热洗、洗井规定
洗井四要素
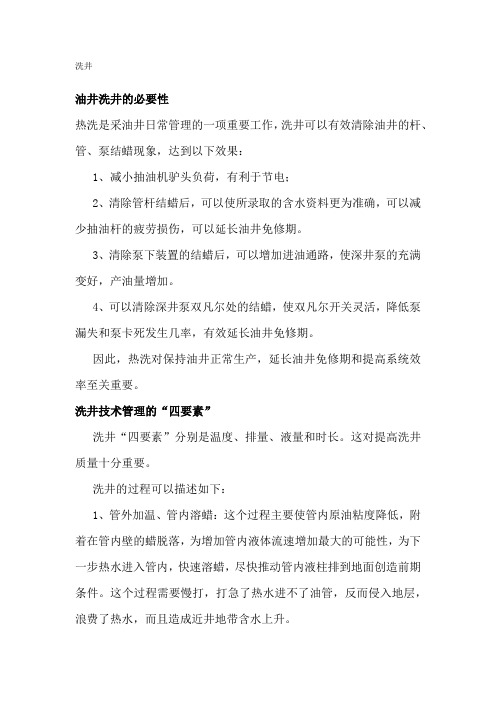
洗井油井洗井的必要性热洗是采油井日常管理的一项重要工作,洗井可以有效清除油井的杆、管、泵结蜡现象,达到以下效果:1、减小抽油机驴头负荷,有利于节电;2、清除管杆结蜡后,可以使所录取的含水资料更为准确,可以减少抽油杆的疲劳损伤,可以延长油井免修期。
3、清除泵下装置的结蜡后,可以增加进油通路,使深井泵的充满变好,产油量增加。
4、可以清除深井泵双凡尔处的结蜡,使双凡尔开关灵活,降低泵漏失和泵卡死发生几率,有效延长油井免修期。
因此,热洗对保持油井正常生产,延长油井免修期和提高系统效率至关重要。
洗井技术管理的“四要素”洗井“四要素”分别是温度、排量、液量和时长。
这对提高洗井质量十分重要。
洗井的过程可以描述如下:1、管外加温、管内溶蜡:这个过程主要使管内原油粘度降低,附着在管内壁的蜡脱落,为增加管内液体流速增加最大的可能性,为下一步热水进入管内,快速溶蜡,尽快推动管内液柱排到地面创造前期条件。
这个过程需要慢打,打急了热水进不了油管,反而侵入地层,浪费了热水,而且造成近井地带含水上升。
2、泵下溶蜡、畅开通路:热水进入油管,一则靠泵的抽吸,二则靠压力挤入泵内,无论哪种作用,都是从泵下装置进入油管,所以,此过程同上一过程是同步进行的,也需要慢打,使泵下装置的蜡溶化好,使热水最多进入油管,使管内蜡溶解好,把热水利用好。
特别是沉没度大,泵充满差的井更需要如此,必要时,这样井需要洗碰同时进行,目的就是畅开热水进泵的通路。
3、热水进管、冲向地面:此时排量应提高一档,使热水在一定速度下排向地面,如果井口发热,则说明热水已到地面,不负责任的洗井多认为此时洗井结束,这是极大错误,此时正时溶蜡的大好时机,需要保持排量继续洗,使蜡很好溶化。
4、增加排量、排出余蜡:通过以上过程,油管内可能存在一定的小蜡块、小蜡球未完全溶化,此时,再增加一下排量,把这些小蜡球、小蜡块排到地面,以收全功。
5、最小排量、清净花管:洗井时可能会使套管内壁的垢、其它脏物等脱落,或使井底脏物泛起,附着在花管上,此时慢慢打,随着水的慢流,这些杂质会离开花管脱落到井下。
对抽油机井热洗质量评价标准的认识
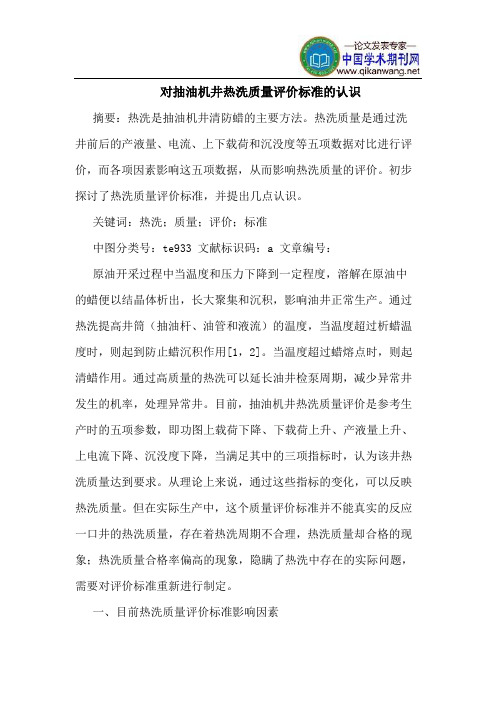
对抽油机井热洗质量评价标准的认识摘要:热洗是抽油机井清防蜡的主要方法。
热洗质量是通过洗井前后的产液量、电流、上下载荷和沉没度等五项数据对比进行评价,而各项因素影响这五项数据,从而影响热洗质量的评价。
初步探讨了热洗质量评价标准,并提出几点认识。
