存货风险控制和管理教育课件
库存控制管理培训教材(PPT 55张)
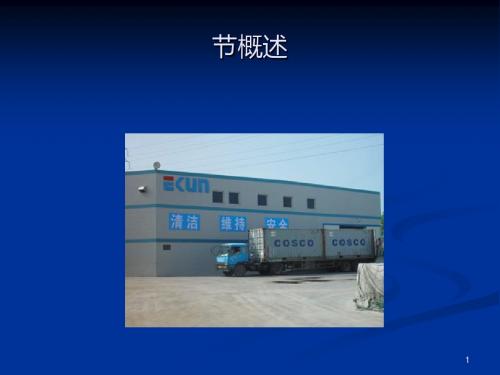
DC Q TC DP K Q 2
D — 年需求量 P — 单位采购成本 C — 每次订货成本 Q — 每次订货批量 K,PF — 单件物品年均保 管费 F — 储存费率 若使TC最小,将上 式 对Q求偏导并令其等 于0,得EOQ公式
24
一、经济订货批量 (三)经济订货批量模型 经济订货批量(EOQ)公式:
16
表3 库存品的累积耗用金额和累积百分比
库存品 代号 b f d h a g i j c e 年耗用金额 (元 ) ③ 1520000 1250000 400000 320000 200000 90000 50000 35000 28000 18000 累积用金额 (元)④ 1520000 2770000 3170000 3490000 3690000 3780000 3830000 3865000 3893000 3911000 累积百分比 (%) 38.9 70.8 81.1 89.2 94.3 96.6 97.9 98.8 99.5 100.0 分类 A A B B B C C C C C
15
表2 各种库存品的年耗用金额 库存品代号 a b c d e f g h i j 年耗用金额(元) ③= ①x ② 200000 1520000 28000 400000 18000 1250000 90000 320000 50000 35000 从大到小次序 5 1 9 3 10 2 6 4 7 8
(三)定期订货方式优缺点 1、优点 可以合并出货,减少订货费; 避免了定量订货每天盘存的做法,减少工作量; 库存管理的计划性强。 2、缺点 安全库存量设置的较大; 每次订货的批量不固定,无法制定出经济订货批 量,因而运营成本较高,经济性较差。
34
存货管理及风险共担培训资料PPT课件( 61页)
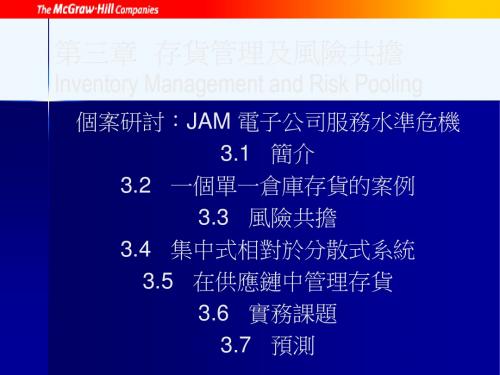
因為固定成本於每次訂購時都必須支付,持有 成本可被視為每一單位產品單位期間的持有成 本h、平均存貨水準Q/2,及週期長度T之乘 績。
3.2.1 經濟批量模式
(The Economic Lot Size Model)
Demand Scenarios
30% 25% 20% 15% 10% 5% 0%
8000 10000 12000 14000 16000 18000
Sales
Dema n d
Proba b il it y
Weighted Deman d
8000 11%
880
10000 11%
1100
12000 28%
3.2.3 供應合約
供應合約中,買方和供應商通常會規範以 下條款: 價格和數量折扣 最小與最大訂購量 運輸前置時間(交期) 產品或原料品質 退貨政策
3.2.3 供應合約
數種不同的供應合約可用來達到風險分擔的效 果,並增加供應鏈中各個成員的利潤:
買回合約 (Buy-Back Contracts) 營收分享合約 (Revenue-Sharing
– 原料存貨 – 在製品存貨(WIP) – 製成品存貨
3.1 簡介
為何要持有存貨?其中一些理由包括:
– 因應顧客需求的非預期變動。 – 許多供應的數量和品質、供應商的成本
和配送時間等出現明顯的不確定情況。 – 運輸公司提供的規模經濟,鼓勵公司運
