在创作最后的杰作一样,一点都不能马虎。
四轴加工中心机安全操作及保养规程
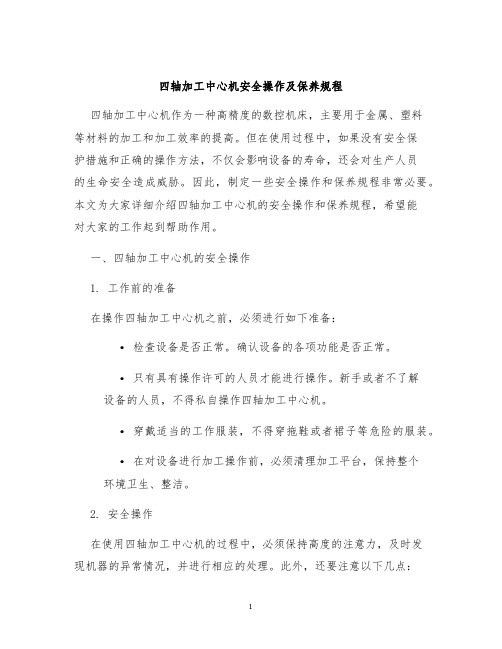
四轴加工中心机安全操作及保养规程四轴加工中心机作为一种高精度的数控机床,主要用于金属、塑料等材料的加工和加工效率的提高。
但在使用过程中,如果没有安全保护措施和正确的操作方法,不仅会影响设备的寿命,还会对生产人员的生命安全造成威胁。
因此,制定一些安全操作和保养规程非常必要。
本文为大家详细介绍四轴加工中心机的安全操作和保养规程,希望能对大家的工作起到帮助作用。
一、四轴加工中心机的安全操作1. 工作前的准备在操作四轴加工中心机之前,必须进行如下准备:•检查设备是否正常。
确认设备的各项功能是否正常。
•只有具有操作许可的人员才能进行操作。
新手或者不了解设备的人员,不得私自操作四轴加工中心机。
•穿戴适当的工作服装,不得穿拖鞋或者裙子等危险的服装。
•在对设备进行加工操作前,必须清理加工平台,保持整个环境卫生、整洁。
2. 安全操作在使用四轴加工中心机的过程中,必须保持高度的注意力,及时发现机器的异常情况,并进行相应的处理。
此外,还要注意以下几点:•在对设备操作之前,必须看清楚操作面板上的指示灯,确保设备处于正常的工作状态。
•对于还未完全确定的工件,必须采用轻切的方式进行雕刻,以避免给工件造成不必要的破损或者损坏。
•对待设备的化合物润滑油,必须使用相应的器具进行处理,不能在操作费电的情况下,使用手伸进去对设备进行润滑。
•在保持安全的前提下,可以对设备的参数进行逐级的提高。
3. 注意事项在对四轴加工中心机进行正式操作之前,还需要注意以下几个问题:•工作人员的肢体不能过于靠近加工处,以免被工件上的刀具切伤。
•必须注意刀具维护,避免刀具的断裂。
•在雕刻过程中,必须对设备进行监控,并及时调整参数,避免对设备和其它物品造成不必要的影响。
•在对设备进行工作时,必须保持空气流畅,避免发生爆炸。
二、四轴加工中心机的保养规程保养四轴加工中心机是非常重要的,能够延长设备的使用寿命,并保证其高效的工作效率。
因此,制定一个完善的保养规程非常有必要。
四轴加工理论讲解
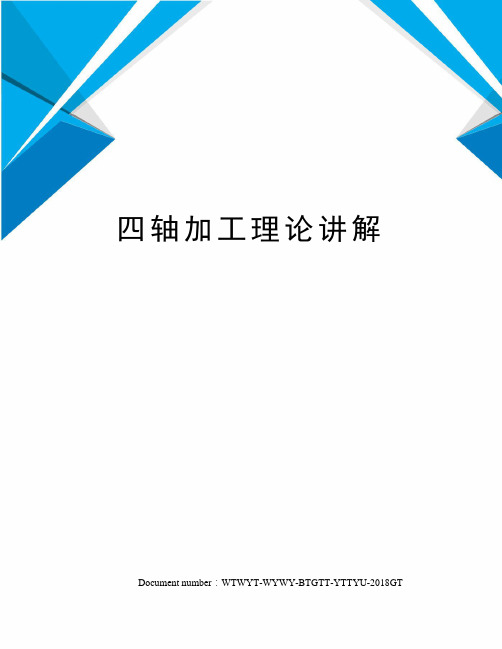
四轴加工理论讲解 Document number:WTWYT-WYWY-BTGTT-YTTYU-2018GT四轴加工典型案例教程第1节四轴机床结构特点与工作原理1.四轴的定义:一台机床上至少有4个坐标,分别为3个直线坐标和1个旋转坐标2.四轴加工特点:(1).三轴加工机床无法加工到的或需要装夹过长(2).提高自由空间曲面的精度、质量和效率(3).四轴与三轴的区别;四轴区别与三轴多一个旋转轴,四轴坐标的确立及其代码的表示Z轴的确定:机床主轴轴线方向或者装夹工件的工作台垂直方向为Z轴X轴的确定:与工件安装面平行的水平面或者在水平面内选择垂直与工件的旋转轴线的方向为X轴,远离主轴轴线的方向为正方向3.直线坐标X轴Y轴Z轴旋转坐标A轴、B轴A轴:绕X轴旋转为A轴(G代码)B轴:绕Y轴旋转为B轴(G代码)XYZ+A、XYZ+B、两种形式四轴XYZ+A适合加工旋转类工件、车铣复合加工XYZ+B工作台相对较小、主轴刚性差、适合加工小产品四轴可以实现产品除底面外5个面都可以做加工,加工前我们必须对产品进行分析,确定四轴机床。
