氯碱工艺流程
氯碱工艺流程

氯碱工艺流程
氯碱工艺是一种重要的化学工业生产流程,它主要用于生产氯气、氢气和氢氧化钠。
这些化学品在工业生产和日常生活中都有着广泛的
应用,因此氯碱工艺的生产对于现代社会的发展具有非常重要的意义。
氯碱工艺的流程主要分为三步:电解、水解和蒸发结晶。
在电解过程中,将氯化钠放入电解池中,并加入适量的水,然后
施加电流来进行电解反应。
这个过程中,氯化钠分解成了氯气和氢气,同时在电极上生成了氢氧化钠。
整个电解过程的化学反应如下:
2 NaCl + 2 H₂O → Cl₂ + H₂ + 2 NaOH
在水解过程中,将刚刚生成的氢氧化钠与适量的水混合。
这个过
程中,氢氧化钠与水反应生成更多的氢氧化钠,同时释放出热。
化学
反应如下:
NaOH + H₂O → Na⁺ + OH⁻ + Heat
最后,在蒸发结晶过程中,将反应所得的溶液进行蒸发,使其浓缩,然后进行结晶,从而得到氢氧化钠的固体结晶体。
整个氯碱工艺流程需要仔细精确的操作和控制,才能保证生产出
高质量的化学品。
在实际操作中,需要考虑到许多因素,如温度、浓度、电流等等,以使产品的质量和产量达到最优化的状态。
总之,氯碱工艺是一项非常重要的工业生产流程,能够生产出许多重要的化学品。
在进行氯碱工艺时,需要细心认真的操作和控制,从而保证产品的质量和产量。
这一流程的应用在化学工业和日常生活中都有着广泛的用途,因此,氯碱工艺的发展和研究必将在未来发挥着越来越重要的作用。
氯碱工业的工艺流程
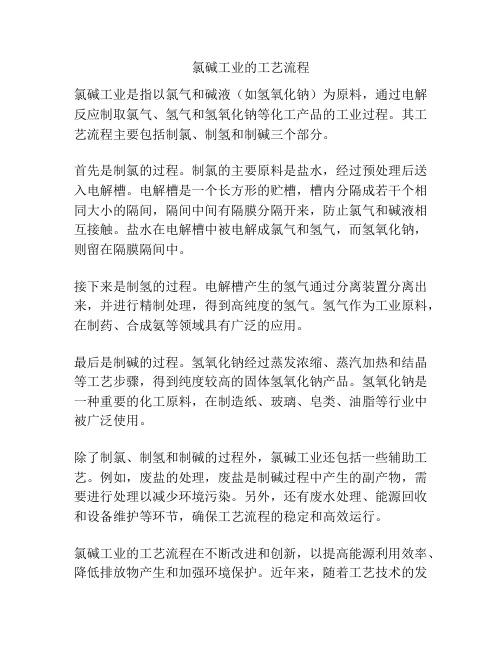
氯碱工业的工艺流程
氯碱工业是指以氯气和碱液(如氢氧化钠)为原料,通过电解反应制取氯气、氢气和氢氧化钠等化工产品的工业过程。
其工艺流程主要包括制氯、制氢和制碱三个部分。
首先是制氯的过程。
制氯的主要原料是盐水,经过预处理后送入电解槽。
电解槽是一个长方形的贮槽,槽内分隔成若干个相同大小的隔间,隔间中间有隔膜分隔开来,防止氯气和碱液相互接触。
盐水在电解槽中被电解成氯气和氢气,而氢氧化钠,则留在隔膜隔间中。
接下来是制氢的过程。
电解槽产生的氢气通过分离装置分离出来,并进行精制处理,得到高纯度的氢气。
氢气作为工业原料,在制药、合成氨等领域具有广泛的应用。
最后是制碱的过程。
氢氧化钠经过蒸发浓缩、蒸汽加热和结晶等工艺步骤,得到纯度较高的固体氢氧化钠产品。
氢氧化钠是一种重要的化工原料,在制造纸、玻璃、皂类、油脂等行业中被广泛使用。
除了制氯、制氢和制碱的过程外,氯碱工业还包括一些辅助工艺。
例如,废盐的处理,废盐是制碱过程中产生的副产物,需要进行处理以减少环境污染。
另外,还有废水处理、能源回收和设备维护等环节,确保工艺流程的稳定和高效运行。
氯碱工业的工艺流程在不断改进和创新,以提高能源利用效率、降低排放物产生和加强环境保护。
近年来,随着工艺技术的发
展,氯碱工业在中国的发展也取得了显著的成就,成为推动经济发展和工业结构优化的重要力量。
总之,氯碱工业的工艺流程主要包括制氯、制氢和制碱三个部分,通过电解反应将盐水转化成化工产品。
这一工艺流程的不断改进和创新,将为中国的经济发展和环境保护做出积极的贡献。
氯碱工艺流程

氯碱生产工艺流程总述永祥树脂有限公司生产系统是由氯碱系统,PVC系统,三氯氢硅系统,及公用系统组成.公用系统又包括水,电,汽。
水,电,汽的正常供应是确保生产平稳运行的关键。
这里我就谈谈氯碱系统的生产流程。
永祥树脂有限公司的氯碱系统是由电解,盐水,氯氢,液氯,冷冻,盐酸,漂液,蒸发,循环水组成的系统。
其主要流程是盐水生产的精盐水经电解生成主要成分是NaoH,NaCl的电解液和氯气,氢气三种物质。
电解液由蒸发经浓缩,并分离其中的NaCl,加水溶解后供盐水工序生产精盐水用。
NaoH经冷却沉降后,送成品桶作为成品销售。
氯气在氯氢工序通过洗涤冷却,干燥,压缩输送到液氯,盐酸,PVC,三氯氢硅。
氯碱片区主要是送液氯和盐酸。
氯气在液氯经冷冻送来的—35℃冷冻盐水液化为液氯,液氯尾气送盐酸和漂液生产盐酸和漂液用.氢气是经氯氢工序洗涤冷却,压缩输送到PVC,三氯氢硅,盐酸。
