泡沫塑料成型中的气泡成核机理讨论
泡沫塑料的发泡方法及原理

上一页 下一页 返回
项目三 泡沫塑料的成型工艺
(3)工艺控制:挤出温度应比挤出聚苯乙烯一般制品时低,不超过120℃。 吹胀比约为6,并配合较快的牵引速度,以便挤出物在张力作用下,大
分子沿牵伸方向定向,物料机械性能提高。 挤出物应在离开口模时立即发泡,并使泡孔能均匀地双向膨胀。 (二)PS一步法挤出发泡板材 将PS树脂和泡孔成核剂(滑石粉)、稳定剂等,在长径比较大的(L/D
模块八 泡沫塑料成型
1 项目一 概述 2 项目二 泡沫塑料的发泡方法及原理 3 项目三 泡沫塑料的成型工艺
返回
项目一 概述
泡沫塑料是整体内含有无数微孔的塑料,它是以塑料(树脂)构成连续相 并以气体作为分散相的两相体系。采用不同的树脂和发泡方法,可制得 性能各异的泡沫塑料。
泡沫塑料有多种分类方法。泡沫塑料按其密度可分为:低发泡、中发泡和 高发泡的泡沫塑料。泡沫塑料按其结构不同又可分为开孔型泡沫塑料和 闭孔型泡沫塑料。泡沫塑料内各个气孔是相互连通的称为开孔型泡沫塑 料,如果泡沫是互相分隔的,则称为闭孔型泡沫塑料。泡沫塑料按其硬 度不同又可分为软质泡沫塑料、半硬质泡沫塑料和硬质泡沫塑料。此外, 还有结构泡沫塑料和组合性泡沫塑料之称,前者具有不发泡或少发泡的 皮层和发泡的芯层,后者则是把微小的中空玻璃、陶瓷微球加入已含固 化剂的树脂中,然后固化成型制得。
上一页 下一页 返回
项目三 泡沫塑料的成型工艺
熟化时最好使空气很快地渗入预发泡珠粒中,而不使发泡剂太多渗出, 否则预发物在模塑时的膨胀就差。
4.模塑成型 (1)过程:常用的模塑方法是蒸汽箱模塑法。熟化珠粒入模,送入液压机
蒸气室,加热发泡剂气化膨胀、塑料软化、进一步膨胀。 (2)工艺控制。 ①温度:温度尽快达到110℃~135℃,蒸汽压偏高达0. 294~0.329 MPa。 ②时间:蒸汽的加热时间依制品的厚度而定,一般5~ 60S。 ③冷却:若制品密度大于0.025 g/cm3,可用洗淋的方法;若制品密度小于 0. 025到cm,因为容易碎裂和收缩,最好用空气冷却。
塑料发泡方法和发泡原理

塑料发泡方法和发泡原理本页仅作为文档封面,使用时可以删除This document is for reference only-rar21year.March塑料发泡方法及发泡原理简介泡沫塑料的品种很多,常用的发泡方法有物理发泡法、化学发泡法和机械发泡法等(一)物理发泡法是指利用物理原理发泡的方法,包括以下三种:①在加压下把惰性气体压入熔融聚合物或糊状复合物中,然后降低压力,升高温度,使溶解的气体释放膨胀而发泡。
目前聚氯乙烤和聚乙烯泡沫塑科等有用这种方法生产的。
优点是气体在发泡后不会留下残渣,不影响泡沫塑料的性能和使用。
缺点是需要高的压力和比较复杂的设备。
②利用低沸点液体蒸发气化而发泡。
