精益生产方式简介(中英文翻译)
精益生产的管理资料——英汉互译

Drive and implement Lean manufacturing across the operations in order to eliminate waste, minimize inventory and maximize flow• Develop procedures in partnering with suppliers in order to achieve Lean manufacturing• Reducing system response time and ensure the production system was capable of immediately changing and adapting to market demands.• Required to collect and analyze data for determining an improvement strategy.• Facilitate and teach Lean manufacturing tools and techniques. Coach existing and new teams with Lean projects.• Ability to strategically prioritize and manage process improvement opportunities in alignment with business goals and objectives.• Working hand in hand with internal six-sigma expert in developing and drive Lean Sigma.• Acts as change agent to instill Lean Sigma culture throughout organization• Must have the ability to lead, work with teams, and understand team dynamics.OEE(Overall Equipment Effectiveness) --- 全局设备效率OEE = (Running time / Loading time) x (Actual Output / Theoretical output) x (Good Output / Actual output)世界级企业的全局设备效率OEE为85%或更好。
精益生产中英文互译
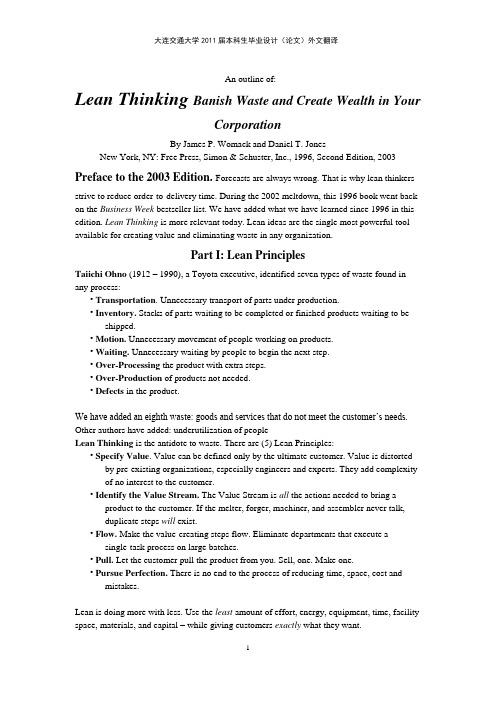
An outline of:Lean Thinking Banish Waste and Create Wealth in YourCorporationBy James P. Womack and Daniel T. JonesNew York, NY: Free Press, Simon & Schuster, Inc., 1996, Second Edition, 2003 Preface to the 2003 Edition. Forecasts are always wrong. That is why lean thinkersstrive to reduce order-to-delivery time. During the 2002 meltdown, this 1996 book went back on the Business Week bestseller list. We have added what we have learned since 1996 in this edition. Lean Thinking is more relevant today. Lean ideas are the single most powerful tool available for creating value and eliminating waste in any organization.Part I: Lean PrinciplesTaiichi Ohno (1912 – 1990), a Toyota executive, identified seven types of waste found in any process:• Transportation. Unnecessary transport of parts under production.• Inventory. Stacks of parts waiting to be completed or finished products waiting to be shipped.• Motion. Unnecessary movement of people working on products.• Waiting. Unnecessary waiting by people to begin the next step.• Over-Processing the product with extra steps.• Over-Production of products not needed.• Defects in the product.We have added an eighth waste: goods and services that do not meet the customer’s needs. Other authors have added: underutilization of peopleLean Thinking is the antidote to waste. There are (5) Lean Principles:• Specify Value. Value can be defined only by the ultimate customer. Value is distorted by pre-existing organizations, especially engineers and experts. They add complexity of no interest to the customer.• Identify the Value Stream. The Value Stream is all the actions needed to bring a product to the customer. If the melter, forger, machiner, and assembler never talk,duplicate steps will exist.• Flow. Make the value-creating steps flow. Eliminate departments that execute a single-task process on large batches.• Pull. Let the customer pull the product from you. Sell, one. Make one.• Pursue Perfection. There is no end to the process of reducing time, space, cost and mistakes.Lean is doing more with less. Use the least amount of effort, energy, equipment, time, facility space, materials, and capital – while giving customers exactly what they want.The Prize We Can Grasp Now. Converting a batch-and-queue system to continuous flow, with pull, will:Double labor productivity• Cut throughput time by 90%• Reduce inventory by 90%• Cut errors by 50%• Cut injuries1: ValueA House or a Hassle-Free Experience? Doyle Wilson Homebuilder found that customers “valued” a hassle-free design process and on-time delivery. All his processes were thenre-aligned to meet this goal.Define Value in Terms of the Whole Product. As the product flows, each firm defines