钢铁制件热镀锌表面缺陷分析及控制
热镀锌常见的质量缺点及产生原因
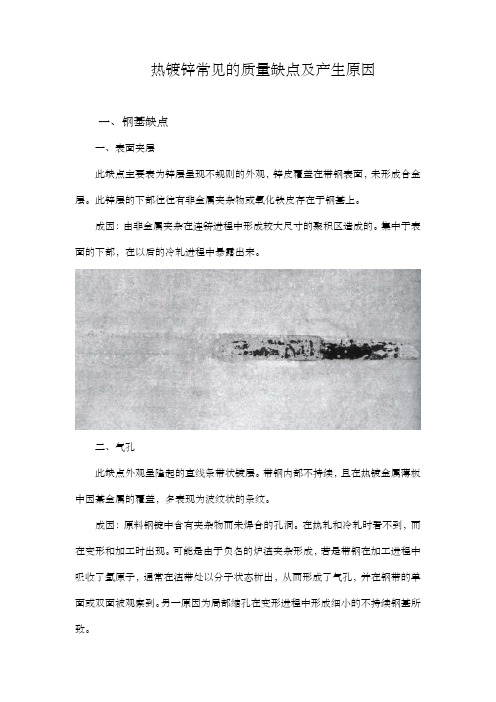
热镀锌常见的质量缺点及产生原因一、钢基缺点一、表面夹层此缺点主要表为锌层呈现不规则的外观,锌皮覆盖在带钢表面,未形成合金层。
此锌层的下部往往有非金属夹杂物或氧化铁皮存在于钢基上。
成因:由非金属夹杂在连铸进程中形成较大尺寸的聚积区造成的。
集中于表面的下部,在以后的冷轧进程中暴露出来。
二、气孔此缺点外观呈隆起的直线条带状镀层。
带钢内部不持续,且在热镀金属薄板中因棊金属的覆盖,多表现为波纹状的条纹。
成因:原料钢锭中含有夹杂物而未焊合的孔洞。
在热轧和冷轧时看不到,而在变形和加工时出现。
可能是由于负名的炉渣夹杂形成,若是带钢在加工进程中吸收了氢原子,通常在渣带处以分子状态析出,从而形成了气孔,并在钢带的单面或双面被观察到。
另一原因为局部缩孔在变形进程中形成细小的不持续钢基所致。
3、孔洞此缺点表现为贯穿带钢上下表面的材料不持续的外观。
成因:材料破裂的结果。
在热轧时,若是带钢横断面局部经受的压力过大,使其应变超过了钢的塑性(应变能力),就会出现孔洞。
带钢愈薄,这种情形就愈明显。
一般情形下,钢中的气孔、粗大的夹杂或轧入的异物、或轧前钢表面存在严峻的机械操作,均会引发带钢横截面强度减弱。
4、氧化铁皮缺点此缺点外观呈镀层下陷的细小的凹坑状和浮雕状,是在热轧时氧化铁皮坑和疤被轧入钢基内而引发。
氧化铁皮虽然可在酸洗时除掉,但不能肃除。
这些缺点的外观呈点状、线状,也可能呈大范围的片状。
残余氧化铁皮在酸洗时如未洗掉则在冷轧时被轧入表面,它们也呈点状、线状和大范围的片状,一般无规则地散布在带钢表面。
成因:在热轧带除鳞时由高压不压力不足造成的。
在热轧时残余的氧化铁皮被轧入带钢;在酸洗不足的情形下冷轧时被轧入。
二者的形态和散布密度不相同。
五、原板擦伤此缺点外观分为两种状态:1)热轧、酸洗、冷轧划痕多为沿轧制方向的沟状条纹,其划痕的镀锌层往往因合金层生长速度较快而致使该处镀层较厚。
在沟槽内一般无氧化铁皮存在。
成因:带钢热轧或冷轧时板面有金属屑碎片,这些金属碎片被推到其端部而形成缺点。
热镀锌带钢表面点状缺陷的分析和改进

11Metallurgical smelting冶金冶炼热镀锌带钢表面点状缺陷的分析和改进佟小磊(唐山钢铁集团责任有限公司,河北 唐山 063000)摘 要:随着社会经济的不断发展,越来越多的新技术和新工艺逐渐应用到热镀锌带钢生产活动当中。
而在热镀锌带制造过程中,由于受到点状缺陷的影响,难以提升整体的制作效果,同时还严重阻碍了相关生产活动的顺利进行,难以有效提升整体的工作质量和水平。
基于此,在本次研究中就结合热镀锌带钢表面点状缺陷形成的原因进行研究讨论,并提出相应的工作建议,加强改进,有效提升整体的生产质量。
通过加强热镀锌带钢表面点状缺陷的改进工作,有效提升其整体的工艺质量和水平。
关键词:热镀锌带钢;表面;点状缺陷;分析;改进中图分类号:TG174.4 文献标识码:A 文章编号:11-5004(2021)04-0011-2 收稿日期:2021-02作者简介:佟小磊,男,生于1993年,汉族,河北承德人,本科,助理工程师,研究方向:镀锌。
通过加强对冷轧厂镀锌产线,热镀锌带钢出现点状缺陷的分析,加强亮点缺陷和麻点缺陷的形貌观测和成分分析。
在整个分析活动开展过程中,结合相应的生产工艺,能够充分了解到出现亮点缺陷的原因,主要是因为锌层表面出现了凹坑。
