旋转叶片的预应力模态分析
风力机叶片与整机的预应力振动模态分析
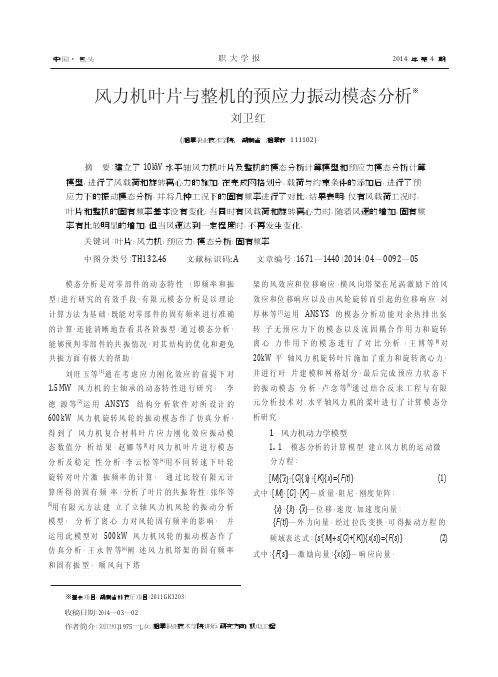
x } x x } {x } 中 国 · 包 头职 大 学 报 2014 年 第 4 期风力机叶片与整机的预应力振动模态分析※刘卫红(湘潭职业技术学院, 湖南省 湘潭市 111102)摘 要:建立了10kW 水平轴风力机叶片及整机的模态分析计算模型和预应力模态分析计算 模型,进行了风载荷和旋转离心力的施加,在完成网格划分、载荷与约束条件的添加后,进行了预 应力下的振动模态分析,并将几种工况下的固有频率进行了对比。
结果表明:仅有风载荷工况时, 叶片和整机的固有频率基本没有变化;当同时有风载荷和旋转离心力时,随着风速的增加,固有频 率有比较明显的增加,但当风速达到一定程度时,不再发生变化。
关键词:叶片;风力机;预应力;模态分析;固有频率 中图分类号:TH132.46文献标识码:A文章编号:1671—1440(2014)04—0092—05模态分析是对零部件的动态特性 (即频率和振 型)进行研究的有效手段,有限元模态分析是以理论 计算方法为基础,既能对零部件的固有频率进行准确 的计算,还能清晰地查看其各阶振型。
通过模态分析, 能够预判零部件的共振情况,对其结构的优化和避免 共振方面有极大的帮助。
刘旺玉等{1]通在考虑应力刚化效应的前提下对1.5M W 风力机的主轴承的动态特性进行研究。
李德 源等[2]运用ANS Y S 结构分析软件对所设计的600kW 风力机旋转风轮的振动模态作了仿真分析,得到了 风力机复合材料叶片应力刚化效应振动模态数值分 析结果。
赵娜等[3]对风力机叶片进行模态分析及稳定 性分析。
李云松等[4]用不同转速下叶轮旋转对叶片激 振频率的计算, 通过比较有限元计算所得的固有频 率,分析了叶片的共振特性。
张华等[5]用有限元方法建 立了立轴风力机风轮的振动分析模型, 分析了离心 力对风轮固有频率的影响, 并运用此模型对500kW 风力机风轮的振动模态作了仿真分析。
王永智等[6]阐 述风力机塔架的固有频率和固有振型、 顺风向下塔架的风效应和位移响应、横风向塔架在尾涡激励下的风 效应和位移响应以及由风轮旋转而引起的位移响应。
旋转预应力条件下的叶片流固耦合模态分析
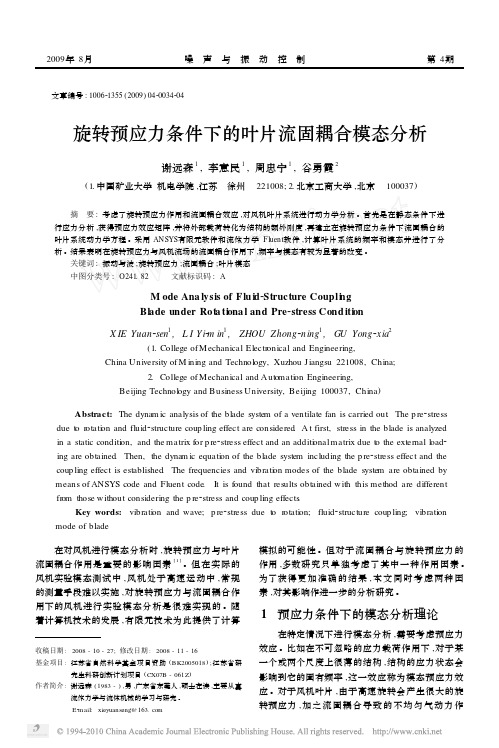
(1. College of M echanical Electronical and Engineering, China University of M ining and Technology, Xuzhou J iangsu 221008, China;
在特定情况下进行模态分析 ,需要考虑预应力 效应 。比如在不可忽略的应力载荷作用下 ,对于某 一个或两个尺度上很薄的结构 ,结构的应力状态会 影响到它的固有频率 ,这一效应称为模态预应力效 应 。对于风机叶片 ,由于高速旋转会产生很大的旋 转预应力 , 加之流固耦合导致的不均匀气动力作
旋转预应力条件下的叶片流固耦合模态分析
