ABB测试台说明书样本
ABB ControlMaster CM10、CM30、CM50和CM15零件列表说明书

—A B B M E A SU R EM ENT A N D A N A LY TI C S | PA RTS LIS T | PL/CM -EN R E V NControlMaster CM10, CM30, CM50 and CM15Universal process controllers and indicator Spare partsMeasurement made easyIntroductionThis parts list contains exploded diagrams of the ControlMaster universal process controllers and indicator for easy identification of spare parts.—SalesService2CO NTRO LM A S TE R CM10, CM30, CM50 A N D CM15 SPA R E PA RTS | PL/CM R E V. N —Parts identificationCM10Figure 1 Identification of parts — CM103 CO NTRO LM A S TE R CM10, CM30, CM50 A N D CM15 SPA R E PA RTS | PL/CM R E V. NItem No.Description Part number 1Snap rivet B11780 2Battery B12792 3Type 1 function key (including items 1, 2, and 4)CM30/0706 4Function key support CM30/01205Mainboard CM30/0701 Mainboard (24 V DC)CM30/07026RS485 communications module upgrade kit CM30/0708 Ethernet communications module upgrade kit CM30/07097Option board 1a (1 relay)CM30/0703 Option board 1 (1 analog O/P, 2 digital I/O and 3 relays)CM30/07048Single panel clamp assembly CM10/0711 9Case moulding CM10/0056 10Thermistor assembly CM30/0052 11Panel seal CM10/0106 12Terminal cover CM10/0115 13Ethernet cable assembly CM30/0070P 14Bezel release tool CM30/0114 15Snap rivet B12722 16Bezel seal (including display dust gasket)CM10/0105 17Switch extender CM10/0107 18Bezel CM10/005319Membrane overlay CM10/0180 Membrane overlay (blank)CM10/018120O-ring B12794 21Light guide CM30/0112 22Display and processor board assembly CM10/0700Key to Figure 14CO NTRO LM A S TE R CM10, CM30, CM50 A N D CM15 SPA R E PA RTS | PL/CM R E V. N —...Parts identificationCM15Figure 2 Identification of parts – CM155 CO NTRO LM A S TE R CM10, CM30, CM50 A N D CM15 SPA R E PA RTS | PL/CM R E V. NItem No.Description Part number1Membrane overlay CM15/0180 Membrane overlay blank CM15/01812O-ring B12794 3Bezel moulding (including display dust gasket)CM15/0053 4Light guide CM30/0112 5Bezel seal CM10/0105 6Switch extender CM15/0107 7Display and processor board assembly CM15/0700 8Snap rivet B12722 9Type 1 function key (including items 11, 12 and 13)CM30/0706 10Type 2 function key CM30/0707 11Function key support CM30/0120 12Snap rivet B11780 13Battery B1279214Mainboard CM30/0701 Mainboard (24 V DC)CM30/070215Single panel clamp assembly CM10/0711 16Terminal cover CM10/0115 17Ethernet cable assembly CM30/0070P 18Panel seal CM10/0106 19Thermistor assembly CM30/0052 20Case assembly CM10/005621RS485 communications module upgrade kit CM30/0708 Ethernet communications module upgrade kit CM30/070922Option board 1a (1 relay)CM30/0703 Option board 1 (1 analog O/P, 2 digital I/O and 3 relays)CM30/070423Bezel release tool CM30/0114 Key to Figure 26CO NTRO LM A S TE R CM10, CM30, CM50 A N D CM15 SPA R E PA RTS | PL/CM R E V. N —...Parts identificationCM30Figure 3 Identification of parts – CM307 CO NTRO LM A S TE R CM10, CM30, CM50 A N D CM15 SPA R E PA RTS | PL/CM R E V. NItem No.Description Part number 1Snap rivet B11780 2Battery B12792 3Type 1 function key (including items 1, 2 and 5)CM30/0706 4Type 2 function key CM30/0707 5Function key support CM30/01206Mainboard CM30/0701 Mainboard (24 V DC)CM30/07027RS485 communications module upgrade kit CM30/0708 Ethernet communications module upgrade kit CM30/07098Option board 1a (1 relay)CM30/0703 Option board 1 (1 analog O/P, 2 digital I/O and 3 relays)CM30/07049Option board 2 (2 analog I/P and 4 digital I/O)CM30/0705 10Single panel clamp assembly CM30/0711 11Terminal cover CM30/0115 12Panel seal CM30/0106 13Thermistor assembly CM30/0052 14Ethernet cable assembly CM30/0070P 15Case assembly CM30/0056 16Bezel release tool CM30/0114 17Snap rivet B12722 18Bezel seal CM30/0105 19Switch extender CM30/0107 20Bezel assembly (including display dust gasket)CM30/005321Membrane overlay CM30/0180 Membrane overlay blank CM30/018122O-ring B12794 23Light guide CM30/0112 24Display and processor assembly CM30/0700Key to Figure 38CO NTRO LM A S TE R CM10, CM30, CM50 A N D CM15 SPA R E PA RTS | PL/CM R E V. N —...Parts identificationCM50Figure 4 Identification of parts – CM509 CO NTRO LM A S TE R CM10, CM30, CM50 A N D CM15 SPA R E PA RTS | PL/CM R E V. NItem No.Description Part number 1Type 1 function key (including items 2, 3 and 5)CM30/0706 2Snap rivet B11780 3Battery B12792 4Type 2 function key CM30/0707 5Function key support CM30/01206Mainboard CM50/0701 Mainboard (24 V DC)CM50/07027RS485 communications module upgrade kit CM30/0708 Ethernet communications module upgrade kit CM30/07098Option board 1 (2 analog I/P, 4 digital I/O, 1 analog O/P and 2 relays)CM50/0703 9Single panel clamp assembly CM30/0711 10Case assembly CM50/0056 11Panel seal CM50/0106 12Terminal cover CM50/0115 13Thermistor assembly CM30/0052 14Ethernet cable assembly CM30/0070P 15Bezel release tool CM30/0114 16Snap rivet B12722 17Display and processor board assembly CM50/0700 18Bezel seal CM50/0105 19Switch extender CM30/0107 20Bezel moulding (including display dust gasket)CM50/005321Membrane overlay CM50/0180 Membrane overlay blank CM50/018122O-ring B12794 23Light guide CM30/0112Key to Figure 410CO NTRO LM A S TE R CM10, CM30, CM50 A N D CM15 SPA R E PA RTS | PL/CM R E V. N—Service / Upgrade kitsCommonDescription Part number Type 1 function key upgrade kit CM30/0706 Type 2 function key upgrade kit CM30/0707 Rs485 communications upgrade kit CM30/0708 Ethernet communications upgrade kit CM30/0709 ConfigPilot PC configuration kit CM30/0715 IrDA bracket CM30/0716CM10, CM15 and CM30Description Part number Main board replacement kit CM30/0701 Main board replacement kit (24 V DC)CM30/0702 Option board 1a – single relay option upgrade kit CM30/0703 Option board 1 – 1 analog O/P, 2 digital I/O and 3 relay option upgrade kit CM30/0704CM10 and CM15Description Part number DIN rail mounting kit CM10/0715 Single panel clamp assembly CM10/0711CM30 and CM50Description Part number Single panel clamp assembly CM30/0711CM10Description Part number Display and processor board replacement kit CM10/0700CM15Description Part number Display and processor board replacement kit CM15/0700CM30Description Part number Display and processor board replacement kit CM30/0700 Option board 2 – 2 analog I/P and 4 digital I/O CM30/0705CM50Description Part number Display and processor board replacement kit CM50/0700 Main board replacement kit CM50/0701 Main board replacement kit (24 V DC)CM50/0702 Option board 1– 2 analog I/P, 1 analog O/P, 4 digital I/O and 2 relay option upgrade kit CM50/070311 CO NTRO LM A S TE R CM10, CM30, CM50 A N D CM15 SPA R E PA RTS | PL/CM R E V. NManualsDescription Part number User manual (base functionality) – CM10, CM30 and CM50IM/CM/B-EN User manual (standard functionality) – CM10, CM30 and CM50IM/CM/S-EN User manual (extended / dual functionality) – CM30 and CM50IM/CM/ED-EN User manual (indicator functionality) – CM15IM/CM/I-EN Communications supplement – CM10, CM15, CM30 and CM50IM/CM/C-EN PackagingDescription Part number CM30 and CM50 outer box CM30/0008 CM30 and CM50 outer box (unprinted)CM30/0009 CM30 and CM50 internal insert CM30/0010 CM10 and CM15 outer box CM10/0008 CM10 and CM15 outer box (unprinted)CM10/0009P L /C M R e v . N 05.2023—ABB Measurement & Analytics For your local ABB contact, visit:/contactsFor more product information, visit:/measurement—We reserve the right to make technical changes or modify the contents of this document without prior notice. With regard to purchase orders, the agreed particulars shall prevail. ABB does not accept any responsibility whatsoever for potential errors or possible lack of information in this document.We reserve all rights in this document and in the subject matter and illustrations contained therein. Any reproduction, disclosure to third parties or utilization of its contents – in whole or in parts – is forbidden without prior written consent of ABB.©ABB 2023All rights reserved.。
ABB 产品信息说明书
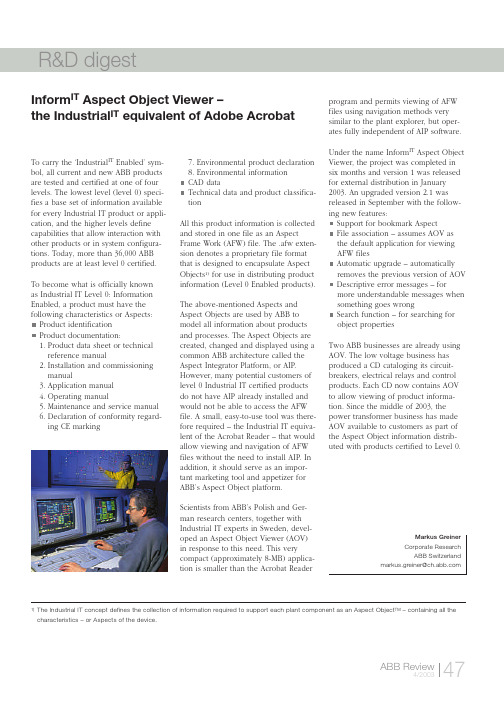
To carry the ‘Industrial IT Enabled’ sym-bol, all current and new ABB products are tested and certified at one of four levels. The lowest level (level 0) speci-fies a base set of information available for every Industrial IT product or appli-cation, and the higher levels define capabilities that allow interaction with other products or in system configura-tions. Today, more than 36,000 ABB products are at least level 0 certified. To become what is officially known as Industrial IT Level 0: Information Enabled, a product must have the following characteristics or Aspects: Product identificationProduct documentation:1.Product data sheet or technicalreference manual2.Installation and commissioningmanual3.Application manual4.Operating manual5.Maintenance and service manual6.Declaration of conformity regard-ing CE marking7.Environmental product declaration8.Environmental informationCAD dataTechnical data and product classifica-tionAll this product information is collectedand stored in one file as an AspectFrame Work (AFW) file. The .afw exten-sion denotes a proprietary file formatthat is designed to encapsulate AspectObjects1)for use in distributing productinformation (Level 0 Enabled products).The above-mentioned Aspects andAspect Objects are used by ABB tomodel all information about productsand processes. The Aspect Objects arecreated, changed and displayed using acommon ABB architecture called theAspect Integrator Platform, or AIP.However, many potential customers oflevel 0 Industrial IT certified productsdo not have AIP already installed andwould not be able to access the AFWfile. A small, easy-to-use tool was there-fore required – the Industrial IT equiva-lent of the Acrobat Reader – that wouldallow viewing and navigation of AFWfiles without the need to install AIP. Inaddition, it should serve as an impor-tant marketing tool and appetizer forABB’s Aspect Object platform.Scientists from ABB’s Polish and Ger-man research centers, together withIndustrial IT experts in Sweden, devel-oped an Aspect Object Viewer (AOV)in response to this need. This verycompact (approximately 8-MB) applica-tion is smaller than the Acrobat Readerprogram and permits viewing of AFWfiles using navigation methods verysimilar to the plant explorer, but oper-ates fully independent of AIP software.Under the name Inform IT Aspect ObjectViewer, the project was completed insix months and version 1 was releasedfor external distribution in January2003. An upgraded version 2.1 wasreleased in September with the follow-ing new features:Support for bookmark AspectFile association – assumes AOV asthe default