关键词:热洗;质量;评价;标准中图分类号:te933 文献标识码:a 文章编号:原油开采过程中当温度和压力下降到一定程度,溶解在原油中的蜡便以结晶体析出,长大聚集和沉积,影响油井正常生产。
通过热洗提高井筒(抽油杆、油管和液流)的温度,当温度超过析蜡温度时,则起到防止蜡沉积作用[1,2]。
当温度超过蜡熔点时,则起清蜡作用。
通过高质量的热洗可以延长油井检泵周期,减少异常井发生的机率,处理异常井。
目前,抽油机井热洗质量评价是参考生产时的五项参数,即功图上载荷下降、下载荷上升、产液量上升、上电流下降、沉没度下降,当满足其中的三项指标时,认为该井热洗质量达到要求。
从理论上来说,通过这些指标的变化,可以反映热洗质量。
但在实际生产中,这个质量评价标准并不能真实的反应一口井的热洗质量,存在着热洗周期不合理,热洗质量却合格的现象;热洗质量合格率偏高的现象,隐瞒了热洗中存在的实际问题,需要对评价标准重新进行制定。
一、目前热洗质量评价标准影响因素1.1热洗质量五项参数分析(1)产液量。
正常量油时,每次量油产量会有一定的波动,现场取三次量油平均值。
此波动在地质要求允许范围内就认为是稳定的。
在评价单井热洗质量时,会存在着量油产量波动使热洗后产量偏低,不能正确反应热洗效果,同时,为了提高热洗合格率,也必然存在人为提高洗后量油产量现象,只要产量在量油波动上限即可。
同时,产液量还受到地层供液、泵况变化、间歇出油、油套压等的影响。
(2)电流。
电流受到取值时间、盘根松紧等因素影响,即使同一口井在不同时间段,电流也会有较大的变化。
(3)沉没度。
试验证明,单井的沉没度在一定时间范围内的变化是很大的,这与地层出液有关,地层的出液并不是绝对均匀的,经常存在间歇出油现象。
热洗、洗井规定
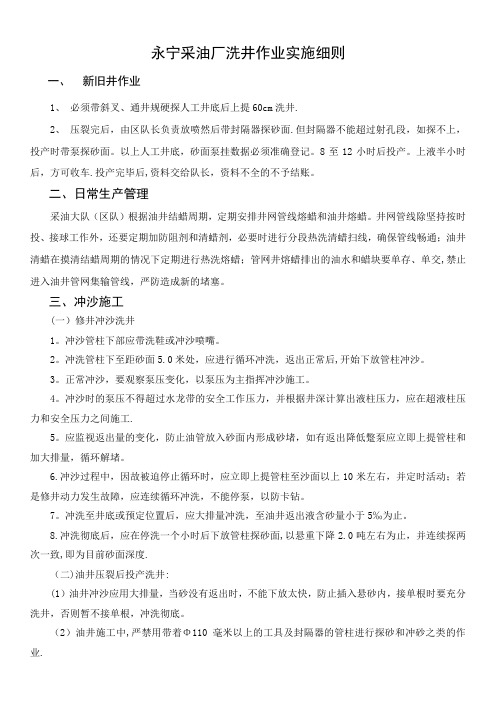
永宁采油厂洗井作业实施细则一、新旧井作业1、必须带斜叉、通井规硬探人工井底后上提60cm洗井.2、压裂完后,由区队长负责放喷然后带封隔器探砂面.但封隔器不能超过射孔段,如探不上,投产时带泵探砂面。
以上人工井底,砂面泵挂数据必须准确登记。
8至12小时后投产。
上液半小时后,方可收车.投产完毕后,资料交给队长,资料不全的不予结账。
二、日常生产管理采油大队(区队)根据油井结蜡周期,定期安排井网管线熔蜡和油井熔蜡。
井网管线除坚持按时投、接球工作外,还要定期加防阻剂和清蜡剂,必要时进行分段热洗清蜡扫线,确保管线畅通;油井清蜡在摸清结蜡周期的情况下定期进行热洗熔蜡;管网井熔蜡排出的油水和蜡块要单存、单交,禁止进入油井管网集输管线,严防造成新的堵塞。
三、冲沙施工(一)修井冲沙洗井1。
冲沙管柱下部应带洗鞋或冲沙喷嘴。
2。
冲洗管柱下至距砂面5.0米处,应进行循环冲洗,返出正常后,开始下放管柱冲沙。