value differently. Think of air travel. Each firm – agent, airline, taxi, currency exchange, customs, immigration – defines their own priorities, duplicates efforts, and works in disharmony with the whole process. The customer is not satisfied.2: The Value StreamThe View from the Aisle. A value stream “map” identifies every action to design, order, and make a specific product. Each step is then sorted into three categories: (1) those that add value, (2) those that add no value but are currently necessary, and (3) those that add no value and can be eliminated. After the third category has been eliminated, the second category should be addressed through flow, pull, and perfection techniques.The Value Stream for a Carton of Cola. The British grocery chain Tesco retails products with thousands of value streams. In the canned cola value stream, three hours of value-added activity take 319 days to perform.3: FlowThe World of Batch-and-Queue. Five-sixths of home-building is waiting for the next set of specialists or rework. Flow principles typically cut half the effort and the time required.The Techniques of Flow. The 1st step is to maintain focus on the product. The 2nd step is to ignore job boundaries and departments IOT remove impediments to continuous flow of the specific product. The 3rd step is to rethink work practices to eliminate backflow, scrap, and stoppages IOT make the product continuously.• Takt time synchronizes the rate of production to the rate of sales. (48) bikes per day sold divided by (8) hours of production = (6) bikes and hour, or (1) bike every tenminutes.• Flow requires all workers and machines to be capable at all times. This requires cross-training.• Flow requires workers to know the status of production at all times. This requires visual controls.• All activities can flow. Concentrate on the value stream for a specific product, eliminateorganizational barriers, and relocate and right-size tools.4: PullPull means that no one upstream should produce anything until the customer downstream asks for it. “Don’t make anything until it is needed, then make it very quickly.” “Sell one, buy one.” “Ship one, make one.”The Bad Old Days of Production. The Toyota bumper replacement system suffered long lead times. The ability to get parts quickly from the next upstream producer enabled re-orders in small amounts. This is the secret to reducing inventory. Cut lead times and inventories. Demand should instantly generate new supply.5: PerfectionThe Incremental Path. Freudenberg-NOK, a gasket manufacturer, improved a single process six times in three years. “Why didn’t they get is right the first time?” Because perfection is continuous.Continuous Radical and Incremental Improvement. If you are spending capital, you are doing it wrong. Once leaders understand the first four lean principles – value specification, value stream identification, flow, andpull – their perfection step starts with policy: a vision of the ideal process, and the step-wise goals and projects to get there. Transparency is everything. Everyone must know what you are attempting to achieve and what area is the first priority. The force behind this is the leader known as the change agent.Part II: From Thinking to Action: The Lean Leap6: The Simple CaseLantech manufacturers stretch wrap machines. “Process Villages” – Sawing department, Machining department, Welding department, Painting department, and Sub-assembly department – all generated long lead times. Batches of ten were manufactured to ship one. Inventory overwhelmed the factory. Order changes created havoc in the plant. “The more inventory yo u have, the less likely you will have the part you need.”