苯加氢制环己烷
苯加氢原理

苯加氢原理苯加氢是一种重要的有机合成反应,通过苯和氢气在催化剂存在下进行加氢反应,生成环己烷。
这一反应在工业上具有重要意义,也是有机化学中的基础知识之一。
本文将介绍苯加氢的原理及其相关知识。
苯加氢反应的原理是利用催化剂的作用,将苯分子中的双键还原成单键,同时将氢气分子中的单键加成到苯环上,生成环己烷。
这一反应通常在高温高压下进行,催化剂通常采用铂、钯等贵金属或其化合物。
催化剂的作用是降低反应的活化能,加速反应速率,提高反应的选择性。
苯加氢反应是一个热力学上比较有利的反应,因为苯分子中的双键能量较高,而环己烷分子中的单键能量较低。
因此,苯加氢反应是一个放热反应,有利于生成环己烷。
在工业上,苯加氢反应通常作为环己烷的生产方法之一,因为环己烷是一种重要的有机溶剂,广泛用于化工生产中。
除了工业上的应用,苯加氢反应在有机合成中也具有重要意义。
通过苯加氢反应,可以将苯环上的双键还原成单键,为后续的有机合成提供重要的中间体。
例如,可以将苯基化合物通过苯加氢反应转化为环己烷基化合物,从而扩大有机合成的适用范围。
苯加氢反应的催化剂选择、反应条件优化等方面是有机化学研究的热点之一。
研究人员通过设计新型催化剂,优化反应条件,提高反应的产率和选择性,不断推动着苯加氢反应的发展。
同时,对苯加氢反应机理的研究也是有机化学领域的重要课题之一,深入了解反应的机理有助于更好地控制反应过程,提高反应的效率和经济性。
总之,苯加氢反应作为一种重要的有机合成反应,具有重要的工业应用价值和研究意义。
通过深入了解苯加氢反应的原理及其相关知识,可以更好地应用和推动这一反应的发展,为有机化学和化工领域的发展做出贡献。
苯加氢制环己烷工艺流程
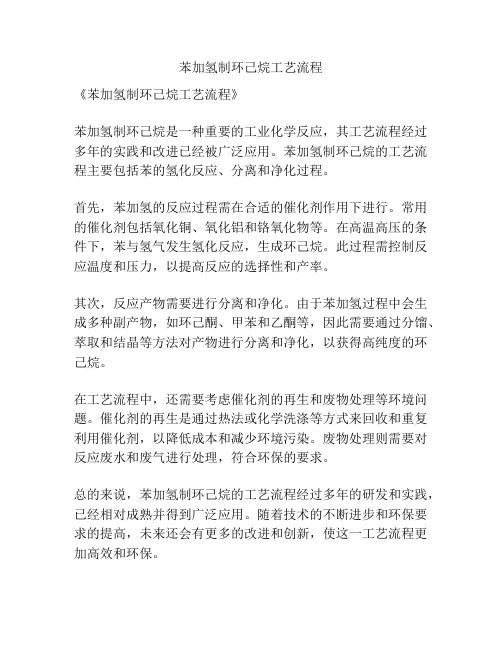
苯加氢制环己烷工艺流程
《苯加氢制环己烷工艺流程》
苯加氢制环己烷是一种重要的工业化学反应,其工艺流程经过多年的实践和改进已经被广泛应用。
苯加氢制环己烷的工艺流程主要包括苯的氢化反应、分离和净化过程。
首先,苯加氢的反应过程需在合适的催化剂作用下进行。
常用的催化剂包括氧化铜、氧化铝和铬氧化物等。
在高温高压的条件下,苯与氢气发生氢化反应,生成环己烷。
此过程需控制反应温度和压力,以提高反应的选择性和产率。
其次,反应产物需要进行分离和净化。
由于苯加氢过程中会生成多种副产物,如环己酮、甲苯和乙酮等,因此需要通过分馏、萃取和结晶等方法对产物进行分离和净化,以获得高纯度的环己烷。
在工艺流程中,还需要考虑催化剂的再生和废物处理等环境问题。
催化剂的再生是通过热法或化学洗涤等方式来回收和重复利用催化剂,以降低成本和减少环境污染。
废物处理则需要对反应废水和废气进行处理,符合环保的要求。
总的来说,苯加氢制环己烷的工艺流程经过多年的研发和实践,已经相对成熟并得到广泛应用。
随着技术的不断进步和环保要求的提高,未来还会有更多的改进和创新,使这一工艺流程更加高效和环保。
苯加氢制环己烷范文
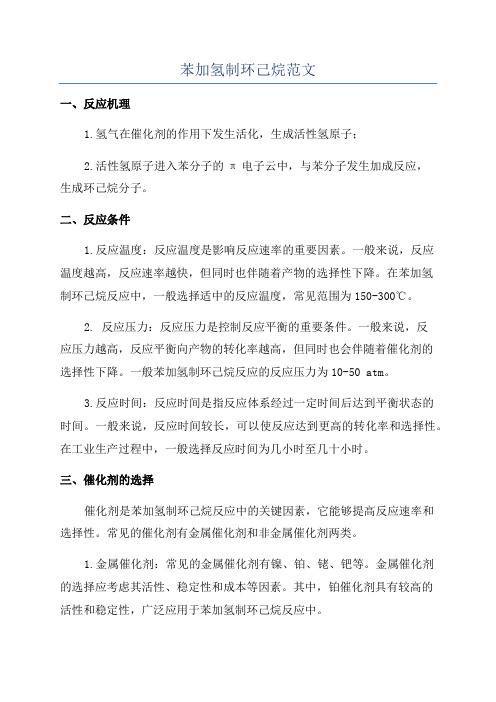
苯加氢制环己烷范文一、反应机理1.氢气在催化剂的作用下发生活化,生成活性氢原子;2.活性氢原子进入苯分子的π电子云中,与苯分子发生加成反应,生成环己烷分子。
二、反应条件1.反应温度:反应温度是影响反应速率的重要因素。
一般来说,反应温度越高,反应速率越快,但同时也伴随着产物的选择性下降。
在苯加氢制环己烷反应中,一般选择适中的反应温度,常见范围为150-300℃。
2. 反应压力:反应压力是控制反应平衡的重要条件。
一般来说,反应压力越高,反应平衡向产物的转化率越高,但同时也会伴随着催化剂的选择性下降。
一般苯加氢制环己烷反应的反应压力为10-50 atm。
3.反应时间:反应时间是指反应体系经过一定时间后达到平衡状态的时间。
一般来说,反应时间较长,可以使反应达到更高的转化率和选择性。
在工业生产过程中,一般选择反应时间为几小时至几十小时。
三、催化剂的选择催化剂是苯加氢制环己烷反应中的关键因素,它能够提高反应速率和选择性。
常见的催化剂有金属催化剂和非金属催化剂两类。
1.金属催化剂:常见的金属催化剂有镍、铂、铑、钯等。
金属催化剂的选择应考虑其活性、稳定性和成本等因素。
其中,铂催化剂具有较高的活性和稳定性,广泛应用于苯加氢制环己烷反应中。
2.非金属催化剂:常见的非金属催化剂有硅胶、氧化锌、活性炭等。
非金属催化剂的选择应考虑其吸附能力、分散性和再生性等因素。
其中,硅胶催化剂具有较高的吸附能力和选择性,被广泛应用于苯加氢制环己烷反应中。
四、工业应用1.环己烷制备:苯加氢制环己烷是制备环己烷的主要方法之一、环己烷是一种重要的溶剂,广泛应用于合成橡胶、石油、塑料等行业。
