《摩托车轮胎通用技术条件》
摩托车轮胎生产工艺配方技术知识

摩托车轮胎生产工艺及配方、结构技术知识一、摩托车轮胎简介由于橡胶具有其它任何材料所不具有的高弹性和高伸长率的特点,因而在国民经济各部门、国防、宇宙开发、日常生活中得到广泛应用。
摩托车轮胎就是以橡胶为主体的制品之一。
我国在六、七十年代橡胶工业比较落后,摩托车及轮胎都未纳入国家标准,规格品种极少,在上海工业基地,也只是在汽车轮胎生产线上生产军用三轮摩托配用的 3.75-19 、3.25-16 摩托车轮胎。
改革开放后,80 年代随着国民经济的发展,重庆军工单位如嘉陵、建设、平山、望江等军工转民用,开始开发不同规格的摩托车,从而带动了相关配套的摩托车轮胎的生产。
由于摩托车机动、灵活、轻便、快捷,广泛用于交通、通讯、运输、体育和军事等诸多方面,从而以之配套的摩托车轮胎企业,面对市场的需求,使轮胎产品适应其复杂、多变、苛刻的使用条件,必须增加规格品种,扩大生产。
重庆已成为我国重要的摩托车生产基地。
威星公司在这大好形势下,抓住机遇,生产出60多个规格,400多种花色品种的轮胎,给各摩托车生产厂家配套。
为确保轮胎质量,迎得信誉,必须严格按照国家GB51 —1997产品标准生产(包括GB/T12983-1997摩胎系列标准, 主要技术内容等效ISO 标准)。
二、橡胶工业部分名词解释1、橡胶:是一种典型高弹性的材料,它在大的变形下能迅速而有力恢复变形且能够被改性。
2、天然橡胶:是一种以异戊二烯为主要成份的不饱和的天然高分子化合物。
3、合成橡胶:以酒精、电石、石油等作原料,用化学方法制成的合成橡胶。
4、生胶:未经塑炼、混炼的橡胶。
5、塑炼:增加生胶塑性的加工过程。
6、配料:将生胶与配合剂按配方规定称量配好。
7、混炼:通过密炼机将配合剂均匀分散在生胶中的加工过程。
8、弹性:物体在使其变形负荷除去后,仍能恢复其原来形状的性质。
9、可塑度:试样受外力压缩发生变形,当外力除去后,仍保持变形的程度。
10、硬度:试片受外力压缩时,所发生的反抗变形的比值。
摩托车轮胎国家标准

摩托车轮胎国家标准摩托车轮胎是摩托车上的重要部件,直接关系到骑行安全和舒适性。
为了保障摩托车轮胎的质量和安全性能,我国对摩托车轮胎制定了一系列国家标准,以规范摩托车轮胎的生产和质量要求。
首先,摩托车轮胎国家标准规定了摩托车轮胎的尺寸和结构。
摩托车轮胎的尺寸包括轮胎的宽度、断面高度、轮胎胎面的宽度等参数,这些参数的规定旨在确保摩托车轮胎能够适配不同型号的摩托车,并且能够保证骑行的稳定性和安全性。
此外,摩托车轮胎的结构也在国家标准中有所规定,包括轮胎的胎体层数、帘线层数、胎面花纹深度等,这些结构参数的规定旨在确保摩托车轮胎具有足够的承载能力和抓地力,以应对不同路况下的骑行需求。
其次,摩托车轮胎国家标准对摩托车轮胎的质量要求进行了详细规定。
摩托车轮胎的质量要求包括外观质量、物理性能、耐久性能等多个方面。
其中,外观质量要求主要包括轮胎表面的缺陷、气泡、气孔等情况,以及轮胎的标识和标志的要求;物理性能要求主要包括轮胎的承载能力、抗侧滑性能、耐磨性能等参数;耐久性能要求主要包括轮胎的耐老化性能、耐疲劳性能等。
这些质量要求的规定旨在确保摩托车轮胎在使用过程中能够保持稳定的性能,具有较长的使用寿命,并且能够在不同路况下保持良好的抓地力和操控性能。
最后,摩托车轮胎国家标准还对摩托车轮胎的检验方法和标志进行了规定。
摩托车轮胎的检验方法主要包括外观检验、物理性能检验、耐久性能检验等内容,这些检验方法的规定旨在确保摩托车轮胎生产过程中能够进行全面、科学的检验,以保证产品质量。
同时,摩托车轮胎的标志规定包括产品标识、生产日期标识、质量合格证标识等内容,这些标志的规定旨在方便消费者了解产品信息,确保产品质量可追溯。
