塑料壳体检验细则
塑胶外壳外观检验标准-超详细
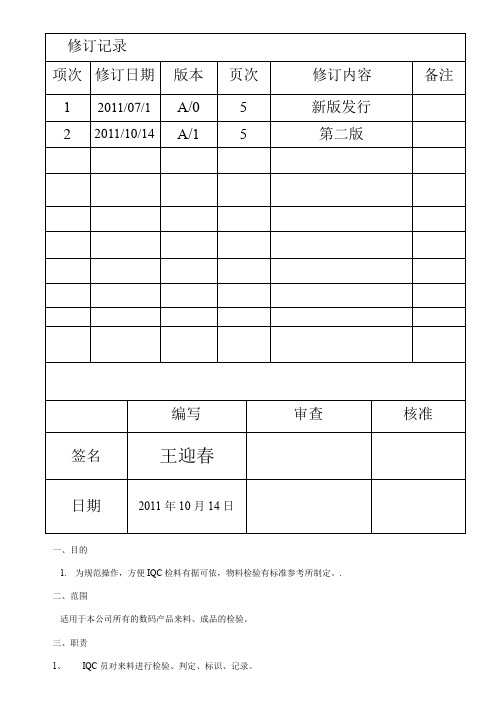
一、目的
1.为规范操作,方便IQC检料有据可依,物料检验有标准参考所制定。
.
二、范围
适用于本公司所有的数码产品来料、成品的检验。
三、职责
1、IQC员对来料进行检验、判定、标识、记录。
2、IQC组长对异常情况的判定、分析、反馈。
3、品质主管、IQC组长、QC组长对不良品的判定、分析、协同采购要求供应商改善,提升产品品质。
四、抽样计划
按GB2828-2003计数抽样程序及抽样表,外观抽样依据MIL-STD-105E 一般Ⅱ级随机抽样
AQL :CR=0
MAJOR: 0.4
MINOR: 1.0
五、规范内容:
5.1缺陷分类
会导致使用人员或财产受到伤害、违反法律法规、产品完全失去应有能力,会严重伤害到企业的信誉.
属安全方面的缺陷。
产品失去商品价值或功能不全,及外观不良严重影响使用者感受,及可能导至客户退货或投诉;
不会降低产品的使用效果、只是存在外观方面的轻微缺陷。
.
5.2检查条件及参数
检验时间:各面目视检查时间约为3秒针
5.3外观检查面设定:外观检查面设定为ABCD四个面
5.3..4:D面:一般为产品的内部
5.4代号
H—变形度(mm)
W—宽度(mm)
S—制件表面积(mm2)
?—缺陷直径(mm)
L—长度(mm)
D—间距(mm)
B 其他:暂无。
塑胶壳检验规范
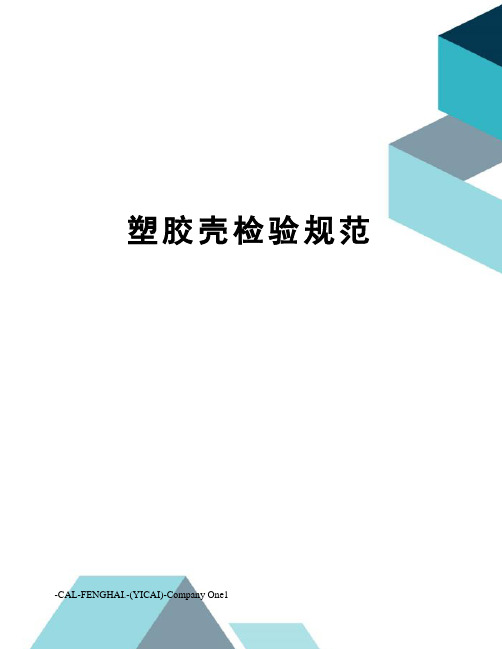
塑胶壳检验规范-CAL-FENGHAI.-(YICAI)-Company One1塑胶壳检验规范1.目的:使进料检验员依此规范进行塑胶壳之进料检验,以确保所购塑胶壳质量符合本公司要求。
2.范围:凡经本公司开发部设计、承认、由采购单位对外购入之各种塑胶壳适用之。
3.定义::缺陷分类:严重缺陷—CR DEFECT: 物料存在有尖点、利边、漏电、等凡是有影响或危及使用者生命安全的缺陷。
主要缺陷—MAJ DEFECT: 物料主要性能指标不合格,导致物料本身失去功能成不能使用的缺陷。
次要缺陷—MIN DEFECT: 该缺点或不符合项目不致影响材料本身功能或易于排除者。
:缺陷术语:1)异色点:与本身颜色不同的杂点或混入树脂中的杂点暴露在表面上。
