常用材料的应力应变曲线
常用混凝土受压应力—应变曲线的比较及应用
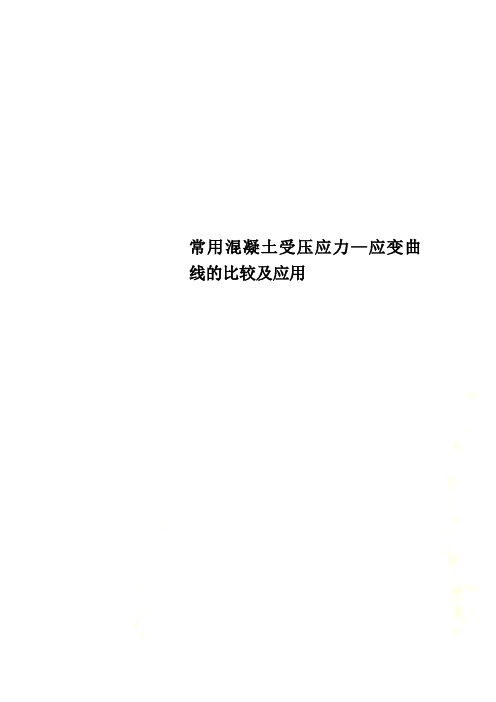
常用混凝土受压应力—应变曲线的比较及应用σσεεp 图1-2 Sargin曲线式中:εc1为相应于压应力峰值σ0的压应变εc1=-0.0022,εc1为从原点到压应力峰值点的割线模量, 1c E =0σ/0.0022,0E 为混凝土初始弹性模量;εu为混凝土极限压应变, 其大小与1c E 、0E 及εc1有关。
1.3清华过镇海曲线清华大学的过镇海教授在1982年结合自己多年的研究成果提出了自己的混凝土受压应力-应变曲线表达式,如图1-3所示。
第I 阶段中,OA 仍为二次抛物线,与德国人R üsch 提出的抛物线模式相同如下:])(2[2000εεεεσσ-⨯= )(0εε≤ (1-1) 第II 阶段中,下降段AB 用有理分式表示如下: 0200)1(εεεεαεεσσ+-=)(0u εεε<< (1-5)σσεε0图1-3 过镇海曲线εAB其中,α,0ε见下表:表1-1 材料 强度等级 水泥标号α 0ε/10-3普通混凝土 C20~C30 325 425 0.4 0.8 1.40 1.60 C40 425 2.0 1.80 陶粒混凝土 CL25 425 4.0 2.00 水泥砂浆 M30~M40325,4254.02.501.4 美国Hognestad 曲线美国人E.Hognestad 在1951年提出的应力-应变全曲线方程分为上升段和下降段,上升段与德国人R üsch 所提出模型的上升段相同,但是下降段采用一条斜率为负的直线来模拟,如图1-4所示,上升段表达式如下:])(2[2000εεεεσσ-⨯= )(0εε≤ (1-1)下降段表达式为:)1(000εεεεασσ---=u)(0u εεε<<(1-6)其中:α=0.015;εu =0.038经过化简以后,表达式变为如下: )()012.0014.0(u 00ε<ε<εε-σ=σ(1-7)σσ0ε2图1-4 Hongestad曲线0.85σ0εu对于以上四种常见的混凝土单轴受压应力—应变曲线先将其优缺点进行总结,如下表:表1-2优点 缺点中国规范(1)OA 段表达式比较简单,又能反映应力—应变曲线上升段的特点;AB 段则更为简单。
应力应变曲线材料力学_图文
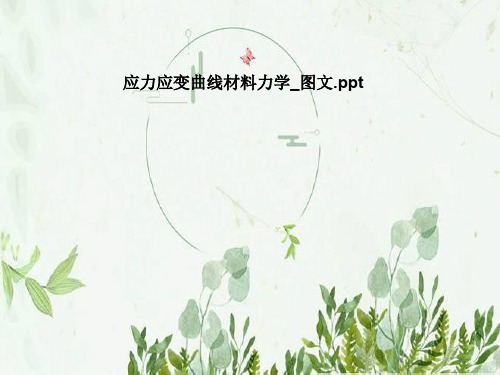
200 A(sp)
E=Etgy=atga a
O
O1 O2 0.1
e 0.2
金属材料的压缩试样,一般制成短圆柱形,柱的 高度约为直径的1.5 ~ 3倍,试样的上下平面有平行 度和光洁度的要求非金属材料,如混凝土、石料等 通常制成正方形。
低碳钢是塑性材料,压缩时的应力–应变图, 如图示。
在屈服以前,压缩时的曲线和拉伸时的曲线 基本重合,屈服以后随着压力的增大,试样被 压成“鼓形”,最后被压成“薄饼”而不发生 断裂,所以低碳钢压缩时无在卸载过程中 应力和应变是线形关系, 这就是卸载定律。
材料的比例极限增高, 延伸率降低,称之为冷作硬 化或加工硬化。
1、弹性范围内卸载、再加载 2、过弹性范围卸载、再加载
5、灰铸铁 对于脆性材料(铸铁),拉伸时的应力
应变曲线为微弯的曲线,没有屈服和径缩现 象,试件突然拉断。断后伸长率约为0.5%。 为典型的脆性材料。
