年产2.8万吨电解槽厂房设计.
铜电解槽设计说明

铜电解槽课程设计电解是从矿石中提取有色金属的主要方法,是大多数有色金属生产的必要工序。
对于铜而言,电解主要有常规电解法、周期反向电流电解法和永久性阴极板电解法。
常规电解法包括阳极加工、始极片生产和制作、装槽、灌液、通电电解、出槽等工序;永久性阴极板电解法包括阳极加工、装槽、灌液、通电电解、出槽、清洗阴极并剥下成品电铜等工序。
铜电解车间的设计一般包括技术经济指标的选择和论证、冶金计算、电解液净化及硫酸盐生产、主要及附属设备计算、车间配置及管理、投资估算、安全,环保与防腐等内容。
完成电解过程使用的主体设备为电解槽,由长方形槽体和附设的供液管、排液斗、出液斗的液面调节堰板等组成。
1 铜电解精炼的方法铜的生产主要视含铜矿石成分及品位而定。
电解分为电解精炼(电解)和电解沉积(电积)。
电解精炼采用可溶性阳极,以火法冶金炼制的粗金属作为阳极进行电解,通过选择性的阳极溶解及阴极沉积,达到分离粗金属中杂质和提纯金属的目的;电解沉积采用不溶性阳极,使经过浸出、净化的电解液中待沉积的金属离子在阴极上还原析出,制得纯金属。
因此,电解精炼是火法冶金工艺提取高纯有色金属的最后精炼工序,而电解沉积则是湿法冶金的最后精炼工序。
目前,在纯铜的生产中,大约有80%的铜采用硫化物矿石通过电解法制取,另有20%的铜采用低品位氧化铜矿通过电积法制取。
(1) 常规电解精炼法常规电解精炼法自19世纪末用于工业生产以来,已成为目前应用最广的一种方法。
在实际生产中,首先是在种板槽中用火法精炼获得的粗铜作为阳极,用钛母板作为阴极,通以一定电流密度的直流电,使阳极铜发生电化学溶解,并在钛母板上析出0.5~1.0mm厚度的纯铜薄片,称为种板。
将其从母板上剥离下来后,经过整平、压纹,再与导电棒、吊耳装配成阴极板(又称始极片),即可作为生产槽所用的阴极,称为阴极板。
然后,将粗铜阳极板和纯铜阴极板相间地装入盛有电解液的生产电解槽内,通入直流电进行电解精炼,铜在阳极上溶解并迁移至阴极进行电沉积,待沉积到一定质量时将其取出,作为电解铜成品。
电解槽安装施工方案
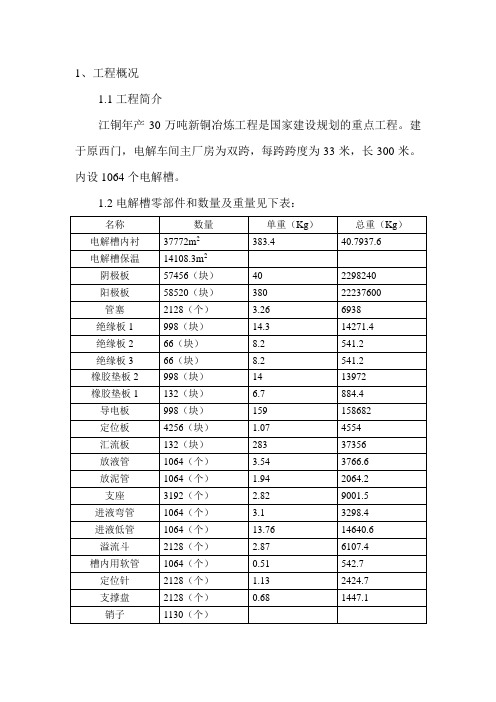
1.1工程简介江铜年产30万吨新铜冶炼工程是国家建设规划的重点工程。
建于原西门,电解车间主厂房为双跨,每跨跨度为33米,长300米。
内设1064个电解槽。
1.2电解槽零部件和数量及重量见下表:2.1施工进度安排(见电解槽安装施工进度计划表)2.2根据安装工程量,配齐所需机具,所配机具要严格检查,不合格的和已损坏的严禁使用。
2.3施工前期准备要求:1)熟悉图纸、编写施工方案,下达技术交底。
2)安装前,行车安装完毕,具备吊装电解槽条件。
3)各种施工机具均应落实到位。
2.4施工程序:主要施工程序如下:基础部分验收基础划线电解槽吊装2.5施工现场准备基础验收必须认真进行,按照有关资料(工艺图、基础图验收标准)根据业主给定的工艺坐标点及标高点,会同业主方,监理方和土建单位,检查基础是否设计及规范要求,应满足表1的规定。
3、基础划线3.1电解槽基础划线①电解槽基础面划出横向中心线。
②电解槽基础面划出纵向中心线。
3.2基础铲麻面电解槽就位前,要将基础铲麻面,并用水冲洗干净。
4、电解槽安装4.1 设备验收电解槽零部件到货后按图分类清点,我方应会同甲方有关部门的现场代表对电解槽零部件组织清点和检查,根据装箱清单和随机文件资料核实零部件,检查零部件合格证,对暂不安装的零部件,应放入仓库保管好,并一一登记,以便查找。
4.2电解槽安装4.2.1电解槽A、B型布置如下表(一)4.2.2电解槽体A、B安装说明4.2.3电解槽安装技术要求:a、安装每个电解槽面纵向和横向的水平误差不得超过1/1000,且必须保证槽间中心距1430mm。
b、槽内极板布置参照“电解槽供电母线正负极方向示意图”。
c、电解槽及定位针和支撑盘定位要求参照“电解槽定位针和支撑盘位置示意图。
安装电解槽及定位针和支撑盘一定要达到图中所示的各尺寸要求,每个槽的定位板高度误差不大于3mm.d、电解槽定位板焊接定位后,表面与槽内衬同时做厚4mmFRP,要求均匀平整。