輸大量貨品,因此也持有大量的存貨。
3.1 簡介
存貨管理的2個重要議題: 1. 需求預測 2. 訂購量計算
Contracts)
库存控制与管理培训课件(PPT 64张)

1、定量与定期库存控制方法
1.1、定量库存控制方法
定量库存控制法概述
定量库存控制法也称为订购点法,是以固定订购点和订购批量为基础的一
种库存量控制方法。
订购批量和订购点的确定
订购批量一般采用经济订购批量(EOQ)。
订购点,则是提出订购时的储备量标准,订购点的确定取决于备运时间的需 要量和保险(安全)储备库存量。
订购点量=10×30+100=400(吨)
保险储备量=(预计日最大耗用量-每天正常耗用量)×订购提前期日数
保险储备量=(40-30)×10=100(吨)
1.4 定量与定期库存控制方法
定量库存控制法的库存量变动
定量库存控制的库存量变动情况如图7-1所示。
双堆法
双 堆法也叫分寸控制法。
1.5 定量与定期库存控制方法
①需要量大的主要原材料,必须严格管理的重要物资,有保管期限制 的物资。 ②需要量变化大而且可以预测的物资。 ③发货繁杂、难以进行连续库存动态登记的物资。
2、EOQ库存控制模型
EOQ库存控制策略 EOQ(Economic Order Quantity),被称为经济订购批量,是侧重从企 业本身经济效益来综合分析物料订购和库存保管费用的一种科学方法。
3.9、MRP采购订货的确定方法
表2 部件B的需求量计算(部件B,提前期=1,批量=20, 1A=2B=2×10=20)
时段(周) 1 毛需求量 已分配量 计划收到 现有库存 (10)
定期库存控制法的优缺点与定量库存控制法相反
1.11 定量与定期库存控制方法
定量与定期库存控制法的适用范围 1.定量库存控制法的适用范围 定量库存控制法一般适用于下列物资: ①单价较低的物资。
企业库存管理与风险分担课件

定期订货模型 时间驱动 Q是变化的
T,盘点期到来时
只在盘点期记录 较大
24
6.持续检查策略
假设:
每日需求随机,但满足正态分布。 分销商每次向制造厂订购产品,需要支付一个固定的成
本K,再加上与订购数成比例的费用。 库存持有成本根据单位时间保存单位库存的费用计算。 提前期固定。 如果顾客订单到达时,手头无库存满足客户需求,这笔
15
单期库存案例
16
固定生产成本10万美元,可变生产成本为单件80美元 单价售价125美元,产品残值20美元
假定公司生产10000件,我们计算得出各种需求状况下的利润
也就是说,当公司生产10000件产品时,有11%的概率获得 140000美元的利润,有89%的概率获得350000美元的利润。 因此,生产10000件产品的平均利润 =140000*11%+350000*89%=326900
式中,AVG AVGL 代表提前期内的平均需求
z AVGLSTD2 AVG2 STDL2 代表将要保持的安全库存
订货批量: Q 2K AVG
h
34
8.定期检查策略
库存水平的检查是周期性的,间隔期是固定的,每次检查后都 要订购适当的数量。
间隔期短的情况:
采用(s,S)策略,如果库存下降到s以下,就订购足够多的产 品使库存量达到S。
考虑的是公司已经拥有库存的情况,如果企业生产就必须 支付固定费用。
需要考虑的问题是企业拥有多少初始库存时就不必再生产
产品?
(如果初始库存刚好是8500件?)
