制药企业-质量风险评估表
药品生产企业风险评估指南

药品生产企业风险评估指南
1概述
(1)适用人群:该评估指南可供安全监管/行业主管部门安全监管专职人员,安全责任主体单位(企业的安全监管等岗位的人员),以及安全管理系统的研发人员参考使用。
(2)编制思路:本指南在进行药品生产企业风险识别中,从生产设备及产品本身、生产过程和管理因素三个方面进行评价。
着重考虑原材料自身因素及生产过程所涉及的可能风险。
通过分析影响药品生产企业安全的各个影响因素,设置各项总分数,在表格中对各项不同内容进行打分。
(3)评分规则:本指南评估采用100分制,根据打分结果按照风险从高到低依次分为红色(85分以上)、橙色(75至85分以下)、黄色(55至75分以下)、蓝色(55分及以下)四个等级。
(4)引用文件(凡未注日期的引用文件,其最新版本适用于本文件):
《关于进一步加强药品生产工作的通知》(粤食药监安〔2011〕9号)
《危险化学品生产储存企业安全风险评估诊断分级指南(试行)》(应急〔2018〕19号)
《危险化学品重大危险源辨识》(GB18218-2018)
《食品药品监管总局关于印发药品生产现场检查风险评定指导原则的通知》(食药监药化监〔2014〕53号)
《中华人民共和国特种设备安全法》(中华人民共和国主席令第四号)
《广东省应急管理厅关于安全风险分级管控办法(试行)》(粤应急规〔2019〕1号)
2评价指标
风险主要指标以及权重见下表:
表药品生产企业风险评价指标及评分标准。
验证和确认的质量风险评估表

验证和确认的范围质量风险评估××××制药有限公司验证和确认范围质量风险评估1.概念:1.1质量风险:指质量危害出现的可能性和严重性的结合。
2.3、风险矩阵图危害发生的可能性(F)启动风险管理过程质量风险管理程序的输出/结果4风险评估方法4.1 风险识别:可能影响产品质量、产量、工艺操作或数据完整性的风险;4.2 风险分析:本案例应用失败模式效果分析,识别潜在的失败模式,对风险发生的频率、严重性和可测量性评分。
4.3 风险判定:包括评估先前确认风险的后果,其基础建立在严重程度、可能性及可检测性上;4.3.1 严重程度(S):测定风险的潜在后果,主要针对可能危害产品质量、患者健康及数据完整性的影响。
严重程度分为四个等级:4.3.2 可能性程度(P):测定风险产生的可能性。
根据积累的经验、工艺/操作复杂性知识或小组提供的其他目标数据,可获得可能性的数值。
为建立统一基线,建立以下等级:4.3.3 可检测性(D):在潜在风险造成危害前,检测发现的可能性,定义如下:RPN(风险优先系数)计算:将各不同因素相乘;严重程度、可能性及可检测性,可获得风险系数( RPN = SPD )RPN > 16 或严重程度= 4高风险水平:此为不可接受风险。
必须尽快采用控制措施,通过提高可检测性及降低风险产生的可能性来降低最终风险水平。
验证应先集中于确认已采用控制措施且持续执行。
严重程度为4时,导致的高风险水平,必须将其降低至RPN最大等于816 ≥RPN ≥8中等风险水平:此风险要求采用控制措施,通过提高可检测性及(或)降低风险产生的可能性来降低最终风险水平。
所采用的措施可以是规程或技术措施,但均应经过验证。
RPN ≤7低风险水平:此风险水平为可接受,无需采用额外的控制措施。
质量风险评估表-可编辑-附件2 验证和确认的质量风险评估。
GMP-风险评估
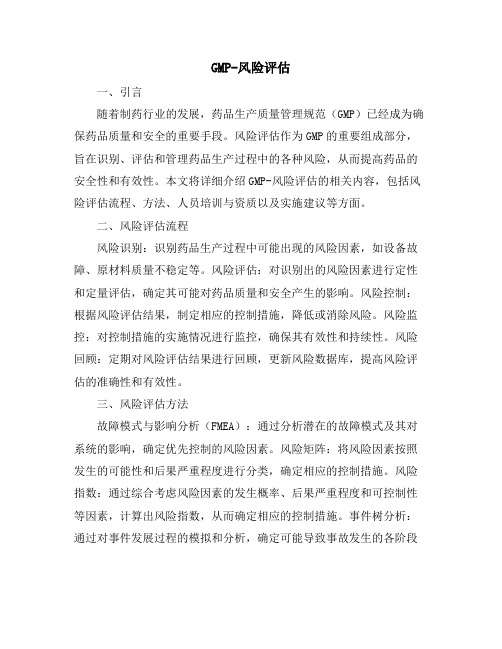