第2节四轴加工优点应运典型零件的工艺方案实际生产加工常发生的问题及其解决方案1.三轴加工的缺点:1.刀具长度过长,刀具成本过高2.刀具振动引发表粗糙度问题3.工序增加,多次装夹4.刀具易破损5.刀具数量增加6.易过切引起不合格工件7.重复对刀产生累积公差2.四轴优点:1.刀具得到很大改善2.加工工序缩短装夹时间3.无需夹具4.提高表面质量5.延长刀具寿命6.生产集中化7.有效提高加工效率和生产效率3.四轴加工主要应运的领域:航空、造船、医学、汽车工业、模具4.四轴应运的典型零件:凸轮、涡轮、蜗杆、螺旋桨、鞋模、人体模型、汽车配件、其他精密零件加工5.四轴加工工工艺及其实际生产加工常发生的问题及其解决方案:(1).四轴工件坐标系的确立、四轴G代码NC程序表示(2).各种不同机台复杂零件的装夹(3).加工辅助线、辅助面的制作(4).四轴加工刀具与工件点接触,非刀轴中心的补偿(5).加工过程中刀具碰撞问题(6).刀轨的校验及其仿真加工(7).不同四轴机器,不同刀轨和后处理第3节结合案例讲解软件的综合使用技巧和新增功能的使用麻花钻四轴加工及其多轴驱动的讲解多轴驱动的应用,四轴加工的基本流程曲面驱动四轴开粗流线加工曲线、点加工2.多轴加工的装夹及其UG5多轴驱动的讲解多轴等高加工多轴外形轮廓加工多轴顺序铣加工第4节几何体9种驱动方法的详细讲解和各参数设置曲线/点驱动方法加工3D刻字、3D流道螺旋式、边界加工曲面加工(重点)曲面必须连续曲面UV方向一致辅助面驱动流线加工(常用)刀轨、径向切削、外形轮廓加工、用户自定义第5节多轴加工18种刀轴方向的控制和复杂零件轴向的判定刀轴:远离直线、朝向直线、远离点、朝向点、相对于矢量、(前倾角、后倾角)垂直于部件、相对于部件插补矢量、插补角度至部件、插补矢量至驱动、(前倾角、后倾角)优化后驱动、垂直于驱动体、侧刃驱动体、相对于驱动体(前倾角、后倾角)前倾角:沿着刀具加工方向来设定倾斜角度侧倾角:刀具加工方向两侧位置夹角的控制如果前倾角控制的是X方向,那么后倾角控制是Y方向,4轴垂直于部件、4轴垂直于驱动当切削方向发生变化后,旋转角度也相对应的发生变化旋转角度:沿着刀具加工方向来设定倾斜角度,加工方向为正角,反方向为负角4轴相对于部件、4轴相对驱动双4轴在部件上、双4轴在驱动上。
数控龙门铣四轴加工技术

数控龙门铣四轴加工技术是一种使用数控机床(数控车床、数控铣床等)进行多轴加工的加工方法,通常包括四个轴,分别是X轴、Y轴、Z轴和C轴。
这种技术可以加工出各种复杂的形状和尺寸,广泛应用于航空航天、汽车、电子、机械等领域。
数控龙门铣四轴加工技术的基本流程如下:
1. 工件的加工准备:将待加工的工件放置在数控龙门铣床上,并进行必要的固定和支撑。
2. 设置数控系统:根据加工需求,设置数控系统的坐标系、刀具长度、刀具半径等参数,确保加工的准确性和安全性。