σbt—拉伸强度极限(约为140MPa)。它是 衡量脆性材料(铸铁)拉伸的唯一强度指标。
二、压缩时的应力——应变曲线 1、试样及试验条件
§9-5
常温、静载
2、低碳钢压缩实验
s (MPa) 400
低碳钢压缩 应力应变曲线
E(sb)
C(ss上)
f1(f)
低碳钢拉伸
g
(se) B
D(ss下)
应力应变曲线
4.塑性指标 试件拉断后,弹性变形消失,但塑性变形仍保 留下来。工程上用试件拉断后遗留下来的变形 表示材料的塑性指标。常用的塑性指标有两个:
伸长率:
%
断面收缩率 :
%
L1 —试件拉断后的标距 L —是原标距 A1 —试件断口处的最小横截面面积 A —原横截面面积。
钢管材料的应力-应变关系曲线选用采用三折线模型
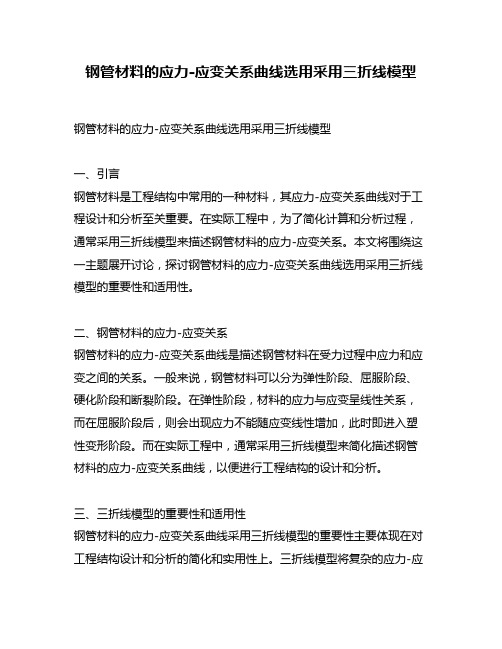
钢管材料的应力-应变关系曲线选用采用三折线模型钢管材料的应力-应变关系曲线选用采用三折线模型一、引言钢管材料是工程结构中常用的一种材料,其应力-应变关系曲线对于工程设计和分析至关重要。
在实际工程中,为了简化计算和分析过程,通常采用三折线模型来描述钢管材料的应力-应变关系。
本文将围绕这一主题展开讨论,探讨钢管材料的应力-应变关系曲线选用采用三折线模型的重要性和适用性。
二、钢管材料的应力-应变关系钢管材料的应力-应变关系曲线是描述钢管材料在受力过程中应力和应变之间的关系。
一般来说,钢管材料可以分为弹性阶段、屈服阶段、硬化阶段和断裂阶段。
在弹性阶段,材料的应力与应变呈线性关系,而在屈服阶段后,则会出现应力不能随应变线性增加,此时即进入塑性变形阶段。
而在实际工程中,通常采用三折线模型来简化描述钢管材料的应力-应变关系曲线,以便进行工程结构的设计和分析。
三、三折线模型的重要性和适用性钢管材料的应力-应变关系曲线采用三折线模型的重要性主要体现在对工程结构设计和分析的简化和实用性上。
三折线模型将复杂的应力-应变关系曲线简化为弹性阶段、屈服阶段和硬化阶段三段直线,极大地简化了工程分析和设计过程。
三折线模型在一定程度上也能够准确地描述钢管材料的力学性能,满足工程实际需求。
四、个人观点和理解在实际工程应用中,对钢管材料的力学性能要求越来越高,因此经常需要进行精确的分析和设计。
三折线模型作为一种简化描述钢管材料应力-应变关系的方法,具有明显的实用性和适用性。
然而,我个人认为在实际工程中,仍然需要结合实际情况进行具体分析,尽量准确地描述钢管材料的应力-应变关系,以确保工程设计和分析的准确性和可靠性。
五、总结与回顾本文围绕钢管材料的应力-应变关系曲线选用采用三折线模型展开了讨论,分析了三折线模型的重要性和适用性,并共享了个人观点和理解。
通过本文的阐述,我相信读者对于钢管材料的应力-应变关系曲线选用采用三折线模型有了更深入的理解,也希望能够为工程实践提供一定的借鉴和参考。
应力应变测试方法综述

应力应变测试方法综述引言:应力应变测试是材料力学性能测试中的重要内容之一,用于研究材料在外力作用下的变形行为。
本文将综述常见的应力应变测试方法,包括拉伸试验、压缩试验、剪切试验和扭转试验。
一、拉伸试验拉伸试验是最常用的应力应变测试方法,用于测量材料在拉伸条件下的力学性能。
试样被拉伸时,应力与应变之间的关系可以通过应力-应变曲线来描述。
常见的应力应变曲线包括弹性阶段、屈服阶段、塑性阶段和断裂阶段。
二、压缩试验压缩试验是将试样置于压力下进行测试的方法。