2)气丝:由于种种原因,气体在产品表面留下的痕迹与底面颜色不同并发亮,带有流动样。
3)塌坑/缩水:由于材料收缩,使产品局部整体表面下陷。
4)熔接缝:产品在成型过程中,二股以上的融熔料相汇合的接线,目视及手感都有感觉。
5)缺料:产品某个部位不饱满。
6)白印:由于内应力,在产品表面产生与本色不同的白色痕迹。
7)批锋:由于种种原因,产品非结构部分产生多余的料8)封堵:应该通透的地方由于滋边造成不通。
9)断裂:塑料理局部断开后的缺陷。
10)拉毛:因摩擦而产生的细皮,附在塑料表面的现象。
11)油丝:油痕,油污(包括脱模式剂)在产品表面留下的痕迹,使该部位发亮,并带有流动样。
4. 检验方式与标准:检验条件:检验环境:将待验物品置于400-1000Lux光源下;检验距离:产品距两眼30-45cm;检验角度:产品与水平面呈45度角;检验速度: 10mm2/Sec;检验项目、方法标准、缺陷分类一览表:5.相关记录表格:《收货验收单》;《每周进料检验统计表》;。
壳塑料件检验标准
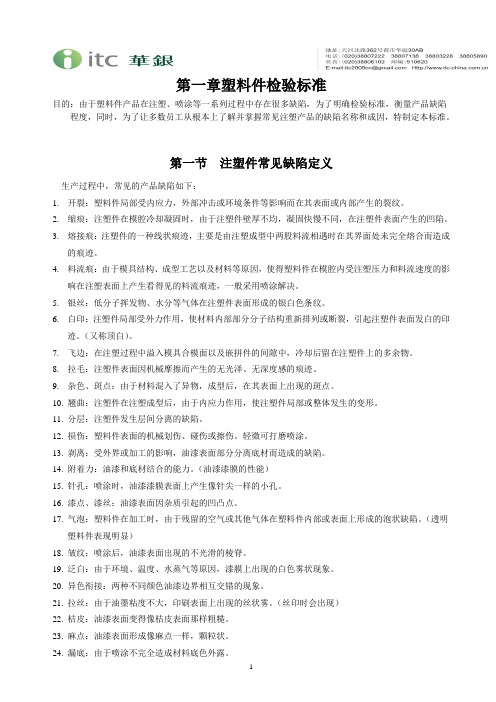
第一章塑料件检验标准目的:由于塑料件产品在注塑、喷涂等一系列过程中存在很多缺陷,为了明确检验标准,衡量产品缺陷程度,同时,为了让多数员工从根本上了解并掌握常见注塑产品的缺陷名称和成因,特制定本标准。
第一节注塑件常见缺陷定义生产过程中,常见的产品缺陷如下:1.开裂:塑料件局部受内应力,外部冲击或环境条件等影响而在其表面或内部产生的裂纹。
2.缩痕:注塑件在模腔冷却凝固时,由于注塑件壁厚不均,凝固快慢不同,在注塑件表面产生的凹陷。
3.熔接痕:注塑件的一种线状痕迹,主要是由注塑成型中两股料流相遇时在其界面处未完全熔合而造成的痕迹。
4.料流痕:由于模具结构、成型工艺以及材料等原因,使得塑料件在模腔内受注塑压力和料流速度的影响在注塑表面上产生看得见的料流痕迹,一般采用喷涂解决。
5.银丝:低分子挥发物、水分等气体在注塑件表面形成的银白色条纹。
6.白印:注塑件局部受外力作用,使材料内部部分分子结构重新排列或断裂,引起注塑件表面发白的印迹。
(又称顶白)。
7.飞边:在注塑过程中溢入模具合模面以及嵌拼件的间隙中,冷却后留在注塑件上的多余物。
8.拉毛:注塑件表面因机械摩擦而产生的无光泽、无深度感的痕迹。