总的来说,摩托车轮胎国家标准的制定,对于保障摩托车轮胎的质量和安全性能具有重要意义。
只有严格遵守国家标准的要求,摩托车轮胎生产企业才能够生产出质量可靠、安全耐用的产品,为广大摩友提供更加可靠的骑行保障。
同时,消费者在购买摩托车轮胎时,也应该选择符合国家标准要求的产品,以确保自身骑行安全和舒适性。
摩托车车轮及轮辋认证规则

产品性能认证规则CQC 16‐499416‐2010摩托车车轮及轮辋认证规则Performance Certification Rules for Motorcycle Wheels and Steel Rim2010年8月16日发布 2010年8月16日实施中国质量认证中心前 言本规则由中国质量认证中心制定、发布,版权归中国质量认证中心所有,任何组织及个人未经中国质量认证中心许可,不得以任何形式全部或部分使用。
本规则代替CQC/RY091-2003《自愿性产品认证特殊要求 摩托车和轻便摩托车轮辋》和CQC/RY092-2003 《自愿性产品认证特殊要求 摩托车和轻便摩托车用轻合金车轮》。
主要变化为规定证书有效期为5年;依据标准中删除方法标准QC/T 211-1996.GB/T13202-1997换版为GB/T13202-2007,QC/T71-93换版为QC/T71-2009;增加QC/T818-2009、QC/T71-2009。
制定单位:中国质量认证中心。
参与起草单位:南昌摩托车质量监督检验所。
主要起草人:王江东、江源浩、任国勤。
1.适用范围本规则适用于钢制或轻合金制摩托车和轻便摩托车车轮及其轮辋(以下简称车轮或轮辋)的CQC标志认证。
2. 认证模式车轮及轮辋的认证模式为:产品型式试验+初始工厂检查+获证后监督。
认证的基本环节包括:a. 认证的申请b. 型式试验c. 初始工厂检查d. 认证结果评价与批准e. 获证后的跟踪检查f. 复审3.认证申请3.1认证单元划分按认证单元申请认证。
生产场地(工厂)不同,视为不同的认证单元。
在如下方面无显著差异的车轮可划分为一个单元:a.车轮的型式(辐条、辐板或整体式)b.轮辋的型号规格;c.车轮主体材料及加工工艺;d.轮毂的外径尺寸;e.轮辐的形状及尺寸。
在如下方面无显著差异的轮辋产品可划分为一个单元:a.轮辋的型号规格;b.轮辋主体材料及加工工艺;c.车轮的型式(辐条、辐板或整体式)。
摩托车和轻便摩托车轻合金车轮试验方法QCT212-1996
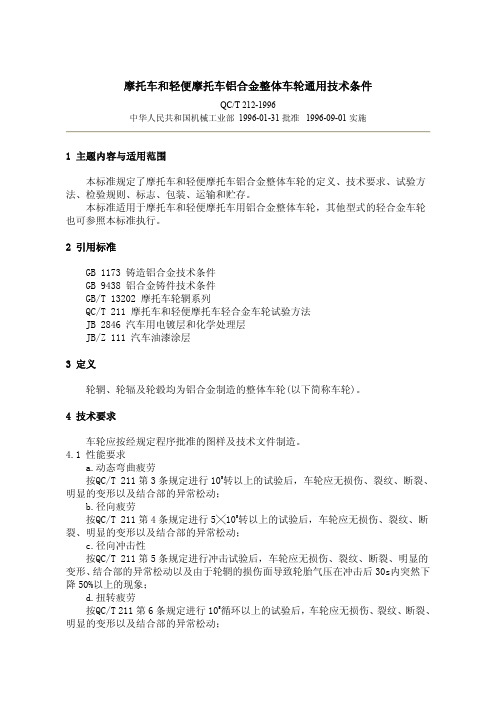
摩托车和轻便摩托车铝合金整体车轮通用技术条件QC/T 212-1996中华人民共和国机械工业部 1996-01-31批准1996-09-01实施1 主题内容与适用范围本标准规定了摩托车和轻便摩托车铝合金整体车轮的定义、技术要求、试验方法、检验规则、标志、包装、运输和贮存。
本标准适用于摩托车和轻便摩托车用铝合金整体车轮,其他型式的轻合金车轮也可参照本标准执行。
2 引用标准GB 1173 铸造铝合金技术条件GB 9438 铝合金铸件技术条件GB/T 13202 摩托车轮辋系列QC/T 211 摩托车和轻便摩托车轻合金车轮试验方法JB 2846 汽车用电镀层和化学处理层JB/Z 111 汽车油漆涂层3 定义轮辋、轮辐及轮毂均为铝合金制造的整体车轮(以下简称车轮)。
4 技术要求车轮应按经规定程序批准的图样及技术文件制造。