3. 启动数控加工程序:将加工程序输入到数控系统中,并通过数控铣床的控制系统启动数控加工程序。
4. 加工执行:数控系统根据加工程序自动执行各个轴的铣削、钻孔、磨削等加工操作,直到达到加工要求。
5. 完成加工:加工完成后,数控系统自动停止加工,并将加工数据记录到数控系统中。
数控龙门铣四轴加工技术具有高精度、高效率、高稳定性等特点,可以加工出各种复杂形状的零部件,广泛应用于航空航天、汽车、电子、机械等领域。
(完整word)四轴加工理论讲解

UG8。
5四轴加工典型案例教程第1节四轴机床结构特点与工作原理1。
四轴的定义:一台机床上至少有4个坐标,分别为3个直线坐标和1个旋转坐标2.四轴加工特点:(1).三轴加工机床无法加工到的或需要装夹过长(2).提高自由空间曲面的精度、质量和效率(3)。
四轴与三轴的区别;四轴区别与三轴多一个旋转轴,四轴坐标的确立及其代码的表示Z轴的确定:机床主轴轴线方向或者装夹工件的工作台垂直方向为Z轴X轴的确定:与工件安装面平行的水平面或者在水平面内选择垂直与工件的旋转轴线的方向为X轴,远离主轴轴线的方向为正方向3。
直线坐标X轴Y轴Z轴旋转坐标A轴、B轴A轴:绕X轴旋转为A轴(G代码)B轴:绕Y轴旋转为B轴(G代码)XYZ+A、 XYZ+B、两种形式四轴XYZ+A 适合加工旋转类工件、车铣复合加工XYZ+B 工作台相对较小、主轴刚性差、适合加工小产品四轴可以实现产品除底面外5个面都可以做加工,加工前我们必须对产品进行分析,确定四轴机床。
第2节四轴加工优点应运典型零件的工艺方案实际生产加工常发生的问题及其解决方案1。
三轴加工的缺点:1。
刀具长度过长,刀具成本过高2。
刀具振动引发表粗糙度问题3.工序增加,多次装夹4.刀具易破损5。
刀具数量增加6。
易过切引起不合格工件7.重复对刀产生累积公差2。
四轴优点:1.刀具得到很大改善2.加工工序缩短装夹时间3。
无需夹具4.提高表面质量5。
延长刀具寿命6.生产集中化7。
有效提高加工效率和生产效率3.四轴加工主要应运的领域: 航空、造船、医学、汽车工业、模具4。
四轴应运的典型零件:凸轮、涡轮、蜗杆、螺旋桨、鞋模、人体模型、汽车配件、其他精密零件加工5.四轴加工工工艺及其实际生产加工常发生的问题及其解决方案:(1).四轴工件坐标系的确立、四轴G代码NC程序表示(2).各种不同机台复杂零件的装夹(3)。
加工辅助线、辅助面的制作(4)。
四轴加工刀具与工件点接触,非刀轴中心的补偿(5).加工过程中刀具碰撞问题(6)。
加工中心四轴关闭参数
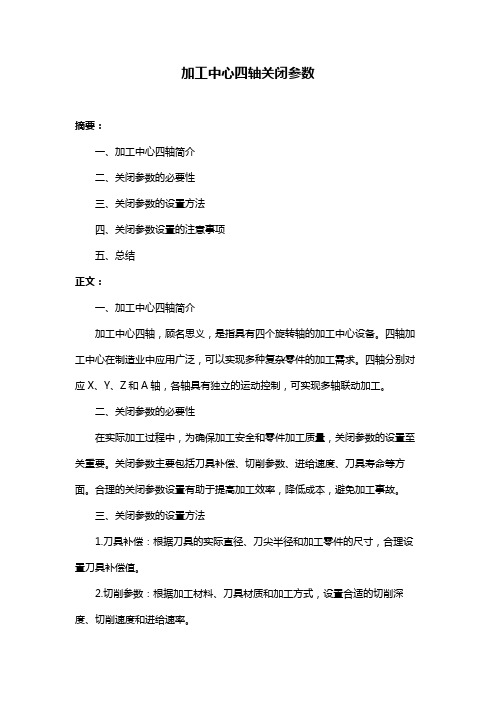
加工中心四轴关闭参数摘要:一、加工中心四轴简介二、关闭参数的必要性三、关闭参数的设置方法四、关闭参数设置的注意事项五、总结正文:一、加工中心四轴简介加工中心四轴,顾名思义,是指具有四个旋转轴的加工中心设备。
四轴加工中心在制造业中应用广泛,可以实现多种复杂零件的加工需求。
四轴分别对应X、Y、Z和A轴,各轴具有独立的运动控制,可实现多轴联动加工。
二、关闭参数的必要性在实际加工过程中,为确保加工安全和零件加工质量,关闭参数的设置至关重要。
