四轴加工理论讲解
四轴加工理论讲解
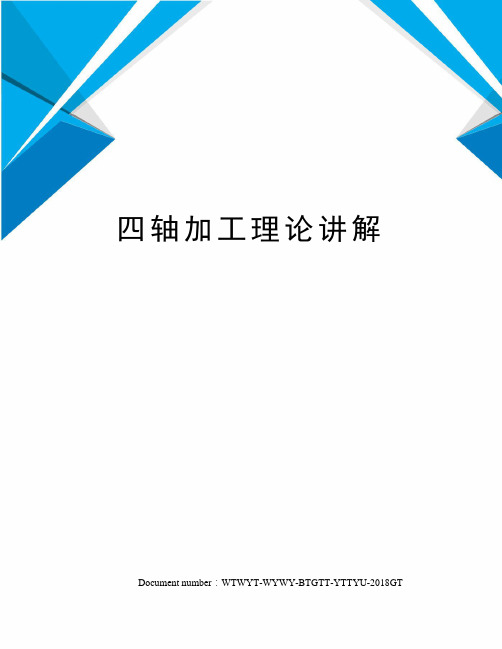
四轴加工理论讲解 Document number:WTWYT-WYWY-BTGTT-YTTYU-2018GT四轴加工典型案例教程第1节四轴机床结构特点与工作原理1.四轴的定义:一台机床上至少有4个坐标,分别为3个直线坐标和1个旋转坐标2.四轴加工特点:(1).三轴加工机床无法加工到的或需要装夹过长(2).提高自由空间曲面的精度、质量和效率(3).四轴与三轴的区别;四轴区别与三轴多一个旋转轴,四轴坐标的确立及其代码的表示Z轴的确定:机床主轴轴线方向或者装夹工件的工作台垂直方向为Z轴X轴的确定:与工件安装面平行的水平面或者在水平面内选择垂直与工件的旋转轴线的方向为X轴,远离主轴轴线的方向为正方向3.直线坐标X轴Y轴Z轴旋转坐标A轴、B轴A轴:绕X轴旋转为A轴(G代码)B轴:绕Y轴旋转为B轴(G代码)XYZ+A、XYZ+B、两种形式四轴XYZ+A适合加工旋转类工件、车铣复合加工XYZ+B工作台相对较小、主轴刚性差、适合加工小产品四轴可以实现产品除底面外5个面都可以做加工,加工前我们必须对产品进行分析,确定四轴机床。
第2节四轴加工优点应运典型零件的工艺方案实际生产加工常发生的问题及其解决方案1.三轴加工的缺点:1.刀具长度过长,刀具成本过高2.刀具振动引发表粗糙度问题3.工序增加,多次装夹4.刀具易破损5.刀具数量增加6.易过切引起不合格工件7.重复对刀产生累积公差2.四轴优点:1.刀具得到很大改善2.加工工序缩短装夹时间3.无需夹具4.提高表面质量5.延长刀具寿命6.生产集中化7.有效提高加工效率和生产效率3.四轴加工主要应运的领域:航空、造船、医学、汽车工业、模具4.四轴应运的典型零件:凸轮、涡轮、蜗杆、螺旋桨、鞋模、人体模型、汽车配件、其他精密零件加工5.四轴加工工工艺及其实际生产加工常发生的问题及其解决方案:(1).四轴工件坐标系的确立、四轴G代码NC程序表示(2).各种不同机台复杂零件的装夹(3).加工辅助线、辅助面的制作(4).四轴加工刀具与工件点接触,非刀轴中心的补偿(5).加工过程中刀具碰撞问题(6).刀轨的校验及其仿真加工(7).不同四轴机器,不同刀轨和后处理第3节结合案例讲解软件的综合使用技巧和新增功能的使用麻花钻四轴加工及其多轴驱动的讲解多轴驱动的应用,四轴加工的基本流程曲面驱动四轴开粗流线加工曲线、点加工2.多轴加工的装夹及其UG5多轴驱动的讲解多轴等高加工多轴外形轮廓加工多轴顺序铣加工第4节几何体9种驱动方法的详细讲解和各参数设置曲线/点驱动方法加工3D刻字、3D流道螺旋式、边界加工曲面加工(重点)曲面必须连续曲面UV方向一致辅助面驱动流线加工(常用)刀轨、径向切削、外形轮廓加工、用户自定义第5节多轴加工18种刀轴方向的控制和复杂零件轴向的判定刀轴:远离直线、朝向直线、远离点、朝向点、相对于矢量、(前倾角、后倾角)垂直于部件、相对于部件插补矢量、插补角度至部件、插补矢量至驱动、(前倾角、后倾角)优化后驱动、垂直于驱动体、侧刃驱动体、相对于驱动体(前倾角、后倾角)前倾角:沿着刀具加工方向来设定倾斜角度侧倾角:刀具加工方向两侧位置夹角的控制如果前倾角控制的是X方向,那么后倾角控制是Y方向,4轴垂直于部件、4轴垂直于驱动当切削方向发生变化后,旋转角度也相对应的发生变化旋转角度:沿着刀具加工方向来设定倾斜角度,加工方向为正角,反方向为负角4轴相对于部件、4轴相对驱动双4轴在部件上、双4轴在驱动上。