与拉伸试验类似,压缩试验可以得到材料的应力-应变曲线。
对于韧性材料,其应力-应变曲线呈现出相似的趋势,但压缩应力往往比拉伸应力大。
三、剪切试验剪切试验是用于测量材料在剪切载荷下的变形行为的方法。
试样在剪切力的作用下,发生切变变形。
剪切试验可以得到剪切应力与剪切应变之间的关系,常用的剪切应力-应变曲线包括线性阶段、屈服阶段、塑性阶段和断裂阶段。
四、扭转试验扭转试验是测量材料在扭转载荷下发生的变形行为的方法。
试样在扭转力的作用下发生扭转变形。
扭转试验可以得到剪切应力与剪切应变之间的关系,常见的应力应变曲线包括弹性阶段、屈服阶段、塑性阶段和断裂阶段。
五、其他应力应变测试方法除了上述常见的应力应变测试方法外,还有一些特殊的测试方法,如冲击试验、疲劳试验等。
冲击试验用于评估材料在高速冲击载荷下的性能,疲劳试验用于研究材料在循环载荷下的疲劳寿命。
六、应力应变测试的应用领域应力应变测试方法广泛应用于材料科学、机械工程、土木工程等领域。
它可以帮助工程师和科学家了解材料的力学性能,评估材料的可靠性和安全性。
在材料研发、产品设计和结构分析中,应力应变测试是不可或缺的工具。
结论:应力应变测试是研究材料力学性能的重要手段,常见的测试方法包括拉伸试验、压缩试验、剪切试验和扭转试验。
通过这些测试方法,可以获得材料的应力-应变曲线,从而评估材料的力学性能和变形行为。
应力应变测试在材料科学和工程领域具有广泛的应用,对于材料的研发和工程设计具有重要意义。
材料拉伸试验应力-应变曲线
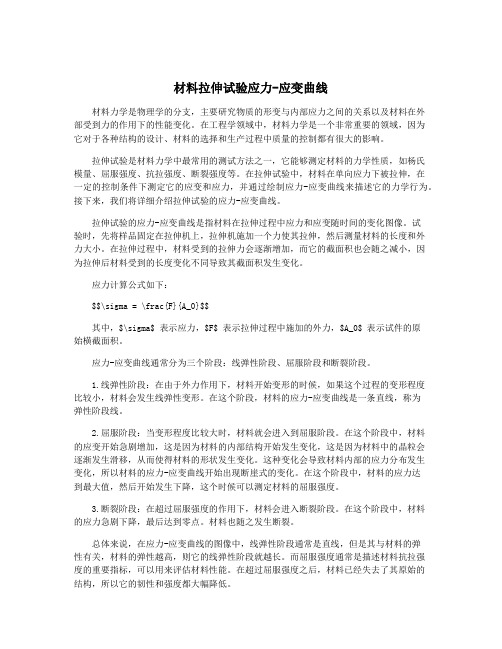
材料拉伸试验应力-应变曲线材料力学是物理学的分支,主要研究物质的形变与内部应力之间的关系以及材料在外部受到力的作用下的性能变化。
在工程学领域中,材料力学是一个非常重要的领域,因为它对于各种结构的设计、材料的选择和生产过程中质量的控制都有很大的影响。
拉伸试验是材料力学中最常用的测试方法之一,它能够测定材料的力学性质,如杨氏模量、屈服强度、抗拉强度、断裂强度等。
在拉伸试验中,材料在单向应力下被拉伸,在一定的控制条件下测定它的应变和应力,并通过绘制应力-应变曲线来描述它的力学行为。
接下来,我们将详细介绍拉伸试验的应力-应变曲线。
拉伸试验的应力-应变曲线是指材料在拉伸过程中应力和应变随时间的变化图像。
试验时,先将样品固定在拉伸机上,拉伸机施加一个力使其拉伸,然后测量材料的长度和外力大小。
在拉伸过程中,材料受到的拉伸力会逐渐增加,而它的截面积也会随之减小,因为拉伸后材料受到的长度变化不同导致其截面积发生变化。
应力计算公式如下:$$\sigma = \frac{F}{A_0}$$其中,$\sigma$ 表示应力,$F$ 表示拉伸过程中施加的外力,$A_0$ 表示试件的原始横截面积。
应力-应变曲线通常分为三个阶段:线弹性阶段、屈服阶段和断裂阶段。
1.线弹性阶段:在由于外力作用下,材料开始变形的时候,如果这个过程的变形程度比较小,材料会发生线弹性变形。
在这个阶段,材料的应力-应变曲线是一条直线,称为弹性阶段线。
2.屈服阶段:当变形程度比较大时,材料就会进入到屈服阶段。
在这个阶段中,材料的应变开始急剧增加,这是因为材料的内部结构开始发生变化,这是因为材料中的晶粒会逐渐发生滑移,从而使得材料的形状发生变化。