2.环己烯制备:环己烷可以通过去氢反应制备环己烯。
环己烯是一种重要的有机合成中间体,可用于制备药物、农药、染料和橡胶等化学品。
3.环己醇制备:环己烷可以通过氧化反应制备环己醇。
环己醇是一种重要的有机溶剂和中间体,广泛用于制备染料、塑料和橡胶等产品。
综上所述,苯加氢制环己烷是一种重要的化学反应,其反应机理、反应条件、催化剂的选择以及工业应用都具有重要意义。
苯加氢制环己烷

四、苯加氢制环己烷环己烷主要占总产量90%以上用来生产环己醇、环己酮及己二酸,后三者是制造尼龙-6和尼龙-66的重要原料;环己烷还用作树脂、油脂、橡胶和增塑剂等的溶剂;用作尼龙原料的高纯度的环己烷主要由苯加氢制得;工业上苯加氢生产环己烷有气相法和液相法两种;虽然美国杜邦公司早已开发成功气相加氢工艺,但大多数工厂仍采用液相加氢工艺,例如美国的Uop公司,法国石油研究所IFP等;气相法的优点是催化剂与产品分离容易,所需反应压力也较低,但设备多而大,投资费用比液相法高;1.反应原理1化学反应在反应条件下,苯与氢可能发生下面各种反应:+nH2→C+CH44反应1若为气相法固定床,用还原Ni作催化剂,反应温度为65~250℃,压力0.5~3.5MPa;若为液相加氢,采用骨架镍或还原Ni为催化剂,反应温度为160~220℃,压力2.7MPa左右,环己烷收率在99%以上;反应2和4在250℃左右的低温下不显着,它们可能是由第Ⅷ族金属催化的氢解型机理引起的,也可能是由双功能催化剂的加氢裂解型机理引起的;双功能催化剂为具有加氢催化活性的某些金属如Pt,Pd或Ni负载在酸性载体SiO2或SiO2/Al2O3上构成,在载体上往往存在强酸中心,它对反应2和4有明显促进作用;因此,选择非酸性载体可以避免这种加氢裂解作用;反应3是环己烷的异构化,它往往被酸催化,在200℃下,异构化反应达到平衡时环己烷生成甲基环戊烷的转化率为68%,将温度升高到300℃时其转化率达83%,因此也必须选择不会引起这种异构化反应的催化剂;在镍催化剂上,250℃时才开始产生甲基环戊烷;2热力学平衡由反应1可知,苯加氢生成环己烷的反应是一个放热的体积摩尔数缩小的可逆反应;在127℃时的平衡常数为7×107,在227℃时为1.86×102;氢压和温度对环己烷中苯的平衡浓度的影响示于图3-2-18;由图3-2-18可见,低温和高压对反应是有利的;相反,反应2和4则受到抑制;环己烷异构化反应是一个等摩尔反应,压力对反应影响不大;温度对反应3平衡的影响示于图3-2-19;由图3-2-19可知,甲基环己烷的平衡浓度随温度的提高而上升;为抑制这一副反应,也要求催化剂在较低温度下就有高的苯加氢活性,而且在催化剂上不存在酸性中心;3催化剂和催化机理对苯加氢有催化活性的金属有:Rh,Ru,Pt,W,Ni,Fe,Pd和Co等;常用金属按活性排列为:Pt>Ni>Pd加氢活性的比例为:K Pt:K ni:K Pd=18:7:1这表明铂的活性比镍高2.6倍;但铂的价格为镍的几百倍,因此选择镍作为催化剂活性组分更经济;如前所述,苯加氢有气相和液相两种方法,对液相加氢而言,要求催化剂是细微颗粒粉末,粒度为20~100μm,能悬浮在反应液中进行液-固相加氢反应;考虑到反应要求低温高活性,而且苯环加氢比烯,炔加氢困难,工业上都选用骨架镍催化剂;用这种催化剂在3.5MPa的压力和不产生副反应的温度200℃下,反应速率很容易达到每克镍每分钟转化0.15mol苯的水平;骨架镍催化剂的制备过程为:先由镍和铝重量比为1在1500~1600℃下制成镍铝合金,然后研磨至粒度为0.04~0.25mm,再用氢氧化钠浸出铝,最后经洗涤和干燥得到高活性,多孔和高强度的骨架催化剂;由于活性高,在空气中极易自燃,故一般将它浸在乙醇中出售或经表面钝化处理变成不自燃的干燥粉末后出售;成品为黑色粉末,镍含量为65%,松密度为2.4g/cm3;苯的气相加氢催化剂为负载型Ni催化剂,要求载体有足够的强度承受工业条件下的机械应力,有足够的比表面积和适宜的孔径分布,能负载足够数量的镍盐氧化镍;此外,还要求载体对副反应没有催化活性;符合上述条件,工业上应用的载体有高纯度氧化铝球Φ2~4mm,SiO2和硅藻土等,比表面积210m2/g,松密度0.91g/cm3,孔隙度0.4cm3/g;现在,工业上应用较多的液相催化剂牌号为法国的NiPS2,气相催化剂牌号为法国的LD143催化剂,它们都是由法国石油研究所IFP开发成功;除上述镍催化剂外,也有采用Ni-Pd催化剂,硫化镍和硫化钯催化剂;硫化物催化剂虽然不怕原料苯中硫化物的毒害,但要求高温450℃和高压31.0MPa;关于催化加氢反应机理,即使像乙烯加氢这样一个简单的反应,认识也不一致;分岐主要集中在①氢是否也发生化学吸附;②作用物在催化剂表面是发生单位独位吸附还是多位吸附;③氢与