线束DFMEA浅析
DFMEA(Design Failure Mode and Effects Analysis,设计失效模式及后果分析)

DFMEA出自 MBA智库百科(/)DFMEA(Design Failure Mode and Effects Analysis,设计失效模式及后果分析)目录[隐藏]• 1 什么是DFMEA• 2 DFMEA基本原则• 3 DFMEA与PFMEA的关系• 4 形式和格式(Forms and Formats)• 5 我们应在何时进行设计失效模式及后果分析?• 6 我们应在什么时间进行设计失效模式及后果分析?•7 我们应在什么时间进行设计失效模式及后果分析?•8 我们应在什么时间进行设计失效模式及后果分析?•9 由谁进行设计失效模式及后果分析?•10 怎样进行设计失效模式及后果分析?•11 怎样进行设计失效模式及后果分析?•12 怎样进行设计失效模式及后果分析?•13 怎样进行设计失效模式及后果分析?•14 DFMEA的案例分析[1]o14.1 实施DFMEA存在的困难o14.2 实施DFMEA的准备工作o14.3 实施DFMEA的流程•15 相关条目•16 参考文献[编辑]什么是DFMEADFMEA是指设计阶段的潜在失效模式分析,是从设计阶段把握产品质量预防的一种手段,是如何在设计研发阶段保证产品在正式生产过程中交付客户过程中如何满足产品质量的一种控制工具。
因为同类型产品的相似性的特点,所以的DFMEA阶段经常后借鉴以前量产过或正在生产中的产品相关设计上的优缺点评估后再针对新产品进行的改进与改善。
[编辑]DFMEA基本原则DFMEA是在最初生产阶段之前,确定潜在的或已知的故障模式,并提供进一步纠正措施的一种规范化分析方法;通常是通过部件、子系统/部件、系统/组件等一系列步骤来完成的。
最初生产阶段是明确为用户生产产品或提供服务的阶段,该阶段的定义非常重要,在该阶段开始之前对设计的修改和更正都不会引起严重的后果,而之后对设计的任何变更都可能造成产品成本的大幅提高。
DFMEA应当由一个以设计责任工程师为组长的跨职能小组来进行,这个小组的成员不仅应当包括可能对设计产生影响的各个部门的代表,还要包括外部顾客或内部顾客在内。
汽车线束DFMEA实例

德信诚培训网汽车线束潜在失效模式及后果分析(设计FMEA)FMEA编号: DF3001B 第1页,共 3页项目功能潜在失效模式潜在失效后果严重度S级别潜在失效起因/机理频度O现行设计控制预防现行设计控制探测探测度RPN建议措施责任及目标完成日期措施结果采取的措施S O DRPN汽车线·传输电能·传递信号绝缘热收缩严重高温使用条件下热收缩过大使导体端部裸露客户不满意6绞向绞距设计过大3 热收缩试验4 72 无6选用绝缘材料不当3 热收缩试验4 72 无绝缘不耐刮磨车辆在运行中产生的震动摩擦使导线绝缘损坏而发生短路7 ▲选用绝缘材料不当2 刮磨试验 4 64 无绝缘沾到润滑油或燃料油时发生溶胀车辆运行时润滑油和燃料油溅到线材表面时使PVC溶胀,绝缘耐压不良6选用绝缘材料不当2耐油试验耐燃料试验4 48 无长时间高温后线材绝缘发生开裂运行在高温仪表区线材发生开裂易对金属发生放电,使部分仪表指示不灵敏7选用绝缘材料不当2 过热试验 4 56 无长时间高温后线材绝缘在压力下发生变形过大运行在高温仪表区线材变形过大易使绝缘电阻过低漏电流过大,使部分仪表指示不灵敏7选用绝缘材料不当2绝缘和护套高温压力试验4 56 无汽车线·传输电能·传递信号长时间低温后线材绝缘发生开裂绝缘在冬季发生开裂,易对金属发生放电,使部分仪表指示不灵敏7选用绝缘材料不当2低温卷绕试验、低温冲击试验4 56 无绝缘电阻低绝缘漏电流过大,使电能衰减严重,使部分仪表指示不灵敏7绝缘层最小厚度规定不足3绝缘电阻试验3 63 无导体电阻过大导线长时间运行产生热量过多加速绝缘老化6导体根数/单根直径设计不当,导体截面积过小2导体电阻试验3 36 无耐电压过低绝缘容易被击穿使指示仪表不灵敏7 ▲选用绝缘材料不当230min工频交流电压试验和击穿电压试验3 42 无。
