某重型车驱动桥后桥壳疲劳强度分析
某重型汽车驱动桥壳疲劳寿命分析

某重型汽车驱动桥壳疲劳寿命分析摘要:本文研究了某重型汽车驱动桥壳的疲劳寿命分析问题。
通过有限元模拟和实验验证相结合的方法,对驱动桥壳的应力分布进行了分析,在此基础上建立了疲劳寿命预测模型,并对驱动桥壳的疲劳寿命进行了预测和分析。
研究结果表明,驱动桥壳的疲劳寿命主要受到载荷大小和工作时间的影响,合理的设计和使用能够有效延长驱动桥壳的使用寿命。
关键词:重型汽车、驱动桥壳、疲劳寿命、有限元模拟、预测模型正文:一、引言重型汽车驱动桥作为汽车的重要组成部分,其安全性、稳定性和寿命等方面的问题备受关注。
其中,驱动桥壳作为驱动桥中的重要部件,发挥着机械传动的作用,其疲劳寿命是影响驱动桥性能的关键因素之一。
因此,以疲劳寿命为指标进行设计和使用,具有重要实际意义。
二、有限元模拟本研究采用有限元模拟方法,对驱动桥壳的应力分布进行了分析。
首先,根据实际工况建立驱动桥壳的有限元模型,并进行初始应力计算;其次,考虑到工况的不确定性和复杂性,采用随机载荷的方法对驱动桥壳进行了多次加载,得到驱动桥壳在不同载荷下的应力分布;最后,基于应力分布和材料的力学参数,对驱动桥壳的疲劳寿命进行预测和分析。
三、实验验证为了验证有限元模拟的预测结果,本研究还进行了实验验证。
在实验中,采用疲劳试验机对驱动桥壳进行了多次加载,得到了驱动桥壳的疲劳寿命数据。
通过对比有限元模拟和实验结果,验证了模型的准确性和可靠性。
四、疲劳寿命预测模型本研究根据有限元模拟和实验结果,建立了驱动桥壳的疲劳寿命预测模型。
该模型考虑了载荷大小、工作时间、材料等因素的影响,可以对驱动桥壳的疲劳寿命进行准确预测和分析。
五、结论本研究对某重型汽车驱动桥壳的疲劳寿命进行了预测和分析。
通过有限元模拟和实验验证相结合的方法,建立了疲劳寿命预测模型,可以对驱动桥壳的疲劳寿命进行准确预测和分析。
研究结果表明,驱动桥壳的疲劳寿命主要受到载荷大小和工作时间的影响,合理的设计和使用能够有效延长驱动桥壳的使用寿命。
某重载铁路货车疲劳强度分析
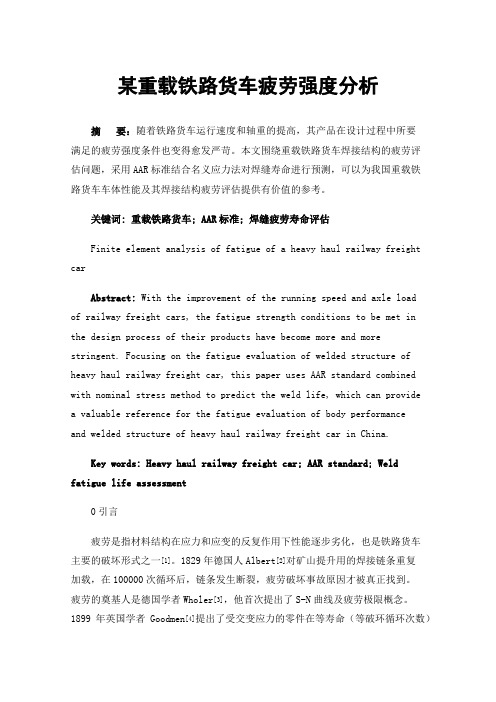
某重载铁路货车疲劳强度分析摘要:随着铁路货车运行速度和轴重的提高,其产品在设计过程中所要满足的疲劳强度条件也变得愈发严苛。
本文围绕重载铁路货车焊接结构的疲劳评估问题,采用AAR标准结合名义应力法对焊缝寿命进行预测,可以为我国重载铁路货车车体性能及其焊接结构疲劳评估提供有价值的参考。
关键词: 重载铁路货车; AAR标准; 焊缝疲劳寿命评估Finite element analysis of fatigue of a heavy haul railway freight carAbstract: With the improvement of the running speed and axle loadof railway freight cars, the fatigue strength conditions to be met in the