吸附在催化剂表面的作用物分子是怎样反应的;以苯加氢生成环己烷为例,就提出了两种不同的机理,一种认为苯分子在催化剂表面发生多位吸附,形成,然后发生加氢反应,生成环己烷;近年来又提出了另一种观点,认为苯分子只与催化剂表面一个活性中心发生化学吸附即独位吸附,形成π-键合吸附物,然后吸附的氢原子逐步加到吸附的苯分子上,即上述二种反应机理,还留待进一步实验验证;4反应动力学Louvain的动力学学派专门研究过在镍催化剂上苯加氢的反应动力学;研究表明,在骨架镍催化剂催化下,苯在高压、液相、温度低于200℃下加氢,苯转化率从低升至90%以上,反应对苯为零级,当转化率在95%以上时,对苯的反应级数变得接近于1;对氢而言,在所研究的压力范围内对氢为零级反应;实验结果示于图3-2-20;这一实验结果可用苯和氢之间的非竞争吸附来解积,并可用下列速率方程式表示:图3-2-20液相苯加氢反应动力学级数的实验测定式中:b B—苯的吸附系数;b c—环己烷的吸附系数C B—苯的浓度;Cc—环己烷的浓度;PH2—氢分压.直到转化率为90%都观察到对苯为零级反应这一现象说明苯在催化剂上强烈吸附,在0~90%这一范围内r等于k,活化能接近54.36kJ/mol;对芳烃在高转化率下的反应级数还没有确切的解释;有可能是因为,在苯浓度很低时,b B C B项与1+bcCc相比变得可以忽略不计,也有可能是因为扩散阻力造成的;对气相催化加氢,经实验测定,有如下动力学方程:r=kp0.5H2反应温度<100℃r=kp0.5苯p3H2反应温度>200℃上列第二式表明,当反应温度大于200℃,氢压的变化对反应速度十分敏感;2.工艺条件的选择1原料的精制原料氢气可来源于合成气,石脑油催化重整气,石油烃蒸气热裂解气以及甲苯烷基化装置来气体,其中的氢含量可在57%~96%之间波动;原料氢气中水和CO会使催化剂中毒,可通过甲烷化让CO转变为对催化剂无毒害的甲烷;接着进行干燥以除去由甲烷化产生的水分;要求水分不得超过反应温度下水在环己烷中的溶解度,若超过,产生的游离水会导致催化剂聚结和失活;氢气中的硫主要是H2S太高,如超过5ul·l-1,则也要用碱液吸收精制方可投入装置使用;苯中的硫化物含量要严格控制,在反应条件下,硫化物会与催化剂反应,生成镍的硫化物和硫醇盐,例如,就噻吩而言,有下面的反应:镍的硫醇盐和镍的硫化物都没有活性;当镍吸附其重量的0.5%~2%的硫时,就会完全失活;为保护催化剂的活性,延长催化剂的使用寿命要求原料苯中硫含量小于5ul·l-1;2反应温度液相加氢反应温度控制在180~200℃,气相加氢反应温度稍高,采用贵金属催化剂和列管式反应器时为220~370℃,采用绝热式反应器和镍催化剂时为200~350℃;在上述温度范围内,催化剂已具有足够快的反应速度,而副反应则不十分明显;3操作压力液相法一般维持在2.0~3.0MPa,以保证主反应器中液相的稳定;在此压力下,由液相蒸发带走的反应热约占总反应热的20%,其余80%由器外换热器移走;气相法操作压力为3.0~3.5Mpa;4空速IFP的NiPS2骨架镍催化剂性能优良,在硫含量为1ppm时,1kg镍可以加氢10t苯,在重量空速WHSV为5的条件下操作,不添加新鲜催化剂的周期寿命可长达2000h;苯的转化率在反应开始时可达99.99%,周期末降至95%;3.CST反应器在苯加氢工艺中的应用气相法有列管式和绝热式两种;液相法,例如IFP法苯加氢工艺采用二个化学反应器;主反应器选用连续搅拌槽式CST反应器;为使催化剂很好的悬浮在反应液中,并使反应热用器外换热器及时移走,除采用氢气鼓泡外,反应液还用泵在换热器和反应器之间作强制循环,以保持固-液-气三相的良好接触;采用CST反应器的优点是可以利用自体致冷作用排除反应热,反应温度也容易控制,不足之处是它属全返混流反应器,转化率不可能很高;由前述反应原理可知,当转化率在95%以下时,反应对苯为零级,此时反应速度很快,对CST反应器,转化率达到95%以上并非难事,再加上它有上述优点,因此选用它作为液相加氢反应器是合适的;工业级环己烷要求苯含量小于1000ug·g-1,即环己烷纯度在99.9%以上;因此,除CST图3-2-21IFP苯加氢工艺的方块图图3-2-22海德拉法流程图图3-2-23IFP法苯加氢生产环己烷工艺流程图反应器外,还需增设一台反应器对反应液作进一步加氢处理;此时若再增设一台CST反应器显然不合适,所需设备多,反应时间长而且转化率达到99.9%以上仍有一定难度;比较合适的是增设一台称之为精制反应器的气相加氢反应器,它属活塞流反应器,转化率可以很高,由于加氢负荷小只有5%的苯,使用催化剂量少,设备也可做得较小;此外,从观察小反应器中温度的变化还可发现主反应器催化剂活性是否正常,若催化剂失活严重,精制反应器因加氢负荷明显增高,温度会迅速上升;图3-2-21示出了IFP法工艺的方块图;由图3-2-21可知,氢气中的CO经甲烷化反应,脱除率可达97%以上CO残留量为300ul·l-1;环己烷经精制反应器后,其中的苯约为20ug·g-1;ul·l-14.