超声检测锻件实操步骤
锻件超声波检测作业指导书

锻件超声波检测作业指导书7.1适用范围:本条适用于碳素钢和低合金钢锻件的超声波检测和缺陷等级评定,不适用于奥氏体粗晶材料的超声检测,也不适用于内外径之比小于80%的环形和筒形锻件的周向横波检测。
7.2检测工艺卡7.2.1检测工艺卡由具有II级UT资质人员编制,工艺卡的编制应与所执行的技术规范及本检测作业指导书相符。
7.2.2检测工艺卡由具有UTIII资质人员或UT检测责任师审核批准。
7.3检测器材:7.3.1仪器选用数字式超声波检测仪或A型脉冲反射式超声波检测仪,其工作频率范围为0.5-10MHz,水平线性误差不大于1%,垂直线性误差不大于5%。
7.3.2探头选用双晶直探头频率为 5 MHz,晶片面积不小于150mm2;单晶直探头,频率为2-5 MHz,圆晶片直径为14-25mm。
7.3.3试块采用纵波单晶直探头时采用JB/T4730-2005规定的CSI 试块;采用纵波双晶探头时采用JB/T4730-2005图8-5规定的CSII标准试块;检测面是曲面时采用CSIII试块。
7.3.4耦合剂:化合浆糊或机油。
7.4检测时机:原则上安排热处理后,槽、孔、台阶加工前进行。
若热处理后锻件形状不适合超声波检测时,也可在热处理前进行,但在热处理后仍应对锻件进行尽可能完全的检测。
7.5检测方法7.5.1执行检测工艺卡的规定7.5.2锻件一般应进行纵波检测,对筒形锻件还应进行横波检测,但扫查部位和验收标准应根据JB/T4730-2005.3附录C的规定。
7.5.3在纵波检测时,原则上应从两面相互垂直的方向进行检测,尽可能的检测带锻件的全体积,但锻件厚度超过400mm 时,应从两端面进行100%的扫查。
7.6检测灵敏度确定7.6.1纵波直探头检测灵敏度的确定当被检部位的厚度大于或等于3倍进场区时,原则上选用底波计算方法确定基准灵敏度,也可以采用试块法确定基准灵敏度。
7.6.2纵波双晶直探头灵敏度确定根据需要选择不同直径的平底孔试块,并依次测试一组不同检测深度的平底孔(至少三个),调节衰减器,使其中最高回波达到满刻度的80%。
01锻件超声波检测操作指导书

检测面
端面检测Leabharlann 例100%验收级别
Ⅱ级
检测灵敏度
试块:500/Φ2平底孔
工件:大平底计算
表面补偿
试块调节:4dB或实测。
用大平底调节:0dB。
本作业指导书未规定事项按NB/T47013.3-2015有关规定执行
扫描线调节
在CS2-31试块上测定探头的声速和零偏;端面深度1:5。
锻件超声检测操作指导书
编号:CZ1000-2018-0001
工
件
参
数
工件名称
锻件
工件编号
/
规格mm
Φ200×500
材料牌号
16MnR
检测时机
机械加工后
表面状态
Ra≤6.3μm
仪器
器材
仪器型号
数字式超声波检测仪XXXX
耦合剂
机油
探头型号
2.5P14Z
对比试块
CS-2-31、500mm大平底
技
术
要
求
检测标准
灵敏度校准及说明
1.用CS-2-31试块调节:把Φ2孔的波峰调节到基准波高(如80%),依次测试一组不同深度的Φ2平底孔(至少3个)按仪器说明书做距离-波幅曲线,把500mm深度的距离-波幅曲线调节到满屏的20%以上作为基准灵敏度,在基准灵敏度提高6dB作为扫查灵敏度。