• The Lean Revolution. Ron Hicks leaned Lantech. He created four cells, one for each product. He defined standard work: on time, on spec, every time. Takt time wasintroduced: number of products needed per day divided by number of hours (8/8 = 1hour). He right-sized machines to fit inside work cells. He implemented quickchangeover to make multiple different parts with little machine downtime.• Result. Lantech cut 30% excess space, doubled product output, cut defects from 8 per product to 0.8 per product, and cut lead time from sixteen weeks to fourteen hours.On-time shipping rose from 20 to 90%.7: A Harder CaseThe Change Agent. Art Byrne was hired as CEO of Wiremold in 1991. “CEOs are timid to change the shop floor.” Byrne led lean training using a manual he wrote himself. He led toursof the plant to observe waste that his managers were now able to see.• Improvements Must be Fast. Three days was Byrne’s standard.• Post a Scorecard for Each Product Team. Wiremold tracked: Productivity – sales per employee, Service – percent delivered on-time, Inventory – turns, and Quality –mistakes.• Teach People How to See. Create a lean training function. Teach all employees the five principles of lean: Value, Value Stream, Flow, Pull, and Perfection. Teach allemployees lean techniques: standard work, takt time, visual control, pull scheduling,and single-piece flow.• Results. Wiremold freed 50% factory floor space, eliminated a warehouse, and converted $11M of inventory into $24M in sales. Lead time fell from four weeks totwo days.8: The Acid TestPratt & Whitney (P&W). In 1991, CEO Karl Krapek and cost-cutter Mark Coran leanedP&W.• Jet Engines. Founded in 1860, P&W led the aircraft engine business by 1929. When they abandoned piston engines to gamble on jets in 1946, business soared. Production inefficiencies were overlooked.• Overcapacity. Faced with competition in the 1980s, P&W rationalized plant layout and addressed development costs. They needed lower production costs and flexibility toreact to customer needs. Why did P&W need so much space, tools, inventory andpeople to get so little done? Daily output of engines and spare parts could fit insideCEO’s office. Failure to manage ass ets. P&W cut people, cut managers, andoverhauled their entire production culture and processes.• The Monument of all Monuments. A “monument” is a machine or process too big to be moved and whose scale requires operating in batch mode. Monuments are evil, generating huge amounts of waste. P&W had an $80M grinding system, representing obsolete thinking. Although speeding up grinding from 75 minutes to 3 minutes and eliminating multiple manual grinding jobs, in actuality grinding jobs took longer (due to eight-hour changeovers and batch scheduling), and required more people (22 computer technicians). P&W retired the $80M monument, returned to 75-minute production.9: Lean Thinking versus German TechnikPorche. Chairman Wendelin Wiedeking introduced lean thinking to Porche. In 1994, the first-ever Porsche rolled off the line with nothing wrong with it.• Engineers. Porche is led by engineers, intrigued with unique solutions that are difficult to manufacture. Workers are craftsmen. Unfortunately, much craftsmanship is waste.Tinkering with the product – repairing and polishing raw materials, troubleshooting,re-assembling elements, repainting and re-fitting – were thought to be necessaryactivities to produce a high-quality product.• Crisis. 1986 was the boom year. 1992 was the crash. Porche products were tooexpensive. Costs and throughput time had to be slashed. New quality focus: “Stopfixing mistakes that should never have been made.” Reduction in inventory: “Whereis the factory? This is the warehouse!”• Just-in-Time (JIT) Game. Porche asked all their suppliers to play a simulation to learn lean concepts. Lean concepts were critical across all firms contributing to the Porche value stream.• The Remarkable Lean Transition at Porche. In five years, through 1997, Porch doubled its productivity, cut manufacturing space in half, cut lead time for a finished vehicle from six weeks to three days, cut supplier defects 90%, cut inventories 90%,and cut first-time-through errors by 55%.