氯碱片区送盐酸,在合成炉与氯气燃烧生成氯化氢气体,经水吸收后生成成品盐酸供销售出售。
液氯尾气在漂液生产池中与石灰水生成漂液供销售出售。
氯碱车间工艺流程简述一.氯碱车间基本概况1.自然条件:氯碱车间位于公司的东部,西部为乙炔车间,南部为聚合乙烯车间,西南为氯乙烯车间,东西向220米,南北向220米。
人员构成:员工212人,其中管理人员18人,一般员工194人,倒班员工为168人.最高气温39℃,最低气温约0℃,平均气温16。
5—18℃。
平均风速为0。
5—2。
0米/秒。
2.生产装置规模:最初设计能力为1万吨/年隔膜碱,正式投产时间1990年,经过多次技改扩产,产量达到约9万吨/年隔膜碱.3.氯碱车间工艺特点:车间压力容器较多,压力控制要求高;工艺介质为有毒有害物质。
二.工艺流程简述:1。
电解工序工艺流程简述:符合工艺要求的精制盐水由盐水工序送入精盐水贮槽,用精盐水泵送入高位槽,自流入盐水预热器,加热至80℃±2℃后注入电解槽内,当供给直流电后,盐水进行电化学反应,在阳极室生成的氯气和在阴极室生成的氢气分别送往氯氢工序处理,阴极室生成的电解碱液断电后经管道流入电解液集中槽,用泵送至蒸发工序。
氯碱工艺的生产工艺

氯碱工艺的生产工艺
氯碱工艺是一种生产氯碱产品(氯气、氢气、氢氧化钠和氯化氢)的工艺。
下面是氯碱工艺的一般生产工艺流程:
1. 原料准备:氯碱工艺的主要原料是盐和水。
盐是通过海水或地下盐水提取的,经过净化和浓缩处理后得到质量合格的氯化钠溶液。
2. 电解槽电解:将氯化钠溶液引入电解槽,通过电解过程将氯化钠分解成氯气和氢气。
在电解槽中,使用膜或水合性的离子交换质子膜将产生的氯气和氢气分开。
3. 氢气处理:从电解槽中收集分离出的氢气,并进行必要的处理和净化。
这些处理可能包括除去杂质、压缩和储存等。
4. 氯气处理:从电解槽中收集分离出的氯气,并进行必要的处理和净化。
这些处理可能包括除去杂质、压缩和储存等。
5. 水处理:将剩余的产物溶液回收并进行处理。
通常,这些溶液中含有氢氧化钠和氯化氢。
通过将氯化氢与水反应,可以生成氢氧化钠。
同时,也可以通过逆向离子交换的方法来提取纯度较高的氢氧化钠。
6. 产品处理和分离:将生产的氯气、氢气、氢氧化钠和氯化氢进行相应的处理
和分离。
这可能包括去除杂质、纯化、压缩和储存等工艺。
7. 废水和废气处理:为了保护环境,对生产过程中产生的废水和废气进行处理。
这可能包括废水处理和气体吸收等工艺。
以上是氯碱工艺的一般生产工艺流程。
不同的氯碱生产厂商可能有所不同,但大体上都是基于上述的工艺进行生产。
氯碱工业生产流程简述

1. 氯气冷却、干燥、压缩;2. 氢气净化、压缩
准备气体产品以满足后续使用或储存要求,确保安全与纯度
液氯生产
1. 将冷却干燥后的氯气液化(-35℃冷冻盐水);2. 收集液氯,处理尾气
得到液态氯产品,提高储存运输效率,尾气再利用
盐酸生产
1. 利用液氯与水反应生成盐酸;2. 调整浓度,储存
制备副产品盐酸,用于化工、冶金等行业
实现环保合规,资源回收再利用Fra bibliotek公用工程与辅助设施
1. 提供蒸汽、冷却水、电力;2. 维护设备、仪表气供应等
保障生产过程所需能源、动力与维护支持
氢氧化钠(烧碱)处理
1. 冷却沉降电解液中的氢氧化钠;2. 过滤、蒸发浓缩;3. 包装成固体或制成不同浓度的液体烧碱
提纯、浓缩并包装氢氧化钠产品,供应下游用户
蒸发
对电解液进行蒸发浓缩,回收NaCl
回收未完全反应的氯化钠,循环回盐水制备工序
废液/废物处理
1. 处理电解过程中产生的含碱废水;2. 回收利用盐泥(含钙、镁、铁等杂质)
氯碱工业生产流程简述
工序
操作步骤
目的/作用
盐水制备
1. 将工业盐与水按比例混合溶解;2. 过滤去除泥沙等杂质;3. 可能加入试剂(如碳酸钠、氯化钡)进行精制
制备浓度适宜(约15%-20%)的纯净盐水溶液,作为电解原料
电解
1. 使用离子交换膜电解槽进行电解;2. 食盐水在直流电作用下发生电化学反应
分离产生氯气(Cl₂)、氢气(H₂)和氢氧化钠(NaOH),实现原料的有效转化