4.1 性能要求a.动态弯曲疲劳按QC/T 211第3条规定进行105转以上的试验后,车轮应无损伤、裂纹、断裂、明显的变形以及结合部的异常松动;b.径向疲劳按QC/T 211第4条规定进行5╳105转以上的试验后,车轮应无损伤、裂纹、断裂、明显的变形以及结合部的异常松动;c.径向冲击性按QC/T 211第5条规定进行冲击试验后,车轮应无损伤、裂纹、断裂、明显的变形、结合部的异常松动以及由于轮辋的损伤面导致轮胎气压在冲击后30s内突然下降50%以上的现象;d.扭转疲劳按QC/T 211第6条规定进行105循环以上的试验后,车轮应无损伤、裂纹、断裂、明显的变形以及结合部的异常松动;e.气密性(仅适用于无内胎车轮)按QC/T 211第7条规定进行试验后,车轮在2min之内沿轮辋周边不应有漏气现象。
4.2 尺寸4.2.1 轮辋的型面轮辋的型面尺寸按GB/T 13202。
4.2.2 轮辋的检验周长轮辋的检验周长尺寸按GB/T 13202。
4.2.3 轮辋的径向圆跳动和端面圆跳动按图1。
4.3 外部质量4.3.1 铸件表面质量应参照GB 9438第4.4条的规定执行。
摩托车(电动、三轮)车胎的技术要求

序号
质量特性
备注
试装
1
与钢圈装配过程中无难装配及难充气现象
试
装
2
装配后轮胎左右晃动不得大于1.8mm;
跳动不得大于1.5mm
路
试
1
A试验速度40±5KM/H
B试验温度(地表温度)50±5OC
C刹车距离8----12米
D载荷230±5kg
F轮胎气压280kpa
1、强制路试耐磨耗试验
后轮应不应低于100次
5
耐久试验
依国家标准
6
高速性能
依国家标准
7真空胎气密性
充汽压力为外胎标示压力的120%,剥去胎侧外层全部胎侧胶,放置48小时气压损失不得超过10%。
2、内胎:
项目
序号
质量特性
备注1
外
观
外观
外观整洁,无破损、裂纹、凹坑不平等缺陷
尺
寸
1
内胎胎管(天然胶料)厚度≥1.0mm
丁基胶内胎胎管厚度≥0.8mm
2Hale Waihona Puke 距离相等的四个同一方向部位,胎管胶料厚度相差不得大于0.2mm
性
能
气密性
将内胎充入适量的气压后,使其体积为原来的150%后浸入水中无气泡产生
与钢圈、外胎装配好后,充入1.5倍额定气压(依外胎标示为准)后停放3天,
气压损失不得大于10%
抗拉强度
高档内胎抗拉强度≥13.5MPa(天然胶)
非高档内胎≥9MPa(天然胶),
丁基胶≥6MPa
扯断
伸长率
高档内胎(天然胶)≥620%,
非高档内胎则≥450%
丁基胶≥650%
接头强度
高档内胎(天然胶)≥9mpa,
摩托车通用技术条件
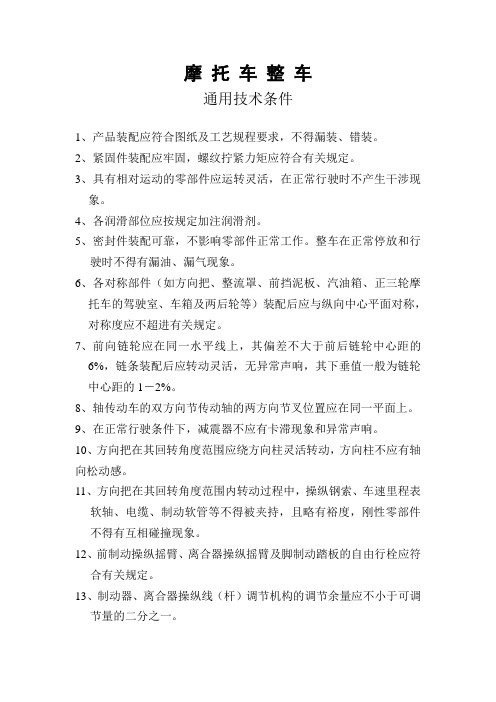
摩托车整车通用技术条件1、产品装配应符合图纸及工艺规程要求,不得漏装、错装。
2、紧固件装配应牢固,螺纹拧紧力矩应符合有关规定。
3、具有相对运动的零部件应运转灵活,在正常行驶时不产生干涉现象。
4、各润滑部位应按规定加注润滑剂。
5、密封件装配可靠,不影响零部件正常工作。
整车在正常停放和行驶时不得有漏油、漏气现象。
6、各对称部件(如方向把、整流罩、前挡泥板、汽油箱、正三轮摩托车的驾驶室、车箱及两后轮等)装配后应与纵向中心平面对称,对称度应不超进有关规定。
7、前向链轮应在同一水平线上,其偏差不大于前后链轮中心距的6%,链条装配后应转动灵活,无异常声响,其下垂值一般为链轮中心距的1-2%。
8、轴传动车的双方向节传动轴的两方向节叉位置应在同一平面上。
9、在正常行驶条件下,减震器不应有卡滞现象和异常声响。
10、方向把在其回转角度范围应绕方向柱灵活转动,方向柱不应有轴向松动感。
11、方向把在其回转角度范围内转动过程中,操纵钢索、车速里程表软轴、电缆、制动软管等不得被夹持,且略有裕度,刚性零部件不得有互相碰撞现象。
12、前制动操纵摇臂、离合器操纵摇臂及脚制动踏板的自由行栓应符合有关规定。
13、制动器、离合器操纵线(杆)调节机构的调节余量应不小于可调节量的二分之一。
