CA6140车床刀具温度单片机控制系统设计
车床CA6140主轴系统的数控化改造及仿真毕业设计
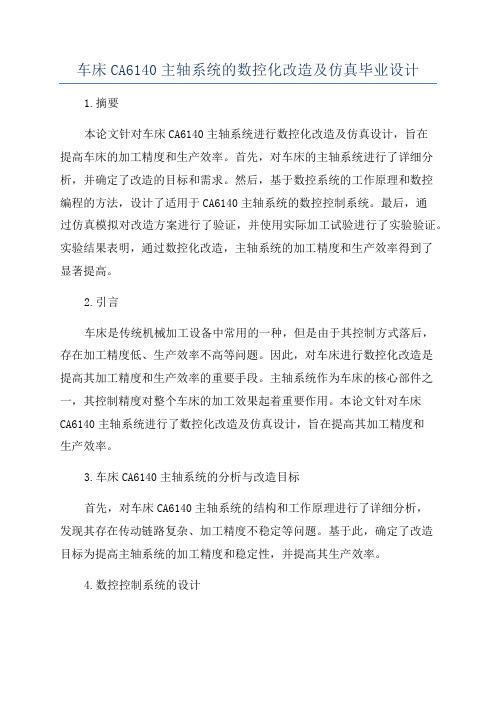
车床CA6140主轴系统的数控化改造及仿真毕业设计1.摘要本论文针对车床CA6140主轴系统进行数控化改造及仿真设计,旨在提高车床的加工精度和生产效率。
首先,对车床的主轴系统进行了详细分析,并确定了改造的目标和需求。
然后,基于数控系统的工作原理和数控编程的方法,设计了适用于CA6140主轴系统的数控控制系统。
最后,通过仿真模拟对改造方案进行了验证,并使用实际加工试验进行了实验验证。
实验结果表明,通过数控化改造,主轴系统的加工精度和生产效率得到了显著提高。
2.引言车床是传统机械加工设备中常用的一种,但是由于其控制方式落后,存在加工精度低、生产效率不高等问题。
因此,对车床进行数控化改造是提高其加工精度和生产效率的重要手段。
主轴系统作为车床的核心部件之一,其控制精度对整个车床的加工效果起着重要作用。
本论文针对车床CA6140主轴系统进行了数控化改造及仿真设计,旨在提高其加工精度和生产效率。
3.车床CA6140主轴系统的分析与改造目标首先,对车床CA6140主轴系统的结构和工作原理进行了详细分析,发现其存在传动链路复杂、加工精度不稳定等问题。
基于此,确定了改造目标为提高主轴系统的加工精度和稳定性,并提高其生产效率。
4.数控控制系统的设计根据数控系统的工作原理和数控编程的方法,设计了适用于CA6140主轴系统的数控控制系统。
首先,选取了适合主轴系统控制的数控设备,并设计了相应的控制算法和程序。
然后,对数控编程进行了详细设计,并使用仿真软件进行了仿真验证。
5.改造方案的仿真与验证为了验证改造方案的有效性,使用仿真软件对其进行了仿真模拟。
首先,建立了CA6140主轴系统数学模型,并将其运行参数与改造后的数控控制系统进行了耦合。
然后,通过调整控制系统的参数,对加工过程进行了仿真模拟,并对加工结果进行了分析和评估。
最后,使用实际加工试验进行了实验验证,并与仿真结果进行了对比分析。
6.结论通过车床CA6140主轴系统的数控化改造及仿真设计,本论文有效提高了主轴系统的加工精度和生产效率。
CA6140数控车床改造设计说明书

设计题目:CA6140车床的数控化改造专业:设计者:指导老师:年月日摘要普通机床的经济型数控改造主要是在合理选择数控系统的前提下,然后再对普通车床进行适当的机械改造,改造的内容主要包括:(1) 床身的改造,为使改造后的机床有较好的精度保持性,除尽可能地减少电器和机械故障的同时,应充分考虑机床零部件的耐磨性,尤其是机床导轨。
(2) 拖板的改造,拖板是数控系统直接控制的对象,所以对其改造尤显重要。
这中间最突出一点就是选用滚珠丝杠代替滚动丝杠,提高了传动的灵敏性和降低功率步进电机力矩损失。
(3) 变速箱体的改造,由于采用数控系统控制,所以要对输入和输出轴以及减速齿轮进行设计,从而再对箱体进行改造。
(4) 刀架的改造,采用数控刀架,这样可以用数控系统直接控制,而且刀架体积小,重复定位精度高,安全可靠。
通过对机床的改造并根据要求选用步进电机作为驱动元件,这样改造后的机床就能基本满足现代化的加工要求。
关键字:普通车床数控改造步进电机经济型数控系统数控刀架一绪论我国数控机床的研制是从1958年开始的,经历了几十年的发展,直至80年代后引进了日本、美国、西班牙等国数控伺服及伺服系统技术后,我国的数控技术才有质的飞跃,应用面逐渐铺开,数控技术产业才逐步形成规模。
由于现代工业的飞速发展,市场需求变的越来越多样化,多品种、中小批量甚至单件生产占有相当大的比重,普通机床已越来越不能满足现代加工工艺及提高劳动生产率的要求。
如果设备全部更新替换,不仅资金投入太大,成本太高,而且原有设备的闲置又将造成极大的浪费。
如今科学技术发展很快,特别是微电子技术和计算机技术的发展更快,应用到数控系统上,它既能提高机床的自动化程度,又能提高加工精度,所以最经济的办法就是进行普通机床的数控改造。
机床数控化改造的优点:(1)改造闲置设备,能发挥机床原有的功能和改造后的新增功能,提高了机床的使用价值,可以提高固定资产的使用效率;(2)适应多品种、小批量零件生产;(3)自动化程度提高、专业性强、加工精度高、生产效率高;(4)降低对工人的操作水平的要求;(5)数控改造费用低、经济性好;(6)数控改造的周期短,可满足生产急需。
