切削用量的三要素
切削运动及切削用量三要素
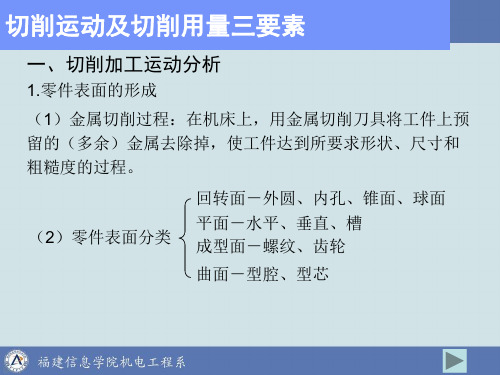
目的:保证零件的加工精度和表面质量的同时考虑刀具耐用度和生产率 选择:根据表面粗糙度的要求选择较小进给量;切削速度要避免产生积屑 瘤,硬质合金刀具采用较高的切削速度,高速钢刀具采用较低的切削速度
综上所述,在保证加工质量的条件下,首先选尽可能大的吃刀量, 其次选用尽可能大的进给量,最后选尽可能高的切削速度。
切削运动及切削用量三要素
一、切削加工运动分析
2.切削运动分类
(2)进给运动:使金属不断投入切削ห้องสมุดไป่ตู้加工出完整表面的运动。速度较低、 消耗功率较少,即可连续,也可间歇,可以没有,有一个或多个。 进给运动方向:是指切削刃选定点相对于工件的瞬时进给运动方向。
切削运动及切削用量三要素
一、切削加工运动分析
2.切削运动分类
影响刀具强度的最大因素是背吃刀量,其次是进给量,最小的 是切削速度;
影响表面质量的最大因素是进给量,其次是切削速度,最小的 是背吃刀量。
切削运动及切削用量三要素
2、切削用量的合理选择
(1) 粗加工
目的:提高生产率,尽快切去全部加工余量,并保证规定的刀具耐用度。 选择:应选取较大的背吃刀量,较大进给量,使余量尽量一次切完,选择 较低或中等切削速度。
切削运动及切削用量三要素
二、切削要素
3、切削层尺寸要素
(1)切削层公称厚度hD mm
hD=f*sinkr
(2)切削层公称宽度bDmm
bD=ap/sinkr
(3)切削层公称横截面积ADmm2
√材料切除率Q mm3/s
切削运动及切削用量三要素
三、车削加工工艺特点及应用
• (1)易保证工件各加工面的位置精度 • (2)加工范围广 • (3)生产率高
切削用量三要素对加工效率的影响

一
下, 在机床 刚度、刀 片形状 允许 时, 粗加工 切深应
在保 留半精 加 工、精 加工 余 量后, 尽 量一 次 切除。 如果 总加工余 量太大 ,一次切 去所有 加工余量 会产
生 明显 的振动 ,甚至 刀具强度 不允许 、机 床功 率不
够,则 可分成 两次或 几次粗加 工。但 第一次切 削深
切 削参数 选择 的合理与 否对切 削加工 的生产效 率、加 工成本 以及保 障产 品的质量 至关重 要,采用
度应尽 量大, 以消除表 面硬皮, 切除 沙眼气孔 等缺
陷,从 而保护 刀尖不 与毛坯接 触。半精 加工和 精加
工,其切削深度是根据加 工精度 和表面粗糙度要求,
由粗 加工后 留下余量 确定 的。最 后一 次切削深 度不 宜太小,否则会产生刮擦,影响加工表面的粗糙度。
四 、切 削用量 三要素 与刀具 耐用度之间的关系 要使 切削 时间最短, 即材料 去除 量最大, 必须
~将切 削速度
使 V C ,f ,a p的乘 积 为最大 。提高 V c ,f , 8 _ p 都 能
提 高 生产率。但 是对 刀具耐用 度的影 响三者是 不相
或进给量逐一调升。
二 进 给 量 f( mm/ r )或 F ( mm/ mi n ); 工 件 或 刀具 的每一转或每一往 复行程 的时间内,刀具与工 件之 间沿进给运动方 向的相对位移。
表面粗糙度理论值 R m a x 计 算公 式 :
F2
Rma x =二 _ 一 x] 0 0 0 (H )
8
先尽 量选用最大 吃刀深 a p( 要考虑 到机床功率及 零 件装 夹刚性满足的条件下) ,然后根据加 工条件选 用 最大 的进给量 f ,最后 才在 刀具耐 用度 或机 床功率所 允许 的情况 下选取最大切 削速度 V c 。
机械制造(第2版)第二章课后习题解答
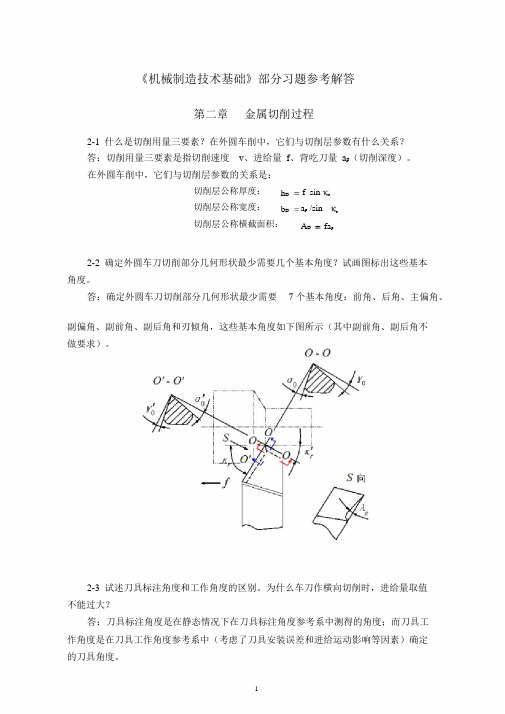
Fc
C a f v K x Fc pFc
yFc n
c Fc
sFc