2.用500mm大平底调节:将500无缺陷处大平底回波调至基准波高80%,再增益45dB为基准灵敏度,在基准灵敏度提高6dB作为扫查灵敏度。
5.密集区缺陷面积占检测总面积>5%。
扫查示意图
编 制
×××UTⅡ
审 核
×××UTⅢ
锻件超声波实操步骤 (大平底)47013-友联
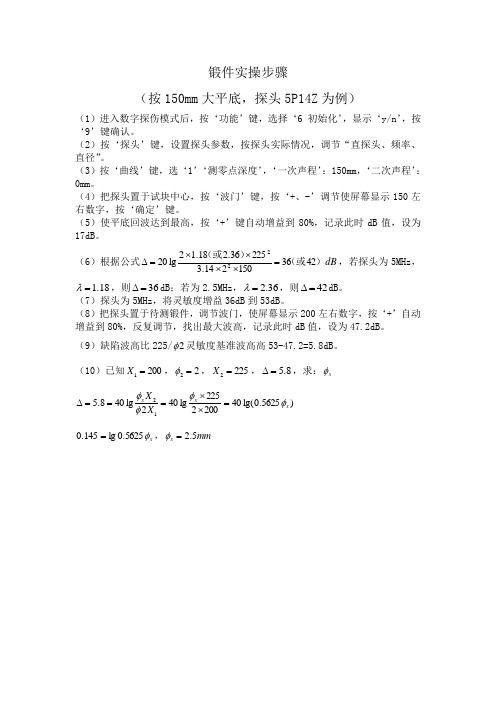
锻件实操步骤
(按150mm 大平底,探头5P14Z 为例)
(1)进入数字探伤模式后,按‘功能’键,选择‘6 初始化’,显示‘y/n ’,按‘9’键确认。
(2)按‘探头’键,设置探头参数,按探头实际情况,调节“直探头、频率、直径”。
(3)按‘曲线’键,选‘1’‘测零点深度’,‘一次声程’:150mm ,‘二次声程’:0mm 。
(4)把探头置于试块中心,按‘波门’键,按‘+、-’调节使屏幕显示150左右数字,按‘确定’键。
(5)使平底回波达到最高,按‘+’键自动增益到80%,记录此时dB 值,设为17dB 。
(6)根据公式dB )(或)(或4236150
214.322536.218.12lg 2022
=⨯⨯⨯⨯=∆,若探头为5MHz ,18.1=λ,则36=∆dB ;若为2.5MHz ,36.2=λ,则42=∆dB 。
(7)探头为5MHz ,将灵敏度增益36dB 到53dB 。
(8)把探头置于待测锻件,调节波门,使屏幕显示200左右数字,按‘+’自动增益到80%,反复调节,找出最大波高,记录此时dB 值,设为47.2dB 。
(9)缺陷波高比225/2φ灵敏度基准波高高53-47.2=5.8dB 。
(10)已知2001=X ,22=φ,2252=X ,8.5=∆,求:x φ
)5625.0lg(40200
2225lg 402lg 408.512x x x X X φφφφ=⨯⨯===∆ x φ5625.0lg 145.0=,mm x 5.2=φ。
锻件纵波探伤步骤
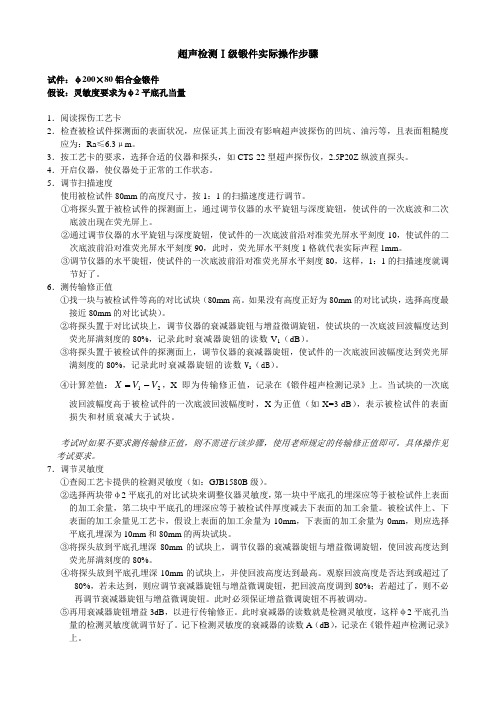
超声检测Ⅰ级锻件实际操作步骤试件:φ200×80铝合金锻件假设:灵敏度要求为φ2平底孔当量1.阅读探伤工艺卡2.检查被检试件探测面的表面状况,应保证其上面没有影响超声波探伤的凹坑、油污等,且表面粗糙度应为:Ra ≤6.3μm 。
3.按工艺卡的要求,选择合适的仪器和探头,如CTS-22型超声探伤仪,2.5P20Z 纵波直探头。
4.开启仪器,使仪器处于正常的工作状态。
5.调节扫描速度使用被检试件80mm 的高度尺寸,按1:1的扫描速度进行调节。
①将探头置于被检试件的探测面上,通过调节仪器的水平旋钮与深度旋钮,使试件的一次底波和二次底波出现在荧光屏上。
②通过调节仪器的水平旋钮与深度旋钮,使试件的一次底波前沿对准荧光屏水平刻度10,使试件的二次底波前沿对准荧光屏水平刻度90,此时,荧光屏水平刻度1格就代表实际声程1mm 。
③调节仪器的水平旋钮,使试件的一次底波前沿对准荧光屏水平刻度80,这样,1:1的扫描速度就调节好了。
6.测传输修正值①找一块与被检试件等高的对比试块(80mm 高。
如果没有高度正好为80mm 的对比试块,选择高度最接近80mm 的对比试块)。
②将探头置于对比试块上,调节仪器的衰减器旋钮与增益微调旋钮,使试块的一次底波回波幅度达到荧光屏满刻度的80%,记录此时衰减器旋钮的读数V 1(dB )。