GMP-风险评估一、引言随着制药行业的发展,药品生产质量管理规范(GMP)已经成为确保药品质量和安全的重要手段。
风险评估作为GMP的重要组成部分,旨在识别、评估和管理药品生产过程中的各种风险,从而提高药品的安全性和有效性。
本文将详细介绍GMP-风险评估的相关内容,包括风险评估流程、方法、人员培训与资质以及实施建议等方面。
二、风险评估流程风险识别:识别药品生产过程中可能出现的风险因素,如设备故障、原材料质量不稳定等。
风险评估:对识别出的风险因素进行定性和定量评估,确定其可能对药品质量和安全产生的影响。
风险控制:根据风险评估结果,制定相应的控制措施,降低或消除风险。
风险监控:对控制措施的实施情况进行监控,确保其有效性和持续性。
风险回顾:定期对风险评估结果进行回顾,更新风险数据库,提高风险评估的准确性和有效性。
三、风险评估方法故障模式与影响分析(FMEA):通过分析潜在的故障模式及其对系统的影响,确定优先控制的风险因素。
风险矩阵:将风险因素按照发生的可能性和后果严重程度进行分类,确定相应的控制措施。
风险指数:通过综合考虑风险因素的发生概率、后果严重程度和可控制性等因素,计算出风险指数,从而确定相应的控制措施。
事件树分析:通过对事件发展过程的模拟和分析,确定可能导致事故发生的各阶段和因素,制定相应的预防措施。
故障树分析:通过分析系统故障的逻辑关系,找出导致故障的原因和因素,制定相应的预防措施。
四、人员培训与资质培训内容:培训员工GMP-风险评估的相关知识和技能,包括但不限于风险评估流程、方法以及相关的管理工具和软件等。
培训形式:采用线上和线下相结合的方式进行培训,包括理论授课、案例分析、实践操作等形式。
资质要求:参与GMP-风险评估的人员应具备相应的专业知识和经验,具备相应的资质证书或经过专业培训。
培训考核:对参与培训的人员进行考核,确保其掌握相关的知识和技能,符合要求的人员可参与GMP-风险评估工作。
质量风险评估

质量风险评估工艺参数关键性评估报告产品名称或者项目名称:产品代号:产品阶段:工艺关键性评估小组成员:研发/技术:生产:QC:QA:评估日期:报告起草(签名/日期):审核(签名/日期):批准(签名/日期):基本定义和方法1、基本定义与概念2、评估流程五步法评估关键工艺参数1)筛选产品与工艺相关的关键质量属性2)筛选影响与工艺相关的关键质量属性的工艺步骤3)筛选影响CQA的工艺参数4)结合工艺参数范围进行风险评估确定工艺参数的内在关键性5)结合控制措施进行风险控制确定工艺参数最终关键性3、风险等级与风险矩阵3.2 风险等级3.3 严重性和可能性矩阵(风险等级)风险等级 严 高 重 中 性 低低 中 高 可能性 内在关键性 严 高 重 中 性 低低 中 高 可能性3.5 可检测性和内在关键性矩阵(风险优先级和关键性判断)风险优先级 可 高 检 中 测 低低 中 高 风险等级 最终关键性 可 高 检 中 测 低非关键 潜在关键 关键内在关键性4.评估报告所需的相关文件产品质量属性评估表1—影响工艺步骤评估质量属性:根据产品质量指标填写智力属性,如外观,溶解度,鉴别,杂质,颗粒度,pH值影响因素:影响质量属性的因素:工艺,物料,GMP或者它们的组合工艺:判断该工艺步骤是否对前面列举的质量属性有影响,选项为有或无工艺步骤号和工艺步骤,如精制步骤,粗品步骤,打粉步骤等,在步骤号加上编号理由或备注:工艺步骤对质量属性影响的理由或者其他备注产品质量属性评估表2—工艺参数影响评估步骤编号:单元操作或步骤编号,结合前表的工艺步骤编号,按照1.1,1.2….2.1,2.2,2.3…顺序编号单元操作或步骤描述:单元操作或步骤描述,如原料投料,加热到反应温度,添加试剂,反应,萃取,结晶,过滤和洗涤,烘干,出料等工艺参数编号,按照1,2,3….顺序编号工艺中的参数,如温度,数量,数量比,浓度,收率,反应时间,投料时间,停留时间,压力,PH,搅拌速度,等对关键质量属性的影响程度;按照后面的分析来判断该工艺参数对关键质量属性的影响程度,分为高,中,低无四个等级。