900 31 0.4 0.75 80 0 1.0 1358N
Fp
xFp
yFp nFp
CFpap f vc K sFp
530 3 0.9 0.4 0.75 80 0 1.5 1075N
Ff
xFf
yFf nFf
CFf ap f vc K sFf
450 31 0.4 0.4 80 0 0.75 702N
再根据 p38公式(2-17),可得切削功率 P c Fcvc 10 3 1358 80/ 60 10 3 1.81 KW
2-11 影响切削力的主要因素有哪些?试论述其影响规律。 答:(P41-42)影响切削力的主要因素有工件材料、切削用量、刀具几何参数、刀具 磨损、切削液和刀具材料。 工件材料的影响:工件材料强度、硬度越高,切削力越大; 切削用量的影响:背吃刀量 ap影响最大,几乎成正比; f 次之,v 最小。
2-13 试分析刀具磨损四种磨损机制的本质与特征,它们各在什么条件下产生? 答:(P47)刀具磨损四种磨损机制的本质和特征: 硬质点划痕:工件材料有硬质点,造成机械磨损,有划痕、划伤。 冷焊磨损:即粘接磨损,在高压高温作用下,刀具材料被粘接、撕裂,导致磨损。 扩散磨损:在高温下刀具材料中金属原子扩散,导致材料软化磨损。 化学磨损:由于化学腐蚀、氧化作用产生的磨损。
2-6 怎样划分切削变形区?第一变形区有哪些变形特点? 答:切削形成过程分为三个变形区。第一变形区切削层金属与工件分离的剪切滑移 区域,第二变形区前刀面与切屑底部的摩擦区域;第三变形区刀具后刀面与已加工表面 的摩擦区域。 第一变形区的变形特点主要是:金属的晶粒在刀具前刀面推挤作用下沿滑移线剪切 滑移,晶粒伸长,晶格位错,剪切应力达到了材料的屈服极限。
机械制造技术基础题库

一、填空1.切削用量的三要素是、、。
2.卧式车床共有传动链4条,其中外传动链条,内传动链条。
3.切削塑性材料,切削变形,切削脆性材料,切削变形。
4.在刀具几何参数中,对刀具耐用度影响较大的是角和角。
5.选择切削用量的顺序是先选,后选,最后选。
6.切削力的来源来自切削层变形和变形的变形抗力与刀具前、后面的力。
7.车外圆时,刀尖高于工件中心则会使工作前角、工作后角。
刀尖低于工件中心则会使工作前角、工作后角。
8.加工塑性金属材料前角加工脆性金属材料时前角。
9.粗加工时,切削用量一般以提高、降低为主。
精加工时,应以保证为主,兼顾与。
10.车内孔时,刀尖高于工件中心则会使工作前角、工作后角。
低于工件中心则会使工作前角、工作后角。
11.工件材料强度相同时,和越高,切削变形越大,切屑与工件对刀具间增加,切削力会越大。
12.材料的强度、硬度越高,前角越,材料塑性越大,前角越。
13.机床夹具由装置、装置、和组成。
14.铣刀方向与工件方向相反称铣削方式。
15.刀具材料分为、、、四大类。
16.切削塑性金属时,切削速度,使切削温度升高,摩擦系数,切削力也随之。
17.粗加工时选择前角,精加工时选择前角。
18.刀具材料应具备、、、。
19.前角增大,切削变形,故切削力也。
20.选择后角的原则是:在不产生的条件下,应适当后角。
21.传统的制造系统可以概括地分为、、三个组成部分。
22.加工钢材料常用类硬质合金,加工铸铁和有色金属常用类硬质合金。
23.主偏角增大,进给力,而背向力则。
24.精加工时,后角取值,粗加工时,后角取值。
25.拉刀是一种、的多刃刀具。
其使用寿命,结构,制造成本。
26.在机床的成形运动中,根据切削过程所起作用不同可分运动和运动。
27.短圆柱销可限制个自由度。
长圆柱销可限制个自由度。
菱形销可限制个自由度。
圆锥销一般只能限止个自由度。
窄V形块限止个自由度。
长V形块限止个自由度。
28.机械加工工艺系统由、、、四要素组成。
切削用量三要素的定义及公式

