钢材表面喷砂处理工艺
喷砂除锈的施工方法
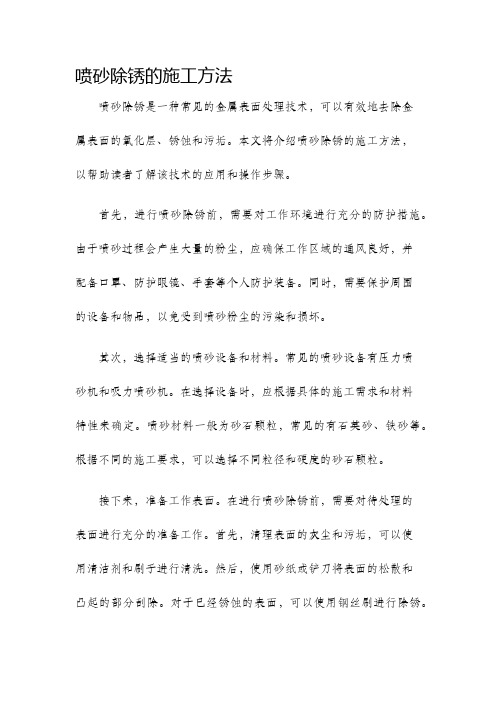
喷砂除锈的施工方法喷砂除锈是一种常见的金属表面处理技术,可以有效地去除金属表面的氧化层、锈蚀和污垢。
本文将介绍喷砂除锈的施工方法,以帮助读者了解该技术的应用和操作步骤。
首先,进行喷砂除锈前,需要对工作环境进行充分的防护措施。
由于喷砂过程会产生大量的粉尘,应确保工作区域的通风良好,并配备口罩、防护眼镜、手套等个人防护装备。
同时,需要保护周围的设备和物品,以免受到喷砂粉尘的污染和损坏。
其次,选择适当的喷砂设备和材料。
常见的喷砂设备有压力喷砂机和吸力喷砂机。
在选择设备时,应根据具体的施工需求和材料特性来确定。
喷砂材料一般为砂石颗粒,常见的有石英砂、铁砂等。
根据不同的施工要求,可以选择不同粒径和硬度的砂石颗粒。
接下来,准备工作表面。
在进行喷砂除锈前,需要对待处理的表面进行充分的准备工作。
首先,清理表面的灰尘和污垢,可以使用清洁剂和刷子进行清洗。
然后,使用砂纸或铲刀将表面的松散和凸起的部分刮除。
对于已经锈蚀的表面,可以使用钢丝刷进行除锈。
然后,进行喷砂除锈操作。
首先,根据具体的施工要求和工件的大小,确定喷砂的工作压力。
然后,将喷砂设备连接到压缩空气源,并调整合适的喷砂角度和距离。
开始喷砂时,应先从较低的压力开始,逐渐增加压力。
同时,要注意保持均匀的喷砂速度和距离,以避免表面产生凹陷或划痕。
在喷砂过程中,要注意控制喷砂的时间和强度。
过长或过强的喷砂可能会造成表面的损坏或形成深度的凹陷。
因此,在施工中要依据实际情况进行调整和控制。
最后,在完成喷砂除锈后,需要对表面进行充分的清洁和处理。
首先,使用清洁剂和水清洗喷砂后的表面,以去除残留的砂石颗粒和粉尘。
然后,可以进行表面的抛光或涂装等后续处理,以增加其耐腐蚀性和美观度。
总结起来,喷砂除锈是一种有效去除金属表面氧化层和锈蚀的技术,具有广泛的应用领域。
在施工过程中,可以通过充分的准备工作、选择适当的设备和材料,并控制喷砂的时间和强度,来实现较好的除锈效果。
但需要注意的是,喷砂过程中会产生大量粉尘和噪音,应根据实际情况采取必要的防护措施和环境管理措施,以确保施工的安全环保。
喷砂除锈刷漆工艺要求
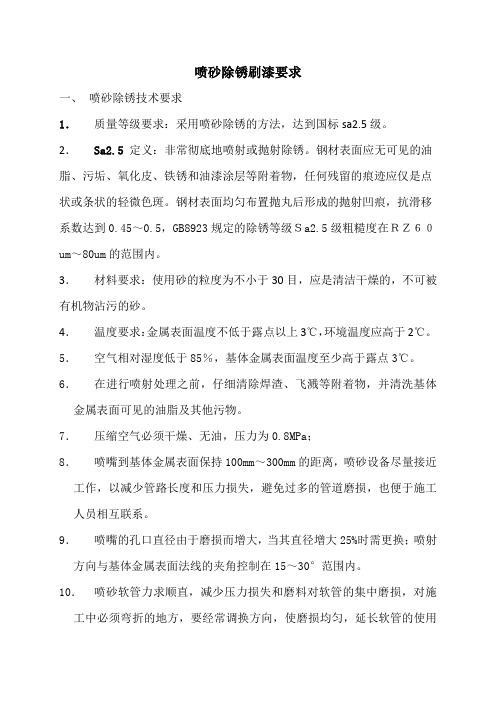
喷砂除锈刷漆要求一、喷砂除锈技术要求1.质量等级要求:采用喷砂除锈的方法,达到国标sa2.5级。
2.Sa2.5定义:非常彻底地喷射或抛射除锈。
钢材表面应无可见的油脂、污垢、氧化皮、铁锈和油漆涂层等附着物,任何残留的痕迹应仅是点状或条状的轻微色斑。
钢材表面均匀布置抛丸后形成的抛射凹痕,抗滑移系数达到0.45~0.5,GB8923规定的除锈等级Sa2.5级粗糙度在RZ60um~80um的范围内。
3.材料要求:使用砂的粒度为不小于30目,应是清洁干燥的,不可被有机物沾污的砂。
4.温度要求:金属表面温度不低于露点以上3℃,环境温度应高于2℃。
5.空气相对湿度低于85%,基体金属表面温度至少高于露点3℃。
6.在进行喷射处理之前,仔细清除焊渣、飞溅等附着物,并清洗基体金属表面可见的油脂及其他污物。
7.压缩空气必须干燥、无油,压力为0.8MPa;8.喷嘴到基体金属表面保持100mm~300mm的距离,喷砂设备尽量接近工作,以减少管路长度和压力损失,避免过多的管道磨损,也便于施工人员相互联系。
9.喷嘴的孔口直径由于磨损而增大,当其直径增大25%时需更换;喷射方向与基体金属表面法线的夹角控制在15~30°范围内。
10.喷砂软管力求顺直,减少压力损失和磨料对软管的集中磨损,对施工中必须弯折的地方,要经常调换方向,使磨损均匀,延长软管的使用寿命;11.表面预处理后,清除浮尘和碎屑,清理后的表面不得用手触摸;12.涂装前如发现基体金属表面被污染或返锈,必须重新进行处理;13.预处理完成经检查合格后需尽快进行喷涂,其间隔时间越短越好。
在潮湿或工业大气压等环境条件下,须在4h内涂装完毕,晴天或温度不大时,最长间隔不超过12h。
二、油漆涂刷工艺过程为:基面清理——检查验收——底漆涂装第一遍——检查验收——底漆涂刷第二遍——检查验收——面漆涂装(是否有看要求)——检查验收1、油漆涂刷时环境温度宜为5~38℃,环境相对湿度不宜大于85%,或者钢材表面不应有结露,涂装后4小时内应保持免受雨淋,在有雨、雾、雪、风沙和较大灰尘时,禁止在户外涂装施工。
喷砂喷漆作业标准

钢材表面喷砂喷漆工艺标准喷砂工艺1.前期控制:使用干喷射方法除锈,在进行喷射处理之前,仔细清除焊渣、飞溅等附着物,并清洗基体金属表面可见的油脂及其他污物. 除锈应在有防尘措施的场地进行,以防止粉尘飞扬。
2.磨料控制:磨料要求粒径为0.63mm~1.6mm的铁丸或钢丸;有棱角、清洁、干燥、没有油污。
3.工艺控制:喷射除锈时,施工现场环境湿度大于80%,或钢材表面温度低于空气露点温度3℃时,应禁止施工。
3.1喷射处理所使用的压缩空气经过冷却装置及油水分离器处理,以保证压缩空气的干燥、无油;压缩空气压力为0.5~0.6MPa;喷嘴最小直径应为4~5mm,喷距为100~200mm之间。
3.2 喷射方向与基体金属表面法线的夹角控制在15°~30°范围内。
喷砂法兰外圆时,要倾斜45°左右,防止沙粒钻进法兰面上。