药品质量风险评估表
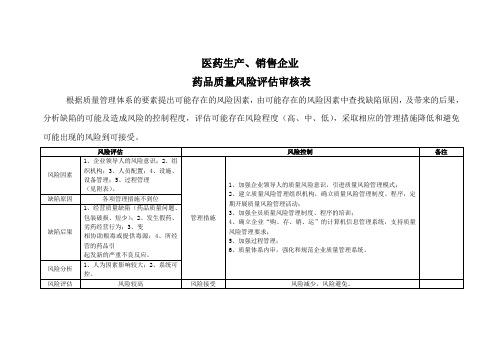
1、药监系统发布假劣药信息遗漏或反馈不及时、未及时启动应急预案;2、质量信息反馈延误;3、药品不良反应信息收集不主动;4、各类质量信息收集不全面,未做汇总分析;5、未及时启动应急预案(药品召回、质量事故调查)。
缺陷后果
1、信息遗漏或反馈延误,造成致死致残个案;2、信息,造成使用假药、劣药;3、信息遗漏或反馈延误,使用药品质量缺陷药品。
缺陷原因
1、收货人人员未凭《药品退货复检单》进行审核退货;2、退货保管员未核实是否由本公司库房发出;3、抽样不到位;4、销后退回检查验收不到位(冷链保存药品退货未判定验收不合格);5、药监部门确认的假劣药品不能执行药品购进退出,确认的假劣药品再次销售;6、召回药品未经质量审核确认重新出库。
缺陷后果
1、销后退回验收合格假药劣药(受污染、变质、失效);2、销后退回验收药品质量缺陷(外观质量问题,包装破损、短少,严重不良反应等)药品;3、假药、劣药再次出库销售。
缺陷后果
1、储存不当,造成药品污染、变质、失效(温湿度影响),成为假、劣药品;2、储存药品过期失效成为劣药;3、储存药品发生质量缺陷(储存造成外观质量问题、包装破损、短少等)药品;4、药品储存批号、数量差错。
风险分析
1、人为因素影响较大;2、系统可控;3、仓库设施、设备更新提高
风险评估
风险高,储存环节保持药品质量稳定是药品经营企业最重要的质量管理环节,其中温湿度控制是关键,直接影响药品质量(特别是冷藏药品温度控制)
缺陷后果
1、验收不合格的假药(受污染等)或劣药;2、验收合格药品质量缺陷(外观质量问题、包装破损、短少等)药品;3、验收延误(冷链药品),造成药品质量缺陷(内在质量)、药品失效
风险分析
1、人为因素影响较大;2、系统可控
企业制药有限公司风险评估报告
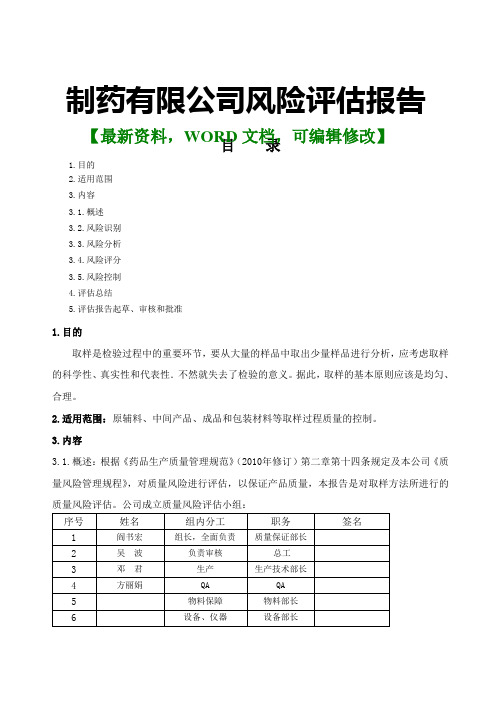
目 录1.目的2.适用范围3.内容 3.1.概述 3.2.风险识别 3.3.风险分析 3.4.风险评分 3.5.风险控制 4.评估总结5.评估报告起草、审核和批准1.目的取样是检验过程中的重要环节,要从大量的样品中取出少量样品进行分析,应考虑取样的科学性、真实性和代表性.不然就失去了检验的意义。
据此,取样的基本原则应该是均匀、合理。
2.适用范围:原辅料、中间产品、成品和包装材料等取样过程质量的控制。
3.内容3.1.概述:根据《药品生产质量管理规范》(2010年修订)第二章第十四条规定及本公司《质量风险管理规程》,对质量风险进行评估,以保证产品质量,本报告是对取样方法所进行的质量风险评估。
公司成立质量风险评估小组:制药有限公司风险评估报告【最新资料,WORD 文档,可编辑修改】3.2.风险识别3.2.1我公司已制定有取样管理制度和取样操作程序,依据风险评估找出制度和程序中潜在的给产品带来的危险,以修订和完善制度和程序,为降低检验风险提供基本的保障。