切削用量三要素的定义及公式好的,以下是为您生成的关于“切削用量三要素的定义及公式”的文章:在咱们日常的机械加工领域中,切削用量三要素那可是相当重要的角色。
这就好比是烹饪中的盐、糖和酱油,用量合适,才能做出美味的菜肴;在机械加工里,切削用量三要素调配恰当,才能加工出合格又精致的零件。
咱先来说说切削速度,这可是三要素中的“速度担当”。
切削速度就是刀具切削刃上选定点相对于工件的主运动的瞬时速度。
想象一下,你拿着一把锋利的刀,快速地在一块木头上划过,这个划过的速度就是切削速度。
公式是 v = πdn/1000 ,这里的 v 表示切削速度,d 是工件待加工表面或刀具的最大直径,n 是主运动的转速。
给您举个小例子吧,我之前在工厂实习的时候,有一次师傅让我加工一个圆柱形的零件。
我一开始没太注意切削速度,就按照自己的想法随便调了机器的转速。
结果呢,加工出来的零件表面那叫一个粗糙,简直没法看。
师傅过来一看,就指出是切削速度不对。
后来在师傅的指导下,我重新计算并调整了切削速度,加工出来的零件那表面光滑得跟镜子似的,我当时心里那个美啊!接下来聊聊进给量,它就像是你一步一步往前走的步伐大小。
进给量是刀具在进给运动方向上相对工件的位移量。
用 f 来表示,单位通常是 mm/r 或者 mm/行程。
比如说车床上车削螺纹,每转一圈刀具沿着轴向移动的距离就是进给量。
有一回,我们车间接到一个紧急订单,要加工一批细小的轴类零件。
我负责其中一部分,为了赶进度,我把进给量调得过大。
结果零件的尺寸偏差超出了允许范围,差点就造成了损失。
这让我深刻认识到,进给量可不能随意乱调,得根据具体的加工要求来。
最后说说背吃刀量,这是刀具切入工件的深度。
就好比你切西瓜,切下去的厚度就是背吃刀量。
用 ap 表示,单位是 mm 。
记得有一次,我在加工一个比较厚的金属板,一开始背吃刀量设置得太小,加工效率特别低,半天也没弄出个样子来。
后来我大胆地增加了背吃刀量,效率一下子就提上去了,但同时也要注意刀具的承受能力,不能一味地加大,不然刀具可能会受损。
金属切削的基础知识

机械制造基础习题一、填空题1.切削用量三要素指的是切削速度、进给量、背吃刀量2.在金属切削过程中,切削运动可分为主运动和进给运动。
其中主运动消耗功率最大,速度最高。
3.金属切削刀具的材料应具备的性能有高的硬度和耐磨性、足够的强度和韧性、高的耐热性和良好的散热性、良好的工艺性与经济性。
4.刀具在高温下能保持高硬度、高耐磨性、足够的强度和韧性.则该刀具的热硬性较高。
5.前刀面和基面的夹角是前角,后刀面与切削平面的夹角是后角,主切削刃在基面上的投影和进给方向之间的夹角是主偏角,主切削刃与基面之间的夹角是角刃倾角。
6.刀具角度中,影响径向分力Fy大小的角度是主偏角。
因此,车削细长轴时,为减小径向分力作用,主偏角常用75°或90°。
7.车外圆时,刀尖高于工件中心,工作前角变大,工作后角变小。
8.切削过程中影响排屑方向的刀具角度是刃倾角,精加工时,刃倾角应取正值。
9.积屑瘤产生的条件是用中等速度切削塑性材料且能形成带状切屑时。
避免积屑瘤的产生,主要控制切削用量中的切削速度。
10.在切削用量中,影响切削力大小最显著的是背吃刀量,影响切削温度大小最显著的是切削速度。
11.切削用力常分解到三个相互垂直的方向上:主切削力与主切削刃上某点的切削速度方向一致;与工件轴线平行的为进给抗力;与工件半径方向一致的是切深抗力力。
12.从提高刀具耐用度出发,粗加工时选择切削消量的顺序应是背吃刀量、进给量、切削速度。
13.孔加工中,镗床主要用于箱体类零件上孔系的加工。
14.在拉削加工中,主运动是拉刀的旋转,进给运动是靠拉刀的齿升量来实现的。
15.合理的刀具耐用度(寿命)包括最高生产率寿命与最低成本寿命两种。
16.转位车刀的切削性能比焊接车刀好(好,差),粗加工孔时,应选择麻花钻(拉刀、麻花钻)刀具。
