(工艺技术)制盐工艺
制盐工艺流程

制盐工艺流程
制盐的基本工艺流程包括以下几个步骤:
1. 采矿:从盐矿或咸水源等地采集盐矿石或咸水。
2. 粉碎:将采集到的盐矿石通过粉碎机或破碎机进行碎石,使其达到适合后续处理的粒度。
3. 溶解:将粉碎后的盐矿石或咸水投入到溶解槽内,加入适量的清水搅拌,使盐矿石中的盐分溶解在水中。
4. 澄清:将溶解后的盐水通过澄清池或澄清器进行澄清处理,去除其中的悬浮物和杂质。
5. 浓缩:将澄清后的盐水通过蒸发器或浓缩器进行蒸发,逐渐提高溶液中盐的浓度。
6. 结晶:将浓缩后的盐水通过结晶器或结晶槽进行结晶处理,使盐逐渐从溶液中晶体化。
7. 分离:将结晶后的盐通过离心机或过滤器进行分离,分离出晶体盐和母液。
8. 干燥:将分离出的盐晶进行烘干处理,使其达到要求的水分含量。
9. 筛分:对烘干后的盐晶进行筛分,去除不符合规格的颗粒。
10. 包装:将筛分后符合规格的盐晶进行包装,以便运输和销售。
以上是制盐的基本工艺流程,不同制盐厂可能会有所差异,具体的工艺流程还需根据不同的盐矿石性质和生产要求进行调整。
工业制盐的工艺流程优化探究

关键词:工业制盐;工艺流程;优化本研究对工业制盐流程的优化主要表现为两个方面:一是提高各项制盐工艺流程的效率,二是减轻制盐工艺浓盐水对环境的污染,两者都需要加强对新技术的开发和应用。
目前,我国大部分制盐企业都采用海水作为原料,再经后续的精制生产精制盐,不仅增大了原盐的消耗,还降低了制盐效率。
本研究首先介绍传统制盐工艺的流程和3项制盐新技术,其次针对制盐工艺流程的优化提出建议。
1传统工业制盐工艺流程传统的海盐制盐工艺[1]采用日晒法,也叫“滩晒法”,就是通过在沿海滩涂筑坝的方式开辟盐田,并利用潮汐涨退的自然规律将海水引入所筑的池中。
池中的海水经过一段时间的曝晒后蒸发成浓度较高的卤水,当卤水的浓度达到一定程度时,会析出氯化钠晶体,就是原盐。
总体而言,海盐的传统制盐工艺流程一般有纳潮、制卤、结晶、收盐四大工序。
1.1纳潮纳潮就是对制盐原料也就是海水的获取过程。
充足的原料供应是制盐工艺流程顺利进行的前提条件。
纳潮包括两种方式:一是借助海水潮汐涨退的自然规律主动纳潮,二是利用设备提供动力,使海水被动纳潮。
主动纳潮是在海水涨潮时引领海水沿所砌筑池子的潮沟自然流入,而被动纳潮是利用轴流泵的动力将海水先抽起、再引到砌筑的池中。
两者相比,自然纳潮受限于自然条件,但是节约成本;动力纳潮有不受自然条件限制的优势,但成本较高。
1.2制卤制卤是在所砌筑的蒸发池中进行的。
要注意观察池中每日海水的蒸发量,记录蒸发池中卤水的走水深度,当卤水浓度逐渐提高并达到一定的程度时,就会得到浓缩的饱和卤水。
1.3结晶饱和卤水继续蒸发和浓缩,浓度会逐渐提高,达到饱和时会析出氯化钠晶体。
该过程如果持续进行,溶液一直维持浓度过饱和的状态,就能持续地析出晶体。
1.4收盐将得到的晶体以人工或者机械的方式收起堆坨,以便后期的精盐处理。
除了上述海盐的制盐工艺外,还有井矿盐和湖盐的制盐工艺。
井矿盐的制盐工艺流程主要分为采卤和制盐。
采卤的方法有很多,例如提捞法、气举法、钻井水溶开采法、自喷采卤等。
盐田法工艺流程

盐田法工艺流程
《盐田法工艺流程》
盐田法是一种古老的制盐工艺,主要流行于中国南部的滨海地区。
盐田法工艺流程主要分为收集海水、晒制盐卤、熬制盐、精制加工等几个主要步骤。
首先是收集海水。
