齿轮测量中心参数
3903t齿轮测量中心内齿轮的测量方法

3903T齿轮测量中心内齿轮的测量方法3903T齿轮测量中心内齿轮的测量方法随着齿轮行业的发展,内齿轮精度的测量日益受到重视。
39xxT 系列齿轮测量中心可用特定附件安装固定被测量的内齿轮,再用内齿测杆,测头装置使测头与被测齿面倒向接触,再选用内齿轮测量软件,虽然能够测量内齿轮,但是对一些操作人员不得其要点艰难操作。
本文将重点介绍在39xxT系列齿轮测量中心测量内齿轮需要注意的问题及操作步骤,供大家参考。
1.测量原理3903T齿轮测量中心是哈尔滨量具刃具集团开发的一种新型的智能化的齿轮测量仪,是采用电子展成法,长、圆光栅数字定位采样,智能化微机控制的全自动循环测量系统。
用其来测量齿轮的齿形、齿向和齿距。
除了能测量圆柱齿轮外,还可以测量滚刀、剃齿刀、插齿刀、涡轮滚刀、齿轮滚刀、涡轮、涡杆、内齿轮等。
测量时被测齿轮由计算机控制,在机械传动机构的作用下,开始旋转,测头贴靠在被测齿面上,从起测点到齿顶从而完成一个齿面齿形的测量。
齿距和齿向的测量原理同齿形基本相同。
主轴的旋转角度、测头的移动量是通过主圆光栅和R轴(切向)光栅精确控制再由计算机通过数学模式计算比较得出测量结果,并且能按相应的精度等级要求自动进行评定,由LED图形显示出来并可打印测量报告单。
2.操作实例以一个内齿圈为实例。
齿轮参数:模数为5m,齿数为49,压力角为20°,齿宽为60mm,变位系数为0.235,螺旋角为0°,基圆半径为115.1123mm,齿顶圆直径为237.76mm,精度等级为ISO-1328-7级。
测量步骤如下:(1)开启仪器第一步:打开电源,将仪器的电源线与供电电源连接,如仪器电柜面板上的红色按钮指示灯亮起,表明仪器已与供电电源接通;第二步:开启计算机,进入windows操作系统;第三步:仪器上电,按绿色启动按钮,仪器各电器部件上电,红色按钮指示灯灭,绿色按钮指示灯亮,仪器各电器部件已上电;第四步:拔起急停按钮,利用面板上的操纵杆对各轴进行手动操作;第五步:点击DearCenter系统图标,进入齿轮测量系统人机界面。
齿轮参数的测定实验报告

齿轮参数的测定实验报告引言齿轮是机械传动中常用的零件,其使用范围广泛,从小型日用品到大型工业机械都需要使用到齿轮。
在齿轮的设计和制造过程中,需要对齿轮参数进行精确的测定。
通过测定齿轮参数,可以确保齿轮的精度和可靠性,满足不同工作条件下的要求。
本实验旨在通过实验方法对齿轮参数进行测定,从而了解不同齿轮参数对齿轮运动学特性的影响。
实验原理1.齿轮齿数计算齿轮齿数是齿轮的基本参数之一。
常见的计算方法有齿轮齿数比计算和模数计算两种。
齿轮齿数比计算需要通过输入齿轮的齿数,再通过给出的齿轮齿数比计算得到另一齿轮的齿数。
模数计算需要先给出齿轮的模数,再通过齿轮齿数计算得到齿轮的分度圆直径。
2.齿轮齿廓测量齿轮齿廓是齿轮的重要性能参数之一,其测量需要用到螺旋测量仪。
通过螺旋测量仪,可以得到齿轮齿廓曲线的三维坐标数据。
通过对齿轮齿廓曲线进行计算和比较,可以评价齿轮的齿廓精度和几何误差。
3.齿间角测量齿间角是齿轮参数中的一个重要参数,直接影响到齿轮的传动精度。
通过齿间角的测量,可以评估齿轮的传动性能和齿间配合情况。
