不锈钢管件加工流程
不锈钢管道施工工艺流程
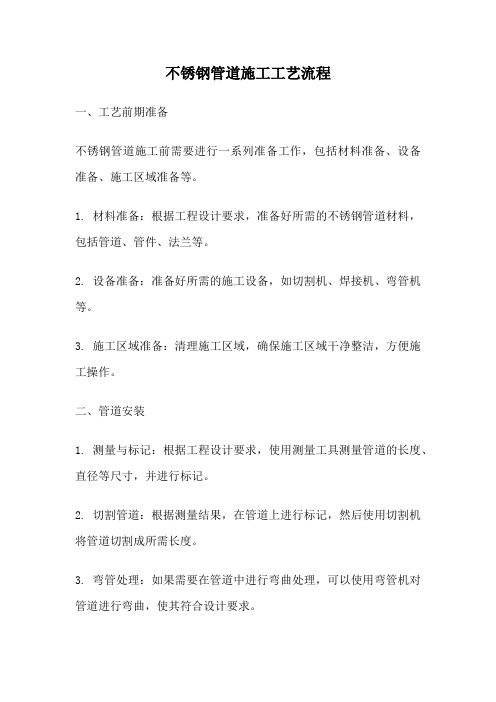
不锈钢管道施工工艺流程一、工艺前期准备不锈钢管道施工前需要进行一系列准备工作,包括材料准备、设备准备、施工区域准备等。
1. 材料准备:根据工程设计要求,准备好所需的不锈钢管道材料,包括管道、管件、法兰等。
2. 设备准备:准备好所需的施工设备,如切割机、焊接机、弯管机等。
3. 施工区域准备:清理施工区域,确保施工区域干净整洁,方便施工操作。
二、管道安装1. 测量与标记:根据工程设计要求,使用测量工具测量管道的长度、直径等尺寸,并进行标记。
2. 切割管道:根据测量结果,在管道上进行标记,然后使用切割机将管道切割成所需长度。
3. 弯管处理:如果需要在管道中进行弯曲处理,可以使用弯管机对管道进行弯曲,使其符合设计要求。
4. 焊接管道:将管道与管道连接处进行焊接,确保焊接质量良好,焊缝牢固。
5. 安装管件:根据设计要求,在管道上安装所需的管件,如法兰、弯头、三通等。
6. 固定管道:将管道固定在支架上,确保管道的稳定性和安全性。
三、管道测试管道安装完成后,需要进行一系列管道测试,以确保管道的质量和安全性。
1. 水压试验:使用水泵将水注入管道中,增加管道内部的压力,观察管道是否有漏水现象。
2. 气密性测试:将管道与压力表连接,增加管道内部的压力,观察压力表的读数是否有变化,以判断管道是否有漏气现象。
3. 强度测试:使用力学测试仪器对管道进行强度测试,以确保管道的承载能力符合设计要求。
四、管道保护管道安装和测试完成后,需要进行管道的保护工作,以延长管道的使用寿命。
1. 防腐处理:对不锈钢管道进行防腐处理,可以使用喷涂、涂刷等方法,提高管道的抗腐蚀性能。
2. 绝缘处理:根据需要,对管道进行绝缘处理,以防止管道表面的温度变化对周围环境的影响。
3. 标识标牌:在管道上设置标识标牌,标明管道的用途、流体介质、流向等信息,方便后续维护和操作。
五、施工总结管道施工完成后,需要进行施工总结和验收,以确保施工质量符合要求。
1. 施工记录:记录管道施工的各项数据和过程,包括材料使用情况、施工工艺、测试结果等。
304不锈钢管安装工艺流程
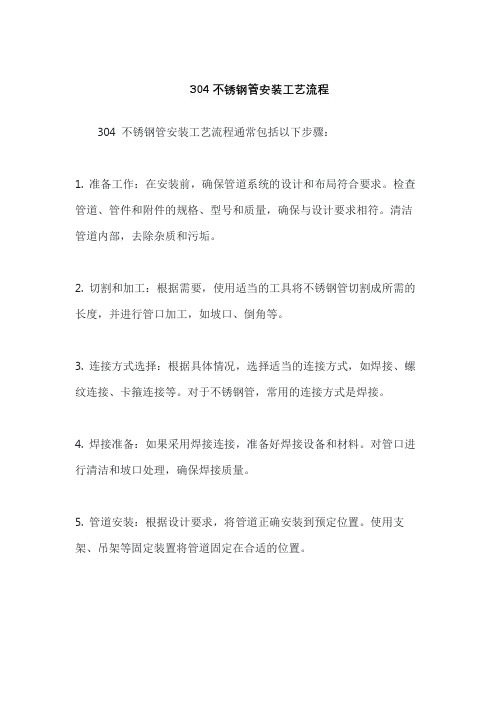
304不锈钢管安装工艺流程
304 不锈钢管安装工艺流程通常包括以下步骤:
1. 准备工作:在安装前,确保管道系统的设计和布局符合要求。
检查管道、管件和附件的规格、型号和质量,确保与设计要求相符。
清洁管道内部,去除杂质和污垢。
2. 切割和加工:根据需要,使用适当的工具将不锈钢管切割成所需的长度,并进行管口加工,如坡口、倒角等。
3. 连接方式选择:根据具体情况,选择适当的连接方式,如焊接、螺纹连接、卡箍连接等。
对于不锈钢管,常用的连接方式是焊接。
4. 焊接准备:如果采用焊接连接,准备好焊接设备和材料。
对管口进行清洁和坡口处理,确保焊接质量。
5. 管道安装:根据设计要求,将管道正确安装到预定位置。
使用支架、吊架等固定装置将管道固定在合适的位置。
6. 连接和固定:根据选择的连接方式,进行管道连接。
确保连接牢固、密封良好。
对于焊接连接,进行焊接操作,遵循焊接规范和标准。
7. 压力测试:安装完成后,进行压力测试以检查管道系统的密封性能。
根据设计要求,进行适当的压力测试,确保无泄漏。
8. 防腐和保温:根据需要,对管道进行防腐处理和保温工作,以保护管道并提高热能效率。
9. 检验和调试:完成安装后,进行检验和调试,确保管道系统正常运行。