盐田地区通常选择潮汐丰富的海域,使用盐田作为盐田法的基地。
工人们利用人力或机械设备将海水引入盐田,填满浅池。
接着是晒制盐卤。
在盛满海水的浅池中,海水经过蒸发,留下盐卤。
盐卤会在太阳下逐渐结晶,形成白色的盐花。
盐花会被人工捞起,这就是最原始的盐制方法。
然后是熬制盐。
将捞起的盐花放入锅中熬制。
锅中的盐花会在慢慢熬制的过程中变成颗粒状的盐粒,这些盐粒就是我们常见的食用盐。
最后是精制加工。
经过熬制的盐还需要经过一系列的加工,比如洗涤、磨粉、筛选等步骤,使盐粒更加纯净、细腻。
整个盐田法制盐工艺流程虽然简单,但却需要对海水、天气、温度等因素有着极高的要求。
同时也是一种对自然及手工工艺的完美融合,体现了古老的智慧和勤劳的民俗风情。
如今这项古老的工艺虽已被现代化的制盐方式替代,但在一些地方,仍然保留着盐田法工艺流程,以传承和弘扬这种古老的文化。
精制盐的制造工艺

精制盐的制造工艺精制盐是指从天然海水或地下盐水中提取纯度更高、杂质更少、营养更丰富的食盐。
其制造过程相比于普通食盐更加复杂,需要经过多次加工、筛选和过滤等环节,以确保最终产品的纯度和品质。
精制盐的制造需要先将天然海水或地下盐水通过管道输送至工厂内的盐池中。
盐池是一个大型的开放式水池,用于收集海水或地下盐水。
这些水源都含有丰富的钠、钙、镁等矿物质,但同时也含有各种杂质和微生物,因此需要进行后续的处理。
接下来,盐池中的海水或地下盐水需要进行加热。
加热的目的是将其中的水分蒸发掉,以便于后续的盐结晶过程。
加热的方式一般有两种,一种是直接用蒸汽进行加热,另一种是利用太阳能进行加热。
前者的加热速度更快,但需要消耗大量的能源,而后者则更加环保,但加热速度较慢。
当海水或地下盐水中的水分蒸发掉后,剩余的盐分就开始结晶。
这个过程需要在密闭的结晶器中进行,以避免外界杂质的污染。
结晶器内的温度和湿度需要严格控制,以保证结晶的效果。
一般来说,结晶过程需要持续数天到数周不等,直到结晶器内的盐结晶达到一定的密度。
当盐结晶达到一定密度后,需要通过机械或手工方式进行筛选和过滤。
这个环节的目的是去除其中的杂质和微生物,以保证最终产品的纯度。
在这个过程中,需要使用不同规格的筛网进行筛选,以去除不同粒径的杂质。
同时,还需要通过活性炭等吸附剂进行过滤,以去除其中的有害物质和异味。
经过多次加工和过滤后的盐,需要进行包装和贴标签。
包装的方式一般有袋装和散装两种,其中袋装的盐更加方便携带和储存,而散装的盐则更加适合用于大型餐饮场所。
贴标签的目的是说明产品的名称、产地、纯度等信息,以便于消费者购买和使用。
精制盐的制造过程相比于普通食盐更加复杂和耗时,需要多次加工和过滤,以确保最终产品的纯度和品质。
在制造过程中,需要严格控制温度、湿度、筛选等环节,以避免外界杂质的污染。
同时,包装和贴标签也是制造过程中不可缺少的环节,以确保产品的销售和使用。
食用盐生产工艺
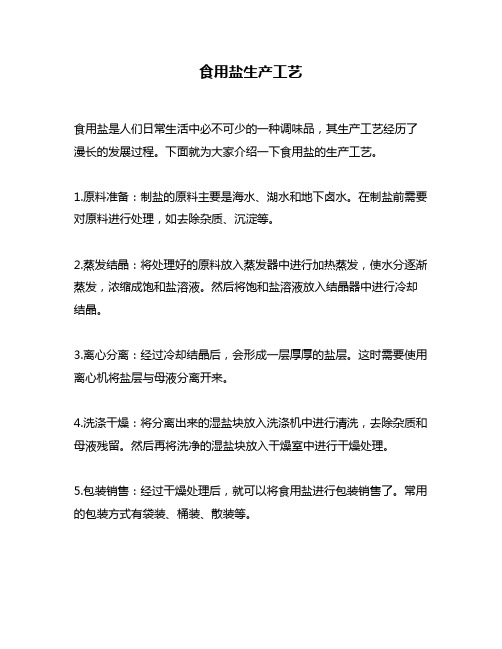
食用盐是人们日常生活中盐的生产工艺。
1.原料准备:制盐的原料主要是海水、湖水和地下卤水。在制盐前需要对原料进行处理,如去除杂质、沉淀等。
2.蒸发结晶:将处理好的原料放入蒸发器中进行加热蒸发,使水分逐渐蒸发,浓缩成饱和盐溶液。然后将饱和盐溶液放入结晶器中进行冷却结晶。
以上就是食用盐的生产工艺,其中涉及到多个环节,每个环节都需要严格控制,以确保生产出符合国家标准的优质食用盐。