数控4轴简单编程方法

数控4轴简单编程方法什么是数控四轴数控四轴是一种具有四个轴向运动控制功能的数控机床,通常用于加工复杂形状的工件或进行多面加工。
它具有高精度、高效率、高刚性、高可靠性等优点,已广泛应用于航空航天、汽车制造、模具加工等领域。
数控四轴编程基础1. 基本概念数控四轴编程是通过预先编写好的程序指令,将加工工艺参数转化为各轴运动的指令,从而实现工件的自动加工。
在四轴编程中,必须清楚以下几个概念:- 坐标系:数控系统中采用的坐标系一般为数学直角坐标系,由X、Y、Z、A四轴构成。
- 原点:数控四轴坐标系中的一个定义点,通常为工件与机床的交点。
- 绝对坐标和相对坐标:绝对坐标是以原点为参考点的坐标,相对坐标是以上一刀具结束位置点为起点的坐标。
2. 数控四轴编程指令数控四轴编程将加工工艺参数转化为各轴运动指令的方式有多种,其中最常用的是G指令和M指令。
- G指令:用于定义运动方式和轴的速度,例如G00表示快速移动,G01表示线性插补运动,G02表示顺时针圆弧插补运动,G03表示逆时针圆弧插补运动。
- M指令:用于定义机床的辅助功能,例如M03表示主轴正转,M04表示主轴反转,M05表示主轴停止。
3. 编程案例以下是一个简单的数控四轴编程案例:markdown程序号:O0001N10 G90 G54 G17 G40 G49 G80N20 S500 M03N30 G43 Z100. H01 M08N40 G01 X50. Y50. Z5. F200.N50 G02 X100. Y100. R50.N60 G03 X150. Y150. R50.N70 G01 Z-10. F100.N80 G00 X0. Y0. Z100.N90 M05N100 M304. 编程步骤进行数控四轴编程时,一般按照以下步骤进行:1. 分析工件图纸,确定加工过程和每个工序的加工要求。
2. 根据工序要求选择合适的刀具,确定坐标系原点和刀具尺寸。
(完整word)四轴加工理论讲解

UG8。
5四轴加工典型案例教程第1节四轴机床结构特点与工作原理1。
四轴的定义:一台机床上至少有4个坐标,分别为3个直线坐标和1个旋转坐标2.四轴加工特点:(1).三轴加工机床无法加工到的或需要装夹过长(2).提高自由空间曲面的精度、质量和效率(3)。
四轴与三轴的区别;四轴区别与三轴多一个旋转轴,四轴坐标的确立及其代码的表示Z轴的确定:机床主轴轴线方向或者装夹工件的工作台垂直方向为Z轴X轴的确定:与工件安装面平行的水平面或者在水平面内选择垂直与工件的旋转轴线的方向为X轴,远离主轴轴线的方向为正方向3。