10. 文档记录:保存安装过程中的相关文档记录,包括管道布局图、安装记录、检验报告等。
以上是304 不锈钢管安装工艺流程的一般步骤。
具体的安装流程可能会因项目的特定要求和现场条件而有所不同。
在安装过程中,应遵循相关的规范和标准,并确保施工质量和安全。
管件生产总结

管件生产总结管件是一种常用的连接材料,在管道系统中起到连接和转换流体的作用。
为了确保管件的质量和生产效率,本文对管件生产进行了总结和梳理,以期对今后的生产工作有所指导和借鉴。
一、生产工艺流程管件生产工艺流程包括材料准备、成型加工、热处理、表面处理和质量检测等环节。
首先,材料准备是确保产品质量的基础,包括选材、切割和装料等工序。
成型加工阶段通过冷挤压、热挤压或锻造等方式将材料成型成管件的预形状。
热处理是为了改善材料的力学性能和组织结构,通过调控温度和时间来保证产品的性能稳定。
表面处理是为了提高管件的耐腐蚀性和装饰性,常见的处理方法有喷丸、镀锌和喷涂等。
最后,通过质量检测环节来评估产品的合格率,确保产品满足客户的需求。
二、生产过程中的问题与对策1.材料质量不稳定:管件生产所使用的原材料具有一定的特殊性,因此材料的质量稳定性对于产品的可靠性至关重要。
为了解决这个问题,我们需要与供应商建立长期合作关系,加强对原材料的质量控制,严格按照规范要求进行抽样检测和验收。
2.成型精度不高:由于管件形状和尺寸的要求较高,成型过程中的不合格率较高。
针对这个问题,我们需要引进先进的成型设备和工艺技术,并加强操作工人的培训,提高他们的技能水平。
同时,建立完善的质量管理体系,进行跟踪检测和及时调整。
3.热处理引起的变形:在热处理过程中,由于温度和冷却速度的不均匀性,容易导致管件变形。
为了避免这个问题,我们应该优化热处理工艺,控制好加热温度和冷却速度,避免过度变形。
同时,加强对热处理过程的监控和检测,及时调整工艺参数。
4.表面处理不合格:表面处理工艺的不合格会影响管件的耐腐蚀性和装饰性。
为了确保表面处理效果,我们需要严格按照工艺要求操作,并加强对操作工人的培训和指导,保证工艺的标准化和稳定性。
此外,加强质量检测环节,对表面处理效果进行抽查和评估。
三、生产管理与优化为了提高生产效率和产品质量,我们需要加强生产管理和优化流程。
首先,建立规范的生产作业指导书,明确每道工序的工艺要求和操作规范,提高生产工人的工作效率和准确性。
不锈钢管安装施工工艺及方法
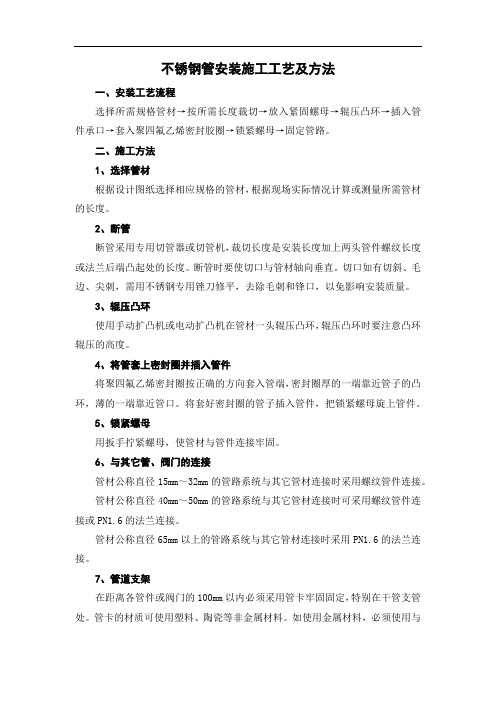
不锈钢管安装施工工艺及方法一、安装工艺流程选择所需规格管材→按所需长度裁切→放入紧固螺母→辊压凸环→插入管件承口→套入聚四氟乙烯密封胶圈→锁紧螺母→固定管路。
二、施工方法1、选择管材根据设计图纸选择相应规格的管材,根据现场实际情况计算或测量所需管材的长度。
2、断管断管采用专用切管器或切管机,裁切长度是安装长度加上两头管件螺纹长度或法兰后端凸起处的长度。
断管时要使切口与管材轴向垂直。
切口如有切斜、毛边、尖刺,需用不锈钢专用锉刀修平,去除毛刺和锋口,以免影响安装质量。
3、辊压凸环使用手动扩凸机或电动扩凸机在管材一头辊压凸环,辊压凸环时要注意凸环辊压的高度。
4、将管套上密封圈并插入管件将聚四氟乙烯密封圈按正确的方向套入管端,密封圈厚的一端靠近管子的凸环,薄的一端靠近管口。
将套好密封圈的管子插入管件,把锁紧螺母旋上管件。
5、锁紧螺母用扳手拧紧螺母,使管材与管件连接牢固。
6、与其它管、阀门的连接管材公称直径15mm~32mm的管路系统与其它管材连接时采用螺纹管件连接。