3.离心分离:经过冷却结晶后,会形成一层厚厚的盐层。这时需要使用离心机将盐层与母液分离开来。
4.洗涤干燥:将分离出来的湿盐块放入洗涤机中进行清洗,去除杂质和母液残留。然后再将洗净的湿盐块放入干燥室中进行干燥处理。
5.包装销售:经过干燥处理后,就可以将食用盐进行包装销售了。常用的包装方式有袋装、桶装、散装等。
四效真空蒸发结晶制盐工艺

四效真空蒸发结晶制盐工艺1.引言1.1 概述概述四效真空蒸发结晶制盐工艺是一种先进而高效的盐制造工艺,该工艺利用了真空蒸发和结晶的原理,通过多效蒸发器的装置,将海水或盐湖水进行多次蒸发,最终实现盐的结晶和提取。
相比传统的盐制造工艺,四效真空蒸发结晶制盐工艺具有许多显著的优势,如高效能利用、节能减排、产品质量优良等。
本文将详细介绍四效真空蒸发结晶制盐工艺的工艺原理和工艺步骤。
首先,我们将对该工艺的原理进行深入探讨,包括了多效蒸发器的工作原理以及盐结晶的原理。
其次,我们将详细描述工艺步骤,包括了原料准备、预处理、蒸发结晶和产品收集等。
通过对每个步骤的详细说明,读者将能够全面了解四效真空蒸发结晶制盐工艺的操作过程和关键环节。
最后,我们将总结该工艺的效果,并对其未来的发展进行展望。
四效真空蒸发结晶制盐工艺在盐制造领域具有广阔的应用前景,其高效能利用和环保特性将对传统盐制造工艺进行深刻的改革。
而随着科技的不断进步和工艺的不断完善,该工艺在未来还将进一步提高盐的生产效率和产品质量。
通过本文的阅读与研究,读者将能够深入了解四效真空蒸发结晶制盐工艺的工艺特点和优势,并为相关行业的从业人员和相关研究者提供宝贵的参考和借鉴。
正文内容将在接下来的章节中进行详细介绍,希望读者能够通过本文的阅读,对该工艺有更深入的了解。
1.2 文章结构本文主要介绍了四效真空蒸发结晶制盐工艺的工艺原理和工艺步骤,并对其进行了综合分析和评价。
文章分为引言、正文和结论三个部分。
在引言部分,首先对文章的内容进行了概述,简要介绍了四效真空蒸发结晶制盐工艺的背景和重要性。
接着介绍了文章的结构,即本文的组织框架和章节安排。
最后,明确了本文的目的,即通过深入研究四效真空蒸发结晶制盐工艺,为其在实际应用中的优化提供参考和指导。
正文部分是本文的核心部分,主要包括两个小节,分别是工艺原理和工艺步骤。
在工艺原理部分,详细介绍了四效真空蒸发结晶制盐工艺的基本原理和背后的化学、物理过程。
制盐的工艺
制盐的工艺制盐的工艺可以分为海盐和岩盐两种。
海盐的制作工艺主要分为以下几个步骤:第一步是采集海水。
采集海水需要选择纯净的海域,远离工业区和污染源,以确保所采集的海水质量良好。
海水采集后,需要进行过滤和沉淀,去除其中的杂质和悬浮物。
第二步是浓缩海水。
经过过滤和沉淀的海水进入浓缩池进行蒸发。
通常有两种浓缩方法,一种是自然蒸发,将海水倒入大型浅盐田,通过太阳辐射和风力使水分蒸发,逐渐浓缩;另一种是人工蒸发,将海水加热,加速水分的蒸发。
第三步是结晶析出盐晶体。
浓缩后的海水进入结晶池,通过提高温度或降低压力的方法,使海水中的盐类随之结晶析出。
通常会有多次结晶过程,每次结晶都会进一步提高盐度,产生更纯净的盐晶体。
第四步是盐晶体的提取和洗涤。
提取盐晶体通常采用离心机或过滤器,将盐晶固体与未结晶的海水分离。
提取后的盐晶体经过洗涤,去除表面的杂质和残余的海水。
第五步是盐晶体的晾晒和干燥。
洗涤后的盐晶体需要进行晾晒和干燥,以去除残余的水分。