14、操纵开关的指示标记应明显,档位转换应清晰、操作应灵活可靠。
15、电器线路应工作正常,绝缘可靠,电缆布线应紧凑有序,插接件应连接可靠。
16、前大灯位置的调整应符合有关规定。
17、锁装置应安装可靠、灵活,开、关应灵活。
18、复位机构工作灵活、可靠,限位机构工作应可靠。
19、在常温启动未经预热的发动机,脚启动一般不应超过5次,电启动不超过15s。
20、离合器分离应彻底,接合应平顺。
21、发动机在怠速工况下15min内不应自动熄火,发动机工作应均匀。
22、在正常行驶条件下,制动应可靠。
23、涂装件表面应光滑、平整,色泽均匀,装饰表面不允许有明显的流痕、麻坑、桔印、裂痕和漏漆等缺陷,非装饰表面不应有露底和严重的流痕及裂痕等缺陷。
力车轮胎标准
力车轮胎标准
力车轮胎,作为一种广泛应用于自行车、电动车、摩托车等交通工具的零部件,其性能和质量直接关系到车辆的行驶安全。
力车轮胎有多种分类,如按用途可分为公路轮胎、山地轮胎、折叠轮胎等;按结构可分为内胎式轮胎和无内胎轮胎等。
力车轮胎的标准要求包括以下几个方面:
1.尺寸:轮胎尺寸应符合国家标准GB/T 2974-2008《轮胎规格》的规定。
2.压力:轮胎的压力应在规定范围内,以保证轮胎的正常使用寿命和性能。
3.材料:轮胎应使用符合国家标准的优质材料,如天然橡胶、合成橡胶等。
4.外观质量:轮胎外观应无明显缺陷,如裂纹、变形、露胎等。
5.耐磨性能:轮胎在规定条件下进行磨损试验,其磨损程度应符合国家标准。
6.耐压性能:轮胎在规定条件下进行压力试验,其变形和损坏程度应符合国家标准。
在选用力车轮胎时,消费者应根据自身需求和车辆类型选择适合的轮胎。
同时,要定期检查轮胎的磨损、气压等情况,确保轮胎在良好的状态下使用。
在使用过程中,避免长时间高速行驶、急刹车等剧烈运动,以免影响轮胎使用寿命。
我国力车轮胎行业在近年来取得了长足的发展,产品质量和性能不断提升,逐渐满足国内外市场的需求。
随着科技的进步和绿色出行理念的普及,力车轮胎行业将继续朝着环保、节能、智能化的方向发展。
力车轮胎企业应加大研发投入,提高创新能力,以满足市场和消费者的需求。
总之,力车轮胎作为交通工具的重要组成部分,其标准、选用和维护都关系到人们的出行安全。
消费者在选购和使用力车轮胎时,应掌握相关知识,确保自身安全和舒适。
BS5892-3:机车和车辆用整体车轮的技术条件(中文版)
内部资料未经确认如有疑义以原文为准英国标准 BS 5892-3(1992版、2009年第二次修订)铁路机车及车辆用材料第三部分:机车和车辆用整体车轮的技术条件前言 31 适用范围 42 定义 43 买方提供资料 44 钢种和热处理 55 制造 76 制造厂家标识 157 检验 198 检验类型和数量 199 试验方法 2210 试验结果 2211 检验的结论 2412 质保书 2413 运输中的保护 24图1—表4中所用符号(非盘式制动车轮) 13图2—表5中所用符号(盘式制动车轮) 14图3—注油孔 17图4—磨耗到限槽的位置 17图5—不平衡的修正和残余应力测试位置 18图6—车轮上的标记位置 18图7—拉伸试验和冲击试验的取样位置 21图8—布氏硬度测试的位置 21表1—化学成分 5表2—成品分析中主要元素在规定范围内的允许偏差 5表3—热处理条件和机械性能 6表4—整体车轮的加工余量和尺寸公差(非盘式制动) 9表5—整体车轮的加工余量和尺寸公差(盘式制动) 11表6—待装配公差 15表7—最大残余不平衡 15表8—试验类型和数量 20BS 5892的本部分是在钢铁标准委员会的指导下制定的,以代替废除的BS 5892-3:1982。
