钛在钢中的作用
钢中微合金元素的作用机理

钢中微合金元素的作用机理钢是一种合金,其主要成分是铁和碳。
微合金元素是添加在钢中的少量杂质元素,包括钛、铌、钒、铝、锰、铬等。
这些微合金元素的添加对钢的性能具有重要的影响。
以下是钢中微合金元素的作用机理。
首先,微合金元素可以提高钢的强度和硬度。
微合金元素的加入可以阻碍晶界流动和位错的运动,从而限制了晶界滑移和位错滑动,降低了钢的塑性变形能力,提高了钢的强度和硬度。
此外,微合金元素还可以形成致密的析出物,如碳化物、氮化物、硫化物等,这些析出物可以增加钢的硬度,从而提高钢的抗拉强度和硬度。
其次,微合金元素可以改善钢的韧性和冷加工性能。
微合金元素的加入可以阻碍晶界弥散,提高了钢的晶界精细度,从而改善了钢的韧性和抗冲击性能。
同时,微合金元素也可以细化钢的晶粒尺寸,提高钢的塑性变形能力,使钢具有较好的冷加工性能。
第三,微合金元素可以提高钢的耐腐蚀性能。
微合金元素的加入可以改善钢的晶界耐蚀性能,减少晶界的腐蚀敏感性。
此外,微合金元素也可以与一些有害杂质元素结合,形成稳定的化合物,减少了钢中有害元素的溶解和析出,从而提高钢的耐腐蚀性能。
另外,微合金元素还可以改变钢的相变行为。
微合金元素的加入可以改变钢的析出序列和析出相,影响钢的相变行为。
例如,铌和钒可以用于控制钢中的碳化物析出,阻止奥氏体向珠光体的相变,从而提高钢的强韧性。
此外,微合金元素还可以优化钢的热处理工艺。
微合金元素的介入可以降低钢的回火敏感性和退火脆性,提高钢的热处理硬化能力,使钢在热处理过程中获得较好的组织和性能。
总的来说,钢中微合金元素的作用机理包括限制晶界滑移和位错滑动、形成致密的析出物、改善晶界精细度和抗腐蚀性能、提高韧性和冷加工性能、改变相变行为和优化热处理工艺等。
这些作用机理使得钢中微合金元素的加入可以显著改善钢的性能,提高钢的使用性能和工艺性能。
合金钢中各元素对其性能的影响

合金钢中各元素对其性能的影响1、碳(C):钢中含碳量增加,屈服点和抗拉强度升高,但塑性和冲击性降低,当碳量0.23%超过时,钢的焊接性能变坏,因此用于焊接的低合金结构钢,含碳量一般不超过0.20%。
碳量高还会降低钢的耐大气腐蚀能力,在露天料场的高碳钢就易锈蚀;此外,碳能增加钢的冷脆性和时效敏感性。
2、硅(Si):在炼钢过程中加硅作为还原剂和脱氧剂,所以镇静钢含有0.15-0.30%的硅。
如果钢中含硅量超过0.50-0.60%,硅就算合金元素。
硅能显著提高钢的弹性极限,屈服点和抗拉强度,故广泛用于作弹簧钢。
在调质结构钢中加入 1.0-1.2%的硅,强度可提高15-20%。
硅和钼、钨、铬等结合,有提高抗腐蚀性和抗氧化的作用,可制造耐热钢。
含硅1-4%的低碳钢,具有极高的导磁率,用于电器工业做矽钢片。
硅量增加,会降低钢的焊接性能。
3、锰(Mn):在炼钢过程中,锰是良好的脱氧剂和脱硫剂,一般钢中含锰0.30-0.50%。
在碳素钢中加入0.70%以上时就算“锰钢”,较一般钢量的钢不但有足够的韧性,且有较高的强度和硬度,提高钢的淬性,改善钢的热加工性能,如16Mn钢比A3屈服点高40%。
含锰11-14%的钢有极高的耐磨性,用于挖土机铲斗,球磨机衬板等。
锰量增高,减弱钢的抗腐蚀能力,降低焊接性能。
4、磷(P):在一般情况下,磷是钢中有害元素,增加钢的冷脆性,使焊接性能变坏,降低塑性,使冷弯性能变坏。
因此通常要求钢中含磷量小于0.045%,优质钢要求更低些。
5、硫(S):硫在通常情况下也是有害元素。