晾晒过程中,盐晶体需要经常翻动,以确保晾晒均匀;干燥则通过自然风力或者人工通风进行。
第六步是盐的包装和储存。
经过晾晒和干燥的盐晶体,需要进行包装和储存以保持其质量。
通常以塑料袋、纸箱或者桶装包装,并存放在干燥通风的库房中,避免潮湿和受潮。
岩盐是通过地下盐矿的开采和提纯过程获得的。
岩盐的制作工艺主要包括以下几个步骤:第一步是盐矿的开采。
岩盐一般存在于地下深处,需要进行开采工作。
开采可以采用矿山巷道方式或者溶蚀洞穴方式进行。
开采过程中需要注意安全,避免坍塌和事故发生。
第二步是破碎和碾磨。
开采得到的盐矿经过破碎设备进行破碎,将盐矿破碎成合适的颗粒大小。
然后通过碾磨机械设备进行碾磨,使盐矿变成细小的颗粒。
第三步是溶解和提纯。
经过破碎和碾磨的盐矿进入溶解池,加入适量的水进行溶解。
溶解后的溶液通过离心或过滤的方式去除杂质和杂质,提高纯度。
第四步是盐水的蒸发。
提纯后的盐水进入蒸发器,进行蒸发过程。
制盐工艺流程
制盐工艺流程
《制盐工艺流程》
制盐是一项古老而重要的工艺,早在古代人类就已经开始利用海水或地下盐水制取盐。
随着科技的发展,制盐工艺也得到了不断的改进和完善。
制盐的工艺流程一般包括以下几个步骤:
1. 浓缩海水或盐水:首先需要将海水或地下盐水进行浓缩。
这一步通常通过蒸发的方式进行,可以利用太阳能或者燃煤、燃气等能源进行加热,将水分蒸发掉,留下含有盐分的浓缩液体。
2. 结晶析出:浓缩液体中的盐分会在适当的温度条件下结晶析出。
这一步可以利用结晶器或者其他设备,通过控制温度和搅拌等操作来促进盐分的结晶。
3. 过滤和干燥:将结晶析出的盐分进行过滤和干燥,得到成品盐。
过滤可以去除残留的杂质,干燥则是为了将盐分中的水分去除,使得盐干燥并且保存更长时间。
以上就是制盐的基本工艺流程。
当然,不同地区和不同的制盐厂可能会有一些细微的差别,但总体来说,这些步骤是基本相似的。
制盐工艺的不断改进,也使得现代制盐更加高效、环保和安全。
总的来说,制盐工艺是一个涵盖了化学、物理等多个领域的复
杂过程,需要精确的控制和合理的操作。
通过不断的研究和创新,相信制盐工艺会更加完善,为人类提供更多优质的食用盐。
真空制盐工艺设计
真空制盐工艺设计引言:制盐是一项古老而重要的工艺,以满足人类对食盐的需求。
然而,传统的制盐方法存在一些局限性,包括能耗高、污染严重等。
为了解决这些问题,科学家们研究出了一种新型的制盐工艺,真空制盐工艺。
本文将详细介绍真空制盐工艺的设计原理、工艺流程和设备选型。
一、设计原理:1.降低盐水的沸点:通过减压操作,可以降低盐水的沸点,从而在低温下蒸发水分。
2.提高盐的产量:在真空环境下,盐水的蒸发速度更快,可以提高盐的产量。
3.节约能源:真空制盐工艺可以大幅度降低能耗,减少对环境的污染。
4.控制盐的质量:通过控制真空度、温度和蒸发时间等参数,可以获得高质量的食盐。
二、工艺流程:1.蒸发器预热:首先,将蒸发器预热到一定温度,以确保加热效果。
2.加盐水:将盐水加入蒸发器,并封闭设备,建立真空环境。
3.降压操作:通过减压系统降低蒸发器内的压力,从而降低盐水的沸点。
4.蒸发过程:在真空环境下,盐水开始蒸发,水分子从盐水中脱离,形成盐蒸汽。
5.盐蒸汽处理:将盐蒸汽引入除湿器进行处理,去除残余的水分和其它杂质。
6.盐收集:将经过处理的盐蒸汽传输到盐收集器中,将蒸发的盐进行收集和储存。
7.盐水循环:将剩余的盐水重新回收到蒸发器中,进行下一轮的蒸发。