毕业设计_CA6140车床电气控制线路设计
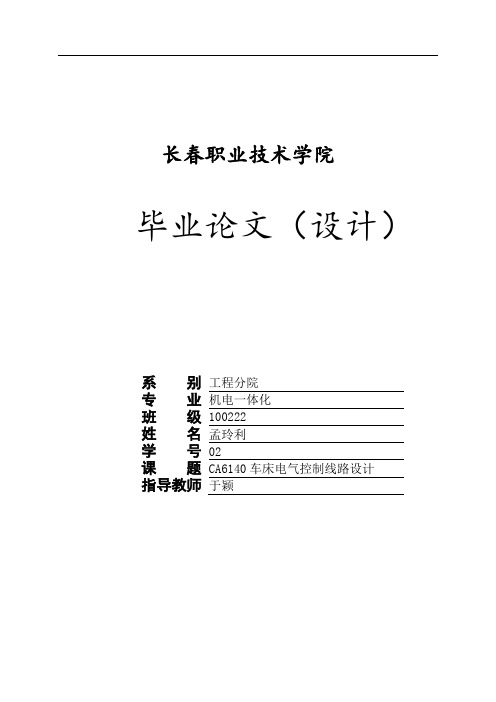
3.2.2主轴电动机M1的控制
SB1是红色蘑菇型的停止按钮,KM1线圈通电吸合并自锁,KM1的主触点闭合,主轴电动机M1启动运转。按一下SB1,接触器KM1断电释放,其主触点和自锁触点都断开,电动机M1断电停止运行。
控制要求:由手动操作控制
(3)运动形式:工件的夹紧与放松
控制要求:由手动操作控制
(4)运动形式:加工过程的冷却
控制要求:冷却泵电动机和主轴电动机要实现顺序控制,冷却泵电动机也不需要正反转和调速
2.4 电动机型号:
主轴电动机M1 Y132M-4-B3380V15.4A7.5KW1450r/min
冷却泵电动M2AOB-25380V 0.32A90W3000 r/min
【关键词】 CA6140 机床 控制线路
1.CA6140车床的主要功能、结构及型号意义
1.1主要功能:CA6140车床是一种应用极为广泛的金属切削机床,能够车削外圆、内圆、端面、螺纹、切断及割槽等,并可以装上钻头或铰刀进行钻孔和铰孔等。
1.2型号意义:如图1-1
图1-1CA6140车床型号意义
2. CA6140卧式车床的主要运动形式及控制要求
2.1主运动
运动形式:主轴通过卡盘或顶尖带动工件的旋转运动:
控制要求:
(1)主轴电动机选用三相笼型异步电动机,不进行调速,主轴采用齿轮箱进行机械有级调速
(2)车削螺纹时要求主轴有正反转,一般由机械方法实现,主轴电动机只作单向旋转
CA6140车床数控化改造设计解析
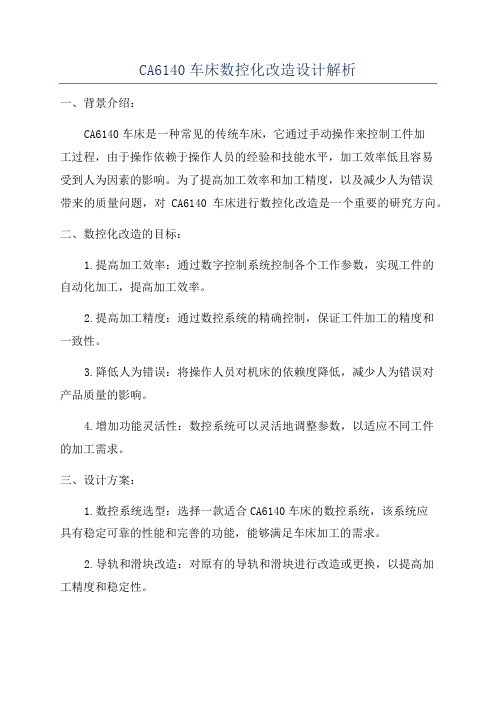
CA6140车床数控化改造设计解析一、背景介绍:CA6140车床是一种常见的传统车床,它通过手动操作来控制工件加工过程,由于操作依赖于操作人员的经验和技能水平,加工效率低且容易受到人为因素的影响。
为了提高加工效率和加工精度,以及减少人为错误带来的质量问题,对CA6140车床进行数控化改造是一个重要的研究方向。
二、数控化改造的目标:1.提高加工效率:通过数字控制系统控制各个工作参数,实现工件的自动化加工,提高加工效率。
2.提高加工精度:通过数控系统的精确控制,保证工件加工的精度和一致性。
3.降低人为错误:将操作人员对机床的依赖度降低,减少人为错误对产品质量的影响。
4.增加功能灵活性:数控系统可以灵活地调整参数,以适应不同工件的加工需求。
三、设计方案:1.数控系统选型:选择一款适合CA6140车床的数控系统,该系统应具有稳定可靠的性能和完善的功能,能够满足车床加工的需求。
2.导轨和滑块改造:对原有的导轨和滑块进行改造或更换,以提高加工精度和稳定性。
3.主轴改造:对原有的主轴进行改造或更换,以提高转速控制的精度和可靠性。
4.伺服电机安装:在车床的各个轴向上安装伺服电机,由数控系统控制其运动,以实现自动化加工。
5.完善的自动化装置:设计并安装自动换刀装置、自动送料装置等,以提高加工效率和减少人为操作。
6.编程软件开发:根据数控系统的特点,开发适合CA6140车床的编程软件,以便操作人员能够方便地进行程序编写和调整。
7.操作界面设计:设计一个简洁明了的操作界面,方便操作人员进行监控和调整。
四、预期效果:1.加工效率提高:数控系统实现了工件的自动化加工,大大提高了加工效率,减少了人为操作的时间。
2.加工精度提高:通过对各个工作参数的精确控制,加工精度得到了显著的提高。
3.缩短交期:由于加工效率提高,交货期可以相应缩短,提高了客户的满意度。
4.减少人为错误:数控系统的自动化控制减少了人为错误的可能性,提高了产品的质量稳定性。
20-基于PLC的CA6140型普通车床控制系统改造PPT模板

年月日
组长 签字
年月 日
教师 签字
年月 日
电气控制与PLC控制基础理论
查找相关知识并学习,该项目任务知识能力 掌握程度
任务工作计划编写规范、认真、详实,计划 符合项目任务要求
对项目任务制定详细的实施方案,并且做出 的方案决策科学、准确
任务实施记录详实、准确、规范
基于PLC的CA6140型普通车床控制系统改造 任务完成质量高低,是否符合技术规范
对项目任务完成过程和完成质量评价公正、 合理、科学、详实