• The German Tradition. The Germans need to stop prioritizing the engineer’s definition of value, “voice of the engineer,” over the customer’s definition of value,“voice of the customer.” A German weakness is a fondness for monster machines that produce large batches: paint booths are an example.• Variety and Refinement Cost. Volkswagen makes four exterior mirrors, nineteen parts each, in seventeen colors. Nissan has four-part mirrors in four colors. Excess varietyoften exceeds the ability of the customer to notice, and his willingness to pay.10: Mighty Toyota; Tiny ShowaShowa has been transformed by its relationship with Toyota. Showa, a radiator manufacturer, had “Process villages” for casting, cleaning, stamping, welding, painting and assembly. Each was run in batch mode with long intervals between tool changes. Mountains of parts were transported and stored between steps.• The Initial Struggle. Taiichi Ohno, lean advisor, promised to reduce three months ofinventory to three days, double labor productivity, and halve plant space for zerocapital investment. This he did.• The Final Element: Rethinking Order-Taking and Scheduling. Showa then leanedorder-taking by scheduling backwards, working to takt time, to synchronize orderswith production slots, exactly four days before shipment time. Orders with incorrectinformation were never passed along.• Toyota Today. Lesson: high-tech automation only works if the plant can run at 100percent output and if the cost of indirect technical support and high-tech tools is lessthan the cost of direct labor saved.Part III: Lean Enterprise11: A Channel for the Stream; a Valley for the ChannelThe Lean Enterprise. No one watches the performance of the whole value stream. Identify all actions to bring a product to the customer, across all firms. There is no privacy. Eachfirm’s costs become transparent.12: Dreaming About PerfectionLong-Distance Travel. Each organization ignores the role of the other parties. The time, cost, and comfort of the total trip are key performance measures. What would travel times be without queues?Construction. 80% of home building is hurry-up and wait, then re-working the construction errors.The Prize We Can Grasp Right Now. Lean thinking can boost productivity while reducing errors, inventories, accidents, space requirements, production lead times, and costs in general. Lean thinking requires little capital.Part IV: Epilogue13: A Steady Advance of Lean ThinkingThis chapter an updated review of Wiremold, Toyota, Porsche, Lantech, and Pratt & Whitney.14: Institutionalizing the RevolutionAn Enhanced Action Plan is the 2003 update to the 1996 plan from Chapter 11.Getting Started [Months 1 – 6]• Find a Change Agent with ability and authority.• Get the Knowledge through an advisor. Start at the big picture before addressing small steps.• Seize a Crisis or create one. Focus on fixing an obvious problem. Small wins. Don’t spend money.• Map your current value streams. Managers need to see. Map also the flow of information going upstream to create a closed circuit. See Rother and Shook, Leaning to See, 1998.• Analyze each step of the Current State. Does this step create value? Is this step capable, available, flexible? Is capacity sufficient? Excessive? Does theinformation flow from the customer smoothly? Every process has a box score:total lead time, value creating time, changeover time, uptime, rework, inventory,every part made every x minutes. If this step went away, what would happen?• Envision the Future State. Draw it.• Begin as soon as possible with an important, visible activity. Convert managers with hand-on activity.