三、设备选型:要实现真空制盐工艺,需要选用合适的设备来完成各个工艺步骤。
1.蒸发器:选择性能稳定、耐高温、耐腐蚀的蒸发器,包括加热管、蒸发室等。
2.泵系统:选择真空泵和减压系统,确保能够实现所需的真空度。
3.除湿器:选择能够有效去除水分和杂质的除湿器,以确保蒸汽的纯度。
4.收集器:选择合适的盐收集器,以便将蒸发的盐进行收集和储存。
5.控制系统:选择先进的自动控制系统,以实现对温度、真空度和蒸发时间等参数的精确控制。
结论:真空制盐工艺是一种高效、节能、环保的制盐方法,可以从根本上解决传统制盐方法存在的问题。
通过合理的设计原理、工艺流程和设备选型,可以实现真空制盐工艺的顺利进行。
现代制盐工艺
现代制盐工艺制盐是一项古老而又重要的工艺,随着科技的发展,现代制盐工艺也在不断创新和改进。
本文将介绍现代制盐工艺的原理、流程和技术。
一、制盐工艺的原理制盐的基本原理是利用水中的溶解盐分,通过蒸发和结晶的方式将盐从水中分离出来。
现代制盐工艺主要分为海盐和岩盐两种,其原理有所不同。
海盐制盐工艺的原理是利用海水中的盐分,经过多级蒸发器蒸发浓缩,最终得到结晶盐。
首先,将海水通过预处理去除杂质和沉淀物,然后进入多级蒸发器,通过蒸发器的加热和冷凝,逐渐提高盐分浓度。
最后,将浓缩的盐水进入结晶器,通过结晶器内的结晶器和分离器,得到高纯度的结晶盐。
岩盐制盐工艺的原理是利用地下盐矿中的盐矿石,通过开采、破碎和溶解的方式,最终得到结晶盐。
首先,将盐矿石通过开采和破碎,得到粉碎的盐矿石。
然后,将盐矿石放入溶解器中,加入适量的水,使盐矿石溶解。
最后,将溶解后的盐水通过过滤和结晶,得到高纯度的结晶盐。
二、制盐工艺的流程无论是海盐还是岩盐的制盐工艺,都包括了一系列的工序和设备。
下面以海盐制盐工艺为例,介绍其基本流程。
1. 海水预处理:海水经过除杂、沉淀和过滤等处理,去除其中的杂质和悬浮物。
2. 多级蒸发:预处理后的海水进入多级蒸发器,通过加热和冷凝,逐渐提高盐分浓度。
3. 结晶器:浓缩后的盐水进入结晶器,通过结晶器内的结晶器和分离器,得到结晶盐。
4. 干燥:将湿润的结晶盐进行干燥处理,去除其中的水分,得到干燥的结晶盐。
5. 分选和包装:对干燥的结晶盐进行分选和包装,最终得到市售的结晶盐产品。
三、现代制盐技术随着科技的不断进步,现代制盐工艺也在不断创新和改进。
现代制盐技术主要包括以下几个方面:1. 能源利用优化:通过利用余热、太阳能和风能等可再生能源,减少能源消耗,提高制盐工艺的能源效率。
2. 节水技术:通过循环利用和膜分离等技术,降低制盐工艺对水资源的消耗,实现节水制盐。
3. 自动化控制:采用现代化的自动化控制系统,实现对制盐工艺的全面监控和控制,提高生产效率和产品质量。
- 1、下载文档前请自行甄别文档内容的完整性,平台不提供额外的编辑、内容补充、找答案等附加服务。
- 2、"仅部分预览"的文档,不可在线预览部分如存在完整性等问题,可反馈申请退款(可完整预览的文档不适用该条件!)。
- 3、如文档侵犯您的权益,请联系客服反馈,我们会尽快为您处理(人工客服工作时间:9:00-18:30)。
制盐工艺第一章卤水净化车间工艺描述1.1 设计依据表1-1:卤水净化工程原卤的成分及其含量净化能力(万m3/年)225.85有效生产时间(h)8000NaCl / (g/l) 290Mg2+ / (g/l) 0.05 CaSO4 (g/l) 2.04Ca2+ / (g/l) 0.60 Mg SO4(g/l) 0.25密度(kg/m3) 1200夏季(℃)20冬季(℃)71.2 卤水净化的必要性卤水净化是指利用物理和化学的方法除去卤水中的杂质的一种工艺。