③将探头置于被检试件的探测面上,调节仪器的衰减器旋钮,使试件的一次底波回波幅度达到荧光屏满刻度的80%,记录此时衰减器旋钮的读数V 2(dB )。
④计算差值:21V V X -=,X 即为传输修正值,记录在《锻件超声检测记录》上。
当试块的一次底波回波幅度高于被检试件的一次底波回波幅度时,X 为正值(如X=3 dB ),表示被检试件的表面损失和材质衰减大于试块。
考试时如果不要求测传输修正值,则不需进行该步骤,使用老师规定的传输修正值即可。
具体操作见考试要求。
7.调节灵敏度①查阅工艺卡提供的检测灵敏度(如:GJB1580B 级)。
超声检测实操步骤

考试程序步骤一、锻件(直探头2.5Pφ14K2)步骤:1、开机——按两次确定键——按功能键——按零(初始化)——按1(当前通道)——长按通道/设置键——改探头参数等—调校。
2、直探头纵波入射点调校:由上一步进入零点/调校键——选择1(入射点调校)(显示调节为,波速5920M/S;一次回波声程100mm;二次回波声程0mm.)——放在CSK-ⅠA试块上,对准中间完好位置找到底面回波,待波稳定后,按确定键,完成入射点调校。
3、调整灵敏度:将直探头放在150/φ3(根据现场情况)试块上,找到其反射波,并用“波门”键调整“+”或“—”使其波门对准150/φ3处的反射波,找到最高波,调节到80%。
记下此时增益Δ1dB,然后计算出150/φ3与225/φ2的回波分贝差Δ2dB,在Δ1dB基础上,调节增益旋钮增至(Δ1+Δ2)dB。
4、锻件检测:将直探头放在225mm,锻件上,全面扫查,找到200mm处缺陷波,用“波门”键调整“+”或“—”使其波门对准200mm处的反射波,使其最高波达到80%,记下此时Δ3dB.5、计算当量:则200mm处缺陷波比225/φ2波高高Δ=(Δ1+Δ2-Δ3)dB。
由公式计算出缺陷当量。
6、根据标准进行评级,整理报告。
最简单做法:锻件:步骤:1、开机——按两次确定键——按功能键——按零(初始化)——按1(当前通道)——长按通道/设置键——改探头参数等—调校。
2、直探头纵波入射点调戏:由上一步进入零点/调校键——选择1(入射点调校)(显示调节为,波速5920M/S;一次回波声程100mm;二次回波声程0mm.)——放在CSK-ⅠA试块上,对准中间完好位置找到底面回波,待波稳定后,按确定键,完成入射点调校。
3、调整灵敏度:将直探头放在150/φ3(根据现场情况)试块上,找到其反射波,并用“波门”键调整“+”或“—”使其波门对准150/φ3处的反射波,找到最高波,调节到80%。
记下此时面板的读数Δ1dB。
锻件超声波探伤记录和报告(试块)47013-友联
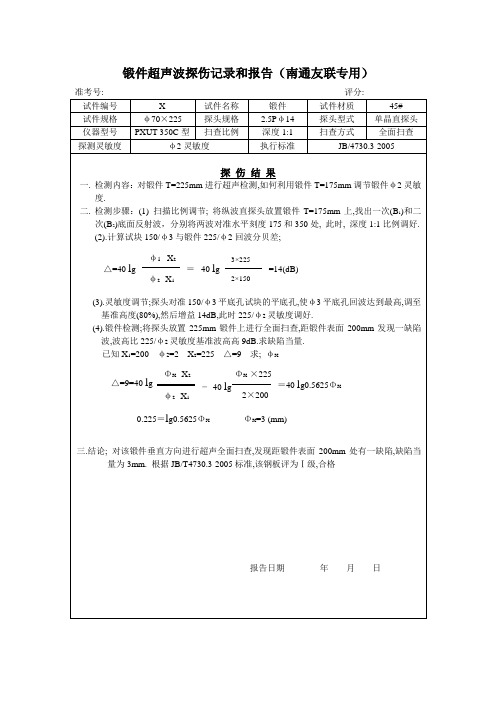
△=9=40 lg
Φ X X2 φ 2 X1
Φ X ×225
= 40 lg
=40 lg0.5625Φ X
2×200
0=3 (mm)
三.结论; 对该锻件垂直方向进行超声全面扫查,发现距锻件表面 200mm 处有一缺陷,缺陷当 量为 3mm. 根据 JB/T4730.3-2005 标准,该钢板评为Ⅰ级,合格
报告日期
年月日
探伤结果
一. 检测内容:对锻件 T=225mm 进行超声检测,如何利用锻件 T=175mm 调节锻件φ 2 灵敏 度.
