模具成型条件参照表B讲解
模具制作标准

十五、分型面设计
• 铸件对动模芯的包紧力大于定模型芯的包 紧力
• 分型面应满足合理的浇铸系统布置需求 • 分型面使模具型腔具有良好的溢流排气条
件 • 分型面设置在金属液最后冲填的部位。 • 在模仁与模框的配合之间,模仁一般高出
摸框0.1-0.3之间,真空模则0.05-0.1之间。
设有冷却水路。 • 当滑块滑动行程过长时,必须在模座上增长导向,通常滑动部位做
到宽度的1.5倍左右为宜,抽芯时滑块在导向槽的部分,要有滑块 滑动部位的2/3在导向滑槽内。 • 斜导柱与导柱孔的配合间隙必须留有0.2MM以上,禁ห้องสมุดไป่ตู้非间隙配合。 • 斜导柱的角度小于滑块锲紧面2度,大滑块的锲尽紧块须伸入下模 15-20MM以斜度面互锁反压。 • 模具上方的滑块最终定位应用弹弓推或拉,行式上不能用钢珠定位, 以避免模具在生产时滑块松动向下滑落导致与顶针及模具的其它配 件相撞。 • 所有的滑块滑动磨檫面必须淬火HRC45度以上,大滑块必须淬火 后氮化增强硬度。
• 锌合金模具在模具试模后10000模次以内(含试 模数量)需进行回火一次,第二次间隔回火时 间30000-50000模次,后续按倍数时间延长, 回火温度在450度高温回火祛除模具应力。
• 在薄壁件和高冲击的深腔模仁必须做氮化
• 在需要增加排气槽面积时,以增大排气槽的宽度与数量 为宜,不宜过分增加其深度,以防生产时金属液贱出。
十三、排渣设计:
• 设计溢流槽时要注意便于从压铸件上去除,在祛除后铝 合金排渣口不超过1MM,锌合金则不超过0.3MM(特殊 结构产品除外)不损坏铸件外观,在溢流槽上开设排气 槽时,应合理设计溢流口,避免过早堵塞排气槽。
模具制作标准
目的:为使模具制作及维修作业能 降低成本,缩短模具制作周期,确
36个常用塑胶原料成型条件,一张表搞定!

36个常用塑胶原料成型条件,一张表搞定!ABS(丙烯腈-丁二烯-苯乙烯共聚合物)1. 依照流动性选定适当之浇道及浇口。
2. 对应浇口位置选择适当熔合状态。
3. 由于高压成形,退缩倾斜须在2°以上。
4. 成形收缩率须在0.5%左右。
5. 常用于镀金品,其注意事项如下:(1) 料管温度宜高,约220℃~250℃;(2) 射出温度宜慢(用二次加压法)、射出压力宜低;(3) 不可用离模剂;(4) 不可有收缩下陷及熔接线之流痕;(5) 成品表面不可有创痕。
6. 加热温度180~290℃、模具温度50~80℃、料管温度200~230℃、喷出料温度200~240℃、射出压力700~1500kg/cm²、最低操作温度260℃。
7. 使用热风干燥机、干燥温度为80~100℃、需时2~4小时(0.3%以下)、料管温度第一段为220~240℃;第二段为210~240℃;第三段为180~230℃;第四段为150~180℃;模具表面温度50~90℃、射出压力500~2100kg/cm²。
8. 温度设定:射嘴203~295℃、前段220~295℃、中段210~290℃、后段180~210℃;螺杆转速70~150rpm、模具温度10~80℃、保压30~60%、背压100~250kg/cm²。
9. 密度1.04~1.06g/cc,变形温度82~122℃,成型收缩率0.4~0.8%,比重1.0~1.2,线膨胀系数0.00006~0.00013/℃,成型收缩率0.3~0.8%,热变形温度66~107℃(88~113℃)。
AS(SAN)丙烯腈-苯乙烯共聚合物1. 成形品有钵裂之虞者,注意成形品设计。
特殊情况使用1°以上之退缩倾斜,注意模具不得有低陷部分。
2. 成形收缩率为0.45%左右、加热温度170~310℃、使用热风干燥机、干燥时间2~3小时(0.1%以下)、干燥温度80~100℃、料管温度180~290℃、。
Moldflow成型条件设定
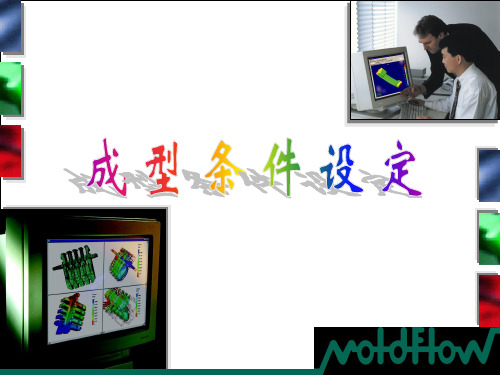
产品内外表面的冷却不均,导致产品产生翘曲,减小此翘曲的方法是使 公母模的冷却均匀,解决方法: 调整冷却水管排布 调整冷却液温度 在积热的地方加强冷却
收 缩 不 均
产品不同区域的收缩大小不一,所以不同区域之间产生内应力,致使产 品产生翘曲。
中间收缩大于四周,产生马鞍形翘曲。
产品各区域收缩不均导致变形, 解决方法: 调整保压曲线 修改产品设计
判断结果
在Buckling和Automatic的分析结果Screen out中会给出一个叫 Lambda的参数,根据这个参数,按照下列原则就可以判断材料是否 屈服:
Lambda<1: 材料出现屈服,用Large Deflection Lambda>1: 材料未出现屈服,用Small Deflection
•Flow - Cool - Flow - Warp (FCFW)
–冷却分析采用料到达此元素时的即时温度做为初始的 料温
–即时温度是用假设的恒定及统一的模温计算出来的
最佳分析序列
哪个序列是最佳的分析序列?
