防爆壳体检验规范
防爆检查内容细则及完好标准
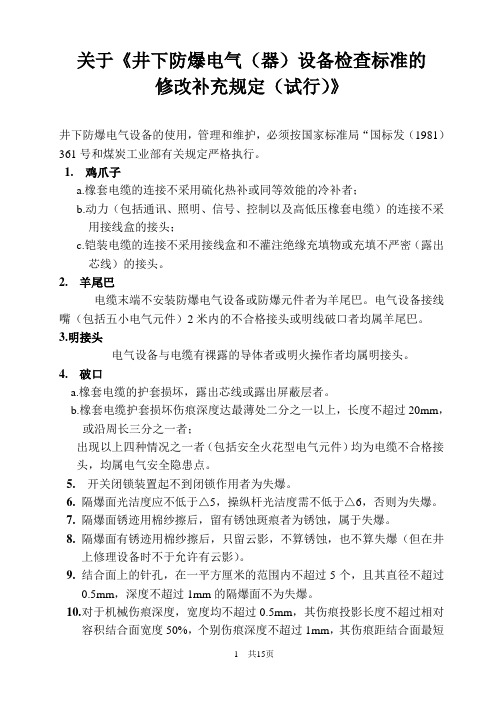
关于《井下防爆电气(器)设备检查标准的修改补充规定(试行)》井下防爆电气设备的使用,管理和维护,必须按国家标准局“国标发(1981)361号和煤炭工业部有关规定严格执行。
1.鸡爪子a.橡套电缆的连接不采用硫化热补或同等效能的冷补者;b.动力(包括通讯、照明、信号、控制以及高低压橡套电缆)的连接不采用接线盒的接头;c.铠装电缆的连接不采用接线盒和不灌注绝缘充填物或充填不严密(露出芯线)的接头。
2. 羊尾巴电缆末端不安装防爆电气设备或防爆元件者为羊尾巴。
电气设备接线嘴(包括五小电气元件)2米内的不合格接头或明线破口者均属羊尾巴。
3.明接头电气设备与电缆有祼露的导体者或明火操作者均属明接头。
4. 破口a.橡套电缆的护套损坏,露出芯线或露出屏蔽层者。
b.橡套电缆护套损坏伤痕深度达最薄处二分之一以上,长度不超过20mm,或沿周长三分之一者;出现以上四种情况之一者(包括安全火花型电气元件)均为电缆不合格接头,均属电气安全隐患点。
5.开关闭锁装置起不到闭锁作用者为失爆。
6.隔爆面光洁度应不低于△5,操纵杆光洁度需不低于△6,否则为失爆。
7.隔爆面锈迹用棉纱擦后,留有锈蚀斑痕者为锈蚀,属于失爆。
8.隔爆面有锈迹用棉纱擦后,只留云影,不算锈蚀,也不算失爆(但在井上修理设备时不于允许有云影)。
9.结合面上的针孔,在一平方厘米的范围内不超过5个,且其直径不超过0.5mm,深度不超过1mm的隔爆面不为失爆。
10.对于机械伤痕深度,宽度均不超过0.5mm,其伤痕投影长度不超过相对容积结合面宽度50%,个别伤痕深度不超过1mm,其伤痕距结合面最短无伤距离相加不大于相应容积规定的结合面宽度不算失爆,但其中有一项超过均为失爆。
11.隔爆面上不允许有油漆和机械性杂物,否则为失爆(如无意造成的油漆痕迹不超过隔爆面宽度的1/8不在此限)。
12.隔爆面应涂以适量的中性凡士林等合格的防锈油(如医用凡士林油)或磷化(磷化后也可涂凡士林油),如无防锈油或磷化面脱落均为失爆。
防爆检查标准

防爆检查标准在工业生产和化工领域,防爆安全一直是一个重要的问题。
为了确保生产过程中的安全,防爆检查标准成为了必不可少的一部分。
本文将就防爆检查标准进行详细介绍,以便于大家更好地了解和应用。
首先,防爆检查标准的制定是基于相关法律法规和标准要求的。
在我国,防爆安全的相关法律法规主要包括《危险化学品安全管理条例》、《煤矿安全规程》等,这些法规对于防爆设备的选择、使用、维护等方面都有详细的规定,企业在进行防爆检查时必须要严格遵守相关法律法规的要求。
其次,防爆检查标准的内容主要包括防爆设备的选择和使用、防爆设备的维护和检修、防爆作业的管理等方面。
在选择和使用防爆设备时,必须要根据生产场所的具体情况和作业要求进行合理的选择,并且要确保设备的正常运行和有效使用。
在维护和检修防爆设备时,要按照相关规定进行定期的检查和维护,并且要及时处理设备的故障和隐患,以确保设备的安全可靠。
在防爆作业的管理方面,要建立健全的防爆管理制度,明确责任人和管理程序,加强对作业人员的安全教育和培训,确保作业的安全进行。
此外,防爆检查标准还要求企业要建立健全的防爆安全管理体系,包括安全生产责任制、安全生产标准化管理、安全生产培训等方面。