为了防止漏喷和空放、减少移位次数,提高磨料利用率和工作效率,在施工前要全面进行考虑,合理安排喷射位置.3.3 经喷砂处理后,钢材表面粗糙度应小于涂层总厚度的1/3~1/2.(RZ50~70μm),应按照技术要求,取相应粗糙度样板做比较.钢材表面的清洁度应达到GB8923规定的除锈等级Sa2.5级(详见GB8923-88《涂装前钢材表面锈蚀等级和除锈等级》)。
3.4 预处理完成经检查合格后需尽快进行喷涂,其间隔时间越短越好。
在潮湿或工业大气压等环境条件下,须在4h内涂装完毕,晴天或温度不大时,最长间隔不超过12h。
4、喷砂质量评定标准:4.1喷砂完成后首先应对喷砂除锈部位进行全面检查,其次要对基体钢材表面进行清洁度和粗糙度检查。
表面清洁度和表面粗糙度的评定须在良好的散射日光下或照度相当的人工条件下进行,检查人员应具有正常的视力,并以目视为准;4.2 评定表面清洁度等级时,被检基体的金属表面与GB8923-1988《涂装前钢材表面锈蚀等级和除锈等级》中Sa2.5级相应的照片进行目视比较评定。
钢材表面喷砂处理工艺标准
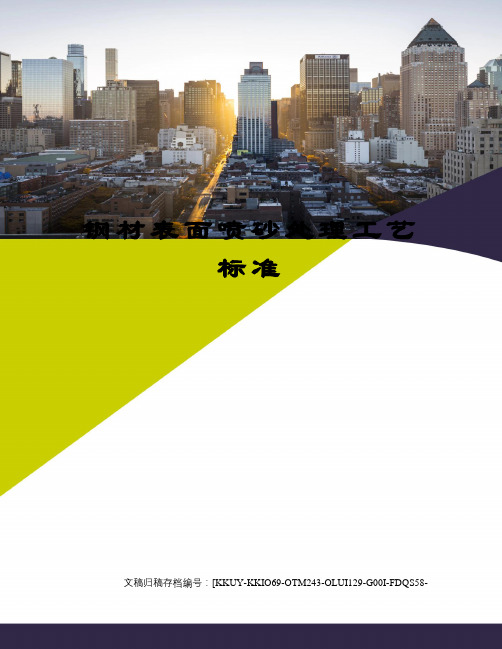
钢材表面喷砂处理工艺标准文稿归稿存档编号:[KKUY-KKIO69-OTM243-OLUI129-G00I-FDQS58-钢材表面喷砂处理工艺标准1、技术要求1.1按SDZ01.1的规范执行,采用喷砂除锈;1.2经处理后的钢材表面应达到GB8923规定的除锈等级Sa2.5级,精糙度在RZ60um~80um的范围内;1.3表面预处理完成后12h内进行油漆涂装。
2、钢材表面喷砂处理的工作条件2.1空气相对湿度低于85%;2.2基体金属表面温度至少高于露点3。
C;2.3在进行喷射处理之前,仔细清除焊渣、飞溅等附着物,并清洗基体金属表面可见的油脂及其他污物。
3、喷砂处理施工要点3.1工艺参数3.1.1磨料选择铸铁砂,粒径为0.5mm~1.5mm。
磨料要求有棱角、清洁、干燥、没有油污;3.1.2喷射处理所有的压缩空气经过冷却装置及油水分离器处理,以保证压缩空气的干燥、无油、压缩空气压力为0.7MPa;3.1.3喷嘴到基体金属表面保持100mm~300mm的距离;3.1.4喷嘴的孔口直径由于磨损而增大,当其直径增大25%时需更换;3.1.5喷射方向与基体金属表面法线的夹角控制在15~30。
范围内。
3.2操作要点3.2.1喷砂设备尽量接近工作,以减少管路长度和压力损失,避免过多的管道磨损,也便于施工人员相互联系;3.2.2喷砂软管力求顺直,减少压力损失和磨料对软管的集中磨损,对施工中必须弯折的地方,要经常调换方向,使磨损均匀,延长软管的使用寿命;3.2.3为了防止漏喷和空放、减少移位次数,提高磨料利用率和工作效率,在施工前要全面进行考虑,合理安排喷射位置,拟定喷射路线;3.2.4视空气压力、出砂量及结构表面污染情况灵活掌握喷嘴移动速度;3.2.5在喷射过程中,根据空气压力、喷嘴直径、结构表面锈蚀状态、处理的质量、效率等对料气比及时进行调整;3.2.6表面预处理后,用干燥、无油的压缩空气清除浮尘和碎屑,清理后的表面不得用手触摸;3.2.7涂装前如发现基体金属表面被污染或返锈,必须重新进行处理;3.2.8预处理完成经检查合格后需尽快进行喷涂,其间隔时间越短越好。
不锈钢喷砂工艺流程

不锈钢喷砂工艺流程
《不锈钢喷砂工艺流程》
不锈钢喷砂是一种常用的表面处理工艺,可以使不锈钢表面获得均匀且细腻的磨砂效果,提高不锈钢表面的质感和美观度。
下面介绍一下不锈钢喷砂的工艺流程。
首先,要准备好不锈钢表面处理设备和材料,包括喷砂机、喷砂液、喷砂沙粒等。
然后,将要处理的不锈钢制品放置在喷砂机内,进行喷砂处理。
在喷砂过程中,要根据不同的喷砂要求和效果调节喷砂机的喷砂压力、喷砂角度和喷砂速度。
接着,进行喷砂处理,将不锈钢表面喷砂成所需的效果。
在喷砂过程中,要注意保持喷砂机的平稳运转,保证不锈钢表面的均匀喷砂效果。
喷砂处理完成后,要对不锈钢表面进行清洗和除尘,以保证表面的清洁度和光洁度。
最后,进行不锈钢表面的喷砂效果检查,对喷砂后的不锈钢表面进行质量检验和光洁度检查,确保不锈钢表面处理的效果符合要求。
总之,不锈钢喷砂工艺是一种常用的表面处理工艺,通过喷砂可以使不锈钢表面获得均匀且细腻的磨砂效果,提高不锈钢表面的质感和美观度。
喷砂工艺流程包括准备工作、喷砂处理、清洗除尘和质量检验等环节,只有在每一个环节都做好,才能获得理想的喷砂效果。
喷砂处理工艺标准
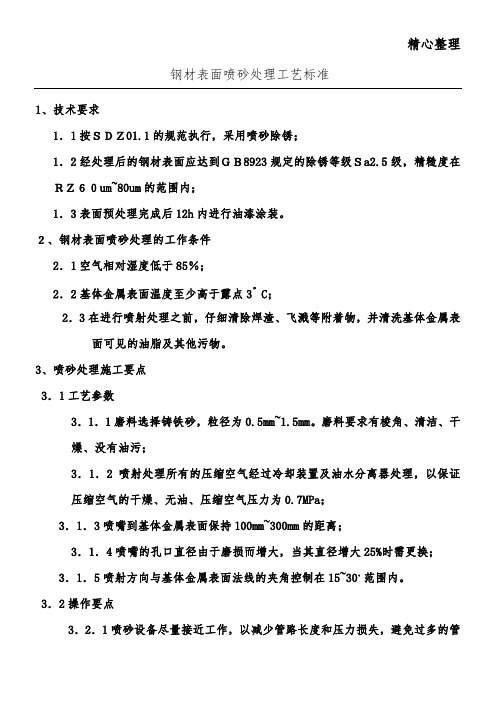
精心整理
钢材表面喷砂处理工艺标准
1、技术要求
1.1按SDZ01.1的规范执行,采用喷砂除锈;
1.2经处理后的钢材表面应达到GB8923规定的除锈等级Sa2.5级,精糙度在RZ60um~80um 的范围内;
1.2.2.233.13.1.3喷嘴到基体金属表面保持100mm~300mm 的距离;
3.1.4喷嘴的孔口直径由于磨损而增大,当其直径增大25%时需更换;
3.1.5喷射方向与基体金属表面法线的夹角控制在15~30。
范围内。
3.2操作要点
3.2.1喷砂设备尽量接近工作,以减少管路长度和压力损失,避免过多的管
道磨损,也便于施工人员相互联系;