是否符合职业规范、是否违反安全文明操作 规程
团队组织、团队协作能力和协作情况,语言 交流表达规范
合计
配分 10 10 10 10 40 10 5 5 100
学生自 评
小组互 评
教师考核
考核标准(续)
项目 成绩
学生 自评
学生自评30% +小组互评30% +教师考评40%
小组 评价
教师 评价
学生 签字
图X4-27 控制系统电路(一)
图X4-28 控制系统电路(二)
图X4-29 DC24V直流电源接线图
任务实施的工作要点
3、PLC控制系统设计 (3)PLC梯形图设计 PLC梯形图设计如图X4-30所示。
图X4-30 PLC梯形图
任务实施的工作要点
4、安装电源等 安装FX2N-16MR PLC,DC 24 V直流电源、DC 24 V隔离继电器,并贴上醒目的文字和符号。 5、按设计的电路图完成控制系统的配线和接线 进行配线接线时所有接线端都要使用冷压接线端头牢固连接,接线端子号要标注,连接导线全部要 用异型号码管编号。 6、连接总电源线 即连接L1,L2,L3进线端、零线N、地线PE,接线端要使用冷压接线端头,连接要牢固、可靠。 7、电气线路检测 借助万用表,对连接好的电气线路进行检测。电气线路检测无误后才能试运行。 8、指令程序的传输 使用GX Developer(或三菱FXGP/WIN-C)编程软件绘制图X4-30所示的PLC梯形图,并进行转 换和PLC程序传输。也可使用FX-20P型手持式编程器进行程序传输。
CA6140普通车床数控化改造设计
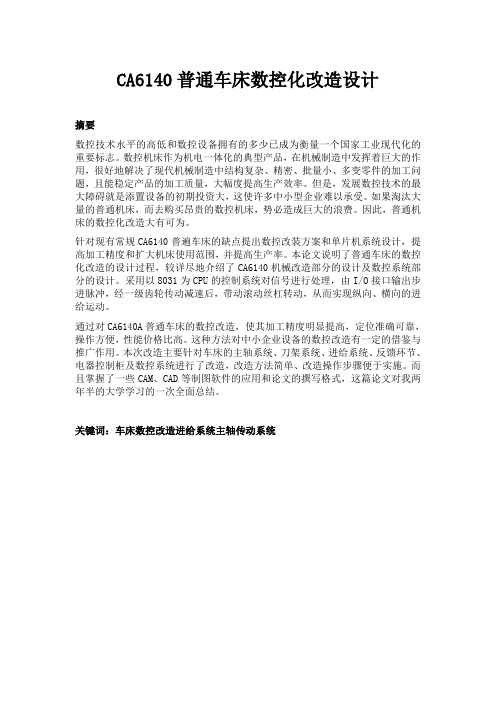
CA6140普通车床数控化改造设计摘要数控技术水平的高低和数控设备拥有的多少已成为衡量一个国家工业现代化的重要标志。
数控机床作为机电一体化的典型产品,在机械制造中发挥着巨大的作用,很好地解决了现代机械制造中结构复杂、精密、批量小、多变零件的加工问题,且能稳定产品的加工质量,大幅度提高生产效率。
但是,发展数控技术的最大障碍就是添置设备的初期投资大,这使许多中小型企业难以承受。
如果淘汰大量的普通机床,而去购买昂贵的数控机床,势必造成巨大的浪费。
因此,普通机床的数控化改造大有可为。
针对现有常规CA6140普遍车床的缺点提出数控改装方案和单片机系统设计,提高加工精度和扩大机床使用范围,并提高生产率。
本论文说明了普通车床的数控化改造的设计过程,较详尽地介绍了CA6140机械改造部分的设计及数控系统部分的设计。
采用以8031为CPU的控制系统对信号进行处理,由I/O接口输出步进脉冲,经一级齿轮传动减速后,带动滚动丝杠转动,从而实现纵向、横向的进给运动。
通过对CA6140A普通车床的数控改造,使其加工精度明显提高,定位准确可靠,操作方便,性能价格比高。
这种方法对中小企业设备的数控改造有一定的借鉴与推广作用。
本次改造主要针对车床的主轴系统、刀架系统、进给系统、反馈环节、电器控制柜及数控系统进行了改造,改造方法简单、改造操作步骤便于实施。
而且掌握了一些CAM、CAD等制图软件的应用和论文的撰写格式,这篇论文对我两年半的大学学习的一次全面总结。
关键词:车床数控改造进给系统主轴传动系统目录引言.................................................... 错误!未定义书签。
1.绪论................................................ 错误!未定义书签。
1.1数控机床优势概述.............................................. - 2 -1.2车床数控改造的现状与国内背景.................................. - 6 -1.3车床数控改造的必要性与可行性.................................. - 8 -2车床数控改造的总体构思与技术方案.................................. - 9 -2.1设计任务...................................................... - 9 -2.2总体方案的论证................................................ - 9 -2.3总体改造方案的确定........................................... - 10 -2.6机械部分的改造............................................... - 10 -2.7数控部分的改造............................................... - 11 -3普通车床主要结构的数控改造....................................... - 11 -3.1数控系统..................................................... - 11 -3.2纵向(Z向)进给系统的改造 ................................... - 13 -3.3横向(X向)进给系统的改造 ................................... - 17 -3.4刀架......................................................... - 18 -3.5主轴传动系统与滑动导轨副的改造............................... - 18 -3.6编码器....................................................... - 19 -4光栅尺安装与调试................................................. - 20 -4.1光栅尺的安装................................................. - 20 -4.2光栅尺的校正................................................. - 20 -5参考点的建立..................................................... - 20 -6如何提高数控机床精度?精度不够如何改进? ........................... - 21 -7结论............................................................. - 23 -引言数控机床作为机电一体化的典型产品,在机械制造业中发挥着巨大的作用,很好的解决了现代机械制造中结构复杂,精密,批量小,多变零件的加工问题,且能稳定产品的和、加工质量。
C6140型车床PLC控制系统设计与装调
C6140型车床PLC控制系统设计与装调
一.C6140型车床控制功能分析
(一)车床运动形式
1.主运动主轴通过卡盘带动工件旋转。
2.进给运动溜板箱把丝杠或光杠的转动传递给刀架部分。
3.辅助运动刀架的快速移动
(二)电气控制电路
二.PLC控制系统硬件电路设计
1.主电路设计
2.控制电路设计
3.元器件清单
元件名称
符号
型号格
数量
功能
隔离开关
QS
HZ15-63/3
1
线路主电源控制
熔断器
FU1
RL1-60/40
3
主线路短路保护
接触器
KM1
CJ20-25/380V
1
主轴电机控制
CA6140车床电气控制改造PLC控制 (2)
CA6140车床电气控制改造PLC控制系统1绪论1.1设计目的及意义20世纪初,由于电动机的出现,使得机床的拖动发生了变革,用电动机代替蒸汽机,机床的电气传动随电动机的发展而发展。
电气传动的控制方式亦经历了一个从低级到高级的发展过程。
最初采用手动控制。
最早的自动控制是20世纪20、30年代出现的继电接触器控制,它可以实现对控制对象的起动、停车、凋速、自动循环以及保护等控制。
它所使用的控制器件结构简单、价廉、控制方式直观、易掌握、工作可靠、易维护,因此在机床控制卜得到长期、广泛的应用。
它的缺点是体积大、功耗大、控制速度慢、改变控制程序困难,由于是有触点控制,在控制复杂时可靠性降低。
为了解决复杂和程序可变控制对象的需要,在20世纪60年代出现了顺序控制器。
它是继电器和半导体元件综合应用的控制装置,具有程序改变容易、通用性较强等优点,广泛用于组合机床、自动线上。
随着计算技术的发展,又出现了以微型计算机为基础的具有编程、存储、逻辑控制及数字运算功能的可编程控制器PLC【1】。