工艺流程1气相法工艺流程气相法有贝克森法、HA-84法、海德拉法、霍德赖法等,其中海德拉法是现有的苯加氢方法中第一个工业化的方法;图3-2-22为海德拉法流程简图;采用三个绝热反应器;反应热通过在反应器间设置的冷却器消除图中末画出,原先采用铂催化剂,以锂盐为助催化剂,后来自行研制出镍催化剂;铂催化剂抗硫性能好,允许苯中硫化物的硫含量达300ul·l-1,但价格昂贵;反应温度200~350℃,为保证苯的高转化率,最后一台反应器出口温度应保持在275℃以下;n氢/n苯通过循环保持在2∶1时,反应器的压力保持在3.0MPa左右,气体每间隔一段时间须放空,务必使系统中气体的氢含量始终保持在30%以上;2液相法工艺流程图3-2-23示出了IFP 法苯加氢生产环己烷工艺流程;进料中氢与苯的克分子比为3.5∶1或更大,以环己烷计的收率在99%以上;。
苯加氢生产环己烷

(年)利润总额=年产品销售收入– 年产品销售税金及附加- 年总成本费用
=45315-45315*14%-27421.50=14721.45万元/年
(税后)静态投资回收期1.9年。
20
7 安全分析
反应器: ❖ 平稳控制反应温度不超过200℃,反应压力不超过
3.1MPa,保持氢分压0.6MPa不变。 所用催化剂雷尼镍遇空气能自燃,因此必须杜绝外 漏。联锁控制系统和安全设施要保持处于良好状态 。
扬程(m) 5 15 5 进口流量 5000m3/h 直径(m) 1.5 1.5
功率(kw) 1 1 1
高度(m) 3 3
0.7 0.7 0.7
2
7.5 7.5 10 15 10 100
19
总操作费用是有直接操作费用、固定操作费用和管理费用三部分组成的。
Fixed Capital Investment(FCI):987万元 /年
E-101D
E-101E
F-101A
F-101B
P-21
V-103
V-101 V-102 P-101 A-C E-101 A-E R-101 A-B F-101 A-B V-103
苯储料罐 氢气储罐 流量泵 换热器 反应器 闪蒸罐 环己烷储罐
14
全流程模拟
H2
B1 B3
3 2
C6H 6
6
B2 B4
。 ❖ 装置区内设置的水幕,要定期检查,保持好用
应急处置
❖ 皮肤接触:脱去被污染的衣着,用肥皂水和清水彻底冲洗皮肤。 ❖ 眼睛接触:提起眼睑,用流动清水或生理盐水冲洗。就医。 ❖ 吸入:迅速脱离现场至空气新鲜处。保持呼吸道通畅。如呼吸困难,给
予输氧。如呼吸停止,立即进行人工呼吸。就医。 ❖ 食入:饮足量温水,催吐。就医。 ❖ 呼吸系统防护:一般不需要特殊防护,高浓度接触时可佩戴自吸过滤式
苯加氢制环己烷
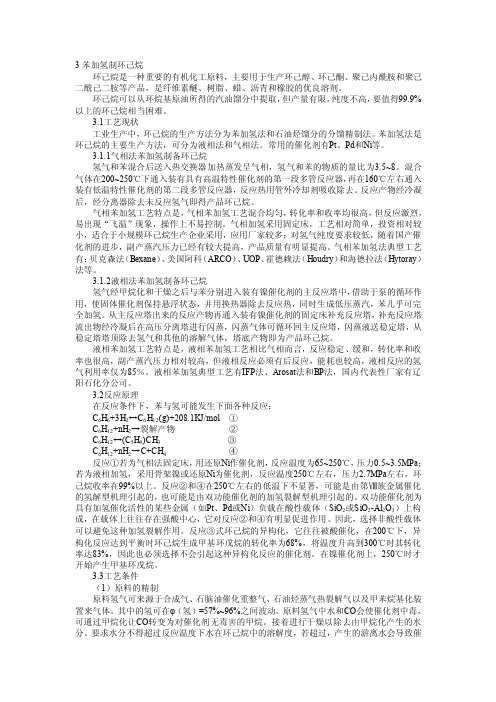
3苯加氢制环己烷环己烷是一种重要的有机化工原料,主要用于生产环己醇、环己酮、聚己内酰胺和聚己二酰己二胺等产品,是纤维素醚、树脂、蜡、沥青和橡胶的优良溶剂。
环己烷可以从环烷基原油所得的汽油馏分中提取,但产量有限,纯度不高,要值得99.9%以上的环己烷相当困难。
3.1工艺现状工业生产中,环己烷的生产方法分为苯加氢法和石油烃馏分的分馏精制法。
苯加氢法是环己烷的主要生产方法,可分为液相法和气相法。
常用的催化剂有Pt、Pd和Ni等。
3.1.1气相法苯加氢制备环己烷氢气和苯混合后送入热交换器加热蒸发呈气相,氢气和苯的物质的量比为3.5~8。
混合气体在200~250℃下通入装有具有高温特性催化剂的第一段多管反应器,再在160℃左右通入装有低温特性催化剂的第二段多管反应器,反应热用管外冷却剂吸收除去。
反应产物经冷凝后,经分离器除去未反应氢气即得产品环己烷。
气相苯加氢工艺特点是,气相苯加氢工艺混合均匀,转化率和收率均很高,但反应激烈,易出现“飞温”现象,操作上不易控制。
气相加氢采用固定床,工艺相对简单,投资相对较小,适合于小规模环己烷生产企业采用,应用厂家较多;对氢气纯度要求较低,随着国产催化剂的进步,副产蒸汽压力已经有较大提高,产品质量有明显提高。
气相苯加氢法典型工艺有:贝克森法(Bexane)、美国阿科(ARCO)、UOP、霍德赖法(Houdry)和海德拉法(Hytoray)法等。
3.1.2液相法苯加氢制备环己烷氢气经甲烷化和干燥之后与苯分别进入装有镍催化剂的主反应塔中,借助于泵的循环作用,使固体催化剂保持悬浮状态,并用换热器除去反应热,同时生成低压蒸汽,苯几乎可完全加氢。