直线坐标X轴Y轴Z轴旋转坐标A轴、B轴A轴:绕X轴旋转为A轴(G代码)B轴:绕Y轴旋转为B轴(G代码)XYZ+A、 XYZ+B、两种形式四轴XYZ+A 适合加工旋转类工件、车铣复合加工XYZ+B 工作台相对较小、主轴刚性差、适合加工小产品四轴可以实现产品除底面外5个面都可以做加工,加工前我们必须对产品进行分析,确定四轴机床。
第2节四轴加工优点应运典型零件的工艺方案实际生产加工常发生的问题及其解决方案1。
三轴加工的缺点:1。
刀具长度过长,刀具成本过高2。
刀具振动引发表粗糙度问题3.工序增加,多次装夹4.刀具易破损5。
刀具数量增加6。
易过切引起不合格工件7.重复对刀产生累积公差2。
四轴优点:1.刀具得到很大改善2.加工工序缩短装夹时间3。
无需夹具4.提高表面质量5。
延长刀具寿命6.生产集中化7。
有效提高加工效率和生产效率3.四轴加工主要应运的领域: 航空、造船、医学、汽车工业、模具4。
四轴应运的典型零件:凸轮、涡轮、蜗杆、螺旋桨、鞋模、人体模型、汽车配件、其他精密零件加工5.四轴加工工工艺及其实际生产加工常发生的问题及其解决方案:(1).四轴工件坐标系的确立、四轴G代码NC程序表示(2).各种不同机台复杂零件的装夹(3)。
加工辅助线、辅助面的制作(4)。
四轴加工刀具与工件点接触,非刀轴中心的补偿(5).加工过程中刀具碰撞问题(6)。
加工中心四轴关闭参数
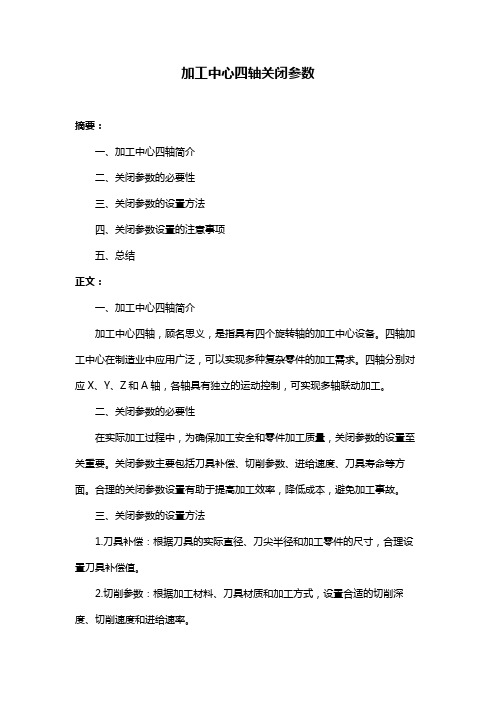
加工中心四轴关闭参数摘要:一、加工中心四轴简介二、关闭参数的必要性三、关闭参数的设置方法四、关闭参数设置的注意事项五、总结正文:一、加工中心四轴简介加工中心四轴,顾名思义,是指具有四个旋转轴的加工中心设备。
四轴加工中心在制造业中应用广泛,可以实现多种复杂零件的加工需求。
四轴分别对应X、Y、Z和A轴,各轴具有独立的运动控制,可实现多轴联动加工。
二、关闭参数的必要性在实际加工过程中,为确保加工安全和零件加工质量,关闭参数的设置至关重要。
关闭参数主要包括刀具补偿、切削参数、进给速度、刀具寿命等方面。
合理的关闭参数设置有助于提高加工效率,降低成本,避免加工事故。
三、关闭参数的设置方法1.刀具补偿:根据刀具的实际直径、刀尖半径和加工零件的尺寸,合理设置刀具补偿值。
2.切削参数:根据加工材料、刀具材质和加工方式,设置合适的切削深度、切削速度和进给速率。
3.进给速度:根据刀具的加工速度、加工零件的尺寸和加工精度要求,设置合适的进给速度。
4.刀具寿命:根据加工量、刀具材质和加工条件,合理设置刀具寿命,确保刀具在使用过程中的安全与稳定。
四、关闭参数设置的注意事项1.结合加工零件的实际需求,充分了解刀具性能,确保参数设置合理。
2.注意各轴之间的协调与配合,避免因轴间不同步导致的加工问题。
3.考虑加工过程中的安全性,避免因参数设置不当导致的设备损坏或人身安全事故。
4.定期检查和调整关闭参数,确保加工中心四轴运行稳定、加工质量可靠。
五、总结加工中心四轴关闭参数设置是保证加工顺利进行的关键环节。
只有合理地设置关闭参数,才能确保加工过程中的安全与质量。