这种变化会导致材料内部的应力分布发生变化,所以材料的应力-应变曲线开始出现断崖式的变化。
在这个阶段中,材料的应力达到最大值,然后开始发生下降,这个时候可以测定材料的屈服强度。
3.断裂阶段:在超过屈服强度的作用下,材料会进入断裂阶段。
压铸adc12 应力应变曲线

压铸ADC12 应力应变曲线一、概述压铸ADC12合金是一种常用的铝合金材料,常用于汽车零部件、电子设备外壳等领域。
在应用过程中,了解其应力应变曲线对于材料的性能评价和工程设计至关重要。
本文将从基本概念、实验方法、结果分析等方面对压铸ADC12的应力应变曲线进行研究。
二、基本概念1. 应力应变曲线应力应变曲线是指在材料受到外力作用时,应力与应变之间的关系曲线。
通过绘制应力应变曲线可以得到材料在受力条件下的各种力学性能参数,如屈服强度、抗拉强度、伸长率等。
2. 压铸ADC12合金压铸ADC12合金是一种含铝高强度铸造铝合金,具有良好的流动性和耐热性,广泛应用于汽车和电子产品的制造。
三、实验方法为了研究压铸ADC12的应力应变曲线,需要进行相应的实验测试。
具体的实验方法包括:1. 材料准备:准备压铸ADC12合金标准试样。
2. 实验装置:使用万能材料试验机或拉伸试验机进行拉伸实验。
3. 实验步骤:将样品固定在试验机上,施加逐渐增大的拉伸力,记录相应的拉伸应变和拉伸应力。
4. 数据处理:根据实验数据绘制应力应变曲线图,并进行对比分析。
四、实验结果分析通过上述实验方法,得到了压铸ADC12合金的应力应变曲线图,并进行了相应的分析。
从图中可以看出,当拉伸应力逐渐增大时,拉伸应变也随之增大,但增长趋势呈现出一定的规律性。
在一定范围内,拉伸应变呈线性增长,而当拉伸应力接近一定数值时,拉伸应变迅速增加,出现了明显的屈服阶段。
此后,随着应力的继续增大,材料开始发生断裂,拉伸应变急剧增加,最终导致材料的断裂。
在实验中还可以得到拉伸强度、屈服强度、断裂强度等关键参数。
这些参数对于材料的工程设计和性能评价具有重要意义。
通过比较不同条件下的实验数据,可以确定压铸ADC12合金在不同应力状态下的性能表现,为工程应用提供参考依据。
五、结论通过对压铸ADC12合金的应力应变曲线进行实验研究,得到了该材料在受力条件下的关键性能参数。
应力应变曲线
应力应变曲线stress-strain curve在工程中,应力和应变是按下式计算的:应力(工程应力或名义应力)σ=P/A。
,应变(工程应变或名义应变)ε=(L-L。
)/L。
式中,P为载荷;A。
为试样的原始截面积;L。
为试样的原始标距长度;L 为试样变形后的长度。
这种应力-应变曲线通常称为工程应力-应变曲线,它与载荷-变形曲线相似,只是坐标不同。
从此曲线上,可以看出低碳钢的变形过程有如下特点:当应力低于σe 时,应力与试样的应变成正比,应力去除,变形消失,即试样处于弹性变形阶段,σe 为材料的弹性极限,它表示材料保持完全弹性变形的最大应力。
当应力超过σe 后,应力与应变之间的直线关系被破坏,并出现屈服平台或屈服齿。
如果卸载,试样的变形只能部分恢复,而保留一部分残余变形,即塑性变形,这说明钢的变形进入弹塑性变形阶段。
σs称为材料的屈服强度或屈服点,对于无明显屈服的金属材料,规定以产生0.2%残余变形的应力值为其屈服极限。
当应力超过σs后,试样发生明显而均匀的塑性变形,若使试样的应变增大,则必须增加应力值,这种随着塑性变形的增大,塑性变形抗力不断增加的现象称为加工硬化或形变强化。