关闭参数主要包括刀具补偿、切削参数、进给速度、刀具寿命等方面。
合理的关闭参数设置有助于提高加工效率,降低成本,避免加工事故。
三、关闭参数的设置方法1.刀具补偿:根据刀具的实际直径、刀尖半径和加工零件的尺寸,合理设置刀具补偿值。
2.切削参数:根据加工材料、刀具材质和加工方式,设置合适的切削深度、切削速度和进给速率。
3.进给速度:根据刀具的加工速度、加工零件的尺寸和加工精度要求,设置合适的进给速度。
4.刀具寿命:根据加工量、刀具材质和加工条件,合理设置刀具寿命,确保刀具在使用过程中的安全与稳定。
四、关闭参数设置的注意事项1.结合加工零件的实际需求,充分了解刀具性能,确保参数设置合理。
2.注意各轴之间的协调与配合,避免因轴间不同步导致的加工问题。
3.考虑加工过程中的安全性,避免因参数设置不当导致的设备损坏或人身安全事故。
4.定期检查和调整关闭参数,确保加工中心四轴运行稳定、加工质量可靠。
五、总结加工中心四轴关闭参数设置是保证加工顺利进行的关键环节。
只有合理地设置关闭参数,才能确保加工过程中的安全与质量。
加工人员应充分了解设备性能、加工零件要求,结合实际情况进行参数设置,不断提高加工效率,降低成本。
四轴加工中心参数

四轴加工中心参数概述四轴加工中心是一种用于进行金属加工的机床,具有四个坐标轴,可进行多轴数控加工。
为了达到最佳加工效果,四轴加工中心需要根据具体的加工需求进行参数调整。
本文将深入探讨四轴加工中心的参数设置,包括加工速度、加工深度、加工精度、半径补偿等方面内容。
加工速度加工速度是指加工中心在进行加工过程中,工具移动的速度。
加工速度直接影响加工效率和加工质量。
一般而言,加工速度越快,加工效率越高,但也容易导致加工质量不稳定。
因此,在设置加工速度时需要考虑多个因素,如材料硬度、工具刃口磨损等。
在参数设置过程中,通常会选择一个合适的加工速度范围,并根据具体情况进行微调。
加工深度加工深度是指工具在加工过程中进入材料的深度。
加工深度的设置主要受材料性质、工具强度和加工精度要求等因素影响。
一般而言,加工深度越大,加工时间越长,但也可以提高加工效率。
然而,加工深度过大可能导致工具折断或产生加工质量问题。
因此,在设置加工深度时需要综合考虑多个因素,为了实现更好的加工效果,常常需要通过实验和经验总结来确定最佳加工深度。
加工精度加工精度是指加工中心在进行加工过程中的精确度和稳定性。
加工精度对于一些精密零部件的加工尤为重要。
在四轴加工中心中,加工精度的设置涉及到多个参数,如进给速度、回转速度、切削速度等。
为了实现更高的加工精度,需要根据加工材料、加工形状和加工要求等因素,逐步调整不同参数,使其在一个合适的范围内。
半径补偿半径补偿是指在进行切削操作时,考虑到刀具半径的大小,通过适当调整刀具路径,保证最终加工出的尺寸与设计尺寸一致。
四轴加工中心通常会有半径补偿功能,可以根据实际情况进行设置。
半径补偿的参数设置与材料硬度、刀具半径、切削速度等有关,需要通过试验和实践来确定最佳参数。
总结四轴加工中心参数的设置对于加工效果和加工质量具有重要影响。