把低沸点液体压入聚合物中或在一定的压力、温度下,使液体溶入聚合物颗粒中,然后将聚合物加热软化,液体也随之蒸发气化而发泡,此法又称为可发性珠粒法。
目前采用该法生产的有聚苯乙烯泡沫塑料和交联聚乙烯泡沫塑料。
作发泡剂用的低沸点液体有:脂肪族烃类(丁烷、戊烷等)。
含氯脂肪族烃类(如二氯甲烷)和含氟脂肪族烃类(如F—11,F—12,F—114等)。
此外,脂环烃类、芳香烃类、醇类、醚类、酮类和醛类等也可使用。
常用低沸点液体发泡剂的。
③在塑料中加入中空微球后经固化而制成泡沫塑料。
此种泡沫塑料称为组合泡沫塑料。
(二)化学发泡法发泡气体是由混合原料中的某些组分在成型过程中发生的化学作用而产生的。
包括以下两种。
(1)发泡气体是由加入的热分解型发泡剂受热分解而产生的,这种发泡剂称为化学发泡剂。
常见的有碳酸氯钠、碳酸铵、偶氮二甲酰胺(俗称AC发泡刑)、偶组二异丁腊和N,N—二甲基N,N-二亚硝基对苯二甲酰胺等。
化学发泡剂的分解温度和发气量,决定其在某一塑料中的应用。
理想的分解型发泡剂应具有以下性能:①发泡剂分解温度范围应比较狭窄稳定;②释放气体的速率必须能控制并且应合理地快速③放出的气体应无毒、无腐蚀性和具有难燃性④发泡剂分解时不应大量放热⑤发泡剂在树脂中具有良好的分散性⑥价廉,在运输和贮藏中稳定⑦发泡剂及其分解残余物应无色、对发泡聚合物的物理和化学性能无影响⑧发泡剂分解时的发气量应较大。
聚丙烯泡沫挤出成型中气泡成核行为的研究
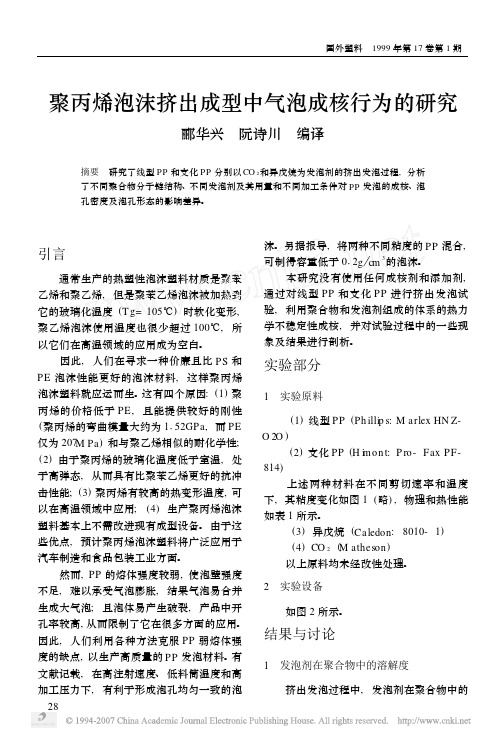
聚丙烯泡沫挤出成型中气泡成核行为的研究郦华兴 阮诗川 编译摘要 研究了线型PP和支化PP分别以CO2和异戊烷为发泡剂的挤出发泡过程,分析了不同聚合物分子链结构、不同发泡剂及其用量和不同加工条件对PP发泡的成核、泡孔密度及泡孔形态的影响差异。
引言 通常生产的热塑性泡沫塑料材质是聚苯乙烯和聚乙烯,但是聚苯乙烯泡沫被加热到它的玻璃化温度(T g=105℃)时软化变形,聚乙烯泡沫使用温度也很少超过100℃,所以它们在高温领域的应用成为空白。
因此,人们在寻求一种价廉且比PS和PE泡沫性能更好的泡沫材料,这样聚丙烯泡沫塑料就应运而生。
这有四个原因:(1)聚丙烯的价格低于PE,且能提供较好的刚性(聚丙烯的弯曲模量大约为1152GPa,而PE 仅为207M Pa)和与聚乙烯相似的耐化学性;(2)由于聚丙烯的玻璃化温度低于室温,处于高弹态,从而具有比聚苯乙烯更好的抗冲击性能;(3)聚丙烯有较高的热变形温度,可以在高温领域中应用;(4)生产聚丙烯泡沫塑料基本上不需改进现有成型设备。
由于这些优点,预计聚丙烯泡沫塑料将广泛应用于汽车制造和食品包装工业方面。
然而,PP的熔体强度较弱,使泡壁强度不足,难以承受气泡膨胀,结果气泡易合并生成大气泡;且泡体易产生破裂,产品中开孔率较高,从而限制了它在很多方面的应用。