3.2.2采用头脑风暴法,由风险评估管理小组开展风险调查,召集物料部、质量保证部、生产技术部有经验的管理人员和技术人员,分别列出取样过程中可能出现和容易出现的风险点,见表一:表一3.3.风险分析依据以往经验进行风险分析,找出风险发生的原因,分析风险发生的可能性、严重性、可检测性,见表二。
表二3.4.风险评分3.4.1 采用ICH Q9推荐的方法FMEA(失效模式及效应分析)进行风险评估和管理。
3.4.2 风险RPN值=风险发生的可能性(P)×严重性(S)×可检测性(D)接受标准RPN值≤83.4.3评分标准表3.4.4 根据以上评分标准,对表2列出的各项风险因素进行打分,见表二。
3.5.风险控制3.5.1风险控制是对风险项提出防止和减轻的控制措施,并对剩余风险进行评估,见表三。
表三3.5.2根据风险因素FMEA表所示,总结风险防控措施如下:3.5.2.1取样管理制度、取样操作规程制定不完善,导致取样漏洞的控制措施:完善取样管理制度、取样操作规程,做到方法科学、程序不漏、可操作性强。
药品生产过程质量风险评估报告模板
药品生产过程质量风险评估报告模板药品生产过程质量风险评估报告模板XXXX胶囊生产过程质量风险管理报告起草人:审核人:审核人:批准人:质量风险管理号:QRM- 起草日期:审核日期:审核日期:批准日期:XXXX药业有限公司年月年月年月年月日日日日目录XXXX胶囊生产过程质量风险管理报告1、简介2、目的3、范围4、引用资料5、风险管理小组组员及职责分工6、质量风险管理流程7、风险管理过程8、风险管理总结及结论9、风险管理回顾审核XXXX胶囊生产过程质量风险管理报告1.简介:1.1产品概述:XXXX胶囊为以化学原料药XXXX和适量等辅料制成的化学药胶囊剂制剂,为耳鼻喉科及皮肤科用药类非处方药药品。
用于缓解过敏性鼻炎有关的症状,如喷嚏、流涕、鼻痒、鼻塞以及眼部痒及灼烧感。
口服药物后,鼻和眼部症状及体征得以迅速缓解。
亦适用于缓解慢性荨麻疹、瘙痒性皮肤病及其他过敏性皮肤病的症状和体征。
规格为10 毫克;贮藏:遮光,密闭保存;包装:铝塑泡罩包装。
每板6粒,每盒1板;每板6粒,每盒2板;每板12粒,每盒1板,每板4粒,每盒1板。
有效期:30个月。
1.2生产批量:35万粒,140万粒。
1.3主要生产工艺过程及参数:,混合速度900转/分,混合时间20分钟;批量为140万粒的预混合和35万粒相同,但原辅料均分4等分进行4次混合。
1.3.3 粘合剂15%聚维酮K30的乙醇溶液的配制:按聚维酮K30:95%乙醇量=1.5:8.5(重量比)进行配置,溶解完全100目滤布过滤。
,用GHL-250型高效混合制粒机中(每次35万粒量),设定混合I和切割I开动设备混合10分钟后,徐徐加入粘合剂(15%聚维酮K30的乙醇溶液),加完后继续混合3-4分钟,收集软材。
,筛网目数为24目。
,每次干燥量为35万粒胶囊的颗粒量,控制干燥温度为50℃~70℃,干燥时间20分钟。
,筛网目数为24目。
,混合速度900转/分,混合时间20分钟;批量为140万粒的总混:用EYH-1000型二维运动混合机进行,混合时间35分钟(此设备无速度调节)。
药品质量风险评估表
1、验收不合格的假药(受污染等)或劣药;2、验收合格药品质量缺陷(外观质量问题、包装破损、短少等)药品;3、验收延误(冷链药品),造成药品质量缺陷(内在质量)、药品失效
风险分析
1、人为因素影响较大;2、系统可控
风险评估
风险较高,验收环节是药品入库管理关键环节,是质量管理重点
风险接受
风险减少、风险可控
风险分析
1、人为因素影响较大;2、系统可控
风险评估
风险较高,药品销后退回验收环节是售出药品重新入库管理关键环节,对药品质量验收合格与否是质量管理重点。