企业要加强对防爆安全管理的重视,做好安全生产工作,确保生产过程中的安全稳定。
总之,防爆检查标准是保障工业生产和化工领域安全生产的重要保障。
企业要严格遵守相关法律法规和标准要求,加强对防爆设备的选择、使用、维护和管理,建立健全的防爆安全管理体系,确保生产过程中的安全稳定。
只有这样,才能有效地预防和控制事故的发生,保障人员的生命财产安全。
希望本文对大家有所帮助,谢谢阅读。
防爆壳体检验要求示范

防爆壳体检验要求示范
一、前言
防爆壳是一种用于防止爆炸发生的装置,因此其质量和性能的检验非常重要。
本文将介绍防爆壳体检验的要求示范,以确保其质量和安全性。
二、外观检验
1.检查防爆壳的表面是否平整,无明显划痕或破损。
2.检查防爆壳的连接部位是否牢固,在正常使用情况下不会松动或脱落。
三、功能性检验
1.测试防爆壳的阻燃性能,使用明火或者高温热源靠近防爆壳,观察其是否能够有效阻止火焰蔓延。
2.测试防爆壳的防爆功能,使用适当的爆炸物模拟装置,在安全条件下进行爆炸,观察防爆壳是否能够有效地抵抗爆炸冲击。
四、安全性检验
1.检查防爆壳是否符合相关安全标准和规定,例如防爆等级、防护能力等。
2.通过非破坏性检测手段,例如X射线检测、超声波检测等,对防爆壳进行内部缺陷检测,确保其内部结构的完整性。
五、可靠性检验
1.对防爆壳进行耐久性测试,例如多次开启和关闭防爆壳门、多次冲
击等,以验证其在长时间使用过程中的可靠性。
2.进行防水性能测试,将防爆壳浸泡在一定深度的水中,观察其内部
是否受到水的侵入。
六、其他检验
1.检查防爆壳的包装是否完好无损,确保在运输和搬运过程中不会损
坏或变形。
2.检查防爆壳的相关标志和标识是否清晰可辨认,例如生产厂家、产
品型号等。
七、结论
根据以上要求示范进行防爆壳体检验,可以有效确保其质量和安全性。
在实际检验中,可以根据实际情况制定具体的检验方案和标准,以满足不
同防爆壳的检验需求。
检验结果应该及时记录和报告,对于不符合要求的
防爆壳应该及时处理、修复或替换,以保证其正常使用和安全性。
防爆壳体检验要求规范

隔爆壳体制造及出厂检验标准编制:审核:批准:隔爆壳体制造及出厂检验标准一、一般规定1.本标准适用于本公司隔爆壳体制造。
如图样或技术文件有特殊要求时应按图样或技术文件的规定执行。
2.本标准中各项规定,凡低于国家标准的,均按国家标准执行。
二、准备3.原材料牌号应符合图纸规定。
4.各种钢材在下料前应核实尺寸,其公差不符合本标准第5条规定者,均需矫正以达到要求公差。
5.钢板、扁钢的直线度及局部波状平面度的偏差不应超过表1的规定,否则必须矫正后方可使用。
表1 单位mm6.钢材的初步矫正,一般在冷态下在辊式矫正机或压力机进行。
用于次要焊接结构的钢板可放在平台上用平锤矫正。
7.钢材的矫正一般变形程度不大时,可用冷矫方法,弯曲较大的钢材应加热至900℃~1100℃时矫正。
矫正后的钢材表面不得有裂纹及明显痕迹,锤击痕深度对钢板为0.5mm,扁钢1mm(立面上)。
三、号料前的准备8.严格按照图样、技术文件、工艺要求及计算展开进行;下料偏差应符合《GB/T1804-1992 一般公差线性尺寸的未注公差》《GB/T1804-m》的要求。
9.样板的制造要考虑到结构在焊接时所产生的收缩量及零件的加工余量。