涉及铁路车辆材料的BS 5892分以下六个部分颁布:第1部分:机车和车辆用轴的技术条件第2部分:锻造和轧制轮心的技术条件第3部分:机车和车辆用整体车轮的技术条件第4部分:锻造和轧制轮箍的技术条件第5部分:镶箍车轮扣环技术条件第6部分:机车和车辆用轮对的技术条件本部分的格式己经作了修改,把以前包括在BS 5892-6部分中的对整体车轮的尺寸公差和表面精度的要求合并到了本部分。
BS 5892的本部分与ISO 1005-6相一致,当然它们不可能等效,它也与UIC 812-3相一致。
BS 5892的第1、2、4、6部分也已作了修改,以保证与本部分的要求相一致。
产品认证:建议本英国标准的用户考虑是否需要在检验和持续监督基础上采用第三方认证,以证明产品符合本英国标准。
摩托车和轻便摩托车轻合金车轮试验方法
摩托车和轻便摩托车轻合金车轮试验方法QC/T 211-1996中华人民共和国机械工业部 1996-01-31批准 1996-09-01实施本标准参照采用ISO 8644-1988《摩托车-轻合金车轮-试验方法》1 主题内容与适用范围本标准规定了摩托车和轻便摩托车轻合金车轮进行动态弯曲疲劳试验,径向疲劳试验、径向冲击试验、扭转疲劳试验和气密性试验的方法。
本标准适用于摩托车和轻便摩托车用轻合金车轮(以下简称车轮)。
2 引用标准GB 522 轮胎静负荷性能测定方法QC/T 212 摩托车和轻便摩托车铝合金整体车轮通用技术条件3 动态弯曲疲劳试验3.1 试验设备当车轮以一恒定转速旋转时,该设备应能在车轮轴心上产生一恒定弯矩。
如图1所示:3.2 试验条件3.2.1 弯矩按下式(1)计算弯矩M,单位:N•m。
•μ•W•r ------------------------(1)M=Sm式中:S—系数,数值等于0.7;mμ—轮胎与地面的摩擦系数,数值等于0.7;W—车轮标定的最大设计载荷,N;r—装有装胎车轮的最大静力半径,m。
按GB 522进行测定。
3.2.2 载荷臂长载荷臂应具备足够的刚度。
其长度的确定,应能使一质量为G的配重正好产生式(1)给定的弯矩M。
3.2.3 弯矩允差试验时,弯矩M允差应为计算值的±5%。
3.3 试验方法将车轮轮辋固定在转盘上,将载荷臂象轮轴安装形式一样固定在车轮上,施加式(1)给定的弯矩M,驱动转盘。
4 径向疲劳试验4.1 试验设备该设备应满足如下要求,如图2所示:a.需具备一直径不小于400mm、宽度大于试验轮胎宽度的转鼓;b.转鼓应以一恒定转速旋转;c.该设备应能向车轮施加一径向载荷,使车轮在一恒定压力下始终与转鼓保持接触。
4.2 试验条件4.2.1 径向载荷按下式(2)计算径向载荷Q,N。
•W ----------------------(2)Q=Sr—系数,数值等于2.25。
摩托车轮胎分类标准
摩托车轮胎分类标准
摩托车轮胎一般根据以下几个方面进行分类:
1.轮胎类型:摩托车轮胎可以分为公路型轮胎、越野型轮胎、
混合型轮胎等。
公路型轮胎适合在平坦的公路上行驶,具有较好的抓地力和操控性能;越野型轮胎适合在非路面、砂石等复杂地形上行驶,具有较好的通过性和抓地力;混合型轮胎则是两者的折中选择,可以适应不同的路况。
2.轮胎尺寸:摩托车轮胎尺寸一般由直径、宽度和扁平比三个
参数来描述,例如120/70-17,其中120表示轮胎宽度(单位
为毫米),70表示扁平比(轮胎高度与宽度的比率),17表
示轮辋直径(单位为英寸)。
不同尺寸的轮胎适用于不同车型和用途。
3.胎纹花纹:轮胎的胎纹花纹也会影响其性能和用途。
常见的
胎纹花纹包括市区型、高速型、花纹型等。
市区型轮胎花纹较为平滑,适合在城市道路上行驶,提供较好的舒适性和操控性;高速型轮胎花纹相对较深,能够提供更强的抓地力和排水性能;花纹型则是一种折中的选择,兼具抓地力和排水性能。