•FCFW 在流动分析的初始时假设恒定的模温
•CFW 假设冷却分析时的初始料温为常温 •对于翘曲的预测,假设恒定的料温比假设恒定模 温预测的更精确
变形的原因
塑料在成形过程中,由于温度、压力等因素 的影响,在材料分子之间产生很大的内应力,在 这种内应力的作用下,产品就产生了变形翘曲。 在应力和应变之间存在着一种特定的关系, 每种材料都不相同。 下面首先从理论上讲述一下应力和应变的关 系。
理想弹性变形
材料在受到应力的作用下会发 生变形,理想的弹性材料应力-应变 如右图所示,应变随着应力的增大 而增大,且成正比(线性)关系。
–因此CFW 是首选的运行序列
第三章成形条件的设定
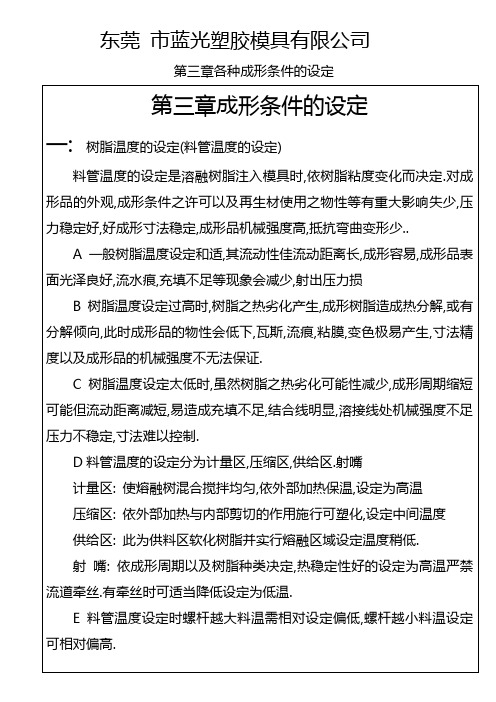
一般背压油压机的设定3-20㎏/㎝电动机相对较大25~200之间,背压设定过低时树脂脱气不充分,计量不稳定背压太高时,计量时间长树脂易烧焦过热分解.射嘴处会溢胶造成泠料,使成形品不稳定.高粘度背压需高,低粘度材质背压需相对偏低.
六:射出压力的设定
射出压力:是将熔融树脂充填于模穴内的压力它以压力为上限值以速度为主.即实际射出压力与射出速度实际值成正比.在能满足部品充填的情况下射
冷却时间与模具温度,材质种类以及部品的结构决定时间的长短.
冷却时间配合模具温度对部品的外形尺寸影响较大,时间越长模具温度越底部品的外形尺寸越大,相反时间越短模温越高部品的外形尺寸越小。
十:射出速度的设定
射出速度的设定参照第四章形多段射出成形的应用。
十一:低压保护的设定
1低压保护设定分低压保护压力,低压锁模压力,高压切换点。
七:保压的设定
保压是以压力为主以速度为辅的压力工程,模具所承受的压力是保压所以保压一般低于射出压力.二次保压低于一次保压力.
模具易产生毛边一次压力也可低于二次压力,一次压力为低压,使充填模穴内熔融树脂表面冷却固化后再切换第二次压力高压确保外观与尺寸的精度.