10.样板的外形尺寸偏差,当外形尺寸小于1米时为±0.4mm;大于1米时为±0.8mm。
11.样板上号料孔眼应用钻床钻孔,或用冲眼冲子冲成,但眼孔直径不能大于2毫米。
12.在样板上划线的偏差应符合下列规定:(1)相邻两孔的中心线的距离偏差为±0.15mm;(2)板边与边孔的中心线的距离偏差为±0.20mm;(3)相间(间隔一孔)钉孔中心线间的距离偏差为±0.30mm;(4)最大两端钉孔中心线的距离偏差为±0.40mm。
13.每个样板必须有标记(工号、图号、材料断面尺寸),样板经质量检查员验收签署后才可使用。
14.划线前,划线工应仔细检查样板是否合乎要求。
15.对单件小批生产的产品,允许直接在钢材上按图样进行划线。
防爆壳体检验要求规范
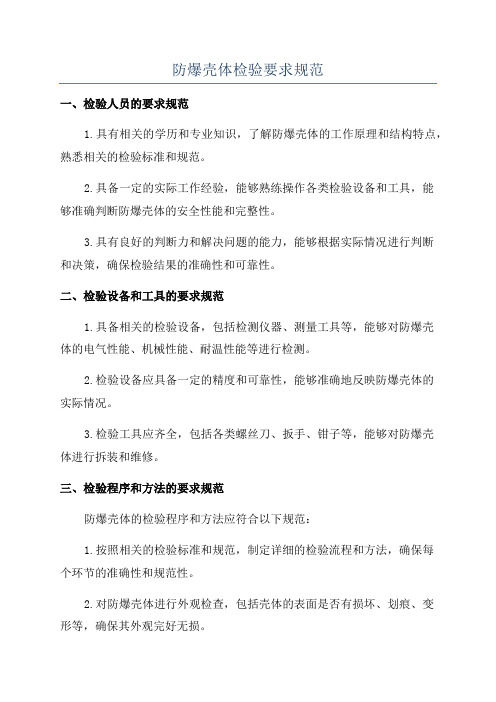
防爆壳体检验要求规范一、检验人员的要求规范1.具有相关的学历和专业知识,了解防爆壳体的工作原理和结构特点,熟悉相关的检验标准和规范。
2.具备一定的实际工作经验,能够熟练操作各类检验设备和工具,能够准确判断防爆壳体的安全性能和完整性。
3.具有良好的判断力和解决问题的能力,能够根据实际情况进行判断和决策,确保检验结果的准确性和可靠性。
二、检验设备和工具的要求规范1.具备相关的检验设备,包括检测仪器、测量工具等,能够对防爆壳体的电气性能、机械性能、耐温性能等进行检测。
2.检验设备应具备一定的精度和可靠性,能够准确地反映防爆壳体的实际情况。
3.检验工具应齐全,包括各类螺丝刀、扳手、钳子等,能够对防爆壳体进行拆装和维修。
三、检验程序和方法的要求规范防爆壳体的检验程序和方法应符合以下规范:1.按照相关的检验标准和规范,制定详细的检验流程和方法,确保每个环节的准确性和规范性。
2.对防爆壳体进行外观检查,包括壳体的表面是否有损坏、划痕、变形等,确保其外观完好无损。
3.对防爆壳体进行电气性能检验,包括耐压测试、绝缘电阻测试、接地测试等,确保其电气性能符合要求。
4.对防爆壳体进行机械性能检验,包括强度测试、密封性测试等,确保其机械性能符合要求。
5.对防爆壳体进行耐温性能检验,包括加热测试、热冲击测试等,确保其能够在高温环境下正常工作。
6.根据检验结果,对防爆壳体进行评估和判定,给出合格或不合格的结论。
四、检验结果的记录和报告的要求规范防爆壳体的检验结果应进行详细的记录和报告,包括以下几个方面:1.记录每个检验环节的检验方法、检验结果和检验日期等,确保记录的准确性和可追溯性。
2.对于不合格项,应记录具体的不合格现象和原因,并提出相应的处理建议。
3.生成详细的检验报告,包括检验结论、不合格项处理情况、检验人员签字等,确保报告的完整性和可信度。
综上所述,防爆壳体检验要求规范涉及到检验人员的要求、检验设备和工具的要求、检验程序和方法的要求,以及检验结果的记录和报告的要求等。
防爆壳体检验要求规范
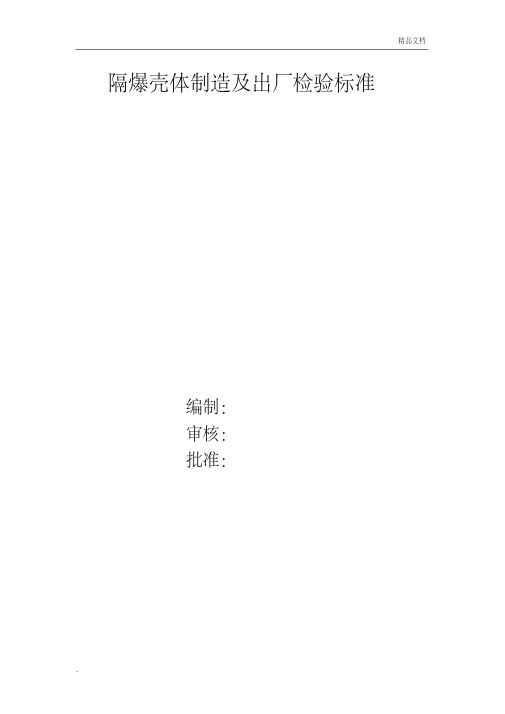
隔爆壳体制造及出厂检验标准编制:审核:批准:隔爆壳体制造及出厂检验标准一、一般规定1.本标准适用于本公司隔爆壳体制造。
如图样或技术文件有特殊要求时应按图样或技术文件的规定执行。
2.本标准中各项规定,凡低于国家标准的,均按国家标准执行。