从主反应塔出来的反应产物再通入装有镍催化剂的固定床补充反应塔,补充反应塔流出物经冷凝后在高压分离塔进行闪蒸,闪蒸气体可循环回主反应塔,闪蒸液送稳定塔,从稳定塔塔顶除去氢气和其他的溶解气体,塔底产物即为产品环己烷。
液相苯加氢工艺特点是,液相苯加氢工艺相比气相而言,反应稳定、缓和,转化率和收率也很高,副产蒸汽压力相对较高,但液相反应必须有后反应,能耗也较高,液相反应的氢气利用率仅为85%。
苯加氢液相制环己烷
四、苯加氢制环己烷环己烷主要(占总产量90%以上)用来生产环己醇、环己酮及己二酸,后三者是制造尼龙-6和尼龙-66的重要原料。
环己烷还用作树脂、油脂、橡胶和增塑剂等的溶剂。
用作尼龙原料的高纯度的环己烷主要由苯加氢制得。
工业上苯加氢生产环己烷有气相法和液相法两种。
虽然美国杜邦公司早已开发成功气相加氢工艺,但大多数工厂仍采用液相加氢工艺,例如美国的Uop公司,法国石油研究所(IFP)等。
气相法的优点是催化剂与产品分离容易,所需反应压力也较低,但设备多而大,投资费用比液相法高。
1.反应原理(1)化学反应在反应条件下,苯与氢可能发生下面各种反应:+nH2→C+CH4(4)反应(1)若为气相法固定床,用还原Ni 作催化剂,反应温度为65~250℃,压力0.5~3.5MPa;若为液相加氢,采用骨架镍或还原Ni为催化剂,反应温度为160~220℃,压力2.7MPa左右,环己烷收率在99%以上。
反应(2)和(4)在250℃左右的低温下不显著,它们可能是由第Ⅷ族金属催化的氢解型机理引起的,也可能是由双功能催化剂的加氢裂解型机理引起的。
双功能催化剂为具有加氢催化活性的某些金属(如Pt,Pd或Ni)负载在酸性载体(SiO2或SiO2/Al2O3)上构成,在载体上往往存在强酸中心,它对反应(2)和(4)有明显促进作用。
因此,选择非酸性载体可以避免这种加氢裂解作用。
反应(3)是环己烷的异构化,它往往被酸催化,在200℃下,异构化反应达到平衡时环己烷生成甲基环戊烷的转化率为68%,将温度升高到300℃时其转化率达83%,因此也必须选择不会引起这种异构化反应的催化剂。
在镍催化剂上,250℃时才开始产生甲基环戊烷。
(2)热力学平衡由反应(1)可知,苯加氢生成环己烷的反应是一个放热的体积(摩尔数)缩小的可逆反应。
在127℃时的平衡常数为7×107,在227℃时为1.86×102。
氢压和温度对环己烷中苯的平衡浓度的影响示于图3-2-18。
苯加氢制环己烷范文
苯加氢制环己烷范文反应机理如下:首先,苯分子与氢气在催化剂的存在下进行反应。
常用的催化剂有铂、铑、钯等贵金属催化剂。
这些催化剂能够在适当的温度和压力条件下有效地催化苯的加氢反应。
其次,苯分子中的π电子与氢气中的氢原子发生反应,形成苯并对氢加成的中间体。
在反应过程中,π电子中的一个电子与氢原子形成共价键,另一个π电子不参与反应。
最后,中间体失去另一个π电子,形成环状结构的六元环化合物环己烷。
在这一步骤中,中间体中的π电子与催化剂的钯原子发生反应,生成钯环己烷中间体。
然后,钯环己烷与氢气发生反应,失去π电子后生成环己烷。
总结起来,苯加氢制环己烷的反应过程可以分为两步:加氢反应和环合反应。
加氢反应由催化剂催化,形成苯并对氢加成的中间体。
环合反应利用中间体失去π电子,形成环己烷的六元环结构。
例如,环己烷可用作溶剂,在化学合成、涂料、橡胶和塑料工业中起重要作用。
此外,环己烷也是一种重要的石油组分,在石油加工过程中有重要的用途。
在实际的生产过程中,苯加氢制环己烷通常需要一定的温度和压力条件。
较低温度和较高压力有利于提高反应速率和产率。
此外,催化剂的选择和使用也对反应的效率和产率有很大的影响。
在实验室中,常常使用自制或商业化的催化剂进行苯加氢制环己烷的反应。
实验条件可以根据具体的需要进行调整,以提高反应的效率和产率。
总之,苯加氢制环己烷是有机化学中的一种重要反应,经典的反应机理是苯与氢气发生加氢反应,生成环己烷。
这个反应具有重要的应用价值,在化学合成和药物研发中起着重要作用。
通过调整反应条件和催化剂的选择,可以有效提高反应的效率和产率。
环己烷安全生产要点(二篇)
环己烷安全生产要点1工艺简述该装置以苯为原料,通过加氢生成环己烷,再用空气氧化生产环己醇和环己酮,简称醇酮。
简要工艺流程是:将苯和氢通过苯泵和氢压缩机送入主反应器,在催化剂雷尼镍的作用下,进行苯加氢反应,生成环己烷。
其反应温度186~200℃,反应压力2.0~3.1MPa,保持氢分压0.6MPa不变。
反应后的气体进入后反应器继续反应,以提高转化率。
从后反应器出来的环己烷蒸气经冷凝后,进入稳定塔蒸馏提纯得环已烷。
将所得环已烷和混合气(循环气和新鲜空气的混合气)送入氧化反应器,环已烷与混合气中的氧进行氧化反应,生成环已基过氧化物和少量的环已醇、环已酮。