design process of their products have become more and more stringent. Focusing on the fatigue evaluation of welded structure of heavy haul railway freight car, this paper uses AAR standard combined with nominal stress method to predict the weld life, which can provide a valuable reference for the fatigue evaluation of body performanceand welded structure of heavy haul railway freight car in China.Key words:Heavy haul railway freight car; AAR standard; Weld fatigue life assessment0引言疲劳是指材料结构在应力和应变的反复作用下性能逐步劣化,也是铁路货车主要的破坏形式之一[1]。
驱动桥疲劳可靠性分析与试验方法
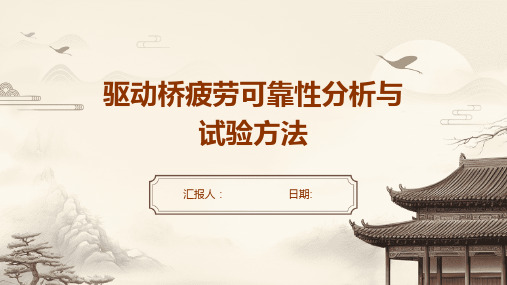
通过应变-强度干涉模型,计算结构或构件的疲劳可靠性。
有限元分析方法
利用有限元软件,对结构或构件进行疲劳可靠性分析。
驱动桥疲劳可靠性模型
基于应力-强度干涉模型的驱动桥疲劳可靠性模型
该模型考虑了应力分布、应力幅值、平均应力等因素对驱动桥疲劳寿命的影响,通过计算应力-强度干涉概率来 评估驱动桥的疲劳可靠性。
对收集到的数据进行整理、分析,提取有关驱动桥疲劳 性能的指标,如S-N曲线、疲劳极限等。
试验数据处理与分析
数据清洗
去除异常数据,确保数据的准 确性和可靠性。
统计分析
对收集到的数据进行统计分析,计 算平均值、标准差等统计指标,评 估驱动桥的可靠性及寿命。
结果评估
根据分析结果,评估驱动桥的疲劳 性能及可靠性,与设计要求进行对 比,为优化产品设计及制造工艺提 供依据。
根据试验结果和仿真分 析,提出优化方案,包 括改进驱动桥的结构设 计和优化材料选择。
进行室内外疲劳试验, 验证优化后的驱动桥的 疲劳可靠性是否满足要 求。
06
CATALOGUE
总结与展望
当前研究的总结
驱动桥疲劳可靠性分析方法
01
研究了驱动桥的疲劳失效机理,建立了疲劳可靠性分析模型,
并提出了相应的修正系数。
05
CATALOGUE
案例分析与应用
某型号汽车驱动桥的疲劳可靠性分析案例
背景介绍
某汽车制造商在市场上批量反映一 款汽车驱动桥存在疲劳可靠性问题 ,要求进行原因分析和解决方案。
问题识别
通过应力-强度干涉模型,分析驱动 桥的应力分布和强度分布,找出导 致疲劳失效的原因。
模型建立
利用有限元分析方法,建立驱动桥 的有限元模型,进行应力仿真和强 度仿真。
基于整车动力学仿真的后桥壳疲劳寿命分析与改进.