而麻点缺陷则是因为板面出现了轻微的硌伤,最终导致其表面的完整性被破坏,严重影响了其整体的使用性能,同时也对整个生产活动带来了许多负面影响。
在热镀锌带钢生产活动开展过程中,常常会因为锌锅表面的锌渣或杂质飞溅,而导致钢表面不完整现象出现,存在许多不可控因素的影响。
随着社会经济的不断发展,热浸镀锌钢板凭借耐蚀性,加工性,涂装性被广泛地应用到家电,汽车,建筑等多个行业当中,具有非常广阔的应用前景。
而在其实际的生产过程中,会受到诸多不可控因素的影响,从而降低其整体的生产质量,严重降低了其整体的经济效益。
对此,本文就着重分析热镀锌带钢表面点状缺陷形成的原因,通过表面显微观察和元素分析,加强缺陷形成机理的推导工作,并提出相应的控制措施。
浅谈热镀锌表面缺陷分析及控制
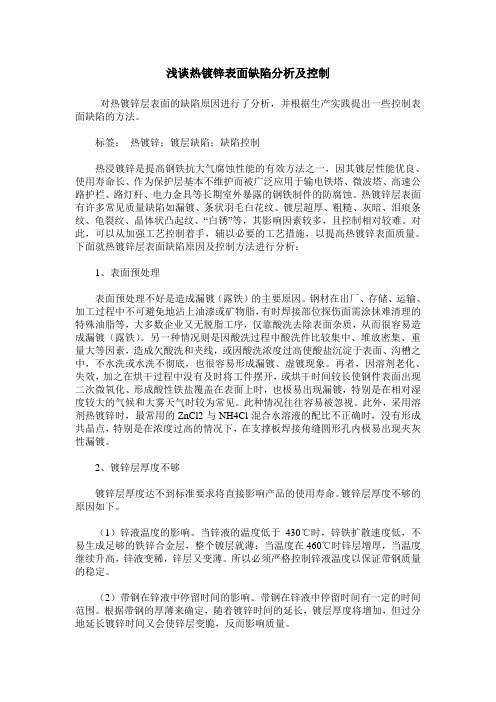
浅谈热镀锌表面缺陷分析及控制对热镀锌层表面的缺陷原因进行了分析,并根据生产实践提出一些控制表面缺陷的方法。
标签:热镀锌;镀层缺陷;缺陷控制热浸镀锌是提高钢铁抗大气腐蚀性能的有效方法之一,因其镀层性能优良、使用寿命长、作为保护层基本不维护而被广泛应用于输电铁塔、微波塔、高速公路护栏、路灯杆、电力金具等长期室外暴露的钢铁制件的防腐蚀。
热镀锌层表面有许多常见质量缺陷如漏镀、条状羽毛白花纹、镀层超厚、粗糙、灰暗、泪痕条纹、龟裂纹、晶体状凸起纹、“白锈”等,其影响因素较多,且控制相对较难。
对此,可以从加强工艺控制着手,辅以必要的工艺措施,以提高热镀锌表面质量。
下面就热镀锌层表面缺陷原因及控制方法进行分析:1、表面预处理表面预处理不好是造成漏镀(露铁)的主要原因。
钢材在出厂、存储、运输、加工过程中不可避免地沾上油漆或矿物脂,有时焊接部位探伤面需涂抹难清理的特殊油脂等,大多数企业又无脱脂工序,仅靠酸洗去除表面杂质,从而很容易造成漏镀(露铁)。
另一种情况则是因酸洗过程中酸洗件比较集中、堆放密集、重量大等因素,造成欠酸洗和夹线,或因酸洗浓度过高使酸盐沉淀于表面、沟槽之中,不水洗或水洗不彻底,也很容易形成漏镀、虚镀现象。
再者,因溶剂老化、失效,加之在烘干过程中没有及时将工件摆开,或烘干时间较长使钢件表面出现二次微氧化、形成酸性铁盐覆盖在表面上时,也极易出现漏镀,特别是在相对湿度较大的气候和大雾天气时较为常见。
此种情况往往容易被忽视。
此外,采用溶剂热镀锌时,最常用的ZnCl2与NH4Cl混合水溶液的配比不正确时,没有形成共晶点,特别是在浓度过高的情况下,在支撑板焊接角缝圆形孔内极易出现夹灰性漏镀。
2、镀锌层厚度不够镀锌层厚度达不到标准要求将直接影响产品的使用寿命。
镀锌层厚度不够的原因如下。
(1)锌液温度的影响。
当锌液的温度低于430℃时,锌铁扩散速度低,不易生成足够的铁锌合金层,整个镀层就薄;当温度在460℃时锌层增厚,当温度继续升高,锌液变稀,锌层又变薄。
连续热镀锌带钢表面缺陷原因分析及解决措施

刘超,助理工程师,2012年毕业于内蒙古科技大学材料成型及控制工程专业。
E-mail:liuchao@连续热镀锌带钢表面缺陷原因分析及解决措施刘超(鞍钢蒂森克虏伯汽车钢有限公司,辽宁大连116600)摘要:介绍了连续热镀锌带钢镀层表面存在的各类常见缺陷,包括锌渣、气刀条痕、划伤、热褶皱、光整羽痕和压印等,并分析了缺陷产生的原因,针对缺陷提出了解决措施。
实践表明,热镀锌带钢的表面质量明显改善,O5板合格率达到了90%以上。