3.2.2喷砂软管力求顺直,减少压力损失和磨料对软管的集中磨损,对施工中必须弯折的地方,要经常调换方向,使磨损均匀,延长软管的使用寿命;
3.2.3为了防止漏喷和空放、减少移位次数,提高磨料利用率和工作效率,在施工前要全面进行考虑,合理安排喷射位置,拟定喷射路线;
最
4
4
4.
锈蚀等级和除锈等级》中相应的照片进行目视比较评定。
Sa2.5级标准为钢材表面处理得非常彻底,即表面无可见的油脂、污垢、氧化皮、铁锈和油漆涂层等附着物,所见的是点状或条纹状的轻微色斑。
4.3评定表面粗糙时,按照GB/T13288《涂装前钢材表面粗糙度等级的评定(比较样块法)》用标准样块目视比较评比粗糙度等级,或用仪器直接测定表面粗糙
度值。
常见金属表面喷砂除锈工艺
金属表面喷砂除锈工艺是利用对空气的压力影响作用,把所需金属粒度的喷砂工艺磨料通过喷枪,对金属零件锈蚀的表面进行喷砂除锈处理。
这种喷砂除锈工艺不仅去锈快,还能对金属表面起到涂装、喷涂的效果,经过喷砂除锈工艺处理过的金属表面可达到干净的,有一定粗糙度的表面要求,从而提高复盖层与零件的结合力。
喷砂除锈工艺常见分为干法喷砂、湿法喷砂、无法喷砂与高压水喷砂等。
干法喷砂尘土大,有碍环保,危害健康;湿法喷砂虽无粉尘,但水分会使表面再度生锈。
防止的办法是在水中加入1%~15%的防锈剂(磷酸三钠、碳酸钠、亚硝酸钠等)和乳化剂或肥皂水,使其表面在短时期内不再生锈,然后再涂保养底漆。
无尘喷砂是将加砂、喷砂和集砂回收等在一密闭系统里连续循环进行,以免粉尘飞扬。
高压水喷砂主要用于大面积除锈,如船体、油舱、油罐、锅炉等,水中也常加入钝化剂和肥皂水。
喷砂工艺材料抛丸或喷砂除锈一、关于除锈质量等级要求2、所有待涂水性无机富锌涂料的钢材表面,必须抛丸或喷砂达到ISO8501-1(GB8923-88)Sa2.5级要求。
1、局部修补涂层时,钢材表面必须打磨至ISO8501-1(GB8923-88)St3级。
二、金属表面喷砂除锈磨料1、为确保抛丸或喷吵后钢材表面达到规定的清洁度和表面粗糙度,喷砂除锈推荐使用棱角状或圆珠状的粒度为0.3-0.8mm的不锈钢砂。
2、所用磨料应是清洁干燥的,不可被有机物沾污。
三、表面粗糙度要求:表面粗糙度要求控制在35~65μm范围内。
四、压缩空气:喷砂用压缩空气,压力应不低于0.5Mpa。
关于金属表面喷砂除锈工艺的介绍,如果还有何疑问,请咨询:400-8290-699,咨询QQ:875564898\2695763754。
钢结构喷砂除锈防腐施工工艺
钢结构喷砂除锈防腐施工工艺一.钢结构喷砂除锈防腐施工工艺(风格A)1. 工艺流程1.1 准备工作1.1.1 确定施工范围和施工条件1.1.2 制定工艺方案和施工计划1.1.3 获取喷砂设备和相应工具1.1.4 检查钢结构表面状态和存在的缺陷1.1.5 做好安全防护措施1.2 喷砂除锈1.2.1 调试喷砂设备并确定操作参数1.2.2 清理钢结构表面尘土和附着物1.2.3 进行喷砂操作,确保均匀、全面覆盖1.3 检查和处理1.3.1 完成喷砂后,对钢结构进行表面检查1.3.2 针对存在的缺陷进行修补和处理1.3.3 检查喷砂质量是否满足要求1.4 防腐施工1.4.1 选择合适的防腐涂料和施工方法1.4.2 涂刷防腐涂料前进行表面处理1.4.3 进行防腐涂料的涂刷和干燥2. 施工注意事项2.1 安全注意事项2.2 喷砂操作注意事项2.3 防腐涂料施工注意事项2.4 钢结构表面缺陷处理注意事项3. 施工质量控制3.1 检测设备的准确性和有效性3.2 对喷砂和防腐施工过程进行监测和记录3.3 进行施工质量检查和评估3.4 确定施工质量验收标准4. 工艺方案调整和优化4.1 根据实际施工情况,及时调整工艺方案4.2 对工艺过程进行持续改进和优化附件:1. 喷砂设备操作手册2. 防腐涂料施工说明书法律名词及注释:1. 钢结构:指用钢材组成的具有一定刚度和强度的结构体系。
2. 喷砂:通过高速喷射流动的磨料,清理钢结构表面的一种机械除锈方法。
3. 防腐涂料:一种具有防腐蚀功能的涂料,可以保护钢结构表面免受环境腐蚀的影响。
4. 施工质量验收标准:用于评估施工质量是否达到要求的衡量标准。
二.钢结构喷砂除锈防腐施工工艺(风格B)1. 施工准备阶段1.1 确定施工范围和工期要求1.2 制定施工方案和安全措施1.3 购置和调试喷砂设备1.4 对钢结构表面进行检查,记录存在的缺陷1.5 确保施工区域清洁、通风良好2. 喷砂除锈操作2.1 根据钢结构的种类和要求,选择合适的喷砂材料和喷砂设备2.2 调整喷砂设备参数,确保喷砂操作效果良好2.3 清理钢结构表面的灰尘和附着物2.4 进行喷砂除锈操作,覆盖全面且均匀3. 检查和处理3.1 完成喷砂除锈后,对钢结构表面进行仔细检查3.2 根据检查结果,采取相应措施处理存在的缺陷3.3 确保喷砂除锈的质量满足要求4. 防腐施工4.1 选择适合的防腐涂料和施工方法4.2 在防腐涂料施工前进行表面处理,如喷涂底漆等4.3 按照施工要求进行防腐涂料的涂刷和干燥5. 施工质量控制5.1 使用准确有效的检测设备进行施工监测和记录5.2 进行施工质量检查和评估5.3 制定施工质量验收标准,确保施工质量符合要求附件:1. 喷砂设备操作手册2. 防腐涂料施工说明书法律名词及注释:1. 钢结构:指由钢材构成的具有一定刚度和强度的结构体系。
不锈钢喷砂工艺规范