2009年(第31卷第2期汽车工程Aut omotive Engineering2009(Vol .31No .22009023基于整车动力学仿真的后桥壳疲劳寿命分析与改进33“985工程”汽车先进设计制造技术科技创新平台项目、国家863计划项目(2002AA503010资助。
原稿收到日期为2008年4月14日,修改稿收到日期为2008年7月21日。
唐应时1,张武1,段心林1,李克安2,和进军1(11湖南大学,汽车车身先进设计制造国家重点实验室,长沙410082;21湖南理工学院机电系,岳阳414000[摘要]针对某越野车在改型过程中后桥壳在台架疲劳试验时出现局部开裂的情况,应用ADAM S/Car 建立了整车动力学模型,进行动力学仿真,得出危险工况冲击载荷下桥壳的受力情况。
采用ANSYSWorkbench 对桥壳进行了疲劳寿命计算,结果与试验吻合。
分析其存在的不足,并提出了改进方案。
对改进后的桥壳再次进行疲劳计算,满足设计要求,试制后进行台架试验,寿命达到国家标准要求。
关键词:动力学仿真;后桥壳;疲劳寿命分析;改进Analysis and Imp r ovement of Rear Axle Housing Fatigue L ifeBased on Vehicle Dyna m ics Simulati onTang Y i n gsh i 1,Zhang W u 1,D uan X i n li n 1,L i Kean 2&He J i n jun111Hunan U niversity,S tate Key Laboratory of A dvanced D esign and M anufacturing for V ehicle B ody,Changsha 410082;21D epart m ent of M echanical and Electrical Engineering,Hunan Institute of Science and Technology,Yueyang 414000[Abstract]I n vie w of crack occurrence of rear axle housing in fatigue test during the course of a S UV modi 2ficati on,a comp lete vehicle dyna m ics model is built using ADAMS/Car and a dyna m ics si m ulati on is conducted with the forces exerted on axle housing in critical i m pact l oading conditi ons obtained .The fatigue life of axle housing is calculated by using ANSYSWorkbench,which well agrees with test results .The causes of defects are analyzed and s ome i m p r ove ment sche mes are p r oposed .The fatiguelife of modified housing is check again,which meets design require ments .Bench tests are als o carried out on trial p r oduced housing with its fatigue life meeting nati onal stand 2ard .Keywords:dynam i cs si m ul a ti on;rear axle housi n g;fa ti gue li fe ana lysis ;i m prove m en t前言驱动桥桥壳是汽车的重要零件之一,它是主减速器、差速器、半轴的外壳,一方面它起着支撑汽车荷重的作用,另一方面将载荷传给车轮,以及将路面反作用力传递给车身,它既是承载件又是传力件[1]。
后桥桥壳强度计算(垂直、牵引、制动、侧滑工况)

后桥桥壳强度计算(垂直、牵引、制动、侧滑工况)根据《汽车车桥设计》的方法进行计算简算。
数据仅供参考。
这种计算只适合设计初期的粗略计算判断。
实际设计时,需结合有限元分析软件,以处理桥壳的细节尺寸,使应力分布在更合理的状态。
本例子计算的桥壳结构如下截图所示(悬架按普通板簧悬架,车辆承载的力作用于桥壳方截面上面的的板簧盖板上-下图中未画出上盖板):说明:折算到桥壳板簧座处的受力时,应该要用10T减去桥总成的重量的。
不过本例子中是按作用在板簧座处的力为额定载荷,到轮胎上时,是额定载荷+桥重量。
这样算更保险点。
相当于叠加了一点安全系数。
注2:上述表格中的计算都是基于水平路面进行的计算。
所以计算结果仅能作为基础参考数据,起到数据统计对比的价值。
如果车桥使用的路况很恶劣,需要额外考虑坡度、凹坑、凸起等其他因素。
附件-计算表格:桥壳强度计算.xlsx项目代号单位数值两板簧座之间的弯矩M M Nm 28665桥壳截面宽 B mm 135 桥壳板簧截面处的静弯曲应力σwj Mpa 98.7因是垂直静弯曲强度计算,所以按2.5倍计算。
地面对后驱动桥左轮的垂向反作用力Z2R N 88519.9地面对左右驱动轮的最大切向反作用力Pmax N 142135.4重力加速度g m/s^2 9.8驱动桥承受的侧向力P2 N板簧对桥壳的垂向作用力-左侧T2L N1565.8原则上讲a+b 的值越大越好。
但是受空间和质量的限制,又不能做的太大,所以一般情况按a+b ≈rr/4。
离)。
因为此值一般都比较小,所以就省略了。
A-A 截面的垂向弯矩 M Nm 41743.0总结:上述计算的汇总信息如下:例如:公路用桥时,1为*.*g ,2为*.*g ,3为*.*g ,4为*.*g 。
(*.*为某一统计经验数值(即几点几个g 。
g 代表额定载荷)。
当有多个方向受力时,需要叠加各个实际载荷方向的数值)恶劣路面用桥时可在上述条件下叠加一些载荷,或是要求更高的安全系数,即在相同载荷条件下,允许的最大应力值必须更小一些。
重型商用车驱动桥壳典型工况计算方法分析

一轮 i 验地
— —
Y,=Y, l o o
.