关键词:连续热镀锌;表面缺陷;产生原因;控制措施中图分类号:TG356文献标识码:A文章编号:1006-4613(2017)06-0062-04Analysis on Causes Leading to Defects on the Surface ofContinuous Hot-dip Galvanizing Steel Strips andCountermeasures for the DefectsLiu Chao(Thyssen Krupp Auto Steel Company Limited of Ansteel,Dalian 116600,Liaoning,China )Abstract :Various kinds of common defects on the surface of continuous hot-dip galvanizingsteel strips including zinc slag,steaks caused by air knife,scratches,wrinkles in hot condition,pinnate marks due to the finishing process and impressions were introduced while the causes leading to the defects were analyzed.Then countermeasures for dealing with the defects were proposed.The production practice showed that the surface quality of the hot-dip galvanizing steel strips was obviously improved and the qualified rate of O5steel sheets was over 90%.Key words :continuous hot-dip galvanizing ;surface defects ;causes ;controlling counter-measures热浸镀锌是应用最广泛的防腐蚀技术之一,可以大幅度提高钢铁材料的耐大气腐蚀性能。
热镀锌带钢表面锌渣缺陷形成分析及改进措施
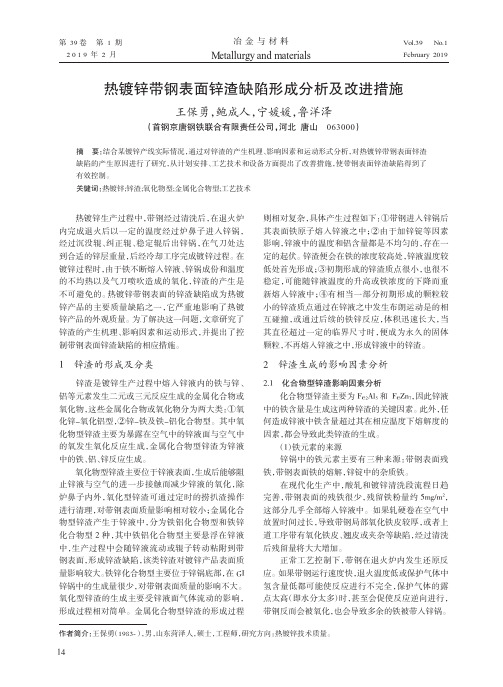
冶金与材料第39卷热镀锌带钢表面锌渣缺陷形成分析及改进措施王保勇,鲍成人,宁媛媛,鲁洋泽(首钢京唐钢铁联合有限责任公司,河北唐山063000)摘要:结合某镀锌产线实际情况,通过对锌渣的产生机理、影响因素和运动形式分析,对热镀锌带钢表面锌渣缺陷的产生原因进行了研究,从计划安排、工艺技术和设备方面提出了改善措施,使带钢表面锌渣缺陷得到了有效控制。
关键词:热镀锌;锌渣;氧化物型;金属化合物型;工艺技术作者简介:王保勇(1983-),男,山东菏泽人,硕士,工程师,研究方向:热镀锌技术质量。
第39卷第1期2019年2月Vol.39No.1February 2019冶金与材料M etallurgy and materials热镀锌生产过程中,带钢经过清洗后,在退火炉内完成退火后以一定的温度经过炉鼻子进入锌锅,经过沉没辊、纠正辊、稳定辊后出锌锅,在气刀处达到合适的锌层重量,后经冷却工序完成镀锌过程。
在镀锌过程时,由于铁不断熔入锌液、锌锅成份和温度的不均热以及气刀喷吹造成的氧化,锌渣的产生是不可避免的。
热镀锌带钢表面的锌渣缺陷成为热镀锌产品的主要质量缺陷之一,它严重地影响了热镀锌产品的外观质量。
为了解决这一问题,文章研究了锌渣的产生机理、影响因素和运动形式,并提出了控制带钢表面锌渣缺陷的相应措施。