二. 检测步骤:(1) 扫描比例调节; 将纵波直探头放置锻件 T=175mm 上,找出一次(B1)和二 次(B2)底面反射波,分别将两波对准水平刻度 175 和 350 处, 此时, 深度 1:1 比例调好. (2).计算试块 150/φ 3 与锻件 225/φ 2 回波分贝差;
△=40 lg
φ 1 X2 φ 2 X1
= 40 lg
3×225 2×150
=14(dB)
(3).灵敏度调节;探头对准 150/φ 3 平底孔试块的平底孔,使φ 3 平底孔回波达到最高,调至 基准高度(80%),然后增益 14dB,此时 225/φ 2 灵敏度调好.
(4).锻件检测;将探头放置 225mm 锻件上进行全面扫查,距锻件表面 200mm 发现一缺陷 波,波高比 225/φ 2 灵敏度基准波高高 9dB.求缺陷当量. 已知 X1=200 φ 2=2 X2=225 △=9 求; φ X
锻件超声波探伤记录和报告(南通友联专用)
准考号: 试件编号 试件规格 仪器型号 探测灵敏度
X
试件名称
φ 70×225 探头规格
PXUT-350C 型 扫查比例
铸、锻件的超声波探伤检测方法

• 锻造裂纹可出现在工件中不同位置,可由缩孔残 余在锻造时扩大产生,表面下气泡锻造产生,柱 状晶粗大引起,轴芯晶间裂纹锻造时引起,非金 属夹杂物引起,锻造加热不当引起,锻造变形不
当引起,经锻温度过低等原因引起。
• 白点是因钢中含氢量较高时由锻造过程中 残余应力热加工后的相变应力和热应力等 原因产生,是一种细微的氢裂纹,在白点 纵向断口上呈银白色的园点或椭圆形斑点, 故称白点。
• 游动波产生原因:(当出现游动回波,可 考虑中心附近危险性缺陷)
• 随探头移动,不同波束射至缺陷,中心波 束射至缺陷,回波高,声程小,边缘波束 射至缺陷,回波低,声程大,在扫描线上 游动范围达25mm,利用游动波的包络线, 可判断缺陷形状。
• 纵波:
• 单探头探测时,探头置于筒形锻件外园面、 内园面和端部探测。
• 三、探测条件选择 • 1.探头选择: • 频率:双晶直探头为5MHZ,单晶直探头为
2MHZ~5MHZ,对晶粒粗大锻件可适当降 低频率,可用1~2.5MHZ。 • 晶片尺寸:Ф14~25mm,常用Ф20mm。
•
• 双晶直探头——检测近表面缺陷。探头晶 片面积不小于150mm2。
• ③当量曲线法:
• a.面板曲线法
• 将不同直径,不同声程Φ平底孔波高绘制曲 线放在面板上,当缺陷波高与某平底孔回 波高一致时,即为该缺陷当量。
• b.相对曲线 dB——当量缺陷
• 利用衰减器,将某孔(平底孔)作出距 离——波幅曲线,探伤时将所有缺陷波均 调到基准波。然后根据衰减器得出读数, 再在dB——当量曲线上查出缺陷当量。
• ④AVG曲线定量法(第二章中已介绍)
• 2.缺陷长度测量法 • ①6dB(半波高)测长法,对平板工件、探
超声波无损检测作业指导书

超声波无损检测作业规范1.0目的本程序规定了依据API14A,对锻件与锻造产品进行超声波探伤测试的方法,人员要求以及接受的标准。
2.0•范围此规范适用于为本公司所有提供超声波探伤的供应商,也适用于诺斯石油工具按照相关规范的要求进行产品超声波探伤测试的情况。
3.0职责质量控制部负责按本规范要求的执行,确保所有产品符合本规范要求。
4.0术语定义无5.0程序5.1 安全与环境5.1.1 在使用者和承包人特殊安全,健康和环境方针的指导下安全地操作是使用者/承包人的责任。
5.1.2 安全操作由供货商的材料安全数据单(MSDS)来控制,在使用者和承包人特殊安全,健康和环境方针的指导下,使用者/承包人应依照本程序负责对浪费或危害环境的做法进行控制。
5.2 人员资格5.2.1 依据以下规范,进行检测、说明及对结果作出评价、记录的人员应具备至少2级资格证明;5.2.2 依据以下规范,所有进行本检测的人员都要求进行每年的视力测试及三年一次的辨色测试;5.2.3 所有无损检测人员应符合ISO9712要求。