摘 要 : 考虑了旋转预应力作用和流固耦合效应 ,对风机叶片系统进行动力学分析 。首先是在静态条件下进 行应力分析 ,获得预应力效应矩阵 ,并将外部载荷转化为结构的额外刚度 ,再建立在旋转预应力条件下流固耦合的 叶片系统动力学方程 。采用 ANSYS有限元软件和流体力学 Fluent软件 ,计算叶片系统的频率和模态并进行了分 析 。结果表明在旋转预应力与风机流场的流固耦合作用下 ,频率与模态有较为显著的改变 。
37
图 5 考虑旋转预应力与流固耦合作用后前 3阶的叶片叶片振型 Fig. 5 the three step s of blade modal under the rotation stress and coup ling2flow condition
扭曲方向与静态时的模态振型相反 。限于篇幅 ,无 法给出全部模态的叶片振型对比 ,但总的说来 ,模 态振型基本上都产生了最大位移位置点转移 ,位移 值减少及振动方向改变等上述的三种状况 。考虑 到模态频率的改变不大 (不超过 5% ) ,可以认为这 种变化是由旋转预应力与流固耦合作用而导致的 。 限于实验条件 ,无法对更加大型的风机进行分析 , 但基于上述模拟可推断 : 对于大型风机 ,其叶片更 加细长 ,受旋转预应力与流固耦合的影响会更为严 重 ,预应力效应会相对加剧 ,其模态改变程度将会 更大 。
旋转叶片的模态及响应分析的开题报告

旋转叶片的模态及响应分析的开题报告一、研究背景及意义:旋转叶片作为风力发电机的核心部件,在运行中承受着复杂的载荷作用。
因此对于其模态及响应分析,非常重要。
通过对旋转叶片的模态及响应分析,可以了解到该组件的固有频率及振动行为等技术参数,为其设计及优化提供了一定的指导。
因此,开展旋转叶片的模态及响应分析研究对于提高风力发电机的安全稳定运行及发电效率有着重要意义。
二、研究内容:本研究旨在通过有限元模拟方法,研究旋转叶片的模态及响应行为。
具体内容包括:1.旋转叶片的有限元建模及验证;2.旋转叶片的静态分析,确定其静态刚度及扭转刚度等技术参数;3.旋转叶片的动态分析,研究其固有频率及振动行为;4.考虑旋转风场对叶片的扰动,分析旋转叶片的响应特性;5.研究旋转叶片的疲劳寿命及其他动态特性。
三、研究方法:本文主要采用有限元分析方法对旋转叶片进行建模及分析。
首先,通过Pro/E或Solidworks等软件进行旋转叶片的三维建模,并导入ANSYS等有限元分析软件进行网格划分。
接着进行静态及动态分析,得到旋转叶片的刚度及振动行为等参数。
最后,考虑旋转风场对叶片的影响,进行模拟模拟旋转叶片的响应。
四、预期结果:本文预期结果如下:1.得到旋转叶片的静态刚度及扭转刚度等技术参数;2.确定旋转叶片的固有频率及振动行为,分析其响应特性;3.分析旋转风场对叶片的影响,研究其响应特性;4.得到旋转叶片的疲劳寿命及其他动态特性;五、研究意义:本研究的意义主要是对风力发电机的优化设计及安全稳定运行提供一定的技术支持。
同时,通过本研究可以提高旋转叶片的性能及寿命,从而为风力发电行业的可持续发展贡献自己的力量。
毕业设计(论文)-预应力对高速旋转轮盘模态的影响分析[管理资料]
![毕业设计(论文)-预应力对高速旋转轮盘模态的影响分析[管理资料]](https://img.taocdn.com/s3/m/c9c4452276a20029bc642d30.png)