加工人员应充分了解设备性能、加工零件要求,结合实际情况进行参数设置,不断提高加工效率,降低成本。
四轴加工中心参数

四轴加工中心参数概述四轴加工中心是一种用于进行金属加工的机床,具有四个坐标轴,可进行多轴数控加工。
为了达到最佳加工效果,四轴加工中心需要根据具体的加工需求进行参数调整。
本文将深入探讨四轴加工中心的参数设置,包括加工速度、加工深度、加工精度、半径补偿等方面内容。
加工速度加工速度是指加工中心在进行加工过程中,工具移动的速度。
加工速度直接影响加工效率和加工质量。
一般而言,加工速度越快,加工效率越高,但也容易导致加工质量不稳定。
因此,在设置加工速度时需要考虑多个因素,如材料硬度、工具刃口磨损等。
在参数设置过程中,通常会选择一个合适的加工速度范围,并根据具体情况进行微调。
加工深度加工深度是指工具在加工过程中进入材料的深度。
加工深度的设置主要受材料性质、工具强度和加工精度要求等因素影响。
一般而言,加工深度越大,加工时间越长,但也可以提高加工效率。
然而,加工深度过大可能导致工具折断或产生加工质量问题。
因此,在设置加工深度时需要综合考虑多个因素,为了实现更好的加工效果,常常需要通过实验和经验总结来确定最佳加工深度。
加工精度加工精度是指加工中心在进行加工过程中的精确度和稳定性。
加工精度对于一些精密零部件的加工尤为重要。
在四轴加工中心中,加工精度的设置涉及到多个参数,如进给速度、回转速度、切削速度等。
为了实现更高的加工精度,需要根据加工材料、加工形状和加工要求等因素,逐步调整不同参数,使其在一个合适的范围内。
半径补偿半径补偿是指在进行切削操作时,考虑到刀具半径的大小,通过适当调整刀具路径,保证最终加工出的尺寸与设计尺寸一致。
四轴加工中心通常会有半径补偿功能,可以根据实际情况进行设置。
半径补偿的参数设置与材料硬度、刀具半径、切削速度等有关,需要通过试验和实践来确定最佳参数。
总结四轴加工中心参数的设置对于加工效果和加工质量具有重要影响。
加工速度、加工深度、加工精度和半径补偿等参数需要根据具体情况进行合理的调整,以满足加工要求。
UG四轴加工讲解
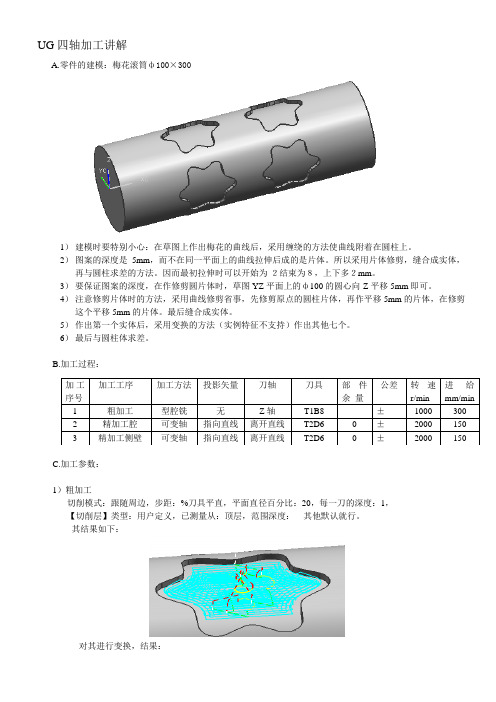
UG四轴加工讲解A.零件的建模:梅花滚筒ф100×3001)建模时要特别小心:在草图上作出梅花的曲线后,采用缠绕的方法使曲线附着在圆柱上。
2)图案的深度是5mm,而不在同一平面上的曲线拉伸后成的是片体。
所以采用片体修剪,缝合成实体,再与圆柱求差的方法。
因而最初拉伸时可以开始为-2结束为8,上下多2mm。
3)要保证图案的深度,在作修剪圆片体时,草图YZ平面上的ф100的圆心向-Z平移5mm即可。
4)注意修剪片体时的方法,采用曲线修剪省事,先修剪原点的圆柱片体,再作平移5mm的片体,在修剪这个平移5mm的片体。
最后缝合成实体。
5)作出第一个实体后,采用变换的方法(实例特征不支持)作出其他七个。
6)最后与圆柱体求差。
B.加工过程:C.加工参数:1)粗加工切削模式:跟随周边,步距:%刀具平直,平面直径百分比:20,每一刀的深度:1,【切削层】类型:用户定义,已测量从:顶层,范围深度:其他默认就行。