1锌渣的形成及分类锌渣是镀锌生产过程中熔入锌液内的铁与锌、铝等元素发生二元或三元反应生成的金属化合物或氧化物,这些金属化合物或氧化物分为两大类:①氧化锌-氧化铝型,②锌-铁及铁-铝化合物型。
其中氧化物型锌渣主要为暴露在空气中的锌液面与空气中的氧发生氧化反应生成,金属化合物型锌渣为锌液中的铁、铝、锌反应生成。
氧化物型锌渣主要位于锌液表面,生成后能够阻止锌液与空气的进一步接触而减少锌液的氧化,除炉鼻子内外,氧化型锌渣可通过定时的捞扒渣操作进行清理,对带钢表面质量影响相对较小;金属化合物型锌渣产生于锌液中,分为铁铝化合物型和铁锌化合物型2种,其中铁铝化合物型主要悬浮在锌液中,生产过程中会随锌液流动或辊子转动粘附到带钢表面,形成锌渣缺陷,该类锌渣对镀锌产品表面质量影响较大。
热镀锌缺陷及事故处理
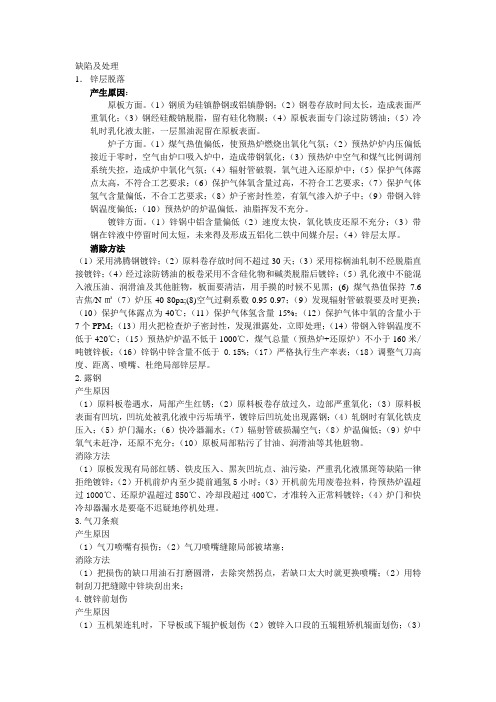
缺陷及处理1.锌层脱落产生原因:原板方面。
(1)钢质为硅镇静钢或铝镇静钢;(2)钢卷存放时间太长,造成表面严重氧化;(3)钢经硅酸钠脱脂,留有硅化物膜;(4)原板表面专门涂过防锈油;(5)冷轧时乳化液太脏,一层黑油泥留在原板表面。
炉子方面。
(1)煤气热值偏低,使预热炉燃烧出氧化气氛;(2)预热炉炉内压偏低接近于零时,空气由炉口吸入炉中,造成带钢氧化;(3)预热炉中空气和煤气比例调剂系统失控,造成炉中氧化气氛;(4)辐射管破裂,氧气进入还原炉中;(5)保护气体露点太高,不符合工艺要求;(6)保护气体氧含量过高,不符合工艺要求;(7)保护气体氢气含量偏低,不合工艺要求;(8)炉子密封性差,有氧气渗入炉子中;(9)带钢入锌锅温度偏低;(10)预热炉的炉温偏低,油脂挥发不充分。
镀锌方面。
(1)锌锅中铝含量偏低(2)速度太快,氧化铁皮还原不充分;(3)带钢在锌液中停留时间太短,未来得及形成五铝化二铁中间媒介层;(4)锌层太厚。
消除方法(1)采用沸腾钢镀锌;(2)原料卷存放时间不超过30天;(3)采用棕榈油轧制不经脱脂直接镀锌;(4)经过涂防锈油的板卷采用不含硅化物和碱类脱脂后镀锌;(5)乳化液中不能混入液压油、润滑油及其他脏物,板面要清洁,用手摸的时候不见黑;(6) 煤气热值保持7.6吉焦/N㎡(7)炉压40-80pa;(8)空气过剩系数0.95-0.97;(9)发现辐射管破裂要及时更换;(10)保护气体露点为-40℃;(11)保护气体氢含量15%;(12)保护气体中氧的含量小于7个PPM;(13)用火把检查炉子密封性,发现泄露处,立即处理;(14)带钢入锌锅温度不低于420℃;(15)预热炉炉温不低于1000℃,煤气总量(预热炉+还原炉)不小于160米/吨镀锌板;(16)锌锅中锌含量不低于0.15%;(17)严格执行生产率表;(18)调整气刀高度、距离、喷嘴、杜绝局部锌层厚。
2.露钢产生原因(1)原料板卷遇水,局部产生红锈;(2)原料板卷存放过久,边部严重氧化;(3)原料板表面有凹坑,凹坑处被乳化液中污垢填平,镀锌后凹坑处出现露钢;(4)轧钢时有氧化铁皮压入;(5)炉门漏水;(6)快冷器漏水;(7)辐射管破损漏空气;(8)炉温偏低;(9)炉中氧气未赶净,还原不充分;(10)原板局部粘污了甘油、润滑油等其他脏物。
热镀锌表面亮点缺陷分析及控制
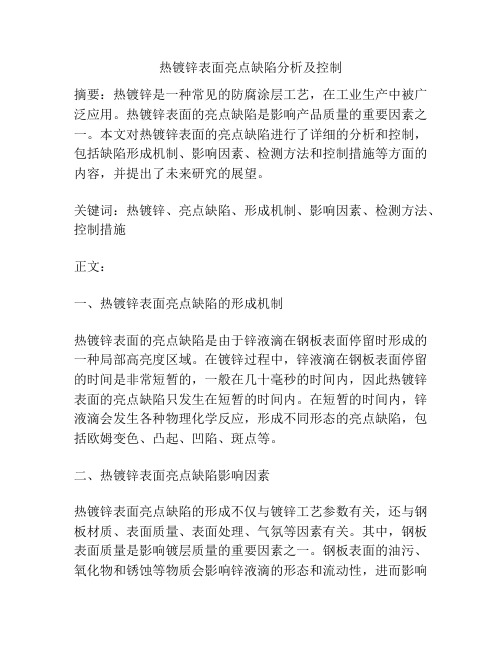
热镀锌表面亮点缺陷分析及控制摘要:热镀锌是一种常见的防腐涂层工艺,在工业生产中被广泛应用。
热镀锌表面的亮点缺陷是影响产品质量的重要因素之一。
本文对热镀锌表面的亮点缺陷进行了详细的分析和控制,包括缺陷形成机制、影响因素、检测方法和控制措施等方面的内容,并提出了未来研究的展望。