加工速度、加工深度、加工精度和半径补偿等参数需要根据具体情况进行合理的调整,以满足加工要求。
简述四轴数控机床加工的基本操作步骤。
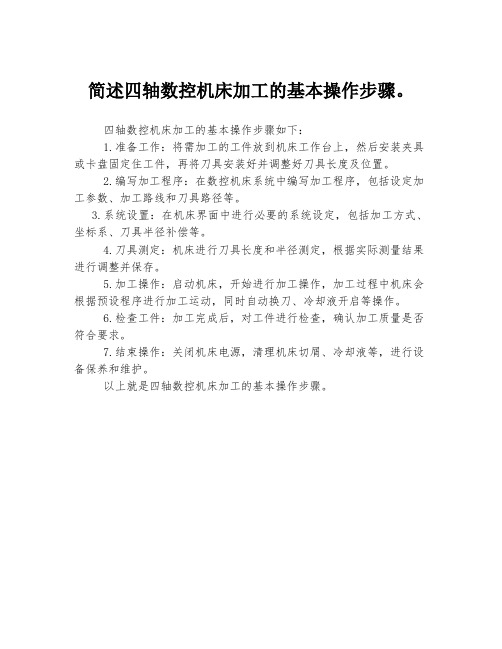
简述四轴数控机床加工的基本操作步骤。
四轴数控机床加工的基本操作步骤如下:
1.准备工作:将需加工的工件放到机床工作台上,然后安装夹具或卡盘固定住工件,再将刀具安装好并调整好刀具长度及位置。
2.编写加工程序:在数控机床系统中编写加工程序,包括设定加工参数、加工路线和刀具路径等。
3.系统设置:在机床界面中进行必要的系统设定,包括加工方式、坐标系、刀具半径补偿等。
4.刀具测定:机床进行刀具长度和半径测定,根据实际测量结果进行调整并保存。
5.加工操作:启动机床,开始进行加工操作,加工过程中机床会根据预设程序进行加工运动,同时自动换刀、冷却液开启等操作。
6.检查工件:加工完成后,对工件进行检查,确认加工质量是否符合要求。
7.结束操作:关闭机床电源,清理机床切屑、冷却液等,进行设备保养和维护。
以上就是四轴数控机床加工的基本操作步骤。
- 1、下载文档前请自行甄别文档内容的完整性,平台不提供额外的编辑、内容补充、找答案等附加服务。
- 2、"仅部分预览"的文档,不可在线预览部分如存在完整性等问题,可反馈申请退款(可完整预览的文档不适用该条件!)。
- 3、如文档侵犯您的权益,请联系客服反馈,我们会尽快为您处理(人工客服工作时间:9:00-18:30)。
先把待挖槽曲面定义成新的构图面,如Number 13,存储后将刀具平面也选为13,然后象作三轴加工一样作出刀具路径。所得到的刀具路径不能直接进行后置处理,因为它带双角度,不能或不一定能后置处理成适合T20 FIDIA控制器的程序格式。所以只有把该刀具路径经模拟后存成几何图素,然后在Top构图面和Top刀具面的状态下,选择该几何图素,作“Contour”加工。加工参数“计算机补偿”和“控制器补偿”均选“OFF”,“刀尖补偿”选择与上次刀具路径一致。如此得到的新刀具路径就相当于帮系统把双角度刀具路径转化成原始构图面(T面)中的刀具路径,将其进行通用后置处理后就得到T20刀头旋转固定A、B角后应走的NC程序。
T20的A、B角的是这样定义的:A角绕X轴旋转,B角绕Y轴旋转,B角是主动角,A角附加在B角上。T20的工作台不旋转,刀头可以作A、B角旋转。在MasterCAM建模时,首先要确定零件实际装夹位置(不超过A、B角定义的范围),构图面选择要与零件实际装夹面一致。
加工叉耳内外形时,实际上是T20的刀头旋转固定双角度A、B角,然后走类似三轴的刀具路径,但这种路径相对装夹面来说却是三维空间线。
MasterCAM在四轴、五轴加工中的应用技巧
一、四轴加工的应用
卫生巾切刀成型辊的数控加工主要是通过用平铣刀和锥度成型刀在XK-715M机床(带旋转轴的三坐标数控机床)上实现的。旋转轴上夹持的切刀成型辊相当于第四轴——A轴,刀具在圆柱体上走空间曲线,就得到刀刃的型面。
那么,如何建出这条卷在圆柱体上的空间曲线呢?