氯碱工艺流程

氯碱工艺流程氯碱工艺是生产氯碱化工产品的一种重要工艺,主要包括电解法和化学法两种。
下面是一个典型的氯碱工艺流程。
首先是氯碱电解法。
这是目前最常用的氯碱工艺,主要是通过电解盐水来制取氯气、氢气和氢氧化钠。
具体步骤如下:1. 盐水制备:将海水经过处理,除去杂质,使其达到制备盐水的要求。
待盐水处理好后,进入蓄盐池。
2. 预处理:将蓄盐池中的盐水送入预处理系统,通过过滤、絮凝、沉淀等工序,去除悬浮物、胶体物质、杂质等。
3. 进料:经过预处理的盐水进入电解槽。
4. 电解:在电解槽中,盐水被电解成氯气和氢气。
电解槽内有阳极和阴极,通过施加适当的电压,使得氯离子在阳极上失去电子转化为氯气,而水在阴极上还原为氢气。
5. 收集和分离:氯气和氢气经过收集系统,分别收集和储存。
而生成的碱液则通过电解槽底部的出口流出。
6. 碱液处理:产生的碱液进入碱液处理系统进行处理,通过回收、浓缩等工序,将其纯化并得到高纯度的氢氧化钠产品。
化学法是另一种氯碱工艺,主要是通过化学反应来制取氯气、氢气和氢氧化钠。
具体步骤如下:1. 盐酸生产:首先,将盐石和浓硫酸进行反应,生成盐酸气体。
2. 还原:将盐酸和金属在反应器中反应,产生氯气和相应的金属盐。
3. 加热分解:将金属盐加热分解,生成金属氧化物。
4. 中和:将金属氧化物与水反应,生成氢氧化钠。
5. 酸化:将氢氧化钠与酸反应,生成质量浓度较高的氢氧化钠溶液。
6. 浓缩和过滤:将氢氧化钠溶液进行浓缩,去除其中的杂质,并将其过滤。
7. 干燥和粉碎:将过滤后的氢氧化钠进行干燥,然后粉碎,最终得到氢氧化钠产品。
以上是一个典型的氯碱工艺流程,根据具体工厂的要求和生产条件,可能会有一些细节上的差异。
随着技术的不断进步和创新,氯碱工艺的流程也在不断优化,以提高生产效率和产品质量。
氯碱生产过程
氯碱生产过程氯碱工业利用电解饱和食盐水溶液制取烧碱(氢氧化钠)和氯气并副产氢气的生产过程.过程包括盐水精制、电解和产品精制等工序,其中主要工序是电解.工业上采用隔膜电解法、水银电解法和离子膜电解法.各法所采用的电解槽结构不同,因而其具体工艺流程及产品规格也有所不同.当前应用较多的是隔膜电解法.盐水精制海盐、岩盐(或称矿盐)、湖盐等固体原盐(NaCl)都是生产氯气和烧碱的原料.为使电解过程顺利进行并保证设备、操作的安全,无论采用哪种电解方法,原料都必须精制.固体盐溶于水中所得的饱和盐水,或来自地下盐井的盐水,在60℃左右加入碳酸钠、氢氧化钠,使其与盐水中的钙、镁杂质反应生成碳酸钙、氢氧化镁等沉淀.盐水中硫酸盐过高时,还需加入氯化钡(或碳酸钡)以生成硫酸钡沉淀.各种沉淀物经过絮凝、澄清、过滤分离后,清盐水加入盐酸调节pH使之成为中性或微酸性,再通过精制的(或回收的)固体盐层重新饱和,并加热到60~80℃,成为一次精制盐水,可供隔膜法或水银法使用.有的盐水中含有铵离子或有机氮化合物,将在隔膜电槽内生成三氯化氮(NCl3),当氯气液化时,三氯化氮积累过多会引起爆炸,故应在饱和盐水中加入少量的次氯酸盐,使转变为可挥发的一氯胺(H2NCl).精制盐水中含有10~15ppm的有效氯,会使氨含量降低到1ppm的安全范围之内.将一次精制盐水再经过滤和螯合树脂吸附,进行二次精制,控制钙、镁含量在0.05ppm以下,才能用于离子膜电槽.电解隔膜法(图1)、水银法(图2)、离子膜法(图3)的电解原理基本相同,即:食盐水溶液在直流电作用下,阴离子在阳极上发生氧化反应,阳离子在阴极上发生还原反应.前者称为阳极过程,后者称为阴极过程.阳极过程在上述各种方法中,阳极过程的主要反应为氯离子被氧化成为氯气:2Cl-→Cl2+2e-在25℃、0.1MPa的中性饱和食盐水溶液中,析氯反应的平衡电极电位为+1.33V.它随氯化钠浓度和温度的降低而增大.溶液中的水分子也可在阳极上氧化并生成氧气,成为与析氯反应相竞争的主要副反应:2H2O→O2+4H++4e-或4OH-→O2+2H2O+4e-在上述条件下,析氧反应的平衡电极电位为+0.82V,所以,阳极上析氧反应比析氯反应容易进行.