几乎所有的卤水都含有Ca2+、Mg2+杂质,而Ca2+、Mg2+杂质的影响表现在对产品质量的影响和对生产过程的影响。
由于CaSO4 具有逆溶解度的特性,在卤水输送、预热、蒸发过程中析出,附着在管道的设备的壁上而结垢,会严重降低传热系数,垢层越大,使传热系数下降越大,从而使设备生产能力降低。
垢层的消除会延长有效工作时间,有效生产量。
卤水中的CaSO4、MgSO4、CaCl2、MgCl2 等杂质会使卤水的沸点升高,粘度增大,因而降低有效传热温度差;另外,杂质越多,真空制盐的母液排放量越大,一方面使热量增大(即能耗高);另一方面降低了NaCl的回收率。
1.3 卤水净化方法及其流程说明1.3.1 卤水净化方法采用石灰-芒硝-二氧化碳法进行净化处理。
1.3.2 流程说明1.3.2.1 一级反应桶对原卤的处理1)一期卤水净化工程一级反应桶对原卤的处理高硝卤连续泵入原卤桶(T-110A/B)。
通过原卤泵(P-110)将原卤分批泵入一级反应桶(T-121~T-123),在一级反应桶(T-121~T-123)开始搅拌前,通过石灰乳泵(P-185)加入来自石灰乳存储桶(T-184)的石灰乳。
在搅拌结束前,通过一级絮凝剂计量泵(P-171)添加来自一级絮凝剂配置桶(T-171)的一级反应絮凝剂。
关闭搅拌器进行泥浆沉淀。
沉淀后,卤水通过卤水泵(P-121)泵入二级反应桶(T-131~T-133),沉淀的泥浆由一级反应泥浆泵(P-151/152)泵入一级反应泥浆桶(T-151)。
整个过程结束后,反应进行了一个循环,并为下一个循环做好准备。
每个循环过程持续约16.2小时。
由于有三个反应桶,所以每个桶可以在5.4 小时内交换一次来自T-110A/B的原卤。
举例来说:当T-121 澄清时,T-122正在添加絮凝剂溶液,T-123正在添加石灰乳。
注意:由于冬季的原卤温度较低,可将原卤泵入板式换热器(HE-110)进行换热,换热后的卤水再打入原卤桶(T-110A/B)。
即对原卤进行预热。
1.3.2.2二级反应桶对一级卤的处理1)卤水净化工程二级反应桶对一级卤的处理通过卤水泵(P-121)将(二期)一级反应桶(T-121~123)内的卤水分批泵入(二期)二级反应桶(T-131~T-133)的其中一个二级反应桶内,进料同时加入来自二级滤液桶(T-163B)内的二级溢流卤水,当(二期)二级反应桶(T-131~T-133)进卤时,烟道气从桶底通入。
当卤水加入完毕后,在搅拌装置开启前,通过二期纯碱液泵(P-192)加入来自纯碱储存桶(T-191A/B)中的纯碱溶液。
在搅拌结束前,通过二级絮凝剂计量泵(P-172)将二级絮凝剂配制桶(T-172B)内的二级反应絮凝剂泵入二级反应桶(T-131~T-133)内。
关闭搅拌器进行泥浆沉淀。
在沉淀结束后,通过卤水泵(P-131)将二级反应桶的卤水泵入精卤桶(T-140)。
最后,利用二级反应泥浆泵(P-161~P-162)将泥浆送入二级反应泥浆桶(T-161)。
整个过程结束后,反应完成一个循环并为下一循环作好准备。
每个循环持续约16.2 小时。
由于二级反应也有三个反应桶,每5.4 小时用其中一个桶交换一级反应桶的卤水一次。