关键词:热镀锌、亮点缺陷、形成机制、影响因素、检测方法、控制措施正文:一、热镀锌表面亮点缺陷的形成机制热镀锌表面的亮点缺陷是由于锌液滴在钢板表面停留时形成的一种局部高亮度区域。
在镀锌过程中,锌液滴在钢板表面停留的时间是非常短暂的,一般在几十毫秒的时间内,因此热镀锌表面的亮点缺陷只发生在短暂的时间内。
在短暂的时间内,锌液滴会发生各种物理化学反应,形成不同形态的亮点缺陷,包括欧姆变色、凸起、凹陷、斑点等。
二、热镀锌表面亮点缺陷影响因素热镀锌表面亮点缺陷的形成不仅与镀锌工艺参数有关,还与钢板材质、表面质量、表面处理、气氛等因素有关。
其中,钢板表面质量是影响镀层质量的重要因素之一。
钢板表面的油污、氧化物和锈蚀等物质会影响锌液滴的形态和流动性,进而影响热镀锌表面的亮点缺陷。
表面处理和气氛的质量也会影响亮点缺陷的形成。
三、热镀锌表面亮点缺陷的检测方法热镀锌表面亮点缺陷的检测方法包括目视检查、显微镜检查、金相分析和电子显微镜分析等方法。
其中,显微镜和电子显微镜分析是目前比较常用的方法。
四、热镀锌表面亮点缺陷的控制措施热镀锌表面亮点缺陷的控制措施包括选用优质的钢板、提高表面质量、控制气氛质量、优化镀锌工艺参数等方面。
要控制热镀锌表面的亮点缺陷,需要将不同的控制措施结合起来,达到系统性、综合性的控制效果。
五、未来研究展望热镀锌表面亮点缺陷的控制是热镀锌工艺研究的一个重要方向。
未来的研究可以从以下几个方面入手:研究亮点缺陷的形成机制和影响因素;开发新的表面处理技术和气氛控制技术,提高表面质量和气氛稳定性;研究镀锌工艺参数与亮点缺陷的关系,以及优化工艺参数,控制亮点缺陷的形成。
热镀锌带钢表面缺陷检查
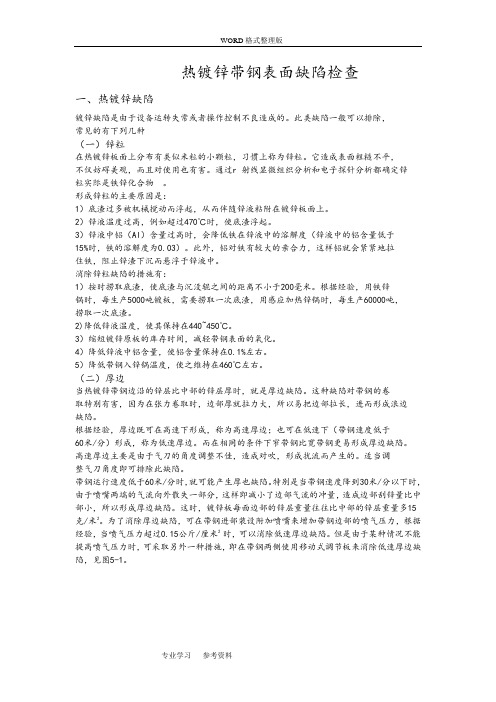
热镀锌带钢表面缺陷检查一、热镀锌缺陷镀锌缺陷是由于设备运转失常或者操作控制不良造成的。
此类缺陷一般可以排除,常见的有下列几种(一)锌粒在热镀锌板面上分布有类似米粒的小颗粒,习惯上称为锌粒。
它造成表面粗糙不平,不仅妨碍美观,而且对使用也有害。
通过r 射线显微组织分析和电子探针分析都确定锌粒实际是铁锌化合物。
形成锌粒的主要原因是:1)底渣过多被机械搅动而浮起,从而伴随锌液粘附在镀锌板面上。
2)锌液温度过高,例如超过470℃时,使底渣浮起。
3)锌液中铝(Al)含量过高时,会降低铁在锌液中的溶解度(锌液中的铝含量低于15%时,铁的溶解度为0.03)。
此外,铝对铁有较大的亲合力,这样铝就会紧紧地拉住铁,阻止锌渣下沉而悬浮于锌液中。
消除锌粒缺陷的措施有:1)按时捞取底渣,使底渣与沉没辊之间的距离不小于200毫米。
根据经验,用铁锌锅时,每生产5000吨镀板,需要捞取一次底渣,用感应加热锌锅时,每生产60000吨,捞取一次底渣。
2)降低锌液温度,使其保持在440~450℃。
3)缩短镀锌原板的库存时间,减轻带钢表面的氧化。
4)降低锌液中铝含量,使铝含量保持在0.1%左右。
5)降低带钢入锌锅温度,使之维持在460℃左右。
(二)厚边当热镀锌带钢边沿的锌层比中部的锌层厚时,就是厚边缺陷。
这种缺陷对带钢的卷取特别有害,因为在张力卷取时,边部厚就拉力大,所以易把边部拉长,进而形成浪边缺陷。
根据经验,厚边既可在高速下形成,称为高速厚边;也可在低速下(带钢速度低于60米/分)形成,称为低速厚边。
而在相同的条件下窄带钢比宽带钢更易形成厚边缺陷。
高速厚边主要是由于气刀的角度调整不佳,造成对吹,形成扰流而产生的。
适当调整气刀角度即可排除此缺陷。
带钢运行速度低于60米/分时,就可能产生厚也缺陷。
