凸模结构设计资料
凸模的设计

2.6.2 凸模的设计
为了使凸模在冲裁时不发生失稳弯曲,凸模
纵向压力P∑应小于或等于临界压力P0,
即P∑≤P0
➢
根据欧拉公式:
Pc
2 EJ
l 2
故
2 EJ
l 2
P
lm ax
2E m J in 2P
2.6.2 凸模的设计
➢ 2、凸模的固定方法
➢ 凸模固定到固定板中的配合或间隙对不要求常拆 换的凸模用N7/m6或M7/m6(双边0.02mm过盈, 需要经常更换的凸模一般用H7/h6(双边0.01mm 的间隙)弹压导板模中凸模与固定板成0.1mm的 双面间隙。
1)铆接固定法:一般用作非圆形小截面直通式凸模 的固定,就是将固定板的型孔倒角(1×45°) 后,再将反铆后的凸模装入,最后一起磨平,如 图2-24左半部份所示。
2.6.2 凸模的设计
图2-30 凸模疲劳强度图算法
3) 如果对凸模寿命要求校核,则可利用疲劳强度图表进行 校核。例如图2-30,已知料厚t=4mm,抗剪强度τ=500Mpa, 凸模直径d=12mm,求得点Ⅱ在冲次n=1×105以上,故可判 断该凸模可冲105次以上。
2.6.2 凸模的设计
4、凸模护套
➢ 当凸模自由长度大于max时,则应采用护套保护凸模。图 2-31 a)、b)是两种简单的圆形凸模护套。
➢ 图a)所示护套1、凸模2均用铆接固定。 ➢ 图b)所示护套1采用台肩固定 ➢ 图c)所示护套1固定在卸料板(或导板)4上。 ➢ 图d)是一种比较完善的凸模护套,三个等分扇形块6固定
在固定板中,具有三个等分扇形的护套1固定在导板4中, 可以在固定扇形块6内滑动,因此可使凸模在任意位置均 处于三方导向与保护之中。但是结构复杂,制造比较困难。
冲孔模具中快换凸模结构的设计

( 方 便 易损 凸 模 的 更换 , 2 ) 这 对 于 加 快 模 具 的 维 修 也 十 分 重
要。 国
参 考 文 献
… 冯 炳尧等 . 具设 计与制 造 模
简 明手册 , 海 :上海 科 学技术 出 上
i 向螺钉 2固定极 38模 4垫极 5上模座 横
p s e s e t i t c n e e e a i e s a a e o s s c r a n o o v ninc e s n s d m g pu c o m a n a n nh f iti o r p a e n o p r is o a o t f i e o s r c u e f e i n r e l c me t f e m s i n d p o d f r t u t r o d sg
( )凸 模尾 部 ‘ 2 V’ 型 槽 、 自 身 实 现 刚 好 与 凸 模 尾 部 ‘ ’型 V
同 轴 度 又 连 通 的 前 部 两 孔 及 后 部 细 牙 螺 纹 孔 、附 加 台 阶 前 短 圆 杆 、 后 圆柱 的 细 牙 紧 固 螺 钉 必 须进 行 设 计 计 算 。 由于 凸 模 的 更 换 涉 及 到 凸 模
a xl r u i a y. i
Ke r s ir i g i e s r c u e f he a i r p a e e t u c y wo d :p e c n d t t r o t r p d e l c m n p n h u d sg ei n
垒
. 了有关 阅 冲孔模具
西 1袂 换 8 模 结 构
版 社 .18 . 95