3。
正常冲沙,要观察泵压变化,以泵压为主指挥冲沙施工。
4。
冲沙时的泵压不得超过水龙带的安全工作压力,并根据井深计算出液柱压力,应在超液柱压力和安全压力之间施工.5。
应监视返出量的变化,防止油管放入砂面内形成砂堵,如有返出降低蹩泵应立即上提管柱和加大排量,循环解堵。
6.冲沙过程中,因故被迫停止循环时,应立即上提管柱至沙面以上10米左右,并定时活动;若是修井动力发生故障,应连续循环冲洗,不能停泵,以防卡钻。
7。
冲洗至井底或预定位置后,应大排量冲洗,至油井返出液含砂量小于5‰为止。
8.冲洗彻底后,应在停洗一个小时后下放管柱探砂面,以悬重下降2.0吨左右为止,并连续探两次一致,即为目前砂面深度.(二)油井压裂后投产洗井:(1)油井冲沙应用大排量,当砂没有返出时,不能下放太快,防止插入悬砂内,接单根时要充分洗井,否则暂不接单根,冲洗彻底。
(2)油井施工中,严禁用带着Φ110毫米以上的工具及封隔器的管柱进行探砂和冲砂之类的作业.(3)压裂、喷砂、冲砂过程中,压力突然升高时,应立即改反洗或马上提管柱。
热洗清蜡车洗井工艺及使用管理

从表 1数据可以看出, 热洗 作业 在油 田的生 产开 发 中起着越来越重要的作用。因此 , 研究 和不断优化热 洗 工艺 , 对保 障油 田产能有着十分重要 的意义 。
表 1 2 0 -2 1 年 油 井 热 洗井 次 05 0 2
年份 20 20 20 08 20 21 21 02 1 0 5 0 6 0 7 2 0 0 9 0 0 0 12 1 ( ̄5月)合计
江 汉 石 油 职 工 大 学 学 报
21 年 O 02 9月
Jun l f i g a e oem es y f tf a dWok r o ra o a h nP t l Umvri af n res Jn r u to S
第 2卷 5
第5 期
热洗 清 蜡 车洗 井 工艺及 使 用 管 理
油井热洗是采油现场管理 的一项经常性的重要 的管 括: 超导清蜡车 、 热洗清蜡车 、 锅炉车 、 煤炉车等 。其 中, 热洗清蜡车具有排量 大( 2 / 、 > 0 m3h)压力高 8MP a 1 a、 2MP 升温快 的特 点 , 广泛应用于地层 能量 高、 供液 充足、 油层埋藏深度不大 ( 0 ) <20 0m 的油井 。热洗后 降回压效果 明显 , 别是对凝 固点高 、 特 易结 蜡井 和稠油 井效果 更明显 。 江汉油 田江汉采 油厂采 油机械大 队特采 队主要 承 担矿区内的生产油井 正常洗井、 解堵 、 管杆 清蜡、 疏通解
冻地面管线等施工作业 , 装备有热洗清蜡车三台。 11 洗井清蜡车结构及主要技术参数 .