11.线束DFMEA

7
被覆材料耐热 度不够
8 进行耐温实验
2
112
增加耐温 实验
荷载电 流不够
线路通断
电线连接 导通
导体易 氧化
加速被覆体老化
8
导体截面积太 小
8 进行老化实验
2
108
增加老化 实验
导电率差,电线发热 8 环境潮湿
6 进行盐雾实验
3
144
增加盐雾 实验
断路
不导通
8
电线内铜丝断 裂
高温使用条件下
绝缘热收缩严重
压试验
3 42
2 附着力试验
3 42
绝缘阻燃性差
绝缘遇火易发生 燃烧
6
选用绝缘材 料不当
2
绝缘剥离试 验
3 36
表面刮伤
刮伤处绝缘过薄 引起耐压不良
7
选用绝缘材 料不当
铜丝少根 导体电阻过大
在第一段水 槽用OD表 7 测量时线材 未完全冷却 引起刮伤
绝缘外径不均匀 外观不良
7
铜丝断线绞 线机不报警
2 阻燃性试验
3 48
检验员每两小时目 测检查,查看是否 3 有刮伤,操作工每 7 147 两小时目测一 次。
操作员每两 2 小时目测铜
丝根数
7 98
4 72
3 热收缩试验
4 72
2 刮磨试验
4 64
选用耐热200℃硅 胶线材
7
2
2
2 8
使用20AWG 导体
8
2
2
3 2
导体进行表面镀锡 处理
8
1
3
2 4
运行在高温仪表
长时间高温后线 材绝缘发生开裂
区线材发生开裂 易对金属发生放 电,使部分仪表
dfmea方法

dfmea方法
dfmea方法是在设计和制造产品时一种可靠性设计的重要方法。
全称为设计失效模式与影响分析。
dfmea方法实际上是FMA(故障模式分析)和FEA(故障影响分析)的组合。
它对各种可能的风险进行评价、分析,以便在现有技术的基础上消除这些风险或将这些风险减小到可接受的水平。
及时性是成功实施的最重要因素之一,它是一个“事前的行为”,而不是“事后的行为”。
DFMEA分析步骤如下:
1.规划与准备:确定分析对象,组建分析团队,收集相关资料。
2.结构分析:识别产品的功能、要求和特性,将产品分解为系统、子系统、
组件及零部件,使用边界图、结构树等表达系统及零部件的关系。
3.功能分析:确保功能、要求和产品特性分配给系统结构元素,使用参数图
等工具进行功能分析。
4.失效分析:识别失效原因、失效模式及失效后果,使用失效网等工具进行
失效分析。
5.风险分析:针对失效原因确定预防措施和探测措施,通过评估严重度、发
生度、探测度来评估风险,并得到采取行动的优先级。
线束DFMEA浅析
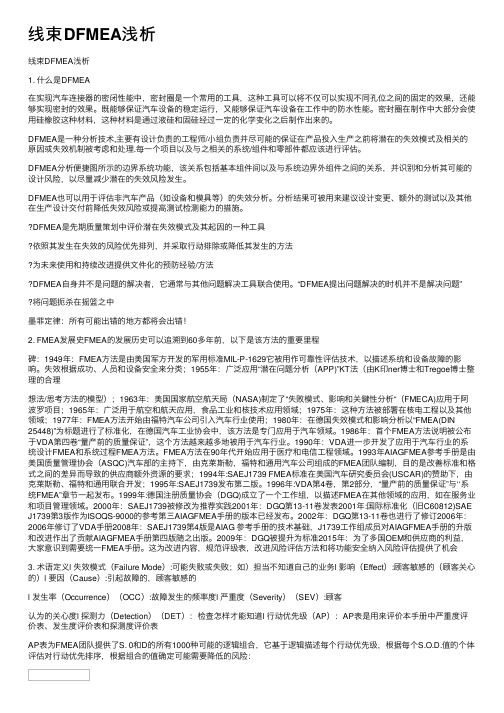
线束DFMEA浅析线束DFMEA浅析1. 什么是DFMEA在实现汽车连接器的密闭性能中,密封圈是⼀个常⽤的⼯具,这种⼯具可以将不仅可以实现不同孔位之间的固定的效果,还能够实现密封的效果。
既能够保证汽车设备的稳定运⾏,⼜能够保证汽车设备在⼯作中的防⽔性能。
密封圈在制作中⼤部分会使⽤硅橡胶这种材料,这种材料是通过液硅和固硅经过⼀定的化学变化之后制作出来的。