1 绪论问题的提出轮盘是发动机的重要零件之一,,转速高,其工作条件十分恶劣,设计要求高、,由于结构要求,大部分轮盘都开有中心孔或其它通气孔,还开有榫槽以便于与叶片联接,、轴向还有较大的温差,承受很大的热应力,,造成重大故障,其原因是轮盘产生了一阶伞型振动的共振,,轮盘结构日趋轻型化,轮盘做得很薄。
因此在高负荷、长寿命的工作情况下,轮盘因振动疲劳而断裂的故障有所增多。
旋转轮盘在高速旋转状态下会表现出与低速或非旋转状态下迥异的力学性能。
许多转子机械受刚度特性和非保守效应的阻尼特性的影响,其运转工况下的动态性能与静止时相比有很大的差异。
在进行高速旋转机械的转子系统动力设计时,需要对转动部件进行模态分析,求解出其固有频率和相应的模态振型。
通过合理的设计使其工作转速尽量远离转子系统的固有频率以避免由于共振而产生开裂破坏。
而对于高速部件,工作时由于受到离心力的影响,其固有频率跟静止时相比会有一定的变化。
为此,在进行模态分析时需要考虑离心力引起的预应力的影响。
如果忽略了预应力的影响就会使原有的系统遭到破坏,降低系统的稳定性和可靠性。
因此掌握高速旋转轮盘运转工况各种转速下的动力特性,对于了解不平衡振动响应以及可能出现的不稳定性等均有实际意义。
国内外研究现状轮盘是旋转机械中的常见部件,如水泵叶轮、风机叶轮轮盘、汽轮机转子上的轮盘等,它的强度、振动是设计、加工中重点考虑的问题之一。
由于轮盘结构复杂, 因此,在利用有限元分析计算时,建模是很重要的一个环节。
文献[1]采用在UG上进行几何建模,运用NASTRAN建立有限元模型,对轮盘进行静强度分析和模态分析。
for (。
它可以在windows95或windowsNT下运行。
、模态、屈曲、热传导、动力学、非线性和设计优化等各种类型分析。
,根据不同的几何模型提供了多种不同的生成和定义有限元模型工具,包括:网格划分、边界和载荷定义。
预应力技术能在不增加零件尺寸及材料性能的前提下,提高其承载能力,使用性能及工作寿命。
风力发电机旋转叶轮模态分析

( o lg o Me h nc l g n e ig n io o g,Xij n Ag iut r l Cl e f e c a ia En ie rn a d Ja t n ni g a r l a Un v riy c u ie st ,Ur mq u i
自由度 , 用 叶根 固定 连接 于轮 毂 的边 界条 件 , 应 叶片 的质量 矩 阵和 刚度矩 阵是 5 ×5 , 入 方 程可 以计 4 4代
可 以看 出, 每个节 点 的变形量均 归一 化处 理 , 假设 并
叶尖 节点 的位移 量是 1 。
表 2是某 1 5MW 风 力发 电机 的叶片 前 6阶摆 .
t o. w
Ke r s: m o lo h o o ;n t r lf e e c y wo d da ft e r t r a u a r qu n y;m u t— d yn m is;d a i tf e n libo y d a c yn m cs if ni g
叶 片是风 力发 电机 中关 键 零 部件 之一 , 结 构 其
关 系 着 整 个 风 力 发 电 机 的 平 稳 运 行 。兆 瓦 级 风 力 发
并 利用 Malb软件 对某 1 5MW 风力 发 电机 单 个 t a .