二、准备3.原材料牌号应符合图纸规定。
4.各种钢材在下料前应核实尺寸,其公差不符合本标准第5条规定者,均需矫正以达到要求公差。
5.钢板、扁钢的直线度及局部波状平面度的偏差不应超过表1的规定,否则必须矫正后方可使用。
表1单位mm厚度(t )在1米长度内的直线度和局部波状凹凸平面度允许偏差(f )测量工具简要≤4 3 钢直尺,1米的平尺>4~8 2 >8~14 1.5 >1416.钢材的初步矫正,一般在冷态下在辊式矫正机或压力机进行。
用于次要焊接结构的钢板可放在平台上用平锤矫正。
7.钢材的矫正一般变形程度不大时,可用冷矫方法,弯曲较大的钢材应加热至900℃~1100℃时矫正。
矫正后的钢材表面不得有裂纹及明显痕迹,锤击痕深度对钢板为0.5mm,扁钢1mm(立面上)。
三、号料前的准备8.严格按照图样、技术文件、工艺要求及计算展开进行;下料偏差应符合《GB/T1804-1992 一般公差线性尺寸的未注公差》《GB/T1804-m》的要求。
9.样板的制造要考虑到结构在焊接时所产生的收缩量及零件的加工余量。
10.样板的外形尺寸偏差,当外形尺寸小于1米时为±0.4mm;大于1米时为±0.8mm。
11.样板上号料孔眼应用钻床钻孔,或用冲眼冲子冲成,但眼孔直径不能大于2毫米。
12.在样板上划线的偏差应符合下列规定:(1)相邻两孔的中心线的距离偏差为±0.15mm;(2)板边与边孔的中心线的距离偏差为±0.20mm;(3)相间(间隔一孔)钉孔中心线间的距离偏差为±0.30mm;(4)最大两端钉孔中心线的距离偏差为±0.40mm。
防爆设备入井验收制度及防爆检查制度
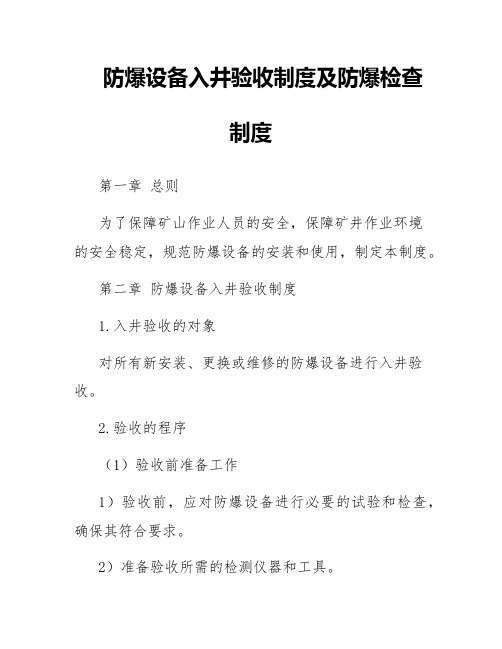
防爆设备入井验收制度及防爆检查制度第一章总则为了保障矿山作业人员的安全,保障矿井作业环境的安全稳定,规范防爆设备的安装和使用,制定本制度。
第二章防爆设备入井验收制度1.入井验收的对象对所有新安装、更换或维修的防爆设备进行入井验收。
2.验收的程序(1)验收前准备工作1)验收前,应对防爆设备进行必要的试验和检查,确保其符合要求。
2)准备验收所需的检测仪器和工具。
(2)验收过程1)验收人员按照相关规定进行验收,并填写验收记录。
2)对设备的防爆等级、安全性能、外观等方面进行全面检查。
3)如发现问题,应及时进行处理,确保设备符合要求。
(3)验收后工作1)验收合格的设备应在设备上盖章确认,并核实验收记录。
2)验收不合格的设备应及时报告并进行处理,直至符合要求。
3.验收人员验收人员应为具有专业资质和经验的人员,确保验收的准确性和有效性。
4.验收频率对于新安装的设备,应在安装完成后进行验收;对于更换或维修的设备,应在安装完成后进行验收。
第三章防爆检查制度1.检查的对象对矿井内的防爆设备进行定期检查,确保设备的安全稳定使用。
2.检查的频率(1)日常检查每日对关键部位的防爆设备进行检查,确保设备正常使用、无损坏和松动。
(2)定期检查根据相关规定,对矿井内的防爆设备进行定期检查,确保设备的安全性能和使用效果。
3.检查的内容(1)防爆设备的防爆等级和性能是否符合要求。
(2)防爆设备的安装和连接是否牢固可靠。
(3)防爆设备的使用是否规范。
(4)防爆设备的外观是否正常,是否有损坏或异物。