DFMEA是⼀种分析技术,主要有设计负责的⼯程师/⼩组负责并尽可能的保证在产品投⼊⽣产之前将潜在的失效模式及相关的原因或失效机制被考虑和处理.每⼀个项⽬以及与之相关的系统/组件和零部件都应该进⾏评估。
DFMEA分析便捷图所⽰的边界系统功能,该关系包括基本组件间以及与系统边界外组件之间的关系,并识别和分析其可能的设计风险,以尽量减少潜在的失效风险发⽣。
DFMEA也可以⽤于评估⾮汽车产品(如设备和模具等)的失效分析。
分析结果可被⽤来建议设计变更、额外的测试以及其他在⽣产设计交付前降低失效风险或提⾼测试检测能⼒的措施。
DFMEA是先期质量策划中评价潜在失效模式及其起因的⼀种⼯具依照其发⽣在失效的风险优先排列,并采取⾏动排除或降低其发⽣的⽅法为未来使⽤和持续改进提供⽂件化的预防经验/⽅法DFMEA⾃⾝并不是问题的解决者,它通常与其他问题解决⼯具联合使⽤。
“DFMEA提出问题解决的时机并不是解决问题”将问题扼杀在摇篮之中墨菲定律:所有可能出错的地⽅都将会出错!2. FMEA发展史FMEA的发展历史可以追溯到60多年前,以下是该⽅法的重要⾥程碑:1949年:FMEA⽅法是由美国军⽅开发的军⽤标准MIL-P-1629它被⽤作可靠性评估技术,以描述系统和设备故障的影响。
失效根据成功、⼈员和设备安全来分类;1955年:⼴泛应⽤“潜在问题分析(APP)”KT法(由K印ner博⼠和Tregoe博⼠整理的合理想法/思考⽅法的模型);1963年:美国国家航空航天局(NASA)制定了“失败模式、影响和关鍵性分析“(FMECA)应⽤于阿波罗项⽬;1965年:⼴泛⽤于航空和航天应⽤,⾷品⼯业和核技术应⽤领域;1975年:这种⽅法被部署在核电⼯程以及其他领域;1977年:FMEA⽅法开始由福特汽车公司引⼊汽车⾏业使⽤;1980年:在德国失效模式和影响分析以“FMEA(DIN 25448)”为标题进⾏了标准化,在德国汽车⼯业协会中,该⽅法是专门应⽤于汽车领域。
DFMEA分析

4
电机选择不合理
XX系统潜在失效模式与影响分析 设计 FMEA
FMEA 号: DFMEA.M9220-
准备人员: FMEA 日期:
、丁伟、刘群艳、阮哲达、姜静、施勤辉。
发生率 探测度 RPN
防止控制
探测控制
推荐的行动
责任与目标完成 时间
根据GB15084-2013规定选择曲 率半径:1.主镜面 /SR1200+300。2.广角镜面 /SR300+50。3.前下视镜 /SR300+50。4.起步镜
7 2 2 28 7 2 2 28
镜面变形
驾驶员看后视野时 不清晰
7
●
镜面反射率选择错 误
驾驶员看后视野时 感觉不舒服
7
● 镜面烤弯变形
要求无未预期 的风噪
风噪过大或难听
用户感觉刺耳不舒 适
3
外形造型不好或镜 壳与背盖间隙过大
后视镜应耐腐 后视镜内金属件锈 后视镜内部零件外
蚀
蚀
观不良
2
在高温作用下,后 后视镜功能减弱或
视镜零部件(如塑 丧失(如镜面移位 料件、电机等)产 、不可调节/折叠
镜杆应与镜臂 镜杆和镜臂配合和 背盖,主镜和广角
牢固连接
设计数据不符。 镜,镜头与镜臂之
6
间的配合间隙不能
满足要求。
镜杆和镜臂配合设 计不合理
后视镜镜头能 可靠折叠且折 叠力适中
折叠力过大:有外
镜头折叠力过大或 力撞击时不易折
过小
叠;折叠力过小:
行车时易抖动
7
下支座定位柱弹簧 ● 工作压力过大或过
小
镜头反复折叠后有 空程或折叠力明显 下降,行车时镜头 易抖动
电源潜在失效模式分析(DFMEA)
项目名称: 过程责任部门: 编制者: 编制日期: FEMA编号: .