5.3 检测方法锻件与精炼轧材的超声波探伤应采用脉冲回波联结或液浸方式进行。
5.4 扫描策划当相应过程文件作出要求时,即采购订单、质量计划、ECN等,应提交超声波探伤测试,并经WGPC质量代表认可后进行。
5.5 设备要求5.5.1 超声波设备5.5.1.1 超声波探伤设备:一个脉冲的反射型超声波探伤器械,频率范围至少为0.5~10兆赫,使用ASTME317最新版本对超声波脉冲检测系统的性能进行评估,其频率不应超过12个月。
5.5.1.2 脉冲/接收器:一个误差±10%或振幅比精确度在1dB的衰减器,设备控制对校准、核对或检测期间的线性影响应当没有或最小。
5.5.1.3 电池组:应当使用超声探伤或同类设备推荐的标准电池,电量低于50%时的电池组不能用于检测,且结果不被接受。
5.5.2 探测装置5.5.2.1 应使用标准直径为0.25~1英寸,且频率为1/2~5兆赫的传感器,选择相应的传感器尺寸与频率进行测量以得到最精确的显示结果。
- 1、下载文档前请自行甄别文档内容的完整性,平台不提供额外的编辑、内容补充、找答案等附加服务。
- 2、"仅部分预览"的文档,不可在线预览部分如存在完整性等问题,可反馈申请退款(可完整预览的文档不适用该条件!)。
- 3、如文档侵犯您的权益,请联系客服反馈,我们会尽快为您处理(人工客服工作时间:9:00-18:30)。
考试程序步骤
一、锻件(直探头2.5Pφ14K2)
步骤:1、开机——按两次确定键——按功能键——按零(初始化)——按1(当前通道)——长按通道/设置键——改探头参数等—调校。
2、直探头纵波入射点调校:由上一步进入零点/调校键——选择1(入射点调校)(显
示调节为,波速5920M/S;一次回波声程100mm;二次回波声程0mm.)——放在CSK-ⅠA试块上,对准中间完好位置找到底面回波,待波稳定后,按确定键,完成入射点调校。
3、调整灵敏度:将直探头放在150/φ3(根据现场情况)试块上,找到其反射波,并
用“波门”键调整“+”或“—”使其波门对准150/φ3处的反射波,找到最高波,调节到80%。
记下此时增益Δ1dB,然后计算出150/φ3与225/φ2的回波分贝差Δ2dB,在Δ1dB基础上,调节增益旋钮增至(Δ1+Δ2)dB。
4、锻件检测:将直探头放在225mm,锻件上,全面扫查,找到200mm处缺陷波,用“波门”键调整“+”或“—”使其波门对准200mm处的反射波,使其最高波达到80%,记下此时Δ3dB.
5、计算当量:则200mm处缺陷波比225/φ2波高高Δ=(Δ1+Δ2-Δ3)dB。
由公式
计算出缺陷当量。
6、根据标准进行评级,整理报告。
最简单做法:
锻件:
步骤:1、开机——按两次确定键——按功能键——按零(初始化)——按1(当前通道)——长按通道/设置键——改探头参数等—调校。
2、直探头纵波入射点调校:由上一步进入零点/调校键——选择1(入射点调校)(显
示调节为,波速5920M/S;一次回波声程100mm;二次回波声程0mm.)——放在CSK-ⅠA试块上,对准中间完好位置找到底面回波,待波稳定后,按确定键,完成入射点调校。
3、调整灵敏度:将直探头放在150/φ3(根据现场情况)试块上,找到其反射波,并
用“波门”键调整“+”或“—”使其波门对准150/φ3处的反射波,找到最高波,调节到80%。
记下此时面板的读数Δ1dB。
4、锻件检测:将直探头放在225mm,锻件上,全面扫查,找到200mm处缺陷波,用“波门”键调整“+”或“—”使其波门对准200mm处的反射波,使其最高波达到80%,记下此时面板右上角的读数Δ2dB.
5、计算当量:则200/φx缺陷波比150/φ3波高高Δ=(Δ2-Δ1)dB。
由公式
计算出缺陷当量。
6、根据标准进行评级,整理报告。