• Demand Immediate Results. Everyone should see results which create psychological momentum. One week: less planning, more doing. Identify the waste and remove it.Communicate with your people by showing results at the scene of action.Creating an Organization to Channel Your Streams [Months 6 – 24]• Reorganize Your Firm by product and value streams. Put a Change Agent in charge of each product.• Create a Lean Promotion Team.• Deal with Excess People Early.• Devise a Growth Strategy.• Remove the Anchor Draggers.• When You’ve Fixed Something, Fix It Again.• New: Convince Your Suppliers and Customers to Take the Steps Just Described.Install Business Systems to Encourage Lean Thinking [Months 24 – 48]Create new ways to keep score.• Create new ways to reward people.• Make everything transparent so everyone can see progress.• Teach lean. Learn lean.• Right-size Your Tools to insert directly into the value stream. Large and fast is more efficient but less effective. This wrong assumption is the cornerstone ofbatch-and-queue thinking.• Pay a bonus. Tie bonus amount to the profitability of the firm.Completing the Transformation [Months 48 – 60] Convert to bottom-up initiatives. Lean ideas are democratic and not top-down. Layers of management can be stripped away.New: Convert From Top-Down Leadership to Bottom-Up Initiatives. Toyota gets brilliant results from average managers using brilliant procedures. Competitors get mediocre results from b rilliant managers using mediocre procedures. Don’t search for brilliant managers. Perfect your processes.Reviewer’s CommentsIn 1988 James Womack first described Toyota as a “lean” corporation. Womack and co-writer Daniel Jones described the Toyota Production System (TPS) in The Machine That Changed the World. In 1990, the two toured companies in Europe, North American, and Japan presenting ideas on how to convert mass production practices to lean practices. Lean Thinking, first published in 1996, is a survey of the lean movement. It clearly describes the waste found in mass production, explains the five principles of lean thinking, and then draws lessons from real companies who have successfully implemented lean ideas. Lean Thinking is not a technical how-to text on production, but an enlightened overview of top-level lean ideas and applications. This updated edition includes lessons that the authors have collected between 1996 and 2003, especially the concept of a lean enterprise – a collection of companies working lean together to produce a single product with the least wasted effort and capital. The book is well-written, researched, and organized, and the authors make a strong case that lean is universal and will benefit any organization in any endeavor. Lean thinking and practices are the single most powerful tool for eliminating waste in any organization.中文翻译概述精益思想去除浪费,并在贵公司创造财富由詹姆斯P.沃麦克和丹尼尔T.琼斯纽约编写,纽约:自由出版社,西蒙与舒斯特公司,1996年。
2精益生产介绍

精益生産 的特點是消除一切浪費,追求精益求精和不斷 改善。去掉生産 環節中一切無用的東西,每個工人及其崗 位的安排原則是必須增值,撤除一切不增值的崗位。精簡 是它的核心,精簡産 品開發設計、生産、管理中一切不 産 生附加值的工作,旨在以最優品質、最低成本和最高效 率對市場需求作出最迅速的回應.
水平的1/10; 4 工廠佔用空間—最低可減至採用大量生産 方式下的1/2; 5 成品庫存最低可減至大量生産 方式下平均庫存水平的 1/4; 6 産 品質量—可大幅度提升;:
精益生産 方式是徹底地追求生産 的合理性、高效性,能夠靈 活 術,地其生基産本適原應理各和種諸需多求方的法高,質對量製産造業品具的有生積産極技的術意和義管。理精技益55
前置時間(Lead time) 爲 此要消除中間停滯,實現“零”停
精益生産 方式的優越性及其意義: 與大量生産 方式相比,日本所採用的精益生産 方式的優越
性主要表現在以下幾個方面: 1.所需人力資源--無論是在産 品開發、生産 系統,還是工
廠的
其他部門,與大量生産 方式下的工廠相比,最低能減至1/2; 2 新産 品開發周期—最低可減至l/2或2/3; 3 生産 過程的在製品庫存最低可減至大量生産 方式下一 般
精益生產的目標: Q:ty,品質; C:Cost,成本; D:Delivery,交貨期;
精益生產的目標就是實現短交期、低成本、高質量.
精益生產目標與企業現場管理目標是完全一致的.
其目標是精益求精,盡善盡美,永無止境的追求 七個零的終極目標。
“零浪費”爲 精益生産 終極目標,具體表現在PICQMDS 七個方面
爲 優化目標。
66
(2)對待庫存的態度不同 大批量生産 方式的庫存管理強調“庫存是必要的惡物”。 精益生産 方式的庫存管理強調“庫存是萬惡之源” 精益生産 方式將生産 中的一切庫存視爲“浪費”,同時 認爲 庫存掩蓋了生産 系統中的缺陷與問題。它一方面強 調供應對生産 的保證,另一方面強調對零庫存的要求,從 而不斷暴露生産 中基本環節的矛盾並加以改進,不斷降低 庫存以消滅庫存産 生的“浪費”。基於此,精益生産 提 出了“消滅一切浪費”的口號。追求零浪費的目標。 (3)業務控制觀不同 傳統的大批量生産 方式的用人制度基於雙方的“雇用”關 係,業務管理中強調達到個人工作高效的分工原則,並以 嚴格的業務稽核來促進與保證,同時稽核工作還防止個人 工作對企業産 生的負效應。 精益生産 源於日本,深受東方文化影響,在專業分工時強 調相互協作及業務流程的精簡(包括不必要的核實工作)
精益生产介绍.