特别是当带钢速度降到30米/分以下时,由于喷嘴两端的气流向外散失一部分,这样即减小了边部气流的冲量,造成边部刮锌量比中部小,所以形成厚边缺陷。
- 1、下载文档前请自行甄别文档内容的完整性,平台不提供额外的编辑、内容补充、找答案等附加服务。
- 2、"仅部分预览"的文档,不可在线预览部分如存在完整性等问题,可反馈申请退款(可完整预览的文档不适用该条件!)。
- 3、如文档侵犯您的权益,请联系客服反馈,我们会尽快为您处理(人工客服工作时间:9:00-18:30)。
材 料 保 护 MATERIALS PROTECTION
Vol. 36 No. 12 Dec. 2003
钢铁制件热镀锌表面缺陷分析及控制
苗立贤1 ,冯 玲2 ,史宪海1 ,刘 颖3 (1. 河南省驻马店热浸镀铝厂总师办 ,河南 驻马店 463000 ;2. 河南省驻马店市农校 ,河南
由参考文献[6 ]Zn2Ni2Fe 三相系统的相图可知 ,450 ℃下热镀 锌时 ,Ni 含量为 0. 055 %的条件下 ,锌液中形成浮渣的可能性是 非常小的 ,因此 ,要十分讲究其添加方法与合金和锌液中的 Ni 含 量[7] 。
悬浮在锌液表面而且十分粘稠 ,极容易粘附在钢铁制件上 ,严重 损害了镀层质量 ,此时仅靠降温捞渣是无济于事的 。一旦发现这 种情况应立即停止添加合金 ,同时采取锌液净化措施 ,把铝含量 降下来 ,在情况不严重时可以考虑适当延长空冷时间 ,以防止镀 层表面急剧水冷后出现气泡和皱纹 。
(3) 锡 、铅 一般情况下锌锭中不含锡 ,仅有微量的铅 。近 年来一些锌合金供应商为了使镀锌温度下降 ,并获得白亮镀层 , 在所谓的多元合金中加入锡 、铅 。当锌液中添加了这种多元合金 后 ,锌液面在 430 ℃下可以出现镜面并能保持 10~20 min ,但在热 镀钢铁制件时 ,镀层表面会出现羽毛状花斑和细小难看的白斑 , 含锡 、铅的合金添加量一旦达到 0. 5 %时 ,就会出现锌花 ,锌灰明 显增多 ,生产效率也下降了 ,给企业造成不应有的损失 。铅和锡 因其熔点低 ,含量过高时 ,迅速使锌液的凝固温度下降 ,在镀锌层 冷却过程中极易形成粗大的结晶和出现龟裂纹现象 ,影响锌层的 表面光滑度和耐腐蚀性能 。晶间腐蚀对杂质铅最敏感 ,腐蚀速度 随镀层中铅含量的增加而加快 ,铅量达到 0. 02 %就会出现晶间腐 蚀 ,在镀层中沿晶界破裂而失去附着力 ,严重时表面会出现黄豆 粒大小的气泡 。因此我们在应用锌铝合金或多元合金时一定要 弄清楚其中铅 、锡 、铝的含量 ,决定是否在锌液中添加 。
在热镀焊接变截面 、不同直径的同一路灯杆时 ,有时在相同 的温度和提升速度下 ,表面会出现不同的质量状况 ,如凹坑 、桔子 皮皱纹状 ,这主要是由不同材质造成的 。文献 [ 4 ]描述了这种表 面凸凹不平的原因 ,在镀锌过程中 ,钢基表面的凸凹会使 Fe2Zn 合金层的生长形态发生变化 。热镀锌层在不含硅钢的不规则表 面上的生长特点是 :在凸起处 ,刚形成的ζ晶体相分离 ,使液态锌 可穿透到ζ/δ界面附近 ,支持ζ相连续快速生长而形成迸发状晶 粒 。在凹入区域 ,由于生长受扩散控制 ,得到紧密稳定的结构 。 其原因在于在凹处由于体积收缩 ,产生足够的压应力使 Fe2Zn 合 金相层稳定 。一旦稳定层形成 ,无论产生稳定性的原因是否存 在 ,稳定性都会保持下来 ,此外在表面凹陷处具有支持富铁层形 成的条件 。由于提供了大面积的表面供体积收缩的合金层生长 , 使反应所需的铁的供应充足 ,而同时锌的供应却由于锌难以进入 凹陷处而减少 ,在这些位置 ,经常发现厚的Γ 层 。钢基体表面弥 散性分布的凸起或凹坑麻点 ,一般是因为锈蚀严重或者过度酸洗 形成的 。对于电力金具类产品 ,应消除机加工时留下的刀纹 ,或 通过布轮抛光等措施来消除表面凹坑麻点 。