application for viewingAFW filesAutomatic upgrade – automaticallyremoves the previous version of AOVDescriptive error messages – formore understandable messages whensomething goes wrongSearch function – for searching forobject propertiesTwo ABB businesses are already usingAOV. The low voltage business hasproduced a CD cataloging its circuit-breakers, electrical relays and controlproducts. Each CD now contains AOVto allow viewing of product informa-tion. Since the middle of 2003, thepower transformer business has madeAOV available to customers as part ofthe Aspect Object information distrib-uted with products certified to Level 0.Inform IT Aspect Object Viewer –the Industrial ITequivalent of Adobe AcrobatMarkus GreinerCorporate ResearchABB Switzerland*********************.com 1)The Industrial IT concept defines the collection of information required to support each plant component as an Aspect Object TM– containing all the characteristics – or Aspects of the device.An ABB collaboration has resulted in an improved programming method that not only speeds up the programming of robot automation tasks, but also opens up areas for automation that are presently inaccessible due to traditional programming being too complex and taking too long in relation to production time.ABB robots have to be extremely versa-tile. Used across almost the whole of in-dustry for tasks ranging from automated assembly and materials handling to arc-welding, every extra ounce of versatility added to them can significantly increase their range of application. As a robot is essentially a moving object, spatial in-formation has to be conveyed accurately and reliably to it. Adding flexibility therefore makes traditional program-ming more complex and time-consum-ing. The advantages to be gained fromfinding new, alternative methods of re-laying information fast (and accurately)to the robot make this field of researchas challenging as it is interesting.With robots playing an ever more im-portant role in our everyday lives, theidea that humans should be able tocommunicate with them using methodsas close as possible to those they use tocommunicate with each other is gainingmomentum. Communication amonghumans is multi-modal (ie, a combina-tion of gesture and speech) and oftenintuitive, and institutions like CarnegieMellon University (CMU) have used thisidea to increase human-machine inter-action. As a world leader in industrialrobot technology, ABB is benefitingfrom this experience by working to-gether with the Advanced MechatronicsLaboratory at CMU on a project whichuses the idea of the human arm andhand gestures as a natural way toconvey spatial information – in otherwords, gesture-based programming.ABB’s approach is backed up by Pro-fessor Pradeep Khosla, head of the AMLand Electrical and Computer Engineer-ing Department at CMU when he says,“As robots enter the human environ-ment and come into contact with inex-perienced users, they need to be ableto interact with the users in an intuitiveway. The keyboard and mouse are nolonger acceptable as the only meansof input.”Gesture-based programmingin a nutshellCMU has been working in the area ofgesture-based programming (GBP) formany years now. The goal of GBP is toprovide a more natural environmentfor the user, and to generate morecomplete and successful programs byfocusing on task experts rather thanprogramming experts.The process begins with a persondemonstrating the task to be pro-grammed. The person’s hand and fin-gertips are observed through a sen-sorized glove with special tactilefingertips. The modular glove systemsenses hand pose, finger joint anglesand fingertip contact conditions.Objects in the environment are sensedwith computer vision while a speechrecognition system extracts high-levelcontrol information. Primitive gestureclasses are extracted from the raw sen-sor information and passed to a gestureinterpretation network. The system isself-adaptive in the sense that knowl-edge of previously acquired skillsretained by the system is used to inter-pret the gestures during training, withcontrol feedback provided during run-time. The output of the GBP system isthe executable program for performingThe ‘human touch’ –advanced robot programmingR&D digest the demonstrated task on the targethardware.What it means for ABBSince robotic arc welding is inherentlythree-dimensional, hand gestureswould be an intuitive tool for provid-ing parameters such as position, veloci-ty, acceleration, size, direction, angleand angular velocity to enable fasterand accurate programming of the ro-bot. Speech would also play an impor-tant part in enhancing this system byproviding high-level control informa-tion. Therefore, CMU scientists togetherwith ABB experts have developed andevaluated a programming system witha multi-modal interface for robotic andarc-welding applications.The system has the following main com-ponents:Cyberglove to measure the positionand movement of the fingers andwrist (gesture sensing)Polhemus Fastrak 6-DOF sensors for position sensingMicrosoft speech recognition system PCWebWare for robot-PC communications ABB robotThe PC mediates between the multi-modal input devices (glove and speech) and the ABB robot. On the input side it runs software that translates raw voice and glove inputs into robot controller commands. On the output side it sends commands to the robot that contain cor-rect position and orientation information based on the appropriate coordinate transformations.The robot is programmed in three modes: absolute, jogging and slave. In absolute mode, ‘waypoints’ are pro-grammed by pointing to and storing various positions in space with the in-dex finger. However, due to the limited accuracy of the positioning system (+/– 5 cm), the stored positions have to be adjusted to meet the required accu-racy (< 1mm) for arc-welding. Theseadjustments can be performed by either‘jogging’ or ‘slaving’. Jogging, as it isused in robotics, means controlling theend effector (a device or tool connect-ed to the end of the robot arm) directlyusing either a joystick or push buttons.In this case the joystick and pushbut-tons are replaced by gestures and voicecommands. For example, the ‘jog’ com-mand makes the robot move a certaindistance in the direction of the indexfinger. In slave mode, the robot mimicsthe motion of the hand using an ad-justable scaling factor. This means thatif the human hand moves a distance of1 cm, the robot responds by moving1 mm (depending on the scale settings)and so on until the desired accuracyhas been reachedThe system has been tested and evaluat-ed in a real arc-welding environmentusing ABB’s IRB140 and IRB1400 robots.The programming system has so farproved capable of producing the neces-sary accuracy, allowing high-qualitywelds to be produced. In addition, ob-servations from the evaluation indicatethat it is a very easy method to learnand master.The joint collaboration between engi-neers at CMU and ABB experts has, inaddition to generating valuable results,built up extensive know-how which willbe used within ABB for further researchin the field of robot programming.Dr. John DolanThe Robotics InstituteCarnegie Mellon University**********.eduMartin StrandAdvanced Industrial Communication GroupABB Corporate ResearchVästerås/Sweden********************.comR&D digestA simulation system that makes use of state-of-the-art web technology is used to train Novolen ®gas-phase polypropy-lene process plant operators on a rigor-ous dynamic plant model via Internet,Intranet, or as a stand-alone system.Simulation-based education is themethod preferred by many companies today for providing ‘on the job’ training.As computational capabilities become ever faster and improved tools appear on the market, computer-based educa-tional services, particularly in the chemi-cal process industries, are expanding.These services can mimic true plant operation through computer simulation,thus providing a safe and efficientmethod of training plant operators and other production personnel. In addition,operators may be trained to handle normal and abnormal plant operating conditions without endangering the actual plant [1].ABB Corporate Research has developed a simulation-based process-learning tool for polypropylene plants. Together with Novolen Technology Holdings C.V.(NTH), a joint venture of ABB LummusGlobal and Equistar, ABB has developed a learning tool aimed at the Novolen process owned by NTH. Called Novolen Operator Training Simulation (Novolen OTS), the tool’s strengths lie in its unique model, the robustness of the software and simulator, and its ease of maintenance and extendability. Because plants using the Novolen process are located around the world, using a web-enabled tool is particularly appropriate.Novolen OTS based training is possible over the Internet, Intranet, or on a stand-alone computer.The targeted users are Novolen process plant operators, operator trainers, and process engineers. A major training ob-jective is that the operators learn the dy-namic characteristics of the plant during standard operation and in abnormal sit-uations, including process disturbances,start-up/shutdown of the plant, and transitions between different product grades. Moreover, they obtain an under-standing of the relationship between operating conditions and resulting prod-uct quality. This permits operators to improve their ability to operate plants and to diagnose problems.The Novolen process plantIn the Novolen ®process, polymerization is conducted in one or two gas-phase reactors. Only two reactors connected in series are needed to produce a wide range of products, including super-high impact copolymers. In addition to the reactors, components in the plant in-clude condensers, degassing vessels,product silos, an extruder, controllers,and emergency valves .OTS component overviewThe main components of the Novolen ®OTS system include:1 A simulator, which includes a model of the process, the control system and the safety interlocksA generic operator station as a human system interfaceA software framework, which inte-grates these main components and provides for simulation services over the Internet.The graphical user interface (GUI) is a generic representation of an operator station . As the Novolen ® OTS is used in self-paced mode, no instructor station is required. A standard web browser,such as Internet Explorer, represents the GUI, displaying simulation results aswell as allowing user input.The components in the user interface,such as valves, numeric text boxes,buttons, level indicators, and