使钢产生热脆性,降低钢的延展性和韧性,在锻造和轧制时造成裂纹。
硫对焊接性能也不利,降低耐腐蚀性。
所以通常要求硫含量小于0.055%,优质钢要求小于0.040%。
在钢中加入0.08-0.20%的硫,可以改善切削加工性,通常称易切削钢。
6、铬(Cr):在结构钢和工具钢中,铬能显著提高强度、硬度和耐磨性,但同时降低塑性和韧性。
各类化学元素在钢中起到的作用

各类化学元素在钢中起到的作用各类化学成分在钢板中起到什么作用:1、碳(C):钢中含碳量增加,屈服点和抗拉强度升高,但塑性和冲击性降低,当碳含量超过0.23%时,钢的焊接性能变坏,因此用于焊接的低合金结构钢,含碳量一般不超过0.20%。
碳量高,还会降低钢的耐大气腐蚀性能,在露天料场的高碳钢就易锈蚀;此外,碳能增加钢的冷脆性和时效敏感性。
2、硅(SI):在炼钢过程中加硅作为还原剂和脱氧剂,所以镇静钢含有0.15%~0.30%的硅。
如果钢中含硅量超过0.50%~0.60%,硅就算合金元素。
硅能显著提高钢的弹性极限,屈服点和抗拉强度,故广泛用于做弹簧钢。
在调制结构钢中加入1.0%~1.2%的硅,强度可提高15%~20%。
硅和钨、钼、铬等相结合,有提高抗腐蚀性和抗氧化性的作用,可制造耐热钢。
含硅1~4%的低碳钢,具有极高的导磁率,用于电器工业做矽钢片。
硅量增加,会降低钢的焊接性能。
(1)、强化铁素体,提高钢的强度和硬度。
(2)、降低钢的临界冷却速度,提高钢的淬透性。
(3)、提高钢的氧化性腐蚀介质中的耐腐性,提高钢的耐热性。
(4)、磁钢中的主要化学元素(含量在0.40%范围内时,改善热裂倾向,含量高时,易形成柱状晶,增加热裂倾向)3、锰(Mn):在炼钢过程中,锰是良好的脱氧剂和脱硫剂,一般钢中含锰0.30~0.50%。
在碳素钢中加0.70%以上时就算“锰钢”,较一般钢量的钢不但有足够的韧性,且有较高的强度和硬度,提高钢的淬性,改善钢的热加工性能,如16Mn钢比A3屈服点高40%。
含锰11~14%的钢具有极高的耐磨性,用于挖土机铲斗,球棒机衬板。
锰量增高,减弱钢的抗腐蚀性,降低焊接性能。
(1)、在含量范围内,对钢具有很大的强化作用,提高强度,硬度和耐磨性。
(2)、降低钢的临界冷却速度,提高钢的淬透性。
(3)、稍稍改善钢的低温韧性。
(4)、在高含量范围内,作为主要的奥式体化元素。
4、磷(P):在一般情况下,磷是钢中有害元素,增加钢的冷淬性,使焊接性能变坏,降低塑性,使冷弯性能变坏。
各种元素对钢材性能的影响

1、碳(C):钢中含碳量增加,屈服点和抗拉强度升高,但塑性和冲击性降低,当碳量0.23%超过时,钢的焊接性能变坏,因此用于焊接的低合金结构钢,含碳量一般不超过0.20%。
碳量高还会降低钢的耐大气腐蚀能力,在露天料场的高碳钢就易锈蚀;此外,碳能增加钢的冷脆性和时效敏感性。
2、硅(Si):在炼钢过程中加硅作为还原剂和脱氧剂,所以镇静钢含有0.15-0.30%的硅。
如果钢中含硅量超过0.50-0.60%,硅就算合金元素。
硅能显著提高钢的弹性极限,屈服点和抗拉强度,故广泛用于作弹簧钢。
在调质结构钢中加入1.0-1.2%的硅,强度可提高15-20%。
硅和钼、钨、铬等结合,有提高抗腐蚀性和抗氧化的作用,可制造耐热钢。
含硅1-4%的低碳钢,具有极高的导磁率,用于电器工业做矽钢片。
硅量增加,会降低钢的焊接性能。
3、锰(Mn):在炼钢过程中,锰是良好的脱氧剂和脱硫剂,一般钢中含锰0.30-0.50%。