项目名称: 过程责任部门: 编制者: 编制日期: FEMA编号: .
项目名称: 过程责任部门: 编制者: 编制日期: FEMA编号: .
项目名称: 过程责任部门: 编制者: 编制日期: FEMA编号: .
过热损坏无
输出
88.5%
项目名称: 过程责任部门: 编制者: 编制日期: FEMA编号: .
项目名称: 过程责任部门: 编制者: 编制日期: FEMA编号: .
项目名称: 过程责任部门: 编制者: 编制日期: FEMA编号: .
项目名称: 过程责任部门: 编制者: 编制日期: FEMA编号: .
项目名称: 过程责任部门: 编制者: 编制日期: FEMA编号: .
项目名称: 过程责任部门: 编制者: 编制日期: FEMA编号: .
文件编号:
潜在过程失效模式及后果分析(设计FMEA)
项目名称: 过程责任部门: 编制者: 编制日期: FEMA编号: .。
电力输配电设备可靠性分析DFMEA
电力输配电设备可靠性分析DFMEA 在电力输配电领域中,设备的可靠性对于保障供电系统的稳定和可持续性起着至关重要的作用。
故本文将对电力输配电设备的可靠性进行分析,采用DFMEA(Design Failure Mode and Effects Analysis)方法,探讨其应用和分析过程。
一、DFMEA简介DFMEA是一种常用于设计阶段的故障模式和影响分析方法,通过分析系统、子系统或部件的潜在故障模式及其对系统性能的影响,以预测和消除潜在的设计缺陷,提高产品的可靠性。
二、电力输配电设备DFMEA分析步骤1. 选择分析对象在电力输配电设备中,可以选择变压器、开关设备、电缆等作为分析对象。
本文以变压器为例进行分析。
2. 列出设备功能和故障模式对选定的变压器设备,列出其功能及可能出现的故障模式。
例如,变压器的功能包括电能转换、绝缘保护等,可能的故障模式包括绕组断线、过热等。
3. 确定故障模式的影响对每个故障模式,确定其对设备以及整个供电系统的影响。
例如,绕组断线可能导致设备停运,影响供电系统的可靠性。
4. 确定故障模式的原因分析导致每个故障模式的潜在原因。
例如,绕组断线可能由于绝缘材料老化、电流过载等原因导致。
5. 评估风险等级根据故障模式的潜在影响和原因,对每个故障模式进行风险评估,确定其风险等级。
通常可以使用风险矩阵进行评估,将潜在影响和原因的严重性进行匹配评估。
6. 制定改进计划根据故障模式的风险等级,制定相应的改进计划,以降低风险。
例如,在绝缘老化导致的绕组断线故障模式中,可以考虑使用更耐老化的绝缘材料,定期检查绕组状态等措施。
7. 进行验证和监控对改进计划进行验证和监控,确保实施后的效果和预期一致。
定期对设备进行检测和维护,并及时记录故障和修复情况,为后续的DFMEA分析提供数据支持。
三、DFMEA的应用意义1. 提前发现潜在风险:通过DFMEA分析,可以在设计阶段及时发现和预防潜在的产品设计缺陷和故障点,降低故障和事故的可能性。
设计失效分析DFMEA经典案例剖析
五:DFMEA应用与表格制作实战第2步 ——找失效点之2-失效模式
•是指系统、子系统或零部件有可能未达到设计 意图的形式。它可能引起更高一级子系统、系
容部分,这里是正文内 容部分,这里是正文
如果DFMEA得到有效应用与执行:
——这些问题都不会发生或者大部分都不会发生!