flares,reflect the current status of the simula-tion. When necessary, the components are used to change the course of the simulation. For instance, valves areclosed/opened by clicking on them, and specific numbers are entered using the numeric text boxes. The condensers,degassing vessels, product silos, extrud-er, controllers, and emergency valves are all represented in the tool.Besides the above-mentioned basic functionality, additional functions are implemented for an enhanced learning experience. For example, the speed of the simulation can be increased in order to use the tool more efficiently,or a snapshot of the current state can be taken and reused in later training sessions.A normal training session starts by navi-gating to the web site of the server.After a login procedure in which access rights are checked, a simulation is start-ed with one of several pre-configured scenarios. The trainee may then change the course of the simulation by chang-ing process parameters, such as flow rates or temperature set-points. These2A new web-based simulation tool for polymer plant operatorsR&D digestchanges result in a dynamic response,which the trainee observes and reacts to accordingly. Stopping the simulation and closing the web browser terminate the session.The Novolen ®OTS can be fully installed and run on a standard off-the-shelf PC.Alternatively, it can be run over theInter/intranet so that only a web browser is needed on the user’s side.TechnologyThe dynamic model is a first-principle based model of the Novolen ®process with major unit operations [2]. It is com-posed of ordinary differential equations and has about 100 states. A wide range of operating conditions was required because the process tool was designed in answer to a major training objective:to focus on the dynamic characteristics of the plant during standard operation (eg, transition between different poly-mer grades) and abnormal situations (eg, a blocked pipe).The model is parameterized to easily permit adjustments that reflect different plant sizes and configurations. Special attention has been given to the integrity of the numerical solution to avoid simu-lation crashes during training.The tool uses a client-server architecture where the simulation services are server based. The GUI is presented on the client’s computer. The interaction be-tween the client and the server takes place via HTTP, the most common com-munication protocol on the Internet.The screens within the tool are built as HTML pages with Java applets repre-senting the data. The HTML-based ap-proach makes it possible to flexibly link to other information sources, and enables integration with other e-learning systems. The use of Java makes it possi-ble to program a variety of specialized components, allowing the user to influ-ence the data in various ways. Despite this, all major browsers with Java capa-bilities can be used for server access.On the server side, a web server frame-work (consisting of a multi-layer archi-tecture) provides the functionalityneeded for dynamic data to flow to and from the web pages. Innermost is an OPC server, which encapsulates the model and provides a standard inter-face to its data. The web server creates an HTTP-based service where data can stream from the OPC to Java servlets.These servlets are connected via HTTP to the Java applets ‘living’ on the client side. ABB developed the internal OPC connectivity by using the Java Native Interface to bridge the gap between Windows 32 applications and Java [3].Value extensionWith Novolen ®OTS, NTH has extended the value proposition of its current tech-nology offering with the creation of a highly robust and extendable tool using standard software and modeling tech-nologies. This tool will enable current and future licensees of the Novolen process to improve the understanding and operation of their plants. Licensees will be able to choose between web-based or stand-alone training sessions.Initial feedback from users has been so positive that many feel such a tool will eventually become essential for any company in the chemical process indus-tries.Reference[1]A. Kroll: Trainingssimulation für die Prozessindustrien: Status, Trends und Ausblick. Teil 1+2. Automatisierungstechnische Praxis atp (2003) 45, no. 2, pp 50–57, and no. 3, pp 55–60.[2]C.-U. Schmidt, R. Böttcher: 2000. ProveT – Training simulator for Novolen Process. 1st European Conf on the Reaction Engineering of Polyolefins, 2000,Lyons, 114–116.[3]R. Nyström, et al: 2003. Web-based training for polymer plant operators using process simulation. Automatisierungstechnik 51, no. 11.Dr. Rasmus NyströmDr. Andreas Kroll Dr. Alexander FrickChristian StichABB Corporate Research CenterLadenburg, GermanyKlaus HüttenDr. Franz Langhauser Dr. Wilhelm Seebass Dr. Meinolf Kersting ABB Lummus GlobalNovolen Technology Division。
ABB 测量与分析 录制与控制产品文档说明书

—ABB ME A SUREMENT & ANALY TIC SRecording and controlThe most complete picture of your process—Measurement made easyYour data, how, where and when you want it. ScreenMaster, ControlMaster and Commander are the names behind a comprehensive range of recording and control instrumentation from ABB that meet the demanding requirements of a broad range of applications in food and beverage, water and manufacturing.The range includes process controllers, digital indicators, chart recorders and paperless recorders. All sharing the same high standards of reliability and flexibility and capable of withstanding the harshest of process environments, they can be used in virtually any location.With a range of communications possibilities, including remote access, our controllers and recorders give you more power over your process than ever before.3—An option for every applicationcan cut the time and cost of deploying engineersto visit individual devices, ideal where skilledstaff are at a premium.We’ve also worked to use technology to take asmuch complexity as possible out of the operationof all our recording and control devices. With theirfull color, clear text displays and easy to useinterface, our ControlMaster process controllersand indicators make installing, commissioningand operating a control system quicker and easierthan ever.The same applies to our touchscreen RVG200paperless data recorder, where an extensive arrayof data recording and control possibilities can beachieved at the touch of a fingertip.With industry increasingly turning towards digitaltechnology, our range of recorders andcontrollers give you all the functionality you need,whether it’s greater control of your process or thestorage, retrieval and sharing of recorded data.By utilizing experience and expertise gainedthrough hundreds of applications across amultitude of industries, we have steadilyexpanded the capabilities of our devices to meetthe growing demands of today’s industrialapplications. Our SM500F and RVG200 paperlessdata recorders, for example, couple extensivesecurity with remote web server and mobiletechnology that offer system-size performancefrom a localized device. By enabling safe anytime,anyplace access to process data, these features4R ECO R D I N G A N D CO NTRO L—ABB ScreenMaster paperless recorders The digital era of data recording and analysisOur family of ScreenMaster paperless data recorders harness the power of digital technology to enable you to do more with your process data. Whether you want a field-mountable device that can be installed anywhere or slick and easy operation using the latest touchscreen technology, ABB’s ScreenMaster devices offer a versatile, secure and proven solution.Use anywhereWall, panel or pipe mounted options enable use in almost any location.Suitable for arduous environmentsNEMA 4X and IP66 protection enables installation in even the wettest or dirtiest conditions.Powerful yet simpleSimple menu interfaces make finding and viewing data easy, with multiple display formats offering a wide choice of viewing options.Flow recordingFlow totalizers enable instantaneous flow rates to be totalized and recorded. An automatic reset capability enables daily, weekly and monthly flow volume reports to be generated and alarms to be raised if predefined flow limits are exceeded.Powerful mathsMath and logic functions enable calculation of equations such as averages and deviations. Results can be displayed, recorded and used to drive alarms and totalizers.Extensive security featuresMeasures include a comprehensive audit log that records configuration changes, calibration changes, system events and other items key to data security. All entries are detailed with operator identification. Operators can securely annotate the chart with comments and signatures. Both recorders can form part of a system fully compliant to 21 CFR Part 11.Ethernet communicationsEthernet communications enable access toarchived data and email facilities. Using the latest telecoms tech the Ethernet features can be used even when a recorder is in a remote location.Remote process monitoringRemote access to a ScreenMaster is possible via the use of any standard web browser. Detailed real-time information is available for current alarm and totalizer conditions, memory card status and many other key process details. Email notificationKeep up to date with the latest process alarms or critical process events with email notifications which can be sent automatically to your PC or smartphone.Real-time data communicationScreenMaster recorders can communicate the process values being monitored to a DCS, SCADA, PLC or other similar system. Alternatively, data values can be communicated to a ScreenMaster for display to the operator and secure logging.Batch recordingA batch recording option enables batch numbers and product type information to be recorded alongside process data. With ABB’s DataManager Pro software, collected batch records can be accessed by searching for their batch number orbatches with common attributes identified.