不锈钢车削方法
3Cr13不锈钢零件批量数控车削技巧

3Cr13不锈钢零件批量数控车削加工技巧3Cr13是一种强度高、塑性好的中碳马氏体不锈钢材料,加工硬化倾向大、切削温度高、易粘刀、切屑不易卷曲与折断、刀具易磨损,加工困难。
[1] [2]传统的研究多在普通车床上进行,侧重于对刀具和切削参数的研究。
受机床本体硬件特性的影响,其研究成果的推广有很大局限性。
本文从数控加工的角度出发,以3Cr13不锈钢零件避雷针头(见图1)的加工为例,图1 避雷针头1 加工工艺简介零件的加工采用两道数控加工工序:工序1完成从8.9至6的外形加工,保证8.9的尺寸精度和表面质量要求;工序2处理R2圆角及其端面,定总长。
由于生产纲领为5000件,安排在两台数控车床上完成。
加工设备型号:CAK6136V/750 (沈阳第一机床厂),数控系统:HNC-21T。
2程序编制将程序原点选定在工件轴线与工件前端面的交点上,以工序1的编程为例编制加工程序如下(见程序清单)。
该程序选用两把可转位机夹车刀:外圆刀刀杆型号:MDJNR2020-K1506 ,刀片:DNMG150604-HM CC115;切刀刀杆型号:ZQ2020R-04,刀片:ZQMX3N11-1E YBC251。
在综合考虑机床、刀具和材料等方面的因素下,选择粗加工时吃刀深度ap=1.2 mm,进给速度F=88 mm/min ,主轴转速n=800 r/min;精加工时,ap=0.2 mm,进给速度F=60mm/ min,主轴转速n=1200r/min。
程序的编制体现了以下技巧:(1)编制N06 G00X17Z2,切削循环起点靠近工件,可减少空行程,缩短进给路线。
(2)编制N10 G81 X-0.5能确保零件端面车削完整,防止由于对刀或装夹中的误差造成进刀量不足而在端面留下小的尾钉。
(3)编制N12G71U1.2R5,退刀量取5mm可防止在倒锥(最大直径相差4mm)加工中的刀具干涉。
(4)针对不锈钢材料加工中刀具易磨损严重的情况,编制N14刀具T01磨损补偿子程序%0001。
1Cr18Ni9Ti不锈钢的切削加工

( 1) 切削速度 Vc 为了保证合理的刀具耐用度, 可适当降低切削 速度。切削不锈钢时, 切削速度通常可按切削普通 碳钢的 40% - 60% 来选取。 ( 2) 背吃刀量 ap 粗加工时余量较大, 应选用较大的背吃刀量, 以 减少走刀次数, 同时可避免刀尖与工件毛坯表皮接 触, 以减轻刀具磨损。但背吃刀量也不宜过大, 否则 会引起振动。粗加工时, 可选取 ap= 2- 5mm。精加 工时, 可选 取较小的背吃刀量, 同时还 要避开硬化 层, 一般可选取 ap= 0 2- 0 5mm。 ( 3) 进给量 f 增大进给量会使切削残留高度和积屑瘤高度加 大, 通常选取 f = 0 1- 0 8mm。为了提高加工表面 质量, 精加 工时应采用较小的 进给量, 但不得小于 0 1mm, 以免在加工硬化区进行切削。还应注意, 进 给量 f 与背吃刀量 ap 成反比。 3 4 切削液的选择