1.2CA6140的现状CA6140是一种应用广泛的金属切削机床,目前采用传统的继电器控制的普通车床在中小型企业任大量使用。
能够车削外圆、内圆、螺纹、螺杆等,它采用继电器接触器电路来实现电气控制系统。
但由于大量的使用了继电器与接触器,再加上继电器系统接线复杂,经常造成接触不良,而且原件老化快,设备故障频繁,不便于维修,故障诊断与排除困难,并存在:(1)触电容易被电弧烧坏而导致接触不良(2)机械方式实现的触点控制反映速度慢(3)继电器的控制功能被固定在线路中,功能单一、灵活性差影响到实际的生产运用。
因此当务之急就是对ca6140车床进行技术改造,以提高企业的设备利用率,提高产品的质量和产量。
11.3设计内容根据设计条件,采用可编程控制器(PLC)对原有继电接触器控制系统进行改造,使机床故障率下降,可靠性和灵活性大大的提高,实现一定的自动化,具体设计要求如下:(1)按下启动按钮SB3,主轴电机M1控制接触器得电,主轴电机启动起来(2)按下停止按钮SB4,主轴电机M1控制接线器失电,主轴电机停止(3)主轴电机启动后,搬动冷却泵电机手动控制开关SB10致闭合位置,冷却泵电机控制继电器KA得电,冷却泵电机启动起来(4)主轴电机启动后,搬动冷却泵电机M2手动控制开关SB10致断开位置,冷却泵电机控制继电器失电,冷却泵电机停止(5)按下点动控制按钮SB12,进刀电机M3控制继电器得电,进刀电机启动运行(6)按下点动控制按钮SB12,进刀电机M3控制继电器失电,进刀电机停止工作(7)过载、短路保护热继电器FR1\FR2任何一个触电断开,接触器KM1、继电器KM2断电,所以电机停止工作2.CA6140车床电气PLC改造方案设计设计要求:1)主轴电机M1先启动,有过载保护,主轴电机M1能控制整个线路的启动和停止2)冷却泵电机M2实现电动和常动,有过载保护,冷却泵电机能独立的启动和停止3)进刀电机M3能独立的启动和停止2.1CA6140车床电气控制原理2.1.1 电气控制原理根据电气传动的要求,由接触器KM1、KM2、KM3分别控制电动机M1、M2、M3,具体电路图如图2-1所示。
学习情境一__CA6140车床控制系统
(二)工作原理
控制过程: 主电路: 合上开关QS→控制回路接上电源 控制回路: 1.电机起动:
5)选用原则
1) 接触器的类型选择 根据接触器所控制负载的轻重和负载电流的类型,
来选择交流接触器或直流接触器。 (2) 额定电压的选择 接触器的额定电压应大于或等于负载回路的电压。 (3) 额定电流的选择 接触器的额定电流应大于或等于被控回路的额定
电流。
2、按钮
按钮是一种结构简单,使用广泛的手动主令电器,在控制电路中 作远距离手动控制电磁式电器用,也可以用来转换各种信号电路和电气 联锁电路等。
5)低压断路器的图形符号和文字符号
图1-10 低压断路器的图形符号和文字符号
二、电气控制线路的绘制
(一)电气控制线路的组成 电气控制线路由以下两部分组成
(二)电气控制线路有三种绘制形式
1、电气原理图
以三相笼型异步电机的起停控制线路为例 说明其绘制原则。见图1-11。
(1)电气原理图中,一般主电路和控制电路分为 两部分画出。主电路通常用粗实线画在图样的左 侧(或上方)。控制和辅助电路一般用细实线画在图 样的右侧(或下方)。控制电路、辅助电路要分开画。 辅助电路是指设备中的信号和照明部分。
学习情境一 CA6140车床控制系统
学习情境一 CA6140车床控制系统
子情境一
子情境二
子情境三 子情境四
三相笼型异步电动机的起停控 制线路 两台电动机顺序起动控制线路 及长动与点动的联锁控制线路 CA6140车床控制线路 PLC基本知识及CA6140车床的 PLC改造
CA6140普通车床进行数控改造设计(全套图纸)