二:DFMEA的重大作用
二:DFMEA的重大作用
1、 FMEA 是 一种统计工具: * 控制工具: 设计控制 / 生產控制 / 过程控制; * 风险性分析工具; * 管理工具: 识别和评估潜在的失效模式及其影响; 确定能够消除或减少潜在的失效发生的改善措施。
• 频度是指某一特定失效起因或机理(已列于前栏目中)出现的可能性。描述频度 级别数着重在其含义而不是具体的数。通过设计更改来消除或控制一个或更多的失 效因或机理出现频度数的唯一途径。 • 潜在失效起因/机理出现频度的评估分为1到10级,在确定这个估计值时,需要考 虑下列问题:
1. 类似零部件或子系统的维修档案及维修服务经验? 2. 零部件是否为以前使用的的零部件或子系统、还是与其相似? 3. 相对先前水平的零部件或子系统所作的变化有多显着? 4. 零部件是否与原来的有根本不同? 5. 零部件是否是全新的? 6. 零部件的用途有无变化? 7. 有哪些环境改变? 8. 针对该用途,是否作了工程分析来估计其预期的可比较的频度数? • 应运用一致的频度分级规则,以保证连续性。所谓的“设计寿命的可能失效率” 是根据零部件、子系统或系统在设计的寿命过程中预计发生的失效(故障)数确定 的。频度数的取值与失效率范围有关,但关不反应实际出现的可能性。
DFMEA_汽车线束线材
参考历史
8
记录,进 行耐温实
验
2
112
红
电 线
2.荷载电 加速被覆体
流不够
老化
8
导体截面积太 小
8
进行老化 实验
2
108
/
连
接 导
3.导体易 氧化
导电率差, 电线发热。
8
环境潮湿
6
进行盐雾 实验
3
144
通
4.断路
不导通
பைடு நூலகம்
8
电线内铜丝断 裂
2 进行电测
2
32
1.电线被 成型时外被
覆耐热度 熔化,产生漏 7
DFMEA设计缺陷模式和影响分
项目
核心 团队
设计责任 负责工程师 关键日期
FMEA 编号: FMEA 初始日期: 制作
项目/ 功能
潜在缺陷 模式
潜在缺陷影 响
严 重 性
潜在缺陷原因
发 生 预防的方 频法 率
可 侦 测 性
R P N
1.电线被 成型时外被
覆耐热度 熔化,产生漏 7
不够
电.
被覆材料耐热 度不够
导体进行
表面镀锡 8 1 3 处理
2 4
增加耐温 实验
增加老化 实验
增加盐雾 实验
选用耐热
200。C硅 7 2 2 胶线材
2 8
使用20AWG 导体
8
2
2
3 2
导体进行
表面镀锡 8 1 3 处理
2 4
计缺陷模式和影响分析
FMEA 编号:
FMEA 初始日期:
确认
修订日期 核准
行动的结果
现行的建 议措施
- 1、下载文档前请自行甄别文档内容的完整性,平台不提供额外的编辑、内容补充、找答案等附加服务。
- 2、"仅部分预览"的文档,不可在线预览部分如存在完整性等问题,可反馈申请退款(可完整预览的文档不适用该条件!)。
- 3、如文档侵犯您的权益,请联系客服反馈,我们会尽快为您处理(人工客服工作时间:9:00-18:30)。
线束DFMEA浅析
1. 什么是DFMEA
在实现汽车连接器的密闭性能中,密封圈是一个常用的工具,这种工具可以将不仅可以实现不同孔位之间的固定的效果,还能够实现密封的效果。
既能够保证汽车设备的稳定运行,又能够保证汽车设备在工作中的防水性能。
密封圈在制作中大部分会使用硅橡胶这种材料,这种材料是通过液硅和固硅经过一定的化学变化之后制作出来的。
DFMEA是一种分析技术,主要有设计负责的工程师/小组负责并尽可能的保证在产品投入生产之前将潜在的失效模式及相关的原因或失效机制被考虑和处理.每一个项目以及与之相关的系统/组件和零部件都应该进行评估。
DFMEA分析便捷图所示的边界系统功能,该关系包括基本组件间以及与系统边界外组件之间的关系,并识别和分析其可能的设计风险,以尽量减少潜在的失效风险发生。
DFMEA也可以用于评估非汽车产品(如设备和模具等)的失效分析。
分析结果可被用来建议设计变更、额外的测试以及其他在生产设计交付前降低失效风险或提高测试检测能力的措施。
•DFMEA是先期质量策划中评价潜在失效模式及其起因的一种工具
•依照其发生在失效的风险优先排列,并采取行动排除或降低其发生的方法
•为未来使用和持续改进提供文件化的预防经验/方法
•DFMEA自身并不是问题的解决者,它通常与其他问题解决工具联合使用。
“DFMEA提出问题解决的时机并不是解决问题”
•将问题扼杀在摇篮之中
墨菲定律:所有可能出错的地方都将会出错!