工艺文件不锈钢喷砂工艺规范目录1 目的及范围 (1)1.1目的 (1)1.2范围 (1)2 规范性引用文件 (1)3设备、工具工装和辅材 (1)4工艺流程 (1)5工艺要求 (2)5.1 准备 (2)5.1.1 工具工装 (2)5.1.2 工件 (2)5.2 遮蔽保护 (2)5.3 喷砂 (2)5.4 清理 (2)5.5 检查 (2)5.5.1 质量要求 (2)5.5.2 注意事项 (2)6 注意事项 (3)1目的及范围1.1 目的本规范规定了不锈钢涂装前的喷砂处理工艺要求,指导相关作业人员进行喷砂作业。
1.2范围本规范适用于不锈钢前处理的喷砂处理工艺规范。
2规范性引用文件3设备、工具工装和辅材4工艺流程5. 工艺要求5.1 准备5.1.1 工具工装a) 喷砂砂粒应坚硬、有棱角、干燥(含水量〈2%〉、无泥土及其它杂质,具体选择见表4。
b) 宜采用石英砂、金刚砂,颗粒以0.5mm-1.5mm为宜,筛选前须晒干,存储与棚内,筛孔大小为:粗筛40孔/cm2(颗粒1.2mm)、细筛372孔/cm2-476孔/cm2 (颗粒0.3mm)。
c) 喷砂用的压缩空气必须经冷却装置及油水分离器处理,以保证干燥、无油;油水分离器必须定期清理。
d) 喷砂操作时,空压机气压为0.2MPa-0.65MPa,气压变幅为0.05MPa-0.1MPa。
5.1.2 工件a) 在喷砂前对零部件留有的残胶清理干净。
b) 表面油污必须采用除油剂或酒精擦拭处理。
c) 柜体吊耳渗透探伤显像剂必须清洗干净。
d) 清除焊渣、飞溅等附着物。
5.2 屏蔽保护a) 根据设计图纸要求,采用不干胶对所需保护的位置进行屏蔽保护。
b) 所有螺孔必须用螺杆进行保护,防止砂粒损伤螺纹。
5.3 喷砂a) 喷嘴到基体表面距离以100mm-300mm为宜。
b) 喷射方向与基体表面法线夹角30°-40°为宜。
c) 喷砂时喷嘴不要长时间停留在某处,对喷枪无法喷射的部位要采取手工或动力工具打磨粗糙。
钢材表面喷砂处理工艺
钢材表面喷砂除锈及防腐处理工艺一、除锈去污的方法钢材除锈大致有以下几种:1、抛丸除锈:利用机械设备的高速运转把一定粒度的钢丸靠抛头的离心力抛出,被抛出的钢丸与构件猛烈碰撞打击从而达到祛除钢材表面锈蚀的目的的一种方法;它使用的钢丸品种有:铸铁丸和钢丝切丸两种,铸铁丸是利用熔化的铁水在喷射并急速冷却的情况下形成的粒度在2~3mm铁丸,表面很圆整;它成本相对便宜但耐用性稍差;在抛丸过程中经反复的撞击铁丸被粉碎而当作粉尘排除;钢丝切丸是用废旧铁丝绳的钢丝切成2mm的小段而成,它的表面带有尖角,除锈效果相对高且不易破碎使用寿命延长,但价格有所提高;后者的抛丸表面更粗糙一些;2、喷丸除锈:利用高压空气带出钢丸喷射到构件表面达到的一种除锈方法;3、喷砂除锈:利用高压空气带出石英砂喷射到构件表面达到的一种除锈方法;可以采用金刚砂、石英砂等,石英砂的来源有:河砂、海砂及人造砂等;砂的成本低且来源广泛,但对环境污染大;除锈完全靠人工操作,除锈后的构件表面粗糙度小,不易达到摩擦系数的要求;海砂在使用前应祛除其盐份;以上两种除锈方法对环境湿度要求小于85%;而金刚砂可以重复利用;4、酸洗除锈:酸洗除锈亦称化学除锈,其原理是利用酸洗液中的酸与金属氧化物进行化学反应,使金属氧化物溶解,而除去钢材表面的锈蚀和污物;但酸洗不能够达到抛丸或喷丸的表面粗糙度效果;且在酸洗除锈后一定要大量清水清洗并钝化处理;它所形成的大量废水、废酸、酸雾造成环境污染;如果处理不当还会造成金属表面过蚀,形成麻点;目前很少采用;5、手工和动力除锈:工具简单施工方便;但劳动强度大,除锈质量差;该法只有在其他方法都不具备的条件下才能局部采用;比如个别构件的修整或安装工地的局部除锈处理等;其常用工具有:砂轮机、铲刀、钢丝刷、砂布等;二、除锈等级标准的要求国家标准GB8923—88涂装前钢材表面修饰等级和除锈等级将除锈等级分成喷射或抛射除锈、手工和动力除锈、火焰除锈三种类型:1、喷射或抛射除锈,用字母“Sa”表示;分四个等级:Sa1轻度的喷射或抛射除锈;钢材表面无可见的油脂或污物,没有附着不牢的氧化皮、铁锈和油漆涂层等附着物;Sa2彻底地喷射或抛射除锈;钢材表面应无可见的油脂和污垢、氧化皮、铁锈等附着物已基本清除,其残留物应是牢固附者的;钢材表面均匀布置抛丸后形成的抛射凹痕,抗滑移系数达到~非常彻底地喷射或抛射除锈;钢材表面应无可见的油脂、污垢、氧化皮、铁锈和油漆涂层等附着物,任何残留的痕迹应仅是点状或条状的轻微色斑;钢材表面均匀布置抛丸后形成的抛射凹痕,抗滑移系数达到~,GB8923规定的除锈等级S级粗糙度在RZ60um~80um的范围内;对于粗糙度的内容见尾页Sa3使钢材表观洁净的喷射或抛射除锈;钢材表面应无可见的油脂、污垢、氧化皮、铁锈和油漆等附着物,该表面应显示均匀的金属光泽;Sa3只适用于高科技比较精密零件;2、手工和动力除锈:以字母“St”表示,分为两个等级:St2彻底手工和动力除锈;钢材表面无可见的油脂、污垢,没有附着不牢的氧化皮、铁锈和油漆涂层等附着物;St3非常彻底手工和动力除锈;钢材表面应无可见的油脂、污垢;并且没有附着不牢的氧化皮、铁锈和油漆涂层等附着物;除锈比St2更为彻底,底材显露部分的表面应具有金属光泽;3、火焰除锈:以字母“F1”表示,它包括在火焰加热作业后,以动力钢丝刷清除加热后附着在