由于电解槽在很大的电流下工作,偏离平衡条件很远,实际电极电位与平衡电极电位并不相等,其差值即为该电极反应在具体放电条件下的过电位.有些相互竞争的反应,由于过电位的不同而改变实际的放电反应顺序.工业上电解食盐水溶液时的阳极过程就属于这种情况.在不同的电极材料表面,析氧反应和析氯反应的过电位也不同,有时相差很大.如在生产中应用的钌-钛金属阳极表面,电流密度为1000~5000A/m2时,析氧反应的实际电极电位要比析氯的高0.25~0.30V(在石墨阳极上高出0.10V左右).因此,实际的阳极过程主要是析氯,而不是析氧.提高电解液中氯离子浓度,控制阳极液pH以降低氢氧离子浓度,并采用较高的电流密度等措施,也都可以增大析氧和析氯反应的电极电位差,有利于抑制析氧反应,而提高氯气纯度和电流效率.阳极析出的氯部分地溶解在阳极液中,生成次氯酸和盐酸.当阴极生成的氢氧化钠,由于扩散或搅动等原因进入阳极液中时,次氯酸被中和,生成易解离的次氯酸盐.而解离出的次氯酸离子(ClO-)则可在阳极氧化,生成氯酸盐并逸出氧气:6ClO-+3H2O→2ClO3-+4Cl-+6H++3/2O2+6e-此反应随阳极液中氢氧离子和次氯酸离子的增多而加剧.结果是既消耗电解产物氯和氢氧化钠,又降低电流效率和产品纯度.加大盐水中氯化钠浓度或提高电解液温度,可以降低氯气的溶解度和次氯酸离子的浓度.而将阳极和阴极的电解产物妥善分开,则是氯碱工业中有效地进行电解过程的关键.隔膜法、水银法和离子膜法就是隔离两极产物的不同方法.阴极过程电解氯化钠水溶液的阴极过程,随所用阴极材料而异.一般条件下,钠离子还原成金属钠的反应很难进行,所以在隔膜法(或离子膜法)中所用的固体阴极(如铁阴极)表面上,其阴极过程为水分子还原析出氢气,同时在阴极附近形成氢氧化钠溶液:2H2O+2e-→H2+2OH-在25℃,电解液含氢氧化钠100g/L、氯化钠180g/L,以及氢的分电解反应的理论分解电压为阳极与阴极的电极电位之差,因此,25℃时隔膜电解槽的理论分解电压为:采用不同的阴极材料,析氢和析钠的电极电位有很大不同.例如:在水银法汞阴极上,由于析氢反应的过电位比析钠的高得多,而析出的钠又容易与汞形成钠汞齐,这样更有利于钠离子的还原,其在汞阴极上反应主要是:Na++e-+xHg→NaHgx将电解槽中生成的钠汞齐引出,进入加有水的解汞槽中,钠汞齐与水反应,生成氢氧化钠溶液和氢,即NaHgx+H2O→Na++OH-+1/2H2↑2+xHg这是水银法和隔膜法主要不同之处.水银法可制得氯化钠含量极低的高纯度、高浓度的氢氧化钠溶液.水银法的电解槽中以汞为阴极,石墨或金属为阳极.解汞槽中以钠汞齐为阳极,石墨为阴极,在碱液中阴阳两极相互接触,组成短路电池以加速汞齐分解.这时钠汞齐中的金属钠作为阳极而溶解,水则在石墨阴极表面还原而析出氢.解汞反应中释放出来的化学能尚难加以利用,因而水银法的电耗比隔膜法高.水银电解槽的槽电压约比隔膜电解槽高1V左右,它相当于解汞反应的分解电压.盐水中钙、镁、铁以及钒、钼、钛、锰等重金属离子含量过高时,也会在汞阴极上还原,生成不稳定的汞齐和汞渣,降低析氢过电位,导致析出氢气并妨碍汞的正常流动.因此水银法电解对盐水的质量要求较高.产品精制包括碱液浓缩、氯气液化和氢气的处理.碱液浓缩隔膜法电解槽生产的碱液(阴极液)含有NaOH10~12%和NaCl16%左右,需要经过蒸发(一般采用三效或四效逆流强制循环蒸发器),用间接蒸汽加热以蒸发水分,于是碱液浓缩并使溶解度较小的氯化钠结晶出来,由盐浆离心机将回收盐分出后,作为盐水重饱和或化盐之用.有的以地下盐水为原料的氯碱厂,利用回收的固体食盐作为水银法的原料,构成隔膜法与水银法并存的氯碱厂.浓缩的碱液经冷却至常温,再滤去析出的细盐晶粒,即为液体烧碱商品.隔膜法制得的50%的氢氧化钠通常含有1.0~1.2%氯化钠,可利用水合法或采用液氨萃取法,均可使盐的含量降低到500ppm以下,因为过程复杂,能耗较高,实际生产中较少应用.水银法电解槽可以直接生产50%氢氧化钠,经过活性炭层除去悬浮的水银微粒,即可作为商品.离子膜法电解槽能生产约35%氢氧化钠的高纯度碱液,可直接作为商品使用,也可再经蒸发器浓缩为50%液体烧碱.氯气的液化从各种电解槽阳极室逸出的氯气,经水喷淋直接冷却,或在钛冷却器内间接冷却,再在串联的干燥塔内用浓硫酸干燥,得到原料氯气;然后进一步压缩在液化器内冷却成为液氯.氢气处理氢气经冷却脱水后作为燃料,或再经干燥压缩贮入钢瓶(或经管道)作为工业原料.。