+ -x5SM500FField-mountable paperless recorder Featuring up to 7 process inputs, 12 recording channels and available with wall, panel and pipe mounting options, the SM500F field-mountable paperless recorder provides a truly simple recording solution that can be used anywhere, anyhow and by anyone.Its fully sealed IP66 and NEMA 4X enclosure make it ideal for even the most hostile environments, including hosedown and dusty applications.RVG200Touchscreen paperless recorderThe RVG200 recorder takes the established operating and securitybenefits of the ScreenMaster range onestep further. Up to 24 process signals can be connected to the RVG200’s analog inputs or transferred to it via digital communications. Features include: • Touchscreen ‘swipe’ operation• Front and rear USB ports for connecting peripheral devices, including a barcode scanner and keyboard • Customizable views• Steam energy calculations • Remote operation • GPS interfaceDataManagerProPowerful data analysis tool that helps you get more from your dataABB’s DataManager Pro advanced data review software opens new possibilities for collecting, interrogating andpresenting recorded data. The software creates a database of recorded data providing secure long-term storage andenabling instant access to data.6R ECO R D I N G A N D CO NTROL—ABB ControlMaster universal process controllers and indicators Control made easyWhether you’re a plant or process manager, electrical engineer, process operator or maintenance engineer, the future of process control instrumentation starts here.ABB has used its experience in controllers and indicators to create the ControlMaster family of process control instruments, offering an intuitive, simple and powerfulsolution for a wide range of process control applications.Scalable hardware and software functionalityI/O, functionality and control template availability is expanded easily with additional plug-and-play input modules and function keys, enabling a singleControlMaster unit to be adapted to handle anything, from basic to complex control applications.Full environmental protectionWith fully-sealed IP66 and NEMA 4Xenclosures or front panels, all ControlMasters offer full protection against water and dust ingress, enabling them to be used in even the most arduous operating conditions.Enjoy the flexibility of field-mountEnjoy the benefits of devices that you can locate practically anywhere, with the field-mounted CMF310 controller and CMF160 indicator. Able to be wall or pipe-mounted out of the box, they can be installed and commissioned in a fraction of the time and cost needed for adapting panel-mounted units.Panel-mount indicatorsThe CM15 is a feature-packed 1/8 DIN universal process indicator, with totalization, level, math, logic,counter and alarm functions.CMF160 field-mount indicatorCM15 panel-mount indicatorDiscover moreCMF310 field-mountcontrollerCM15panel-mountindicator CMF160field-mountindicatorPanel-mount controllers7ConfigPilot is the configuration platform for the entire range of ABB’s ControlMaster controllers and indicators. With an identical menu structure to the ControlMaster, ConfigPilot is instantly familiar. Configurations can be created from scratch off-line or read from a ControlMaster device. Once complete a configuration can be written to a ControlMaster via its front panel IrDA port or saved for future use. In addition ConfigPilot’s reporting capabilities hugely simplify creation of configuration documentation.Get up and running quickly with ConfigPilotPanel-mount controllersAvailable in 1/8, 1/4 and 1/2 DIN options, our ControlMasterpanel-mount controllers offer a simple, ready to use control solution.Suitable for basic to demanding applications, functionalityincludes cascade, feed forward, adaptive, predictive and ratio control strategies, plus Ethernet, RS485, Modbus TCP/RTU and a web server for remote process monitoring.CM10 1/8 DIN panel-mount controller CM50 3 x 6 DIN panel-mount controllerProfile controlProfile control enablessetpoint profiling for thermal processing applications. Two versions are available; a basic single program version and an advanced, multi-program version with sequencing. Profile-specific displaysprovide a clear overview of the profile progress, including program name and timeremaining, with more detailed information available at the press of a button.Advanced functions The ControlMaster range gives you even greater functionality. Features include math, totalization, a frequency input, logic, gain scheduling, split output, valve control and real time alarms.Template based configuration ControlMasterconfiguration is vastly simplified by using application templates. Selecting the template best suited to your process requirements configures I/O and control functionality automatically while display templates are also selected automatically.c8R ECO R D I N G A N D CO NTROL—ABB Commander circular chart recorders The tried and tested paper chart recorderRobust and easy to use, our Commander circular chart recorders have established a reputation for their reliable performance in a host of industrial applications including water and waste water treatment, food, pharmaceuticals and tyre production.A range of advanced functions, plus NEMA 4X and IP66 protection, makeCommander recorders the first choice wherever paper chart recording is required.Recording versatilityStatus at a glanceIntuitive operationsystem prevents unauthorized access to configuration menus.Math and logicUser configurable math functions, mass flow calculations and totalizers are all fully supported. The logic capability allowsinterlocking and the integration of discrete and continuous functions to solve a wide range of process problems.Discover more9MODBUS RS485 communications Communication with PCs or PLCs is achieved via the RS485 serial communications link, enabling the Commander 1900 to serve as the front end of plant-wide data acquisition systems. Using the MODBUS RTU protocol, all process inputs and other variables can be read continuously by a host PC running on a wide variety of standard SCADA packages.Install anywhereThe unit can be wall/pipe or panel mounted anywhere in the plant and, with its rating of NEMA 4X and IP66, it can be subjected to rigorousBuilt to meet your process’s needsA high level of I/O fitted as standardenables Commander recorders tomeet the requirements of mostprocesses out of the box. In addition,plug-and-play modules can be addedat any time to further extend arecorder’s I/O capability.Timers and clockTwo real-time eventstriggered by the recorder’sclock can be configured tooperate relays, start/stopthe chart or enable otheractions within the record.Options for everyapplicationC1900RC circular chartrecorder / controllerC1950 pasteurizerrecorder / controllerC1300 municipal recorder withflow totalizer displayC1960 Multi-recipeprofile recorder / controllerIntegrated PID loopsOffering dual integrated PIDloops, the C1900 chart recordercan be utilized as both a recorderand controller, eliminating thespace and cost associated withusing separate devices.10R ECO R D I N G A N D CO NTRO L—The ABB controller and recorder range Comprehensive solutions for food and beverage, water and manufacturing Water and wastewaterFood and BeverageKnowing what happens where, when and for how longare key considerations in making sure that food andbeverage products are produced to the right quality andunder the correct conditions. Our recording and controlequipment can be used in a wide variety of applicationsto ensure production processes perform properly and tohelp keep track of every product:AbstractionBatch recording PasteurizationSpirit distillation andbrewingCarbonation controland monitoringTemperature monitoring in fridges,freezers and cold roomsSteam usage monitoring Retort control and monitoringRVG200 recorder guides and videosScan this QR code to view anddownload application guides andvideos explaining how the RVG200can be used across differentindustrial applications.SM500F recorder guides and videosScan this QR code to view and downloadapplication guides and videos explaininghow the SM500F can be used acrossdifferent industrial applications.Cooking and bakingGuides and videos11Heat treatmentHeat treatment of metals for the aerospace,automotive and general engineering industriesmust be controlled rigorously to ensure thereliability of the parts being produced. Oursolutions include the ControlMaster range ofprocess controllers, plus the RVG200 paperlessrecorder with AMS2750 compliant inputs.Tyres and rubberOur multi-recipe profile controllers can help youachieve the precise pressure, temperature andtime control demanded during the curing of tyresand other rubber products.MarineMarine operators are subject to increasinglystrict emissions legislation governing theiremissions to air and sea. Our RVG200 paperlessdata recorders with GPS can be used to satisfyMARPOL regulations requiring the accuratecontrol and recording of bilge water dischargesfrom ships.PharmaceuticalsThe use of electronic devices in pharmaceuticalsproduction is strictly regulated to ensure thehighest levels of product quality and safety. OurSM500F and RVG200 paperless data recorders,together with our DataManager Pro data analysissoftware, can help you comply with theregulations, including the FDA’s 21CFR Part 11rules governing data security.Electrical power monitoringOur SM500F and RVG200 paperless datarecorders provide an ideal solution for localizedenergy consumption monitoring. Using collecteddata, you can find ways to reduce your energycosts and cut your carbon emissions.CMF310 controller guides and videosScan this QR code for application guidesand videos about the CMF310 field-mountcontroller and how it can be used acrossdifferent industrial applications.ControlMaster panel-mount controllersguides and videosScan this QR code to see how ourControlMaster panel-mount controllerscan help to solve a broad range ofapplication challenges.P B /R e c o r d e r s a n d C o n t r o l l e r s -E N R e v . B 06.2019—ABB LimitedMeasurement & Analytics Howard Road Eaton Socon St. NeotsCambridgeshire PE19 8EUTel: +44 (0)1480 475321ABB Inc.Measurement & Analytics 125 E. County Line Road Warminster PA 18974 USATel: +1 215 674 6000© Copyright 2019 ABB. All rights reserved.Specifications subject to change without notice.。
ABB测试台说明书
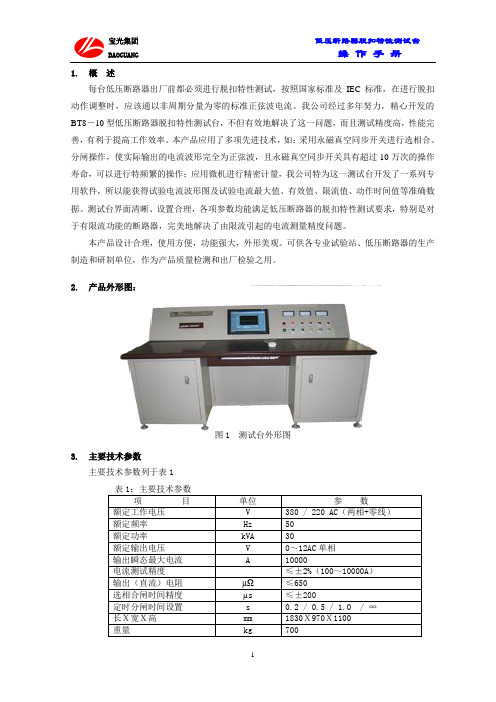
1.概述每台低压断路器出厂前都必须进行脱扣特性测试,按照国家标准及IEC标准,在进行脱扣动作调整时,应该通以非周期分量为零的标准正弦波电流。
我公司经过多年努力,精心开发的BT8―10型低压断路器脱扣特性测试台,不但有效地解决了这一问题,而且测试精度高,性能完善,有利于提高工作效率。
本产品应用了多项先进技术,如:采用永磁真空同步开关进行选相合、分闸操作,使实际输出的电流波形完全为正弦波,且永磁真空同步开关具有超过10万次的操作寿命,可以进行特频繁的操作;应用微机进行精密计量,我公司特为这一测试台开发了一系列专用软件,所以能获得试验电流波形图及试验电流最大值、有效值、限流值、动作时间值等准确数据。
测试台界面清晰、设置合理,各项参数均能满足低压断路器的脱扣特性测试要求,特别是对于有限流功能的断路器,完美地解决了由限流引起的电流测量精度问题。
本产品设计合理,使用方便,功能强大,外形美观。
可供各专业试验站、低压断路器的生产制造和研制单位,作为产品质量检测和出厂检验之用。
2.产品外形图:图1 测试台外形图3.主要技术参数主要技术参数列于表14.主要元件:4.1 多磁路变压器为得到稳定、可靠的大电流,我们选用国家定点专业厂家生产的多磁路变压器,以满足设备的各项测试要求。
4.1.1 多磁路变压器技术参数多磁路变压器的技术参数如表2所示表2:多磁路变压器的技术参数4.1.2 多磁路变压器工作原理为了得到稳定的正弦波输出电流,多磁路变压器TD(见图2)设四个单元磁路A、B、C、D, 总的二次输出电压为U2A, U2B, U2C, U2D之和。
U2 = U2A+ U2B+ U2C+ U2D图2 多磁路变压器工作原理图接在二次输出电流回路中有选相合闸开关ZK和被试断路器S,分流器FL。