4.检查记录每次检查均应填写检查记录,并对发现的问题进行记录并及时处理。
5.检查人员检查人员应为具有相关资质和经验的专业人员,确保检查工作的准确性和有效性。
6.对检查结果的处理对于检查结果发现的问题,应及时进行整改和处理,确保设备的安全稳定使用。
第四章防爆设备管理1.防爆设备的接收、发放和使用应按规定进行,确保设备的正常使用和安全保障。
2.对于损坏或过期的防爆设备,应及时更换。
防爆检查标准

防爆检查标准防爆检查是指对可能发生爆炸危险的场所、设备和工艺进行定期检查,以确保其安全运行。
防爆检查标准是对防爆设备和防爆场所进行检查的依据,它的制定和执行对于保障人员生命财产安全具有重要意义。
本文将就防爆检查标准进行详细介绍,以便各单位和个人能够更好地了解和执行相关标准。
首先,防爆检查标准应包括对防爆设备和防爆场所的具体要求。
对于防爆设备,应包括其安全使用、维护、保养和检修等方面的要求,例如防爆电气设备的防护等级、防爆灯具的防爆等级等。
对于防爆场所,应包括其防爆区域的划分、防爆设备的设置和使用、防爆标志的设置等方面的要求,确保防爆场所内的设备和工艺能够安全运行。
其次,防爆检查标准应包括对防爆设备和防爆场所的检查内容和方法。
检查内容应包括对设备和场所的全面检查,包括设备的外观、电气连接、接地情况、防爆设备的完好性等方面的检查。
检查方法应包括目视检查、测量检查、试验检查等,以确保对设备和场所进行全面、细致的检查。
另外,防爆检查标准应包括对检查结果的评定和处理要求。
对于检查结果,应根据实际情况进行评定,对于存在安全隐患的设备和场所应及时进行处理,包括停止使用、维修更换等。
对于检查结果的处理,应包括对于安全隐患的整改要求和时限,确保安全隐患能够得到及时有效的处理。
最后,防爆检查标准应包括对防爆检查的管理和执行要求。
管理要求包括对防爆检查的组织、计划、实施和监督等方面的要求,确保防爆检查能够得到有效的管理和执行。
执行要求包括对防爆检查人员的资质、培训和责任等方面的要求,确保防爆检查能够得到专业、严格的执行。
综上所述,防爆检查标准是对防爆设备和防爆场所进行检查的依据,其制定和执行对于保障人员生命财产安全具有重要意义。
各单位和个人应严格执行相关标准,确保防爆设备和防爆场所的安全运行,防范和减少事故的发生。
希望本文能够对各单位和个人有所帮助,促进防爆检查工作的规范和落实。
- 1、下载文档前请自行甄别文档内容的完整性,平台不提供额外的编辑、内容补充、找答案等附加服务。
- 2、"仅部分预览"的文档,不可在线预览部分如存在完整性等问题,可反馈申请退款(可完整预览的文档不适用该条件!)。
- 3、如文档侵犯您的权益,请联系客服反馈,我们会尽快为您处理(人工客服工作时间:9:00-18:30)。
隔爆壳体制造及出厂检验标准编制:审核:批准:隔爆壳体制造及出厂检验标准一、一般规定1.本标准适用于本公司隔爆壳体制造。
如图样或技术文件有特殊要求时应按图样或技术文件的规定执行。
2.本标准中各项规定,凡低于国家标准的,均按国家标准执行。
二、准备3.原材料牌号应符合图纸规定。
4.各种钢材在下料前应核实尺寸,其公差不符合本标准第5条规定者,均需矫正以达到要求公差。
5.钢板、扁钢的直线度及局部波状平面度的偏差不应超过表1的规定,否则必须矫正后方可使用。