因此,人们利用各种方法克服PP弱熔体强度的缺点,以生产高质量的PP发泡材料。
有文献记载,在高注射速度、低料筒温度和高加工压力下,有利于形成泡孔均匀一致的泡沫。
另据报导,将两种不同粘度的PP混合,可制得容重低于012g c m3的泡沫。
本研究没有使用任何成核剂和添加剂,通过对线型PP和支化PP进行挤出发泡试验,利用聚合物和发泡剂组成的体系的热力学不稳定性成核,并对试验过程中的一些现象及结果进行剖析。
实验部分1 实验原料 (1)线型PP(Ph illi p s:M arlex HN Z-O2O) (2)支化PP(H i m on t:P ro-Fax PF-814) 上述两种材料在不同剪切速率和温度下,其粘度变化如图1(略),物理和热性能如表1所示。
泡沫塑料气泡膨胀的动量质量和热量传递理论

r ve d M o e t m r n f r  ̄ a s t a se n e t ta s e u i g b b e e p n ig a e a ay e n x l e . e iwe . m n u ta s e , l s r n fr a d h a r n f r d rn ub l x a d n r n l z d a e p  ̄n d d F t r ie t n n t d r rt s a e p e it d u u edr ci sa dsu yp i ie r rdce . o o i
Ke y wor ds
fa pa t , u bee p n ig,e e r hd v lp n o m lsi b b l x a dn rs a c e eo me t c
0 引 言
泡沫塑 料是 一种 以气 体为填 料的复合材料 , 同不发 泡塑 料相 比t 有一个 由气 体组成 的分 散相 , 它 气固两相间的织态结 构 、 面特性及气 固两相 的物理力学性能 和热性 能等影 响泡 界 沫塑料的结构 。 因此它的某些物理 机械 性能、 隔热性能和电性 能等均 忧于一般塑料 , 比如 它质量轻 、 比强度高 , 具有优 异的 隔音 、 吸音、 隔热 、 电绝缘性 能和吸 收冲击载荷等特性 , 因而广
A b ta t sr c
I hsp p r te te r e eo me to u be e p n ig o o m lsi th me a d a r a s n t i a e ,h h o yd v lp n fb b l x a dn ffa pa tca o n b o d i
维普资讯
・1 第 5期 6卷
泡 沫塑 料气 泡 膨胀 的动 量质 量 和 热量传 递 理 论
气泡工艺技术原理
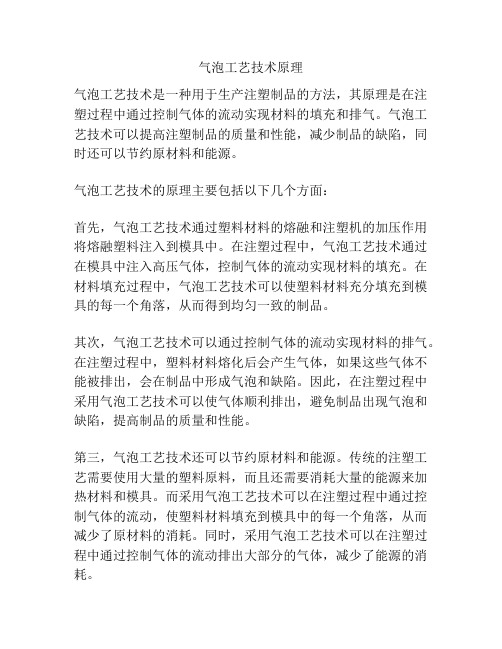
气泡工艺技术原理
气泡工艺技术是一种用于生产注塑制品的方法,其原理是在注塑过程中通过控制气体的流动实现材料的填充和排气。