2. FMEA发展史FMEA的发展历史可以追溯到60多年前,以下是该方法的重要里程
碑:1949年:FMEA方法是由美国军方开发的军用标准MIL-P-1629它被用作可靠性评估技术,以描述系统和设备故障的影响。
失效根据成功、人员和设备安全来分类;1955年:广泛应用“潜在问题分析(APP)”KT法(由K印ner博士和Tregoe博士整理的合理
想法/思考方法的模型);1963年:美国国家航空航天局(NASA)制定了“失败模式、影响和关鍵性分析“(FMECA)应用于阿波罗项目;1965年:广泛用于航空和航天应用,食品工业和核技术应用领域;1975年:这种方法被部署在核电工程以及其他领域;1977年:FMEA方法开始由福特汽车公司引入汽车行业使用;1980年:在德国失效模式和影响分析以“FMEA(DIN 25448)”为标题进行了标准化,在德国汽车工业协会中,该方法是专门应用于汽车领域。
1986年:首个FMEA方法说明被公布于VDA第四卷“量产前的质量保证”,这个方法越来越多地被用于汽车行业。
1990年:VDA进一步开发了应用于汽车行业的系统设计FMEA和系统过程FMEA方法。
FMEA方法在90年代开始应用于医疗和电信工程领域。
1993年AIAGFMEA参考手册是由美国质量管理协会(ASQC)汽车部的主持下,由克莱斯勒,福特和通用汽车公司组成的FMEA团队编制,目的是改善标准和格式之间的差异而导致的供应商额外资源的要求;1994年:SAEJ1739 FMEA标准在美国汽车研究委员会(USCAR)的赞助下,由克莱斯勒、福特和通用联合开发;1995年:SAEJ1739发布第二版。
1996年:VDA第4卷,第2部分,“量产前的质量保证”与‘‘系统FMEA”章节一起发布。
1999年:德国注册质量协会(DGQ)成立了一个工作组,以描述FMEA在其他领域的应用,如在服务业和项目管理领域。
2000年:SAEJ1739被修改为推荐实践2001年:DGQ第13-11卷发表2001年:国际标准化(旧C60812)SAE J1739第3版作为ISOQS-9000的参考第三AIAGFMEA手册的版本已经发布。
2002年:DGQ第13-11卷也进行了修订2006年:2006年修订了VDA手册2008年:SAEJ1739第4版是AIAG 参考手册的技术基础,J1739工作组成员对AIAGFMEA手册的升版和改进作出了贡献AIAGFMEA手册第四版随之出版。
2009年:DGQ被提升为标准2015年:为了多国OEM和供应商的利益,大家意识到需要统一FMEA手册。
这为改进内容,规范评级表,改进风险评估方法和将功能安全纳入风险评估提供了机会
3. 术语定义l 失效模式(Failure Mode):可能失败或失败;如)担当不知道自己的业务l 影响(Effect):顾客敏感的(顾客关心的)l 要因(Cause):引起故障的,顾客敏感的
l 发生率(Occurrence)(OCC):故障发生的频率度l 严重度(Severity)(SEV):顾客
认为的关心度l 探测力(Detection)(DET):检查怎样才能知道l 行动优先级(AP):AP表是用来评价本手册中严重度评价表、发生度评价表和探测度评价表
AP表为FMEA团队提供了S. 0和D的所有1000种可能的逻辑组合,它基于逻辑描述每个行动优先级,根据每个S.O.D.值的个体评估对行动优先排序,根据组合的值确定可能需要降低的风险:
3.1 失效定义
3.2 潜在失效模式
•列出所有失效,不一定肯定发生