目录一、绪论1.1 引言.............................. (1)1.2机床数控改造的目的.......................... (2)1.3数控系统的产生和发展....................... .. (2)1.3.1数控系统的出现和发展 (2)1.3.2数控系统的发展趋势 (2)1.4CA6140的数控改造............... . (4)1.4.1数控系统的选择 (4)1.4.2CPU和存储器 (5)1.4.3I/O接口线路 (6)1.4.4其他部件的选择 (6)二、数据参数的选择及其计算2.1 纵向进给系统的设计计算............. (7)2.1.1选择脉冲当量 (7)2.1.2计算切削力 (7)2.1.3 滚珠丝杠螺母副的计算和选型 (8)2.1.4齿轮及步进电机的有关计算 (10)2.2横向进给系统的设计计算 (12)2.2.1 切削力计算 (12)2.2.2滚珠丝杠设计计算 (12)2.2.3齿轮及步进电机的有关计算 (14)2.3 自动刀架的设计 (15)2.3.1刀架的回转和选位................... . (16)2.3.2减速机构的设计计算..................... (17)2.3.3蜗杆传动的设计计算..................... (20)2.3.4螺旋升降装置的设计计算 (23)三、数控系统硬件电路设计3.1概述............................ . . . (27)3.2单片机控制系统设计 (28)3.2.1主要技术特性及硬件配制 (28)3.2.2存储空间的分配 (28)3.2.3 I/O地址分配 (28)3.2.4单片机部分电路设计图如图纸所示 (29)3.2.5光电隔离电路 (29)3.2.6功率放大电路 (29)3.2.7其他辅助电路........................... (30)四、软件设计部分4.1概述................................. . . . . (30)4.2总体方案设计 (31)4.3插补方法的确定 (31)4.4进给控制字FCW的设置 (33)致谢 ............................... . (34)参考文献 (35)一、绪论1.1引言随着社会生产和科学技术的迅速发展,机械产品的性能和质量不断提高,产品的更新换代也不断加速,因此对机床不仅要求具有较高的精度和生产率,而且应能迅速地适应产品零件的变换。
- 1、下载文档前请自行甄别文档内容的完整性,平台不提供额外的编辑、内容补充、找答案等附加服务。
- 2、"仅部分预览"的文档,不可在线预览部分如存在完整性等问题,可反馈申请退款(可完整预览的文档不适用该条件!)。
- 3、如文档侵犯您的权益,请联系客服反馈,我们会尽快为您处理(人工客服工作时间:9:00-18:30)。
CA6140车床刀具温度单片机控制系统设计当今社会上各种机械加工业都在迅猛发展,车床是机械加工核心工具,随着科学技术的发展,车床也在不断向着高精度、高效率、高自动化方向发展,数控车床已经成为主流设备,逐渐取代老旧的普通车床。
我国目前机床总量约400余万台,但其中数控机床总数只有20余万台,机床的数控化率极低。
国内起步较晚,技术较为落后,有着大量的老旧车床,又因其缺乏专业的维修与保养,促使机床的工作精度大大降低。
而从国外购置新型数控车床的价格又颇为昂贵,普通企业根本无法负担。
在机械制造业中, 虽然已发展出各种不同的零件成型工艺, 但目前仍有90% 以上的机械零件是通过切削加工制成。
在切削过程中, 机床作功转换为等量的切削热, 这些切削热除少量逸散到周围介质中以外, 其余均传入刀具、切屑和工件中, 刀具、工件和机床温升将加速刀具磨损, 引起工件热变形, 严重时甚至引起机床热变形。
因此,在机床的切削加工过程当中,对切削温度的测量非常重要。
在高速车床当中,为了提高车床加工精度,刀具在切削过程中的受热变形一定要控制住,这个仅仅知道刀具温度是不够的,还需要引入自动控制技术进行实时控制。
本论文以CA6140普通车床为研究对象,根据数控技术原理,运用了单片机应用技术、自动控制技术和测试传感器技术,提出了车床刀具温度的控制系统方案。
设计了基于MCS-51单片机的车床刀具温度控制电路和软件。
第一章绪论1.1课题的研究背景和研究意义金属切削加工是机械制造中应用最为广泛的加工方式之一。
金属切削加工使用刀具或磨具从工件表面切除多余材料,以实现零件的几何形状、尺寸精度、表面粗糙度和表面层质量。
刀具作为切削过程的直接执行者,在切削加工过程中不可避免地会发生磨损或破损。
刀具磨损或破损会使零件的加工精度下降,零件表面粗糙度及表层质量恶化,严重时将使刀具失去切削能力,甚至危及机床设备。
因为切削热而产生的温度变化是造成刀具磨损,破损的一个重要原因。