汽 车 的簧上 载 荷 ,而沿 左右 轮胎 中心线 ,地 面给 轮
力 ( 胎时 则沿 双 胎 中心 ) 双 ,受 力如 图 1 示 。 所
轮与 胎】
2 驱 动桥 有 限 元计 算方 法
驱动桥有 限元计算的前期 环节是建立桥 壳几1
型 建立 的好 坏 直接关
系计算 结果 的正 确 与 否 ,针 对较 复 杂的桥
壳 结 构 , 用 三 维 软 采
.
1 l
件UG来 建 立 几何 模
型 ,如图2 示 。 所
在 有 限 元 分 析 图 1 驱动桥桥 壳受力示意 图
t 驱动 桥壳 是 汽 车的 主要 传 力件 和承 载件 ,而汽 车 车 亍 驶工 况 复杂 ,行 驶条 件 又是 千变 万化 ,因此要 精确
《 重型汽车》H A Y T U K 2 1 . E V R C 004
中 ,前处 理关 键环 节
图 2 后驱动桥几佰
是 网格划 分 ,一般 是将 导 入到An y 软 件 中的 ss 用 有限 元工 具 进行 网格划 分 ,模 型 采 用三 维 8
Qic ei h n is
施 一 围 — | 霸 } _ :
元 ,分 别用 8 4 0 6 7 个 实体单 元和 3 4 个 0 l 5 节 点 代 替 原 实 体 模
型 ,如 图3 示 。 所 本 文 采 用 先 利
车 向右 侧滑 ,作为 载荷 施加 在 有限 元 模型 的相 应 位置 ,然
后在 轮 距 的位置 增 加约 束 ,进 行求 解 计算 。两 种桥 壳 模型 的最 大变形 量分 别为 1 1 4 .6 mm和 1 1 7 . 5 mm,右侧 车轮板 簧 座 至过 渡 圆角处 的 桥壳 上 、下 表面 的 应力 值较 大 ,最 大等 图3 有 限元划 分 网格模 型 效应 力分 别为 l 8 a 1 5 a 3 MP 和 3 MP ,安 全 系数分 别为4. 3 1 和
重型商用车驱动桥壳典型工况计算方法分析
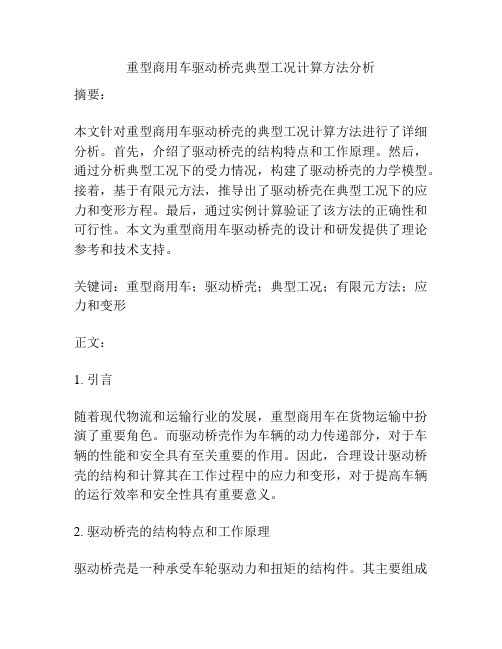
重型商用车驱动桥壳典型工况计算方法分析摘要:本文针对重型商用车驱动桥壳的典型工况计算方法进行了详细分析。
首先,介绍了驱动桥壳的结构特点和工作原理。
然后,通过分析典型工况下的受力情况,构建了驱动桥壳的力学模型。
接着,基于有限元方法,推导出了驱动桥壳在典型工况下的应力和变形方程。
最后,通过实例计算验证了该方法的正确性和可行性。
本文为重型商用车驱动桥壳的设计和研发提供了理论参考和技术支持。
关键词:重型商用车;驱动桥壳;典型工况;有限元方法;应力和变形正文:1. 引言随着现代物流和运输行业的发展,重型商用车在货物运输中扮演了重要角色。
而驱动桥壳作为车辆的动力传递部分,对于车辆的性能和安全具有至关重要的作用。
因此,合理设计驱动桥壳的结构和计算其在工作过程中的应力和变形,对于提高车辆的运行效率和安全性具有重要意义。
2. 驱动桥壳的结构特点和工作原理驱动桥壳是一种承受车轮驱动力和扭矩的结构件。
其主要组成部分包括两侧的桥壳外壳、差速器、行星齿轮和轴承等。
驱动桥壳的工作原理是,发动机输出的动力通过变速器、万向节、传动轴和驱动桥传递到车轮,驱动车轮运动。