有四台氧化反应器,一、二、三、四氧化反应器的反应温度依次是181℃、175℃、167℃、166℃,反应压力均是1.9MPa。
氧化反应产物经预浓缩、氧化洗涤、脱水后送入脱氧化反应器,在催化剂铬酸叔丁酯的作用下进行反应,生成环已醇和环已酮,简称醇酮。
醇酮产物经脱环已烷、精馏后,得到产品醇酮。
该装置的物料苯、氢、环已烷均是易燃易爆物质;环已醇、环已酮可燃可爆。
苯、环已烷、醇酮都有毒。
活性雷尼镍催化剂遇空气能自燃;催化剂铬酸酐有强腐蚀性。
2重点部位2.1加氢反应器苯加氢反应在反应器中进行,由于苯和氢都是易燃、易爆物质,且反应温度和压力都较高,如果控制不好,是很危险的。
反应器设有联锁控制系统和水喷淋系统。
2.2氧化反应器在四个反应器中,环已烷直接用空气进行氧化反应。
因环已烷易燃、易爆,又有空气存在,所以危险性很大。
氧化反应后的尾气容易形成爆炸性混合物,因此在四个氧化反应器的上部,都设有测尾气中氧含量的在线分析仪,控制尾气中的含氧量在3.5%(体积)以下,超限发出声光报警。
为控制好进氧化反应器的混合气中的氧含量,在气-气混合器的出口,设有测混合气中氧含量的在线分析仪,控制其含氧量在15%(体)以下。
氧化应器设有联锁控制系统及水喷淋、蒸汽灭火设施。
2.3脱过氧化反应器环已基过氧化物的分解反应在脱过氧化反应器中进,反应温度92℃,反应压力0.03MPa。
环己烷的生产工艺
一、环己烷的工艺介绍:工业生产中,环己烷的生产方法分为苯加氢法和石油烃馏分的分馏精制法。
苯加氢法是环己烷的主要生产方法,可分为液相法和气相法。
液相苯加氢的工艺特点是反应稳定、平和,转化率和收率也很高;但必须要有后反应,,能耗也较高,氢气的利用率仅为85% ;典型工艺有IFP 法、BP 法和Arosat法。
气相苯加氢的工艺特点是工艺气体混合均匀,转化率和收率均很高,但反应激烈,易出现飞温现象;典型工艺有Brxane,ARCO,UOP,Houdry,Hy-toray法。
二、反应物与产物的介绍:1.氢气分子式:H2沸点:-252.77℃(20.38K)熔点:-259.2℃密度:0.09kg/m3相对分子质量:2.016方法:电解、裂解、煤制气等三相点:-254.4℃液体密度(平衡状态,-252.8℃):169kg/m3气体密度(101.325kPa,0℃):0.0899kg/m3比容(101.325kPa,21.2℃):5.987m3/kg气液容积比(15℃,100kPa):974L/L临界温度:-234.8℃临界压力:1664.8kPa临界密度:66.8kg/m3熔化热(-254.5℃)(平衡态):48.84kJ/kg气化热△Hv(-249.5℃):305kJ/kg热值:1.4108 J/kg规格:含有少量的甲烷2%左右。
2苯名称:中文名称:安息油,净苯,动力苯,纯苯,溶液苯,困净苯,困净苯别名:Benzol,Phenyl hydride,Phenyl hydride ,Cyclohexatriene ,Coal naphtha ,Phene化学式:C6H6相对分子质量:78.11性状:无色透明液体。
有芳香气味。
具强折光性。
易挥发。
能与乙醇、乙醚、丙酮、四氯化碳、二硫化碳、冰乙酸和油类任意混溶,微溶于水。
燃烧时的火焰光亮而带黑烟。
相对密度(d154)0.8787。
熔点5.5℃。
沸点80.1℃。
折光率(n20D)1.50108。
- 1、下载文档前请自行甄别文档内容的完整性,平台不提供额外的编辑、内容补充、找答案等附加服务。
- 2、"仅部分预览"的文档,不可在线预览部分如存在完整性等问题,可反馈申请退款(可完整预览的文档不适用该条件!)。
- 3、如文档侵犯您的权益,请联系客服反馈,我们会尽快为您处理(人工客服工作时间:9:00-18:30)。
苯加氢制环己烷四、苯加氢制环己烷环己烷主要(占总产量90%以上)用来生产环己醇、环己酮及己二酸,后三者是制造尼龙-6和尼龙-66的重要原料。
环己烷还用作树脂、油脂、橡胶和增塑剂等的溶剂。
用作尼龙原料的高纯度的环己烷主要由苯加氢制得。
工业上苯加氢生产环己烷有气相法和液相法两种。
虽然美国杜邦公司早已开发成功气相加氢工艺,但大多数工厂仍采用液相加氢工艺,例如美国的Uop公司,法国石油研究所(IFP)等。
气相法的优点是催化剂与产品分离容易,所需反应压力也较低,但设备多而大,投资费用比液相法高。
1.反应原理(1)化学反应在反应条件下,苯与氢可能发生下面各种反应:+nH2→C+CH4(4)反应(1)若为气相法固定床,用还原Ni作催化剂,反应温度为65~250℃,压力0.5~3.5MPa;若为液相加氢,采用骨架镍或还原Ni为催化剂,反应温度为160~220℃,压力2.7MPa左右,环己烷收率在99%以上。