当应力达到σb时试样的均匀变形阶段即告终止,此最大应力σb称为材料的强度极限或抗拉强度,它表示材料对最大均匀塑性变形的抗力。
在σb值之后,试样开始发生不均匀塑性变形并形成缩颈,应力下降,最后应力达到σk时试样断裂。
σk为材料的条件断裂强度,它表示材料对塑性的极限抗力。
上述应力-应变曲线中的应力和应变是以试样的初始尺寸进行计算的,事实上,在拉伸过程中试样的尺寸是在不断变化的,此时的真实应力S应该是瞬时载荷(P)除以试样的瞬时截面积(A),即:S=P/A;同样,真实应变e应该是瞬时伸长量除以瞬时长度de=dL/L。
下图是真应力-真应变曲线,它不像应力-应变曲线那样在载荷达到最大值后转而下降,而是继续上升直至断裂,这说明金属在塑性变形过程中不断地发生加工硬化,从而外加应力必须不断增高,才能使变形继续进行,即使在出现缩颈之后,缩颈处的真实应力仍在升高,这就排除了应力-应变曲线中应力下降的假象。
金属材料应力应变曲线优秀文档
称为屈服点(或屈服极限)。在屈服阶段卸载,将 出现不能消失的塑性变形。工程上一般不允许构 件发生塑性变形,并把塑性变形作为塑性材料破
坏的标志,所以屈服点 s是衡量材料强度的一
个重要指标。
(3)强化阶段 抗拉强度 b
经过屈服阶段后,曲线从c点又开始逐渐上升,说
应的应力值记作σe ,称为材料的弹性极限。
弹性极限与比例极限非常接近,工程实际中通常对二者不
作严格区分,而近似地用比例极限代替弹性极限。
(2)屈服阶段 屈服点 s
曲线超过b点后,出现了一段锯齿形曲线, 这—阶段应力没有增加,而应变依然在增加,材 料好像失去了抵抗变形的能力,把这种应力不增 加而应变显著增加的现象称作屈服,bc段称为屈
4.塑性指标 试件拉断后,弹性变形消失,但塑性变形仍保 留下来。工程上用试件拉断后遗留下来的变形 表示材料的塑性指标。常用的塑性指标有两个:
伸长率: L1 L 100 %
L
断面收缩率 : A A1 100 %
A L1 —试件拉断后的标距
L —是原标距 A1 —试件断口处的最小横截面面积 A —原横截面面积。
oa段是直线,应力与应变在此段成正比关系,材料
符合虎克定律,直线oa的斜率
就是材料
的弹性模量,直线部分最高点所对ta应n的应E力值记
作σp,称为材料的比例极限。曲线超过a点,图上
ab段已不再是直线,说明材料已不符合虎克定律。
但在ab段内卸载,变形也随之消失,说明ab段也
发生弹性变形,所以ab段称为弹性阶段。b点所对
变形的能力)( ) σbt—拉伸强度极限(约为140MPa)。
曲线最高点所对应的应力值记作, 称为材料的抗拉强度(或强度极限),它是衡量材料强度的又一个重要指均标匀。 塑性变形
不锈钢和钛合金应力应变曲线
不锈钢和钛合金应力应变曲线全文共四篇示例,供读者参考第一篇示例:不锈钢和钛合金是在工程领域中常见的两种金属材料,它们具有优异的性能和广泛的应用领域。
在工程设计和制造过程中,对材料的应力应变性能有着关键的要求,因此研究材料的应力应变曲线对于工程实践具有重要意义。
不锈钢是一种在一定条件下具有抗腐蚀性的钢,主要成分为铁、锰、铬等元素。
不锈钢具有较高的强度和硬度,同时具有良好的延展性和韧性。
不锈钢的应力应变曲线通常表现为线性弹性行为和屈服点后的塑性变形。
在应力作用下,不锈钢表现出较强的耐疲劳性能,能够承受较多的循环载荷而不导致塑性变形。