将输出电压U2 调到所需值,再将试品断路器S合闸,当永磁真空同步开关ZK合闸后,试验回路出现电流.试验电流在分流器FL上产生的电压信号输入至微机并进行运算。
ABB-free@home 技术手册:运动检测器 MD-F-1.0.1说明书
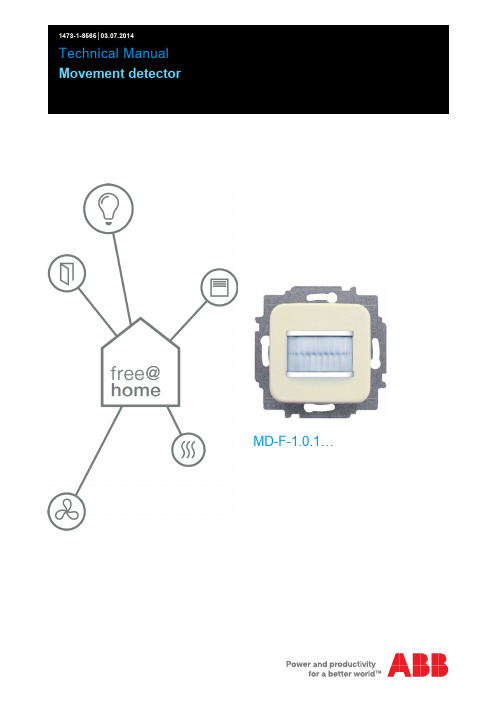
Technical Manual Movement detectorMD-F-1.0.1…ABB-free@home®Content1Notes on the instruction manual ________________________________________________________ 3 2Safety ____________________________________________________________________________ 42.1Used symbols ________________________________________________________________________ 42.2Intended use _________________________________________________________________________ 52.3Improper use _________________________________________________________________________ 52.4Target group / qualification of personnel ____________________________________________________ 52.5Safety instructions _____________________________________________________________________ 63Information on protection of the environment ______________________________________________ 7 4Product description __________________________________________________________________ 84.1Scope of supply _______________________________________________________________________ 84.2Type overview ________________________________________________________________________ 94.3Function overview _____________________________________________________________________ 94.4Device overview of movement detector _____________________________________________________ 95Technical data _____________________________________________________________________ 105.1Main overview _______________________________________________________________________ 105.2Dimensions _________________________________________________________________________ 105.3Circuit diagrams ______________________________________________________________________ 115.4Detection range ______________________________________________________________________ 116Mounting _________________________________________________________________________ 126.1Planning instructions __________________________________________________________________ 126.2Safety instructions for mounting _________________________________________________________ 126.3Mounting / Installation _________________________________________________________________ 137Commissioning ____________________________________________________________________ 147.1Allocation of devices and specifying channels ______________________________________________ 147.2Setting options per channel _____________________________________________________________ 187.3Linking _____________________________________________________________________________ 198Updating options ___________________________________________________________________ 21 9Operation _________________________________________________________________________ 22 10Maintenance ______________________________________________________________________ 2310.1Cleaning ___________________________________________________________________________ 23ABB-free@home®Notes on the instruction manual 1 Notes on the instruction manualPlease read this manual through carefully and adhere to the information containedtherein. This will assist you in preventing damage to persons and property and ensurereliable operation and long service life of the device.Please keep this manual in a safe place.If you pass the device on, also include this manual.Busch-Jaeger accepts no liability for failure to observe the instructions in this manual.If you require additional information or have questions about the device, please contactBusch-Jaeger or visit our Internet site at:/freeathome2 SafetyThe device has been constructed according to the latest valid regulations governingtechnology and is operationally reliable. It has been tested and left the factory in atechnically safe and reliable state.However, residual hazards remain. Read and adhere to the safety instructions to pre-vent such hazards.Busch-Jaeger accepts no liability for failure to observe the safety instructions.2.1 UsedsymbolsThe following symbols point to dangers involved in the use of the device and provide practical instructions.WarningThis symbol in connection with the signal word "Warning" indicatesa dangerous situation which could lead to immediate death or toserious injury.Attention - damage to propertyThis symbol indicates a possibly damaging situation for the product.Non-observance can lead to damage or destruction of the product.Note...This symbol indicates information or references to additional usefultopics. This is not a signal word for a dangerous situation.This symbol indicates information on the protection of the environ-ment.The following symbols are used in the manual to draw attention to special dangers: This symbol indicates a dangerous situation due to electric current.If such a sign is ignored, it can lead to serious injuries or evendeath.2.2 IntendeduseThis device is a movement detector for decentralized flush-mounted installation.The device is intended for the following:» operation according to the listed technical data,» installation in dry interior rooms and suitable flush-mounted boxes,» use with the connecting options available on the device.The intended use also includes adherence to all specifications in this mnaual.use2.3 ImproperEach use not listed in chapter 2.2 is deemed improper use and can lead to personal injury and damage to property.Busch-Jaeger is not liable for damages caused by use deemed contrary to the in-tended use of the device. The associated risk is borne exclusively by the us-er/operator.The device is not intended for the following:» unauthorized structural changes,» repairs,» use outdoors or in bathroom areas,» use with an additional bus coupler» as substitute for an alarm system.2.4 Target group / qualification of personnelInstallation, commissioning and maintenance of the device must only be carried out by trained and properly qualified electrical installers.The electrical installers must have read and understood the manual and follow theinstructions provided.The electrical installers must adhere to the valid national regulations in their country governing the installation, functional test, repair and maintenance of electrical prod-ucts.The electrical installers must be familiar with and correctly apply the "Five safetyregulations" (DIN VDE 0105, EN 50110):1. Disconnect from power;2. Secure against being re-connected;3. Ensure there is no voltage;4. Connect to earth and short-circuit;5. Cover or barricade adjacent live parts.instructions2.5 SafetyWarningElectric voltage! Risk of death and fire due to electrical voltage of230 V.Dangerous currents flow through the body when coming into director indirect contact with live components. This can result in electricshock, burns or even death.» Work on the 230 V supply system may only be performed byauthorised and qualified electricians.» Disconnect the mains power supply before installation /disassembly.» Never use the device with damaged connecting cables.» Do not open covers firmly bolted to the housing of the device.» Use the device only in a technically faultless state.» Do not make changes to or perform repairs on the device, on itscomponents or its accessories.» Keep the device away from water and wet surroundings.Attention - damage to propertyRisk of damaging the device due to external factors.Moisture and contamination can damage or destroy the device.» Protect the device against humidity, dirt and damage duringtransport, storage and operation.ABB-free@home®Information on protection of theenvironment 3 Information on protection of the environmentAll packaging materials and devices bear the markings and test seals for properdisposal.The products meet the legal requirements, in particular the laws governing elec-tronic and electrical devices and the REACH ordinance (EU Directive2002/96/EG WEEE and 2002/95/EG RoHS), (EU-REACH Directive and Law forthe Execution of the Directive (EG) No.1907/2006).The device contains valuable raw materials which can be recycled. Used electric and electronic devices must not be disposed of with domestic waste.» Always dispose of the packaging material and electric devicesand their components via the authorized collecting depots and disposal companies.4 Product descriptionFig. 1: Product overview[1] Flush-mounted insert (with integrated cover)[2] Cover frame (not included in scope of delivery)The movement detector sensor (with bus coupler) can be assigned to an availa-ble switch actuator. The devices respond to moving body heat and switch on thelights. They have not been pre-programmed. The devices do not serve as a sub-stitute for an alarm system.The sensor is integrated in a flush-mounted insert [1].The integrated bus coupler makes possible the connection to the free@home bus line.4.1Scope of supplyThe scope of supply only contains the flush-mounted insert [1], including the pre-mounted cover. It must still be completed with a suitable cover frame [2].Note ...Additional information about the cover frame ranges is available in the electronic catalogue ().4.2 TypeoverviewTable 1: Overview of types4.3 FunctionoverviewThe following table provides an overview of the possible functions and applica-tions of the device:Movement detectorSensor for movement- and brightness-dependent control of free@home functions Table 2: Function overview4.4 Device overview of movement detectorFig. 2: Device overview of movement detector[1] Type plate[2] Bus connection terminalABB-free@home®Technical data 5 Technicaldata5.1 MainoverviewParameters ValuePower Supply24 V DC (via bus line)Bus subscribers 1 (12mA)Connection Bus connection terminal: 0.4-0.8 mmLine type J-Y(St)Y, 2 x 2x 0.8 mmWire stripping 6-7 mmOpening angle 180 °Brightness limit value 1 – 500 luxMounting height 1.1 m to 1.3 mProtection IP20Ambient temperature -5 °C – +45 °CStorage T° -20 °C – +70 °CTable 3: Technical data5.2 DimensionsNote...All dimensions are specified in mm. All device types listed in thismanual have the same dimensions.Fig. 3: DimensionsABB-free@home ®Technical data5.3 Circuit diagramsFig. 4: Electrical connection5.4 Detection rangeFig. 5: Detection range[1] Mounting heights / Detection levels; [2] Detection range (0 °C – + 36 °C);[3] Horizontal reduction of the detection range by maskingca. 