( )图 l 示 ,横 向 螺纹 孔 1 所
其 孔 口设 置 在 固 定 板 的 侧 壁 面 Ql
凸模结构基本形式

什么是凸模,它有哪几种结构形式?8 y. c! P6 J9 D% M, f$ M( M: R+ l凸模,又叫阳模,是成型塑件内表面的部件,在注射成型中通常装在注射机的动模板上,所以,习惯上又叫动模。
由于注塑成型中常让塑件留在凸模上,所以,在凸模上常装有顶出机构,以方便塑件的脱模。
凸模按结构形式,主要有以下几类。
# O, R; f+ a0 D( c/ x, @) O(1) 整体式凸模( y2 x( |# H/ x3 w; n7 x! N这类凸模是用整块模具材料直接加工而成,如图4-73所示。
它结构简单、牢固、刚性好,不易变形,制作较容易,塑件质量好,无接缝的溢料痕迹。
但塑件形状复杂时不易加工,对优质模具材料的消耗量也大。
这种模具多适合形状简单的小型塑件加工。
1 M4 m1 i1 H8 W, P7 r( M/ vq% r0 P* W% b3 D5 q" D图1:整体式凸模(直通式和台阶式。
直通式凸模的工作部分和固定部分的形状与尺寸做成一样,这类凸模一般采用线切割方法进行加工。
台阶式凸模一般采用机械加工,当形状复杂时,成形部分常采用成型磨削。
)9 z0 i, t6 Y) u2 s# {1 v$ i(2) 组合式凸模对于内表面复杂的塑件,或形状虽不复杂,但为了节省较昂贵的模具材料,可以采用组合式凸模结构。
它适用于大中型模具,还便于设置模具的冷却回路,图2所示为几种常见组合式凸模。
1 _' ~6 _" l5 @2 S: T" o8 B$ N+ m% W: \, d5 {# J4 h图2:组合式凸模a)整体嵌入式b)锥销定位式c)止口嵌入式1) 整体嵌人式凸模(图a)。
这种结构是采用整体嵌人固定板,用轴肩和支承板连接,它有利于合理选择模具材料并对凸模进行合适的热处理,它适合于形状简单,机械加工容易的凸模。
3 m$ y- j/ b c) _" v2) 锥销定位式凸模(图b)。
3-6-1工作零件结构设计
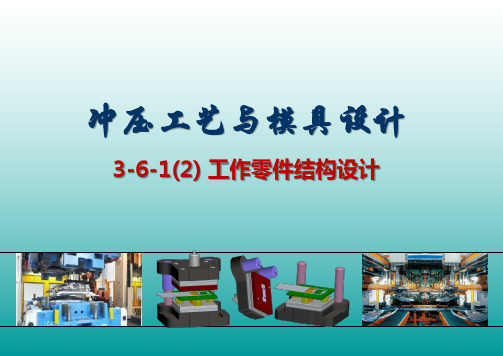
直通式整体式凸模
台阶式整体式凸模
②组合式凸模:即凸模刃口工作部分与安装固定部分采用镶拼组合的方式。
组合目的:约贵重模具材料,多用于大型冲模和硬质合金模;或加强小凸
模的强度。
固定 部分(普
通钢)
工作 部分(硬 质合金)
冲压工艺与模具设计
2、圆形凸模的结构形式与标准
圆形凸模一般都是台阶整体式, 由工作部分和固定部分组成。对于直 径过小的凸模,增加过渡段。
台阶固定法
小凸模安装保护套
冲压工艺与模具设计
2)螺钉固定法
多用于固定尺寸较大 的直通式凸模或安装在模3)压板固定法
多用于固定尺寸较小的直通 式凸模,便于拆卸更换。
4)其它固定法
其它还有铆接固 定法、黏结固定法, 过盈固定法
铆接和黏结固定法
工作零件结构设计
螺钉固定法
压板固定法
压板
冲压工艺与模具设计
4、凸模的长度确定
工作零件结构设计
凸模设计长度 :
L = h1+h2+h3+h附加
其中: L ——凸模长度(mm); h1——凸模固定板厚度( mm ); h2——卸料板厚度( mm ); h3——导料板厚度( mm ); h附加——附加长度( mm ),
一般取经验值10~20 mm .