例如:当T-131 碳化时,T-132澄清即将结束,T-133 正在澄清。
将二级反应桶(T-131~T-133)内的卤水分批泵入精卤桶(T-140),精卤泵(P-140A/B)只有其中一个运行连续运行,另一个备用。
1.3.2.3 沉淀物分离与处理1)一级反应所产生的泥浆处理一级反应桶(T-121~T-123)产生的沉淀物泵入一级反应泥浆桶(T-151)。
一级反应泥浆桶(T-151)桶设有搅拌装置避免泥浆的沉降。
一级泥浆泵(P-151)将一级反应泥浆桶(T-151)内的泥浆连续泵入一级反应泥浆沉降桶(T-152), 一级反应泥浆沉降桶(T-152)的卤水从泥浆中分离出来。
在一级反应泥浆沉降桶(T-152)内安装刮刀(AG-152)将浓缩的泥浆连续刮下。
分离出卤水溢流流入一级滤液桶(T-153)。
泥浆从一级反应泥浆沉降桶(T-152)出来后,由一级泥浆泵(P-152)连续泵入一级转鼓真空过滤机(T-154),其中滤液利用一级真空泵(P-157)被吸入了一级汽水分离器(SP-154),一级汽水分离器(SP-154)内卤水进一步由一级滤液泵(P-156)送入一级滤液桶(T-153)。
由一级转鼓真空过滤机(T-154)过滤后的滤饼从转鼓刮下来,掉进仓库车间作最后处理。
2)二级反应所产生的泥浆处理二级反应桶(T-131~T-133)产生的沉淀物泵入二级反应泥浆桶(T-161)。
二级反应泥浆桶(T-161)桶设有搅拌装置避免泥浆的沉降。
二级泥浆泵(P-161)将二级反应泥浆桶(T-161)内的泥浆泵入二级反应泥浆沉降桶(T-162),二级反应泥浆沉降桶(T-162)的卤水从泥浆中分离出来。
在二级反应泥浆沉降桶(T-162)内安装刮刀(AG-162)将浓缩的泥浆连续刮下。
分离出卤水溢流流入二级滤液桶(T-163)。
泥浆从二级反应泥浆沉降桶(T-162)出来后,由二级泥浆泵(P-162)泵入二级转鼓真空过滤机(T-164),其中滤液利用二级真空泵(P-167)被吸入了二级汽水分离器(SP-164),二级汽水分离器(SP-164)内卤水进一步由二级滤液泵(P-166)送入二级滤液桶(T-163)。
由二级转鼓真空过滤机(T-164)过滤后的滤饼从转鼓内刮下来,掉进车间作最后处理。
1.3.2.4反应过程药品的添加1)一级反应桶石灰乳的添加一级反应石灰的添加是分批定量的,将石灰仓(T-181)内的石灰通过石灰称重料仓(T-182)称重后再通过螺旋输送机(SC-182)送入石灰配置桶(T-183),利用一级溢流桶(T-153)内的卤水进行配制,外加搅拌器AG-183 对其搅拌。
利用石灰乳泵(P-183)将石灰乳送至石灰乳储存桶(T-184)储存,然后利用石灰乳泵(P-185)送往一级反应沉清桶(T-121~T-123)所需的桶内。
配制石灰乳应该包括10%的固体石灰。
一级反应桶(T-121~123)总进料量为2602Kg/(桶·批);2)一级反应桶絮凝剂的添加一级反应絮凝剂的添加是分批定量的,絮凝剂送一级絮凝剂配制桶(T-171),高温冷凝水对其进行稀释,外加搅拌器AG-171对其搅拌。
利用一级絮凝剂计量泵(P-171)将絮凝剂溶液送往一级反应沉清桶(T-121~T-123)所需的桶内;二级反应絮凝剂的添加是分批定量的,絮凝剂送二级絮凝剂配制桶(T-172),高温冷凝水对其进行稀释,外加搅拌器AG-172 对其搅拌。