22
5.多次订货
➢持续检查策略
在这种策略中,库存每天都要检查,当库存达到特定水平或 订货点时就下达订单。 当库存可以持续检查时,这种库存策略最适用---如采用计算 机化系统。
库存控制与管理培训课程(PPT52张)
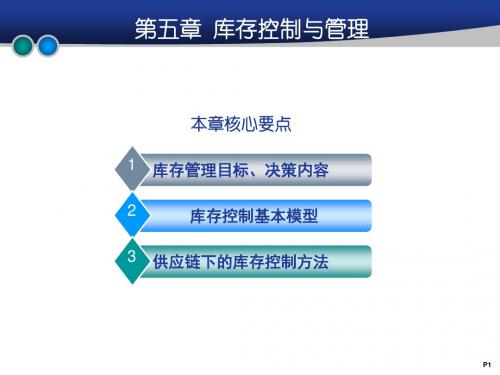
再订货点法 工作原理
持续不断监视库存的变化,当库存下降到某个预定点时, 即按固定量订货,经过一段提前期,订货到达补充库存。又 称永续库存系统。
特点
持续检查库存余量有利于控制 固定订货批量 数据更新及时灵活(定期、即期) 管理工作量较大 需要定期核查库存状态
P9
再订货点法:经济订货批量 EOQ
库存=经常性库存+安全库存 ROP一部分是提前期内的常规库存,即提前期内的平均需 求或预计需求,另一部分是为弥补需求和提前期的不确定 性而格外设置的库存,即安全库存(SS)。 提前期内的常规库存可以通过对历史数据的统计预测分析 得来。 安全库存是一种额外持有的库存,它作为一种缓冲器用来 补偿在订货提前期内实际需求量超过期望需求量或实际提 前期超过期望提前期所产生的需求。 安全库存的多少也取决与对客户服务水平要求的高低!
调节库存
调节库存是指为调节需求或订货的不平衡、订货速度不均 衡、各生产阶段的产出不均衡而设置的库存。
在途库存
在途库存是指处于运输过程以及停放在相邻两个工作地点 之间或相邻两个组织之间的库存。
P4
库存成本的构成
购入成本
当物资从外部购买时,购入成本指单位购入价格;当物资由企业 内部生产时,指单位生产成本。
当Q取其它值时,可按同样方法算出EL(Q),结 果如表2所示,由表2可以得出最佳订货量为30份。
期望利润最大法
比较不同订货量下的期望利润,取期望利润最大 的订货量作为最佳订货量设订货量为Q时的期望利 润为Ep(Q)。
不确定型的再订货点控制模型
需求不确定、提前期不确定、需求和提前期不确定
是长时间内需求反复发生,库存需要不断补充的。 确定型,需求和提前期固定时 • 即刻补货(经济订货批量 EOQ ) • 非即刻补货(订货生产批量 POQ ) 不确定型 • 从条件分 :需求不确定; 提前期不确定; 需求和提前期都不确定 • 从管理方法分: » 再订货点法
存货管理风险与关键环节控制教材
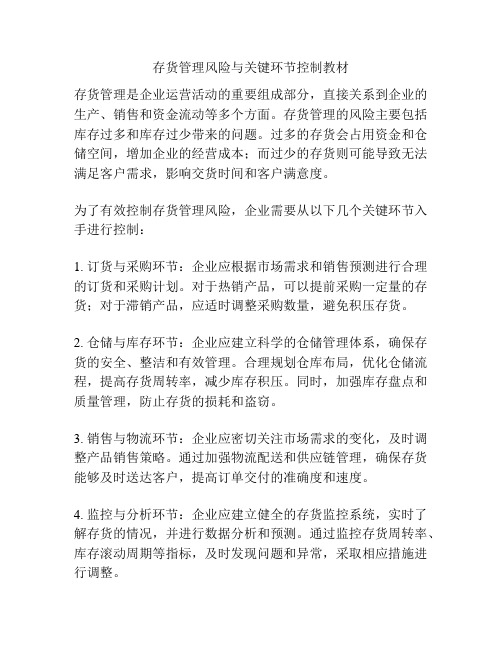
存货管理风险与关键环节控制教材存货管理是企业运营活动的重要组成部分,直接关系到企业的生产、销售和资金流动等多个方面。
存货管理的风险主要包括库存过多和库存过少带来的问题。
过多的存货会占用资金和仓储空间,增加企业的经营成本;而过少的存货则可能导致无法满足客户需求,影响交货时间和客户满意度。
为了有效控制存货管理风险,企业需要从以下几个关键环节入手进行控制:1. 订货与采购环节:企业应根据市场需求和销售预测进行合理的订货和采购计划。
对于热销产品,可以提前采购一定量的存货;对于滞销产品,应适时调整采购数量,避免积压存货。
2. 仓储与库存环节:企业应建立科学的仓储管理体系,确保存货的安全、整洁和有效管理。
合理规划仓库布局,优化仓储流程,提高存货周转率,减少库存积压。
同时,加强库存盘点和质量管理,防止存货的损耗和盗窃。
3. 销售与物流环节:企业应密切关注市场需求的变化,及时调整产品销售策略。