管材公称直径40mm~50mm的管路系统与其它管材连接时可采用螺纹管件连接或PN1.6的法兰连接。
管材公称直径65mm以上的管路系统与其它管材连接时采用PN1.6的法兰连接。
7、管道支架在距离各管件或阀门的100mm以内必须采用管卡牢固固定,特别在干管支管处。
管卡的材质可使用塑料、陶瓷等非金属材料。
如使用金属材料,必须使用与管材相同的材质的不锈钢。
卡凸式不锈钢管的立管和水平管的支撑间距应符合设计规定。
8、管道暗敷(1)管道室内暗敷当管道穿越墙壁、楼板及嵌墙暗敷时,应配合土建工程预留孔、槽。
以确保安装的安全和方便。
留孔或开槽的尺寸宜符合下列规定:预留孔洞的尺寸宜比管外径大50~100mm;嵌墙暗管的墙槽深度宜为管道外径加20mm,宽度宜为管道外径加45~50mm;架空管道管顶上部的净空尺寸不宜小于100mm。
管道暗敷严禁开横槽,以免影响土建结构;可在土建砌墙时根据砖的模块在暗敷管道的部位砌事先预制且带有水平槽的水泥砖。
不锈钢压铸工艺流程

不锈钢压铸工艺流程
要想完成一件精密铸造产品所需的工序很复杂,首先制模+熔炼(温度1600°C) →浇注→振壳+切割(切割浇口)→粗磨(磨去浇口)→酸洗(目的:去除铸造氧化皮酸洗液:硝酸50%、氢氟酸50%温度: 50-60°C 时间20 30分钟冲洗水温:50°C) - +吊抛(目的:去除铸造表面氧
化皮合金钢丸:直径0.2-0.4mm 时间: 20-30分钟)精喷目的:局部小
孔抛光不方便的地方使用喷砂处理。
→固溶化的目的是获得单相奥氏体组织:工艺:加热温度到1080°C;时间:壁厚25mm/n;冷却:常温水。
时间: > 30s→吊抛的目的是去除热处理时产生的氧化皮合金钢丸:
直径0.2-0.4mm时间: 10-1 5分钟- +整形- +钝化目的是使不锈钢
表面生成保护膜酸洗液:酸洗液:硝酸50%、氢氟酸50%温度: 50-60°C 时间3-5分钟冲洗水温: 90°C →然后就不锈钢铸件的工序就完成了终检入库。
XX有限公司精密铸造、丕锈钢铸件、不锈钢铸造、硅溶胶精密
铸造为主,其产品包括缝制配件、纺织配件、门窗配件、家具配件、管件阀门、快速接头、船用五金、机械五金、五金工具等精铸件、产品广泛应用于机械、建筑、船舶、汽车、缝纫机、家居、医疗等领域。
无缝不锈钢管件MPS文件

АААAAA重工股份有限企业无缝管件制造工艺规范文件号: ZZWD-LB-01 项目号:日期: .阶段:A版无缝管件制造工艺规范(M PS文件)说明编制审核批准日期供招标目录1 22 23 24 35 36 37 48 129 1410 1611 1612 1813 1814 2015 2016 201范围本文件规定了ААА用 2207 等材质钢制对焊无缝不锈钢管件生产的基本参数、原资料、制造工艺、资料性能、几何尺寸与同意误差、工艺质量与缺点修理、查验与实验、标记、涂层与保护、质量证明书及装运的要求。
本制造工艺规范应与 GB/T 12459-2005《钢制对焊无缝管件》标准及招标技术要求一同使用,凡是发现与 GB/T 12459-2005 《钢制对焊无缝管件》标准及招标技术要求相矛盾的条款,应以最严格的为准。
2规范性引用文件以下文件中的条款经过本文件的引用而成为本文件的条款。
凡是注日期的引用文件,其随后所有的改正单(不包含勘误的内容)或订正版均不合用于本文件,但是,鼓舞依据本文件达成协议的各方研究能否可使用这些文件的最新版本。
凡是不注日期的引用文件,其最新版本合用于本文件。