•利用经验和头脑风暴
•过程/零件怎样不满足要求
•无论工程规范如何,顾客认为的拒收条件是什么
•潜在失效类型和原因如下,但不仅限于:
•功能性能设计不完善(指定的材料不正确,几何形状不正确,选择的应用部件不正确,指定的表面不正确,行程规格不合适,指定的摩擦材料不合适,润滑能力不足,设计寿命不足,算法不正确,维护说明不当等)•系统交互(机械接U,流体流量,热源,控制器反馈
等)•随时间变化(屈服,疲劳,材料不稳定,蠕变,磨损,腐蚀,化学氧化,电迁移,过度应力等)•外部环境(热,冷,潮湿,振动,道路碎片,路面盐等)•车辆操作员的错误行为(使用了错误的档位,使用了错误的踏板,超速,牵引,燃料类型错误,维修损坏等)•个体变化(公差范围内的变化)•制造缺乏稳健的设计(几何形状允许向后或倒置安装零件,零件缺乏明显的设计特征,运输容器设计导致零件划伤或粘在一起,零件处理导致损坏等)•软件问题(未定义状态,不完整的代码测试,损坏的代码/数据)
3.3 典型的失效模式失效模式应以规范化技术术语描述,不同于顾客察觉的现象
3.4 潜在失效的后果
4. DFMEA团队-需要谁加入团队?
核心团队由以下人员组成:
•协调员(项目经理)
•设计工程师
•系统工程师
•零部件工程师
•测试工程师
•质量/可靠性工程师
•负责产品开发的其他人员
核心团队成员负责准备FMEA分析(步驟1-3)并参加FMEA会议。
其他扩展团队成员可以根据需要参与,由FMEA协调员协调
扩展团队可能由以下人员组成:
•技术专家
•过程/制造工程师
•维修工程师
•功能安全工程师
•采购
•供应商
•客户代表
•其他具有专业知识的人员将帮助核心团队分析产品的特定方面
4.1 DFMEA小组的守则
•决定前召开小组会议
•决定谁将参加
•预先准备议题
•主张进行会议笔记或记录
•建立基本准则
•遵守事先的议程
•评价会议
•不允许中断
4.2 头脑风暴
头脑风暴是一种技法,可以技法小组成员产生大量的有创意的点子。
有纽约广告代理的老板Alex F Osborn在1930年发明,其前提是在一般的讨论中,人们害怕别人批评而约束
自己,因此而不能产生有创意的点子。
头脑风暴包括创造一种氛围,让人们感到无拘无束,此时人们可能提出在平时认为不太可能的解决方案,但往往收到意想不到的效果。
4.3 头脑风暴4大原则(会议前向成员解释)
•暂缓下结论:不批评其他人的观点,更不要嘲笑人或其观点
•自由:鼓励参与者梦想或遐想,鼓励大胆及愚蠢的建议,但不提议无任何建议或离座闲逛•数量:鼓励大量建议
•交叉培养:鼓励一个小组的建议被其他小组的成员扩展或开发,将所有人的建议写在题板上以便被全部人都能够看到,同事编号。
但建议减少或小组成员感到空洞时,千万不要说丧气话。
5. DMFEA时间-什么时候?
•在产品开发开始之前,概念阶段启动FMEA计划
•在充分了解设计概念时,启动DFMEA
•在充分了解生产概念时,启动PFMEA
•DFMEA和PFMEA应在同一时间段内执行,以同时优化产品和过程设计
•DFMEA到PFMEA的信息流
•在用于报价的设计规范发布之前,完成DFMEA分析
•在生产模具开始之前,完成DFMEA措施
•在过程最终决策之前,完成PFMEA分析
•在PPAP/PPA之前,完成PFMEA措施
6. DMFEA意图-我们为什么在这里?
每个FMEA团队的成员都需要对FMEA的目的和意图进行培训,使得小组成员给出时间承诺并参与有意义的主动分析。
建议进行意识水平培训,其中包括6步FMEA过程的概述。