其结果如下:对其进行变换,结果:加工序号加工工序加工方法投影矢量刀轴刀具部件余量公差转速r/min进给mm/min1 粗加工型腔铣无Z轴T1B8 ±1000 3002 精加工腔可变轴指向直线离开直线T2D6 0 ±2000 1503 精加工侧壁可变轴指向直线离开直线T2D6 0 ±2000 150其中,CA VITY_MILL_1_1为第一个(即原始生成的)CA VITY_MILL_2_1为将CA VITY_MILL_1_1轴向(+X)平移100复制出来的。
其他6个刀轨为“绕直线旋转”“Multiple Copies”(多重复制)出来的。
2)精加工腔(采用可变轴铣,即4轴联动)a.采用边界的驱动方式来限制刀具的切削区域创建的边界生成的刀轨边界只能创建在平面上,所以刀轨在上下显得余量很大b.其他采用精加工的默认参数即可。
c.将刀轨复制平移,然后Multiple Copies。
四轴加工实例讲义

四轴加工实例教程讲义讲授教师:_____ __2011年月日一、加工任务概述利用图1-1 所示的“福”字图片,通过Mastercam 的四轴加工功能得到笔筒造型。
具体步骤如下:1)把图片中的“福”字转化成Mastercam 可读入的Autodesk 格式,或利用Mastercam9.1 自带的功能,直接可以把图片格式转换成线条。
2)经过编辑后,得到我们加工笔筒所需要的线条图形,再把图形缠绕在直径为95mm 的圆筒上3)通过Mastercam 的四轴加工功能得到笔筒造型。
图1-1 未编辑前的福字为图片格式经过图片转换,再加上修饰花边,加工后即为如图1-2 效果。
图1-2 经过图片转换经过图片转换、、修饰后的加工效果二、工艺方案笔筒的加工工艺方案如表所示。
1)工艺设计笔筒的加工工艺方案笔筒毛坯如图1-3 所示,材质为铝镁合金5050。
在实际加工中,毛坯已没有夹持余量,不可能再用三爪夹持笔筒外圆的方法加工,但可设计一阶梯芯轴,用三爪夹持心轴,找正后,把笔筒套入芯轴,并用顶尖顶牢,由于实际加工过程中,切削力很小,笔筒内孔与芯轴之间为精密配合,顶尖顶牢后,预紧力完全满足加工切削力的要求。
装夹方案设计如图1-4 所示。
图1-3 笔筒毛坯半剖视图图1-4 笔筒加工示意图2)芯轴设计经测量,笔筒的内孔直径为φ80.01mm,故芯轴直径选用φ80h5 (0+0.015),最小间隙为0.01mm,最大间隙为0.025mm,可以满足装配加工要求。
芯轴设计方案如图1-5 所示。
图1-5 芯轴设计图形三、加工模型准备1)图片转换 Mastercam9.1 版本能针对图片加工,且开发了图片直接转换成线条的程序,具体操作方法如下:步骤 1 选择需要的图片:单击“MAIN MENE”→“File”→“Converters”→“Next menu”→“Rast2vec”,选择要选的图片“福字”,如图1-6 所示。