GB/T 223钢铁及合金化学剖析方法GB/T 228金属资料室温拉伸试验方法GB/T 229金属资料夏比摆锤冲击试验方法GB/T金属资料布氏硬度试验第 1 部分:试验方法GB/T 4237-2007不锈钢热轧钢板和钢带GB/T 9445-2008无损检测人员资格判定与认证GB/T 10561钢中非金属夹杂物显微评定方法GB/T 12459-2005钢制对焊无缝管件NB/T 47010-2010承压设施用不锈钢和耐热钢锻件NB/T 47013承压设施无损检测ISO 9001质量管理系统要求ASTM A370钢产品机械性能试验的方法和定义ASTM E45钢中夹杂物含量确实定方法3制造工艺流程表热推弯头制造工艺流程成品弯头(热成型)1.原资料进厂;2. 原资料的查验及查收;3. 钢管下料;4. 推制成型;5. 热办理 * ;6. 坡口;7. 表面办理;8. 无损探伤;9. 尺寸及外观查验; 10. 刷漆; 11. 表记; 12. 坡口防备; 13. 寄存及装运注: * 为特别加工工序。
薄壁不锈钢管的施工工艺
薄壁不锈钢管的施工工艺1、施工工艺流程施工准备→材料进场检验→下料→放线→支、吊架制作安装→阀门检验→管道焊接安装→酸洗、钝化→系统试压→管道清洗a.不锈钢管焊接工艺:焊接母材:不锈钢管,壁厚δ=1.5-2mm,材质304焊接材料:不锈钢焊丝,φ1.5-2.0mm,材质304焊接形式:手工无填充氩弧自熔焊(管道全充气)钨极规格:φ=2.0mm焊机电流:60~160A焊机氩气流量:9~20ml/s管内氩气流量:根据焊工操作手法而定。
质量标准:焊缝外观与母体表面平齐,呈鱼鳞状,无氧化、气孔、裂纹凸凹表面熔合、错边等缺陷,焊缝宽度为母材厚度的2倍左右。
单面焊接双面成形。
内壁要求:光滑,与母体内壁平齐,其它同上。
焊接检验及质量控制:焊接质量检验包括焊接前、焊接过程中和焊接结束后三个过程,一般应注意以下几点:(1)对多层焊接来说焊缝外观检验应在外行尺寸范围内,焊缝余高1~2mm,焊缝宽度约为坡口宽度,大于坡口两侧1~2mm,表面不得有气孔、裂纹等。
(2)焊缝边缘与母材应圆滑过渡,全部焊缝应成形美观。
(3)无损检验探伤按照国家标准执行。
(4)质量控制除前面所述之外,还应遵守下列原则:①严禁在焊件上引弧、试电流等。
②多层焊时接头应错开,收弧时将弧坑填满。
③采用氩弧焊时保证焊接一次完成。
④焊接完毕后清除焊缝及焊接时飞溅等杂物。
⑤认真填写焊接工作记录等有关焊接表格。
b、操作工艺:将对接两部件的两个端面用坐拐尺卡校修磨绝对平齐、垂直,达到两端面靠近后无透视线为准,多焊点将两端面点焊牢固,距焊缝两端加堵成腔,调整好充气气压和焊机气压,使充气处于流动状态。
将管内空气排净后再施焊。
对于管道内充氩气一般采用的方法有:①采用堵板将管道焊件两头堵上,用氩气胶管把氩气送入管内,被焊管件内的氩气纯度达到焊接要求时方可进行施焊,压力流速为0. 3―0.5升/分钟。
②采用速溶纸将管道焊件离焊口30mm处堵上,从焊口处用氩气胶管直接送气到管内,以达到氩弧焊接条件要求,完成焊接。
不锈钢管件标准
不锈钢管件标准不锈钢管件是一种广泛应用于工业、建筑和家居等领域的管道连接件,其质量和标准对于工程项目的安全和稳定至关重要。
以下将介绍不锈钢管件的相关标准,以便大家更好地了解和选择合适的产品。
首先,不锈钢管件的材质标准是非常重要的。
通常情况下,不锈钢管件的材质应符合国家标准GB/T14976-2002和GB/T14975-2002的要求。
这两项标准分别规定了不锈钢无缝管和不锈钢焊接管的材质和化学成分,确保了管件的耐腐蚀性和机械性能。
其次,不锈钢管件的尺寸标准也是至关重要的。