2)冲裁凸模按结构形式分:
整体式凸模和组合式凸模
①整体式凸模
圆形凸模
异形凸模
➢直通式:多用于形状不规则的异形凸模,可用线切割或成形磨加工,
加工方便简单,但不好固定。
➢台阶式:多用于圆形或规则的异形凸模,圆形台阶式凸模可车削加
工,异形需铣削加工,便于固定,但异形凸模台阶不易加工。
冲压工艺与模具设计
凸模与凹模的结构设计

凸模与凹模的结构设计凸模和凹模是一种常见的结构设计,在制造过程中起到了重要的作用。
本文将从凸模和凹模的定义、使用场景、设计原则和常见问题等方面进行探讨,共计1200字以上。
一、凸模与凹模的定义凸模是一种具有凸起结构的模具,用于在制造过程中成形凹陷或控制形变。
凹模则是一种具有凹进结构的模具,用于制造造成凸起或控制形变。
凸模和凹模是通过模切或冲压等方法对金属、塑料等材料进行成形的重要工具。
二、凸模与凹模的使用场景凸模和凹模广泛应用于各种行业,如汽车制造、航空航天、电子设备、家电等。
在汽车制造过程中,凸模可用于车身、发动机、底盘等零部件的成型;凹模则可用于制作车身外壳、细节零件等。
在电子设备制造中,凸模可用于冲压电路板、塑料外壳等;凹模则可用于塑料外壳成型。
凸模和凹模的应用范围非常广泛,适用于各种材料的成型。
三、凸模与凹模的设计原则1.基于产品要求:模具的设计应基于产品要求,包括材料选择、尺寸要求、成型方式等。
凸模和凹模的设计应满足产品的形状、尺寸、质量要求。
2.结构合理:凸模和凹模的结构设计应具备合理性,包括凸模凹模的接触方式、固定方式、导向方式等。
模具应具有稳定性、刚度和刚性等特点,以确保成型的精度和质量。
3.使用寿命:凸模和凹模的设计应考虑到使用寿命,选择合适的材料和加工工艺,以延长模具的使用寿命。
同时,设计时应注意凸模和凹模的易损部位,采取合适的保护措施。
4.可制造性:凸模和凹模的设计应具备可制造性,即要考虑到加工、装配和维护的便捷性。
设计时应充分考虑到制造成本和制造难度,以提高生产效率。
四、凸模与凹模的常见问题1.磨损:凸模和凹模在使用过程中会因摩擦而磨损,导致模具失效。
解决方法可以是采用更耐磨的材料、表面处理等。
2.热变形:在高温条件下,凸模和凹模可能发生热变形,导致尺寸偏差。
解决方法可以是采用耐热材料、增加冷却系统等。
3.排气不畅:在成型过程中,凸模和凹模可能会困住气体,影响成型质量。
解决方法可以是增加通气孔、改进冲压方式等。
(完整版)冲压模具凸模工艺设计

冲压模具凸模工艺设计课程设计一、零件工艺分析二、确定工艺方案三、工艺计算四、选用加工设备五、填写工艺卡六、零件数控编程七、凹凸模线切割编程一、零件工艺分析该零件是复合模具的冲压凸模,用于冲压件的冲孔。
凸模结构属于三段式阶梯轴,其硬度和韧性要求较高,凸模刃口的耐磨性能要求较高。
凸模零件下段需要与凹凸模结构之间采用孔轴相配合,同时需要精准冲孔,对于零件的加工精度也有极高的技术要求。
本零件采用Cr12材料制成,可保证足够的刚度和强度,同时经过热处理工艺使材料硬度达58~62HRC,以加强凸模零件刃口的耐磨性。
查其主要配合尺寸为Ømm 、Ømm、Ømm,为IT6~IT10级。
为满足装配后冲孔精度要求,凸模工作部分与凹凸模的同轴度,三段阶梯轴Ø35mm、Ø30mm、Ø22mm之间有同轴度的形位公差要求,Ø22mm段凸模为IT6级,各表面粗糙度Ra0.4µm.本零件以Ø22mm轴段中心轴为设计基准,测量基准和定位基准,在车削一道工序中加工出三段阶梯轴凸模结构。
二、确定工艺方案由零件的形状表明,其为旋转件,所以车削为基本工序,凸模工作部分的平面可由铣削工序完成。
工件的基本尺寸加工经粗车、半精车、精车工序可达到要求。
根据凸模零件的精度要求精车作为首道工序,精车后的尺寸精度可达到IT6 ~ IT8级,表面粗糙度为Ra1.6 ~ 0.8µm。
车削时留0.15mm 的修光余量。
为了达到配合要求,需要对工件进行磨削工序,提高零件的配合尺寸精度,磨削后留0.05mm的修光余量。
1、毛坯尺寸选择根据零件的材料要求,材料选为Cr12轧钢件。
根据凸模零件的旋转轴径大小,留机械加工余量后可选定毛坯尺寸为Ø38mm轧钢棒料,长度为78mm,即Ø38mm×78mm。
2、工艺方案的确定根据各道加工工序,对其做不同的组合,排除顺序,即得出工艺方案。
弯曲模凸模的设计

弯曲模凸模的设计
一 材料的选择及热处理要求
选择凹模材料为Cr12MoV ,热处理硬度为58~60HRC 。
二 凸模结构尺寸
1.圆角半径
(1)凸模圆角半径。
弯曲件的相对圆角半径55.146<==t r ,取凸模圆角半径 6==r r p
2.凸模横向尺寸及公差
工件为内形尺寸标注,应以凸模为基准,间隙取在凹模上。
根据工件未注公差按IT14级计算,查公差表得62.0050+。
取凸模为IT7
根据公差表查得公差为0.03.