9.杂色、斑点:由于材料混入了异物,成型后,在其表面上出现的斑点。
10.翘曲:注塑件在注塑成型后,由于内应力作用,使注塑件局部或整体发生的变形。
11.分层:注塑件发生层间分离的缺陷。
12.损伤:塑料件表面的机械划伤、碰伤或擦伤。
轻微可打磨喷涂。
13.剥离:受外界或加工的影响,油漆表面部分分离底材而造成的缺陷。
14.附着力:油漆和底材结合的能力。
(油漆漆膜的性能)15.针孔:喷涂时,油漆漆膜表面上产生像针尖一样的小孔。
16.漆点、漆丝:油漆表面因杂质引起的凹凸点。
17.气泡:塑料件在加工时,由于残留的空气或其他气体在塑料件内部或表面上形成的泡状缺陷。
(透明塑料件表现明显)18.皱纹:喷涂后,油漆表面出现的不光滑的棱脊。
19.泛白:由于环境、温度、水蒸气等原因,漆膜上出现的白色雾状现象。
某公司手机外壳塑胶件外观检验标准
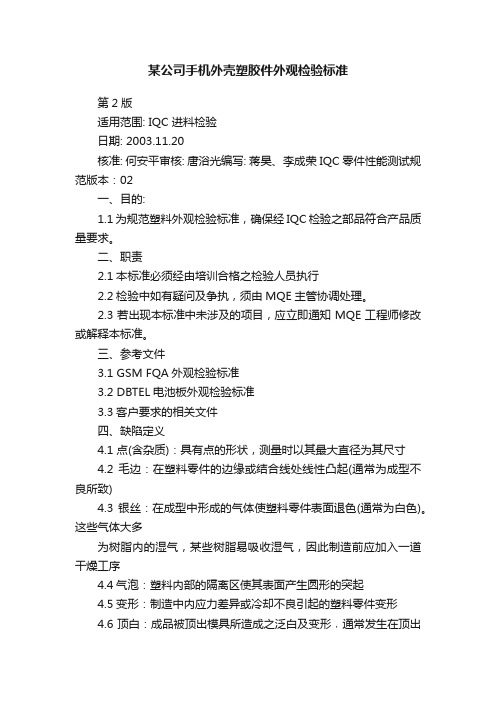
某公司手机外壳塑胶件外观检验标准第2版适用范围: IQC 进料检验日期: 2003.11.20核准: 何安平审核: 唐浴光编写: 蒋昊、李成荣IQC零件性能测试规范版本:02一、目的:1.1为规范塑料外观检验标准,确保经IQC检验之部品符合产品质量要求。
二、职责2.1本标准必须经由培训合格之检验人员执行2.2检验中如有疑问及争执,须由MQE主管协调处理。
2.3若出现本标准中未涉及的项目,应立即通知MQE工程师修改或解释本标准。
三、参考文件3.1 GSM FQA外观检验标准3.2 DBTEL电池板外观检验标准3.3客户要求的相关文件四、缺陷定义4.1 点(含杂质):具有点的形状,测量时以其最大直径为其尺寸4.2 毛边:在塑料零件的边缘或结合线处线性凸起(通常为成型不良所致)4.3 银丝:在成型中形成的气体使塑料零件表面退色(通常为白色)。
这些气体大多为树脂内的湿气,某些树脂易吸收湿气,因此制造前应加入一道干燥工序4.4气泡:塑料内部的隔离区使其表面产生圆形的突起4.5变形:制造中内应力差异或冷却不良引起的塑料零件变形4.6顶白:成品被顶出模具所造成之泛白及变形﹐通常发生在顶出稍的另一端(母模面)4.7缺料:由于模具的损坏或其它原因﹐造成成品有射不饱和缺料情形.4.8断印:印刷中由于杂质或其它原因造成印刷字体中的白点等情况。