根据国家标准GB/T12459-2005和GB/T13401-2005,不锈钢管件的尺寸应符合相关的公称直径、壁厚和长度要求,以保证管道连接的密封性和稳定性。
在选择不锈钢管件时,需要根据具体工程需求和管道规格来确定合适的尺寸标准。
另外,不锈钢管件的加工工艺标准也需要引起重视。
国家标准GB/T12459-2005和GB/T13401-2005规定了不锈钢管件的加工工艺要求,包括热压成型、冷挤压、焊接等工艺流程,以确保管件的内部结构和表面质量符合相关标准,保证了管件的使用寿命和安全性。
此外,不锈钢管件的检验标准也是不可忽视的。
根据国家标准GB/T3728-2008和GB/T3729-2008,不锈钢管件的检验应包括外观检查、尺寸检查、化学成分分析、力学性能测试等内容,以保证管件的质量符合相关标准要求,确保了工程项目的安全和可靠性。
总的来说,不锈钢管件的标准涉及材质、尺寸、加工工艺和检验等多个方面,这些标准的制定和执行对于保障工程项目的质量和安全具有重要意义。
在选择不锈钢管件时,需要严格按照相关标准要求进行选型和采购,以确保管道连接的稳定性和可靠性。
希望本文能够帮助大家更好地了解不锈钢管件的标准,为工程项目的顺利进行提供参考和指导。
钢制管件制造工艺规范
钢制管件制造工艺规范(MPS文件)目录1 范围 (2)2 规范性引用文件 (2)3 制造工艺流程 (3)4 管件基本参数 (4)5 原材料要求 (5)6 制造工艺要求 (6)7 性能要求 (15)8 几何尺寸、形状允许偏差 (16)9 工艺质量和缺陷处理 (18)10 检验和试验 (18)11 设计验证试验 (22)12 标志 (24)13 防护与包装 (24)14 产品质量合格证明书 (25)1 范围1.1 本文件规定了山东港联化董家口港-潍坊-鲁中、鲁北输油管道工程管(一期)管件采购项目用L245N、L360M、L450M等材质钢制管件生产的基本参数、原材料、制造工艺、材料性能、几何尺寸与允许偏差、工艺质量与缺陷修补、检验与实验、标志、涂层与保护、质量证明书及装运的要求。
1.2 本MPS文件应和GB/T 12459-2005《钢制对焊无缝管件》、GB/T 13401-2005《钢板制对焊管件》、GB/T 19326-2012《钢制承插焊、螺纹和对焊支管座》标准及D1630D-GI00-PR01-SP14《清管三通技术规格书》一起使用,凡是出现与GB/T 12459-2005 《钢制对焊无缝管件》、GB/T 13401-2005 《钢板制对焊管件》、GB/T 19326-2012《钢制承插焊、螺纹和对焊支管座》标准及D1630D-GI00-PR01-SP14《清管三通技术规格书》相冲突的条款,应以最严格的为准。
2 规范性引用文件下列文件中的条款通过本文件的引用而成为本文件的条款。
凡是注日期的引用文件,其随后所有的修改单(不包括勘误的内容)或修订版均不适用于本文件,然而,鼓励根据本文件达成协议的各方研究是否可使用这些文件的最新版本。
凡是不注日期的引用文件,其最新版本适用于本文件。
GB 150 钢制压力容器GB/T 223 钢铁及合金化学分析方法GB/T 228 金属材料室温拉伸试验方法GB/T 229 金属材料夏比摆锤冲击试验方法GB/T 232 金属材料弯曲试验方法GB/T 9711-2011 石油天然气工业管线输送系统用钢管GB/T 10561 钢中非金属夹杂物显微评定方法GB/T 12459-2005 钢制对焊无缝管件GB/T 13401-2005 钢板制对焊管件GB/T 19326-2012 钢制承插焊、螺纹和对焊支管座GB 50251 输气管道工程设计规范GB 50253 