反应(2)和(4)在250℃左右的低温下不显著,它们可能是由第Ⅷ族金属催化的氢解型机理引起的,也可能是由双功能催化剂的加氢裂解型机理引起的。
双功能催化剂为具有加氢催化活性的某些金属(如Pt,Pd或Ni)负载在酸性载体(SiO2或SiO2/Al2O3)上构成,在载体上往往存在强酸中心,它对反应(2)和(4)有明显促进作用。
因此,选择非酸性载体可以避免这种加氢裂解作用。
反应(3)是环己烷的异构化,它往往被酸催化,在200℃下,异构化反应达到平衡时环己烷生成甲基环戊烷的转化率为68%,将温度升高到300℃时其转化率达83%,因此也必须选择不会引起这种异构化反应的催化剂。
在镍催化剂上,250℃时才开始产生甲基环戊烷。
(2)热力学平衡由反应(1)可知,苯加氢生成环己烷的反应是一个放热的体积(摩尔数)缩小的可逆反应。
在127℃时的平衡常数为7×10,在227℃时为1.86×10。
氢压和温度对环己烷中苯的平衡浓度的影响示于图3-2-18。
由图3-2-18可见,低温和高压对反应是有利的。
相反,反应(2)和(4)则受到抑制;环己烷异构化反应是一个等摩尔反应,压力对反应影响不大。
温度对反应(3)平衡的影响示于图3-2-19。
由图3-2-19可知,甲基环己烷的平衡浓度随温度的提高而上升。
为抑制这一副反应,也要求催化剂在较低温度下就有高的苯加氢活性,而且在催化剂上不存在酸性中心。
(3)催化剂和催化机理对苯加氢有催化活性的金属有:Rh,Ru,Pt,W,Ni,Fe,Pd和Co等。
常用金属按活性排列为:Pt>Ni>Pd加氢活性的比例为:KPt:Kni:KPd=18:7:1这表明铂的活性比镍高2.6倍。
但铂的价格为镍的几百倍,因此选择镍作为催化剂活性组分更经济。
如前所述,苯加氢有气相和液相两种方法,对液相加氢而言,要求催化剂72是细微颗粒(粉末,粒度为20~100μm),能悬浮在反应液中进行液-固相加氢反应。
考虑到反应要求低温高活性,而且苯环加氢比烯,炔加氢困难,工业上都选用骨架镍催化剂。
用这种催化剂在3.5MPa的压力和不产生副反应的温度(200℃)下,反应速率很容易达到每克镍每分钟转化0.15mol苯的水平。
骨架镍催化剂的制备过程为:先由镍和铝(重量比为1)在1500~1600℃下制成镍铝合金,然后研磨至粒度为0.04~0.25mm,再用氢氧化钠浸出铝,最后经洗涤和干燥得到高活性,多孔和高强度的骨架催化剂。
由于活性高,在空气中极易自燃,故一般将它浸在乙醇中出售或经表面钝化处理变成不自燃的干燥粉末后出售。
成品为黑色粉末,镍含量为65%,松密度为2.4g/cm3;苯的气相加氢催化剂为负载型Ni催化剂,要求载体有足够的强度承受工业条件下的机械应力,有足够的比表面积和适宜的孔径分布,能负载足够数量的镍盐(氧化镍)。
此外,还要求载体对副反应没有催化活性。
符合上述条件,工业上应用的载体有高纯度氧化铝球(Φ2~24mm),SiO2和硅藻土等,比表面积210m/g,松33密度0.91g/cm,孔隙度0.4cm/g。
现在,工业上应用较多的液相催化剂牌号为法国的NiPS2,气相催化剂牌号为法国的LD143催化剂,它们都是由法国石油研究所(IFP)开发成功。
除上述镍催化剂外,也有采用Ni-Pd催化剂,硫化镍和硫化钯催化剂。
硫化物催化剂虽然不怕原料苯中硫化物的毒害,但要求高温(450℃)和高压(31.0MPa)。
关于催化加氢反应机理,即使像乙烯加氢这样一个简单的反应,认识也不一致。
分岐主要集中在①氢是否也发生化学吸附;②作用物在催化剂表面是发生单位(独位)吸附还是多位吸附;③氢与吸附在催化剂表面的作用物分子是怎样反应的。
以苯加氢生成环己烷为例,就提出了两种不同的机理,一种认为苯分子在催化剂表面发生多位吸附,形成,然后发生加氢反应,生成环己烷。
近年来又提出了另一种观点,认为苯分子只与催化剂表面一个活性中心发生化学吸附(即独位吸附),形成π-键合吸附物,然后吸附的氢原子逐步加到吸附的苯分子上,即上述二种反应机理,还留待进一步实验验证。
(4)反应动力学 Louvain的动力学学派专门研究过在镍催化剂上苯加氢的反应动力学。
研究表明,在骨架镍催化剂催化下,苯在高压、液相、温度低于200℃下加氢,苯转化率从低升至90%以上,反应对苯为零级,当转化率在95%以上时,对苯的反应级数变得接近于1。
对氢而言,在所研究的压力范围内对氢为零级反应。
实验结果示于图3-2-20。
这一实验结果可用苯和氢之间的非竞争吸附来解积,并可用下列速率方程式表示:图3-2-20 液相苯加氢反应动力学级数的实验测定式中: bB—苯的吸附系数;bc—环己烷的吸附系数CB—苯的浓度;Cc—环己烷的浓度;PH2—氢分压.直到转化率为90%都观察到对苯为零级反应这一现象说明苯在催化剂上强烈吸附,在0~90%这一范围内r等于k,活化能接近54.36kJ/mol。