4.9漏印:印刷内容缺划或缺角或字体断印缺陷大于0.3mm,也被认为有漏印。
4.10色差:指实际部品颜色与承认样品颜色或色号比对超出允收值。
4.11同色点: 指颜色与部品颜色相接近的点;反之为异色点。
4.12流水纹:由于成形的原因﹐在浇口处留下的热溶塑料流动的条纹4.13熔接痕:由于两条或更多的熔融的塑料流汇聚,而形成在零件表面的线性痕迹4.14装配缝隙:除了设计时规定的缝隙外,由两部组件装配造成的缝隙4.15细碎划伤:无深度的表面擦伤或痕迹(通常为手工操作时造成)4.16硬划伤:硬物或锐器造成零件表面的深度线性伤痕(通常为手工操作时造成)4.17凹痕缩水:零件表面出现凹陷的痕迹或尺寸小于设计尺寸(通常为成型不良所致)4.18颜色分离:塑料生产中,流动区出现的条状或点状色痕(通常由于加入再生材料引起)4.19不可见:指瑕疵直径<0.03mm为不可见,LENS透明区除外(依每部品材料所订定之检测距离)4.20碰伤:产品表面或边缘遭硬物撞击而产生的痕迹4.21油斑:附着在对象表面的油性液体4.22漏喷:应喷漆之产品表面部份因异常原因而导致油漆没有喷到露出底材之现象4.23修边不良:产品边缘处因人工修边而产生缺口等不规则形状4.24毛屑:分布在喷漆件表面的线型杂质。
某公司塑胶面壳检验规范

A=0
R=1
变形翘起不得超过0.5mm
测试平板塞规
8.
耐摩擦
测试
用施加约1.6kgf的橡胶类橡皮在检验机壳上以25.4mm的行程每分钟30次往返摩擦。
N=5
A=0
R=1
喷油部分65回数后底料不能看见,丝印部分35回数后文字能判读出来。
橡皮、
电子称
9.
硬度测试
用施加了1kgf荷重的2B铅笔芯以45度角在机壳喷油表体上移动10mm,共5次。
R=1
样品
实际装配
3.
功能键
各功能键、开关、旋钮连续按30∽40次,操作应灵活可靠反应正确。
N=5
A=0
R=1
说明书
实际操作
4.
尺寸
尺寸应与样板或规格书相符
N=5
Aห้องสมุดไป่ตู้0
R=1
规格书或样品
卡尺
5.
破坏性
实验
常温下将被实验品以1m高度自由跌落后,其外观、尺寸应符合以上1、4点要求。
N=5
A=0
R=1
依检验
N=5
A=0
R=1
无剥离刮伤、割伤等现象
2B铅笔、
电子称
10.