14˚ca. 5˚1,1 m -1,3 m6 Mountinginstructions6.1 PlanningNote...Planning and application instructions for the system are available in**********************************************/freeathome.6.2 Safety instructions for mountingWarning - Risk of death due to electrical voltageDangerous currents flow through the body when coming into di-rect or indirect contact with live components. This results in elec-tric shock, burns or even death.Work improperly carried out on electrical systems is a hazard toone's own life and that of the user. Also fires and serious damageto property can result.» Install the device only if you have the necessary electrical engi-neering knowledge and experience (see chapter 2.4).» Use suitable personal protective clothing.» Use suitable tools and measuring devices.» Check the supply network type (TN system, IT system,TT system) to secure the following power supply conditions(classic connection to ground, protective earthing, necessaryadditional measures, etc.).» Observe the correct polarity.6.3 MountingInstallation/» Turn the device into the correct installationposition.- The bus connection terminal [1] must be atthe bottom. Array» Connect the free@home bus line with thebus connection terminal [1].Observe the correct polarity!» Insert the device into the flush-mountedbox and screw it on.7 CommissioningCommissioning is always carried out via the Web-based surface of the SystemAccess Point.The System Access Point establishes the connection between the free@homeparticipants and the smartphone, tablet or PC. It is used to identify and programthe participants during commissioning.Devices which are physically connected to the free@home bus, log themselvesautomatically into the System Access Point. They transmit information about their type and supported functions (see Table 2, chapter 4.3).During initial commissioning all devices are given a generic name (e.g. move-ment detector1, etc.). The user must change this name to a name practical forthe system (Example: "Movement detector living room light" for a movementdetector that controls the living room light.The devices must be parameterised for the use of additional functions.Commissioning of the movement detectors is described in the following chapters.Here it is assumed that the basic commissioning steps of the overall system have already been carried out. General knowledge about the Web-based commission-ing software of the System Access Point is assumed.Note ...General information about commissioning and parameterization isavailable in the technical reference manual and the online Help of the"System Access Point".7.1 Allocation of devices and specifying channelsThe devices connected to the system must be identified, i.e. they are allocated toa room according to their function and are given a descriptive name.The allocation is made via the allocation function of the Web-based user interface of the System Access Point.7.1.1 AddingdeviceFig. 6: Adding device» In the "Add device" bar select the desired application and pull it via drag-and-drop onto the floor plan in the working area.Fig. 7: Allocation- A pop-up window opens automatically which lists all the devices suitable for the application selected.Identification via serial numberFig. 8 Identification via serial number» Compare the short 3-digit number of the identity label, which should be glued to the device plan, with the numbers in the list and in this way identify the de-vice you are searching for and, if necessary, also the channel.Assigning a nameFig. 9: Assigning a name» Enter a name that is easy to understand and under which the application is to be displayed later (e.g. "Movement detector living room"). » Press the tick at the bottom right to take over the entry.Note ...The settings of the device can be adjusted via the Web-based user interface of the System Access Point.These settings, however, can only be made in part with a fitter ac-cess (see online Help of the System Access Point). The parameter settings remain as described above.Movement detecRXUABB700000012ABB700000012RXU7.2 Setting options per channelGeneral settings and special parameter settings can be made for each channel.The settings are made via the allocation function of the Web-based user interface of the System Access Point.Device selectionFig. 10: Device selection» Select the device icon [1] in the floor plan of the working area view.-All setting options for the respective channel are displayed in the list view [2]. For rockers (sensors) the corresponding rocker must be selected.The following settings are available.7.2.1Settings for movement detectorSensor settings (movement detector settings)[1]Changing the name[2]Deleting the channel via 'X'[3]Switching of the actuator via the button [4]Switch-on behavior:Selection of the brightness conditions at which the device is to respond.1214327.3 LinkingThe movement detectors and actuators created via the allocation function can now be linked with each other.The linking in the list view is then made via the linking function of the Web-based user interface of the System Access Point.Connecting actuator and sensorFig. 11: Connecting actuator and sensor» To connect an actuator with a sensor, first click on the desired sensor [1] which is to operate the actuator and then on the actuator [2]. » Press the tick [3] at the bottom right to take over the entry.-A blue connecting line indicates the link between the two devices. The con-figuration is now transmitted automatically to the devices. The transmission can (depending on the number of affected devices) take a number of sec-onds. During the transmission a progress bar is displayed around the devic-es affected.123Connecting an actuator with an additional sensor12Fig. 12: Connecting actuator and sensor» To connect the actuator with an additional sensor, first click on the second desired sensor [1] which is to operate the actuator and then on the actuator[2].- An additional blue connecting line appears between the second sensor and the actuator.- After the transmission has been completed the sensor can be operated di-rectly locally.ABB-free@home®Updating optionsoptions8 UpdatingA Firmware update is carried out via the Web-based user interface of the SystemAccess Point.ABB-free@home®Operation Operation9The devices respond to moving body heat and switch on the connected actuators.Action by the user is therefore not necessary.ABB-free@home®Maintenance 10 MaintenanceThe unit is maintenance-free. In case of damage (e.g., during transport or stor-age), do not perform repairs. Once the device is opened, the warranty is void!Access to the device must be guaranteed for operation, testing, inspection,maintenance and repairs (according to DIN VDE 0100-520).10.1 CleaningDirty units can be cleaned with a dry cloth. If this is not sufficient, a cloth slightlymoistened with a soap solution can be used. Caustic cleaning agents or solventsmust not be used.ABB-free@home ®1473-1-8565 | 03.07.2014A member of the ABB GroupBusch-Jaeger Elektro GmbH PO Box58505 LüdenscheidFreisenbergstraße 2 58513 Lüdenscheid ***************.comCentral sales service: Tel.: +49 2351 956-1600 Fax: +49 2351 956-1700NoteWe reserve the right to at all times make technical changes as well as changes to the contents of this document without prior notice. The detailed specifications agreed upon apply for orders. ABB accepts no responsibility for possible errors or incompleteness in this document.We reserve all rights to this docu-ment and the topics and illustrations contained therein. The document and its contents, or extracts thereof, must not be reproduced, transmitted or reused by third parties without prior written consent by ABB.Copyright© 2014 Busch-Jaeger Elektro GmbH All rights reserved。
ABB 测量仪器与分析设备产品指南说明书

Performance ImprovementLifecycle ManagementRapid ResponsePredictive maintenance Condition monitoringPreventive maintenance Lifecycle assessment Spare Parts managementTechnical support Corrective maintenance Workshop RepairBase Agreement Terms & conditions Price agreements Contract management IB Lifecycle status Recommended spares—A B B M E A SU R EM ENT & A N A LY TI C S | PRO DUC T G U I DEABB Measurement Care support services Eight key factsCustomizable service modules from our Measurement Care program Measurement made easyIntroductionABB recently launched a highly flexible, modular and cost-effective range of services for measurement products and analyzers called Measurement Care. A highly customizable service agreement,Measurement Care consists primarily of threeservice modules – one to get your process back up quickly, one to manage instruments over their lifetimes, and lastly, one that aims at process improvements. These modules are called Rapid Response, Lifecycle Management and Performance Improvement. Under this umbrella of services, ABB will help identify and tailor the optimal support for a customer’s particular situation.Q & AWe sat down with Saverio Barbero Lodigiani, who heads up the Measurement Care program for ABB, to discuss the program’s benefits – see responses overleaf…—Measurement Care service agreementRepairsMaintenanceSpares partsMeasurementCare…Q & AWhat ABB products qualify for Measurement Care agreements?Included are products for measuring flow, pressure, temperature, level, thickness, flatness and tension, together with valve positioners and analyzers for liquids and gases.How does ABB handle support for Measurement Care?We’ve attempted to make it as easy and convenient for customers as possible. You have a single point of contact for contract management when needed – someone who knows you as well as your agreement terms, conditions and scope of supply.What are some service examples that fall within the Rapid Response module?Well, suppose lack of a field instrument or analyzer operation adversely affects your process to thepoint that you require quick action. ABB will agree to get a professional to your site within a mutually agreed time to get your process back to normal quickly. We’ll expedite the right part to facilitateswift repairs. In other situations, troubleshooting by a specialist via remote support or resident on-site ABB engineer can lead to even faster process recovery. In addition, we give priority to off-line repairs. This occurs when we request that youunplug the device from the process and ship it to an ABB repair facility. We will perform the repair and send the device back to you within an agreed time.What Measurement Care services are available on a regular basis?Our Lifecycle Module includes the inspection and condition monitoring of measurement products and analyzers at regular intervals. These services help to increase process uptime throughout aninstrument’s lifetime. We’ll recommend spare parts inventories for maintaining and / or replacing products when onsite or remote inspections indicate these actions are warranted.How