(4)用修改后的MPGEN5X_FANUC.PST后置处理程序后处理(Post)后得到的NC文件如图5所示。
图3
图4
图5
三、5轴加工拔模角面的应用
比如,实际中要在如图6所示的模具上加工扭转槽F,其底部带R3倒圆,槽的两个侧壁是空间扭转直纹面。加工方法是先在三轴上粗铣该槽,留精加工余量,然后在5轴铣床上用5轴联动方式精加工槽各面到位。考虑到槽宽及底部的R3倒圆,选用φ8(R3)铣刀加工。
MasterCAM V9在4轴和5轴加工中的应用
一、开发FIDIA T205轴后置处理程序
笔者利用MasterCAM V9提供的一个通用5轴后处理程序模板,即MPGEN5X_FANUC.PST,首先在充分了解模板的结构和内容的基础上,修改该程序模板的某些设置,即可得到适应FIDIA T20系统的5轴后置处理程序。
首先,在MasterCAM8.0中,根据切刀理论刃口展开图画出不同刀具的中心轨迹展开图,这是二维曲线。
然后,利用主菜单的转换→卷筒→串连,用串连的方式选取刀具轨迹曲线→然后设定卷筒直径、旋转轴X及曲线放置在的导动曲面,将空间曲线以投影方式投到圆柱面上进行加工。
二、5轴钻孔的应用
我们在实际加工中,往往需要钻曲面上的5轴法向孔或者石油钻头上的5轴切削齿孔,这些孔均要在T20上进行。以前的做法是在MasterCAM中先作出这些5轴孔的轴线,然后一根一根分析计算出每根线的B、A角度,最后手工在NC文件中输入B、A角度值。这种方法效率不高,而且容易出错。借助MasterCAM V9中Drill5ax的5轴钻孔功能,得到5轴钻孔刀具路径,然后用修改后的5轴后置处理程序进行POST,即可自动获得钻法线孔的NC文件。这样不仅提高了编程效率,同时又减少了出错机率。以图2钻曲面法向孔为例,说明MasterCAM V9中Drill5ax5轴钻孔功能的应用。
rot_ccw_pos : 1 #Axis signed dir, 0 = CW positive, 1 = CCW positive
之后,进入“NC管理”菜单→更改后置处理文件→选中MPFAN-1.PST文件,再对NCI文件进行后置处理,产生符合XK-715M机床的NC格式。
二、五轴加工的应用
以在FIDIA系统的T20上加工双角度叉耳内外形为例,说明用MasterCAM8.0实现T20上带固定角度的五轴加工。
分析最终产生的T20固定角度五轴加工NC程序,首先要加入刀头的A、B角信息,然后再走出三维空间线。
1.在MasterCAM 8.0中获得A、B角信息
按照上述装夹方式建出叉耳型面后,先作出待挖槽曲面的法失,然后在Front构图面(前视图)分析该法矢的信息,其中的角度信息就是我们要求的B角值;再在3D构图面状态,求出该法矢与Y轴的夹角,就得到A角的值。
图2
(1)先按曲面上的点作出曲面法向孔轴线;
(2)生成法向孔加工刀具路径:选择Toolpaths-Multiaxis-Drill5ax,出现图3所示对话框,点击“Points/Lines”选项,用Endpoints方式选择每个法向孔轴线的下端点,相当于控制了刀具轴线的方向;
(3)选完要加工的点后,出现5轴钻孔对话框,参数设置如图4所示;
# Rotary Axis Settings
# --------------------------
vmc : 1 #0 = Horizontal Machine, 1 = Vertical Mill
rot_on_x: 1 #Default Rotary Axis Orientation, See ques. 164. #0 = Off, 1 = About X, 2 = About Y, 3 = About Z
1. FIDIA T20的配置
主轴头双摆动,B为主动旋转轴,A为从动旋转轴,B轴在XZ平面内摆动,A轴在YZ平面内摆动,B轴的范围是±360°,A轴的范围≤+104°
2.修改MPGEN5X_FANUC.PST文件
针对FIDIA T20的配置修改MPGEN5X_FANUC.PST文件,如图1所示。
图1
虽然同样是FANUC系统,但XK-715M机床和加工中心控制器的所使用的格式稍有区别,所以在用MasterCAM后处理产生NC程序之前需修改后置处理文件MPFAN.PST。
方法如下:进入文件→编辑→*.PST→找到系统默认的MPFAN.PST文件,先作备份,如另存为MPFAN-1.PST文件,然后打开,找到下面清单中的变量rot_ccw_pos : 1,将其改为rot_ccw_pos : 0,并存盘。