耐酒精性测试
用施加了1kgf/CM2荷重并含有0.5ml消毒用乙醇酒精(76.9-81.4%)的圆棒形棉布或纱布以1秒往返1次的速度在机壳上移动。
N=5
A=0
R=1
喷油部分10回数往返后表面无不良,丝印部分10回数往返后文字能判读出来
酒精、棉布/纱布、电子称
注:针对面壳
塑胶外壳
(含装配机壳的上盖、中盖、后盖等系列)
适用范围:各种类型塑胶外壳
塑料外壳检测标准

SAMCO-SVC06/VM06系列塑料壳体测试标准
一、材质:
PC+PBT
二、材料特性:
材料特性请参照特性表
三、测试范围:
针对SAMCO-SVC06/VM06系列
四、产品控制:
1.供货商提供每批次产品相应测试报告。
2.供货商提供每批次产品的物性表及相关的检测报告。
3.定期到供货商进行相关的测试验证。
4.如果物性表及相关检测报告上面的粒子供货商和塑料产品供货商有所变动,应及时查实。
五、测试方法:采用冲击试验仪
图2
图1 图3
●将冲击试验仪(图1)上面的1kg冲击块调至1米处(图2)。
●将产品放在冲击试验仪下面的底座上,将冲击检测部位对准冲击块(图3)。
●将1kg冲击块从1米处瞬间落下,对产品进行冲击(四个方位都要进行冲击)。
●检查冲击部位是否有破损,同时检查产品周边是否有破损开裂现象。
●受冲击的产品整体不可有破损开裂现象。
塑胶壳检验标准

4.3.3.1连续10批检验合格。
4.3.3.2 10批中不合格品(或缺陷)总数在界限个数以下。
4.3.3.3生产正常。
4.3.3.4主管者认为有必要,以上四个条件必须同时满足。
4.3.4放宽检查转正常检查的条件
4.3.4.1 1批检验不合格。
4.3.4.2生产不正常。
5.1.5核对样板:
5.1.5.1结构样板(每个模号、穴号都需要与相应结构板相符合);
5.1.5.2颜色样板(需核对认可供应商、喷油范围;颜色偏差与机型色板有色差时,可核对上下限度样板);
5.1.5.3丝印(核对丝印范围,字体颜色效果,歪斜程度)
5.2外观检验:环境在光度为600------800LUX的条件下,人眼与被检测面距离为25------35CM。观察角度与被检测面为正负45度,观察时间为10秒正负5秒。(如附图:)
宽度(W)
A面
B面
C面
三级
L≤3mm
W≤0.05 mm
2
3
4
0.05mm<W≤0.1mm
1
2
3
W>0.1mm
0
1
2
3mm<L≤5.0mm
W≤0.05mm
1
2
3
0.05mm<W≤0.1mm
0
1
2
W>0.1mm
0
0
1
L>5.0 mm
W≤0.05mm
0
1
2
0.0
W>0.1mm
不允许接收
三划为轻划痕,不反光时难看出,在某一固定的角度才能看见的划痕。
5.3.1机壳的配合缝、错位通用标准判定
序号
项目
外壳外观检验标准
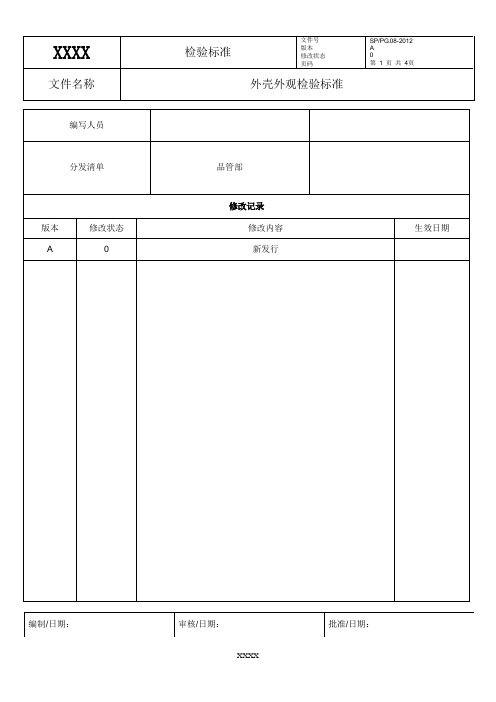
1、目的:经过适当的检验,建立判定标准,以确保产品品质。
2、适用范围:检验规范适用于本公司塑胶外壳产品之检验标准。
3、定义:3.1 测量面定义A面:暴露在外面且在正常使用中可直接看到的主要表面,B面:暴露在外面且在正常使用中不直接看到的次要表面及产品配件的外表面,C面:正常使用时看不到,只能在装卸电池时才可看到的内表面,D面:塑胶壳内部,在正常使用情况下用户看不到的表面。