电解槽设计模版范文

电解槽设计模版范文一、引言电解槽作为重要的工业设备之一,在电化学过程中扮演着至关重要的角色。
良好的电解槽设计可以提高电化学反应效率,降低能耗,提高产品质量。
本文将基于电解槽的国内外研究成果,提出一种电解槽设计模版,用于指导电解槽设计过程。
二、电解槽设计模版1.控制要求:(1)电解槽要满足电解质与电极的反应要求,保证反应正常进行。
(2)电解槽要有合适的温度控制机制,以保证反应的温度在可控范围内。
(3)电解槽要有稳定的电力供应,以保证电化学反应持续进行。
2.电解槽结构:(1)电解槽结构要合理,能够容纳电解质和电极,并提供充分的反应表面积。
(2)电解槽结构要具备良好的材料耐腐蚀性能,以承受电解质的腐蚀。
(3)电解槽要有充分的流体动力学设计,以促进反应物的迅速扩散和产物的快速分离。
3.电解槽操作:(1)电解槽操作要简便,易于维护。
(2)电解槽操作要考虑人员的安全以及环境保护措施。
(3)电解槽操作要有合理的自动化设备,以提高生产效率。
4.实验条件:(1)电解槽的操作温度、电流密度以及电解质浓度等要有明确的实验条件。
(2)应根据实际需要选择适当的电极材料、电解质种类和浓度等。
(3)应有一定规范的操作步骤,以保证实验过程的准确性和可复制性。
5.安全与环保:(1)电解槽要提供有效的安全保护措施,以防止人员因意外事故而受伤。
(2)电解槽要有合理的废物处理系统,以减少环境污染。
(3)电解槽要遵守国家和地方的环保法规,以确保生产过程不对周围环境造成污染。
三、结论本文提出了一个电解槽设计模版,包括控制要求、电解槽结构、电解槽操作、实验条件以及安全与环保等几个方面。
这些都是电解槽设计过程中需要考虑的重要因素,通过合理的设计和操作,可以提高电解槽的效率和安全性,从而提高产品质量和降低能耗。
未来的研究可以进一步完善电解槽设计模版,以应对不同类型的电化学反应需求。
5、电解槽安装施工方案

1、工程概况8万吨/年离子膜烧碱装置,电解槽是离子膜烧碱装置的核心设备,本次工程数量共6台,安装在电解单元的专用电解槽厂房内。
电解槽采用,电解槽中,通直流电,在阴极(鲆丝网)和阳极(钛网)上发生电化学反应生成主产物碱液和副产物氢气、氯气,碱液经蒸发、干燥、精制后,制得烧碱。
副产物氢气和氯气经冷却、压缩、干燥等处理后生成高纯盐酸和液氯等产品。
由于电解槽设备安装按照施工图纸和设备的随机技术资料,本方案仅对设备安装的一般要求作简要阐述,待以后根据装配图纸、随机资料和施工现场条件要求进行详细编制,以指导现场实际安装施工。
2、安装施工程序3、施工准备3.1 所有施工人员应熟悉电解槽安装技术资料,包括设备制造装配图及零部件图、设备安装说明性文件、专用工具使用说明书、工艺安装图、设备装箱单及合格证等。
3.2对设备安装所需手段用料、辅助材料、施工机具、车辆等进行预先准备。
3.3每一步工序施工前都要组织有关管理人员(技术、质量、安全)对所有施工作业人员进行技术交底,使作业人员对工程的情况、施工的程序和要求有全面深入的了解,同时也了解本设备安装的质量、安全方面的要求。
4、基础验收及处理4.1基础验收的条件基础验收应会同建设单位、监理单位、土建施工和安装各专业技术负责人及施工班组联合进行。
基础验收应具备的条件如下:●土建施工专业已提交基础实测记录和必要的竣工图、说明及质量证明文件;●基础混凝土强度达到设计强度的75%以上;●基础表面和地脚螺栓预留孔中的油污、碎石、泥土、积水等均清除干净;●基础上明显标出标高基准线和纵横中心线;●必要的检测器具按要求准备齐全4.2 基础验收标准●基础表面应清理干净,无裂纹、蜂窝、空洞、露筋等缺陷,预留地脚螺栓孔洞内无杂物积水;●按土建图纸及设备随机技术文件要求,对基础的尺寸及位置进行检查,其允许偏差符合规范及标准要求。
超出允许偏差的要进行修整处理.4.3 基础处理●在距基础表面100mm标高处划线,并在地脚螺栓预留孔两旁合适位置凿去适当高度的基础,准备规格为220*110*19的平垫铁,采用座浆法用无收缩速干性水泥砂浆座浆垫铁,恢复到原有基础标高。
某电解铝生产车间规划设计报告

某电解铝生产车间规划设计报告摘要大型化是当今世界铝电解技术发展的大趋势。