理措施 , 包括油井热油洗、 热水洗 、 输油管系扫线等 , 主要
是清洗油井或输油管系管壁上的结蜡 , 防止管系因结蜡严
重而堵塞 。随着油 田的深入开发, 热洗井次逐年增加 , 自 20 年 以来 , 05 历年热洗井次统计数据如表 1所示 。
油井热洗操作规程
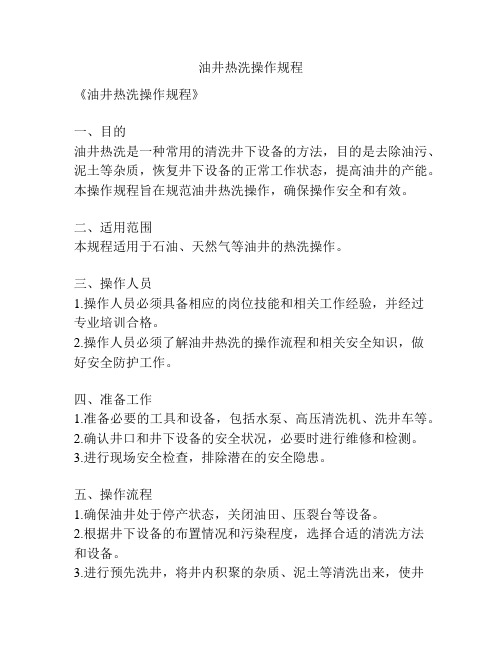
油井热洗操作规程《油井热洗操作规程》一、目的油井热洗是一种常用的清洗井下设备的方法,目的是去除油污、泥土等杂质,恢复井下设备的正常工作状态,提高油井的产能。
本操作规程旨在规范油井热洗操作,确保操作安全和有效。
二、适用范围本规程适用于石油、天然气等油井的热洗操作。
三、操作人员1.操作人员必须具备相应的岗位技能和相关工作经验,并经过专业培训合格。
2.操作人员必须了解油井热洗的操作流程和相关安全知识,做好安全防护工作。
四、准备工作1.准备必要的工具和设备,包括水泵、高压清洗机、洗井车等。
2.确认井口和井下设备的安全状况,必要时进行维修和检测。
3.进行现场安全检查,排除潜在的安全隐患。
五、操作流程1.确保油井处于停产状态,关闭油田、压裂台等设备。
2.根据井下设备的布置情况和污染程度,选择合适的清洗方法和设备。
3.进行预先洗井,将井内积聚的杂质、泥土等清洗出来,使井底清洁无杂质。
4.接通高压水源和高压清洗机,对井下设备进行高压冲洗,确保每个部位都被认真清洗。
5.根据清洗效果进行检查,如发现污垢未清洗干净,需进行再次清洗直到彻底清洁。
六、安全注意事项1.操作人员必须戴好安全防护用具,避免被高压水柱击中。
2.严禁在高压清洗机工作时站在喷水的方向上,以免发生意外。
3.清洗过程中如发现异常情况,应立即停止操作并报告相关负责人。
七、记录和评估1.在操作过程中,应对每一次操作进行记录,包括清洗前的设备状态、清洗方法和设备、清洗后的效果等。
2.对每次清洗的效果进行评估,以便及时发现问题并对操作流程进行调整和改进。
八、结束工作1.清洗工作结束后,对油井设备进行检查和维护,确保设备状态良好。
2.清洗设备进行清洗,保持设备清洁,以备下次使用。
上述规程为油井热洗操作的一般性规程,具体操作应按照实际情况制定相应的操作方案,并在专业人员的指导和监督下进行操作。
石油工程技术 井下作业 常规洗井作业

常规洗井作业洗井是在地面向井筒内打入具有一定性能的洗井液,把井壁和油管上的结蜡、死油、铁锈、杂质等脏污混合到洗井液中带到地面的施工。
洗井是井下作业施工的一项常规项目,在抽油机、稠油井、注水井及结蜡严重的井施工时,一般都要洗井。
1洗井液的要求1.1洗井液的性能要根据井筒污染情况和地层物性来确定,要求洗井液与油水层有良好的配伍性。
1.2在油层含有黏土矿物的井中,要在洗井液中加入防膨剂。
1.3在低压漏失井洗井时,要在洗井液中加入增黏剂和暂堵剂或采取混气措施。
1.4在稠油井洗井时,要在洗井液中加入表面活性剂或高效洗油剂,或用热油洗井。
1.5在结蜡严重或蜡卡的抽油机井洗井时,要提高洗井液的温度至70℃以上。
1.6洗井液的相对密度、黏度、PH值和添加剂性能应符合施工设计要求。