一般来说不锈钢被认为是切削加工性能较差的金属材料1cr18ni9ti不锈钢尤为突出45钢相比其相对可切削性仅为013015属于典型的难加工材料不锈钢的主要切削特点不锈钢的切削加工具有以下特点切削力大奥氏体不锈钢表现尤为突出这种材料虽然硬度不高例如1cr18ni9ti的硬度hb187但塑性很好断后伸长率因此在切削过程中塑性变形大使切削力增加合理选择切削加工工艺由于1cr18ni9ti不锈钢切削加工性差因此必须合理选择切削加工工艺以获得良好的加工效果收稿日期
收稿日期: 2008 年 11 月
相同加工条件下, 1Cr18Ni9T i 的单位切削力比 45 钢 大 25% 以上。
车削奥氏体不锈钢的加工要点

(r t gad d e gpa t i h u i nn 2 0 0 hn ; h nagA rnui lP leh i Istt h nag Pi i n y i l ,J z o, a i 1 10 , ia S ey oa ta o t nc ntu ,Se yn, nn n n n Lo g C n e c yc i e Lan g 1O 3,hn) i i l0 4C ia on
不锈钢 归为难加工材料。 关键词 : 奥氏体不锈钢 ; 车削加 工; 材料 中圈分类号 :Q 2 . + T 3 06 7 6 文献标识码 : A
文章编 号 :0 7 8 2 (0 2 0— 0 2 0 10 — 30 2 1 ) 10 7 — 2
Bre a y i f t e t r i g o u t n tc sa n e s se l p o e sng p i t if An l ss o h u n n f a se ii t i ls te r c s i o n s
象。
量 、 具 参 数 、 削 条 件 。 些 对 于 奥 氏体 不 锈 钢 的 加 工 就 显 刀 切 这
得 极 为 重要 。
( ) 氏体 不锈钢 的综合 性能优 良, 2奥 塑性 和韧性高 , 的 它
延 伸 率 、 面 收缩 率 和 冲 击 值 都 较 高 。C 8 i i 氏 体 不 锈 断 1 d N9 奥 T
() 4奥氏体不锈钢 中存在较多的碳化钛( i) TC 颗粒 , 硬度相
对 :我 们 选 择 的 f 硬度 商 。这种 颗 粒 枉 奥 氏体 小 锈 钢 什 j L, } 中, 会增 大对 于刀 具 的 冲击 , 剧 加
不锈钢车削参数
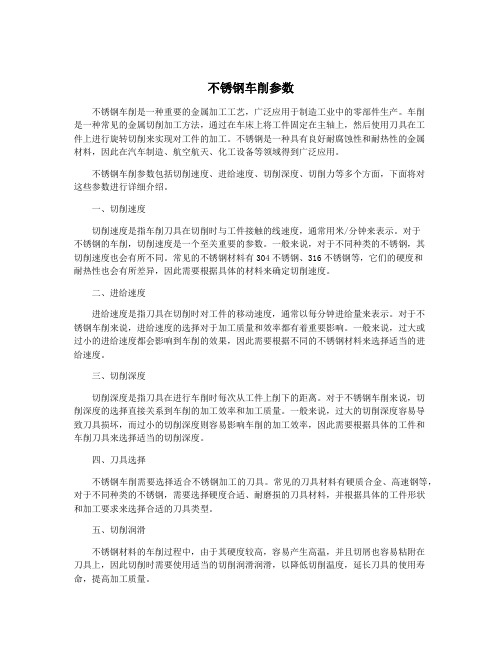
不锈钢车削参数不锈钢车削是一种重要的金属加工工艺,广泛应用于制造工业中的零部件生产。
车削是一种常见的金属切削加工方法,通过在车床上将工件固定在主轴上,然后使用刀具在工件上进行旋转切削来实现对工件的加工。
不锈钢是一种具有良好耐腐蚀性和耐热性的金属材料,因此在汽车制造、航空航天、化工设备等领域得到广泛应用。
不锈钢车削参数包括切削速度、进给速度、切削深度、切削力等多个方面,下面将对这些参数进行详细介绍。
一、切削速度切削速度是指车削刀具在切削时与工件接触的线速度,通常用米/分钟来表示。
对于不锈钢的车削,切削速度是一个至关重要的参数。
一般来说,对于不同种类的不锈钢,其切削速度也会有所不同。