在现有的320kA~350kA大型铝电解槽基础上,进一步开发并建设高效、稳定和更为节能的400kA大型铝电解槽技术是当今世界各大铝业公司研究和追求的目标。
并且我国已经有多家铝电解企业已经建成400kA级铝电解生产线。
我们紧随时代步伐,设计了400kA预焙槽铝电解车间。
车间设计包括厂址选择、电解槽设计、电压平衡、能量平衡劳动定员及成本核算等。
该设计的年产量为22万吨,电流效率高达94%。
经过多方论证厂址选择伊川县工业园区。
前言自上世纪80年代以来,我国电解铝技术取得了很大的发展,尤其在大型预焙铝电解槽的设计技术、制造技术、生产技术等领域形成了自己的大型铝电解技术体系,开发成功了300kA~400kA大型铝电解槽。
先进的300kA~350kA大型预焙槽及其配套技术得到了广泛应用,从而减少了能量消耗和环境污染,但与国外先进电解槽相比较,我国电解槽在设计、制作、电解槽单位面积产铝量及吨铝直流电耗等方面还存在一定差距[1]。
我国自主研发的400kA级大型预焙阳极铝电解槽技术,于08年由中国铝业兰州分公司、沈阳铝镁设计研究院研制开发获得成功。
并与2008年3月21日通过了由中国有色金属工业协会组织的科学技术成果鉴定。
现安装于中国铝业兰州分公司SY400电解槽[2],技术指标先进,同比350kA,300kA电解槽具备投资省,经济效益高的特点,能够满足建设技术起点高、装备先进、大规模的铝电解系列,单系列产能超过320kt/a以上,为中国铝工业的国际化奠定坚实的基础。
同时SY400电解技术具备是世界领先水平的电解技术,是当前世界系列生产电流强度最大,单槽产量最大,综合指标最先进并具有自主知识产权的铝电解槽。
与之前的300kA和350kA级的电解槽相比,400kA级大型预焙阳极铝电解槽技术具有以下创新点:1、优化设计了合理的母线配置,提高了大型槽磁流体稳定性;2、采用5段上烟道结构设计,有利于提高集气效率和改善环境;3、采用电解厂房通风和电解槽整体热平衡相结合、摇篮架与槽壳整体焊接、槽壳外部焊接散热片、电解槽小面采用摇篮架与槽壳焊接、电解槽槽壳和内衬整体位于操作面下等技术,保证了大型电解槽的热稳定性,改善了劳动环境;4、采用阴极炭块与阳极炭块投影相对应的技术,有利于阳极和阴极的电流分布均匀;5、采用了电解槽全面控制和标准化操作体系,有效控制电解槽热平衡与物料平衡,开发了适应大型槽稳定、安全的焙烧启动技术,形成了400kA电解槽生产操作管理技术;6、采用四种不同品质阴极炭块进行工业试验,均达到了400kA电解槽试验目标。
电解槽正常生产的主要技术参数

电解槽正常生产的主要技术参数电解槽是一种用于电解反应的装置,主要用于电解制取金属或化学品。
电解槽的主要技术参数决定了电解反应的效率和产品质量。
下面将介绍电解槽正常生产的主要技术参数。
1.电解槽尺寸:电解槽的尺寸是影响电解反应效率的重要因素。
通常来说,电解槽的大小应根据生产需要进行设计,使得电流分布均匀,电解产物得以充分沉积。
电解槽尺寸的设计要考虑电解物质的浓度、溶液的流动性以及产物颗粒的沉积特性等因素。
2.电解槽材质:电解槽的材质选择直接影响到电解反应的效果和电解槽的使用寿命。
常用的电解槽材质有钢、铁、铝、钛、铅等。
不同材质对电解物质的耐蚀性和传热性能有差异,因此需要根据具体的工艺要求选择合适的材质。
3.电解液组成:电解槽正常生产的另一个重要技术参数是电解液的组成。
电解液一般由溶剂和溶质组成,溶剂可以是纯水或其他溶液,溶质通常是需要电解的金属离子或化学物质。
电解液的组成要根据具体的电解反应选择合适的浓度和比例,以确保电解反应的高效进行。
4.电解槽温度:电解槽温度是影响电解反应速度和产物质量的重要因素。
温度过高会导致电解液的蒸发和损失,温度过低会降低离子迁移速率。
因此,要根据电解反应的需求,根据具体情况选择合适的温度。
5.电流密度:电流密度是电解槽正常生产中的另一个重要技术参数。
电流密度的大小决定着电解反应速度和电解产物的质量。
高电流密度会导致电解槽温升过高,产物的颗粒过细,而低电流密度则会导致电解反应速度缓慢。
因此,需要根据具体工艺要求选择合适的电流密度。