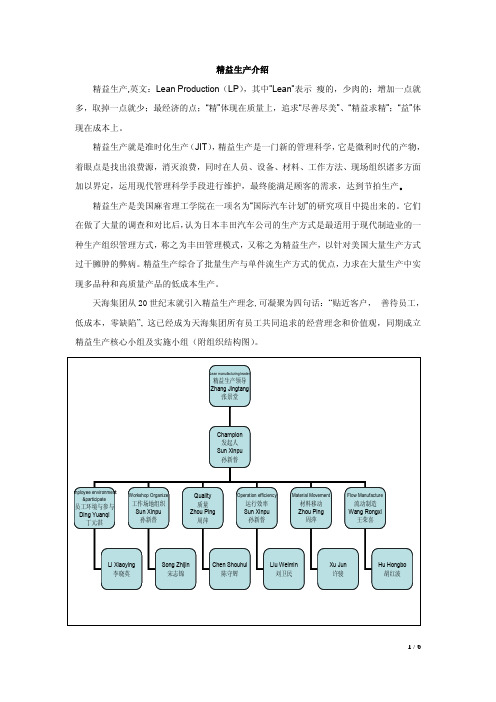
精益生产介绍精益生产,英文:Lean Production(LP),其中”Lean”表示瘦的,少肉的;增加一点就多,取掉一点就少;最经济的点;“精”体现在质量上,追求“尽善尽美”、“精益求精”;“益”体现在成本上。
精益生产就是准时化生产(JIT),精益生产是一门新的管理科学,它是微利时代的产物,着眼点是找出浪费源,消灭浪费,同时在人员、设备、材料、工作方法、现场组织诸多方面加以界定,运用现代管理科学手段进行维护,最终能满足顾客的需求,达到节拍生产。
精益生产是美国麻省理工学院在一项名为“国际汽车计划”的研究项目中提出来的。
它们在做了大量的调查和对比后,认为日本丰田汽车公司的生产方式是最适用于现代制造业的一种生产组织管理方式,称之为丰田管理模式,又称之为精益生产,以针对美国大量生产方式过干臃肿的弊病。
精益生产综合了批量生产与单件流生产方式的优点,力求在大量生产中实现多品种和高质量产品的低成本生产。
精益生产作为一种从环境到管理目标都全新的管理思想,在天海集团所有员工实际与实践努力中取得成功,是一套与企业环境、文化以及管理方法高度融合的管理体系。
精益生产的特点:(1)拉动式准时化生产(Just in time )精益生产是一种流畅制造,是按照顾客的需求节拍来平衡我们的生产节拍,所以如何来平衡我们的生产节拍是我们追求的目标,在一个以顾客为本的制造价值流中,如何快捷高效的满足顾客,我们首推Push 体系,Push 体系实际是一种推动式生产,那是根据顾客的需求,直接安排生产,每道工序完成直接进入下一道工序,中间没有库存,没有等待,最后入库发货的一种没有停顿的生产方式,但这是在生产品种较少,生产批量较大的情况下进行的,也就是说是一种卖方市场的一种产物,但随着市场竞争的加剧,微利时代的来临,没有任何一家公司敢宣称自己的市场是卖方市场,这就要求每生产一种产品要考虑是否顾客需要,生产多少由顾客决定,什么时间生产由顾客决定,JIT (准时化生产)就应运而生,所谓JIT 就是说:在顾客需要的时间,根据顾客需要的量,生产顾客需要的品种。
精益生产常用语英文翻译

精益生产常用语英文翻译精益生产常用语英文翻译精益生产的概念和基本原则The concept and principle of lean production六西格玛品质论坛精益生产的历史:TPS及其演变The history of lean production: TPS and its changing精益生产的原则The principle of lean production:价值和浪费;快速响应客户Value and Muda, quick response 精益生产的思想Lean production thinking追求完美和持续改善Seek perfect and continuous improvement七大浪费 7-Muda精益生产的基础The fundamental of lean production5S的含义The meaning of 5S:整理、整顿、清扫、清洁、素养SEIRI, SEITON, SEISO, SEIKETSU, and SEITSUKE5S的推行方法The implement methods for 5S5S的实务技巧 5S implement skills5S实施过程的优化 5S implement process optimizing流线化生产Flow production流线化生产的八个条件 8-condition for flow production单元设计Cellular layout流线化生产的设备选择Equipment selecting for flow production看板管理Kanban managemento什么是看板What is Kanban看板的实施方法The implement methods for Kanban实施看板管理的限制条件The limited condition of Kanban management implement 快速换线SMED快速换线的理念 The idea of SMED内部作业与外部作业的分离Separate the-operation between outside and inside 将内部作业转化为外部作业Turn the inside-operation to