常见的不锈钢材料有304不锈钢、316不锈钢等,它们的硬度和耐热性也会有所差异,因此需要根据具体的材料来确定切削速度。
二、进给速度进给速度是指刀具在切削时对工件的移动速度,通常以每分钟进给量来表示。
对于不锈钢车削来说,进给速度的选择对于加工质量和效率都有着重要影响。
一般来说,过大或过小的进给速度都会影响到车削的效果,因此需要根据不同的不锈钢材料来选择适当的进给速度。
三、切削深度切削深度是指刀具在进行车削时每次从工件上削下的距离。
对于不锈钢车削来说,切削深度的选择直接关系到车削的加工效率和加工质量。
一般来说,过大的切削深度容易导致刀具损坏,而过小的切削深度则容易影响车削的加工效率,因此需要根据具体的工件和车削刀具来选择适当的切削深度。
四、刀具选择不锈钢车削需要选择适合不锈钢加工的刀具。
常见的刀具材料有硬质合金、高速钢等,对于不同种类的不锈钢,需要选择硬度合适、耐磨损的刀具材料,并根据具体的工件形状和加工要求来选择合适的刀具类型。
五、切削润滑不锈钢材料的车削过程中,由于其硬度较高,容易产生高温,并且切屑也容易粘附在刀具上,因此切削时需要使用适当的切削润滑润滑,以降低切削温度,延长刀具的使用寿命,提高加工质量。
通过对不锈钢车削参数的合理选择,在保证车削加工效率的还能够得到尺寸精确、表面光滑的加工零件。
不锈钢车削加工特点及加工工艺
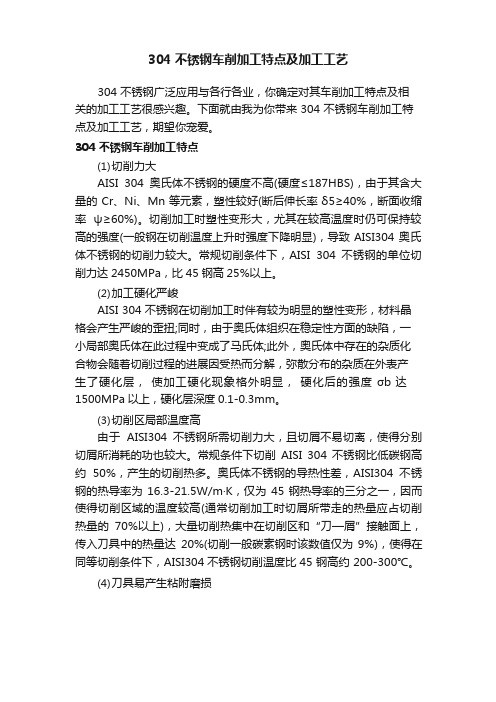
304 不锈钢车削加工特点及加工工艺304 不锈钢广泛应用与各行各业,你确定对其车削加工特点及相关的加工工艺很感兴趣。
下面就由我为你带来 304 不锈钢车削加工特点及加工工艺,期望你宠爱。
304 不锈钢车削加工特点(1)切削力大AISI 304 奥氏体不锈钢的硬度不高(硬度≤187HBS),由于其含大量的 Cr、Ni、Mn 等元素,塑性较好(断后伸长率δ5≥40%,断面收缩率ψ≥60%)。
切削加工时塑性变形大,尤其在较高温度时仍可保持较高的强度(一般钢在切削温度上升时强度下降明显),导致 AISI304 奥氏体不锈钢的切削力较大。
常规切削条件下,AISI 304 不锈钢的单位切削力达 2450MPa,比 45 钢高 25%以上。
(2)加工硬化严峻AISI 304 不锈钢在切削加工时伴有较为明显的塑性变形,材料晶格会产生严峻的歪扭;同时,由于奥氏体组织在稳定性方面的缺陷,一小局部奥氏体在此过程中变成了马氏体;此外,奥氏体中存在的杂质化合物会随着切削过程的进展因受热而分解,弥散分布的杂质在外表产生了硬化层,使加工硬化现象格外明显,硬化后的强度σb达1500MPa 以上,硬化层深度 0.1-0.3mm。
(3)切削区局部温度高由于AISI304 不锈钢所需切削力大,且切屑不易切离,使得分别切屑所消耗的功也较大。
常规条件下切削AISI 304 不锈钢比低碳钢高约50%,产生的切削热多。
奥氏体不锈钢的导热性差,AISI304 不锈钢的热导率为 16.3-21.5W/m·K,仅为 45 钢热导率的三分之一,因而使得切削区域的温度较高(通常切削加工时切屑所带走的热量应占切削热量的70%以上),大量切削热集中在切削区和“刀—屑”接触面上,传入刀具中的热量达20%(切削一般碳素钢时该数值仅为9%),使得在同等切削条件下,AISI304 不锈钢切削温度比 45 钢高约 200-300℃。