钢材表面的产物;只有一个等级F1,钢材表面应无氧化皮、铁锈和油漆涂层等附着物,任何残留的痕迹应仅为表面变色不同颜色的暗影三、施工要求1、空气相对湿度低于85%,基体金属表面温度至少高于露点3℃;2、在进行喷射处理之前,仔细清除焊渣、飞溅等附着物,并清洗基体金属表面可见的油脂及其他污物;3、压缩空气必须干燥、无油,压力为;4、喷嘴到基体金属表面保持100mm~300mm的距离,喷砂设备尽量接近工作,以减少管路长度和压力损失,避免过多的管道磨损,也便于施工人员相互联系;5、喷嘴的孔口直径由于磨损而增大,当其直径增大25%时需更换;喷射方向与基体金属表面法线的夹角控制在15~30°范围内;6、喷砂软管力求顺直,减少压力损失和磨料对软管的集中磨损,对施工中必须弯折的地方,要经常调换方向,使磨损均匀,延长软管的使用寿命;7、为了防止漏喷和空放、减少移位次数,提高磨料利用率和工作效率,在施工前要全面进行考虑,合理安排喷射位置,拟定喷射路线;8、视空气压力、出砂量及结构表面污染情况灵活掌握喷嘴移动速度;9、在喷射过程中,根据空气压力、喷嘴直径、结构表面锈蚀状态、处理的质量、效率等对料气比及时进行调整;10、表面预处理后,用干燥、无油的压缩空气清除浮尘和碎屑,清理后的表面不得用手触摸;11、涂装前如发现基体金属表面被污染或返锈,必须重新进行处理;12、预处理完成经检查合格后需尽快进行喷涂,其间隔时间越短越好;在潮湿或工业大气压等环境条件下,须在4h内涂装完毕,晴天或温度不大时,最长间隔不超过12h;四、质量评定1、表面清洁度和表面粗糙度的评定须在良好的散射日光下或照度相当的人工条件下进行;2、评定表面清洁度等级时,被检基体的金属表面与GB8923涂装前钢材表面锈蚀等级和除锈等级中相应的照片进行目视比较评定;3、评定表面粗糙时,按照G B/ T 13288涂装前钢材表面粗糙度等级的评定比较样块法用标准样块目视比较评比粗糙度等级,或用仪器直接测定表面粗糙度值;五、油漆涂刷工艺过程为:基面清理——检查验收——底漆涂装第一遍——检查验收——底漆涂刷第二遍——检查验收——面漆涂装是否有第二遍看要求——检查验收1、油漆涂刷时环境温度宜为5~38℃,环境相对湿度不宜大于85%,或者钢材表面不应有结露,涂装后4小时内应保持免受雨淋,在有雨、雾、雪、风沙和较大灰尘时,禁止在户外涂装施工;2、涂装前应对涂料名称、型号、颜色进行检查,确认是否与设计规定相符,产品出厂日期是否超过贮存期限,与规定不相符或超过贮存期的涂料不得使用;涂料及其辅助材料,宜贮存在通风良好的阴凉库房内,温度应控制在5~35℃,按原包装密封保管;涂料及其辅料属于易燃品,库房附近杜绝火源,并有明显的“严禁烟火”的标志牌和灭火工具;3、涂料开桶后,用手动搅拌,直到涂料液体均匀为止,同时检查涂料的外观质量,不得有析出结块现象;对禁止涂漆的部位,应在涂装前采取措施遮蔽保护;4、涂装施工方法涂装施工可采用刷涂、滚涂、空气喷涂和高压喷涂方法;具体施工方法应根据涂装场所的条件,被涂物形状大小、涂料品种及设计要求等选择合理的涂装工艺;1刷涂刷涂是以刷子用手工涂漆的一种方法,涂刷时应蘸少量油漆,刷毛浸入油漆的部分应为毛长的1/3~1/2;涂刷顺序,一般应按自上而下、从左向右、先里后外、先斜后直、先难后易,先横后竖,纵横交错,先立面后平面进行施工的原则,使漆膜均匀、致密、光滑和平整;漆膜的刷涂厚度应均匀,防止流挂、起皱和漏涂;2滚涂滚涂是用辊子涂装的一种方法,适用于一定品种的涂料;涂料应倒入装有滚涂板的容器内,将滚子的一半浸入涂料,然后提起在滚涂板板上来回滚涂几次,使滚子全部均匀浸透涂料并把多余的涂料滚压掉;把滚子按W形轻轻滚动,将涂料大致的涂布于被涂构件上,然后滚子上下密集滚动,将涂料均匀地分布开,最后使滚子按一定的方向滚平表面并修饰;滚动时初始用力要轻,以防流淌,随后逐渐用力,使涂层均匀;3空气喷涂空气喷涂法是以压缩空气的气流使涂料雾化成雾状带入喷枪,喷涂于被涂构件面上的一种涂装方法;进行喷涂时,必须将空气压力、喷出量和喷雾幅度等参数调整到适当程度,以保证喷涂质量;喷涂“施工粘度”按有关规定执行,喷枪压力为—,喷嘴与物面的距离:大型枪为20~30cm,小型枪为15—25cm;喷枪应依次保持与物面垂直或平行地动动,运行的速度为30~60cm/s,操作要稳定;每行涂层边缘的搭接宽度应保持一致,前后搭接宽度一般为喷涂幅度的1/4~1/3;多层次喷涂时,各层应纵横交叉施工,第一层横向施工时,第二层则要纵向施工;喷枪使用后,应立即用溶剂清洗干净;4高压无气喷涂高压无气喷涂法是用密封容器内的高压泵输送涂料,当涂料从喷嘴喷出时,产生体积骤然膨胀而分散雾化,高速地喷在物面上;喷涂时喷嘴与物面距离32~38cm,喷流的喷射角度30~60度,喷流幅度为喷射大面积的物件为30~40cm,喷射较大面积物件为20~30cm,喷射较小面积物件为15~25cm,喷枪移动速度60~100cm/s;每行涂层的搭接边应为涂层幅度的1/6~1/5;喷涂完毕后,立即用溶剂清洗设备,同时排出喷枪内的剩余涂料,吸入溶剂作彻底的循环清洗,拆下高压软管用压缩空气吹净管内的溶剂;5、涂层要求1涂装遍数、涂层厚度及遍数均应符合设计要求;当设计对涂层厚度无要求时,应按钢结构工程施工质量验收规范GB 