叶片和 叶轮 的振动 模 态进 行 了仿 真分 析 , 将 计 算 并
风 力发 电机旋 转 叶轮模 态 分析
汪 萍萍 , 新 维 崔
( 疆农业大学 机械交通学院 , 鲁木齐 新 乌 摘 805) 3 0 2
要 : 在 多体 动 力 学 理 论 的基 础 上 , 于 有 限 元 法 对 叶 片 进行 离散 化 , 立 了 风 力 发 电机 柔 性 叶 片 的 动力 学 方 基 建
旋转叶片动应力非接触测量方法研究综述

旋转叶片动应力非接触测量方法研究综述旋转叶片动应力是研究叶片在旋转过程中所受到的力和应力的重要参数,对于叶片的设计和优化具有重要的意义。
然而,传统的叶片动应力测量方法往往需要接触叶片表面,这样不仅会对叶片产生一定的干扰,还会增加测量的难度和复杂度。
因此,非接触测量方法成为了研究的热点。
在非接触测量方法中,光学方法是最常用的一种。
光学方法利用激光干涉技术或光栅投影技术,通过测量叶片表面的位移或形变来间接反推叶片的动应力。
其中,激光干涉技术是一种基于光的干涉原理,通过测量光的相位差来确定叶片表面的位移或形变。
这种方法具有高精度、高灵敏度的优点,能够实时监测叶片的动态应力变化。
光栅投影技术则是利用光栅投影仪投射光栅图案到叶片表面,通过观察光栅图案的形变来反推叶片的应力分布情况。
这种方法简单直观,适用于实时监测叶片的应力状态。
除了光学方法,磁力感应方法也是一种常用的非接触测量方法。
磁力感应方法是利用磁场的变化来间接反推叶片的应力状态。
通过在叶片表面附近布置磁场传感器,可以测量到叶片表面的磁场分布情况。
根据磁场的变化规律,可以推导出叶片的应力分布情况。
这种方法具有无接触、无干扰的优点,适用于恶劣环境下的叶片应力监测。
声波方法和红外热像法也是非接触测量叶片动应力的方法之一。
声波方法利用声波在叶片表面传播的速度和振动频率来反推叶片的应力状态。
红外热像法则是利用红外热像仪测量叶片表面的温度分布情况,通过分析温度的变化来间接推导叶片的应力分布情况。
这两种方法具有快速、灵敏的特点,适用于大范围、连续监测叶片的应力状态。
非接触测量叶片动应力的方法有多种,每种方法都有其适用的场景和优势。
随着科技的不断进步和创新,相信非接触测量方法在叶片动应力研究中的应用将会越来越广泛,为叶片设计和优化提供更加准确、可靠的数据支持。
电动四轮割草机核心部件预应力模态分析
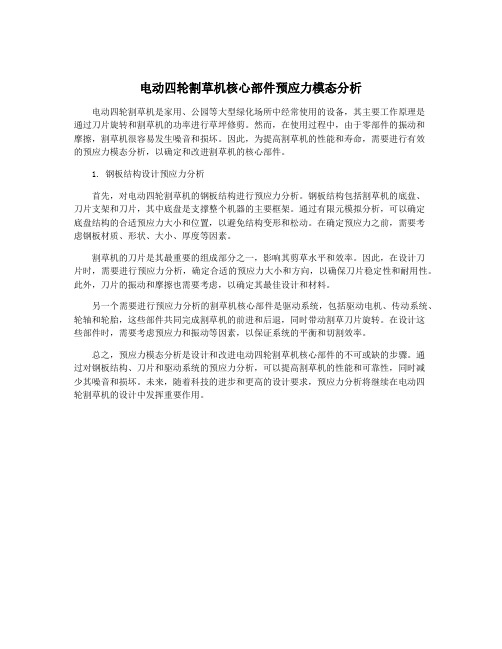
电动四轮割草机核心部件预应力模态分析
电动四轮割草机是家用、公园等大型绿化场所中经常使用的设备,其主要工作原理是
通过刀片旋转和割草机的功率进行草坪修剪。
然而,在使用过程中,由于零部件的振动和
摩擦,割草机很容易发生噪音和损坏。
因此,为提高割草机的性能和寿命,需要进行有效
的预应力模态分析,以确定和改进割草机的核心部件。
1. 钢板结构设计预应力分析
首先,对电动四轮割草机的钢板结构进行预应力分析。
钢板结构包括割草机的底盘、
刀片支架和刀片,其中底盘是支撑整个机器的主要框架。
通过有限元模拟分析,可以确定
底盘结构的合适预应力大小和位置,以避免结构变形和松动。
在确定预应力之前,需要考
虑钢板材质、形状、大小、厚度等因素。
割草机的刀片是其最重要的组成部分之一,影响其剪草水平和效率。
因此,在设计刀
片时,需要进行预应力分析,确定合适的预应力大小和方向,以确保刀片稳定性和耐用性。
此外,刀片的振动和摩擦也需要考虑,以确定其最佳设计和材料。
另一个需要进行预应力分析的割草机核心部件是驱动系统,包括驱动电机、传动系统、轮轴和轮胎,这些部件共同完成割草机的前进和后退,同时带动割草刀片旋转。
在设计这
些部件时,需要考虑预应力和振动等因素,以保证系统的平衡和切割效率。
总之,预应力模态分析是设计和改进电动四轮割草机核心部件的不可或缺的步骤。
通
过对钢板结构、刀片和驱动系统的预应力分析,可以提高割草机的性能和可靠性,同时减
少其噪音和损坏。
未来,随着科技的进步和更高的设计要求,预应力分析将继续在电动四
轮割草机的设计中发挥重要作用。
风力机叶片模态分析及稳定性分析

风力机叶片模态分析及稳定性分析来源:中国玻璃钢综合信息网近年来,“能源危机”越来越引起人们的重视,能源短缺使得可再生能源得到空前发展。
风能作为取之不尽用之不竭的可再生能源在近几年得到了迅速发展,世界上不少国家都把开发利用风能作为一项能源政策。