实验步骤根据测定到的齿轮分度圆直径,通过模数计算测得齿轮齿数,将齿轮齿数记录下来。
通过给定的齿轮齿数比,可计算出另一齿轮的齿数。
通过齿间角测量器对齿轮齿间角进行测量,并记录齿间角的数值。
实验结果与分析通过实验测量得到齿轮的齿数、齿廓、齿间角等参数,得到如下数据:齿轮1的齿数为20,模数为1.5mm,齿廓误差为±0.01mm,齿间角为22.5度。
通过计算机对齿轮齿廓进行比较分析,得到齿轮1和齿轮2的齿廓精度都较高,且几何误差较小。
通过齿间角的测量,发现齿轮1和齿轮2的齿间角都符合设计要求。
可以认为齿轮1和齿轮2均符合齿轮设计要求,并且具有一定的传动精度。
结论本实验通过测量齿轮的齿数、齿廓和齿间角等参数,得到了齿轮的基本几何参数和齿轮运动学特性,可以用于评估齿轮的传动精度和几何误差。
实验结果表明,齿轮齿数、齿廓和齿间角对齿轮的传动精度和齿轮工作状态有着重要的影响。
齿轮测量参数详解

齿轮测量参数详解齿轮是一种常见的机械传动元件,广泛应用于各种机械设备中。
为了确保齿轮传动的正常运行,需要对齿轮的一些参数进行测量和评估。
本文将详细介绍齿轮测量参数及其意义。
我们来了解一下齿轮的基本参数。
齿轮的基本参数包括模数、齿数、压力角、齿宽等。
模数是指齿轮齿数与齿轮外径之比,它决定了齿轮齿面的形状和尺寸。
齿数是指齿轮上齿的数量,它决定了齿轮的传动比。
压力角是指齿轮齿面与齿轮轴线之间的夹角,它影响了齿轮的传动效率和噪声水平。
齿宽是指齿轮齿面的宽度,它决定了齿轮的承载能力和传动平稳性。
我们需要测量齿轮的几何参数。
齿轮的几何参数包括齿高、齿顶高、齿根高、齿距、齿厚等。
齿高是指齿轮齿面到基圆的距离,它决定了齿轮的强度和刚度。
齿顶高是指齿轮齿面到齿顶的距离,它决定了齿轮的接触性能和传动效率。
齿根高是指齿轮齿面到齿根的距离,它决定了齿轮的承载能力和传动平稳性。
齿距是指相邻两齿顶之间的距离,它决定了齿轮的传动精度和噪声水平。
齿厚是指齿轮齿面的厚度,它决定了齿轮的强度和刚度。
然后,我们需要测量齿轮的配合参数。
齿轮的配合参数包括齿隙、啮合度、啮合角等。
齿隙是指两个啮合齿轮齿面之间的距离,它决定了齿轮的自由度和传动平稳性。
啮合度是指两个啮合齿轮齿面的配合程度,它决定了齿轮的传动效率和噪声水平。
啮合角是指齿轮齿面与齿轮轴线之间的夹角,它决定了齿轮的传动效率和噪声水平。
我们需要评估齿轮的质量参数。
齿轮的质量参数包括齿面粗糙度、齿轮硬度、齿轮材料等。
齿面粗糙度是指齿轮齿面的表面粗糙程度,它影响了齿轮的噪声水平和传动效率。
齿轮硬度是指齿轮材料的硬度水平,它决定了齿轮的耐磨性和承载能力。
齿轮材料是指齿轮的制造材料,它影响了齿轮的强度、刚度和耐磨性。
齿轮测量参数对于确保齿轮传动的正常运行至关重要。
通过测量和评估齿轮的参数,可以了解齿轮的几何形状、配合性能和质量状况,为齿轮的设计、制造和使用提供依据。
因此,对齿轮的参数进行准确、全面的测量和评估是非常必要的。
伞齿轮齿厚测量参数表

伞齿轮齿厚测量参数表引言伞齿轮是一种传动元件,通常用于减速器、齿轮箱等机械设备中。
齿厚是伞齿轮的重要尺寸参数之一,它的准确测量对于确保齿轮传动正常运转至关重要。
本文将详细介绍伞齿轮齿厚测量的参数表。