对于不锈钢和钛合金的应力应变曲线,可以通过材料拉伸试验进行研究。
拉伸试验是一种常见的材料力学性能测试方法,通过施加拉伸载荷使材料发生拉伸变形,从而测定材料的应力应变性能。
在拉伸试验中,通过测量载荷和位移的关系,可以得到材料的应力应变曲线。
根据应力应变曲线的不同特征,可以分析材料的力学性能和工程应用特点。
不锈钢和钛合金的应力应变曲线在不同加载条件下表现出不同的特点。
在常温下,不锈钢的应力应变曲线呈现出明显的屈服点和塑性变形区域,具有良好的抗拉伸性能。
而在高温下,不锈钢的应力应变曲线可能出现软化现象,导致材料的强度和硬度降低。
相比之下,钛合金具有较高的热稳定性,在高温下仍能保持良好的力学性能。
在工程实践中,了解不锈钢和钛合金的应力应变曲线对于正确选择材料、设计结构和预测材料的使用寿命具有重要意义。
通过对材料的应力应变曲线进行研究和分析,可以评估材料的力学性能、疲劳寿命和变形行为,为工程设计和制造提供重要参考。
针对不同应力应变条件下的不锈钢和钛合金材料,可以根据其特性进行合理的工程应用和改进设计,以实现更高的安全性和可靠性。
第二篇示例:不锈钢和钛合金是常见的金属材料,在工业领域中被广泛应用。
在工程实践中,了解这两种材料的应力应变曲线对于设计和使用具有重要意义。
本文将重点介绍不锈钢和钛合金的应力应变曲线及其特点。
10.9级m20高强螺栓应力应变曲线
10.9级M20高强螺栓应力应变曲线螺栓是一种常用的紧固件,广泛应用于建筑、机械、汽车等领域。
在许多工程中,尤其是在受力较大的场合,需要使用高强度的螺栓来保证连接的安全性和稳定性。
10.9级M20高强螺栓是一种常见的高强度螺栓,在工程中具有重要的作用。
本文将深入探讨10.9级M20高强螺栓的应力应变曲线,以期加深人们对该螺栓性能的理解。
1. 10.9级M20高强螺栓的材料特性10.9级M20高强螺栓是一种采用碳素钢制造的螺栓,其主要材料特性包括硬度高、强度大、耐磨性好等。
碳素钢是一种常见的结构钢,具有较高的抗拉强度和屈服强度,适合用于制造要求高强度的零件和部件。
10.9级M20高强螺栓正是利用了碳素钢的优良性能,具有出色的抗拉性能和扭矩扭转能力。
2. 应力应变曲线的基本概念应力应变曲线是材料力学中的重要概念,用于描述材料在受力过程中的应力和应变的关系。
通常情况下,应力应变曲线是通过在试验中施加不同的力,测量材料的应变和应力,然后绘制应力应变曲线图来表示。
应力应变曲线能够直观地反映材料的力学性能和性质,对于工程设计和材料选择具有重要指导意义。
3. 10.9级M20高强螺栓的应力应变曲线特点10.9级M20高强螺栓的应力应变曲线可以通过实验获得,一般来说,其特点包括以下几个方面:(1) 线性阶段:在应力较小的范围内,10.9级M20高强螺栓的应力应变曲线表现为线性关系,即应力和应变成正比。
这表明在小应力作用下,螺栓的变形是弹性变形,去除外力后能够完全恢复。
(2) 屈服阶段:随着外力的增大,10.9级M20高强螺栓的应力应变曲线将进入屈服阶段,即应变增大速率迅速增加,而应力不再呈线性增加。
这表明螺栓已经发生了塑性变形,继续增加外力将导致螺栓的应变持续增加而应力不再增加。
(3) 极限阶段:在继续增加外力的情况下,10.9级M20高强螺栓最终将达到其极限强度,此时螺栓将发生断裂或变形,应力应变曲线将出现急剧下降。