风机叶片是风力机的关键部件之一,目前大型风机叶片的材料主要是轻质高强、耐腐蚀性好、具有可设计性的复合材料,由于叶片采用复合材料铺层设计,结构异常复杂,单纯的经典理论解析计算已难以精确计算出叶片的强度和刚度,为此需要进行有限元的仿真模拟。
本文采用ANSYS的参数化语言APDL直接建模,然后赋材料属性、划分网格,进行叶片模态分析,较好地模拟了叶片的真实结构,计算了叶片在自由状态下的固有频率和在20RPM下的预应力频率。
最后加载极限载荷校核了叶片各截面稳定性。
1叶片模型的建立1.1建立几何模型叶片截面的翼型数据通过CA TIA导出,结合弦长和扭转角计算出实际叶片截面的坐标。
在AN-SYS的程序中形成如下格式:k,,838.309405,-83.92648,0k,,771.63901,-338.19972,0根据1MW叶片翼型的特点,将叶片分为45个截面,每个截面上有86个关键点。
通过Bspline命令将每个翼型上的关键点连成18条曲线,然后将叶片翼型上的曲线通过纵向直线连接。
最后通过Askin命令建立曲面,每两个翼型截面之间就有18个曲面,建完所有曲面就生成了叶片蒙皮的几何模型。
如图1(a)所示,再布置上主梁、腹板,形成整体叶片的几何模型。
1.2建立有限元模型在单元类型的选择上,根据叶片特点,主要采用shell91和shell99单元,其中shell91单元用于模拟夹芯结构。
在定义材料性能参数时,主要采用定义实常数的方式来模拟材料的性能、铺层角和铺层厚度。
之后选择合适的单元尺寸进行网格划分,最终形成叶片的有限元模型。
该模型共有21295个节点,共划分了7414个高精度的壳单元。
- 1、下载文档前请自行甄别文档内容的完整性,平台不提供额外的编辑、内容补充、找答案等附加服务。
- 2、"仅部分预览"的文档,不可在线预览部分如存在完整性等问题,可反馈申请退款(可完整预览的文档不适用该条件!)。
- 3、如文档侵犯您的权益,请联系客服反馈,我们会尽快为您处理(人工客服工作时间:9:00-18:30)。
旋转叶片的预应力模态分析1、首先打开输入参数
2、定义单元类型
点击add
选择shell
选择181单元3、定义材料
点Material Models
输入材料的弹性模量和泊松比
输入材料的密度
4、输入shell单元的截面
点击add/edit
输入上面定义的参数T
5、生成关键点
点in active cs,出现如下图框
一次输入四个关键点
点apply
输入第四个关键点,点Ok,如下图所示四个关键点
6、生成面
点area->arbitrary->Through KPs
一次选编号为1,2,3,4的关键点,点击OK,生成如下图的面
7、划分网格
点MeshTool
点Global->set,设置面单元的大小
输入0.005后,点击Ok。
点击Mesh,选择上面建好的面
点OK,生成单元
可以查看生成的shell单元厚度
8、求解
选择分析类型
选择静态分析
点击Ok
9、激活预应力选项
勾选Calculate prestress effects
点击Ok
10、添加位移约束
对线L4进行全约束
选择线,点OK 弹出
点OK
11、添加转速
点OK
12、求解
可以得到其应力图
13、进行模态分析
选择模态求解器
点OK
对模态进行选项分析
14、进行模态求解
可以查看前五阶的频率
***** INDEX OF DATA SETS ON RESULTS FILE *****
SET TIME/FREQ LOAD STEP SUBSTEP CUMULATIVE
1 46.571 1 1 1
2 155.97 1 2 2
3 182.01 1 3 3
4 247.33 1 4 4
5 305.27 1 5 5
第一阶阵型图
第二阶阵型图
第三阶阵型图
第四阶阵型图
第五阶阵型图
15、转速为OMIGA=1000是模态分析
前五阶模态
***** INDEX OF DATA SETS ON RESULTS FILE *****
SET TIME/FREQ LOAD STEP SUBSTEP CUMULATIVE
1 197.73 1 1 1
2 213.60 1 2 2
3 365.38 1 3 3
4 712.52 1 4 4
5 727.64 1 5 5
第一阶阵型图
第二阶阵型图
第三阶阵型图
第四阶阵型图
第五阶阵型图。