气泡工艺技术可以提高注塑制品的质量和性能,减少制品的缺陷,同时还可以节约原材料和能源。
气泡工艺技术的原理主要包括以下几个方面:
首先,气泡工艺技术通过塑料材料的熔融和注塑机的加压作用将熔融塑料注入到模具中。
在注塑过程中,气泡工艺技术通过在模具中注入高压气体,控制气体的流动实现材料的填充。
在材料填充过程中,气泡工艺技术可以使塑料材料充分填充到模具的每一个角落,从而得到均匀一致的制品。
其次,气泡工艺技术可以通过控制气体的流动实现材料的排气。
在注塑过程中,塑料材料熔化后会产生气体,如果这些气体不能被排出,会在制品中形成气泡和缺陷。
因此,在注塑过程中采用气泡工艺技术可以使气体顺利排出,避免制品出现气泡和缺陷,提高制品的质量和性能。
第三,气泡工艺技术还可以节约原材料和能源。
传统的注塑工艺需要使用大量的塑料原料,而且还需要消耗大量的能源来加热材料和模具。
而采用气泡工艺技术可以在注塑过程中通过控制气体的流动,使塑料材料填充到模具中的每一个角落,从而减少了原材料的消耗。
同时,采用气泡工艺技术可以在注塑过程中通过控制气体的流动排出大部分的气体,减少了能源的消耗。
综上所述,气泡工艺技术是一种通过控制气体的流动实现材料的填充和排气的方法。
气泡工艺技术可以提高注塑制品的质量和性能,减少制品的缺陷,同时还可以节约原材料和能源。
在注塑行业中,气泡工艺技术已经得到了广泛的应用,并成为了注塑制品生产的重要工艺之一。
泡沫塑料成型工艺
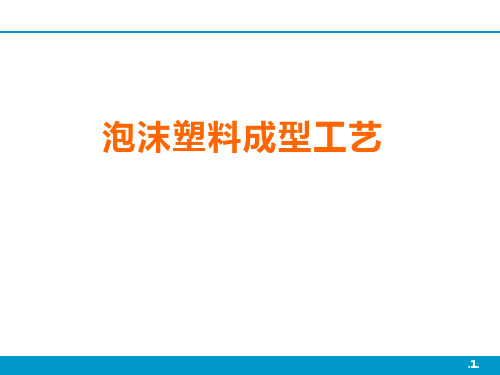
稳定气泡。 Ø 其三,通过对冷却或交联作用来提高聚合物的熔体黏度,
以达到稳定气泡的目的。
.7.
第一节 气泡形成原理和发泡方法
三、泡沫塑料的发泡方法
① 物理发泡法 ② 化学发泡法 ③ 机械发泡法
.8.
第一节 气泡形成原理和发泡方法
有机发泡剂一般都有其促进剂和抑制剂 5.发泡效率
单位重量的发泡剂产生气体的体积
.20.
第三节 化学发泡法
二、工艺举例(SPVC泡沫鞋底)
原材料的预处理→配制→捏合→塑炼→称量→剪片→模压 发泡→热处理→停放→冲切→打眼→装攀→检验→包装
.21.
第三节 化学发泡法
三、聚氨酯泡沫塑料及其成型
1.原料 (1)二异氰酸酯类 (2)多元醇 (3)催化剂:胺类或有机锡 (4)发泡剂:分为内、外发泡剂两种 (5)表面活性剂 (6)其它助剂:阻燃剂、防老剂等
均相成核:形成粗大而不均匀的泡孔。
.5.
第一节 气泡形成原理和发泡方法
二、泡沫塑料气泡形成原理
2.气泡核的增长 ① 气体的受热膨胀以及气泡的合并,促使气泡不继地增长; ② 成核作用导致气泡数量的增加; 影响因素:表面张力和粘度
.6.
第一节 气泡形成原理和发泡方法
二、泡沫塑料气泡形成原理
3.气泡核的稳定 Ø 其一,加入表面活性剂以利于形成微小的气泡从而减少气
.16.