6.搅拌方式:7.支架结构:电解槽的支架结构也是正常生产的关键技术参数之一、支架结构需要具备足够的强度和稳定性,以保证电解槽在长时间运行过程中不发生变形或破裂。
支架结构还需要考虑电解槽的便于操作和维修。
总之,电解槽正常生产的主要技术参数包括电解槽尺寸、材质、电解液组成、温度、电流密度、搅拌方式和支架结构等。
这些技术参数的选择和调整将直接影响到电解反应的效率和产品的质量。
铜电解车间设计

前言同时人类历史上发现的最早的金属,约一万年前,人们就已经将统计工程为各种生活用品和生产用具。
到现在,世界上生产痛的方法主要分火法炼铜,湿法炼铜。
火法炼铜是指在高温炉中进行的痛的冶炼过程,而湿法是在常温或者是在一百摄氏度左右进行的冶金过程。
经过活法和湿法得到的铜主要是得到可以进行电解精炼的阳极铜。
铜电解精炼工艺1869年首次在工业上应用,阳极使用粗铜板,阴极使用始极片电解生产阴极铜的电解精炼工艺称为传统法。
在随后的一百多年的发展历程中其基本原则和理论并没有发生多大的变化,而在围绕提高技术装备水平、扩大生产规模提高阴极铜质量、降低能耗和人工消耗等方面,则有了巨大的进步,这种进步在近几十年间尤为显著。
直到1978年PLY铜精炼有限公司汤斯维尔铜电解精炼厂使用永久性不锈钢阴极板替代传统工艺使用的铜始极片,阴极铜产品由自动剥片机上剥取的方法就是后来的ISA法铜电解技术。
ISA法和传统法相比,其最大的优点是减少了始极片的生产工序,降低了生产车间的投资成本,减少了日常维护费用,生产作业的周期也大为缩短,能够持续生产高质量的阴极铜,可以说ISA法铜电解技术是传统法的突破性发展。
本设计根据毕业设计任务书的要求在综合比较各种铜电解工艺的基础上做出最终的设计方案,设计采用ISA法新工艺,对铜精矿的选取、备料、熔炼、阳极浇铸等工艺进行了一般性的论述。
本次设计的重点是电解车间工艺的初步设计,其中包括工艺流程的选择、设备的选型、定员、技术经济核算等方面。
设计中采用的主要参数和指标是以贵溪冶炼厂电解工艺的参数为基准,使设计理论更合理,更符合实际工厂生产的需要。
文献综述1.1铜1.1.1铜的性质铜属第四周期第一副族元素。
原子序数29,原子量63.57,密度为8.89g/cm-3(20℃),熔点1083℃,沸点2310℃。
铜是一种玫瑰红色、柔软、具有较高的导电性、传热性、延展性、抗拉性和耐腐蚀性的金属。
铜易于锻造和压延,能拉成很细的铜丝,能压成0.0026mm厚的铜箔;在金属中铜的导电性仅次于银。
年产万吨电铜电解车间的设计

01
02
03
原料来源
确保电解铜原料的供应稳 定,选择可靠的供应商, 并建立长期合作关系。
原料储存
设计合理的原料仓库,确 保原料的储存安全,防止 潮湿、氧化和污染。
原料检验
对进厂的原料进行质量检 验,确保原料的质量符合 生产要求。
电解过程
电解液制备
根据生产需要,配制适当 浓度的电解液,保证电解 过程的顺利进行。
放路径。
废水回用
考虑将处理后的废水进行回用 ,以减少生产过程中的用水量
。
CHAPTER
03
电解车间设备选型与布局
设备选型
电解槽
选择适合电铜生产的电解槽,确 保电解液循环流畅,电流效率高
。
电源设备
根据电解槽数量和生产需求,选择 合适的电源设备,如整流器或直流 电源。
辅助设备
包括循环水系统、冷却系统、通风 系统等,确保设备正常运行和环境 保护。
设备布局
流程顺序
按照电解铜的生产流程,合理安排设备布局,确 保物料流动顺畅。
空间利用
充分利用车间空间,合理规划设备间距和高度, 提高空间利用率。
安全间距
确保设备之间留有足够的安全间距,防止事故发 生。
设备安装与维护
安装规范
遵循设备制造商提供的安装规范,确保设备安装牢固、准确。
调试与试运行
对安装完成的设备进行调试和试运行,确保设备性能达标。
辅助设施
包括供电、供水、供气等设施的建设费用,以及环保设施、安全设 施等的投资。
成本分析
直接材料成本
根据生产工艺要求,计算每吨 电铜所需的原材料、辅助材料
等费用。
人工成本
根据生产规模和工艺要求,确 定所需员工数量和相应的人工 费用。
- 1、下载文档前请自行甄别文档内容的完整性,平台不提供额外的编辑、内容补充、找答案等附加服务。