1.7注水井洗井液水质要求:1.7.1总含铁量小于0.5mg/L。
1.7.2含油量小于30mg/L。
1.7.3PH值为6.5-8.5。
1.7.4固体悬浮物含量:用清水时,2-3mg/L;用油田污水时,2-5mg/L。
1.8洗井液量为井筒容积的2倍以上。
1.9当地层压力大于静水柱压力时,可采用水基洗井液。
1.10当地层压力小于静水柱压力时,可采用油基洗井液或选择暂堵、蜡球封堵、大排量联泵洗井、气化液洗井等方式。
2洗井方式的选择2.1正洗井。
洗井液从油管打入,从油套环空返出。
正洗井一般用在油管结蜡严重的井。
2.2反洗井。
洗井液从油套环空打入,从油管返出。
反洗井一般用在抽油机井、注水井、套管结蜡严重的井。
正洗井和反洗井各有利弊,正洗井对井底造成的回压较小,但洗井液在油套环空中上返的速度稍慢,对套管壁上脏物的冲洗力度相对小些;反洗井对井底造成的回压较大,洗井液在油管中上返的速度较快,对套管壁上脏污的冲洗力度相对大些。
为保护油层,当管柱结构允许时,应采取正洗井。
3洗井程序及要求3.1按施工设计的管柱结构要求,将洗井管柱下至预定深度。
3.2连接地面管线,地面管线试压至设计施工泵压的1.5倍,经5min后不刺不漏为合格。
Q-SY HB 0022-2001油井热洗工艺规程
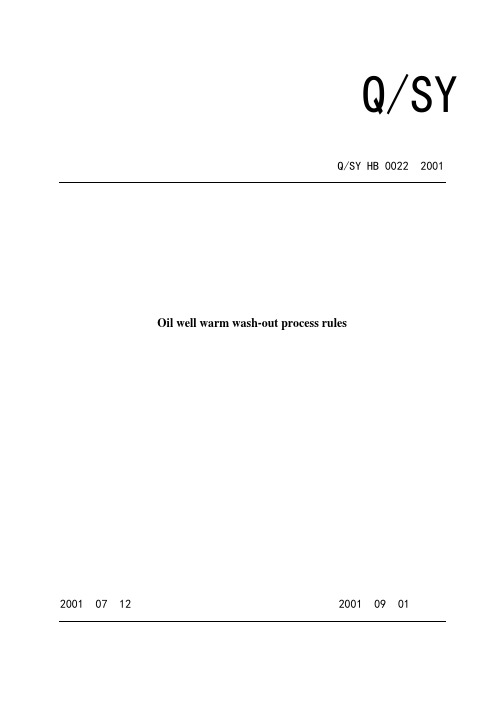
1
Q/SY HB 0022—2001
分 油 井 技 术 状 况 热 洗技 术 要 求
类 产液量(t/d)
含水(%) 泵效(%) 泵径(mm) 动液面(mm)
泵出口温度(℃) 油井返出温度 (℃)
表 3-1
四步热洗 ≤30 ≤30 ≤30 44 >700
>75 ≥60
三步热洗 31-70 31-70 31-70 56.57 500-700
2
Q/SY HB 0022—2001
3.5.5 每 30min 观察测量一次电流值。 3.5.6 油井洗通后,当返出液体温度达到 60-65℃时,倒换流程恢复正常生产。 3.5.7 每 30min 观察一次洗井泵压、油套压及热洗温度,并做好记录,及时判断有无油套窜 通迹象。 3.5.8 有计量设施可测热洗排量的,每 30min 记录一次;无计量设施的,可按计算排量,但 要严格控制好排量。 3.5.9 每 30min 测电流一次并做好记录。 3.6 抽油机井自身热循环洗井。 3.6.1 连好热洗车和抽油机井自身热循环洗井流程,并仔细检查,确保不漏不渗,安全可 靠。 3.6.2 倒通洗井流程,点燃加热炉加热油井产出液体。 3.6.3 电机电流恢复到洗通时的正常工作电流后,再维持 30 min 左右,加热炉灭火。 3.6.4 倒换流程,使生产的原油进到该井的集油管线,再关闭洗井流程上的所有闸门,使油 井恢复正常生产。 3.6.5 录取资料要求同 3.5.4 和 3.5.5。 3.7 工作要求及注意事项 3.7.1 检查油井套压:对于套压高于设计洗井压力的油井,洗井前应先放调套管气,降低套 压到热洗泵压以下。 3.7.2 循环开始时,控制好洗井油(水)温度(高于蜡熔点 10℃左右为宜),再逐渐提高 热油(水)温度。 3.7.3 洗井要彻底,油井洗通后洗井油(水)返出温度不低于 60℃。 3.7.4 热洗过程中,严防高温高压热油(水)伤人。 3.7.5 热洗时要及时准确地取全取准热洗资料。 3.7.6 油井热洗后,不准停抽。 3.7.7 严格执行“三不洗井”,即设备(电器、机泵、热洗车辆、流程)有故障未排除不洗 井,热油(水)温度低于 70℃不洗井,热洗泵压力低于设计压力 0.5mpa 不洗井。 3.8 热洗效果评价:
油井热洗
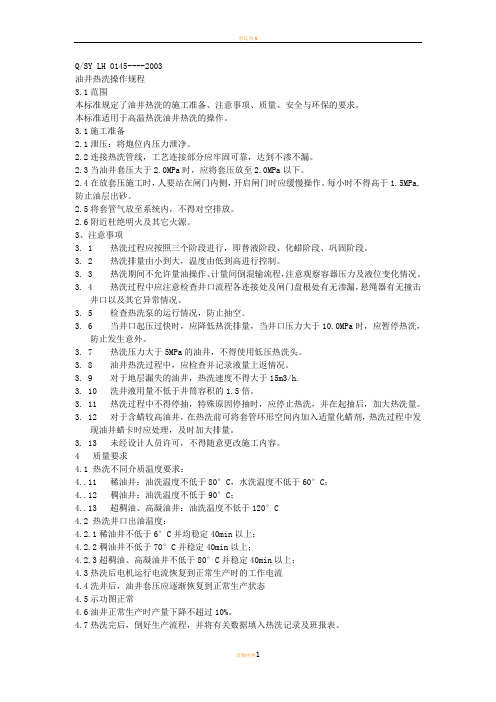
Q/SY LH 0145----2003油井热洗操作规程3.1范围本标准规定了油井热洗的施工准备、注意事项、质量、安全与环保的要求。
本标准适用于高温热洗油井热洗的操作。
3.1施工准备2.1泄压:将炮位内压力泄净。
2.2连接热洗管线,工艺连接部分应牢固可靠,达到不渗不漏。
2.3当油井套压大于2.0MPa时,应将套压放至2.0MPa以下。
2.4在放套压施工时,人要站在闸门内侧,开启闸门时应缓慢操作。
每小时不得高于1.5MPa,防止油层出砂。
2.5将套管气放至系统内,不得对空排放。
2.6附近杜绝明火及其它火源。
3、注意事项3. 1热洗过程应按照三个阶段进行,即替液阶段、化蜡阶段、巩固阶段。
3. 2热洗排量由小到大,温度由低到高进行控制。
3. 3热洗期间不允许量油操作、计量间倒混输流程,注意观察容器压力及液位变化情况。
3. 4热洗过程中应注意检查井口流程各连接处及闸门盘根处有无渗漏,悬绳器有无撞击井口以及其它异常情况。
3. 5检查热洗泵的运行情况,防止抽空。
3. 6当井口起压过快时,应降低热洗排量,当井口压力大于10.0MPa时,应暂停热洗,防止发生意外。
3. 7热洗压力大于5MPa的油井,不得使用低压热洗头。
3. 8油井热洗过程中,应检查并记录液量上返情况。
3. 9对于地层漏失的油井,热洗速度不得大于15m3/h.3. 10洗井液用量不低于井筒容积的1.5倍。
3. 11热洗过程中不得停抽,特殊原因停抽时,应停止热洗,并在起抽后,加大热洗量。
3. 12对于含蜡较高油井,在热洗前可将套管环形空间内加入适量化蜡剂,热洗过程中发现油井蜡卡时应处理,及时加大排量。
3. 13未经设计人员许可,不得随意更改施工内容。
4质量要求4.1热洗不同介质温度要求:4..11稀油井:油洗温度不低于80°C,水洗温度不低于60°C;4..12稠油井:油洗温度不低于90°C;4..13超稠油、高凝油井:油洗温度不低于120°C4.2热洗井口出油温度:4.2.1稀油井不低于6°C并均稳定40min以上;4.2.2稠油井不低于70°C并稳定40min以上;4.2.3超稠油、高凝油井不低于80°C并稳定40min以上;4.3热洗后电机运行电流恢复到正常生产时的工作电流4.4洗井后,油井套压应逐渐恢复到正常生产状态4.5示功图正常4.6油井正常生产时产量下降不超过10%。
- 1、下载文档前请自行甄别文档内容的完整性,平台不提供额外的编辑、内容补充、找答案等附加服务。
- 2、"仅部分预览"的文档,不可在线预览部分如存在完整性等问题,可反馈申请退款(可完整预览的文档不适用该条件!)。