在这个过程中,驱动桥壳需要承受来自发动机输出的扭矩和转速,以及车轮带来的驱动力和牵引力等多种力的作用,因此需要具备良好的强度和刚度。
3. 典型工况下的受力情况及力学模型驱动桥壳的受力情况取决于其工作状态和外界环境因素。
在实际使用中,驱动桥壳通常会面临竞速、爬坡、负载等多种典型工况。
以竞速工况为例,驱动桥壳需要承受高速旋转和冲击载荷等多种力的作用。
为了建立驱动桥壳的力学模型,对其受力情况进行分析是必要的。
在竞速工况下,驱动桥壳承受的主要力包括转矩力、轴向力、弯曲力等。
基于以上受力特点,可以构建驱动桥壳的力学模型,该模型包括驱动轮轴、差速器、行星齿轮、轴承、固定支撑和轮胎等组成部分。
在该模型中,驱动轮轴的旋转速度和扭矩作用于差速器的输入端,然后通过差速器、行星齿轮等装置传递到驱动桥壳的两侧。
驱动桥桥壳的疲劳寿命分析
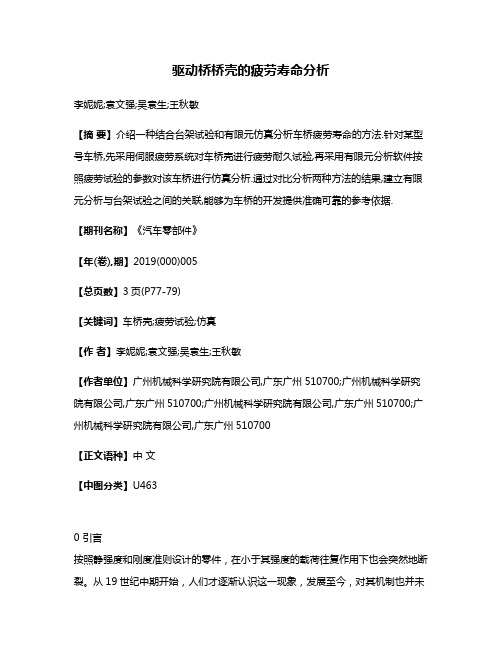
驱动桥桥壳的疲劳寿命分析李妮妮;袁文强;吴袁生;王秋敏【摘要】介绍一种结合台架试验和有限元仿真分析车桥疲劳寿命的方法.针对某型号车桥,先采用伺服疲劳系统对车桥壳进行疲劳耐久试验,再采用有限元分析软件按照疲劳试验的参数对该车桥进行仿真分析.通过对比分析两种方法的结果,建立有限元分析与台架试验之间的关联,能够为车桥的开发提供准确可靠的参考依据.【期刊名称】《汽车零部件》【年(卷),期】2019(000)005【总页数】3页(P77-79)【关键词】车桥壳;疲劳试验;仿真【作者】李妮妮;袁文强;吴袁生;王秋敏【作者单位】广州机械科学研究院有限公司,广东广州510700;广州机械科学研究院有限公司,广东广州510700;广州机械科学研究院有限公司,广东广州510700;广州机械科学研究院有限公司,广东广州510700【正文语种】中文【中图分类】U4630 引言按照静强度和刚度准则设计的零件,在小于其强度的载荷往复作用下也会突然地断裂。
从19世纪中期开始,人们才逐渐认识这一现象,发展至今,对其机制也并未完全掌握。
大多数机械结构和零部件都在循环载荷下工作,往复循环的载荷会使满足刚度强度的零件逐渐产生裂纹直至突然断裂,即为机械疲劳现象。
机械疲劳是机械结构和零部件的主要破坏形式,据统计有50%~90%的机械失效都源于疲劳破坏[1]。
疲劳寿命分析就是通过分析机械构件在其工作周期内的载荷、应力、结构、材料特性和扩展机制等来确定设计中存在的问题并估算产品工作寿命的过程。
对零件的疲劳寿命研究主要有两种方法:一种方法是疲劳耐久台架试验,模拟使用工况对零件样品施加载荷,统计零件的疲劳寿命、破坏形式和破坏位置等信息;另一种是计算分析的方法,采用有限元软件,结合零件的载荷、材料特性、结构和表面质量等因素,分析零件的疲劳寿命和失效位置。
疲劳试验结果准确但是耗时长、成本高。
相比而言仿真分析则简单许多,但是由于零件疲劳涉及的影响因素众多,仿真分析往往很难合理设置各个影响因素的大小,一旦将各个影响因素设置正确后,仿真分析可以很方便地得出分析结果,进而对零件做出优化,进行部分结构改进后依然能采用仿真结果。
- 1、下载文档前请自行甄别文档内容的完整性,平台不提供额外的编辑、内容补充、找答案等附加服务。