风险接受
风险减少、风险避免
售后服务环节
风险因素
质量信息、质量查询、质量投诉、用户访问、药品不良反应监测/报告、药品召回、质量事故调查
管理措施
1、确立企业“购、储、销、运”的计算机信息管理系统,支持质量管理人员确认的暂停出库指令;2、对质量管理人员加强药品质量信息、质量查询、质量投诉及用户访问管理制度、程序的培训;3、质量管理人员掌握对药品不良反应监测和报告管理制度、药品召回管理制度、药品质量事故处理管理制度的熟练运用;对各类应急预案的启动清楚了解程序;4、质量管理人员严格执行质量否决权赋予的责任。
风险接受
风险减少、风险避免、风险转移
销售环节
风险因素
销售客户选择、销售管理
管理措施
1、确立企业“购、储、销”的计算机信息管理系统,未经质量审核的客户,系统不支持开票、出库,问题药品,系统锁定;2、规范销售人员销售行为;3、对销售人员加强药品销售管理制度、程序的培训;4、严格执行特殊管理药品的管理制度的要求。
风险分析
1、人为因素影响较大;2、系统可控;3、新的严重不良反应(未知风险)
药品生产过程质量风险评估报告模板
药品生产过程质量风险评估报告模板一、背景与目的:随着医疗水平的提高和人们对健康的重视,药品生产过程的安全性和质量控制显得尤为重要。
药品生产过程中的各个环节都存在一定的风险和隐患,为了保障药品质量,降低生产过程中的风险,我们进行了药品生产过程质量风险评估。
本报告的目的是对药品生产过程中的质量风险进行评估,提出相应的改进建议,以保障药品的安全性。
二、评估方法:1.采用“风险评估矩阵法”对药品生产过程中的各个环节进行风险评估。
根据风险的可能性和影响程度,将风险划分为低风险、中风险和高风险。
三、评估结果:在对药品生产过程中的各个环节进行风险评估后,我们得出以下结论:1.原料采购环节存在较高风险:原料的采购需要严格按照国家相关规定进行,存在一定的供应链风险。
因此,在原料采购环节应加强供应商的评估和监管,并建立可追溯系统,确保原料的质量可靠。
2.生产工艺环节存在中等风险:生产工艺是影响药品质量的关键环节之一、在生产工艺上,应加强工艺参数的控制,严格按照标准操作规程进行操作,防止出现差错或污染。
此外,应建立完善的变更控制制度,确保工艺变更的可控性和可追溯性。
3.检验检测环节存在较低风险:检验检测环节是保障药品质量的最后一道防线。
在检验检测环节,应加强仪器设备的维护和校准,确保结果的准确性。
此外,应制定完善的检验检测标准和方法,以确保检验结果的可靠性。
四、改进建议:基于对药品生产过程质量风险的评估结果,我们提出以下改进建议:1.建立健全原料采购管理制度,加强供应商的评估和监管。
2.加强生产工艺的控制,严格按照标准操作规程进行操作。
3.建立完善的变更控制制度,确保工艺变更的可控性和可追溯性。
4.加强仪器设备的维护和校准,制定完善的检验检测标准和方法。
5.定期进行内部审计和风险评估,及时发现和解决潜在的质量风险。
六、结论:通过对药品生产过程质量风险的评估,我们找出了存在的问题和风险,并提出了相应的改进建议。
只有加强对药品生产过程质量的管理和监控,才能降低质量风险,确保药品的安全性。
制药企业风险评估
制药企业风险评估制药企业作为一种高风险行业,面临着多种风险因素。
本文将对制药企业可能面临的风险进行评估,并提出相应的风险管理措施。
首先,制药企业面临的市场风险较大。
市场需求的不确定性和市场竞争的激烈程度使得企业面临着产品销售不达预期的风险。