对芳烃在高转化率下的反应级数还没有确切的解释。
有可能是因为,在苯浓度很低时,bBCB项与(1+bcCc)相比变得可以忽略不计,也有可能是因为扩散阻力造成的。
对气相催化加氢,经实验测定,有如下动力学方程:r=k*pr=k*p度>200℃) 0.5H20.5苯 (反应温度H2 (反应温上列第二式表明,当反应温度大于200℃,氢压的变化对反应速度十分敏感。
2.工艺条件的选择(1)原料的精制原料氢气可来源于合成气,石脑油催化重整气,石油烃蒸气热裂解气以及甲苯烷基化装臵来气体,其中的氢含量可在57%~96%之间波动。
原料氢气中水和CO会使催化剂中毒,可通过甲烷化让CO转变为对催化剂无毒害的甲烷。
接着进行干燥以除去由甲烷化产生的水分。
要求水分不得超过反应温度下水在环己烷中的溶解度,若超过,产生的游离水会导致催化剂聚结和失活。
氢气中的硫(主要是H2S)太高,如超过-15ul〃l,则也要用碱液吸收精制方可投入装臵使用。
苯中的硫化物含量要严格控制,在反应条件下,硫化物会与催化剂反应,生成镍的硫化物和硫醇盐,例如,就噻吩而言,有下面的反应:镍的硫醇盐和镍的硫化物都没有活性。
当镍吸附其重量的0.5%~2%的硫时,就会完全失活。
为保护催化剂的活性,延长催化剂的使-1用寿命要求原料苯中硫含量小于5 ul〃l 。
(2)反应温度液相加氢反应温度控制在180~200℃,气相加氢反应温度稍高,采用贵金属催化剂和列管式反应器时为220~370℃,采用绝热式反应器和镍催化剂时为200~350℃。
在上述温度范围内,催化剂已具有足够快的反应速度,而副反应则不十分明显。
(3)操作压力液相法一般维持在2.0~3.0MPa,以保证主反应器中液相的稳定。
在此压力下,由液相蒸发带走的反应热约占总反应热的20%,其余80%由器外换热器移走。
气相法操作压力为3.0~3.5Mpa。
(4)空速 IFP的NiPS2骨架镍催化剂性能优良,在硫含量为1ppm时,1kg镍可以加氢10t苯,在重量空速(WHSV)为5的条件下操作,不添加新鲜催化剂的周期寿命可长达2000h。
苯的转化率在反应开始时可达99.99%,周期末降至95%。
3.CST反应器在苯加氢工艺中的应用气相法有列管式和绝热式两种。
液相法,例如IFP法苯加氢工艺采用二个化学反应器。
主反应器选用连续搅拌槽式(CST)反应器。
为使催化剂很好的悬浮在反应液中,并使反应热用器外换热器及时移走,除采用氢气鼓泡外,反应液还用泵在换热器和反应器之间作强制循环,以保持固-液-气三相的良好接触。
采用CST反应器的优点是可以利用自体致冷作用排除反应热,反应温度也容易控制,不足之处是它属全返混流反应器,转化率不可能很高。
由前述反应原理可知,当转化率在95%以下时,反应对苯为零级,此时反应速度很快,对CST反应器,转化率达到95%以上并非难事,再加上它有上述优点,因此选用它作为液相加氢反应器是合适的。
工-1业级环己烷要求苯含量小于1000ug〃g,即环己烷纯度在99.9%以上。
因此,除CST图3-2-21 IFP苯加氢工艺的方块图图3-2-22 海德拉法流程图图3-2-23 IFP法苯加氢生产环己烷工艺流程图反应器外,还需增设一台反应器对反应液作进一步加氢处理。
此时若再增设一台CST反应器显然不合适,所需设备多,反应时间长而且转化率达到99.9%以上仍有一定难度。
比较合适的是增设一台称之为精制反应器的气相加氢反应器,它属活塞流反应器,转化率可以很高,由于加氢负荷小(只有5%的苯),使用催化剂量少,设备也可做得较小。
此外,从观察小反应器中温度的变化还可发现主反应器催化剂活性是否正常,若催化剂失活严重,精制反应器因加氢负荷明显增高,温度会迅速上升。
图3-2-21示出了IFP法工艺的方块图。
由图3-2-21可知,氢气中的CO经甲烷化反应,脱除率可达97%以上(CO残留量为-1300ul〃l);环己烷经精制反应器后,其中的-1 -1苯约为20ug〃g。
ul〃l4.工艺流程(1)气相法工艺流程气相法有贝克森法、HA-84法、海德拉法、霍德赖法等,其中海德拉法是现有的苯加氢方法中第一个工业化的方法。
图3-2-22为海德拉法流程简图。
采用三个绝热反应器。
反应热通过在反应器间设臵的冷却器消除(图中末画出),原先采用铂催化剂,以锂盐为助催化剂,后来自行研制出镍催化剂。
铂催化剂抗硫性能好,-1允许苯中硫化物的硫含量达300 ul〃l,但价格昂贵。
反应温度200~350℃,为保证苯的高转化率,最后一台反应器出口温度应保持在275℃以下。
n(氢)/n(苯)通过循环保持在2∶1时,反应器的压力保持在3.0MPa左右,气体每间隔一段时间须放空,务必使系统中气体的氢含量始终保持在30%以上。
(2)液相法工艺流程图3-2-23示出了IFP法苯加氢生产环己烷工艺流程。