表1 单位mm6.钢材的初步矫正,一般在冷态下在辊式矫正机或压力机进行。
用于次要焊接结构的钢板可放在平台上用平锤矫正。
7.钢材的矫正一般变形程度不大时,可用冷矫方法,弯曲较大的钢材应加热至900℃~1100℃时矫正。
矫正后的钢材表面不得有裂纹及明显痕迹,锤击痕深度对钢板为0.5mm,扁钢1mm(立面上)。
三、号料前的准备8.严格按照图样、技术文件、工艺要求及计算展开进行;下料偏差应符合《GB/T1804-1992 一般公差线性尺寸的未注公差》《GB/T1804-m》的要求。
9.样板的制造要考虑到结构在焊接时所产生的收缩量及零件的加工余量。
10.样板的外形尺寸偏差,当外形尺寸小于1米时为±0.4mm;大于1米时为±0.8mm。
11.样板上号料孔眼应用钻床钻孔,或用冲眼冲子冲成,但眼孔直径不能大于2毫米。
12.在样板上划线的偏差应符合下列规定:(1)相邻两孔的中心线的距离偏差为±0.15mm;(2)板边与边孔的中心线的距离偏差为±0.20mm;(3)相间(间隔一孔)钉孔中心线间的距离偏差为±0.30mm;(4)最大两端钉孔中心线的距离偏差为±0.40mm。
13.每个样板必须有标记(工号、图号、材料断面尺寸),样板经质量检查员验收签署后才可使用。
14.划线前,划线工应仔细检查样板是否合乎要求。
15.对单件小批生产的产品,允许直接在钢材上按图样进行划线。
16.号料时应考虑留出工艺损耗量。
四、切料17.钢材可以用机械剪切、锯床、气割等方法。
18.切料后,边棱上的堆积物、毛刺和凸起部分均应清除。
切料尺寸偏差应符合下列规定(1)钢板的机械剪切线与号线的偏差不大于表2的规定。
表2 单位mm(2)钢板下料时,沿长度或宽度方向的偏斜(如图1)不得超过板料剪切偏差所允许的范围(表2)正负图1(3)气割后要保留号料线,气割线与号料线的偏差,对于手工切割时不超过±1.5毫米,对自动或半自动的切割不超过1毫米。
19.框架法兰下料偏差(如图2)图2L 端加工的偏差为+2~+4。
L 端不加工的偏差为-0.5~+1,端面斜偏差不超过0.5mm ,但不能超过两端不加工面的偏差值(如图3)。
图320.出线板下料不分长短边偏差为-0.5-1.0。
21.底板下料不分长短边偏差为-0.5-1.0,对角线性偏差不超过1.5mm 。
22.出线室的钢板展开长度下料偏差为+1.0-0.5,宽度偏差为+2.0 +1.0。
23.方箱体展开长度下料偏差为+2.0 +1.0,对角线性偏差不超过1.5mm 。
圆箱体展开长度下料偏差为+3.0 +1.0,对角线性偏差不超过1.5mm 。
24.接线室上盖下料不分长短边偏差为+1.0 +0.5.25.各种内腔安装底板下料不分长短边偏差为±1。
五、焊接件的对装要求26.对拼装前,全部零部件须经检查合格。
27.对装结构零件及整个结构时,必须严格保持图样上的标准尺寸。
尺寸不合格的零件,禁止用强力矫正,以防引起过大的应力;但允许用轻轻打击,用弓形卡牵引的方法进行零件的局部调整。
但隔爆面加工后的部件严禁矫正。
28.结构件边缘上的裂纹和其他缺陷,经技术检查部门同意后,允许焊补。
29.对装焊接零件时,焊接间隙及焊接件相互位置的偏差应符合下列规定:(1)对装对接接头(图4)时,当对接两板厚度相同,两个焊边允许的偏差按表3规定。
图4表330.坡口的焊接形式及偏差 表4。