50205-2001的规定执行:涂层干漆膜总厚度室处应为150um,室内应为125um,其允许偏差为-25um;每遍涂层干漆膜厚度的允许偏差为-5um;2当设计对涂装无遍数规定时:防锈底漆为二遍,底漆两遍时,目测为看不到金属暗色,面漆为一至二遍,面漆涂刷后看不到底漆暗色为准;各涂层间隔时间应符合油漆专业厂家的技术要求;涂层二层或二层以上涂料时,应在前层干燥后方可涂后一层,涂漆时应对前一层漆面上的灰尘及有碍于下层涂漆质量的流挂、皱皮等进行清理,并防止局部漏涂;3表面处理后到涂漆的时间间隔不应超过6小时,在此期间表面应保持洁净,严禁沾水,油污等,漆膜固化时间与环境温度、相对湿度和涂料有关,每道涂层涂装后,表面至少在4小时内不得被雨淋和玷污;4涂层干燥后外观色泽应均匀一致,表面应平整光滑、丰满、无流挂、起皱、露底、气泡、针孔、龟裂、脱落和粘有脏物,凡出现上述缺陷时,应及时进行修补;各种底漆或防锈漆要求最低的除锈等级六、涂层干漆膜厚度检测漆膜厚度的检验干膜可用测量仪器,如膜厚仪;按同类构件数抽查10%,但均不应少于3件,每件测5处,每处的数值为3个相距50mm的测点干漆膜厚度的平均值;涂料、涂装遍数、涂层厚度均应符合设计要求,涂层干漆膜总厚度室处应为150um,室内应为125um,其允许偏差为-25um;每遍涂层干漆膜厚度的允许偏差为-5um;目视检查涂层表面,表面应平滑,色彩均匀,无明显起皱、流挂、无漏涂,附着力良好;七、成品保护措施对地面、屋墙面板、通风及消防管道、设备等现场成品加强保护,涂刷时采取遮盖措施,如有污染必须尽快用清水及干布进行清除;对涂装完毕的成品应妥善保护,以防损坏;定期对施工人员进行安全质量教育,加强其成品保护意识;由专人负责成品保护的监督事宜;八、安全措施在进行涂装作业时,必须采取各种预防措施,以防止意外事故发生和对施工人员进行必要的个人防护;进行涂装前必须检查所需的照明、通风、脚手架等设备是否完备可靠,焊接是否已经结束,当油漆在通风条件较差的环境中进行施工,应采用较强制通风,以保证施工人员的安全和漆膜的干燥;为了防止油漆溅到皮肤上或眼睛内,施工时必须穿戴工作服、手套、防护眼镜;如油漆溅到皮肤上,在用肥皂和清水洗净,最好不要用溶剂;如油漆溅入眼睛内,应立即以清水进行冲洗,然后立即找医生检查;在使用手工或风动工具除锈或除旧漆膜时,为了避免眼睛受伤和吸入灰尘,应戴防护眼镜和防尘口罩;操作人员如有头晕、头痛、恶心、呕吐等不适感觉,应立即到有新鲜空气的地方,直至原工作处的通风得到改善后才可继续进行涂装;如吸入过量和溶剂气体或漆雾而晕厥者,则应立即将其移至空气新鲜的地方,使其逐渐复原,但不要进行强迫运动;九、消防措施施工现场应建立和执行防火管理制度,由生产部经理总负责,由安全员专管;油漆、稀释剂等易燃物品应存放于专用仓库,配备消防设施如灭火器和消防砂箱等,严禁烟火;施工现场设施符合消防要求的消防设施,并保持完好的备用状态;油漆涂装附近区域禁止吸烟;所有施工人员要加强安全教育,懂得必要的防火、灭火、救火知识;现场设置防火标志牌,任何人不得私自挪动标志牌和消防设施;十、埋地管道刷环氧沥青漆防腐要求1、管道已做除锈并验收合格;2、刷一遍环氧沥青漆,要求看不到金属暗色为准;3、等第一遍干透以后缠一层玻璃丝布,搭接不少于5公分,缠绕紧密;4、刷第二遍环氧沥青漆;5、待沥青漆不沾布以后,缠第二层玻璃丝布,刷第三遍沥青漆;6、要求管两头各预留10公分的焊接管头,等就地焊接完毕后,焊口部分做两布三油,并对管道碰坏的防腐部分进行修复;7、当缠布时因斜度太大导致玻璃丝布起皱时,可两层布一起缠,搭接必须超过一半,然后涂刷两遍底漆;备注:粗糙度定义:喷砂砂粒冲击并向外反弹,这种冲击造成表面几千分之一寸的压痕,叫基础图式;回弹会使某些表面向外高出几千分之一寸,低的叫“谷”,高的叫“峰”,每一个沙粒冲击表面都会造成一个“谷”和一个“峰”,这就是基础图式粗糙度的形成原因;它用MILL密耳表示,一密耳是1/1000秒;形成的基础图式值应是总涂层系统的30%,不宜超过干膜涂层厚度的1/3,一般防腐在50-70um之间;1微米um =毫米mm 1密耳=秒=毫米mm表面粗糙度的值必须在一定的范围,太低则涂层附着力欠佳,太高则容易造成底漆覆盖不够而点蚀或者涂层对基材的封闭性不好,截留空气;一般要求时涂层总厚度的三分之一左右,但不超过防锈底漆的厚度;表面粗糙度划分为14个等级,粗糙度um:雾状镜面、镜状光泽面、亮光泽面、暗光泽面、不可见加工痕迹的方向、微见加工痕迹的方向、可见加工痕迹的方向、看不清加工痕迹、微见加工痕迹、可见加工痕迹、微见刀痕、25可见刀痕、50明显可见刀痕、100喷砂除锈的优点:喷砂设备金属零件的基本不受损坏,尺寸精度不会改变;零件表面不受污染,磨料不会与零件的材为发生化学反应;喷砂设备可以很容易的处理凹槽等难以接触的部位,多种粒度的磨料可以选择使用;处理成本大幅度降低,主要体现在喷砂设备工作效率的提高,能满足各种各样的表面光整要求,比化学处理更安全,更方便;能耗低,费用省;喷砂设备不污染环境,省去了环境治理费用;。
- 1、下载文档前请自行甄别文档内容的完整性,平台不提供额外的编辑、内容补充、找答案等附加服务。
- 2、"仅部分预览"的文档,不可在线预览部分如存在完整性等问题,可反馈申请退款(可完整预览的文档不适用该条件!)。
- 3、如文档侵犯您的权益,请联系客服反馈,我们会尽快为您处理(人工客服工作时间:9:00-18:30)。