伞齿轮齿厚测量参数表伞齿轮齿厚测量参数表是一个系统记录伞齿轮齿厚测量参数的表格。
通过对伞齿轮进行测量并记录相关数据,可以了解齿轮的尺寸精度、制造工艺以及装配质量等方面的信息。
表头说明伞齿轮齿厚测量参数表的表头应包含以下信息: 1. 伞齿轮型号:记录伞齿轮的型号信息; 2. 齿轮编号:标识每个齿轮的唯一编号,方便对照和查询; 3. 测量员:记录进行齿厚测量的测量员姓名; 4. 测量日期:记录进行齿厚测量的日期。
主要参数列伞齿轮齿厚测量参数表的主要参数列应包含以下信息: 1. 齿轮位置:记录齿轮在伞齿轮系统中的位置,如第一级、第二级等; 2. 齿轮齿数:记录齿轮的齿数,用于计算齿轮模数; 3. 齿厚测量值:记录测得的齿厚值; 4. 齿厚公差:记录齿厚的公差范围,与设计要求相比较,评估齿厚尺寸的偏差情况; 5. 测量设备:记录用于齿厚测量的设备名称或型号; 6. 测量方法:记录齿厚测量的具体方法,包括测量位置、测量原理等; 7. 测量结果评定:记录对测量结果的评定,如合格、不合格等。
表格示例下面是一个简化的伞齿轮齿厚测量参数表的示例:伞齿轮型号齿轮编号测量员测量日期齿轮位置齿轮齿数齿厚测量值(mm)齿厚公差(mm)测量设备测量方法测量结果评定XYZ-001 G001 张三2021-01-01第一级50 5.00 ±0.10 数字千分尺直接测量法合格XYZ-001 G002 李四2021-01-01第一级50 4.95 ±0.10 数字千分尺直接测量法合格XYZ-001 G003 王五2021-01-01第一级50 5.05 ±0.10 数字千分尺直接测量法合格伞齿轮齿厚测量参数表的应用与意义伞齿轮齿厚测量参数表的应用与意义主要表现在以下几个方面:齿轮质量控制通过对伞齿轮齿厚进行测量并记录参数,可以及时掌握齿轮的尺寸精度情况。
哈量Econ30型齿轮测量中心

73WMEM·2020年 第5期产品推介哈量: Econ30型齿轮测量中心哈尔滨量具刃具集团有限责任公司Econ30(3003A)型齿轮测量中心是哈量集团遵循可靠性设计开发理念,采用模块化设计和控制手段,开发的一款应对市场需求的样试新产品,也是哈量近期销售主推的新产品。
Econ 30型齿轮测量中心,基本配置软件可以测量圆柱齿轮,可选测量软件有:齿轮滚刀测量软件、蜗轮滚刀测量软件、剃齿刀测量软件、插齿刀测量软件、蜗杆测量软件、蜗轮测量软件、直齿锥齿轮测量软件、斜齿锥齿轮测量软件、弧齿锥齿轮测量软件等,并可按客户要求扩展。
该产品在开发过程中,充分考虑到各类客户的实际需求,功能和精度指标都能达到国内领先水平。
一、产品简介Econ30型齿轮测量中心应用电子展成测量方法,采用长、圆光栅数字定位采样,并配备智能化微机控制(CNC)的全自动测量系统,可全自动完成测量循环;仪器直线轴采用直线电机控制技术,并具有偏心修正功能,在被测齿轮一次装夹中,自动完成齿轮齿廓、螺旋线、齿距及径向跳动等测量项目的检测。
该样机具有结构合理、生产协调性好、控制稳定、产品的性价比高,市场竞争力强等特点和优势。
Econ30型齿轮测量中心在设计思路上综合了哈量小模数齿轮测量中心的原有技术特点和优势,加大了仪器成本和模块化通用型考量力度,启动机械系统模块化设计,缩短加工周期,降低研制成本;对电控系统进行全新设计开发,增强电气系统的稳定性和兼容性,增加功能可扩展性开发,从而实现产品性能提升目标,并切实地降低生产和售后升级维护服务成本。