氯碱 工艺流程
氯碱工艺流程
氯碱工艺是指通过电解盐水或盐酸溶液制取氯气、氢气和氢氧化钠的过程。
氯碱工业是化工工业中的重要分支,广泛应用于化肥生产、食品加工、制药、纺织、造纸等领域。
下面是一个典型的氯碱工艺流程。
首先,盐水制备。
氯碱工艺的原料是食盐,通常用食盐和水按一定比例溶解得到盐水溶液,通常浓度在15-20%之间。
然后,盐水预处理。
盐水中常含有杂质如镁离子、硫酸根离子等,这些杂质会对电解过程产生负面影响,因此需要进行预处理。
预处理方法包括硫酸加入法、硫酸镁法、高锰酸钾法等。
接下来,电解。
盐水经过预处理后进入电解槽,电解槽是氯碱工艺的关键设备。
电解槽通常采用钢制容器,容器内分为阳极和阴极两部分,中间设有隔膜。
盐水进入阳极侧,经过电解产生氯气和氢气,同时在阴极侧产生氢氧化钠。
电解反应方程式如下:
2Cl- → Cl2↑ + 2e-
2H2O + 2e- → H2↑ + 2OH-
然后,氯气和氢气的分离。
电解槽产生的氯气和氢气需要通过分离装置分离开来。
氯气可以通过压力差等原理得到,而氢气则需经过压缩和纯化处理。
最后,氢氧化钠生产。
氢氧化钠是氯碱工艺的主要产品之一,是一种重要的化学原料。
电解槽生成的氢氧化钠溶液会经过过
滤、浓缩等处理,然后进行蒸发浓缩,最终得到固体氢氧化钠。
总之,氯碱工艺是通过电解盐水或盐酸溶液制取氯气、氢气和氢氧化钠的过程。
它是化工工业中的重要分支,具有广泛的应用价值。
通过盐水制备、盐水预处理、电解、氯气和氢气的分离以及氢氧化钠生产等步骤,可以实现氯碱工艺的有效运行。
氯碱工业 工艺流程
氯碱工业工艺流程氯碱工业是指以氯、氢、氧为原料生产氯气、氢气、氢氧化钠、氯化钠等产品的一类工业。
氯碱工业的主要工艺流程包括电解氯法和电解氢氧化钠法。
电解氯法是氯碱工业的主要生产方法之一。
首先,将氯化钠(NaCl)溶解在水中,得到氯化钠溶液。
然后,将氯化钠溶液导入电解槽中,电解槽中有一对电极,即阳极和阴极。
通电后,电解槽中的氯化钠溶液开始电解分解。
在电解过程中,阳极上发生氧化反应,生成氯气(Cl2),而阴极上发生还原反应,生成氢气(H2)。
氯气和氢气随着电解过程分别在阳极和阴极处收集。
同时,电解槽中的溶液中的氯化钠逐渐消耗,再生成氢氧化钠(NaOH)。
在阳极处,氧化反应使得氯离子(Cl-)失去电子,变为氯气。
在阴极处,还原反应使得水中的氢离子(H+)接受电子,变为氢气。
氯气和氢气采集后可分别用于制取消毒剂和化学原料。
电解氢氧化钠法是氯碱工业的另一种常用生产方法。
首先,将氯化钠溶解在水中,得到氯化钠溶液。
然后,将氯化钠溶液导入电解槽中,电解槽中有一对电极,即阳极和阴极。
通电后,电解槽中的氯化钠溶液开始电解分解。
在电解过程中,阳极上发生氧化反应,生成氯气(Cl2),而阴极上发生还原反应,生成氢气(H2)。
氯气和氢气随着电解过程分别在阳极和阴极处收集。
与电解氯法不同的是,电解氢氧化钠法在电解槽的中间还额外放入一个隔膜,用于分隔阳极和阴极两侧的溶液。
隔膜的作用是阻止氯离子和氢氧化钠生成的氢氧根离子(OH-)相遇,从而使得电解槽的阳极侧为氯气,阴极侧为氢气。
电解槽中的溶液在电解过程中逐渐消耗,生成氢氧化钠(NaOH)。
氯气和氢气采集后可分别用于制取消毒剂和化学原料。
总结来说,氯碱工业的工艺流程主要包括电解氯法和电解氢氧化钠法。
通过这两种工艺,可以生产出氯气、氢气、氢氧化钠等多种产品,广泛应用于化工、制药、环保等领域。
氯碱生产工艺流程 (1)
7
三氯化氮
液
<-40
<-71
(7)
助燃
易爆
甲
60g/t
8
氯化钡
晶
965
1560
(8)
(15)
注:⑴强烈的刺激和腐蚀性。
⑵对皮肤粘膜等组织有强烈的刺激和腐蚀作用。