输油管道工程设计规范NB/T 47008-2010 承压设备用碳素钢和合金钢锻件NB/T 47013-2015 承压设备无损检测NB/T 47014-2011 承压设备用焊接工艺JB/T 4711 压力容器涂敷与运输包装SY/T 0609 优质钢制对焊管件规范Q/SY GJX106 油气输送管道工程用DN400及以上管件技术条件ISO 9001 质量管理体系要求API SPEC 5L Specification for Line PipeASTM A370 钢产品机械性能试验的方法和定义ASNT No.SNT-TC-1A 无损检测人员资格资质与认定ASTM E45 钢中夹杂物含量的确定方法TSG Z6002-2010 特种设备焊接操作人员考核细则3 制造工艺流程表3.1 钢板制对焊弯头制造工艺流程表3.2 热推弯头制造工艺流程表3.3 推制弯头制造工艺流程表3.4 模压三通制造工艺流程表3.5 模压三通制造工艺流程表3.6 管帽制造工艺流程表3.7 钢板制对焊异径接头制造工艺流程表3.8 对焊支管座制造工艺流程表3.9 清管三通制造工艺流程4 管件基本参数管件的基本生产参数均需符合山东港联化董家口港-潍坊-鲁中、鲁北输油管道工程管(一期)管件采购项目管件招标文件的要求。
不锈钢风管施工方案
不锈钢风管施工方案1) 不锈钢风管的加工流程不锈钢板风管和管件板材厚度(mm)不锈钢法兰(mm)风管法兰螺栓连接与密封垫粘贴示意图:法兰对接图2) 不锈钢风管安装工艺①风管支吊架的选择及安装风管支吊架间距严格按照设计文件及规范要求执行。
若厂房内公用管架间距大于规范规定值,则采用中间抱箍双吊形式固定在楼板下。
支吊架的固定方式应根据设计文件和施工验收规范确定,风管支(托)架安装必须牢固,应注意下列事项:a.支(托)架应牢固,焊缝饱满,螺孔应采用机加工,与风管接触面应平整。
b.式。
主、干风管长度超过20m 时,按照规范要求设置固定支架。
c.管束及管束垫皮的选择 管束抱箍吊装示意:现场实际安装图片:d.根据风管口径的大小,选择相应的管束规格大小,同时为避免风管表面与管束表面的摩擦,及减少震动,增加牢固性,在管束与风管结合面粘贴橡胶管束垫片。
双吊抱箍双吊抱箍②现场卸货及材料摆放搬运注意事项:a.产品到现场后需要人力及机械进行卸货,搬运,在此过程中要注意对产品进行保护,避免人为操作造成风管的表面及内部破损:b.风管运动指定位置后需要摆放整齐,避免杂乱。
注:所有的管束均需配备橡胶垫皮。
③阀门的安装:a.风阀叶片材质为与风管同材质,外形为流线形,宽度不得小于16.5mm,转轴为不小于10mm之钢轴,转轴两侧为青铜或COATING TEFLON或尼龙制轴衬或滚珠轴承,转轴应可指示风门开度,当风门全关时气密性需良好,风门叶片须有连杆,连接使成八字形风门,此风门与风管连街处须以橡胶圈为垫片。
b.所有风阀应标示全开、全关或正常位置,系统运转时风门在任何开度均不得产生任何震动及噪音。
c.安装前的检查和确认,阀门安装前需最终确认所安装阀门的形式、大小、位置是否正确。
d.在安装前操作手柄及执行机构检查动作是否灵活,有无卡死现象。
e.安装时需要注意气流方向和手柄位置,在不影响功能的情况下,尽量把阀门手柄位置留在方便操作的地方。
- 1、下载文档前请自行甄别文档内容的完整性,平台不提供额外的编辑、内容补充、找答案等附加服务。
- 2、"仅部分预览"的文档,不可在线预览部分如存在完整性等问题,可反馈申请退款(可完整预览的文档不适用该条件!)。
- 3、如文档侵犯您的权益,请联系客服反馈,我们会尽快为您处理(人工客服工作时间:9:00-18:30)。