表431.框架法兰焊接偏差,m 偏差应减去a 1、a 2长度的误差(图5)。
c =±0.3L=±1.0H=±1.0图5 m=±1.5六、焊接技术条件 (一)一般规则32.焊工应经专门培训考核合格,才能担任焊接工作,持证上岗。
33.焊接专职检查人员应由具有一定理论及实践经验的人员担任,并需经总工程师(或公司技术总负责人)审批。
34.检查人员对违反规定的焊接作业,有权制止,直至得到纠正。
(二)技术要求35.Ⅰ、Ⅱ级焊缝破口的加工采用机械的方法(门法兰、箱体法兰、接线上腔法兰)。
Ⅰ、Ⅱ级焊缝破口的加工可采用气割等方法。
36.焊接材料的选用,应根据木材的化学成分、机械性能、焊前预热及焊后回火等综合考虑。
37.多层焊接时,在焊接每层焊缝以前,应对前一层焊缝进行检查,如发现夹渣、气孔和裂纹时,应将缺陷部分除净再焊。
38.不同厚度钢板焊接时,如图中未注明焊脚高度,则其焊脚高度等于薄板的厚度。
(三)焊接工艺的要求39.焊接接头形式和尺寸按表4选用。
40.焊前应将坡口表面及内外侧10毫米范围内的油、锈污物及水气清除干净。
41.焊接工艺对外界环境的要求(1)恶劣天气(下雨、下雪、大风及高湿度等室外作业)如无有效措施,禁止施焊。
(2)当焊接温度低于0℃时,应考虑在始焊外100毫米范围内预热到约15℃(手触感温暖),不准用重锤打击所焊的构件,在焊接过程中保证焊缝能够自由收缩。
(3)壳体焊接一般应在室内进行,室温不得低于5℃,当室温低于0℃时按要求(2)。
(四)焊接变形的矫正42.焊接构件如有变形,允许用局部加热的方法矫正。
加热温度为800~850℃,但不允许在300~500℃时矫正。
低碳钢焊接构件的矫正可在冷态下进行。
(五)焊接的检查及验收43.验收应在焊接构件4小时后进行(完全冷却后)。
44.焊件检查前应将焊缝上的渣皮及飞溅物等清除干净。
45.用肉眼或借助放大镜环件检查焊缝的外观质量。
46.用尺或样板抽查焊缝及构件的几何尺寸。
47.焊缝的形状偏差及外部应无明显缺陷。
咬边的深度不应超过0.5mm,最长不超过焊缝长度的10%。
不允许烧穿,不允许有裂纹,不允许鳞状波纹高低不一致或太高,不允许有皱纹形成不均匀。
焊缝不均匀偏差Δ=1.5mm。
最大不超过Δ=2mm。
(图6)图6焊缝高度不正确:①平焊凸出偏差0.5~1mm。
②角焊高度不够,偏差4~12±0.5mm。
③不允许有焊缝间断,不允许有漏出弧坑状的缺陷,未焊头未按有关规定执行,不允许有气孔。
mm的偏差。
④焊缝尺寸不正确K=+1.0-0.548.检查人员及操作者的代号标记自定。
(六)静压试验应根据《GB3836.2-2000》15.1.2执行,机械加工及验收一、技术条件及验收49.原材料应符合图纸规定,如不符合时,在保证零件机械性能和使用寿命的条件下可按照的材料代用制度代用。
50.零件的加工表面上,不允许又降低零件精度及寿命的缺陷(如沟痕、碰伤等)。
加工后各部毛刺应除净,切断时留下的余头要削平。
51.在图纸上未注明零件的倒钝或圆角尺寸,加工时一般须有0.2~0.5×45°的倒棱或半径为0.2~0.5毫米的圆角。
52.过度圆角或圆根表面粗糙度,应按与之相连接地两表面中等级较高的粗糙度加工。
53.零件加工后在转移工序、车间或仓库存放的,必须防止其表面碰伤、锈蚀及变形。