凸模横向尺寸为:
03
.000
465.50)62.075.050()75.0min ---=⨯+=∆+=p
p
L L P δδ( 凸模纵向尺寸应比弯曲件大,又比凹模小,因此取凸模纵向尺寸为95mm 。
3.凸模高度
(1)凸模总高度:
弯曲件的高度工h 为55mm ,料厚为4mm ,凸模安装高度1安h 为30mm ,
凸模安全距离安h 为15mm 。
凸模总高度为;
mm h h r h t h h 1101530864-55`-100=++++=++++=安安工凸
(2)凸模的长度和宽度方向尺寸为:取凸模长度尺寸L=50,
凸模宽度B=95。
凸模零件图如下图所示
Ra6.3
技术要求:
热处理硬度为
58-60HRC。
凸模板数控加工工艺设计

凸模板数控加工工艺设计图1.1 凸模板零件图1.1零件工艺性分析1.1.1 零件结构和功用分析凸模板如图1.1所示,凸模,又叫阳模,是成型塑件内表面的部件,在注射成型中通常装在注射机的动模板上,所以,习惯上又叫动模。
由于注塑成型中常让塑件留在凸模上,所以,在凸模上常装有顶出机构,以方便塑件的脱模。
凸模按结构形式,主要分为整体式凸模、组合式凸模。
该凸模板的结构简单,其结构特点是孔较多、两侧的腰形槽较小,因此在加工时需着重考虑对刀对零件精度的影响、切削力、转孔的速度和进给量等对零件的影响。
1.1.2 零件图纸分析1由零件图可知,该零件形状简单、腰子形键槽尺寸较小。
凸模板的尺寸精度要求并不是很高,采用铣削加工就可以达到要求,但是其形状位置精度要求较高,对称度0.03,同轴度要求为0.1,垂直度为0.04,由于模具对尺寸精度的要求比较高,加工中主要要保证的精度要求。
零件的尺寸标注采用统一的基准即设计基准,无多余尺寸与封闭尺寸。
1.1.3 主要技术要求分析(1)大平面的精度:上表面的粗糙度3.2,它的精度将直接影响到加工的精度精度。
(2)孔的位置精度:同一平面上导柱孔的位置度误差会影响生产出来的零件不合格,甚至合模时不能合上。
1.1.4 毛坯和材料的分析凸模板为单件,属于单件小批量生产。
凸模板材料为 YL15 ,毛坯重量约为0.9Kg。
毛坯为铝板切割而成,制作时毛坯的X轴方向加工余量为2mm公差为±0.02,毛坯的Y轴方向加工余量为20mm公差为±0.02,毛坯的Z轴方向加工余量为2mm 公差为±0.02。
加工毛坯时,为了保证加工面的加工精度,选择侧面的粗糙度较好一边为粗加工基准,从而保证其它面的垂直度和平行度。
加工其它两个侧面时,使用平口钳和已加工的侧面为定位基准,这样不仅可以使加工余量均匀而且保证加工精度。
在加工上表面和下表面时使用已加工面作为定位基准,满足“互为基准”及“基准重合”原则以保证加工精度。
- 1、下载文档前请自行甄别文档内容的完整性,平台不提供额外的编辑、内容补充、找答案等附加服务。
- 2、"仅部分预览"的文档,不可在线预览部分如存在完整性等问题,可反馈申请退款(可完整预览的文档不适用该条件!)。