54
钢铁制件热镀锌表面缺陷分析及控制
增长而使ζ相破裂并被挤出凹处开始形成较厚的ζ相 ,形成凸起 物[3] ,此时钢基体龟裂纹凹陷则变为龟裂 (晶体) 凸起纹 。根据化 验分析 ,凸起物是η相中镶嵌着ζ相颗粒 。有时钢铁制件在轧制 过程中 ,表面氧化皮可能进入钢基体 ,在此后的酸洗中也会造成 表面不平 。夹层铁皮在热镀时会出现黄豆大小的气泡 ,断续出现 在镀层下面 。因此用户应选用表面质量好的钢材 。
热浸镀锌是提高钢铁抗大气腐蚀性能的有效方法之一 ,因其 镀层性能优良 、使用寿命长 、作为保护层基本不维护而被广泛应 用于输电铁塔 、微波塔 、高速公路护栏 、路灯杆 、电力金具等长期 室外暴露的钢铁制件的防腐蚀 。热镀锌层表面有许多常见质量 缺陷如漏镀 、条状羽毛白花纹 、镀层超厚 、粗糙 、灰暗 、泪痕条纹 、 龟裂纹 、晶体状凸起纹 、“白锈”等 ,其影响因素较多 ,且控制相对 较难 。对此 ,可以从加强工艺控制着手 ,辅以必要的工艺措施 ,以 提高热镀锌表面质量 。
[ 收稿日期 ] 2003 - 05 - 22
图 圣德林效应曲线图 Si 含量在 0. 05 %~0. 10 %或大于 0. 30 %时 ,镀层不再是层 次分明的由钢基体到τ、δ、ζ和η相的正常组织 ,而呈现出很厚的 不连续的片状ζ相为主的组织 ,有点类似低硅钢在 500 ℃时 Fe2 Zn 剧烈反应时所得到的组织[1] 。钢铁制件在常规热镀锌温度 455 ℃下浸镀时 ,从工件浸入锌液到工件热透 、助镀剂反应完毕 、 清除锌液表面的锌灰后提升工件 ,整个浸镀一般不少于 1. 5~3. 0 min ,在这种温度和时间下 ,在含 Si 量处于圣德林效应区内 ,随着 浸镀时间的增加 ,镀层将会更厚 。为此 ,热镀锌行业一向认为 ,适 宜热镀锌的钢材只能是含硅量低的沸腾钢 ,含硅量高的镇静钢被 认为是不适宜热镀锌的 。但现在钢铁企业逐渐普及连续铸钢技 术 ,用此技术生产的钢大都是含硅量较高的镇静钢或半镇静钢 。 如某企业热镀国内某大型钢铁企业生产 Q235 钢制的护栏板 、输 电单柱钢管塔和路灯杆时 ,在 455 ℃锌液温度下 ,时常出现大片 灰暗镀层 ,以及在出锌液面后约 0. 5 min 左右时间内 ,出现泪痕状 条纹 ,其流动性很差 ,使产品质量明显降低 ,锌耗增加 ,这种现象 可能与基体中 P 和 S 的含量较高有关[2] 。钢基体中元素偏析和 钢锭头部以及局部碳化物聚集都是造成片状灰暗层的主要因素 。 而在轧制过程中水淬不充分 、不合理则是造成镀层出现明显龟裂 纹的因素 。在热镀路灯杆 (圆形) 时常出现一些竖直形细小间断 性木纹状条纹 ,这种缺陷可能是在卷制时表面出现裂纹所致 。在 热镀时 ,合金层ζ相的生长速度比δ1 相快 ,在一定时间后 δ, 1 相生 长速度加快 ,因此在凹处开始形成较厚的ζ相 ,由于δ1 相的快速
(2) 铝 铝是热镀锌中最常用的添加元素 。在锌液中添加 不同浓度的铝可以获得不同性质的镀锌层 。一般认为热镀锌时 , 在锌液中加入 < 1 %(质量分数 ,下同) 的铝可以起到下列作用 : ① 提高镀层光亮性 ; ②减少锌液面的氧化 ; ③抑制脆性 。而 在 实 际 生 产 中 , 锌 液 中 含 有 0. 005 %~0. 020 %Al 就可以达到镀层光亮的目的 ,并可减少锌液 表面的氧化和锌灰的产生 。必须指出 ,添加铝的方式宜采用 Zn2 Al 中间合金的添加方式 。往往由于添加的中间合金的质量问题 以及添加铝和锌铝合金的方法不当或过快 ,导致锌液中形成大量 的铝 、铁化合物 ,这种密度小于锌液的锌铝铁三元“面渣”或颗粒