4.材料和结构:摩托车轮胎的材料和结构也会影响其性能和用途。
常见的材料有橡胶和钢丝,而结构则分为斜线式和无内胎式。
斜线式轮胎一般用于摩托车,使用内部胎垫来支撑轮胎;无内胎式轮胎则一般用于电动车和自行车,不需要内部胎垫。
这些分类标准可以帮助骑手选择适合自己用途和需求的摩托车轮胎。
- 1、下载文档前请自行甄别文档内容的完整性,平台不提供额外的编辑、内容补充、找答案等附加服务。
- 2、"仅部分预览"的文档,不可在线预览部分如存在完整性等问题,可反馈申请退款(可完整预览的文档不适用该条件!)。
- 3、如文档侵犯您的权益,请联系客服反馈,我们会尽快为您处理(人工客服工作时间:9:00-18:30)。
Q/ZS 宗申产业集团有限公司企业标准Q/ZSJY 62-2006代替Q/ZSJY 62 -2005摩托车和轻便摩托车轮胎通用技术条件2006-10-21发布2006-10-23实施宗申产业集团有限公司发布前言本标准与Q/ZSJY 62-2005的异同:1 调整了以下指标:——邵尔硬度;——扯断强度;——扯断伸长率;——定伸强度;——永久变形;——阿克隆磨耗;——耐臭氧无龟裂;——外胎的胎面与帘子布层附着力;——接头拉伸强度(A类);——气门嘴胶座与胎身粘合强力;——耐久性试验参数。
2 调整了标准的格式。
本标准由宗申产业集团有限公司标准认证技术委员会提出。
本标准由宗申产业集团有限公司标准认证技术委员会归口管理。
本标准由宗申产业集团有限公司技术中心主任吴健批准。
本标准起草单位:宗申产业集团技术中心。
本标准主要起草人:---。
本标准首次发布时间:2005年8月20日。
本标准备案号:QZSJ/0058。
Ⅰ摩托车和轻便摩托车轮胎通用技术条件1 范围本标准规定了摩托车和轻便摩托车轮胎的材料、要求、试验方法、检验规则、标志、包装、运输及贮存。
本标准适用于摩托车和轻便摩托车轮胎(以下简称“轮胎”)。
2 规范性引用文件下列文件中的条款通过本标准引用而成为本标准的条款。
凡是注日期的引用文件,其随后所有的修改单(不包括勘误的内容)或修订版均不适用于本标准。
然而,鼓励根据本标准达成协议的各方研究是否可使用这些文件的最新版本。
凡是不注日期的引用文件,其最新版本适用于本标准。
GB/T 518-1997 摩托车轮胎GB/T 519-1993 充气轮胎物理机械性能试验方法GB/T 521-2003 轮胎外缘尺寸测量方法GB/T 2828.1-2003 逐批检查计数抽样程序及抽样表(适用于连续批的检查)GB/T 2983-1997 摩托车轮胎系列GB/T 7036.2-1997 冲气轮胎内胎第2部分:摩托车轮胎内胎GB/T 7762-2003 硫化橡胶或热塑性橡胶耐臭氧龟裂静态拉伸试验GB/T 13203-1991 摩托车轮胎强度性能试验方法GB/T 13204-2002 摩托车轮胎高速性能试验方法转鼓法GB/T 13205-1991 摩托车轮胎耐久性能试验方法转鼓法HG/T 2177-1998 轮胎外观质量3 材料3.1 轮胎外胎3.1.1 外胎材料可选用:生胶(包括天然橡胶,顺丁橡胶、丁苯橡胶等合成橡胶,再生胶)。
3.1.2 骨架纤维材料(包括棉纤维、人造丝、尼龙、聚酯、玻璃纤维、钢丝等)以及炭黑和填充物等。
3.2轮胎内胎内胎材料可选用:a) 天然橡胶及天然橡胶并用胶内胎(简称“A类”);b) 丁基橡胶及丁基橡胶并用内胎(简称“B类”)。
4 要求4.1 规格、尺寸和基本参数4.1.1 轮胎外胎的规格、尺寸和基本参数应符合GB/T 2983-1997的规定;其中新胎尺寸公差:a) 断面宽度为±4%;b) 外直径为±1%。
4.1.2 轮胎内胎规格应符合GB /T 518-1997的规定。
4.2 安全性能4.2.1 强度性能轮胎外胎强度性能见表1。