不锈钢管件制造工艺流程
下料成形(焊接)热处理表面处理切削加工无损检测表面防护标志
① 下料
管件所用材料主要为管子、板材和棒材,根据材料特性和产品所用坯料的形状选择下料方法。
坯料的形状、尺寸和其它要求根据不同产品的工艺规定进行。
对于管子,常用的下料方法有带锯床或弓锯床切割、气割、等离子切割。
对于板材,常用的下料方法有气割、等离子切割、冲床冲切。
对于棒材,常用的下料方法有带锯床或弓锯床切割、冲剪切割。
② 成形(焊接)
对所有管件的制造工艺来说,成形是其不可缺少的工序。
因不同产品的成形工艺不尽相同,需要的篇幅较长,将在第15.2.4节中另外予以描述。
这里,对部分成形工序中所包括的加热及焊接作一概略介绍。
a.. 加热
对采用热成形方法制造管件而言,为满足成形工艺中对材料变形的要求,成形时需要对坯料进行加热。
加热温度通常视材料和工艺需要确定。
热推弯头或热弯弯管成形时,通常采用中频或高频感应加热的方法,也有采用火焰加热的方法。
这种加热方式是与弯头或弯管成形过程同步进行的连续加热,管坯在运动中被加热并完成成形过程。
热压弯头、热压三通或锻件成形时,通常采用反射炉加热的方法、火焰加热的方法、感应加热的方法或电炉加热的方法等。
这种加热是先行将管坯加热到所需要的温度,再放入模具中压制或锻制成形。
b. 焊接
带焊缝的管件包括两种情况,一种是用焊管制造的管件,对管件制造厂来说,采用焊管的成形工艺与采用无缝管的成形工艺基本相同,管件成形过程不包括焊接工序;另一种是由管件制造厂完成管件成形所需要的焊接工序,如单片压制后再进行组装焊接成形的弯头、用钢板卷筒后焊接成管坯再进行压制的三通等。
管件的焊接方法常用的有手工电弧焊、气体保护焊以及自动焊等。
制造厂应编制焊接工艺规程用以指导焊接工作,并应按相应规范要求进行焊接工艺评定,以验证焊接工艺规程的正确性和评定焊工的施焊能力。
从事管件焊接作业的焊工应通过质量技术监督部门的考试并取得相应资质证书方可从事相关钢种的焊接工作(根据一些行业的规定,用于一些行业的焊接管件要取得行业规定的焊工考试和焊接工艺评定,如船用管件的焊接要取得相应船级社的焊工考试和焊接工艺评定)。
③ 热处理
热处理工序是管件制造的重要组成部分。
通过加热、保温及冷却的热处理步骤,消除成形过程产生的加工硬化、残余应力、金属变形缺陷等,使成形后管件的金属组织、性能发生变化,恢复到变形加工前的状态或使其性能得到改善和提高。
常用的热处理装备为反射炉、电炉等;通常的控制方式为炉内的热电偶通过传感器连接到温度-时间自动记录仪的控制装置上进行。
不同的管件产品标准中对热处理的规定不尽相同。
并非所有经过变形的管件均要进行热处理,通常,对于低碳钢材料的管件其最终成形温度不低于723℃(再结晶温度)时,可不用进行热处理,因在此温度条件下其最终的组织状态基本上是正火状态,低于这一温度或高于980℃时应进行热处理;合金钢或不锈钢材料的管件不论采用冷成形或热成形,均应进行热处理。
对热处理的常规检验一般通过硬度试验完成。
④表面处理
管件的表面处理通常采用喷砂、抛丸、打磨、酸洗等方法进行,以清除产品表面的锈蚀,划痕等,使产品达到光滑的表面,满足后续加工、检验的要求。
对采用抛丸进行表面处理的管件,其表面硬度会略有增加。
⑤ 切削加工
切削加工是完成管件的焊接端部、结构尺寸、形位公差加工的工序。
对有的管件产品切削加工还包括内、外径的加工。
切削加工主要通过专用机床或通用机床完成;对于尺寸过大的管件,当现有机床能力无法满足加工要求时,还可以用其它方法完成加工,例如大口径弯头采用的气割后打磨的方法。