1. 3 锌液中其他成分
锌液中夹杂过多其他金属成分或有害元素 ,可能造成如锌渣 颗粒粘附在镀层表面和一些非正常的花纹 、龟裂纹等缺陷 。
(1) 铁 热镀锌一段时间后 ,钢制件表面会出现锌堆积和微 小锌渣颗粒 ,致使镀层表面粗糙 ,光滑度也随之下降 。这种微小 颗粒一般是 Fe2Zn 合金颗粒渣 。在 450 ℃镀锌时 ,铁在锌液中的 饱和溶解度为 0. 02 % ,锌液中铁的含量超过此值时 ,会析出ζ和 δ1 相形成锌渣 ,由于这种颗粒渣与锌密度差异不大 ,其聚集下沉 很慢 ,悬浮在锌液中的合金渣会夹在锌液中被制件带出 ,镶嵌在 镀层中 ,从而影响镀锌层的表面质量 。锌液中铁的来源一般有锌 锅的腐蚀 、制件的溶解 、助镀剂中的铁离子及制件上的铁盐 4 方 面 。因此 ,为了获得平整光滑的镀层 ,必须严格控制锌液中铁含 量 ,减少铁离子的带入 ,控制锌液温度 ,避免锌液温度的忽高忽 低 ,降低锌锅的腐蚀速度等 。一般锌液中铁含量应 < 0. 08 %[5] , 当锌液中铁含量 > 0. 20 %时 ,必须降温静置并打捞锌渣 。
1. 2 钢铁制件基体
钢铁制件基体状态不良往往造成镀层灰暗 、龟裂纹等表面缺 陷 。即使在镀锌工艺合理 、稳定的情况下 ,钢铁制件的基体状态 对镀锌层表面质量影响也十分突出 。时常因钢基体的化学成分 碳 、硅 、磷等元素的影响和冶炼轧制过程中某种因素的影响 ,使其 有害元素偏析 ,从而在镀层表面出现片状灰暗镀层 、龟裂纹 、晶体 状凸起纹 、木纹状条纹 、夹皮裂纹等明显缺陷 。
(4) 镍 锌液中的镍是为了解决热锓镀中因钢材中含硅出 现的圣德林现象而作为合金元素加入的 ,是近几年来国内逐渐认 同的解决镀层色差现象的一种新工艺技术 。在锌液中添加锌镍 合金可有效地降低锌和铁原子在ζ相中的扩散速度 ,因而可以控 制浸镀层厚度的增长 ,当锌液中 Ni 含量为 0. 06 %时 ζ, 相金属间 化合物中 Ni 含量可达 0. 8 % ,加入 Ni 后ζ相的厚度增长明显得到 控制 δ, 相的厚度相应有所增加 ,因而可有效地控制浸镀层厚度 的增长 ,并能改善锌液的流动性能 。因此 ,使用锌镍合金进行热 浸镀锌的镀层厚度更加均匀 ,表面更光亮 ,锌花少 。
驻马店 463000 ;3. 广西南宁送变电公司铁塔厂 ,广西 南宁 530031)
[ 摘 要 ] 对钢铁制件热镀锌层表面的缺陷原因进行了分析 ,并根据生产实践提出一些控制表面缺陷的方法 。 [ 关键词 ] 钢铁制件 ;热镀锌 ;镀层缺陷 ;缺陷控制 [ 中图分类号 ] TG174. 43 [ 文献标识码 ] B [ 文章编号 ] 1001 - 1560 (2003) 12 - 0056 - 03
在生产中 ,如果使用的 Zn2Ni 合金没有形成共晶结构或添加 方法不当 ,则可能造成锌液中出现浮渣 、小颗粒锌渣现象 。形成 此种现象的机理现已得到证实 ,即在使用 Zn2Ni 合金进行热浸镀 的锌液中 ,有 2 种不同的金属间化合物即 :ζ相 (含有~0. 8 %Ni 的 FeZn13同晶体) 和 Γ2 相 (含~3. 0 %Ni 的 Fe6Ni5Zn89 同晶体) 。其 中 ,形成Γ2 相是造成锌液中悬浮小颗粒渣子形成的根本原因 。 从金属学角度上讲 ,Γ2 相的形成即悬浮渣粒的出现取决于锌液 中镍的含量及液体金属的温度 。