钢材表面喷砂处理工艺钢材表面喷砂除锈及防腐处理工艺一、除锈去污的方法钢材除锈大致有以下几种:1、抛丸除锈:利用机械设备的高速运转把一定粒度的钢丸靠抛头的离心力抛出,被抛出的钢丸与构件猛烈碰撞打击从而达到祛除钢材表面锈蚀的目的的一种方法。
它使用的钢丸品种有:铸铁丸和钢丝切丸两种,铸铁丸是利用熔化的铁水在喷射并急速冷却的情况下形成的粒度在2~3mm铁丸,表面很圆整。
它成本相对便宜但耐用性稍差。
在抛丸过程中经反复的撞击铁丸被粉碎而当作粉尘排除。
钢丝切丸是用废旧铁丝绳的钢丝切成2mm的小段而成,它的表面带有尖角,除锈效果相对高且不易破碎使用寿命延长,但价格有所提高。
后者的抛丸表面更粗糙一些。
2、喷丸除锈:利用高压空气带出钢丸喷射到构件表面达到的一种除锈方法。
3、喷砂除锈:利用高压空气带出石英砂喷射到构件表面达到的一种除锈方法。
可以采用金刚砂、石英砂等,石英砂的来源有:河砂、海砂及人造砂等。
砂的成本低且来源广泛,但对环境污染大;除锈完全靠人工操作,除锈后的构件表面粗糙度小,不易达到摩擦系数的要求。
海砂在使用前应祛除其盐份。
以上两种除锈方法对环境湿度要求小于85%。
而金刚砂可以重复利用。
4、酸洗除锈:酸洗除锈亦称化学除锈,其原理是利用酸洗液中的酸与金属氧化物进行化学反应,使金属氧化物溶解,而除去钢材表面的锈蚀和污物。
但酸洗不能够达到抛丸或喷丸的表面粗糙度效果。
且在酸洗除锈后一定要大量清水清洗并钝化处理;它所形成的大量废水、废酸、酸雾造成环境污染。
如果处理不当还会造成金属表面过蚀,形成麻点。
目前很少采用。
5、手工和动力除锈:工具简单施工方便。
但劳动强度大,除锈质量差。
该法只有在其他方法都不具备的条件下才能局部采用。
比如个别构件的修整或安装工地的局部除锈处理等。
其常用工具有:砂轮机、铲刀、钢丝刷、砂布等。
二、除锈等级标准的要求国家标准GB8923—88《涂装前钢材表面修饰等级和除锈等级》将除锈等级分成喷射或抛射除锈、手工和动力除锈、火焰除锈三种类型:1、喷射或抛射除锈,用字母“Sa”表示。
分四个等级:Sa1 轻度的喷射或抛射除锈。
钢材表面无可见的油脂或污物,没有附着不牢的氧化皮、铁锈和油漆涂层等附着物。
Sa2 彻底地喷射或抛射除锈。
钢材表面应无可见的油脂和污垢、氧化皮、铁锈等附着物已基本清除,其残留物应是牢固附者的。
钢材表面均匀布置抛丸后形成的抛射凹痕,抗滑移系数达到0.35~0.45Sa2.5 非常彻底地喷射或抛射除锈。
钢材表面应无可见的油脂、污垢、氧化皮、铁锈和油漆涂层等附着物,任何残留的痕迹应仅是点状或条状的轻微色斑。
钢材表面均匀布置抛丸后形成的抛射凹痕,抗滑移系数达到0.45~0.5,GB8923规定的除锈等级Sa2.5级粗糙度在RZ60um~80um的范围内。
(对于粗糙度的内容见尾页)Sa3 使钢材表观洁净的喷射或抛射除锈。
钢材表面应无可见的油脂、污垢、氧化皮、铁锈和油漆等附着物,该表面应显示均匀的金属光泽。
Sa3只适用于高科技比较精密零件。
2、手工和动力除锈:以字母“St”表示,分为两个等级:St2 彻底手工和动力除锈。
钢材表面无可见的油脂、污垢,没有附着不牢的氧化皮、铁锈和油漆涂层等附着物。
St3 非常彻底手工和动力除锈。
钢材表面应无可见的油脂、污垢。
并且没有附着不牢的氧化皮、铁锈和油漆涂层等附着物。
除锈比St2更为彻底,底材显露部分的表面应具有金属光泽。
3、火焰除锈:以字母“F1”表示,它包括在火焰加热作业后,以动力钢丝刷清除加热后附着在钢材表面的产物。
只有一个等级F1,钢材表面应无氧化皮、铁锈和油漆涂层等附着物,任何残留的痕迹应仅为表面变色(不同颜色的暗影)三、施工要求1、空气相对湿度低于85%,基体金属表面温度至少高于露点3℃。
2、在进行喷射处理之前,仔细清除焊渣、飞溅等附着物,并清洗基体金属表面可见的油脂及其他污物。
3、压缩空气必须干燥、无油,压力为0.8MPa;4、喷嘴到基体金属表面保持100mm~300mm的距离,喷砂设备尽量接近工作,以减少管路长度和压力损失,避免过多的管道磨损,也便于施工人员相互联系。
5、喷嘴的孔口直径由于磨损而增大,当其直径增大25%时需更换;喷射方向与基体金属表面法线的夹角控制在15~30°范围内。
6、喷砂软管力求顺直,减少压力损失和磨料对软管的集中磨损,对施工中必须弯折的地方,要经常调换方向,使磨损均匀,延长软管的使用寿命;7、为了防止漏喷和空放、减少移位次数,提高磨料利用率和工作效率,在施工前要全面进行考虑,合理安排喷射位置,拟定喷射路线;8、视空气压力、出砂量及结构表面污染情况灵活掌握喷嘴移动速度;9、在喷射过程中,根据空气压力、喷嘴直径、结构表面锈蚀状态、处理的质量、效率等对料气比及时进行调整;10、表面预处理后,用干燥、无油的压缩空气清除浮尘和碎屑,清理后的表面不得用手触摸;11、涂装前如发现基体金属表面被污染或返锈,必须重新进行处理;12、预处理完成经检查合格后需尽快进行喷涂,其间隔时间越短越好。
在潮湿或工业大气压等环境条件下,须在4h内涂装完毕,晴天或温度不大时,最长间隔不超过12h。
四、质量评定1、表面清洁度和表面粗糙度的评定须在良好的散射日光下或照度相当的人工条件下进行。
2、评定表面清洁度等级时,被检基体的金属表面与GB8923《涂装前钢材表面锈蚀等级和除锈等级》中相应的照片进行目视比较评定。