管件的外观、尺寸检验通常在切削加工后进行。
⑥ 无损检测
无损检测是检验材料和管件加工过程可能出现的缺陷的重要工序。
多数管件产品标准中对于无损检测的要求进行了规定,但要求不尽一致。
除满足产品标准规定和订货要求进行无损检测外,一些对质量控制较为严格的制造厂还根据材料、加工工艺和内部质量控制规定制定无损检测要求,以保证出厂产品的质量。
实际工作中管件无损检测合格等级的判定应根据订货要求或标准的明确规定。
因管件的表面基本上为原管、板或锻件状态,对管件表面质量的无损检测(MT、PT)而言,如无明确等级要求可按Ⅱ级,但不论合格等级如何规定,对于夹层和裂纹这种不易判定深度的缺陷均应视为不合格。
对管件内部质量的无损检测(RT、UT、)而言,如无明确等级要求射线检测应按Ⅱ级(例如焊缝的检测),超声波检测应按Ⅰ级。
为防止热处理过程中产品可能出现的缺陷的情况,管件最终的无损检测应在热处理之后进行。
我国管件制造厂无损检测通常使用的是JB/T 4730规范。
从事无损检测工作的人员应按有关规定取得相应资格。
⑦ 表面防护
对碳钢、合金钢管件的表面防护通常采用涂漆的方法,对不锈钢采用酸洗后钝化的方法(对于全部表面切削加工的不锈钢管件,可不必钝化处理)。
管件表面防护的主要目的是防腐,同时也达到产品外表美观的效果。
通常,订货方对表面防护提出具体要求,制造厂按订货方的要求完成管件表面的防护。
⑧ 标志
标志是产品不可或缺的组成部分,是实现可追溯性要求的依据。
通常,产品标准中对标志内容和方法进行了规定。
管件的标志内容一般包括制造厂商标或名称、材料等级、规格以及订货要求的其它内容。
标志的方法包括永久性标志,如钢印、雕刻、电蚀等;非永久性标志,如喷印、标签等。
⑨ 其它
除上述常规的制造工艺流程以外,为控制原材料质量,制造厂还应完成原辅材料的检验,确保所用材料的正确;为满足订货或材料的特殊要求,还应进行如金相组织、晶间腐蚀、铁素体等检验和试验,保证提供的产品满足顾客的使用要求。
碳当量越大,被焊材料的淬硬倾向越大,焊接区域容易产生冷裂纹。
碳当量与焊接热影响的淬硬及冷裂纹倾向之所以有关,是因为:
碳当量大时在焊接热影响区易产生淬硬的马氏体组织,对裂纹和氢淬敏感。
淬硬会形成更多的晶格缺陷,在焊缝中应力和热力不平衡的条件下,晶格缺陷会称为裂纹源,增加了焊缝中形成冷裂纹的倾向。
较低的碳含量使得在靠近焊缝的热影响区中所析出的碳化物减至最少,而碳化物的析出可能导致不锈钢在某些环境中产生晶间腐蚀(焊接侵蚀)。
由于含碳量过饱和,引起马氏体强度和硬度提高、塑性降低,脆性增大。
碳在不锈钢中具有两重性,因为碳的存在能显著扩大奥氏体组织并提高钢的强度,
而另一方面钢中碳含量增多会与铬形成碳化物,即碳化铬,使固溶体中含铬量相对减少,大量微电池的存在会降低钢的耐蚀性。
尤其是降低抗晶间腐蚀能力,易使钢产生晶间腐蚀,
对导致硬度加大和更脆弱的焊接性能
钢中含碳量增加,屈服点和抗拉强度升高,但塑性和冲击性降低,当含碳量超过0.23%时,钢的焊接性能变坏,因此用于焊接的低合金结构钢,含碳量一般不超过0.20%。
碳量高还会降低钢的耐大气腐蚀能力,在露天料场的高碳钢就易锈蚀;此外,碳能增加钢的冷脆性和时效敏感性。
碳(c):不锈钢管中含碳量增加,屈服点和抗拉强度升高,但塑性和冲击性降低,当碳量0.23%超过时,不锈钢管的焊接性能变坏,因此用于焊接的低合金结构钢,含碳量一般不超过0.20%。
碳量高还会降低钢的耐大气腐蚀能力,在露天料场的高碳钢就易锈蚀;此外,碳能增加不锈钢管的冷脆性和时效敏感性。
碳偏移,造成贫铬,形成晶间腐蚀。