为了应对市场风险,企业应进行全面的市场调研,了解目标市场的需求和竞争状况,并及时调整自己的产品线和市场策略,以适应市场环境的变化。
其次,制药企业面临的法律风险较高。
由于制药行业的特殊性,企业需要遵守严格的法律法规和相关的准入要求。
未能按照要求开展研发和生产,或者存在安全隐患,都有可能面临罚款、产品召回等法律责任。
为了降低法律风险,企业应建立健全的法律合规制度,加强内部员工培训,确保企业在法律框架内合规运营。
此外,制药企业还存在研发风险。
制药产品的研发需要投入大量的资金和时间,而其成功率相对较低。
研发过程中可能会遇到技术难题、临床试验失败以及专利保护等问题。
为了管理研发风险,企业应加强研发团队的管理,提高研发人员的技术素质,同时多元化研发项目,降低单一项目失败的影响。
此外,制药企业还存在供应链风险。
供应链的延误或中断可能会导致产品生产和销售的停滞以及客户满意度的下降。
为了管理供应链风险,企业应与供应商建立长期的战略合作关系,确保供应链的稳定性和可靠性。
此外,企业可以建立备份供应商,并定期进行供应链的评估和风险分析,及时应对潜在的风险。
最后,制药企业还面临信息安全风险。
随着信息化程度的增加,制药企业面临来自内部和外部的信息泄露、黑客攻击等威胁。
为了保护企业的信息安全,企业应建立完善的信息安全管理体系,加强员工的信息安全意识和培训,同时与专业的信息安全公司合作,进行安全漏洞的扫描和修复。
综上所述,制药企业面临着市场风险、法律风险、研发风险、供应链风险和信息安全风险。
企业应采取相应的风险管理措施,包括市场调研、法律合规制度建立、研发团队管理、供应链管理和信息安全管理等,以降低风险并提高企业的竞争力和可持续发展能力。
- 1、下载文档前请自行甄别文档内容的完整性,平台不提供额外的编辑、内容补充、找答案等附加服务。
- 2、"仅部分预览"的文档,不可在线预览部分如存在完整性等问题,可反馈申请退款(可完整预览的文档不适用该条件!)。
- 3、如文档侵犯您的权益,请联系客服反馈,我们会尽快为您处理(人工客服工作时间:9:00-18:30)。
编号:
第二部分执行正式风险评估
一、数据评估(总结数据的充分性,有效性及其他相关方面)
二、风险识别(总结以下风险识别)
三、风险分析及评估(汇总和/或附上FMEA分析表或HACCP分析表格)
附件确认: _______________________
签名/日期
(续前页)
质量风险评估表
编号:
四、风险控制实施的标准
质量风险评估表
第一部分 启动质量风险管理程序
一、风险项目名称(确定问题):
二、风险管理小组
组长:
其它资源要求
成员:
·
·
·
三、存在的危险源(填写以下内容或参见单独报告)
四、风险发生后的危害
五、目前的控制方式
计划
计划开始时间:
计划完成时间:
文件责任
姓名
职位
签名
日期
险分析报告编号:
附件确认: _______________________
签名/日期
二、实施风险控制方式前后的风险对比
三、实施结论
文件责任
姓名
职位
签名
日期
编写
审 核
审 核
批准
是否关闭风险管理程序
□是 □否 需重新进行风险评估。
质量受权人签名/日期:
五、拟定采用的控制方式(汇总控制风险所需的措施)及实施计划(包括控制方式的开始时间、完成时间,控制方式的负责部门及负责人)。
(若空间不够填写可增加附件)
文件责任
姓名
职位
签名
日期
编写
审 核
审 核
批准
质量风险评估表
编号:
第三部分:风险控制执行完毕后的风险再评估
一、控制方式实施后的风险结果
风险再分析及评估(汇总和/或附上FMEA分析表或HACCP分析表格)