- 2、"仅部分预览"的文档,不可在线预览部分如存在完整性等问题,可反馈申请退款(可完整预览的文档不适用该条件!)。
- 3、如文档侵犯您的权益,请联系客服反馈,我们会尽快为您处理(人工客服工作时间:9:00-18:30)。
某重型车驱动桥后桥壳疲劳强度分析
针对重型驱动桥桥壳在截面形状过渡处容易产生裂纹甚至断裂的问题,首先用proe对某重型车驱动桥桥壳结构进行几何建模,并基于ANSYS workbench对其进行几何模型简化,完成有限元模型的建立。
根据重型车的实际工作状况对有限元模型施加脉冲动态载荷仿真得出其疲劳特性云图,观察分析桥壳不同位置疲劳寿命情况,为桥壳的结构设计提供参考。
标签:驱动桥桥壳;疲劳强度;ANSYS workbench
1 概述
驱动桥位于汽车传动系统末端,是汽车总成中的主要承载件和传力件。
在一般的汽车结构中,用于支承并保护主减速器、差速器和半轴等并将发动机发出的扭矩和转速传递到左、右驱动轮。
其使用频繁,故障率较高,生产质量和性能直接影响到车辆的整体性能和有效使用寿命。
因此,桥壳必须具有足够的强度、刚度、良好的动态特性和疲劳寿命。
2 有限元模型的建立
根据桥壳的CAD 图纸,用Pro/E 建立了三維几何模型如图1所示,为了使有限元模型既能反应实物的重要性能特征,又要实现划分网格简便并减少单元数量,从而保证较高的计算精度并相应的减少计算量,对桥壳的某些特征进行了简化,得到有限元模型如图2所示。
3 桥壳疲劳强度分析
驱动桥桥壳的疲劳损伤属于低应力高周疲劳,利用ANSYS后处理中的Fatigue模块可以有效精确的对驱动桥壳的疲劳损伤进行分析与仿真。
在驱动桥的静力分析的理论基础上采用弹塑性假设和Miner疲劳累积损伤法则得出桥壳模型的疲劳寿命循环次数和最小安全系数,达到预测驱动桥的疲劳寿命的目的。
文章桥壳本体所用的材料为ZG25Mn,正火处理。
其疲劳性能参数如表1所示。
由结构静力分析可知,汽车在不平路面冲击载荷作用下后桥壳的等效应力最大,因此在不平路面冲击载荷作用工况下对桥壳进行疲劳分析。
在workbench中输入疲劳强度降低因子,采用古德曼法修正平均应力对构件疲劳强度的影响。
根据重型车的实际工作状况,对桥壳施加脉冲载荷,即施加的最大载荷是使桥壳产生最大应力时所受的载荷,最小的载荷为零。
经过计算可得后桥壳疲劳寿命图如图3所示,桥壳安全系数图如4所示。
由疲劳寿命云图3 所示,桥壳的最低的寿命是1×107次,远远超出《汽车
驱动桥台架试验评价指标》中设计寿命80万次的规定。
由桥壳的安全系数图4所示,桥壳最低安全系数为1.8409,处于半轴套管与后桥壳的联接处,这是由于截面过渡处存在集中应力的影响,但是桥壳最低安全系数仍大于1,证明桥壳仍是安全的,符合桥壳台架试验的规定。
4 结束语
采用弹塑性假设和Miner疲劳累积损伤法则,结合修正的驱动桥壳的材料S-N曲线,基于ANSYS workbench 对驱动后桥进行了疲劳强度分析。
将得出的仿真结果与国内汽车后桥的相关标准进行对比发现驱动桥设计合理、符合标准。
驱动后桥寿命(循环次数)超过100万次,危险截面出现在在半轴套筒和桥壳连接处,最小安全系数为1.8409。
因此,在对驱动桥桥壳设计时要提高桥壳截面过渡处的强度以保证整体的疲劳强度。