切削温度升高后,刀具的磨损量增大,降低了工件的加工精度,这些都是切削过程中不利的一面。
因此有必要研究切削过程中热量的产生和传递的规律,了解刀具中温度的分布状态。
多年来,人们对于切削温度的研究也给予了足够的重视。
但因为切削温度的研究无论是在实验室测量方法还是理论分析上,基本上局限于连续车削和稳定状态下的切削温度的研究。
因此设计一个在线的自动控制的刀具温度控制系统,是防止设备的损坏,工件的报废并保证机床无故障运行的必然手段。
1.2国内外研究现状随着红外温度检测技术的发展,国内外研究人员开始利用红外热辐射法进行非接触式检测刀具或者工件的表面切削温度。
该方法利用红外传感器聚焦于刀具表面的固定位置,然后通过刀具表面的辐射强度检测刀具表面的切削温度,由传热学原理可知,刀具切削区温度的变化会造成刀具表面的切削温度的变化,从而可以通过试验测量刀具表面的切削温度的变化来间接识别刀具的状态[1]。
1.2.1国外研究现状目前研究切削温度一般通过试验测量和理论计算两种方法。
其中,Jehnming Lin[2]先测得铣削被加工表面的温度,然后再利用热传导反求法来推算铣刀的铣削温度。
Sarat[3]利用边界元有限元混合法建立车刀和工件的温度分布的有限元模型,分析出刀具和工件的温度分布情况。
Yahya Dogu 等[4]利用有限元方法建立正交切削过程中刀具的温度分布的有限元模型,同时说明了有限元法比解析法能更好地模拟温度的分布情况。
E. Ceretti 等利用热电偶测量刀具温度,同时利用软件仿真金属车削加工的过程,结合试验测量值进行修正完善仿真的过程。
Fang Du 等在假设切削过程中,刀具和工件的导热系数,比热以及密度稳定的情况下,建立涂层车刀的一维的温度分布的模型,分析出刀具一维温度分布的情况。
Pradip Majumdar 等详细阐述了切削过程中切削热产生的过程,以及第一第二变形区产生的热流密度,明确了切削过程中的刀具的温度分布边界条件,最后建立了刀具的有限元温度分布模型。
Rui Li 等[5]利用斜切削模型计算热流密度,建立钻削过程中钻头的的温度分布的有限元模型,结合试验测量值进行修正完善钻头的温度分布模型,分析出钻头的温度分布情况。
1.2.2国内研究现状国内研究人员对红外测温技术也早已经展开研究,山东大学的王兰[6]利用红外线测温技术,用 PLC做硬件结构,测试 110KV 干式变压器的温度进行实时监控,从而设计出一套包含采集,处理,显示的功能的完整的测温监控系统。
陈东生[7]等利用红外测温仪,快速移动传感器对其工件进行匀速扫描来实现工件温度分布的监控,结果表明能够快速地反应工件温度的分布变化,其精度可达±1℃,满足监控的要求。
赵友权等[8]分析了常低温辐射测量误差和物体发射率的关系,并针对测量过程中的发射率校正做了较详细的分析。
杨巧凤[9,10]等采用红外辐射测量技术对铝合金铣削温度进行了间接的,相似的,直观的测量,通过测得工件表面的相对温度来推导临界铣削速度。
1.3方案背景技术简介1.3.1数控车床数控技术,简称数控(Numerical Control),是利用数字化信息对机械运动及加工过程进行控制的一种方法。
由于现代数控技术都采用了计算机进行控制,因此,也可以称为计算机数控(Computer Numerical Control)。
采用了数控技术进行控制的机床,或者说装备了数控系统的机床称为数控机床。
它是综合应用计算机、自动控制、自动检测及精密机械制造技术等高新技术于一体的典型机电一体化产品,是现代制造技术的基础。
它很好地解决了形状结构复杂、精度要求高、小批量及多变零件的加工问题且能稳定产品的加工质量,降低工人劳动强度,大幅度提高生产效率。
机床控制也是数控技术应用最早、最广泛的领域,因此,数控机床的水平代表了当前数控技术的发展水平和方向。
与普通机床相比,数控机床能够自动换刀、自动变更切削参数,完成平面、回旋面、平面曲线的加工,加工精度和生产效率都比较高,因而应用日益广泛[11]。
1.3.2温度检测的主要方法常用的切削温度测量方法主要有热电偶法、光辐射法、热辐射法、金相结构法等。
传统的温度测量采用的是热电偶方法[12],当两种不同材质组成的材料副(如切削加工中的刀具—工件)接近并受热时,会因表层电子溢出而产生溢出电动势,并在材料副的接触界面间形成电位差(即热电势)。