3.2 缺陷分类定义A. 严重缺陷(CRI.):可能对机器或装备的操作员造成伤害;潜在危险性的效应,会导致与安全有关的失效或不符合政府法规;影响机械或电气性能,产品在组装后或在客户使用时会发生重大品质事件的缺陷。
B. 主要缺陷(MAJ.):性能不能达到预期的目标,但不至于引起危险或不安全现象,导致最终影响使用性能和装配;客户很难接受或存在客户抱怨风险的。
C. 次要缺陷(MIN.):不满足规定的要求但不会影响产品使用功能的;客户不易发现,发现后通过沟通能是客户接受的。
3.3 注塑缺陷不良定义缩水:塑件表面局部由于填充不足或注塑压力不够而形成的凹坑。
熔接线:塑料熔体在型腔中流动时,遇到阻碍物(型芯等物体)时,熔体在绕过阻碍物后不能很好的融合,而在塑料件的表面形成一条明显的线。
顶出痕:由于塑料件的抱紧力,顶杆区域受到顶出力所产生的痕迹或凸起。
破裂:因内应力或机械损伤而造成在塑料件表面上的裂纹。
油渍:在塑料件表面残留的油污。
翘起或变形:塑料件成型时由于受力不均或应力而造成塑料件的变形。
飞边:由于注塑工艺或模具原因,造成在塑料件的边缘分型面处产生的废边。
划痕:由于硬物摩擦而造成塑料件表面现行划伤。
凹凸点:由于模具的损坏等原因造成塑料件表面出现的高低不平。
斑点:在塑料件表面和内部的细微粒和杂质。
3.4装配组件缺陷不良定义段差:装配组合件装配后在接缝处配合面产生的错位。
缝隙:装配组合件装配时的间隙超过标准间隙而产生的缝隙。
变形:由于装配尺寸误差,毛边等原因而造成装配组合件变形现象。
- 1、下载文档前请自行甄别文档内容的完整性,平台不提供额外的编辑、内容补充、找答案等附加服务。
- 2、"仅部分预览"的文档,不可在线预览部分如存在完整性等问题,可反馈申请退款(可完整预览的文档不适用该条件!)。
- 3、如文档侵犯您的权益,请联系客服反馈,我们会尽快为您处理(人工客服工作时间:9:00-18:30)。
塑料壳体检验细则
1. 目的
a. 作为公司采购原材料塑料壳体检验依据
2. 适用范围
b. 适用于本公司所采购塑料壳体的通用检验
3. 抽样计划
c. 依GBT 2828.1,LEVEL I正常检验一次抽样方案;具体抽样方式请参考表1、表2-A
4. 参考文件
d. 相应型号塑料壳体图纸及封样
5. 允收水准(AQL)
e. 严重缺点(CR): 0.4; 主要缺点(MA):2.5; 次要缺点(MI):6
6. 检验标准定义:
序号 检验项目 缺点定义 检验项目 检验方式 检验水平 备注
1 标识 MI
f. 来料报检单、壳体外包装型号标称一致;外包装应规范、整洁,并具有产品标识,
应无破损、污物等不良现象,型号标称与塑料A壳体的型号标识一致;
g. 产品标签清晰,内容应注明物料名称、规格型号、数量、生产日期、产品厂家等标
识;
目测 Ⅱ
按照检验顺序
填写检验记录,全
部评测后判识元
件合格性。
检测结果满足技
术要求的为合格
品,填写《来料检
验单》,并办理入
库,不合格品填写
《不合格品处理
单》。
注意静电防护
2 品相 MI
h. 生产厂家为合格供方,生产批号在12个月以内;
i. 要求丝印字体美观、边缘清晰、整齐,所有文字及图案均丝印符合要求;
j. 按设计文件规定,要求产品配套物件齐全;
k. 凡透明视窗必须有保护膜进行保护;
目测 Ⅱ
3 外观检查 MI
l. 外表面光滑,无明显缺陷,拐角处应过度均匀圆滑,去毛刺、飞边等;
m. 断裂、疮面、塌坑及顶白,不允许;