54.零件的尺寸未注公差时,其偏差值按GB/T1804-m级。
55.各种螺纹加工其精度等级为6H或6g。
56.隔爆面加工粗糙度不低于,按钮孔的粗糙度不低于。
二、划钻孔、铰孔57.严格按图样要求进行,其钻孔粗糙度不低于,铰孔不低于。
58.出线板上面的孔位置度偏差不大于1mm,必须进行铰孔,达到其技术要求及公差。
59.划钻孔的部位相对偏差为1.5mm。
60.各种法兰框架、盖板划钻孔,相邻两孔偏差不大于0.3mm,多孔最大公差带不大于0.4mm。
61.钻铰孔应垂直,每100mm长度其偏差不大于0.30mm(如图7)。
图762.开门铰链必须采用铰孔配销轴方法,钻铰链轴销孔,焊接前应保证有足够的配钻铰孔余量。
63.加工各种按钮杆应严格按图样要求,其直径超差量均不大于-0.005mm。
64.其他加工件偏差均不低于GB/T1804-C级。
三、隔爆面加工前处理65.壳体焊接完成后,经过48小时的自然冷却后,对其进行内应力振动时效处理,较小壳体处理时间不小于20分钟,较大壳体处理时间不小于30分钟。
如采用回火处理,回火温度应控制在600~650℃,保温时间1小时,保温后以小于2.5~3℃/分的速度缓慢冷却至30℃以下出路或随炉冷却。
消除内应力后,应仔细检查焊缝质量,如发现焊缝有裂纹应进行补焊,在进行相关水压试验检查。
66.抛丸处理应将加工过部位进行保护处理,不得损坏其加工后的隔爆面、螺孔、窗口、出线孔、绝缘座孔等部位。
四、其他部分67.带螺纹联通节无螺纹部分应保证长度在12.5+1mm螺纹精度等级不低于7g级,粗糙度不低于。
68.组合开关扭杆,开关扭杆,开槽对称度偏差不大于0.07mm。
69.按钮套座的孔加工必须铰制达到公差要求,粗糙度不低于,最低不得低于。
70.按钮杆粗糙度不得低于,其几何尺寸满足图样要求。
71.各种卡快加工面粗糙度不得低于。
72.大联通节内孔加工粗糙度不得低于,其公称尺寸+0.40mm。
73.快开门的加工部件必须严格按图样加工,粗糙度及精度不得降低。
拼装、装配及验收一、一般规定74.所有机件(包括外购件),必须经技术检查部门检查合格后,方准装配。
75.应在装配前,操作者必须熟悉装配技术文件及要求,了解其结构、性能和装配数据,周密考虑装配方法和程序。
76.熟悉GB3836.1-2000、GB3836.2-2000中的技术要求。
77.熟悉本标准的各项规定。
二、技术条件78.所有零部件装配前必须将切削、毛刺、油污等杂物清除干净。
79.隔爆面不得有划痕、锈蚀和任何损伤。
必须对隔爆面采取有效保护措施。
80.装配前必须将隔爆面进行防蚀处理,处理时严格按有关规程进行。
81.装配转动部位应涂少量润滑脂。
82.装配弹簧时,不准拉长或切短。
83.装配过程中的机械加工(如钻孔。
铰孔、攻丝等)工序和焊接工序应符合本标准中的有关规定。
84.整机装配应清理干净所有部位的毛刺、焊渣和油污等。
三、紧固件装配(一)螺纹连接85.螺栓螺钉头部或螺母的端面必须与被紧固的零件表面均匀接触,不许用手锤矫正螺栓的歪斜。
86.螺孔攻丝后,中心线对接合面的垂直度极限偏差不大于0.03%。
87.紧固螺钉时,要根据被联接件的形状、螺钉分布情况,对称逐次拧紧。
89.螺栓紧固后漏出螺母的长度应有1~3丝;沉头螺钉拧紧后钉头不得凸出被联接件表面。