利用二级絮凝剂计量泵(P-172)将絮凝剂溶液送往二级反应沉清桶(T-131~T-133)所需的桶内;注意:絮凝剂溶液成分应该基于实践经验。
3)二级反应桶纯碱溶液的添加二级反应纯碱的添加是分批定量的,纯碱通过人工将纯碱送入纯碱配置桶(T-191A/B),利用二级溢流桶(T-163)内的卤水进行配制,外加搅拌器AG-191A/B 对其搅拌。
利用纯碱液泵(P-192), 将纯碱溶液送至二级反应沉清桶(T-131~T-133)所需的桶内;配制的溶液应该包括?%的固体纯碱。
二级反应桶(T-131~133)总进料量为?Kg/(桶·批);1.3.3 效用1.3.3.1 烟道气烟道气加入二级反应桶为二级反应过程提供CO21.3.3.2 密封水绝大多数泵考虑密封水。
1.3.3.3 冷凝水高温冷凝水用于絮凝剂溶液的配制。
1.3.3.4 冲洗水冲洗水用于冲洗一级泥浆桶(T-151)到一级泥浆沉降桶(T-152)的管线、一级泥浆沉降桶(T-152)到一级转鼓真空过滤机(T-154)的管道和一级反应桶(T-121~T-123)排泥浆的管道。
(二级同上)1.3.4 控制系统车间应该由DCS 系统进行控制和监控,DCS系统位于综合楼内。
各个桶内的液位由一体式超声波物位仪监测。
石灰乳和纯碱溶液的流量由流量计进行控制。
反应桶的澄清情况、转鼓真空过滤机的运行情况、泥浆的洗涤情况、纯碱和石灰乳以及絮凝剂的配制由视频进行监控。
1.4烟道气压缩车间1生产规模烟道气压缩车间是为卤水净化车间提供co2的烟道气(co2含量10%计),根据卤水净化生产规模,确定压缩车间的供气能力为3300M3\h.2 生产方法烟道气经洗涤后,采用水环式压缩机抽取,压缩送入卤水净化车间。
3车间特点烟道气压缩为间歇操作,布置在本工程南面的镇江宏顺电厂内,所需水,电根据中盐镇江有限公司与镇江宏顺热电有限公司签署的<蒸气、烟道气、循环水供应合作协议>由镇江宏顺地热电有限公司提供。
4主要设备烟道气采用水环压缩机压缩输送。
该机具有对被压缩气体要求低,压力稳定、适中,动力消耗等优点。
生产工艺流程:石灰乳助沉剂↓原卤→一级反应沉清→泥浆脱水↓一级净化卤水助沉剂→二级反应沉清→泥浆脱水↓烟道气↗过滤→净化车间去制盐5主要设备净化车间主要设备除泵类外,其它主要设备如反应沉清罐,原卤罐、化碱桶等均为非标设备,全部为国内采购或加工制造。
泥浆脱水采用转鼓真空过滤机,该机泥浆过滤效果好,价格便宜,维修方便。
二、盐硝车间2.1生产规模本工程盐硝车间为年产60万吨真空精制盐,副产无水硫酸钠3.25万吨,粉盐1万吨。
2.2生产方法从硫酸钠氯化钠型矿盐卤水中分离盐硝的盐硝联产工艺,主要有真空制盐+冷冻提硝工艺、真空制盐+盐析法提硝工艺以及真空制盐+母液回收工艺有可分为单效机械热压缩制盐+母液回收法工艺(MVR)和多效真空蒸发+母液回收工艺(ME)。
真空制盐、母液回收法提硝工艺:投资与真空制盐、冷冻析硝工艺相当及真空制盐、母液回收工艺提硝工艺高,单位产品消耗蒸汽,电量较为小,产品氯化钠和硫酸钠的质量高。
真空制盐、母液回收法提硝工艺:即卤水首先进行真空蒸发制盐,浓缩后的母液进入母液回收系统,在母液回收系统内盐、硝分别在盐罐、硝罐内结晶析出。
析出的盐、硝从盐(硝)腿排、出,然后进行增稠、离心脱水,湿盐一部分经输盐栈桥直接去厂区北面的仓储车间,另一部分进入干燥床通过输盐栈桥去厂区北面的仓储车间;无水硫酸钠经干燥后至包装车间,粉盐送至包装间进行包装。