n. 气泡、缺料、银丝、异色点、流水纹、熔接痕(结合线)、颜色分离、针孔、滋边、
封堵、拉毛及油丝在A面和B面出现是不允许的;而对于有涂层的,漆点、垂流、
皱皮、露底及分界线不清在A面和B面出现是不允许的;C面在不影响装配时,可
以允许轻微缺陷(依限度样板为标准)。
目测(视力1.0,
正常光线目测
3秒左右)
表面定义:
A面:本体或
与其它组件组
Ⅱ
o. 划伤 :A面不允许;B面和C面划伤长度小于15mm,宽度小于0.3mm,累计长度小于25mm,间距大于70mm可以接收。 p. 异常凹凸痕:A面和B面不允许;C面在目视距离500mm以内看不到,且不影响装配时可以接收。 q. 飞边:应该修饰均匀平滑,缺陷不超过分模线0.8mm的,且不影响装配的可以接收。 r. 缩水:依限度样板为标准;允许不影响整机功能的轻微缩水。 s. 变形:曲率为该部分全长的1/500(以水平桌面或玻璃平面为参考面),且组装后不影响外观的轻微变形可接收。 t. 杂料:A面半径0.2mm以下3点以内,点与点的距离50mm以上可允许;B面半径0.3mm以下3点以内,点与点的距离50mm以上可允许;C面径0.5mm以下3点以内,点与点的距离50mm以上可允许。 u. 条纹:A面不允许;B面和C面长度小于15mm,宽度小于2mm,间隔距离大于50mm,总数量小于5个可接收。 v. 油污:A面不允许。B面和C面允许少量的不造成污染的离型剂或顶针油。 w. 烧焦:A面和B面不允许。C面允许与背景颜色差异不甚明显的烧焦色纹。 装成产品后,
可以从外部直
观看见的面;
B面:表底壳底
部外表面及需
要移动检查才
可能看到的
面;
C面:本体或与
其它组件组装
成产品后,在
整个产品内
部,外部无法
直观看见的面
4 尺寸测量与配合 MA x. 随机抽取样品,按照被检测对象相应设计图纸的标注尺寸进行测量,有公差要求的按照要求检验,无公差要求的按照附表1及附表2检验,误差应满足要求; y. 将配件装入壳体相应的位置,应能自如地装上去而且宽松程度符合规定。 z. 对于有嵌件的产品:嵌入件不得凹陷、凸出、熔料不足或孔内有溢料,且要对嵌入件 进行试装(例如:嵌入件是螺纹孔的,孔内必须有螺纹,且要使用配套螺钉进行试装) aa. 对于气表壳体,要求装配好产品后对成品气表进行检测(含老化走字采样、流量误差等); 游标卡尺 螺丝刀 校验台 S-1
5 性能试验 CR bb. 跌落试验:让壳子从2.5m的高度自由落到地面上,壳体应无损伤和破裂; 高低温箱 S-1
cc. 高低温测试:高温70℃ 2小时,低温-20℃~ -25℃ 2小时,试验过后看有没有开
裂、变形;
dd. 使用比设计螺钉直径大0.3毫米左右的螺钉装配,看开裂程度,品质好的应只是发白,
不会开裂;
ee. 使用四氯化碳溶剂滴在受力部位20分钟后观察,受力点看有没有开裂;
8 老化测试 CR
ff. 常用表壳到货数量超过2000只时,(分阶段)每批取样2只放在做好标记。放在室
外做自然老化测试。
老化台 2套
拟制
审核
标记 数量 更改单号 签名 日期 批准
附表1:
基本尺寸(mm)
精 度 等 级
1 2 3 4 5 6 7 8 9 10
公 差 数 值 (mm)
~3
0.02 0.03 0.04 0.06 0.08 0.12 0.16 0.24 0.32 0.48
>3~6
0.03 0.04 0.05 0.07 0.08 0.14 0.18 0.28 0.36 0.56