⑶对眼睛和呼吸道粘膜有刺激作用。
⑷高浓度引起窒息。
⑸对眼睛和呼吸道粘膜有刺激作用。
⑹对呼吸道粘膜有刺激。
⑺对呼吸道、眼和皮肤有强烈刺激。
330
(2)
助燃
乙
Ⅱ
2
(10)
3
盐酸
液
-114.8纯
108.6
20%
(3)
Ⅱ
15
(11)
4
H2
气
400
-259.2
-252.8
(4)
4.1%~74.1%
易燃
易爆
甲
(12)
5
Cl2
气
-101
-34.5
(5)
助燃
易爆
乙
Ⅱ
1
(13)
6
氨
气
651
-77.7
-33.5
(6)
15.7%~
27.4%
易燃
易爆
乙
Ⅵ
30
二合一盐酸工艺流程简图:
Cl2高温
H2 HCL气体
地沟排空
8.漂液工序工艺流程简述:
用手推车将石灰运入石灰池,配制成规定浓度的石灰乳,靠位差流入反应池,循环泵将反应池中石灰乳抽出送入喷射器,在喷射器中与来自氯处理或液氯工序的Cl2混合共同进入反应器生成次氯酸钙,反应液经循环泵多次循环喷射提高有效氯浓度,当有效氯达到规定要求则由循环泵送高位槽,在高位槽中经沉清后转入产品槽,经产品泵送用户运输车。
- 1、下载文档前请自行甄别文档内容的完整性,平台不提供额外的编辑、内容补充、找答案等附加服务。
- 2、"仅部分预览"的文档,不可在线预览部分如存在完整性等问题,可反馈申请退款(可完整预览的文档不适用该条件!)。
- 3、如文档侵犯您的权益,请联系客服反馈,我们会尽快为您处理(人工客服工作时间:9:00-18:30)。
氯碱生产工艺流程总述永祥树脂有限公司生产系统是由氯碱系统,PVC系统,三氯氢硅系统,及公用系统组成。
公用系统又包括水,电,汽。
水,电,汽的正常供应是确保生产平稳运行的关键。
这里我就谈谈氯碱系统的生产流程。
永祥树脂有限公司的氯碱系统是由电解,盐水,氯氢,液氯,冷冻,盐酸,漂液,蒸发,循环水组成的系统。
其主要流程是盐水生产的精盐水经电解生成主要成分是NaoH,NaCl的电解液和氯气,氢气三种物质。
电解液由蒸发经浓缩,并分离其中的NaCl,加水溶解后供盐水工序生产精盐水用。
NaoH经冷却沉降后,送成品桶作为成品销售。
氯气在氯氢工序通过洗涤冷却,干燥,压缩输送到液氯,盐酸,PVC,三氯氢硅。
氯碱片区主要是送液氯和盐酸。
氯气在液氯经冷冻送来的-35℃冷冻盐水液化为液氯,液氯尾气送盐酸和漂液生产盐酸和漂液用。
氢气是经氯氢工序洗涤冷却,压缩输送到PVC,三氯氢硅,盐酸。
氯碱片区送盐酸,在合成炉与氯气燃烧生成氯化氢气体,经水吸收后生成成品盐酸供销售出售。
液氯尾气在漂液生产池中与石灰水生成漂液供销售出售。
氯碱车间工艺流程简述一.氯碱车间基本概况1.自然条件:氯碱车间位于公司的东部,西部为乙炔车间,南部为聚合乙烯车间,西南为氯乙烯车间,东西向220米,南北向220米。
人员构成:员工212人,其中管理人员18人,一般员工194人,倒班员工为168人。
最高气温39℃,最低气温约0℃,平均气温16.5—18℃。
平均风速为0.5—2.0米/秒。
2.生产装置规模:最初设计能力为1万吨/年隔膜碱,正式投产时间1990年,经过多次技改扩产,产量达到约9万吨/年隔膜碱。
3.氯碱车间工艺特点:车间压力容器较多,压力控制要求高;工艺介质为有毒有害物质。
二.工艺流程简述:1.电解工序工艺流程简述:符合工艺要求的精制盐水由盐水工序送入精盐水贮槽,用精盐水泵送入高位槽,自流入盐水预热器,加热至80℃±2℃后注入电解槽内,当供给直流电后,盐水进行电化学反应,在阳极室生成的氯气和在阴极室生成的氢气分别送往氯氢工序处理,阴极室生成的电解碱液断电后经管道流入电解液集中槽,用泵送至蒸发工序。
电解工艺流程简图:直流电氢气ﻩ泵ﻩ冷凝水2.氯处理工序工艺流程简述:电解生产70-85℃的湿氯气,经氯气洗涤塔用工业水洗涤后,进入Ⅰ段钛冷却器用工业水冷却,再进入Ⅱ段钛冷却器用+5℃盐水进一步冷却到12-15℃,然后进入泡沫干燥塔、泡罩塔用硫酸干燥,干燥后的氯气经过酸雾捕集器后用氯气压缩机压缩输送到各用氯岗位。