加大机械、电气和软件联合开发力度,在实现该类齿轮量仪在整体成本合理降低的前提下,进一步增强产品功能优势地位和竞争力,最终实现制造方和市场用户双赢。
设计开发路线方案及目的:(1)机械结构零件采用通用化设计理念,实现模块化生产,减少机加零件种类,降低加工管理成本。
(2)优化电气布线,电器柜、拖链布线实现“倒序”模块化快速布线,将整机布线时间缩短一半 。
齿轮测量实验报告
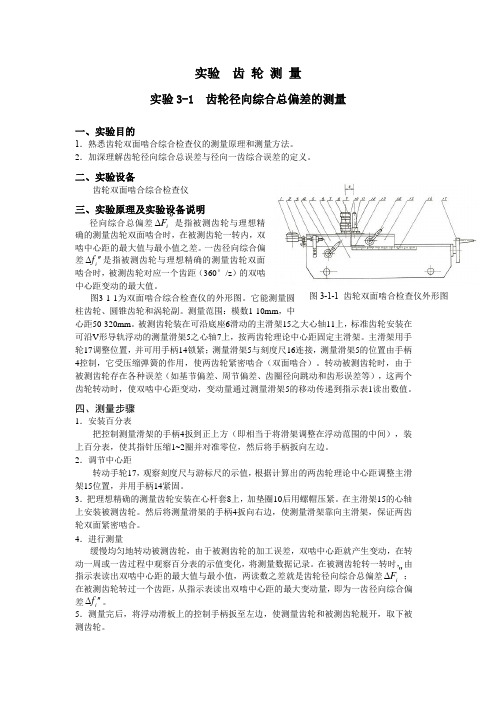
实验 齿 轮 测 量实验3-1 齿轮径向综合总偏差的测量一、实验目的1.熟悉齿轮双面啮合综合检查仪的测量原理和测量方法。
2.加深理解齿轮径向综合总误差与径向一齿综合误差的定义。
二、实验设备齿轮双面啮合综合检查仪三、实验原理及实验设备说明径向综合总偏差"∆i F 是指被测齿轮与理想精确的测量齿轮双面啮合时,在被测齿轮一转内,双啮中心距的最大值与最小值之差。
一齿径向综合偏差i f ''∆是指被测齿轮与理想精确的测量齿轮双面啮合时,被测齿轮对应一个齿距(360°/z )的双啮中心距变动的最大值。
图3-1-1为双面啮合综合检查仪的外形图。
它能测量圆柱齿轮、圆锥齿轮和涡轮副。
测量范围:模数1-10mm ,中心距50-320mm 。
被测齿轮装在可沿底座6滑动的主滑架15之大心轴11上,标准齿轮安装在可沿V 形导轨浮动的测量滑架5之心轴7上,按两齿轮理论中心距固定主滑架。
主滑架用手轮17调整位置,并可用手柄14锁紧;测量滑架5与刻度尺16连接,测量滑架5的位置由手柄4控制,它受压缩弹簧的作用,使两齿轮紧密啮合(双面啮合)。
转动被测齿轮时,由于被测齿轮存在各种误差(如基节偏差、周节偏差、齿圈径向跳动和齿形误差等),这两个齿轮转动时,使双啮中心距变动,变动量通过测量滑架5的移动传递到指示表1读出数值。
四、测量步骤1.安装百分表把控制测量滑架的手柄4扳到正上方(即相当于将滑架调整在浮动范围的中间),装上百分表,使其指针压缩1~2圈并对准零位,然后将手柄扳向左边。
2.调节中心距转动手轮17,观察刻度尺与游标尺的示值,根据计算出的两齿轮理论中心距调整主滑架15位置,并用手柄14紧固。
3.把理想精确的测量齿轮安装在心杆套8上,加垫圈10后用螺帽压紧。
在主滑架15的心轴上安装被测齿轮。
然后将测量滑架的手柄4扳向右边,使测量滑架靠向主滑架,保证两齿轮双面紧密啮合。
4.进行测量缓慢均匀地转动被测齿轮,由于被测齿轮的加工误差,双啮中心距就产生变动,在转动一周或一齿过程中观察百分表的示值变化,将测量数据记录。
最新HT350型齿轮测量中心技术协议
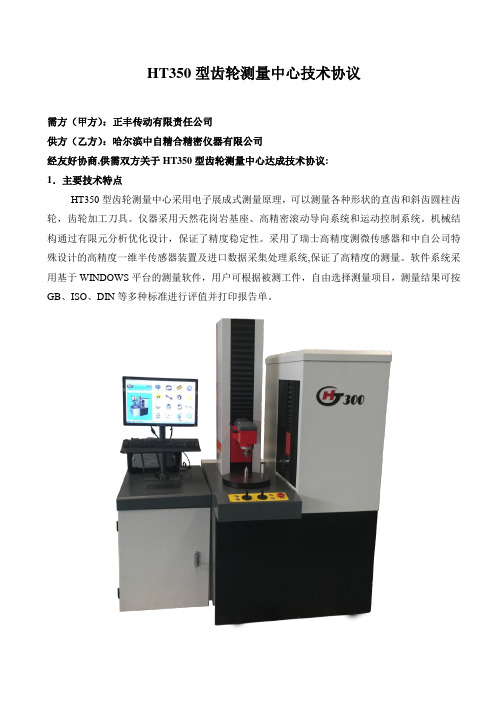
HT350型齿轮测量中心技术协议需方(甲方):正丰传动有限责任公司供方(乙方):哈尔滨中自精合精密仪器有限公司经友好协商,供需双方关于HT350型齿轮测量中心达成技术协议:1.主要技术特点HT350型齿轮测量中心采用电子展成式测量原理,可以测量各种形状的直齿和斜齿圆柱齿轮,齿轮加工刀具。