(4)刀具易产生粘附磨损由于奥氏体不锈钢的高温强度高,加工硬化倾向大,因此,切削负荷重,奥氏体不锈钢与刀具和切屑之间会由于切削过程中其与刀具之间的亲合趋势显著增加,从而不行避开地产生粘结、集中等现象,并生成“切屑瘤”,造成刀具粘附磨损。
304不锈钢车削的高压断屑技术研究

304不锈钢车削的高压断屑技术研究
戚远大;周永胜;崔成林
【期刊名称】《组合机床与自动化加工技术》
【年(卷),期】2022()2
【摘要】针对304不锈钢的车削过程中铁屑折断难,经常导致铁屑缠刀、加工表面划伤、排屑困难、影响自动化生产线的稳定运行等问题,设计开发7 MPa高压供液系统为车削过程提供高压冷却液。
在高压冷却环境下,试验比较304不锈钢在粗、精加工的不同车削参数、刀片情况下的铁屑状态。
研究结果表明,7 MPa高压冷却可以解决304不锈钢精加工铁屑不易折断的问题。
铁屑的长度与冷却压力、切削参数、刀片有关,通过匹配适当的切削参数和刀片,铁屑长度可以被控制在较短的范围内。
在此基础上,提出了一套针对304不锈钢车削加工的高压断屑方案,实现铁屑的可靠折断。
【总页数】4页(P112-114)
【作者】戚远大;周永胜;崔成林
【作者单位】沈阳机床集团有限责任公司
【正文语种】中文
【中图分类】TH161;TG51
【相关文献】
1.车削中三维复杂断屑槽刀具断屑仿真研究
2.简易车削断屑装置及其断屑规律研究
3.车削加工切屑形状分析及合理断屑方法
4.不锈钢车削刀片槽型断屑仿真研究
5.伊斯卡推出适合切断不锈钢的新型断屑槽及IC5400牌号
因版权原因,仅展示原文概要,查看原文内容请购买。
浅谈不锈钢材料的车削加工
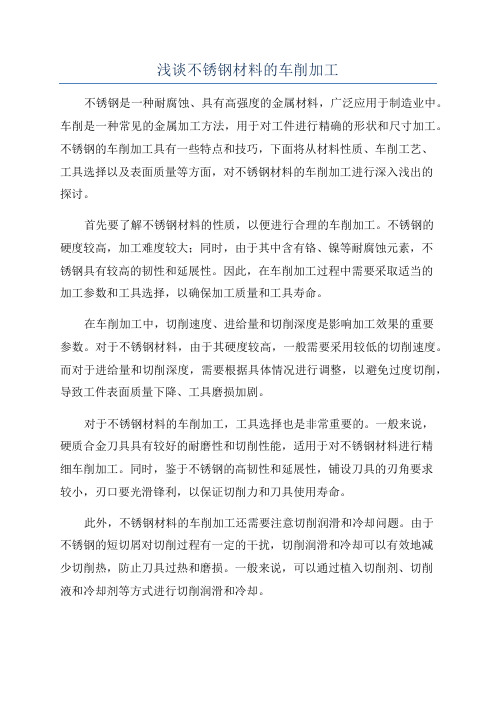
浅谈不锈钢材料的车削加工不锈钢是一种耐腐蚀、具有高强度的金属材料,广泛应用于制造业中。
车削是一种常见的金属加工方法,用于对工件进行精确的形状和尺寸加工。
不锈钢的车削加工具有一些特点和技巧,下面将从材料性质、车削工艺、工具选择以及表面质量等方面,对不锈钢材料的车削加工进行深入浅出的探讨。
首先要了解不锈钢材料的性质,以便进行合理的车削加工。
不锈钢的硬度较高,加工难度较大;同时,由于其中含有铬、镍等耐腐蚀元素,不锈钢具有较高的韧性和延展性。
因此,在车削加工过程中需要采取适当的加工参数和工具选择,以确保加工质量和工具寿命。
在车削加工中,切削速度、进给量和切削深度是影响加工效果的重要参数。
对于不锈钢材料,由于其硬度较高,一般需要采用较低的切削速度。
而对于进给量和切削深度,需要根据具体情况进行调整,以避免过度切削,导致工件表面质量下降、工具磨损加剧。
对于不锈钢材料的车削加工,工具选择也是非常重要的。
一般来说,硬质合金刀具具有较好的耐磨性和切削性能,适用于对不锈钢材料进行精细车削加工。
同时,鉴于不锈钢的高韧性和延展性,铺设刀具的刃角要求较小,刃口要光滑锋利,以保证切削力和刀具使用寿命。