但当有下列情况之一者,允许表1中数值的60%作为下限值:a)当胎体骨架材料为棉或人造丝帘线的斜交轮胎;b)当半球型压头达到轮辋而所有测定点胎体均未被破坏,所测定值未达到表1中规定指标值时。
4.2.2 高速性能轮胎外胎经高速试验后,其外观应无脱层、裂口、掉块、帘线断裂、爆破、胎面接头脱开等缺陷。
4.2.3 耐久性能轮胎外胎经耐久性试验后,其外观应无胎面、胎侧、帘布层、胎圈之间的脱层、帘线断裂、帘布层裂缝到达下层帘线、胎面接头脱开、胎面或胎侧胶掉块及龟裂等缺陷。
4.3 轮胎外胎物理机械性能4.3.1 轮胎外胎物理机械性能见表2。
4.3.2 附着力外胎的胎面与帘子布层附着力应≥8.5 kN/m,轮胎外胎的帘子层间附着力应≥7 kN/m。
4.4轮胎内胎的物理机械性能轮胎内胎物理机械性能见表3。
4.5 外观4.5.1 胎面磨耗标志每条轮胎外胎应沿周向等距离地3个以上能观察到花纹沟的剩余深度为0.8mm的标志(当轮胎花纹磨至胎面磨耗标志时,不得继续使用)。
且标志应正确、清晰,不易脱落。
4.5.2 内胎外观应符合GB/T 7036.2-1997中4.4的规定。
4.5.3 轮胎外胎不应有各部件间脱层、海绵状、钢丝圈上抽和断裂、多根帘线断裂、胎里帘线起褶楞和胎冠出胶边帘线等严重影响使用寿命的缺陷。
垫带外形不应有残缺和带身裂开。
4.5.4 轮胎外胎的根须长度应<1mm。
4.5.5 轮胎外胎和垫带的其他外观应符合HG/T 2177-1998的规定。
5 检验规则5.1 出厂检验5.1.1出厂检验由制造厂质量检验部门负责进行,检验合格后应附有产品检验合格证。
5.1.2 出厂检验检验项目为4.1.1、4.1.2、4.3.2、4.5。
5.1.3 出厂检验未检项目,制造厂应提供相应的检验报告,并保证符合本标准的规定。
5.2 入厂检验5.2.1 入厂检验由验收方质量检验部门负责,检验合格后方能入厂。
5.2.2 入厂检验检验项目为4.1.1、4.1.2、4.3.2、4.5。
5.2.3 入厂检验GB/T 2828.1-2003规定的正常一次抽样方案进行,其检查水平(IL)为II级,接受质量限(AQL)为1.0。
5.3 型式检验5.3.1 有下列情况之一时,应进行型式检验:a) 新产品或老产品转厂生产的试制定型检验;b) 正式生产后,如结构、材料、工艺有较大改变,可能影响产品性能时;c) 停产一年后,恢复生产时;d) 累计产量达10000条或每生产半年时;e) 收货方有特殊要求时;f) 国家质量监督机构提出型式检验要求时。
5.4.2 型式检验项目为第4章规定的全部项目。
5.4.3 做型式检验的轮胎应从入厂检验的同批产品中随机抽取,其样本数为4件;先按入厂检验项目进行复检,复检合格后再进行型式检验。
5.4.4 型式检验应全部符合本标准的规定;若有不合格项目时,应重新加倍抽取样件就不合格项目进行复检;若仍不合格,则判该批轮胎为不合格品。
6 试验方法6.1 轮胎外胎充气后的外直径和断面宽度按GB/T 521-1993的规定进行。
6.2 轮胎外胎的强度性能按GB/T 13203-1991的规定进行。
6.3 轮胎外胎的高速性能按GB/T 13204-2002的规定进行。
6.4 轮胎外胎的耐久性能按GB/T 13205-1991的规定进行,具体参数见表5。
6.5 轮胎外胎物理机械性能按GB/T 519-1993的规定进行,其中耐臭氧试验按GB/T 7762-2003的规定进行。
6.6 外胎的胎面与帘子布层附着力按GB/T 519-1993的规定进行。
6.7 轮胎外胎的帘子层间附着力按GB/T 519-1993的规定进行。
6.8 轮胎内胎物理机械性能按GB/T 7036.2-1997 的规定进行。