3、评定表面粗糙时,按照G B/ T 13288《涂装前钢材表面粗糙度等级的评定(比较样块法)》用标准样块目视比较评比粗糙度等级,或用仪器直接测定表面粗糙度值。
五、油漆涂刷工艺过程为:基面清理——检查验收——底漆涂装第一遍——检查验收——底漆涂刷第二遍——检查验收——面漆涂装(是否有第二遍看要求)——检查验收1、油漆涂刷时环境温度宜为5~38℃,环境相对湿度不宜大于85%,或者钢材表面不应有结露,涂装后4小时内应保持免受雨淋,在有雨、雾、雪、风沙和较大灰尘时,禁止在户外涂装施工。
2、涂装前应对涂料名称、型号、颜色进行检查,确认是否与设计规定相符,产品出厂日期是否超过贮存期限,与规定不相符或超过贮存期的涂料不得使用。
涂料及其辅助材料,宜贮存在通风良好的阴凉库房内,温度应控制在5~35℃,按原包装密封保管。
涂料及其辅料属于易燃品,库房附近杜绝火源,并有明显的“严禁烟火”的标志牌和灭火工具。
3、涂料开桶后,用手动搅拌,直到涂料液体均匀为止,同时检查涂料的外观质量,不得有析出结块现象。
对禁止涂漆的部位,应在涂装前采取措施遮蔽保护。
4、涂装施工方法涂装施工可采用刷涂、滚涂、空气喷涂和高压喷涂方法。
具体施工方法应根据涂装场所的条件,被涂物形状大小、涂料品种及设计要求等选择合理的涂装工艺。
(1)刷涂刷涂是以刷子用手工涂漆的一种方法,涂刷时应蘸少量油漆,刷毛浸入油漆的部分应为毛长的1/3~1/2。
涂刷顺序,一般应按自上而下、从左向右、先里后外、先斜后直、先难后易,先横后竖,纵横交错,先立面后平面进行施工的原则,使漆膜均匀、致密、光滑和平整。
漆膜的刷涂厚度应均匀,防止流挂、起皱和漏涂。
(2)滚涂滚涂是用辊子涂装的一种方法,适用于一定品种的涂料。
涂料应倒入装有滚涂板的容器内,将滚子的一半浸入涂料,然后提起在滚涂板板上来回滚涂几次,使滚子全部均匀浸透涂料并把多余的涂料滚压掉。
把滚子按W 形轻轻滚动,将涂料大致的涂布于被涂构件上,然后滚子上下密集滚动,将涂料均匀地分布开,最后使滚子按一定的方向滚平表面并修饰。
滚动时初始用力要轻,以防流淌,随后逐渐用力,使涂层均匀。
(3)空气喷涂空气喷涂法是以压缩空气的气流使涂料雾化成雾状带入喷枪,喷涂于被涂构件面上的一种涂装方法。
进行喷涂时,必须将空气压力、喷出量和喷雾幅度等参数调整到适当程度,以保证喷涂质量。
喷涂“施工粘度”按有关规定执行,喷枪压力为0.3—0.5Mpa,喷嘴与物面的距离:大型枪为20~30cm,小型枪为15—25cm。
喷枪应依次保持与物面垂直或平行地动动,运行的速度为30~60cm/s,操作要稳定。
每行涂层边缘的搭接宽度应保持一致,前后搭接宽度一般为喷涂幅度的1/4~1/3。
多层次喷涂时,各层应纵横交叉施工,第一层横向施工时,第二层则要纵向施工。
喷枪使用后,应立即用溶剂清洗干净。
(4)高压无气喷涂高压无气喷涂法是用密封容器内的高压泵输送涂料,当涂料从喷嘴喷出时,产生体积骤然膨胀而分散雾化,高速地喷在物面上。
喷涂时喷嘴与物面距离32~38cm,喷流的喷射角度30~60度,喷流幅度为喷射大面积的物件为30~40cm,喷射较大面积物件为20~30cm,喷射较小面积物件为15~25cm,喷枪移动速度60~100cm/s。
每行涂层的搭接边应为涂层幅度的1/6~1/5。
喷涂完毕后,立即用溶剂清洗设备,同时排出喷枪内的剩余涂料,吸入溶剂作彻底的循环清洗,拆下高压软管用压缩空气吹净管内的溶剂。
5、涂层要求(1)涂装遍数、涂层厚度及遍数均应符合设计要求。
当设计对涂层厚度无要求时,应按《钢结构工程施工质量验收规范》GB 50205-2001的规定执行:涂层干漆膜总厚度室处应为150um,室内应为125um,其允许偏差为-25um。
每遍涂层干漆膜厚度的允许偏差为-5um。
(2)当设计对涂装无遍数规定时:防锈底漆为二遍,底漆两遍时,目测为看不到金属暗色,面漆为一至二遍,面漆涂刷后看不到底漆暗色为准。
各涂层间隔时间应符合油漆专业厂家的技术要求。
涂层二层或二层以上涂料时,应在前层干燥后方可涂后一层,涂漆时应对前一层漆面上的灰尘及有碍于下层涂漆质量的流挂、皱皮等进行清理,并防止局部漏涂。
(3)表面处理后到涂漆的时间间隔不应超过6小时,在此期间表面应保持洁净,严禁沾水,油污等,漆膜固化时间与环境温度、相对湿度和涂料有关,每道涂层涂装后,表面至少在4小时内不得被雨淋和玷污。
(4)涂层干燥后外观色泽应均匀一致,表面应平整光滑、丰满、无流挂、起皱、露底、气泡、针孔、龟裂、脱落和粘有脏物,凡出现上述缺陷时,应及时进行修补。
各种底漆或防锈漆要求最低的除锈等级涂料品种除锈等级油性酚醛、醇酸底漆或防锈漆St2高氯化聚乙烯、氯化橡胶、氯磺化聚乙烯、聚氨酯等底Sa2漆或防锈漆无机富锌、有机硅、过氯乙烯等底漆Sa2.5六、涂层干漆膜厚度检测漆膜厚度的检验(干膜)可用测量仪器,如膜厚仪;按同类构件数抽查10%,但均不应少于3件,每件测5处,每处的数值为3个相距50mm的测点干漆膜厚度的平均值。
涂料、涂装遍数、涂层厚度均应符合设计要求,涂层干漆膜总厚度室处应为150um,室内应为125um,其允许偏差为-25um。
每遍涂层干漆膜厚度的允许偏差为-5um。
目视检查涂层表面,表面应平滑,色彩均匀,无明显起皱、流挂、无漏涂,附着力良好。