第二节 物理发泡法
一、EPS泡沫塑料的物理发泡
3.熟化 ① 定义:将预发泡的膨胀体在空气中放置一段时间,让空
气渗入,以利于进一步加工 ② 原理:利用空气的渗入填补水蒸汽及发泡剂冷凝后形成
聚合物发泡过程中气泡成核的研究

聚合物发泡过程中气泡成核的研究聚合物发泡技术是一种重要的工业制造技术,广泛应用于轻量化材料、保温材料、隔音材料和缓冲材料等领域。
在聚合物发泡过程中,气体通过物理或化学反应进入聚合物体系中,形成孔洞,从而使材料体积减小,密度降低。
气泡成核是聚合物发泡过程中不可或缺的环节,其对聚合物发泡性能及材料质量具有重要影响。
一、气泡成核机制气泡成核机制有物理成核和化学成核两种。
物理成核是指在聚合物体系中存在一定的微小纳米矿物粒子、沉淀物或其他微粒表面,气体在其表面吸附并沉积形成气泡,这种成核方式对温度敏感,与扰动等因素有密切关系。
化学成核是指在聚合物体系中添加成核剂,利用成核剂作用使气体发生化学反应后形成气泡,可在较宽的温度范围内发生。
二、影响气泡成核的因素气泡成核的过程涉及多种因素,其中聚合物分子结构对气泡成核具有决定性作用。
聚合物分子中的两个相邻分子链,如两个互为邻原子,不同原子之间的键能较强,而链内的键能较小,在一定温度范围内,分子链能较好地扭转、挠曲和移动,形成有机晶体,成为气泡成核的基础。
此外,溶液浓度对气泡成核也有影响,溶液中溶质浓度越高,溶剂中溶质成核的机会相对更大。
三、成核剂成核剂是实现气泡成核的一种辅助物质,通常为化学物品或物理物体。
成核剂作用于聚合物体系时,一方面可以提高聚合物分子链的扭转移动性,提高其晶体化程度;另一方面也可以直接作用于气体分子,促进其吸附沉积,从而达到促进气泡成核的效果。
尼龙、PET等合成纤维材料就是利用纤维表面的成核效应将它们进行融合,进而制成纤维而成的。
此外,羧化剂、二元酸硬脂酸锌等化学成核剂也是常用的气泡成核辅助剂。
四、研究现状及未来展望目前,针对聚合物发泡过程中气泡成核的研究主要集中在以下几方面:(1)研究气泡起始密度以及孔径分布,对聚合物发泡过程中气泡成核的动力学和热力学进行深入探究。
(2)开发新型成核剂,探索适用于各种气泡成核场合的成核剂,提高聚合物发泡效率。
塑料发泡原理

塑料发泡原理
塑料发泡原理即指的是在塑料制品中加入发泡剂,通过发泡剂在高温下分解产生气体,使塑料材料膨胀成多孔结构的过程。
这种处理方法能够有效地减少塑料的密度,提高塑料制品的轻量化效果,同时也可以增加塑料制品的绝缘性能和吸音性能。
塑料发泡的原理主要有两种,一种是物理发泡,另一种是化学发泡。
物理发泡是指在高温下将发泡剂加入到塑料中,其中的发泡剂会在加热的过程中分解产生大量气体。
这些气体在塑料中形成微小的气泡,使塑料变得蓬松轻盈。
而气泡的形成主要是通过发泡剂在高温下变成气体,然后在塑料体内产生气体泡沫。
化学发泡则是在塑料中加入一种特殊的发泡剂,在高温下发生分解反应产生气体。
这种发泡剂又称为发泡剂,它能够在塑料中产生大量的气体泡沫。
发泡剂通过与塑料反应,产生气体使塑料膨胀,形成多孔的结构。
无论是物理发泡还是化学发泡,都需要在高温下进行。
高温可以促使发泡剂分解产生气体,并使气体在塑料中均匀分布。
当气体泡沫扩散到整个塑料体内时,停止加热,塑料冷却后,气泡会固定在塑料中形成多孔结构。
在发泡过程中,还可以适当调节发泡剂的用量和发泡时间,以控制塑料的密度和孔径的大小。
综上所述,塑料发泡原理的关键是通过加入发泡剂,在高温下
分解产生气体,使塑料形成多孔结构。
这种发泡处理方法可以降低塑料制品的密度,提高其轻量化效果,同时也能够改善其绝缘性能和吸音性能。
- 1、下载文档前请自行甄别文档内容的完整性,平台不提供额外的编辑、内容补充、找答案等附加服务。
- 2、"仅部分预览"的文档,不可在线预览部分如存在完整性等问题,可反馈申请退款(可完整预览的文档不适用该条件!)。