在碳素钢中加入0.70%以上时就算“锰钢”,较一般钢量的钢不但有足够的韧性,且有较高的强度和硬度,提高钢的淬性,改善钢的热加工性能,如16Mn钢比A3屈服点高40%。
含锰11-14%的钢有极高的耐磨性,用于挖土机铲斗,球磨机衬板等。
锰量增高,减弱钢的抗腐蚀能力,降低焊接性能。
4、磷(P):在一般情况下,磷是钢中有害元素,增加钢的冷脆性,使焊接性能变坏,降低塑性,使冷弯性能变坏。
因此通常要求钢中含磷量小于0.045%,优质钢要求更低些。
5、硫(S):硫在通常情况下也是有害元素。
使钢产生热脆性,降低钢的延展性和韧性,在锻造和轧制时造成裂纹。
硫对焊接性能也不利,降低耐腐蚀性。
所以通常要求硫含量小于0.055%,优质钢要求小于0.040%。
在钢中加入0.08-0.20%的硫,可以改善切削加工性,通常称易切削钢。
6、铬(Cr):在结构钢和工具钢中,铬能显著提高强度、硬度和耐磨性,但同时降低塑性和韧性。
铬又能提高钢的抗氧化性和耐腐蚀性,因而是不锈钢,耐热钢的重要合金元素。
各种元素对钢材性能的影响
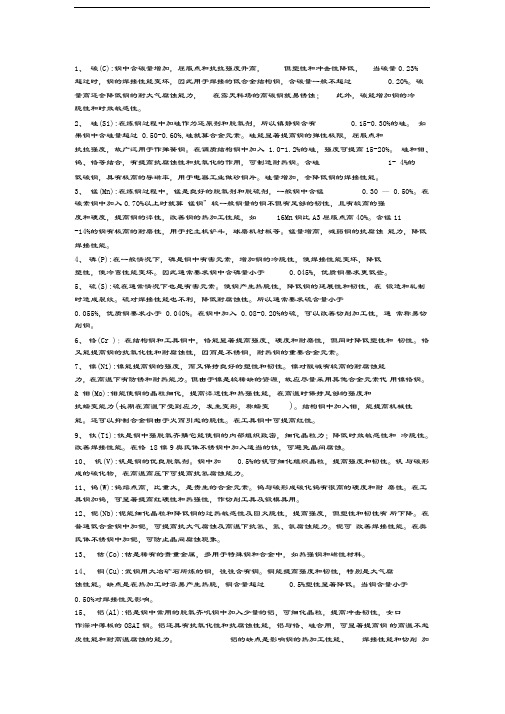
1、碳(C):钢中含碳量增加,屈服点和抗拉强度升高,但塑性和冲击性降低,当碳量0.23%超过时,钢的焊接性能变坏,因此用于焊接的低合金结构钢,含碳量一般不超过0.20%。
碳量高还会降低钢的耐大气腐蚀能力,在露天料场的高碳钢就易锈蚀;此外,碳能增加钢的冷脆性和时效敏感性。
2、硅(Si):在炼钢过程中加硅作为还原剂和脱氧剂,所以镇静钢含有0.15-0.30%的硅。
如果钢中含硅量超过 0.50-0.60%,硅就算合金元素。
硅能显著提高钢的弹性极限,屈服点和抗拉强度,故广泛用于作弹簧钢。
在调质结构钢中加入 1.0-1.2%的硅,强度可提高15-20%。
硅和钼、钨、铬等结合,有提高抗腐蚀性和抗氧化的作用,可制造耐热钢。
含硅1- 4%的低碳钢,具有极高的导磁率,用于电器工业做矽钢片。
硅量增加,会降低钢的焊接性能。
3、锰(Mn):在炼钢过程中,锰是良好的脱氧剂和脱硫剂,一般钢中含锰0.30 — 0.50%。
在碳素钢中加入0.70%以上时就算锰钢”较一般钢量的钢不但有足够的韧性,且有较高的强度和硬度,提高钢的淬性,改善钢的热加工性能,如16Mn钢比A3屈服点高40%。
含锰11-14%的钢有极高的耐磨性,用于挖土机铲斗,球磨机衬板等。
锰量增高,减弱钢的抗腐蚀能力,降低焊接性能。
4、磷(P):在一般情况下,磷是钢中有害元素,增加钢的冷脆性,使焊接性能变坏,降低塑性,使冷弯性能变坏。
因此通常要求钢中含磷量小于0.045%,优质钢要求更低些。
5、硫(S):硫在通常情况下也是有害元素。
使钢产生热脆性,降低钢的延展性和韧性,在锻造和轧制时造成裂纹。
硫对焊接性能也不利,降低耐腐蚀性。
所以通常要求硫含量小于0.055%,优质钢要求小于 0.040%。
在钢中加入 0.08-0.20%的硫,可以改善切削加工性,通常称易切削钢。
6、铬(Cr ):在结构钢和工具钢中,铬能显著提高强度、硬度和耐磨性,但同时降低塑性和韧性。
铬又能提高钢的抗氧化性和耐腐蚀性,因而是不锈钢,耐热钢的重要合金元素。
钛7不锈钢成分
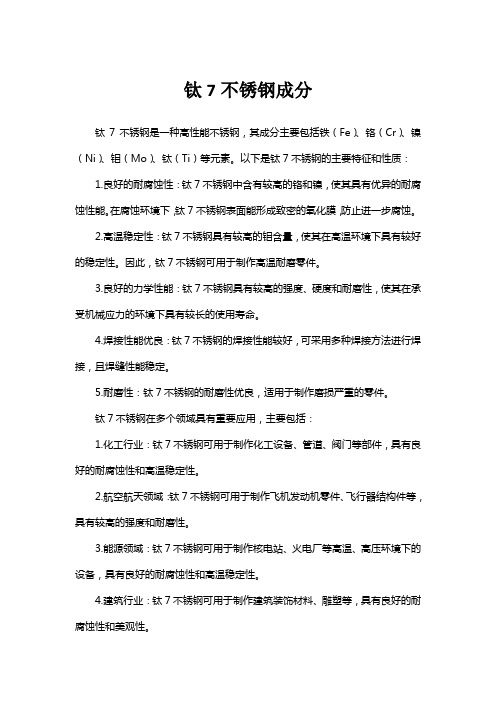
钛7不锈钢成分
钛7不锈钢是一种高性能不锈钢,其成分主要包括铁(Fe)、铬(Cr)、镍(Ni)、钼(Mo)、钛(Ti)等元素。
以下是钛7不锈钢的主要特征和性质:
1.良好的耐腐蚀性:钛7不锈钢中含有较高的铬和镍,使其具有优异的耐腐蚀性能。
在腐蚀环境下,钛7不锈钢表面能形成致密的氧化膜,防止进一步腐蚀。
2.高温稳定性:钛7不锈钢具有较高的钼含量,使其在高温环境下具有较好的稳定性。
因此,钛7不锈钢可用于制作高温耐磨零件。
3.良好的力学性能:钛7不锈钢具有较高的强度、硬度和耐磨性,使其在承受机械应力的环境下具有较长的使用寿命。
4.焊接性能优良:钛7不锈钢的焊接性能较好,可采用多种焊接方法进行焊接,且焊缝性能稳定。
5.耐磨性:钛7不锈钢的耐磨性优良,适用于制作磨损严重的零件。
钛7不锈钢在多个领域具有重要应用,主要包括:
1.化工行业:钛7不锈钢可用于制作化工设备、管道、阀门等部件,具有良好的耐腐蚀性和高温稳定性。
2.航空航天领域:钛7不锈钢可用于制作飞机发动机零件、飞行器结构件等,具有较高的强度和耐磨性。
3.能源领域:钛7不锈钢可用于制作核电站、火电厂等高温、高压环境下的设备,具有良好的耐腐蚀性和高温稳定性。
4.建筑行业:钛7不锈钢可用于制作建筑装饰材料、雕塑等,具有良好的耐腐蚀性和美观性。
5.食品医药行业:钛7不锈钢可用于制作食品加工设备、制药设备等,具有良好的卫生性能和耐腐蚀性。
6.交通运输领域:钛7不锈钢可用于制作汽车、火车等交通工具的零部件,具有较高的耐磨性和强度。
总之,钛7不锈钢凭借其优异的性能和广泛的应用领域,在我国的工业发展中发挥着重要作用。
钛在钢中的物理冶金学基础
第一章钛在钢中的物理冶金学基础1.引言钛[1](Titanium)是位于元素周期表第四周期(第一长周期)第IV副族的过渡族金属元素,原子序数为22,其外层电子结构为3d2 4s2,原子量47.867(1)[2]。
钛是英国化学家Gregor R W (1762-1817)在1791年研究钛铁矿和金红石时发现的。
四年后的1795年,德国化学家Klaproth M H (1743-1817)在分析匈牙利产的红色金红石时也发现了这种元素,他主张采用为铀命名的方法,引用希腊神话中泰坦神族“Titanic”的名字给这种新元素起名为Titanium[1]。
中文按其译音定名为钛。
Gregor和Klaproth当时所研究的钛是粉末状的二氧化钛,而不是金属钛。
因为钛的氧化物极其稳定,而且金属钛能与氧、氮、氢、碳等非金属元素强烈化合,所以单质钛很难制取。
直到1910年美国化学家Hunter M A 才第一次用钠还原法(亨特法)制得纯度达99.9%的金属钛[1]。
钛是具有固态多型性相变的元素,相变点882.5℃,该温度之上为体心立方结构的β钛,900℃时的点阵常数为0.332nm,而该温度之下为密排六方结构的α钛,室温(20℃)下的点阵常数为a=0.29506nm,c=0.46788nm,c/a=1.5857,接近于密排六方结构的理想值(8/3)1/2即1.633。
由此可计算得到其最近邻原子间距为0.28939nm,配位数为12时的原子半径为0.14609nm,比铁的原子半径大14.4%左右;其理论摩尔体积为1.0622×10-5m3/mol,理论密度为4.506 g/cm3,实际密度为4.506-4.516g/cm3,显著小于铁(理论密度7.875 g/cm3,实际密度7.870 g/cm3),故通常将钛归类为轻金属。
α钛和β钛的晶体结构见图1-1。
图1-1 hcp的α钛和bcc的β钛的晶体结构α钛的定压比热C p=22.133+10.251×10-3T(298-1155K)J/(K∙mol),β钛的定压比热C p =19.832+7.908×10-3T(1155-1933K)J/(K∙mol),β→α相变潜热为4142J/mol。