about training?Flexible training options for your in-houseworkforce are also part of the Lifecycle Module. Our professional training services qualify yourengineers, maintenance and operations staff for running a safe and productive plant. Your personnel can receive training in our classrooms, at your plant, via webinar or online using our eLearning courses.Can ABB handle on-demand calibration of measurement products?Yes. In fact ABB pioneered onsite verification ofaccuracies in the field by our service engineers. This eliminates the need and expense of removing the unit from its installation and shipping to our laboratory. Otherwise ABB’s global calibrationlaboratories incorporate the latest technology and processes to calibrate all ABB measurementproducts as well as those from many other global manufacturers. Calibration results are traceable to international standards.How does Measurement Care services help to improve process performance?Our service experts have extensive application knowledge. They can evaluate plant conditions, identify opportunities for improvement and implement a cost-effective performanceenhancement program. They’ll also recommend an ongoing upgrade / replacement plan to secure peak performance of the installed base, keeping your plant competitive.Can ABB provide advanced services to protect measurement integrity and optimize process uptime when ABB service engineers are not on-site?Yes. We can remotely check the health andperformance of your measurement devices to an agreed timetable. Based on the results we’ll propose a plan to optimize reliability and / or recommend practices for predictive maintenance.For more informationFor more information on ABB Measurement Care services, please click the following link or copy / paste it into your browser:/products/measurement-products/service/service-agreements/measurement-careP G /S E A 100/2-E N R e v . A 01.2018—We reserve the right to make technical changes or modify the contents of this document without prior notice. With regard to purchase orders, the agreed particulars shall prevail. ABB does not accept any responsibility whatsoever for potential errors or possible lack of information in this document.We reserve all rights in this document and in the subject matter and illustrations contained therein. Any reproduction,disclosure to third parties or utilization of its contents – in whole or in parts – isforbidden without prior written consent of ABB. ©ABB 2018All rights reserved—To find your local ABB contact, visit:/contactsFor more information visit:/measurement3KXS110004R5301—Rapid response,lifecycle management and performanceimprovement services。
【VIP专享】ABB使用说明书最新版

前言衷心感谢您使用“华振”牌智能变频供水设备,我们将为您提供优质的产品和星级的售后服务。
我公司吸取行业内智能变频供水设备的技术精髓,集长期从事水泵行业和智能变频供水设备的设计经验,研制开发的ZBH第三代、第四代、第五代、第六代智能变频供水设备,已广泛运于高层建筑、住宅楼、商住楼、新老小区降耗节能改造、高级宾馆、医院、学校、工矿企业的生产生活用水等,是一种节能型,现代化,智能化的变频供水设备。
本使用说明书向您详细介绍了“华振”牌系列智能变频供水设备的产品说明、技术说明、操作、故障处理,保养维护等各方面内容。
为了更好的使用智能变频供水设备,请您在操作前仔细阅读本说明书,这将会:●帮助您了解智能变频供水设备的结构及性能特点。
●避免由于操作不当而引起的设备故障。
●提高设备的使用寿命。
●增强设备使用的可靠性。
值得注意的是,本说明书的资料及图形在出版时是正确的,但我公司产品的结构和性能总在不断地改进和完善,本说明书的相关内容可能有变化,恕不一一通知,敬请谅解。
感谢您对“华振”的信任,衷心地祝愿您在事业中大展宏图,取得辉煌成就。
成都华振供水设备有限公司- 1 -))1 MΩ电阻与机壳连接用于模拟输入电位器的给定电压输出.10 V±2%))1 MΩ电阻与机壳连接频率。
0…20 mA ( 数字输入6,可编程。
默认Ω。
数字输入最大电压一般显示性能软键功能每个软键上方的文字描述的是当前软键功能的含义。
显示对比度同时按住 MENU (菜单)键和 UP (向上)或DOWN (向下)可以改变显示对比- 5 -顶行液晶屏的顶行显示变频器的基本的状态信息。
• LOC (本地) - 表示变频器处于本地控制,即控制命令来自控制盘。
• REM (远程) - 表示变频器处于远程控制, 例如 I/O (X1) 或现场总线。
• - 显示变频器和电机的旋转状态:4、应用宏的选择 中崛供水设备应用宏选择,用于泵的循环软起控制中,在ABB 变频器设置中9902的值为15(SPFC 控制).注意! 参数2108 START INHIBIT (禁止起动)必须保持为默认设置0 (OFF)。
ABB RobotStudio 5.14.01 SP1 手册说明书

What’s New? RobotStudio5.14.01 SP1Revision: -The information in this manual is subject to change without notice and should not be construed as a commitment by ABB. ABB assumes no responsibility for any errors that may appear in this manual.Except as may be expressly stated anywhere in this manual, nothing herein shall be construed as any kind of guarantee or warranty by ABB for losses, damages to persons or property, fitness for a specific purpose or the like.In no event shall ABB be liable for incidental or consequential damages arising from use of this manual and products described herein.This manual and parts thereof must not be reproduced or copied without ABB's written permission, and contents thereof must not be imparted to a third party nor be used for any unauthorized purpose. Contravention will be prosecuted.Additional copies of this document may be obtained from ABB at its then current charge.© Copyright 2011 ABB All rights reserved.ABB ABRobotics ProductsSE-721 68 VästeråsSweden1 What’s New in 5.14.01 SP1?OverviewThis section provides information about the new features and problems corrected in thisrelease.1.1 Solved IssuesTwo different memory problems are resolved in this Service Pack:The first issue, adressing the problem that the size of the station is increased with everysave. This was primary a problem for stations with lots of graphical components(geometry) that would result in an increase of the station file size for each save.The second issue concerned libraries that was connected and then disconnected. Thiscould in some cases cause a memory exception.2 What’s New in 5.14.01?OverviewThis section provides information about the new features and problems corrected in this release.2.1 Online MonitorThe parameters for defining update rate, warning and error levels for joint limits and singularities has been added to the RobotStudio Options pages.2.2 AutoPathThe AutoPath feature can be used to create a path based on the edges of the surfaces of a part. The function only allows a path to be created along adjacent faces. The parameter that defines the maximum distance between two faces to be considered adjacent has been added to the RobotStudio Options page.2.3 Collada import and exportRobotStudio can now import files in the format Collada version 1.4.1 (.dae) using the function Import Geometry . Objects can be exported in the Collada format using the function Export Geometry . The static geometry of an entire station can be exported in the collada format by selecting the station node of the Layout browser and selecting Export Geometry.2.4 Measurement markupThe x,y,z values of a measurement are displayed in a markup together with the totaldistance.2.5 Access Level ALL no longer needed of input signalsSignals of a VC no longer need to be defined to have Access Level = ALL in the I/OConfiguration database to change its values from RobotStudio. It is sufficient to havethem defined with Access Level = DEFAULT.2.6 Preview image of Pack & Go filesA preview image of the station contained in a Pack&Go file will be displayed in thepreview pane of Windows Explorer in Windows 7.2.7 New robot models – IRB5300-12The IRB5300-12 (the so-called door opener) is available in RobotStudio 5.14.013 What’s New in 5.14?OverviewThis section provides information about the new features in RobotStudio 5.14.3.1 Microsoft Office 2010 Fluent User InterfaceFluent UIThe RobotStudio 5.14 user interface is redesigned and now uses the Microsoft OfficeFluent user interface (UI). Introduced in the RobotStudio 5.11, the Fluent UI isdesigned to make it easier for people to find and use the full range of features thatRobotStudio provide, and to preserve an uncluttered workspace.The RibbonThe ribbon, part of the Fluent UI, was designed to optimize key RobotStudio scenariosto make them easier to use. The ribbon provides quicker access to all the commands inRobotStudio and allows for easier future additions and customizations. You can makeyour favorite commands available in the quick access toolbar, embedded in the title bar.To help maximize the space of the graphical viewer, the ribbon can be hidden.Backstage ViewThe Microsoft Office Backstage is part of the Fluent UI and a companion feature to theribbon. The Backstage view, which can be accessed from the File menu, helps you findfrequently used features for managing RobotStudio files. (The File tab replaces theRobotStudio Button and File menu that were used in earlier releases of RobotStudio.)3.2 Activation and LicensingVersion independent activation key: RobotStudio 5.xStarting with RobotStudio 5.14, the activation key that activates RobotStudio 5.14 willalso activate all future versions (both major and minor) of RobotStudio 5. This isindicated by the version of the installed license key in RobotStudio. The versiondisplayed in the license information dialog is now 5.x.3.3 GeneralDocument Manager ReferencesReferences to files and folders can be added to a station through the DocumentManager. Referenced folders can optionally be included in the Pack and Go file. Thereis also an option to completely embed a file in the station.New Robot ModelsSimulation models for the following new robots have been added to RobotStudio ∙IRB2600ID (15kg/1.85m)∙IRB2600ID (8kg/2.0m)∙IRB460∙IRB760Station name in title barThe name of the currently opened station has been added to the title bar.Improvements of CAD based path generation (AutoPath)The function ’Path from Curve’ for automatic creation of path based on a curve, hasbeen improved. It is not longer required to have a curve prepared as it can work on theedges of a piece of geometry. Of course, if a curve is available, it can be used for thepath generation as before. The user interface has been simplified and advanced optionsfor angle tuning, approach and depart targets removed. Also, a preview of the path isavailable to indicate what the result will be before the command is executed.Tuning of targets can be done through the new Reference Frame available in the SetPosition and Rotate tools. Approach and depart targets can be created using the regularcopy/paste functions in combination with the tuning feature. The function has beenrenamed to AutoPath to reflect the re-design.Online MonitorThe Online Monitor can be described as a virtual web camera that monitors theconnected robot and visualizes its movements. The graphical view that shows the robotmodel is updated with the true robot position every second. If the robot is in a singularposition or at a joint limit you will get an indication in the view. Only TCP robots willbe shown as external axes are not supported.Adjust RobtargetsThe Premium feature Adjust Robtargets allows programs that has been programmedwith the wrong TCP (tooldata) or work object (wobjdata) to be corrected. The jointangles of the robot will remain the same.Accelerated simulationAn option to run the simulation as fast as possible has been added to the SimulationAccuracy section of the RobotStudio options. With this option selected, RobotStudiowill fire the next time step as soon as the calculation for the previous one is completed.The predicted execution times for the Virtual Controllers will not be affected.Station Viewer Improvements: Acceleration and Seek BarThe simulation replay of the Station Viewer can now accelerated up to 200% of thenormal execution speed. It is also possible to reduce the time or even play thesimulation backwards. In addition, a seek bar has been added that shows simulationprogress and allows the simulation to be started at a particular point.Simulation Step / Pause / ResumeA simulation can now be stepped forward one tick at the time. First, start the simulation as usual by pressing the Play button. Then, you can pause the simulation by pressing the Pause button. When paused, the Play button will be renamed to Resume , and the Pause button will be renamed into Step . Now, the simulation can be stepped forward one time step (tick) at the time by pressing the Step button.Before starting the simulation the Play button is enabled. When the simulation is running, the Pause button is enabled. When paused, the Play , and Pause buttons are renamed, Resume and Step, respectively, see below.