八:射出时间的设定
射出时间一般小部品追求快速充填即0.5秒以下再以保压确保外观与尺寸.
3当模具发生异常时是以低压保护压力为上限合模,为了确保模具的安全性低压保护压力设定越小越好。
4低压保护位置的设定-般大于或等于成品的厚度,有斜销的模具应大于斜销的长度。
5
东莞市蓝光塑胶模具有限公司
第三章各种成形条件的设定
5高压切换点的设定确保公母模已完全靠近以机台实际显示设定,以不同机台加大于0.02或0.1。
十二:射出位置的设定
成型条件分析与设定课件
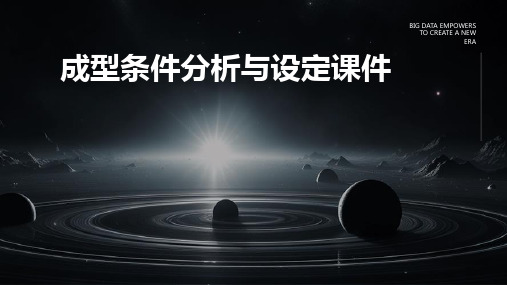
01
成型条件分析的重要性
BIG DATA EMPOWERS TO CREATE A NEW
ERA
定义与特点
成型条件分析是指对产品制造过程中各种因素的影响程度进行分析,以确定最佳的 成型工艺和条件。
成型条件分析需要考虑材料、工艺、设备、环境等因素,以及它们之间的相互作用 。
成型条件分析的特点包括系统性、综合性、实践性等。
05
成型条件与模具设计的关系
BIG DATA EMPOWERS TO CREATE A NEW
ERA
模具类型与成型条件的关系
注塑模具
适用于热塑性塑料,可快速生产 ,但模具成本高,不合适小批量
生产。
压铸模具
适用于铝合金、锌合金等金属材 料,生产效率高,但模具成本也
较高。
挤出模具
适用于塑料、橡胶等材料的连续 生产,成本低,但生产效率相对
公道安排生产计划
根据设备能力和生产需求,公道安排生产计划,避免设备闲置和过 度使用。
提高员工技能水平
通过培训和技能提升,提高员工的操作技能水平,减少操作失误和设 备故障。
07
成型条件与产品成本的关系
BIG DATA EMPOWERS TO CREATE A NEW
ERA
材料成本的控制方法
优化产品设计
成型条件分析与设定课件
BIG DATA EMPOWERS TO CREATE A NEW
ERA
• 成型条件分析的重要性 • 成型条件分析的方法 • 成型条件对产品性能的影响 • 成型条件的设定与调整 • 成型条件与模具设计的关系 • 成型条件与生产效率的关系 • 成型条件与产品成本的关系
目录
CONTENTS
优化模具设计和成型工艺条件,以提 高制品的表面质量和光洁度。对于外 观要求高的制品,可以采用抛光、喷 涂、贴膜等后处理工艺来提高其美观 度和使用感受。同时,注意控制原材 料的质量和稳定性,以避免因原材料 波动导致的产品外观问题。
成型条件知识.ppt
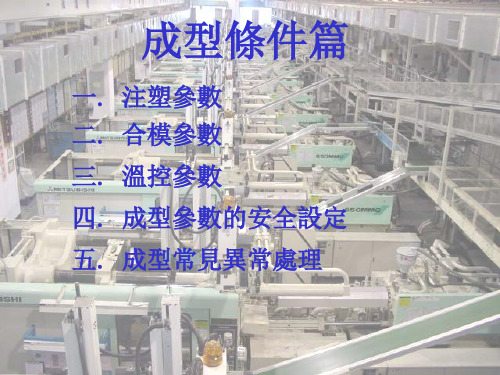
作用: 背壓的提高有助於螺槽中物料的密實, 驅赶走物料中的氣體,改善塑化質量. 但過大的背壓會增加計量段螺槽熔體 的反流和漏流,降低熔體輸送能力,增加 功率消耗.
一. 注塑參數
預塑背壓
設定原則 1. 背壓的調整應考慮塑膠原料的性質.
2. 背壓的調整應參考製品的表觀質量 和尺寸精度.
模腔,反之,如果調整過大,不僅會造成制品溢邊,脹 模等不良現象,還會造成壓力波動甚至系統過載.
一. 注塑參數
注射壓力
1. 必在注塑機的額定壓力范圍內.
設定原則 2. 設定時盡量用低壓.
3. 盡量避免在高速時采用高壓,以 免异常狀況發生.