17.当主偏角增大时,刀具耐用度增加(增加,减少),当切削温度提高时,耐用度减少(增加、减少)。
18.当工件材料硬度提高时,切削力增加(增加,减少);当切削速度提高时,切削变形减少(增加、减少)。
什么是合理的切削用量

•
3)刀具材料的切削性能越好时,切削速度也可选得 越高。因此,硬质合金刀具的切削速度可选得比高 速钢高度好几倍,而涂层硬质合金、陶瓷、金刚石 个立方氧化硼刀具的切削速度又可选得比硬质合金 刀具高许多。 此外,在确定精加工、半精加工的切削速度时, 应注意避开积屑瘤和鳞刺产生的区域; 在易发生振动的情况下,切削速度应避开自激震动 的临界速度, 在加工带硬皮的铸锻件时,加工大件、细长件和薄 壁件时,以及断续切削时,应选用较低的切削速度。
切削速度υc的选择
• 在ap和f选定以后,可在保证刀具合理耐用度的条件下, 用计算的方法或用查表法确定切削速度υc的值。在具体确 定υc值时,一般应遵循下述原则:
•
1)粗车时,切削深度和进给量均较大,故选择较低的 切削速度;精车时,则选择较高的切削速度。 2)工件材料的加工性较差时,应选较低的切削速度。 故加工灰铸铁的切削速度应较加工中碳钢低,而加工铝合 金和铜合金的切削速度则较加工钢高得多。
• 在选择切削用量时,考虑的侧重点也应有 所区别。 • 粗加工时,应尽量保证较高的金属切除率 和必要的刀具耐用度,故一般优先选择尽 可能大的切削深度ap,其次选择较大的进 给量f,最后根据刀具耐用度要求,确定合 适的切削速度。 • 精加工时,首先应保证工件的加工精度和 表面质量要求,故一般选用较小的进给量f 和切削深度ap,而尽可能选用较高的切削 速度υc。
• •
前刀面磨损
(2)后刀面磨损 如图所示,在切削刃参加切削工作的各 点上,一般后刀面磨损是不均匀的。在后刀 面磨损带中间部位的B区上,磨损比较均匀, 平均磨损带宽度以VB表示,而最大磨损带宽 度以VBmax表示。加工脆性材料时,由于形 成崩碎切屑,一般出现后刀面的磨损;切削 塑性材料时,当切削速度较低,切削厚度较 薄时较容易产生后刀面的磨损。
切削用量三要素

根据已选定的背吃刀量ap、进给量f及刀具耐用度T,就可 按公式计算切削速度Vc和机床转速n。
切削用量及选择
① 粗车时,ap 、f均较大,所以Vc较低,精加工时,ap 、f均较小, 所以Vc较高。
② 工件材料强度、硬度较高时,应选较低的Vc;反之,Vc较高。 材料加工性越差,Vc较低。
对于粗加工来说,要尽可能保证较高的金属切除率和必要 的刀具耐用度。
提高切削速度,增大进给量和背吃刀量,都能提高金属切除率。但在
这三个因素中,影响刀具耐用度最大的是切削速度,其次是进给量,影 响最小的是背吃刀量。所以,在选择粗加工切削用量时,应优先考虑采
用大的背吃刀量,其次考虑采用大的进给量,最后才能根据刀具耐用度 的要求,选定合理的切削速度。
由此可见,选择切削用量的基本原则是首先选取尽可能大 的背吃刀量;其次要在机床动力和刚度允许的范围内,同时又满 足已加工表面粗糙度的要求的情况下,选取尽可能大的进给量, 最后利用《切削用量手册》选取或用公式计算确定最佳切削速度。
切削用量及选择
3.2 切削用量三要素的确定
(1)背吃刀量的选择
背吃刀量根据加工余量确定。
切削用量及选择
半精加工、精加工时首先要保证加工精度和表面质量, 同时应兼顾必要的刀具耐用度和生产效率,此时的背吃刀量 根据粗加工留下的余量确定。为了减小工艺系统的弹性变形, 减小已加工表面的残留面积,半精加工尤其是精加工,一般 多采用较小的背吃刀量和进给量。为抑制积屑瘤和鳞制的产 生,用硬质合金刀具进行精加工时一般多采用较高的切削速 度;高速钢刀具则一般多采用较低的切削速度。
已加工表面和待加工表面间的垂直距离,单位为mm。
对于外圆车削的深度可用下式计算:
ap=(dw-dm)/ 2 mm