- 3、如文档侵犯您的权益,请联系客服反馈,我们会尽快为您处理(人工客服工作时间:9:00-18:30)。
永宁采油厂洗井作业实施细则
一、新旧井作业
1、必须带斜叉、通井规硬探人工井底后上提60cm洗井。
2、压裂完后,由区队长负责放喷然后带封隔器探砂面。
但封隔器不能超过射孔段,如探不上,投产时带泵探砂面。
以上人工井底,砂面泵挂数据必须准确登记。
8至12小时后投产。
上液半小时后,方可收车。
投产完毕后,资料交给队长,资料不全的不予结账。
二、日常生产管理
采油大队(区队)根据油井结蜡周期,定期安排井网管线熔蜡和油井熔蜡。
井网管线除坚持按时投、接球工作外,还要定期加防阻剂和清蜡剂,必要时进行分段热洗清蜡扫线,确保管线畅通;油井清蜡在摸清结蜡周期的情况下定期进行热洗熔蜡;管网井熔蜡排出的油水和蜡块要单存、单交,禁止进入油井管网集输管线,严防造成新的堵塞。
三、冲沙施工
(一)修井冲沙洗井
1.冲沙管柱下部应带洗鞋或冲沙喷嘴。
2.冲洗管柱下至距砂面5.0米处,应进行循环冲洗,返出正常后,开始下放管柱冲沙。
3.正常冲沙,要观察泵压变化,以泵压为主指挥冲沙施工。
4.冲沙时的泵压不得超过水龙带的安全工作压力,并根据井深计算出液柱压力,应在超液柱压力和安全压力之间施工。
5.应监视返出量的变化,防止油管放入砂面内形成砂堵,如有返出降低蹩泵应立即上提管柱和加大排量,循环解堵。
6.冲沙过程中,因故被迫停止循环时,应立即上提管柱至沙面以上10米左右,并定时活动;若是修井动力发生故障,应连续循环冲洗,不能停泵,以防卡钻。
7.冲洗至井底或预定位置后,应大排量冲洗,至油井返出液含砂量小于5‰为止。
8.冲洗彻底后,应在停洗一个小时后下放管柱探砂面,以悬重下降2.0吨左右为止,并连续探两次一致,即为目前砂面深度。
(二)油井压裂后投产洗井:
(1)油井冲沙应用大排量,当砂没有返出时,不能下放太快,防止插入悬砂内,接单根时要充分洗井,否则暂不接单根,冲洗彻底。
(2)油井施工中,严禁用带着Φ110毫米以上的工具及封隔器的管柱进行探砂和冲砂之类的作业。
(3)压裂、喷砂、冲砂过程中,压力突然升高时,应立即改反洗或马上提管柱。
四、热油洗蜡作业管理
(一)油井热洗周期的确定,主要根据油井生产能力的大小、原油的物性、含蜡情况及蜡的性质,并结合热洗液的性质及摸索的洗井周期确定:
1、油井日产油量在8.0吨以上和新井投产井,洗井周期在80-100天。
2、油井日产油量在5.0-8.0吨之间的油井,洗井周期在110-130天。
3、油井日产油量在5.0吨以下的油井,洗井周期在150天左右。
4、有一些特殊低产井和中、高含水井,洗井周期为半年一次。
(二)抽油井热洗前的准备工作:
1、生产调度室按洗井安排,当日在下达第二天的洗井任务的同时,向有关服务、配合单位下服务、配合任务。
2、热洗班按洗井井号的要求,准备好洗井车,保证按时洗井。
3、热洗配合车辆要保证热洗过程中连续供液。
4、热洗用液、用药保证按要求保质保量供给。
5、热洗井必须做好以下工作:
(1)储油罐:必须保证有两个半空的油罐,以便备进返出液。