- 3、如文档侵犯您的权益,请联系客服反馈,我们会尽快为您处理(人工客服工作时间:9:00-18:30)。
第二章 冲裁工艺与冲裁模设计
圆 形 凸 模
第二章 冲裁工艺与冲裁模设计
非圆形凸模
第二章 冲裁工艺与冲裁模设计
大、中型凸模
冲 小 孔 凸 模 保 护 与 导 向 结 构
第二章 冲裁工艺与冲裁模设计
1、9.定位板 2、 3、4.小凸模 5.冲击块 7.小压板 8.大压板 10.侧压块
超短凸模的小孔冲模
第二章
冲裁工艺及模具设计
4t d
五、凸模强度校核
(一)凸模抗压能力校核 (二)凸模纵向抗弯能力校核 d2 Lmax 95 圆凸模 一般凸模-无导向
Lmax
F
J 425 F
第二章 冲裁工艺与冲裁模设计
一、工作零件
1.凸模 (1)凸模的结构形式及其固定方法
1)圆形凸模:阶梯式、快换式 2)非圆形凸模: 阶梯式、直通式
本次课总结
1、凸模 (1)凸模的结构形式及其固定方法 (2)凸模长度计算 (3)凸模的镶拼结构
凸模的结构设计
一.凸模结构设计的三原则 (一)精确定位 (二)防止拔出 (三)防止转动 二.圆凸模的结构要素
三、凸模结构类型 (一)标准圆凸模 (二)凸缘式凸模 (三)铆装式凸模 (四)直通式凸模 (五)镶拼式凸模
第模长度的确定 (一)固定卸料方式的凸模长度 凸模长度按下式计算: L=h1+h2+h3+ h (二)弹压卸料方式的凸模长度 凸模长度按下式计算: L=h1+h4+h5-0.2mm
第二章 冲裁工艺与冲裁模设计
凸模长度尺寸
第二章 冲裁工艺与冲裁模设计
局 部 放 大 图
第二章 冲裁工艺与冲裁模设计
第二章 冲裁工艺与冲裁模设计
局 部 放 大 图
第二章 冲裁工艺与冲裁模设计
第二章 冲裁工艺与冲裁模设计
第二章 冲裁工艺与冲裁模设计
第二章 冲裁工艺与冲裁模设计
第二章 冲裁工艺与冲裁模设计
②采用短凸模的冲孔模 ③在冲模的其它结构设计与制造上采取保护小凸模措施
提高模架刚度和精度; 采用较大的冲裁间隙; 保证凸、凹模间隙的均匀性并减小工作表面粗糙度等; 采用斜刃壁凹模以减小冲裁力。
第二章 冲裁工艺与冲裁模设计
一、工作零件
1.凸模(续) (1)凸模的结构形式及其固定方法(续)
结构:
整体式、镶拼式、阶梯式、直通式、带护套式和快换式等。
3)大、中型凸模:整体式、镶拼式
台肩固定、螺钉压紧
台肩固定、铆接、
粘结剂浇注法固定 螺钉和销钉固定
4)冲小孔凸模:带护套式(见下页)
第二章 冲裁工艺与冲裁模设计
5)冲小孔凸模(续) 小孔:d<t或d<1mm的圆孔和面积A<1mm2的异形孔。 提高其强度和刚度的措施: ①冲小孔凸模加保护与导向:加保护套
固定方法:
台肩固定、铆接、螺钉和销钉固定,粘结剂浇注法固定等。
第二章 冲裁工艺与冲裁模设计
一、工作零件(续)
1.凸模(续) (2)凸模长度计算
当采用固定卸料板和导料板时,其凸模长度按下式计算: L h1 h2 h3 h
当采用弹压卸料板时,其凸模长度按下式计算: L h1 h2 t h (3)凸模的强度校核 冲裁凸模的强度效核计算公式见表2.9.2