→ → ScreenRecorder support for Microsoft Windows Media formatSupport for Windows Media version 8 and 9 has been added to the Screen Recorder . In addition, movies can be recorded using the H.264 / MPEG-4 encoder that creates high-quality recordings with a high compression ratio. The AVI format is still availableand allows the selection of any available codec on the computer.NOTE!The Microsoft Windows Media and H.264 encoders are only available for Windows 7,not for Windows XP.Transparent texturesTo simply modeling and increase realism, support for transparent textures has beenadded to RobotStudio. The textures are applied using the Graphical Appearance tool.The feature supports textures in .PNG format.Target Reference FrameThe reference frame of a target has now been exposed in RobotStudio. Until now, it hasonly been available in ArcWelding PowerPac. The target reference frame allows atarget to be offset relative to the original position. This is useful if the targets have beencreated using a CAD-model and it is required to offset the target position to compensatefor the robot tool. The Reference Frame is available in the Set Position and RotatetoolsImproved performance for Configurations and AutoConfigThe different ways a robot arm can use to reach a certain target is controlled by theconfdata in RAPID and can be set using the Configurations tool in RobotStudio.The performance of the calculation of the available arm configurations are now donedirectly by the virtual controller, which gives a dramatic increase in performance. Theimproved performance can be seen when using RobotWare 5.14.Collision Detection performance improved.The Collision Detection computation has been improved to make use of multiple CPUcores, if available, and uses the SSE (Streaming SIMD Extensions) instruction set forbest performance.Nine decimals in generated RAPID codeThe number of decimals used for specifying the position and orientation data ofgenerated robtargets, tooldata, and wobjdata are now limited to nine. Thiswill increase readability of the generated RAPID code. Accuracy is not affected sincethe data is declared in RAPID as num (single precision) that uses the eight firstdecimals.MarkupsA markup is a text box displayed in the 3D graphics. It can be used to highlight areas ofinterest. Markups become part of the Station Viewer.AutoConfig optionsNew options related to AutoConfig∙Verify. Verifies existing configuration∙Reset. Marks current configuration as unverified to enable for optimization using AutoConfigSignal AnalyzerSignals to be analyzed are defined in the Signal Setup tool for viewing and analysis inthe Signal Analyzer.The tool allows robot performance tuning and signal debugging.The table below lists the signals that can be analyzed and their dependency onRobotWare..Signal name RW availabilityController Signals / <system name> / EventLog<domain> Any RW versionController Signals / <system name> / Mechanical Units / I/O System<all signals> Any RW versionController Signals / <system name> / Mechanical Units / ROB_x / JointJ1-J6 Any RW versionNear Limit Any RW versionController Signals / <system name> / Mechanical Units / ROB_x / TargetFine Point Any RW versionTarget Reached Any RW versionController Signals / <system name> / Mechanical Units / ROB_x / TCPMaximum Linear Acceleration in World1RW version ≥ 5.14Orientation Q1-Q4 Current Workobject RW version ≥ 5.14Orientation Speed in Current Workobject RW version ≥ 5.14Pos X, Y, Z in Current Workobject RW version ≥ 5.14Robot Configuration cf1, cf4, cf6, cfx RW version ≥ 5.14Speed in Current Workobject RW version ≥ 5.14Total Motor Power RW version ≥ 5.14Smart Components<all signals> <no RW needed>The Signals are visualized in the graph below.Using the Signal History tool, signal recordings can be exported to Excel, renamed, ordeleted.NOTE!The maximum number of signals that can be exported is limited to 26.1 The signal ’Maximum Linear Acceleration in World’ provides the maximum acceleration of the current move instruction.RAPID ProfilerThe new RAPID Profiler is a tool for measuring and analyzing procedure executiontimes of the robot program. It is a Premium feature that can be used to identify thecritical procedures that offer great potential for cycle time reduction. Special attention ispaid to Wait-instructions and MultiMove synchronization semaphores. Reducingwaiting times is the obvious way to reduce the program execution time.NOTE!∙The Spy function does not produce useful output for systems based on theRobotWare option CAP (Continuous Application Platform). This is the case for e.g.systems with ArcWelding. This affects the RAPID Profiler that analyses the loggenerated by the Spy function.∙For accurate results, the last move instruction of all procedures should be a fine point. Otherwise the estimated time for that procedure will be underestimated. External axis interpolationDefines optimal external axis value with respect to robot TCP3.4 Smart Component ImprovementsSmart Component: LogicExpressionA gate whose output is determined by a logic expression. Supports logic operatorsAND, OR, NOT and XOR. Advanced gates can be easily created using theLogicExpression gate. The overall complexity of a smart component is reduced sincethe gate logic can be handled by one base component.Example: output = input5 XOR (input1 AND input2) OR (NOT input3)Smart Component Viewer FilterThe objects of the SmartComponent viewer can now be filtered to reduce thecomplexity.∙signals∙properties∙only connected componentsProperty Detectable added to graphical objectsAllows graphical objects to be made invisible to SmartComponent sensors3.5 ScreenMaker ImprovementsLanguage SupportScreenMaker supports the same set of languages that RobotStudio supports. Thelanguages are applicable for the User Interface which includes the ribbon and dialogsand not for the controls and its properties .ScreenMaker TemplatesScreenMaker now includes the three templates Basic, Advanced and Extended, whichrepresent typical uses of ScreenaMaker.Launch Virtual Flexpendant after deployingThe new option to automatically launch the Virtual FlexPendant after the currentScreenMaker application have been deployed is available in the ScreenMakerproperties.Access of shared dataShared RAPID data can now be accessed using ScreenMakerConditional Trigger ControlA new control for configuring the execution of events based on condition. Thefollowing table describes the conditions and datatypes supportedCondition RAPID Signals Application VariablesAND bool NA boolOR bool NA boolXOR bool NA boolNOTEQUAL Any Type Any Type Any TypeEQUAL Any Type Any Type Any TypeGREATER num, dnum num, dnum num, dnum (0/1)LESSER num, dnum num, dnum num, dnum(0/1)ScreenMaker Doctor detects missing RAPID and Signal dataThe ScreenMaker Doctor now detects missing RAPID and Signal data that has beenbound in the ScreenMaker project but does not exist in the connected controller. TheScreenMaker project must be connected to the controller to detect RAPID and Signaldata. The ScreenMaker Doctor does not detect actions that are defined as part of events.For example: If an action has been defined to Read Rapid Data into ApplicationVariable.Increment / Decrement controlA new control for incrementing and decrementing a NUM/DNUM.。
- 1、下载文档前请自行甄别文档内容的完整性,平台不提供额外的编辑、内容补充、找答案等附加服务。
- 2、"仅部分预览"的文档,不可在线预览部分如存在完整性等问题,可反馈申请退款(可完整预览的文档不适用该条件!)。
- 3、如文档侵犯您的权益,请联系客服反馈,我们会尽快为您处理(人工客服工作时间:9:00-18:30)。
1.概述
每台低压断路器出厂前都必须进行脱扣特性测试, 按照国家标准及IEC标准, 在进行脱扣动作调整时, 应该通以非周期分量为零的标准正弦波电流。
我公司经过多年努力, 精心开发的BT8―10型低压断路器脱扣特性测试台, 不但有效地解决了这一问题, 而且测试精度高, 性能完善, 有利于提高工作效率。
本产品应用了多项先进技术, 如: 采用永磁真空同步开关进行选相合、分闸操作, 使实际输出的电流波形完全为正弦波, 且永磁真空同步开关具有超过10万次的操作寿命, 能够进行特频繁的操作; 应用微机进行精密计量, 我公司特为这一测试台开发了一系列专用软件, 因此能获得试验电流波形图及试验电流最大值、有效值、限流值、动作时间值等准确数据。
测试台界面清晰、设置合理, 各项参数均能满足低压断路器的脱扣特性测试要求, 特别是对于有限流功能的断路器, 完美地解决了由限流引起的电流测量精度问题。
本产品设计合理, 使用方便, 功能强大, 外形美观。
可供各专业试验站、低压断路器的生产制造和研制单位, 作为产品质量检测和出厂检验之用。
2.产品外形图:
图1 测试台外形图
3.主要技术参数
主要技术参数列于表1
表1: 主要技术参数
4.主要元件:
4.1 多磁路变压器
为得到稳定、可靠的大电流, 我们选用国家定点专业厂家生产的多磁路变压器, 以满足设备的各项测试要求。
4.1.1 多磁路变压器技术参数
多磁路变压器的技术参数如表2所示
表2: 多磁路变压器的技术参数
4.1.2 多磁路变压器工作原理
为了得到稳定的正弦波输出电流,多磁路变压器TD( 见图2)设四个单元磁路A、B、 C、 D, 总的二次输出电压为U2A, U2B, U2C, U2D之和。
U2 = U2A+ U2B+ U2C+ U2D
图2 多磁路变压器工作原理图
接在二次输出电流回路中有选相合闸开关ZK和被试断路器S, 分流器FL。
将输出电压U2 调到所需值, 再将试品断路器S合闸, 当永磁真空同步开关ZK合闸后, 试验回路出现电流.试验电流在分流器FL上产生的电压信号输入至微机并进行运算。
由于瞬动特性试验电流值( I) 很大, 永磁真空同步开关ZK合闸后, 被试断路器S立即分闸。
但作为设备的后备保护, 要求ZK合闸后, 经一定设定时间, ZK自动分闸, 详见第7条第3款。
必要时用手动分闸。
4.2 FLP1-10型低感分流器
为了测量试验回路的电流大小.需要在二次回路中串联低感分流器FL, 从FL上检测到精确的电压信号, 输入至微机进行采样计算。
低感分流器主要技术参数:
短时工作电流: 10 kA
信号电阻: 304.5 µΩ
输出信号电压: 3 V
4.3 调压器:
为得到连续可调、稳定的电压, 由两台TEDGC-5kVA 02~50V单相调压器同轴组装串联而成, 要求:
输入电压 380V AC单相
输出电压 0至430V AC单相
输出电流 23A
4.4 永磁真空同步开关:
采用BTM ─ D10型永磁真空同步开关( 以下简称同步开关) , 该开关应用最新先进技术, 采用单稳态永磁机构, 传动简单可靠, 永磁机构控制单元采用全电子化智能化控制。
由主开关电源、控制电源、电容器组、推挽驱动MOSFET开关器件、分合闸位置检测器、光电隔离器件、开关电压检测器等组成。
控制单元根据断口电压信号的采样, 经过逻辑计算后发出分、合闸指令。
经过高性能的电子元器件的选用、严格的工艺和调试控制、合理的测量电路及运算电路设计来减小控制信号的离散性, 使得选相合闸时间精度≤±200 µs , 其主要技术如下:
4.4.1 同步开关电参数
a)额定工作电压: 380 V AC;
b)额定电流: 1250 A;
c)额定短时耐受电流: 25 kA( 1s) ;
d)额定短路关合电流: 63kA( 峰值) 。
4.4.2、同步开关机械参数: 图3 永磁真空同步开关外形图
a)开距: 4±0.1 mm;
b)超行程: 2±0.5 mm
c)合闸速度 0.2±0.1 m/s;
d)分闸速度 0.3±0.1 m/s
e)合闸弹跳: 0 ms
4.4.3、同步开关外形见图3
5.系统原理图
5.1系统一次原理图见图4
图4 一次原理图
5.2系统二次原理图见图5
图5 二次原理图
6. 开机及参数设置
6.1 开机
测试台操作台面分下图所示三个区: 测试区屏幕显示区控制面板。