图1-6 利用Mastercam9.1 图片加工功能选择图片步骤 2 把原图形转换为黑白图形:单击“Linear Black/White conversion”→拖动调节按钮,改变图形颜色→单击“OK”按钮,如图1-7 所示。
UG四轴加工讲解

UG 四轴加工讲解A.零件的建模:梅花滚筒ф100×3001) 建模时要特别小心:在草图上作出梅花的曲线后,采用缠绕的方法使曲线附着在圆柱上。
2) 图案的深度是5mm ,而不在同一平面上的曲线拉伸后成的是片体。
所以采用片体修剪,缝合成实体,再与圆柱求差的方法。
因而最初拉伸时可以开始为-2结束为8,上下多2mm 。
3) 要保证图案的深度,在作修剪圆片体时,草图YZ 平面上的ф100的圆心向-Z 平移5mm 即可。
4) 注意修剪片体时的方法,采用曲线修剪省事,先修剪原点的圆柱片体,再作平移5mm 的片体,在修剪这个平移5mm 的片体。
最后缝合成实体。
5) 作出第一个实体后,采用变换的方法(实例特征不支持)作出其他七个。
6) 最后与圆柱体求差。
B.加工过程:C.加工参数:1)粗加工切削模式:跟随周边,步距:%刀具平直,平面直径百分比:20,每一刀的深度:1, 【切削层】类型:用户定义,已测量从:顶层,范围深度:5.0 其他默认就行。
其结果如下:加工序号 加工工序 加工方法 投影矢量 刀轴 刀具 部件余 量 公差 转速r/min 进给mm/min 1 粗加工 型腔铣 无 Z 轴 T1B8 0.5 ±0.05 1000 300 2 精加工腔 可变轴 指向直线 离开直线 T2D6 0 ±0.01 2000 150 3精加工侧壁可变轴指向直线离开直线T2D6±0.012000150对其进行变换,结果:其中,CAVITY_MILL_1_1为第一个(即原始生成的)CAVITY_MILL_2_1为将CAVITY_MILL_1_1轴向(+X)平移100复制出来的。
其他6个刀轨为“绕直线旋转”“Multiple Copies”(多重复制)出来的。
2)精加工腔(采用可变轴铣,即4轴联动)a.采用边界的驱动方式来限制刀具的切削区域创建的边界生成的刀轨边界只能创建在平面上,所以刀轨在上下显得余量很大b.其他采用精加工的默认参数即可。
- 1、下载文档前请自行甄别文档内容的完整性,平台不提供额外的编辑、内容补充、找答案等附加服务。
- 2、"仅部分预览"的文档,不可在线预览部分如存在完整性等问题,可反馈申请退款(可完整预览的文档不适用该条件!)。
- 3、如文档侵犯您的权益,请联系客服反馈,我们会尽快为您处理(人工客服工作时间:9:00-18:30)。
四轴加工理论讲解
This model paper was revised by the Standardization Office on December 10, 2020
U G8.5四轴加工典型案例教程第1节四轴机床结构特点与工作原理
1.四轴的定义:一台机床上至少有4个坐标,分别为3个直线坐标和1个旋转坐标
2.四轴加工特点:
(1).三轴加工机床无法加工到的或需要装夹过长
(2).提高自由空间曲面的精度、质量和效率
(3).四轴与三轴的区别;四轴区别与三轴多一个旋转轴,四轴坐标的确立及其代码的表示