- 2、"仅部分预览"的文档,不可在线预览部分如存在完整性等问题,可反馈申请退款(可完整预览的文档不适用该条件!)。
- 3、如文档侵犯您的权益,请联系客服反馈,我们会尽快为您处理(人工客服工作时间:9:00-18:30)。
东北大学有色冶金课程设计(铜电解)题目:年产2.8万吨铜电解车间设计班级:冶金工程1103姓名:马林林学号:20110075目录1.概述 ............................................................................................. - 3 -1.1电解精炼的目的和任务................................................................................................ - 3 -1.2电铜的质量标准............................................................................................................ - 3 -1.2.1高纯阴极铜(Cu-CATH-1)化学成分.................................................................. - 3 -1.2.2一号铜化学成分的质量分数............................................................................. - 4 -1.3铜电解一般工艺流程.................................................................................................... - 4 -2.冶金计算..................................................................................... - 5 -2.1已知条件........................................................................................................................ - 5 -2.2 计算............................................................................................................................... - 5 -3.主体设备设计............................................................................. - 7 -3.1电解槽材质与结构........................................................................................................ - 7 -3.2商品电解槽总数............................................................................................................ - 8 -3.3电解槽的极板数............................................................................................................ - 8 -3.4电解槽尺寸的确定........................................................................................................ - 9 -3.5种板电解槽数................................................................................................................ - 9 -3.6净液量及脱铜槽数...................................................................................................... - 10 -3.6.1净液量............................................................................................................... - 10 -3.6.2脱铜槽数........................................................................................................... - 11 -3.7槽边导电排、槽间导电板和阴极导电棒的选择与计算.......................................... - 11 -3.7.1槽边导电排....................................................................................................... - 11 -3.7.2 槽间导电板...................................................................................................... - 12 -3.7.3 阴极导电棒...................................................................................................... - 12 -3.8设计总结........................................................................................................................ - 9 -4.图纸 ........................................................................................... - 12 -5.参考文献................................................................................... - 12 -1.概述1.1电解精炼的目的和任务火法精炼产出的阳极铜中Cu的质量分数一般为99.2%~99.7%,其中还有一定数量的杂质。
这些杂质的存在会使铜的某些物理性质和机械性能变坏,因此,为了提高铜的性能,使其达到各种应用的要求,同时回收其中的有价金属,尤其是贵金属和稀散金属,必须进行电解精炼。
电解精炼是以火法精炼产出的阳极板为阳极,以电解产出的薄铜片(始极片)为阴极,以硫酸铜和硫酸的水溶液为电解液,在直流电的作用下,阳极铜电化学溶解,溶液中铜离子在阴极上析出。
1.2电铜的质量标准阴极铜按化学成分分为高纯阴极铜(Cu-CATH-1)和标准阴极铜(Cu-CATH-2)两个牌号。
1.2.1高纯阴极铜(Cu-CATH-1)化学成分表1 高纯阴极铜(Cu-CATH-1)化学成分%1.2.2一号铜化学成分的质量分数电解精炼的产品是电铜(即阴极铜),其标准见表2。