>6~10
0.03 0.04 0.06 0.08 0.10 0.16 0.20 0.32 0.40 0.64
>10~14
0.03 0.05 0.06 0.09 0.12 0.18 0.22 0.36 0.44 0.72
>14~18
0.04 0.05 0.07 0.10 0.12 0.20 0.24 0.40 0.48 0.80
>18~24
0.04 0.06 0.08 0.11 0.14 0.22 0.28 0.44 0.56 0.88
>24~30
0.05 0.06 0.09 0.12 0.16 0.24 0.32 0.48 0.64 0.96
>30~40
0.05 0.07 0.10 0.13 0.18 0.26 0.36 0.52 0.72 1.0
>40~50
0.06 0.08 0.11 0.14 0.20 0.28 0.40 0.56 0.80 1.2
>50~65
0.06 0.09 0.12 0.16 0.22 0.32 0.46 0.64 0.92 1.4
>65~80
0.07 0.10 0.14 0.19 0.26 0.38 0.52 0.76 1.0 1.6
>80~100
0.08 0.12 0.16 0.22 0.30 0.44 0.60 0.88 1.2 1.8
>100~120
0.09 0.13 0.18 0.25 0.34 0.50 0.68 1.0 1.4 2.0
>120~140
0.10 0.15 0.20 0.28 0.38 0.56 0.76 1.1 1.5 2.2
>140~160
0.12 0.16 0.22 0.31 0.42 0.62 0.84 1.2 1.7 2.4
>160~180
0.13 0.18 0.24 0.34 0.46 0.68 0.92 1.4 1.8 2.7
>180~200
0.14 0.20 0.26 0.37 0.50 0.74 1.0 1.5 2.0 3.0
>200~225
0.15 0.22 0.28 0.41 0.56 0.82 1.1 1.6 2.2 3.3
>225~250
0.16 0.24 0.30 0.45 0.62 0.90 1.2 1.8 2.4 3.6
>250~280
0.18 0.26 0.34 0.50 0.68 1.0 1.3 2.0 2.6 4.0
>280~315
0.20 0.28 0.38 0.55 0.74 1.1 1.4 2.2 2.8 4.4
>315~355
0.22 0.30 0.42 0.60 0.82 1.2 1.6 2.4 3.2 4.8
在图纸上无公差要求又不在附表二中的,自由尺寸建议采用上表的10级精度;对于基准孔,取表中数值冠以(+)号;对于基准轴,冠以(-);对于中心距尺寸
可以取表中数值一半,冠以(±)号。
附表2、塑料件尺寸自由公差精度等级:
材料名称 自由公差精度等级
聚碳酸脂(PC)、聚砜、聚苯醚
聚乙烯类(如PS、AS、ABS等)
聚甲基丙烯酸甲酯(如372、510、613等)
玻璃纤维增强塑料(玻璃纤维含量30%以上)
7
聚酰胺类(如1010、610、9、6、66等),聚氯乙烯(硬)
7
聚丙烯、聚甲醛、醋酸纤维素、聚乙烯(高密度)
8
聚乙烯(低密度)、聚氯乙烯(软)
9
由于各种塑料收缩率变化范围的差别,每种塑料建议按上表选取相应自由公差值。