- 3、如文档侵犯您的权益,请联系客服反馈,我们会尽快为您处理(人工客服工作时间:9:00-18:30)。
泡沫塑料成型中的气泡成核机理讨论
塑料发泡过程中的初始阶段是在塑料熔体或者液体中形成大量初始气泡核的过程,然后使气泡核膨胀形成发泡体。
所谓气泡核是指原始微泡,也就是气体分子最初在聚合物熔体或者溶液中聚集的地方。
气泡核的形成对于成型出泡体的质量具有关键作用。
假如在熔体中能够同时出现大量均匀分布的气泡核,则常常能够得到泡孔均匀细密的优质泡体,假如气泡核不是同时出现的,而是逐步出现,延续的时间较长,则得到的泡孔较少,而且很大,泡孔尺寸分布不均匀、泡体的密度也很大的劣质泡沫。
因此,在泡沫塑料的成型过程中如何有效地控制气泡成核就很关键。
要控制气泡核的形成就必须了解气泡成核的机理,气泡核是如何形成的,什么是阻力、何为动力。
现有的气泡成核机理分为三个大类:
(1)利用聚合物的自由体积作为成核点形成气泡核
(2)利用聚合物熔体中的低势能点作为发泡成核点
(3)气液相混合直接形成气泡核。
以下分别进行阐述。
(1)利用聚合物的自由体积作为成核点形成气泡核
聚合的体积由两部分组成:一部分是其自身的体积;一部分是各个分子之间的体积,以“孔穴”的形式分布于整个高聚物中,称为自由体积。
Fox和Flory认为,任何高聚物,当温度降至玻璃化转变温度以下时,其自由体积分数都为一定值,0.025。
在一定的温度和压力下,发泡剂可以浸入这些自由体积中,然后通过升温或卸压,使发泡剂气化,从而形成气泡成核点。
利用自由体积作为成核点进行发泡必须注意以下几点:
(1)最为发泡基体的聚合物,其分子中必须含有足够的自由体积,以供聚集足够量的物理发泡剂渗入,形成气泡核;
(2)不同聚合物中的自由体积不同,并非任何一种发泡剂都可以渗透进入任意一种聚合物中形成气泡核,必须进行实验验证;
(3)聚集在自由体积中的发泡剂,其分子在不停的扩散运动,因此含有此类发泡剂的聚合物不应再大气中停留太长时间,以免发泡剂扩散到大气,影响成核质量,要注意密封
(4)发泡剂渗入自由体积的速度可以通过加压来进行,升温容易加速分子运动,发泡剂容易散失,影响成核效果。
(2)利用聚合物熔体中的低势能点作为发泡成核点
要在聚合物熔体中形成大量均匀分布的气泡核,必须在熔体中同时存在大量的过饱和气体和大量均匀分布的热点。
聚合物熔体中的热点之所以能够成为成核点,从宏观上看,热点处的熔体温度较高,使熔体黏度下降,表面张力下降,使熔体中的过饱和气体容易在此处聚集从而形成气泡核。
从微观上看,聚合物熔体中热点处的分子动能增加而势能下降,分子中势能的下降为熔体中过饱和气体的析出提供了有力条件。
因此聚合物熔体中的热点之所以成为成核电视因此此处的聚合物分子热势能降低,使熔体中的过饱和气体分子容易从此处析出聚集而成气泡核。
在实际生产中我们可以通过多种途径在熔体中形成低势能点,如加入成核剂,形成势能较低的界面,从而使熔体中的过饱和气体容易从此析出,形成气泡核。
(挤出发泡或者注射发泡常采用此机理)
(3)气液相混合直接形成气泡核
该机理多用于热固性泡沫塑料的成型。
此类气泡核的形成是通过发泡剂(惰性气体或者低沸点挥发性液体)与聚合物液体直接混合形成。
成核的气体来自发泡剂,不用先溶解入聚合物熔体、液体或者聚集在聚合物的自由体积内,而是直接用气体与聚合物溶液混合,形成大量气泡。
原材料(包括发泡剂)在混合头中进行强烈混合,使发泡剂气体或者液体与聚合物溶液充分混合,同时进行的缩聚反应使溶液的黏弹性增强,使它有足够的强度包住气体,形成大量气泡。
随反应的进行,树脂溶液逐渐失去流动性,使泡体固化定型。
这类城和方法的效果取决于气液相混合的力度和树脂溶液缩聚反应的速度相匹配。
具有一定黏弹性的液体才能包住气体,形成气泡。
因此在制定原材料配方和成型工艺时,必须注意控制缩聚反应的速度,使树脂溶液能够适时包住被分散的气体,形成大量气泡,同时还能使泡体及时固化定型。