钢铁冶炼中的钒钛回收利用
钢铁冶炼中的钒钛回收利用随着钢铁产业的不断发展和技术水平的提高,钒钛作为一种重要的非铁金属,在钢铁冶炼过程中发挥着越来越重要的作用。
钢铁冶炼中的钒钛资源是比较稀缺而又重要的资源之一,因此对钢铁冶炼中的钒钛回收利用显得尤为重要。
一、钒钛在钢铁冶炼中的应用钒钛是一种重要的非铁金属,在钢铁冶炼中作为合金元素广泛应用。
钛可以增强钢材的抗腐蚀性和耐久性,钒可以提高钢材的强度和塑性,使得钢材具有良好的耐磨性和韧性。
在新能源汽车的发展和钢铁产业的升级中,钛和钒在钢铁冶炼中的应用越发重要。
钢铁冶炼中的钒钛主要来自于铁矿石。
在钢铁冶炼过程中,钒钛元素通常存在于铁矿石的化学成分中,因此钒钛的回收利用能够提高铁矿石的综合利用率,实现钒钛资源的最大化利用。
二、钢铁冶炼中的钒钛回收方案在钢铁冶炼中,钒钛通常随着废弃物一起被排放出去,这不仅浪费了钒钛资源,而且对环境也造成了一定的污染。
因此,如何回收利用钢铁冶炼中的钒钛,成为了一个亟需解决的问题。
目前,钢铁冶炼中的钒钛回收主要有以下几种方案:1. 湿式法湿式法是将回收钢铁冶炼中的钒钛化学反应后,通过沉淀、过滤和离心等工艺步骤,提取钒钛元素。
湿式法对钒钛元素的回收率相对较高,在某些情况下,可以达到90%以上。
2. 干法法干法法是将钢铁冶炼中的废弃物进行高温热解,将其中的钒、钛氧化还原,使其转化为钒钛合金。
干法法对硫、氢等有毒气体的处理相对困难,需要高度的技术支持和环境保护。
3. 深度热压法深度热压法是在高温、高压状态下,将钒钛元素提取出来。
该法对环境污染比较小,并且操作简便,但是对设备的要求较高,投资成本比较高。
以上三种方案各有优缺点,对于具体回收工作应根据实际情况选择合适的方案。
三、目前钢铁冶炼中的钒钛回收利用现状中国是世界上最大的钢铁生产国,也是大量钒钛资源的消耗国。
近年来,随着国家政策的扶持和技术的进步,钢铁冶炼中的钒钛回收利用工作也得到了一定程度的改善。
1. 国家政策扶持中国在近几年实行了一系列环保政策,加大了对钢铁企业环境、资源利用方面的监控和执法力度。
GCr15轴承钢中微量钛的作用与控制
a b o v et h e o r y , b e a r i n g s t e e l GCr l 5 i s p r o d u c e d b y B0F r e in f i n g( L F+ RH) — ÷ CC o f r e c t a n g u l r a b i l l e t i n t h e
低钢 中 T i 和 N 的含量 , 并抑制选分结 晶偏析。 依 据上述理论 , 采用 “ 转炉 一 ( L F + R H ) 精炼 一 矩形坯连 铸”生产工艺路线 , 进行 了 G C r I 5 轴承钢工业性试验 。试验 中, 通过使用低钛铬铁 、转炉 出钢过程铬
合金化 、 L F精炼使用 低钛原料并造还原渣 、 R H控制压力和循环时 问、投入电磁搅拌 和轻压 F 装备等 , 最终成 品钛含量 为 2 2 x 1 0 ~ 。 结果表明 , 转炉铬 合金化 、 L F精炼过程抑制增钛量 , 是转炉冶炼低钛 GC r I 5 轴承钢 的关 键控制环节。