(2)洗井前24小时不准放压、放喷,保证洗井时油井正常生产。
(3)采油工必须在油井现场,准备好常用工具,用具作好配合。
(三)抽油井热洗工艺技术:
1、坚持七个“不能洗”:洗井设备保证不了连续施工不能洗;供液设备保证不了连续供液不能洗;热洗液质量(热洗液量、温度、添加剂)保证不了设计要求不能洗;抽油设备保证不了洗后24小时以上连续排抽不能洗;储油罐容量保证不了容纳返排液不能洗;井口严重漏失不能洗;安全条件不具备不能洗井。
2、把好热洗过程四个关:热洗液温度关;热洗过程中不同阶段的排量关;热洗中真实的返出温度关;热洗用液量关。
3、抽油井热洗液量
根据目前油井生产现状,热洗班车辆设备的实际情况以及地层亏空的现状,为降低热洗成本,减少不必要的浪费,特作以下规定。
(1)一般常规热洗井的热洗液量均为24M3,特殊井特殊处理。
(2)符合以下条件之一的抽油井热洗液量为18—20M3。
<1>泵挂深度不超过1000m的;
<2>动液面在700m之内的;
<3>投产未超过一年的;
<4>油井日产液量10M3以上的;
<5>套压达到4.5MPa以上的;
<6>注水对应见效井;
<7>开采侏罗系的。
<8>部分长2层
(3)符合以下条件之一的抽油井热洗液量为30M3以上。
<1>泵深超过1500m的;
<2>结蜡严重的;
<3>热洗周期超过半年以上的。
4、抽油井热洗前停产规定
为了保证热洗效果,恢复地层压力,减少地层漏失,低产油井热洗前应采取必要的停产。
(1)抽油井日产液量在2M3以下,热洗前停产48小时。
(2)抽油井日产液量在2-3M3,热洗前停产24小时。
(四)抽油井热洗工艺施工:
1、按技术要求和准备工作规定达到要求后,应开始洗井施工。
2、连接洗井管线,进行试压、试泵。
3、做好油井返排液工作,取出油嘴,检查进罐管线牢固性。
4、按安全管理规定检查到位。
5、检查流程、记录有关资料后,开始洗井,开抽生产。
炉子、泵、供液罐专人负责。
6、油井洗好后方能停洗,搞好井场卫生,并向采油工讲清洗井参数、洗后生产中注意事项后,方能离开井场。
(五)热洗施工安全管理:
1、备好防火设施。
2、洗井时井口和罐区25米以内严禁明火。
3、罐区禁止放油。
4、洗井是带压作业,管线要试压大于洗井压力。
5、洗井前全面检查洗井全部流程是否畅通。
6、当油井套压高时,须先启泵使泵压大于套压1.0MPA时,立即开套压阀门冼井,
7、当洗井液返出时,要有专人控制排液。
若喷势大,气量大,应立即停车,待排液稳定后再开洗。
8、洗井中炉子、排气管不准排出火苗,洗井车排气管周围不得有油物。
9、洗井时罐区和地面管线严禁靠近和跨越。
(六)抽油井热洗后生产技术管理:
1、洗井后保证油井24小时以上连续生产排液。
2、排液用生产闸门控制,尽快排出井内洗井液。
3、油井产液量计算,把洗井情况及变化认真填写报表。
高气油比油井管理
1、定压放套管气; 基层员工依据套压高放,出砂不放;沉没度低放,能量足不放;确定最佳点放,无效不放。
摸索合理控制放气速度,确定出每口井的最佳套管压力点。
2、加深泵挂至油层顶部;
3、加井底气锚等配套措施可减轻气体影响;
Welcome !!! 欢迎您的下载,资料仅供参考!。