1.3铜电解一般工艺流程酸铜精炼酸镍精炼铜电解精炼一般工艺流程图2.冶金计算2.1已知条件年产电解铜2.8万吨电流效率:96%残极率:16%铜电解回收率:99.9%年工作日:360d日通电时数:24h电解槽作业率:95%每片阴极面积:0.77×0.74×2m2电流强度:10000A阳极成分及电解过程中各元素的分配率见表3和表4表3 阳极成分元素Cu Ni Pb As Sb Bi Zn Fe Sn O Au Ag99.38 0.08 0.13 0.016 0.04 0.003 0.001 0.004 0.001 0.02 0.003 0.085 含量/%表4 电解过程中各元素的分配率元素进入溶液/% 进入阳极泥/% 进入阴极/%Cu 1.93 0.07 98Ni 89.5 10 0.4Pb —96.5 3.5As 63 30 7Sb 25 65 10Bi 15 80 5Zn 93 4 3Fe 72 10 18Sn 5 85 10O —100 —Au —99 1Ag —98 22.2计算根据以上数据计算出阳极泥率,阳极泥成分,电铜成分,最后编制出铜电解精炼物料平衡表。
表5阳极率和阳极泥成分计算元素 进入阳极泥的量占阳极溶解量的百分数/%阳极泥成分/%Cu 99.38×0.0007=0.069566 20.24 Ni 0.08×0.10=0.008 2.33 Pb 0.13×0.095=0.12545 36.49 As 0.016×0.3=0.0048 1.40 Sb 0.04×0.65=0.026 7.56 Bi 0.003×0.80=0.0024 0.70 Zn 0.001×0.04=0.00004 0.01 Fe 0.004×0.10=0.0004 0.12 Sn 0.001×0.85=0.00085 0.25 O 0.02×1.0=0.02 5.82 Au 0.003×0.99=0.00297 0.86 Ag 0.085×0.98=0.083324.23 阳极泥率 0.343776100.00表6阴极铜成分计算元素 阴极析出量占阳极溶解量的百分数/%阴极铜成分 Cu 99.38×0.98=97.3924 99.98694 Ni 0.08×0.004=0.00032 0.00033 Pb 0.13×0.035=0.00455 0.00467 As 0.016×0.07=0.00112 0.00115 Sb 0.04×0.10=0.004 0.00411 Bi 0.003×0.05=0.00015 0.00015 Zn 0.001×0.03=0.00003 0.00003 Fe 0.004×0.18=0.00072 0.00074 Sn 0.001×0.10=0.0001 0.00010 Au 0.003×0.01=0.00003 0.00003 Ag 0.085×0.02=0.001700.00175 合计97.40512100 根据以上有关数据,进行物料平衡计算如下28000t 电铜中的含铜量 28000×99.98694%=27996.343t生产28000t 电铜所需铜量 27996.343/99.9%(铜电解回收率)=28024.368t 生产28000t 电铜要进入阳极泥中的铜量 %98343.27996×0.07%=19.997t阳极泥量 19.997/20.24%=98.801t 生产28000t 电铜要进入溶液中的铜量%98343.27996×1.93%=551.357t生产28000t 电铜所需阳极数量%38.99%161357.551997.19368.28024⨯-++)(=34254.907t阳极含铜量 34254.907×99.38%=34042.527t 残极数量 34254.907×16%=5480.785t 残极含铜量 5480.785×99.38%=5446.804t 用上述结果编制物料平衡表如下 表7铜电解精炼物料平衡表进料物料名称数量/t铜含量/% 纯铜量/t 铜阳极 34254.90799.38 34042.527 合计34042.527出料物料名称 数量/t 铜含量/% 纯铜量/t 阴极铜 28000 99.98694 27996.343 残极 5480.785 99.38 5446.804 阳极泥 98.801 20.24 19.997 电解液 551.357 损失 28.026 合计34042.5273.主体设备设计3.1电解槽材质与结构本电解槽的材质以钢筋混凝土为槽体,采用耐酸、耐高温性能好的铅板作内衬。