此外,不锈钢材料的车削加工还需要注意切削润滑和冷却问题。
由于不锈钢的短切屑对切削过程有一定的干扰,切削润滑和冷却可以有效地减少切削热,防止刀具过热和磨损。
一般来说,可以通过植入切削剂、切削液和冷却剂等方式进行切削润滑和冷却。
最后,不锈钢材料的车削加工后还需要进行相应的表面处理,以提高工件的表面质量和防锈性能。
一般可以采用研磨、抛光等方式进行表面处理,以增加工件的光洁度和美观度。
总之,不锈钢材料的车削加工是一项综合性的任务,需要考虑材料性质、车削工艺、工具选择以及表面质量等多个方面的因素。
只有合理选择加工参数和工具,严格控制加工过程,才能获得满意的加工效果和产品质量。
同时,注重切削润滑和冷却、以及后续表面处理,也是保证不锈钢材料车削加工成功的关键。
不锈钢的车削技巧

不锈钢的车削技巧主要包括以下几个方面:1.刀具选择:选择适合不锈钢车削的刀具非常重要。
通常,选择具有较高耐热性、耐磨性和与不锈钢亲和作用小的刀具材料,如高碳、高钒或钼系的高速钢。
此外,刀具的几何形状和角度也需要根据具体加工要求进行选择。
2.切削用量选择:切削用量包括切削速度、进给量和切削深度。
对于不锈钢的车削,切削速度通常较低,一般为普通碳钢切削速度的40%~60%。
进给量和切削深度也需要根据具体情况进行选择,以避免刀具过度磨损和工件表面质量下降。
3.冷却液选择:使用合适的冷却液可以有效降低切削温度,减少刀具磨损和提高工件表面质量。
对于不锈钢的车削,通常选择具有较好冷却和润滑性能的冷却液。
4.操作技巧:在车削不锈钢时,需要注意以下几点操作技巧:首先,保持刀具的锋利,及时更换磨损的刀具;其次,避免使用过大的切削用量,以减少刀具的受力;最后,注意工件的装夹方式和切削力的方向,以避免工件变形或振动。
此外,还需要注意以下几点:1.由于不锈钢的塑性大、韧性高,车削时容易产生积屑瘤和鳞刺,这不仅影响工件的表面粗糙度,还会使刀具的磨损加快。
因此,需要选择合适的刀具材料和几何角度,以及合理的切削用量来避免这些问题的产生。
2.不锈钢的导热性差,导致切削热无法及时散出,使刀具的刃口温度升高,加剧刀具磨损。
为了降低切削温度,可以采用浇注冷却液的方法。
3.在车削过程中,应随时注意观察切削情况,如发现异常现象(如振动、噪声、温度升高等),应及时采取措施进行调整。
4.对于不同种类和规格的不锈钢材料,其车削性能也会有所不同。
因此,在实际加工前,最好先进行一些试验性切削,以确定最佳的切削参数和工艺方案。
总之,掌握不锈钢的车削技巧需要综合考虑多个因素,包括刀具选择、切削用量、冷却液和操作技巧等。
通过合理的选择和调整这些参数,可以提高加工效率、降低生产成本并获得高质量的工件。
- 1、下载文档前请自行甄别文档内容的完整性,平台不提供额外的编辑、内容补充、找答案等附加服务。
- 2、"仅部分预览"的文档,不可在线预览部分如存在完整性等问题,可反馈申请退款(可完整预览的文档不适用该条件!)。
- 3、如文档侵犯您的权益,请联系客服反馈,我们会尽快为您处理(人工客服工作时间:9:00-18:30)。
复合
°°
°
5 1 185
涂层
用) Ra~
刀片
5
Ra1.6
3.