6.9 轮胎外观及标志用目力观察及通用量具测量。
7 标志、包装、运输和贮存7.1 标志在每条轮胎上应模刻下列标志,其标志应在装上轮辋后仍可见:a)规格、商标或制造厂名;b)层级、骨架材料;c)最大负荷与相应气压;d)标准轮辋;e)速度级标志(公制系列轮胎);f)TUBELESS(无内胎轮胎);g)行驶方向记号(轮胎花纹有行驶方向的轮胎);h)胎面磨耗标志位置的“△”型标记;i)生产日期及批号;j)其它相关文件规定的标志。
7.2 包装将内胎装在外胎内,并向内胎中充以适量空气,使之与外胎内壁相接触,再以绳捆2处以上。
7.3 运输7.3.1 运输途中应避免日晒雨淋。
7.3.2 运输途中应防止轮胎遭受机械损伤。
7.3.3轮胎运输中应避免与油类、易燃及化学腐蚀等物品混装。
7.4 贮存7.4.1 轮胎应贮存在室温为-15°C~35°C、相对湿度不大于80%的室内。
7.4.2 轮胎应贮存在离地面200mm的垫板或货架上,并不应靠墙,并应垂直直径向堆放,堆码应不超过3层,堆垛上不应放置其他物品,每4个月至少倒垛一次。
7.4.3轮胎不应与油类、易燃及化学腐蚀等物品贮放在一起,并应远离热源。
7.4.4 轮胎正常储存条件下,储存期(自出厂日期起)为1年,1年内轮胎仍应符合本标准的规定。
《摩托车和轻便摩托车轮胎通用技术条件》企业标准编制:校对:审核:审定:标准化:批准:宗申产业集团有限公司技术中心2006年10月《摩托车和轻便摩托车轮胎通用技术条件》企业标准编制说明1 任务来源针对轮胎实物与Q/ZSJY 62-2005《摩托车轮胎通用技术条件》存在的差异而修订本标准。
2 标准编制依据本标准参照了Q/ZSJY 62-2005《摩托车轮胎通用技术条件》和相关试验数据。
3 本标准主要内容说明本标准完成讨论稿的编制后,集团技术中心曾组织由轮胎制造厂、摩托车制造公司、集团技术中心参加的标准审查会;由于与会代表对标准讨论稿中涉及的指标参数的值存在较大的分歧,因此会议一致决定,轮胎制造厂分别送两种规格的轮胎,由技术中心(检测中心)进行全性能检测,再根据检测结果确定标准讨论稿中的指标参数。
参数确定后,集团技术中心再次组织相关单位进行会审,与会代表提出了部分修改意见,且被采纳,从而完成了标准报批稿的编制。
本标准与Q/ZSJY 62-2005《摩托车轮胎通用技术条件》的异同:——将邵尔硬度A由65±5 调整为60±5;——将扯断强度由≥15 MPa 调整为≥16 MPa;——将扯断伸长率由≥480% 调整为≥400%;——将300%定伸强度由≥6.5 MPa调整为≥8MPa;——将永久变形由≤28% 调整为≤25%;——将阿克隆磨耗由≤0.3 cm3(1.61 km)调整为≤0.18 cm3(1.61 km);——将耐臭氧无龟裂由72h无龟裂调整为3h无裂纹、8小时不断裂;——将外胎的胎面与帘子布层附着力由8kN/m 调整为8.5kN/m;——将接头拉伸强度(A类)由≥8.3MPa调整为≥6.5MPa;——将气门嘴胶座与胎身粘合强力(A类、断面>3.00)由≥150N/m 调整为≥3.5kN/m,(A类、断面≤3.00)由≥150N调整为≥400N ,(B类、断面>3.00和断面≤3.00)由≥150N调整为≥300N。
——耐久性试验参数:(80km/h,4h)负荷率由110% 调整为100%,,(80km/h,6h)负荷率由130% 调整为110%,(80km/h,24h)负荷率由150% 调整为115%。
4贯彻标准的要求与措施摩托车轮胎应严格按本标准的规定进行检验及验收,从而提高产品质量,在竞争激烈的市场中立于不败之地。
《摩托车和轻便摩托车轮胎通用技术条件》企业标准企业标准起草小组2006年10月6。