通过加强物流配送和供应链管理,确保存货能够及时送达客户,提高订单交付的准确度和速度。
4. 监控与分析环节:企业应建立健全的存货监控系统,实时了解存货的情况,并进行数据分析和预测。
通过监控存货周转率、库存滚动周期等指标,及时发现问题和异常,采取相应措施进行调整。
5. 供应商管理环节:企业应认真选择和管理供应商,建立长期稳定的合作关系。
与供应商进行有效沟通和协调,共同制定合理的供货计划,避免因供货不及时、质量问题等原因带来的存货管理风险。
在进行存货管理的过程中,企业还可以利用信息化技术,如ERP系统等,实现存货管理的自动化和精细化。
通过提高信息的透明度和可追溯性,有助于企业更好地控制存货管理风险。
综上所述,存货管理风险是企业经营中不可忽视的一环,合理的存货管理是实现企业高效运营和可持续发展的重要保障。
通过对存货管理的关键环节进行科学控制,企业可以有效降低风险,提高运营效率,实现可持续发展。
存货管理及风险共担(ppt 19)

policy)
每隔固定时间检查,决定订购量与确认过时产品 每隔固定时间检查,决定订购量与确认过时产品
使用率,前置时间和安全存货的严格管理 减少安全存货水准 可藉减少前置时间达成 导入或实施周期盘点作业 以每天盘点部份,一年盘点数次取代 以每天盘点部份,一年盘点数次取代
www.3722. 来自 中国最大的资料库下载
3.7.1 判断法 Judgment Methods
判断法是以系统性的方法综合不同专家的意 见. 一组专家可以组合起来以获取共识,靠沟通 与分享资讯. 德尔菲法(Delphi method) 是一种结构性的技 术.在不集合专家到同一个地点的状况下, 藉问卷方式获得专家一致的意见.此技术是 为避免决策过程中的风险和个人喜好而设计.
www.3722. 来自 中国最大的资料库下载第ຫໍສະໝຸດ 章 存货管理及风险共担谢谢
www.3722. 来自 中国最大的资料库下载
第三章 存货管理及风险共担
�
第三章 存货管理及风险共担
3.5 在供应链中管理存货
考虑同一家公司一个多设施的供应链.公司的 目的在管理其存货以降低整体系统成本,因此 考虑不同设施间的互动以及这些互动对每个设 施所采取存货政策的影响. 单一仓库服务某些供应商的二项假设:
1. 2.
存货决策由单一决策者制订,且其目标是使整体系统 成本减到最小. 决策者可获取各零售商和仓库的存货资讯.
www.3722. 来自 中国最大的资料库下载
第三章 存货管理及风险共担
3.7.2 市场研究法 Market Research Methods
市场测试法 (market testing) 和市场调查 (market surveys) 方法可以有效建立预测.尤其是对新产 品的预测. 市场测试法:潜在顾客的焦点团体被集合且试用 新产品,其反应情况可以用来推断整个市场对产 品的需求. 市场调查:包括从不同潜在顾客搜集产品资料, 主要是透过当面访谈,电话抽访,问卷等方式进 行.
物资仓储管理风险识别与控制ppt课件

二0一五年七月
1
课堂或现场培训注意事项
紧急逃生出口 手机静音 守时(团队) 参与,关注课程、积极发言 每次一人发言 不在教室吸烟 其他事项
由培训老师结合培训内容和 培训对象特点开展经验分享
课程安排
一、常见的风险 二、风险识别 三、风险评价 四、风险控制 ……….