刀具的几何角度和结构的选取
对于良好的刀具材料,选择合理的几何角度则显得尤为重要。
• 前角 γ:一般车削马氏体不锈钢刀具前角取10°~20°较为适宜。 • 后角 α:一般取5°~8°较合适,最大不过10°。 • 刃倾角 λ:一般选取 λ 为-10°~30°。 • 主偏角 Kr 应根据工件的形状、加工部位和装刀情况来选择。 • 刃口表面粗糙度应不大于 Ra0.4~Ra0.2。 • 在结构上,我们对外圆车刀采用外斜式圆弧断屑槽,靠刀尖处切屑卷曲半径大,靠 外缘处切屑卷曲半径小,切屑将翻向待加工表面而折断,断屑情况好。而对切断刀,我
5.
选用适当的冷却润滑液 车削不锈钢用的冷却润滑液,应该具有以下几个特点:
• 高的冷却性能,保证能带走大量的切削热。 • 不锈钢韧性大,切削时易产生刀瘤,恶化加工表面,这就要求冷却润滑液有高的润 滑性能,能起到较好的润滑作用。 • 渗透性好,对不易被切离的切屑,能起到较好的楔裂、扩散和内润滑作用。 常用的加工不锈钢的冷却润滑液有如下几种:硫化油、硫化豆油,煤油加油酸或植物油、四 氯化碳加矿物油、乳化液等。 考虑到硫对机床有一定的腐蚀作用,植物油(如豆油)容易附在机床上结痂和变质,我们选用 了四氯化碳与机油按重量比为1:9的混合物。其中四氧化碳渗透性好,机油的润滑性好。试 验证明,这种冷却润滑液适用于表面粗糙度要求小的不锈钢零件的半精加工和精加工工序, 特别适合于马氏体类不锈钢零件的车加工。
3结论
由于采取了一系列措施,我们对 3Cr13 不锈钢材料的加工已完全处于正常状态。磨刀次数 只有试生产时的 1/3,提高了生产效率,零件质量完全达到设计要求。
表1
切削用
量 刀具 加工表
3Cr13钢 ν s 耐用 面粗糙
材料 m/ m 度
度
mi m min
μm
n /r
HB240( 退火)
45 0 90~ Ra6.3~
~. 115 Ra3.2
55 1
45 0
HRC25~
95~
~.
30(调质)
110
55 1
Ra3.2
45 0
HRC35~
60~
~.