仪器采用天然花岗岩基座、高精密滚动导向系统和运动控制系统。
机械结构通过有限元分析优化设计,保证了精度稳定性。
采用了瑞士高精度测微传感器和中自公司特殊设计的高精度一维半传感器装置及进口数据采集处理系统,保证了高精度的测量。
软件系统采用基于WINDOWS平台的测量软件,用户可根据被测工件,自由选择测量项目,测量结果可按GB、ISO、DIN等多种标准进行评值并打印报告单。
2.主要测量功能和技术指标2.1 主要测量功能(丰田标准软件格式)1)圆柱齿轮测量误差评值软件(含渐开线花键):a、齿廓(Fα、ffα、fHα、Cα)、螺旋线(Fβ、ffβ、fHβ、Cβ)、齿距(fpt、fu、Fp、Fpk)、齿圈径跳(Fr),齿厚变动量(Rs);b、测量公法线Wk、跨棒距M、齿厚、齿槽宽;c、齿轮参数分析;d、齿轮扭曲分析;e、齿轮齿面三维测量分析;f、齿轮火前火后分析;g、齿轮组测量,一次测量完一个齿轮串上所有齿轮;h、包含多个国家评价标准:G10095-2008、ISO1328-1997、DIN3961/2-1978、AGMA200-88、JISB1702-1998、GB10098-88、JISB1702-1976、GB2363-90小模数标准、DIN5481-1(花键)、DIN5481-15(花键)、ANSI-B92.1-1996(花键)、GB3478.1-1995(花键),客户自定义;2)圆柱内齿轮测量误差评值软件(含渐开线花键):a、齿廓(Fα、ffα、fHα、Cα)、螺旋线(Fβ、ffβ、fHβ、Cβ)、齿距(fpt、fu、Fp、Fpk)、齿圈径跳(Fr),齿厚变动量(Rs);b、测量公法线Wk、跨棒距M、齿厚、齿槽宽;c、齿轮参数分析;d、齿轮火前火后分析;e、齿轮组测量,一次测量完一个齿轮串上所有齿轮;f、包含多个国家评价标准:G10095-2008、ISO1328-1997、DIN3961/2-1978、AGMA200-88、JISB1702-1998、GB10098-88、JISB1702-1976、GB2363-90小模数标准、DIN5481-1(花键)、DIN5481-15(花键)、ANSI-B92.1-1996(花键)、GB3478.1-1995(花键),客户自定义;3)齿轮插刀测量误差评值软件:a、测量项目:刃口齿形、截面齿形、螺旋线、轴向齿距、刀齿前刃面径向性、啮合线、轴台径向跳动、轴台端面跳动、顶刃前角、顶刃后角、切削面跳动等;b、评价标准:JB/T 3095.2、GB/T 6082-2001、DIN1892-1977、客户自定义公差。
齿轮主要参数及测量
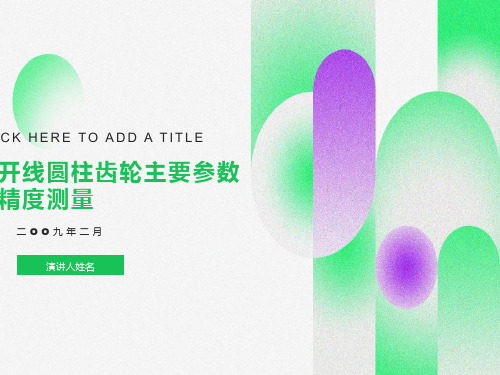
②测量仪器——齿厚卡尺,如图所示。
公法线平均长度偏差(上偏差Ewms、下偏差Ewmi)
ΔEwm =(W1+W2+…WZ)/Z-W公称 定义:在齿轮一周内,公法线平均长度和公称值之差。
不同的齿轮,要求也不同:
低速重载齿轮:侧重载荷分布均匀;
高速齿轮:侧重传动平稳性;
分度齿轮:侧重传动准确性,且传动侧隙要小。
每个公差组都分为12个精度等级,齿厚偏差用C D E F..14个代号表示
第Ⅰ公差组——控制传递运动的准确性 第Ⅱ公差组——控制传动的平稳性、噪声、振动等 第Ⅲ公差组——控制载荷分布均匀性