由于特定材料副在一定温升条件下形成的热电势是一定的,因此可根据热电势的大小来测定材料副(即热电偶)的受热状态及温度变化情况。
采用热电偶法的测温装置结构简单,测量方便,是目前较成熟也较常用的切削温度测量方法。
根据不同的测量原理和用途, 热电偶法又可细分为自然热电偶法、人工热电偶法、半人工热电偶法、等效热电偶法。
然而在实际加工中几乎没有一种工件允许在其内部埋置热电偶,且其热惯性大,响应慢。
金相结构法[13]是基于金属材料在高温下会发生相应的金相结构变化这一原理进行测温的。
但是这种方法的应用范围局限于金属材料制成的刀具,并只能在高温下才能观察到材料明显的组织结构变化;金相结构法的观测和分析的工作量也较大;利用扫描电镜法也存在以下缺点:只能测量600℃以上的高温;样件制作相当繁琐;且为事后破坏性测量,不方便推广应用于加工现场;所确定的切削温度分布状态属于定量分析;设备复杂,技术难度高,实际应用受到一定限制。
光、热辐射法,采用光、热辐射法测量切削温度的原理是: 刀具、切屑和工件材料受热时都会产生一定强度的光、热辐射, 且辐射强度随温度升高而加大, 因此可通过测量光、热辐射的能量间接测定切削温度。
主要分为辐射高温计法、红外照相法、红外热像仪法。
辐射测温传感器不直接与被测物相接触,这样测量传感器不会改变被测对象的温度场分布,也不会受到工作介质的影响,而且不必与被测对象达到热平衡,因此它特别适合于被测物体表面温度的非接触测量。
此外,辐射测温元件的响应时间很短,因而它便于进行动态、瞬态的温度测量。
正是由于辐射测温具有这么多的优点,因此适用于实际加工过程的刀具温度测量。
本论文结合实际加工过程应用选用红外测温方法。
1.4本课题的主要研究内容本论文以CA6140普通车床为研究对象,通过红外测温法测量车床刀具表面温度进行监控刀具状态,同时根据反馈的刀具温度控制切削速度。
主要工作如下:(1)了解CA6140车床结构和运行过程,确定电控系统的控制要求。
(2)总结了刀具状态监控的常用方法和切削温度的常用测量方法,分析了红外测温法的原理,特点以及应用。
(3)提出车床刀具温度控制方案,设计基于单片机MCS-51的温度信号采集电路,包括单片机的最小系统电路、AD转换电路、信号调理电路等。
(4)配合温控系统的硬件电路,设计系统软件,包括监控软件,它是整个控制系统的核心,专门用来协调各执行模块和操作者的关系。
二是执行软件,它是用来完成各种实质性的功能如测量、显示等功能。
1.5本章小结本章在介绍课题背景和研究意义的前提下,重点介绍了红外测温技术的国内外研究现状,并分析了红外测温技术运用在车床刀具温度测量的可行性[14],最后对本课题主要研究内容进行了阐述。
第二章车床结构及系统总体设计方案2.1 CA6140车床简介CA6140普通卧式车床主要由主轴箱、床鞍、刀架部件、尾座、进给箱、溜板箱、床身等部件组成[15]。
如图2.1所示。
图2.1 CA6140普通卧式车床(1)主轴箱。
它固定在机床身的左端,装在主轴箱中的主轴(主轴为中空,不仅可以用于更长的棒料的加工及机床线路的铺设还可以增加主轴的刚性),通过夹盘等夹具装夹工件。
主轴箱的功用是支撑并传动主轴,使主轴带动工件按照规定的转速旋转。
(2)床鞍和刀架部件。
它位于床身的中部,并可沿床身上的刀架轨道做纵向移动。
刀架部件位于床鞍上,其功能是装夹车刀,并使车刀做纵向、横向或斜向运动。
(3)尾座。
它位于床身的尾座轨道上,并可沿导轨纵向调整位置。
尾座的功能是用后顶尖支撑工件。
在尾座上还可以安装钻头等加工刀具,以进行孔加工。
(4)进给箱。
它固定在床身的左前侧、主轴箱的底部。
其功能是改变被加工螺纹的螺距或机动进给的进给量。
(5)溜板箱。
它固定在刀架部件的底部,可带动刀架一起做纵向、横向进给、快速移动或螺纹加工。
在溜板箱上装有各种操作手柄及按钮,工作时工人可以方便地操作机床。
(6)床身。
床身固定在左床腿和右床腿上。
床身是机床的基本支撑件。
在床身上安装着机床的各个主要部件,工作时床身使它们保持准确的相对位置。
2.2系统总体设计方案本次设计采用MCS-51单片机作为控制芯片,采用红外温度传感器采集刀具温度信号[16,17]。
通过红外温度传感器将采集的温度信号转换成与之相对应的电信号,经过放大处理送入A/D转换器进行A/D转换,将模拟信号转换成数字信号送入到控制芯片进行数据处理。