氯气处理工艺流程简图:ﻩﻩ3.氢气处理工艺流程简述:电解生产80℃的湿氢气经Ⅰ段、Ⅱ段氢气洗涤塔用工业水洗涤后,送氢气压缩机加压后经过Ⅰ段氢气冷却器用工业水对其进行冷却,再进入Ⅱ段氢气冷却器用+5℃盐水进行冷却到12℃,经过水捕雾器进入氢气分配台至各用氢单位。
氢气处理工艺流程简图:ﻩa.单级氨压机工艺流程:由高压液氨贮槽出来的液氨压力13.765绝压,温度+35℃,经蒸发器氨节流阀绝热节流膨胀后进入氨蒸发器的螺旋管内进行蒸发,螺旋管内的液氨吸收NaCl冷冻盐水的热量,液氨在等温等压下蒸发成气氨,使蒸发器内的NaCl盐水温度降至+5℃,由盐水泵输送给使用部门。
0℃的气氨经管路吸收环境的热量过热至+10℃进入单级氨压机,绝热压缩经油分离器分离油后,气氨进入氨冷凝器,在等温等压下的气氨把热量传给冷却水转走,而气氨冷凝成液氨进入液氨贮槽,循环使用。
单级制冷工艺流程简图:b. 双级氨压机工艺流程:由高压液氨贮槽出来的液氨,压力13.765绝压,温度+35℃,分两部分分别进入中间冷却器:一部分经氨节流阀绝热节流膨胀后进入中间冷却器,产生低温-9℃的气氨,冷却低压级出来的气氨。
另一部份高压液氨通过中间冷却器的蛇管进行再冷却,冷却至-2—--4℃的高压液氨,经蒸发器氨节流绝热节流膨胀后进入氨蒸发器的螺旋管内进行蒸发。
螺旋管内的液氨吸收CaCl2冷冻盐水的热量,液氨在等温等压下蒸发成气氨,使蒸发器外的CaCl2冷冻盐水冷却至-35℃,由盐水泵输运给使用部门。
-40℃的气氨经氨液分离器,过热至-35℃进入双级氨压缩机低压级进口。
经低压级压缩进入中间冷却器分离油、氨后,冷却至-2—-7℃的气氨进入高压级,经绝热压缩后的高压气氨经油分离器分离油后,进入氨冷凝器在等温等压下的气氨把热量传给冷却水移走,而气氨冷凝成液氨进入液氨贮槽,循环使用。
双级制冷工艺流程简图:c. 螺杆式压缩机工艺流程:3#氢处理冷冻站采用蒸汽压缩式冷冻机,以下各部份组成一个闭合的循环系统:蒸发器,压缩机,冷凝器和节流阀。
如下图所示:1 / 1--制冷剂(工质)R 22按图中箭头方向依靠螺杆式压缩机的抽吸和压缩,周而复始地循环,,在冷凝器中冷凝放热交替变换物理状态(使用普通循环水冷却液化),R 22本身在经节流后在蒸发器中膨胀吸热,蒸发器内的冷媒水温度降至+5℃,经过冷媒水桶由冷媒水泵输送给使用部门。
6.液氯工序工艺流程简述:由氯氢工序送来的干燥氯气经氯气除沫器进入列管式氯气液化气与-35℃的冷冻盐水逆流换热进行液化,液氯进入液氯贮槽,计量后送液氯充装岗位,液气尾气送后续尾气岗位。
氯气液化工艺流程简图: 尾氯含氢4% 由来去用尾氯岗位 的氯气>80%7.盐酸工艺流程简述:由氯氢处理送来的氢气、氯气以及液氯工段送来尾氯分别经缓冲罐,阻火器进入二合一炉的灯头燃烧生成氯化氢气体,经过雨淋管冷却后由块孔石墨冷却器进一步冷却,再进入降漠吸收塔用稀酸吸收成>31%的浓盐酸进入中转槽。
未被吸收的气体进入尾气吸收塔工业水吸收得到6%左右的稀酸由快孔石墨冷却器冷却后进入降漠吸收塔,仍未被吸收塔吸收的气体用喷射泵抽至排空槽放入地沟,不凝气体经阻火器放空。
二合一盐酸工艺流程简图:高温HCL三.主要危险有害因素分析:1.主要原料、中间产品、产品数量及理化性质、危险危害特性见表1、表22.危险危害特性:表2主要原料、中间产品、产品理化数据及注:⑴强烈的刺激和腐蚀性。
⑵对皮肤粘膜等组织有强烈的刺激和腐蚀作用。
⑶对眼睛和呼吸道粘膜有刺激作用。
⑷高浓度引起窒息。
⑸对眼睛和呼吸道粘膜有刺激作用。
⑹对呼吸道粘膜有刺激。
⑺对呼吸道、眼和皮肤有强烈刺激。
⑻吸入含入引起急性中毒。
⑼第8.2类碱性腐蚀品。
⑽第8.1类酸性腐蚀品。
⑾第8.1类酸性腐蚀品。
⑿第2.1类易燃气体。
⒀第2.3类有毒气体。
⒁第2.3类有毒气体。
⒂第6.1类毒害品。
3.危险危害因素分析:由表1和表2可见,烧碱和液氯生产过程中的主要物料氢气易燃易爆,具有火灾爆炸危险性,氯气、氨气、烧碱、盐酸、硫酸和氯化钡具有毒物危害性,烧碱、盐酸、硫酸、氯气和氯化钡具有较强腐蚀性,三氯化氮具有助燃爆炸性。