Ab s t r a c t : By s t u d y i n g t h e r o l e o f i T i n b e a r i n g s t e e l GCr I 5 , f o r ma t i o n c o n d i t i o n a n d c o n t r o l l i n g o f IN T i n c l u s i o n s ,t h e f o l l o wi n g c o n c l u s i o n s c a n b e o b t a i n e d .Th e T i N i n c l u s i o n s p r e c i p i t a t e a n d g r o w i n s o l i d i i f c a t i o n o f mo l en t s t e e l b e l o w t h e l i q u i d ’ S t e mp e r a t u r e o f mo l mn s t e e 1 . T h e e f f e c t i v e wa y o f d e c r e a s i n g i N T i n c l u s i o n s i s ed r u c i n g t h e c o n t e n t o f T i a n d N i n t h e s t e e 1 . a n d r e s t r a i n i n g s e g eg r a t i o n . Ac c o r d i n g t O t h e
常用合金元素在钢中的作用
几种常用合金元素在钢中的作用为了合金化而加入的合金元素,最常用的有硅、锰、铬、镍、钼、钨、钒,钛,铌、硼、铝等。
现分别说明它们在钢中的作用。
1、硅在钢中的作用:(1)提高钢中固溶体的强度和冷加工硬化程度使钢的韧性和塑性降低。
(2) 硅能显著地提高钢的弹性极限、屈服极限和屈强比,这是一般弹簧钢。
(3)耐腐蚀性。
硅的质量分数为15%一20%的高硅铸铁,是很好的耐酸材料。
含有硅的钢在氧化气氛中加热时,表面也将形成一层SiO2薄膜,从而提高钢在高温时的抗氧化性。
缺点:(4)使钢的焊接性能恶化。
2、锰在钢中的作用(1)锰提高钢的淬透性。
(2)锰对提高低碳和中碳珠光体钢的强度有显著的作用。
(3)锰对钢的高温瞬时强度有所提高。
锰钢的主要缺点是,①含锰较高时,有较明显的回火脆性现象;②锰有促进晶粒长大的作用,因此锰钢对过热较敏感t在热处理工艺上必须注意。
这种缺点可用加入细化晶粒元素如钼、钒、钛等来克服:⑧当锰的质量分数超过1%时,会使钢的焊接性能变坏,④锰会使钢的耐锈蚀性能降低。
3、铬在钢中的作用(1)铬可提高钢的强度和硬度。
(2)铬可提高钢的高温机械性能。
(3)使钢具有良好的抗腐蚀性和抗氧化性(4)阻止石墨化(5)提高淬透性。
缺点:①铬是显著提高钢的脆性转变温度②铬能促进钢的回火脆性。
4、镍在钢中的作用(1)可提高钢的强度而不显著降低其韧性。
(2)镍可降低钢的脆性转变温度,即可提高钢的低温韧性。
(3)改善钢的加工性和可焊性。
(4)镍可以提高钢的抗腐蚀能力,不仅能耐酸,而且能抗碱和大气的腐蚀。
5、钼在钢中的作用(1)钼对铁素体有固溶强化作用。
(2)提高钢热强性(3)抗氢侵蚀的作用。
(4)提高钢的淬透性。
缺点:钼的主要不良作用是它能使低合金钼钢发生石墨化的倾向。
6、钨在钢中的作用(1) 提高强度(2)提高钢的高温强度。
(3)提高钢的抗氢性能。
(4)是使钢具有热硬性。
因此钨是高速工具钢中的主要合金元素。
7、钒在钢中的作用(1)热强性。