一. 注塑參數
保壓壓力
定義:在注射壓力作用下,熔體充滿模腔之后,制品在 模內邊冷卻邊收縮,為了補縮需要繼續維持熔體 流動的注射壓力稱保壓壓力.
二. 合模參數
頂出摩擦力
頂出力必須大于制品和模具表面的摩擦力時制品才能脫模,
注塑制品脫模過程是很重要的階段,將對制品尺寸精度和表 面質量產生影響.
粘附摩擦系數和滑動摩擦系數是影響脫模力的直接因素, 與模腔表面溫度和粗糙度有關.
三. 溫控參數
干燥溫度
定義:為保證成型品質而事先對聚合物
進行干燥所需要的溫度
聚合物C≒ 0.85,對非結晶型聚合物C ≒0.93
一. 注塑參數
計量行程(預塑行程)
定義: 螺杆計量(預塑)過程中后退的距離稱計量(預塑)行程
制品所需的注射量是用計量行程L來調整的,其大小與 計量行程的精度有關,如果計量行程調節太小會造成注射量 不足,如果計量行程調整的太大,使料筒前部每次注射后的余 料太多,使熔體溫度不均或過熱分解,計量行程的重复精度的 高低會影響注射的波動.
成型条件标准表标准格式

锁模
1段 2段 3段 4段
±10℃ ±10℃
1段
/ ±10℃ / ±10℃ 2段 3段
/ ±10℃ / / ±10℃ / 4段 开模
注:温度由射嘴至下料口(不含下料
口温度)依次设置
±10℃ ±10℃
/ ±10
℃
/ ±10
℃
/ ±10℃ 注:热流道温度
由左至右设置
/ ±10℃ 。
顶针 进1 进2 退1 退2
速度 ±5% 55 50 35
/
35 25 85
/ 速度 ±5% 速度 ±5% 35 27 20
/
压力 ±5% / 位置 ±10% 230 射胶压力 2550 特殊装置 / 抽芯速度 /
// 30 1.55 切换方式 射座后退 抽芯时间
15 / 位置
/ /
/
/
/
/
80 180 365 /
顶出保持 0.8 熔胶时间
射出标准条件表
年
月
日
部门:
客户
原料
机台名 称: 模号
机台吨位: 周期时间/s
品名
干燥时间/h
模具尺寸
螺杆直径/mm
机种
干燥温度/℃
模穴数
冷却时间/s
锁模力
颜色
毛重/g
净重/g
使用夹具
主
副
主副
顶针确认
有
无
料筒道温度 射嘴
热流道温度1: 热流道温度2:
/ ±10℃ / ±10℃
/ ±10℃ / / ±10℃ /
背压 20 / 20
低压保护时 间
抽芯压力 / 进芯速度
压力 ±5% 压力 ±5%
位置
注塑成形条件设定

注塑成型技术成形条件设定目录第一章安装模具1,理论锁模力计算 (3)2,模具相关尺寸确认 (7)3,模具安装 (11)第二章温度设定1,料筒温度设定 (13)2,模具温度设定 (13)3,干燥温度设定 (14)第三章计量设定1,理论计量值计算 (16)2,计量值设定 (17)第四章压力设定1,填充压力设定 (20)2,保压设定 (21)3,背压设定 (25)4,锁模压力设定 (27)第五章速度设定1,填充速度设定 (29)2,保压速度设定 (32)3,计量减压速度设定 (33)4,开合模顶出速度设定 (34)第六章位置设定1,V—P位置设定 (37)2,速度切换位置设定 (39)3,开合模及顶出位置设定 (40)第七章时间设定1,射出时间设定 (42)2,冷却时间设定 (43)3,计量时间控制 (45)4,周期时间控制 (47)第一章 安装模具一, 理论锁模力计算当融体注入模具型腔时,注射压力通过融体液压传递到模具型腔内,此时,需要一定的力来保证模具的闭合维持现状,这个力就是锁模力。
通常我们的注塑机就是按锁模力的大小来分类的,比如30吨,即锁模力就是30吨。
那么,在我们的实际生产中,锁模力合不合适呢,还需计算才知道。
产品实际所需锁模力大于机台锁模力时,可能会出现披锋现象,产品实际所需锁模力一定要小于机台锁模力方可量产,当然,若过小则造成资源浪费,也不合适,在此,将介召一下理论锁模力的计算方法;计算公式;F = K × P × A × 10F-----锁模力(吨)K-----安全系数(1-1.2)P-----模腔平均压力(kg )A-----产品和浇注系统在分型面上的最大投影面积(cm )2 -3单位转换;• 吨 ----- Kg ----- N1吨=1000Kg = 9.8kn1Kg=9.8N1N=(1/9.8)Kg=0.102Kg1kn=102Kg=0.102吨• Mp ----- PaPa=1N/mMPa=10 Pa=1000000Pa1m =10 cm1Mp=10 N/m =10 N/cm =100 N/cm =10.2Kg/cm模腔平均压力;当融体注入模具型腔时,注射压力通过射嘴,主流道,分流道与浇口后,压力液压传递到模具型腔内的压力已有一定的压力损失,那么模腔平均压力肯定会比螺杆的射出压力小,压力损失的太小与模具结构,材料特性,机器特性及其条件设定有关。