2、危险源:可能导致死亡、伤害、职业病、财产损失、工作环境破 坏或这些情况组合的根源或状态。危险源由三个要素构成:潜在危 险性、存在条件和触发因素。
二、风险识别(危害因素辨识)
(一)相关概念:
3、风险:危险的程度(矩阵法,低、中、高)。风险用在生产系统中事故发 生的可能性与严重性的结合给出。
4、风险评价:是指通过识别生产经营活动中存在的危险、有害因素,并运用 定性或定量的统计分析方法确定其风险严重程度,进而确定风险控制的优先 顺序和风险控制措施,以达到改善安全生产环境、减少和杜绝安全生产事故 的目标而采取的措施和规定。
2、所有进入分公司作业场所人员的活动或服务,包括承包商和访问者;
3、作业场所内的所有设备、设施(包括组织内部和外界所提供的); 4、周边环境存在的危害因素以及危害因素的各种类型。 •危害因素识别(全员参与)完成后,拟出危害因素识别清单,填写WZ/HSEJL -01《危害因素辨识及评价表》,列出所识别出的危害因素。(全员风险表, 公司清单、评介、重要目录(分级控制))
一、物资仓储管理过程中常见的风险
(一)物资装卸风险
1、人员:人员无资质、未培训、选择位置不当、未按操作规范操作 、 指挥、捆绑等;
2、物资装卸选用机具、设备、吊具不当; 3、机具、设备故障所带来的风险;(保养、作业前检查) 4、作业环境所带来的风险等。(隔离、地面条件、
- 1、下载文档前请自行甄别文档内容的完整性,平台不提供额外的编辑、内容补充、找答案等附加服务。
- 2、"仅部分预览"的文档,不可在线预览部分如存在完整性等问题,可反馈申请退款(可完整预览的文档不适用该条件!)。
- 3、如文档侵犯您的权益,请联系客服反馈,我们会尽快为您处理(人工客服工作时间:9:00-18:30)。
4 遠隔地・低頻度棚 遠隔地・低頻度 部品搬入
遠隔地・低頻度
部品ピック
空箱整理場
5
Bレーン
1
部品供給
02 08 空箱回収
L /O カウンタ
1.2.2 外物流方式介绍---乘合便
各种各样的从供应商收集并纳入的方法。
短周期、小批量、多频次、平准化的引取
供应商
多频次引取 Ex.8次/天
工厂
多频次引取和物流效率都可兼顾
式样单位
这次关于排列的平准化
(计划条件)
根据条件 进行均等的生产
1.2.1 平准化生产
——按平均化进行生产・・・
工作量的稳定化
如果2台连续作业的话会有很大的作业迟缓! 所以希望有间隔的投入!
2台连续生产非常困难!!
部品供给的稳定化
按这种样子进行运搬 是放不进部品棚的!
这个部品 怎么处理
生产线速度 (1人的作业时间 1分/台)
P IC S
分散A L C
順引F A X
生 産 指 示
英泰
豊通
79便/日
順 引 き
DOCK
受 入
検収場
大物 空置場
5
大物ストアー
7
24
・
Pレーン
05 08
・
・ ・
6
・
・
・
6
5
4
3
2
1
空箱置場
空箱セット
5 ルート別
5
順建て場 順建 P J 棚
3
仕分け棚
2
PC3
部品搬入 部品ピック
PC3 PC2 PC2
供应商A
制造工厂
用于解决货量较大,路线特殊的供应商。
1.2.2 外物流方式介绍---顺引
供应商
指示信息
序号 种类
116611 A A 116622 B B 116633 C C 116644 D D 116655 E E 116666 F F
按照生产顺序进行原材料的引取
生产线旁没有多余的库存! 原材料的放置空间减小, 有效提高生产效率!