Z轴的确定:机床主轴轴线方向或者装夹工件的工作台垂直方向为Z轴
X轴的确定:与工件安装面平行的水平面或者在水平面内选择垂直与工件的旋转轴线的方向为X轴,远离主轴轴线的方向为正方向
3.直线坐标X轴Y轴Z轴
旋转坐标A轴、B轴
A轴:绕X轴旋转为A轴(G代码)
B轴:绕Y轴旋转为B轴(G代码)
XYZ+A、XYZ+B、两种形式四轴
XYZ+A适合加工旋转类工件、车铣复合加工
XYZ+B工作台相对较小、主轴刚性差、适合加工小产品
四轴可以实现产品除底面外5个面都可以做加工,加工前我们必须对产品进行分析,确定四轴机床。
第2节四轴加工优点应运典型零件的工艺方案实际生产加工常发生的问题及其解决方案
1.三轴加工的缺点:1.刀具长度过长,刀具成本过高
2.刀具振动引发表粗糙度问题
3.工序增加,多次装夹
4.刀具易破损
5.刀具数量增加
6.易过切引起不合格工件
7.重复对刀产生累积公差
2.四轴优点:1.刀具得到很大改善2.加工工序缩短装夹时间
3.无需夹具
4.提高表面质量
5.延长刀具寿命
6.生产集中化
7.有效提高加工效率和生产效率
3.四轴加工主要应运的领域:航空、造船、医学、汽车工业、模具
4.四轴应运的典型零件:凸轮、涡轮、蜗杆、螺旋桨、鞋模、人体模型、汽车配件、其他精密零件加工
5.四轴加工工工艺及其实际生产加工常发生的问题及其解决方案:
(1).四轴工件坐标系的确立、四轴G代码NC程序表示
(2).各种不同机台复杂零件的装夹
(3).加工辅助线、辅助面的制作
(4).四轴加工刀具与工件点接触,非刀轴中心的补偿
(5).加工过程中刀具碰撞问题
(6).刀轨的校验及其仿真加工
(7).不同四轴机器,不同刀轨和后处理
第3节结合案例讲解软件的综合使用技巧和UG8.5新增功能的使用
麻花钻四轴加工及其UG8.5多轴驱动的讲解
1.UG多轴驱动的应用,四轴加工的基本流程
曲面驱动四轴开粗
流线加工
曲线、点加工
2.多轴加工的装夹及其UG5多轴驱动的讲解
多轴等高加工
多轴外形轮廓加工
多轴顺序铣加工
第4节UG8.5几何体9种驱动方法的详细讲解和各参数设置
曲线/点驱动方法加工3D刻字、3D流道
螺旋式、边界加工
曲面加工(重点)曲面必须连续曲面UV方向一致辅助面驱动
流线加工(常用)
刀轨、径向切削、外形轮廓加工、用户自定义
第5节UG8.5多轴加工18种刀轴方向的控制和复杂零件轴向的判定刀轴:
远离直线、朝向直线、远离点、朝向点、
相对于矢量、(前倾角、后倾角)垂直于部件、相对于部件
插补矢量、插补角度至部件、插补矢量至驱动、(前倾角、后倾角)优化后驱动、
垂直于驱动体、侧刃驱动体、相对于驱动体(前倾角、后倾角)
前倾角:沿着刀具加工方向来设定倾斜角度
侧倾角:刀具加工方向两侧位置夹角的控制
如果前倾角控制的是X方向,那么后倾角控制是Y方向,
4轴垂直于部件、4轴垂直于驱动
当切削方向发生变化后,旋转角度也相对应的发生变化
旋转角度:沿着刀具加工方向来设定倾斜角度,加工方向为正角,反方向为负角
4轴相对于部件、4轴相对驱动
双4轴在部件上、双4轴在驱动上。