结合工艺生产的特点及操作特性,可知隔膜电解装置的主要危险有害因素是火灾爆炸危险性和化学品泄漏造成的多人中毒、呛伤、灼伤危害。
液氯生产过程主要危险有害因素是氯气泄漏、氨气泄漏造成的多人中毒危险性,其次是氯气与氢气、氨气的易燃易爆及设备(汽化器、钢瓶)爆炸。
四.事故危险源:依据生产单元的危险性程度确定如下危险性较大的生产单元为事故危险源。
见表3 危险生产单元依据工艺操作条件及处理物质的危险程度,确定如下危险设备为事故危险源见表4危险生产设备重大事故发生后应急处理预案1.事故报警:当发生突发性危险化学品泄漏或火灾爆炸事故时,现场人员应在保护好自身安全的情况下,及时确认事故发生的部位,并向当班主任报告,逐级报告各有关部门。
报警过程中应着重说明事故发生的地点、时间、泄漏的化学品名称及泄漏量、事故性质、危险程度及有无人员伤亡及报警者姓名和联系电话。
2.紧急疏散:突发泄漏发生后,根据危险化学品泄漏的扩散情况及火焰辐射热所涉及到的范围建立警戒区,并在通往事故现场的主要干道实行交通管制。
警戒区边界有警示标志,并有专人警戒,如氯气小量泄漏,隔离150m,氯气大量泄漏,隔离450m。
除消防及应急处理人员(穿好个体防护服、防护器具)外,其他人员禁止进入警戒区。
泄漏的化学品为易燃品时,事故警戒区内严禁火种。
迅速将警戒区内与事故应急处理无关人员撤离。
如果泄漏的化学品有毒时,需佩戴个人防护用品,并有相应的监护措施。
撤离时应向上风向转移,有专人引导,并在撤离的线路上设立标志,指明方向。
最后查清是否有人留在污染区与着火区。
各生产单元有两个以上畅通无阻的紧急出口,并标有明显标志。
3.现场急救:发生后,受伤者应积极采取自救措施。
救援人员在做好自身保护的同时,尽快帮助受伤者脱离事故现场,积极进行救治。
本装置可能泄漏的化学品具体中毒救治措施见表5 可能泄漏的化学品的危险特性、中毒症状和其他伤害救护措施4.泄漏控制:装置发生泄漏事故时,迅速查明泄漏点和原因,凡能经切断气源或做倒槽(罐)等处理措施而消除事故的,以自救为主,如泄漏本单位不能控制,车间会同有关部门及领导,视泄漏情况能否得到控制做出局部或全部停车决定。
如需紧急停车,即由公司调度协调迅速执行。
间主要设备、管线、容器等泄漏后的控制措施见表6。
表6可能泄漏的设备等处理方法行泄漏控制过程中,应急处理人员必须配备必要的个人防护用具,如泄漏化学品为易燃、易爆的,严禁携带火种。
应急处理时严禁单独行动,应2~3人采取集体行动,要有监护人,必要时用水枪或水炮掩护。
处理应在调度指挥下进行,通过关闭有关阀门、停止作业或通过采取改变工艺流程、物料走副线、局部停车、打循环、减负荷运行等办法来控制或消除泄漏的化学品量。
泄漏被控制后,及时将现场泄漏物进行处理,防止二次事故的发生。
5. 泄漏化学品处置方法:设备管线发生泄漏后,应采取措施修补或消除泄漏化学品。
本车间可能泄漏化学品的处置方法见表7。
表7 可能泄漏的化学品的处置方法6.火灾控制:火灾,在报警的同时,组织力量根据不同性质的物质燃烧采取相应灭火措施。
在火灾尚未扩大到不可控制之前,使用适当的移动式灭火器来控制火灾,迅速关闭发生火灾部位的上游阀门。
切断进入火灾事故地点的一切物料,然后立即启用现有的各种消防设备、器材扑灭初期火灾和控制火源,火势较大时,由消防队来扑灭。
电气设备着火:断电灭火:扑救方法与一般火灾扑救相同。
带电灭火:用不导电的灭火剂:CO2、“1211”、干粉等,灭火人员戴绝缘手套和穿绝缘靴,水枪喷嘴装接地线时可以用喷雾水灭火,对有油的电气设备,也可用干燥的黄砂盖住火焰。
7.事故抢修:事故得到控制后,汇报车间应根据实际情况对设备、厂房等进行修复,检修工作应按轻重缓急适当安排工作量和工作进度,检修完毕后,要经安全确认无误,符合开车条件方可投入运行。
8.事故调查:事故发生后,应立即进行事故原因分析,对于事故调查应按以下几个方面进行: 严格遵守事故调查程序,配合上级主管部门的工作;在抢修的同时就开始事故现场的初步勘查,尽量收集能够证明事故原因的各种材料依据;组织有关人员进行事故原因分析,确定事故的直接原因和间接原因,确定事故责任者;组织相关的材料向上级汇报或存档。