01
(4)切向综合误差ΔFi´
(5)径向综合误差ΔFi" (公差Fi")
①定义:被测齿轮与理想精确的测量齿轮双 面啮合时,在被测齿轮一转内,双 啮中心距的最大变动量。
②测量:双啮仪,如图所示。
齿距累积误差ΔFp;
径向综合误差ΔFi"与公法线长度变动ΔFw ;
齿圈径向跳动ΔFr与公法线长度变动ΔFw ;
测量仪器——渐开线检查仪
01
04
02
03
基节偏差Δfpb(基节极限偏差±fpb)
定义:实际基节和公称基节之差。
一齿切向综合误差Δfi´(需要时,加检齿距 偏差Δfpt);
测量仪器——基节仪 在评定传递运动平稳性时,根据齿轮传动的用途、生产及检验条件,在下列方案中任选之一即可。
齿形误差Δff与齿距偏差Δfpt ;
渐开线圆柱齿轮主要参数 及精度测量
CLICK HERE TO ADD A TITLE
- 1、下载文档前请自行甄别文档内容的完整性,平台不提供额外的编辑、内容补充、找答案等附加服务。
- 2、"仅部分预览"的文档,不可在线预览部分如存在完整性等问题,可反馈申请退款(可完整预览的文档不适用该条件!)。
- 3、如文档侵犯您的权益,请联系客服反馈,我们会尽快为您处理(人工客服工作时间:9:00-18:30)。
ZD-KG03-09 右旋 20 1.375 35°
8 37°0′ 33°50′ 29°0′
1.04 1.69 2.47 0.45
0 20.1 29.23 25.07 1.01 1.43 0.06 0.12
加工方法
大圆弧齿轮精切机床调整参数
加工方法 切齿机床型号 机床安装根锥角 水平轮位修正量 床位 垂直轮位 偏心角 摇台角 分齿跳齿数 滚比挂轮齿数(A) 滚比挂轮齿数(B)
铣齿法
滚比挂轮齿数(C) 滚比挂轮齿数(D)
齿轮测量中心测量大小圆弧所需要的各项齿轮基本参数
ZD-KG03-08 左旋 16
螺旋角 凸面压力角 凹面压力角 齿面宽 面锥角 节锥角 根锥角 齿顶高 齿根高 工作齿高 面锥定点超过错交点的距离 根锥顶点超过错交点的距离 轮冠至错交点之距离 外端直径 安装距 法向弦齿齿顶高 法向弦齿厚 小轮偏置距 轴交角 安装基面类型 加工方法
35°
8 30°33′ 26°10′ 20°40′
1.43 1.3 2.47 0.52 0 21.62 24.56 24.62 1.33 1.59
60
小圆弧齿轮精切机床调整参数-凹面
切齿机床型号 机床安装根锥角 水平轮位修正量 床位 垂直轮位 偏心角 摇台角 分齿跳齿数 滚比挂轮齿数(A) 滚比挂轮齿数(B) 滚比挂轮齿数(C)
YX10Z
滚比挂轮齿数(D)
小圆弧齿轮精切机床调整参数-凸面
切齿机床型号 机床安装根锥角 水平轮位修正量 床位 垂直轮位 偏心角 摇台角 分齿跳齿数 滚比挂轮齿数(A) 滚比挂轮齿数(B) 滚比挂轮齿数(C) 滚比挂轮齿数(D)
YX10Z
大小圆弧所需要的各项参数
大圆弧齿轮基本参数
零件图号 旋向 齿数 模数 螺旋角 凸面压力角 凹面压力角 齿面宽 面锥角 节锥角 根锥角 齿顶高 齿根高 工作齿高 面锥定点超过错交点的距离 根锥顶点超过错交点的距离 轮冠至错交点之距离 外端直径 安装距 法向弦齿齿顶高 法向弦齿厚 最小齿侧间隙 最大齿侧间隙