発注~納入L /T =2 日
3464m3/日
MAX→24オーダー
乗合便 1 4 0 8 パレ/日
9 8 2 4 箱/日(計2 1 0 0 スキット)
長春地区
仕入先
仕入先
2ルート 7 便/日
乗合便 発注~納入L /T =5 日
293m3/日
MAX→12オーダー
9 7 パレ/日 1 2 1 箱/日(計1 5 スキット)
8H库存 6H库存 4H库存 2H库存
最大容量 最大库存 安全库存 最低库存
1.1.4 库存基准的考虑要素
最大容量 最大库存 安全库存 最低库存
原材料库存 在制品库存 成品库存
所占面积、 生产批量、 运输批量等 生产批量、 运输批量、 物流周期等 生产批量、 运输批量、 物流周期等 生产批量、 异常频率、 物流周期等
T T C C
T -L M S
T M C 生産管理部
セット&バルクオーダー
タイムライン情報 荷量情報
生産管理課
G PPS PA M S
部品系 P -S M S
NQC
生計デ-タ-
e-kan b an
L P IP
内示
CCR 生産指示
G -A LC
T F T M 塗装吊り上 情報F A X 情報を基き 部品順序並び
現調部品
上海地区
仕入先
仕入先
乗合便
サブ1 2 ルート 仕入先 1 4 便/日
1 1 6 2 箱/日(計8 5 スキット)
発注~納入L /T =6 日
MAX→24オーダー
上海中継地 部品集荷 部品出荷
メン-1ルート 3 便/日
89.28m3/日
天津地区
仕入先
仕入先
サブ2ルート 6便/日 メン-2 4 ルート 1 5 1 便/日
(モジュール-)
利通物流 コンテナ-保管
9 本/日
モジュール ○A 5 5 本 ○w 2 0 本
T F L 物流 デバン・開梱 P C 搬入・出荷
オーダー数 J A 、J E →2 4 オーダー J D →1 4 オーダー J J →8 オーダー
1 4 便/日
2 7 7 3 箱/日 (計3 0 0 パレ)
1.2 丰田物流库存体系
1.2.1 平准化生产 1.2.2 外物流方式介绍 1.2.3 内物流方式介绍
1.2.1 平准化生产
平准化是
生产物品(和销售相联)的种类和数量的总和平均化
量
・生产线 ・式样
・量的平准化
・每一天中排列的平准化 (连续性,间隔性・・・)
N
N+1
N+2
年间・月间・周间・日・小时
顾客
物料流
信息流
1.1.2 库存的种类
最大容量 最大库存 安全库存 最低库存
当前部品放置区域能够存放的最大库存值 在保证安全生产前提下,考虑外物流设定的最大库存值
在保证安全生产前提下设定的最小库存值 为防止出现不满足当日生产需求而设定的警示库存
1.1.3 库存基准的设定
保证生产顺利进行,吸收生产过程中的波动, 而设定的库存范围,称作库存基准。
1.2.2 外物流方式介绍---中继地
供应商
通过主线与分线路的分离,实现高效率的主线运输!
短距离运输
分路线
主路线
远距离运输
工厂
供应商
中间仓库 中间过渡机能
多回/日
积载率高
中间仓库起到分割货量的机能,从而实现远距离多回运输
1.2.2 外物流方式介绍---直纳
通过专用车辆运送制定供应商的货物,实现积载效率提升! 1次/日
0.8分/台
物流的稳定化
如果第1车和第2车能平均的话 这样的事情就不会发生!!
0.9分/台
1.1分/台 每一台的作业时间
装的不好!
工厂 第1车 第2车
1.2.2 外物流方式介绍
C K D 部品
仕入先 仕入先
仕入先
オーダー情報 発注~天津港LT=21日
飛島物流 センター
名 古 屋 港 コンテナー
天
津 港 在庫6日分
引取 信息
生产顺序
⑥
⑤
④
③
②
①
工厂
166 F 166 F
165 E 165 E
164 D 164 D
163 C 163 C
162 B 162 B
161 A 161 A
1.2.3 内物流方式介绍
DOCK
受 入
8
检收场
大物 空置場
存货风险控 制和管理 PPT讲座
第一章 库存与物流管理
1.1 库存的概念和分类
1.1.1 库存相关的物流过程
供应商
采购物流
原材料运输 (集合便)
生产物流
生产过程 零部件搬运
供给
销售物流 完成车
1.1.2 库存的种类
采购物流
供应者
原材料库存
生产物流
在制品储存
销售物流
完成品储存
1.1.5 工厂在库基准设定案例
顺引
顺引 供应商
1车/H、16台/车 16~32台(1H~2H)
外地 供应商
指示纳入
1车/1~2日
本地中继地
受存
配
入储
货
2~3日
纸看板后补充
4车/日
PC区
受
入
存
检
储
查
工厂
大件顺引区
上 线 供 给
本地 供应商
本地 供应商
乘合便
本地 供应商
4车/日
4~6H
1~2H
1.2 丰田物流库存体系