38(调质)
75
1切削过程中的难点及原因分析
在零件试生产时,我们按车削普通碳钢的工艺方法对3Cr13不锈钢进行了车削试验,结果是 刀具磨损非常严重,生产率极低,零件表面质量达不到要求。 比较3Cr13钢与40钢、45钢等碳素结构钢的机械性能可知,3Cr1 3钢的强度比40钢和45钢 高,它是一种强度高、塑性好的中碳马氏体不锈钢。由于切削时加工硬化严重,切削抗力大, 切削温度高,导致刀具磨损严重,磨刀次数增多,增加了停机时间和机床调整时间,降低了 生产率。同时又容易粘刀,产生积屑瘤,引起工件尺寸的变化并影响表面粗糙度,而且切屑 不易卷曲和折断,易损伤工件已加工表面,影响零件质量。所以,不能用切削45钢的工艺 来切削3Cr13,也不能把通用车床上的加工方法照搬到自动车床上来。因为一般自动车床装刀 较少,要求最好一次走刀就能使被加工表面达到要求的尺寸和表面粗糙度,以保证较高的生 产率。
55 1
Ra3.2
2.
刀具材料的选择
在自动车床上车削不锈钢,一般使用的硬质合金的刀具材料有:YG6、YG8、YT15、YT30、 YW1、YW2等材料。 常用的高速钢刀具有:W18Cr4V、W6M05Cr4V2AL 等材料。我们在切削参数相同的条件
下,对几种材料的刀具进行了车削对比试验,从表2可见:采用 TiC-TiCN-TiN 复合涂层刀片 的外圆车刀,耐用度比较高,切削速度可取高,工件表面质量好,生产率高。但是,没有这
种材料的切断刀片。通过表2的对比试验,YW2硬质合金的切削性能也不错,我们选用 YW2 材料的刀片作为切断刀。
表2不同刀具材料切削对比试验
刀具 材料
刀具的几何角度
主刃 前后
偏倾 角角
角角 γα
Kr λ
切削
用量 刀
νs 具
m
耐
/ m用
mm 度
i / min
加工 表面 粗糙
度 μm
nr
4
1
5 0 72
8 90 -1
YG8 5
~. ~
°° 0
°
5 1 82
3.2
5
4
1
5 0 80
8 90 -1
YT14 5
~. ~
°° 0
°
5 1 95
Ra3.2
5
4
1
5 0 90
8 90 -1
YW2 5
~ . ~ Ra3.2
°° 0
°
5 1 110
5
Tic-T
Ra6.3
iCN-
4 (切断
1
5 0 128
TiN
8 90
2
-4 ~ . ~
2主要技术措施
1.
通过热处理,改变材料的硬度
马氏体不锈钢在热处理后的不同硬度,对车削加工的影响很大。表1是用 YW2材料的车刀对 热处理后不同硬度的3Cr13钢的车削情况。可见,退火状0.10.10.1态的马氏体不锈钢虽然硬 度低,但车削性能差,这是因为材料塑性和韧性大,组织不均匀,粘附,熔着性强,切削过
程易产生刀瘤,不易获得较好的表面质量。而调质处理后硬度在 HRC30以下的3Cr13材料, 车削加工性较好,易达到较好的表面质量。用硬度在 HRC30以上的材料加工出的零件,表 面质量虽然较好,但刀具易磨损。所以,在条件允许的情况下,可以在材料进厂后,先进行
调质处理,硬度达到 HRC25~HRC30,然后再进行切削加工。
们将副偏角控制在1o 以内,这样可以改善排屑条件、延长刀具的使用寿命。
4.
合理选择切削用量 切削理论认为,切削速度 v 对切削温度和刀具耐用度的影响最大,走刀量 s 次之,吃刀量 t 最小,而在自动车床上一次走刀加工工件的表面,其吃刀量 t 是由零件尺寸与材料毛坯尺寸 来决定的,一般为0~3mm;难加工材料的切削速度往往比普通钢的切削速度低得多。 走刀量 s 对刀具耐用度影响不如切削速度大,但会影响断屑和排屑,拉伤、擦伤工件表面, 影响加工的表面质量,一般认为吃刀深度大时,走刀量应减小,而切断的走刀量又比车外圆 要小。在被加工表面粗糙度要求不高时,s 选用0.1mm/r~0.2mm/r。 总之,对于难加工材料,一般选用较低的切削速度、中等的走刀量。