- 1、下载文档前请自行甄别文档内容的完整性,平台不提供额外的编辑、内容补充、找答案等附加服务。
- 2、"仅部分预览"的文档,不可在线预览部分如存在完整性等问题,可反馈申请退款(可完整预览的文档不适用该条件!)。
- 3、如文档侵犯您的权益,请联系客服反馈,我们会尽快为您处理(人工客服工作时间:9:00-18:30)。
模具成型条件参照表
模号 料号
试模次数 1 注塑机号 1# 材料 PBT+30%GF 产品名称 FC-10本体
开模人
试模人
韩培齐
颜色 黑色 产品单重 0.77克 模具温控制方式
耗用工时 2H
新次料比 100%: % 水口单重 10.38克 水温 ■ 油温 口 耗用原料 2Kg 干燥时间 2---5H 模穴数
32穴
模具温度 42±5℃ 周期时间 16±2〞 成型 温度 射咀温度 一段温度 二段温度 三段温度 240---280
220---260 200---240
200---240
℃
射胶
射五 射四 射三 射二 射一 % Bar mm
速度 70---99 压力 50---85 位置
时间
1---3 秒 射胶控制 口 位置 ■ 时间
保压
保四 保三 保二 保一 % Bar 秒 % Bar mm
速度 40---70 压力 40---65 时间
1.0—3.0
加料
前松退 加料一 加料二
加料三 后松退 速度 60---95 50---80 压力 60---100 50---80 位置
40---65
45---75
时间
秒 松退状态 口 前松退 ■后松退 松退控制 口位置 口前后松退 ■时间 锁模
快速 低速 低压 高压 % Bar
速度 30---55 20---45
10---25
10---25 压力 30---60 0 0 100---130 位置
90---130
60---90
48±2
mm 进以启动位置 mm 绞牙进启动位置 mm
开模 减速 中速 快速 慢速 %
速度 10---25 15---40 35---65 10---30 压力 8---25 10---25 25---55 35---70 Bar 位置
220---260
200---240
180---220
40---80
mm
抽芯启动位置一 mm 绞牙退进启动位置一 mm 抽芯启动位置二 mm 绞牙退进启动位置二 mm
模具成型条件参照表
模号
料号
试模次数 1
注塑机号 9# 材料 PA66 无纤 产品名称 JP01本体(格林客供) 开模人
试模人
韩培齐
颜色 淡绿色 产品单重 5.2克 模具温控制方式
耗用工时 2H
新次料比 100%: % 水口单重 克 水温 ■ 油温 口 耗用原料 2Kg 干燥时间 4H 模穴数
8穴
模具温度 43±5℃ 周期时间 20±2〞 成型 温度 射咀温度 一段温度 二段温度 三段温度 260---290
250---280 240---270
230---260
℃
射胶
射五 射四 射三 射二 射一 % Bar mm
速度 70---95 压力 50---75 位置
时间
1---3 秒 射胶控制 口 位置 ■ 时间
保压
保四 保三 保二 保一 % Bar 秒 % Bar mm
速度 45---65 压力 40---60 时间
1.0—3.0
加料
前松退 加料一 加料二
加料三 后松退 速度 65---95 50---75 压力 60---85 50---75 位置
70---90
75---95
时间
秒 松退状态 口 前松退 ■后松退 松退控制 口位置 口前后松退 ■时间 锁模
快速 低速 低压 高压 % Bar
速度 30---55 20---40
5---20
10---25 压力 30---50 0 0 100---130 位置
100---130
70---100
52±1
mm 进以启动位置 mm 绞牙进启动位置 mm
开模 减速 中速 快速 慢速 %
速度 5---25 10---30 35---55 5---20 压力 8---20 5---25 25---45 40---60 Bar 位置
200---220
180---200
160---180
60---80
mm
抽芯启动位置一 mm 绞牙退进启动位置一 mm
表单编号:BZC-RDT-009G/0。