outside operation作业的优化Operation optimizing精益生产的设备管理Equipment management in lean production TPMTPM的概念和发展The concept and development of TPMTPM的设备基础管理Equipment essential management of TPM六西格玛品质论坛TPM的八大支柱8 columns of TPM六西格玛品质论坛TPM实施的十三步骤13 phases for TPM implementing案例分析Case studyo工厂5S分析(根据现场拍摄照片)Workshop 5S analysis (depends on photos taken from on-site)工厂生产线设置分析Production line layout analysis快速换线案例分析Case study for SMED内部作业与外部作业的分离Separate the operation between outside and inside 六西格玛品质论坛将内部作业转化为外部作业Turn the inside operation tooutside operation六西格玛品质论坛精益生产的设备管理Equipment management in lean production TPMTPM的八大支柱8 columns of TPMTPM实施的十三步骤13 phases for TPM implementing案例分析Case study工厂5S分析(根据现场拍摄照片)Workshop 5S analysis (depends on photos taken from on-site)工厂生产线设置分析Production line layout analysis快速换线案例分析Case study for SMED六西格玛品质论坛TPM案例分析 Case analysis for TPM六西格玛品质论坛批量生产与均衡生产Batch production and level production 快速换线的好处The benefits from QCO 换线时间和换线中的浪费Change time and waste in changeover operations内部和外部换线时间Internal and External Change Time换线作业中的浪费Waste in changeover operations消除调整Eliminate adjustment8采用功能化标准Adopt functional standards协同工作Work in parallel换线小窍门Tips for QCO application。
精益生产术语中英文版
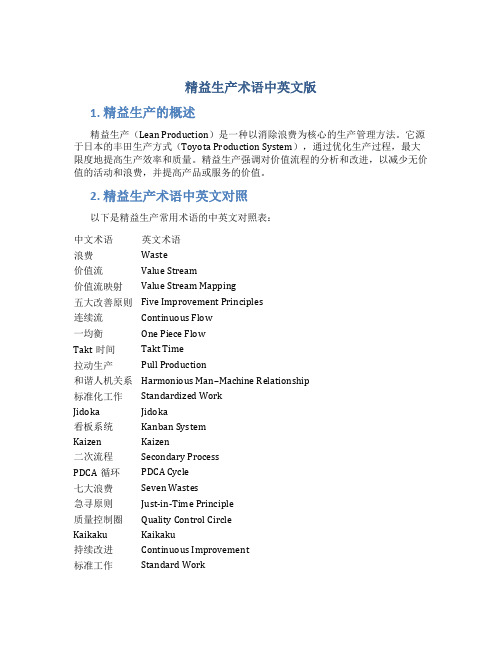
精益生产术语中英文版1. 精益生产的概述精益生产(Lean Production)是一种以消除浪费为核心的生产管理方法。
它源于日本的丰田生产方式(Toyota Production System),通过优化生产过程,最大限度地提高生产效率和质量。
精益生产强调对价值流程的分析和改进,以减少无价值的活动和浪费,并提高产品或服务的价值。
2. 精益生产术语中英文对照以下是精益生产常用术语的中英文对照表:中文术语英文术语浪费Waste价值流Value Stream价值流映射Value Stream Mapping五大改善原则Five Improvement Principles连续流Continuous Flow一均衡One Piece FlowTakt时间Takt Time拉动生产Pull Production和谐人机关系Harmonious Man–Machine Relationship标准化工作Standardized WorkJidoka Jidoka看板系统Kanban SystemKaizen Kaizen二次流程Secondary ProcessPDCA循环PDCA Cycle七大浪费Seven Wastes急寻原则Just-in-Time Principle质量控制圈Quality Control CircleKaikaku Kaikaku持续改进Continuous Improvement标准工作Standard Work3. 精益生产术语解释3.1 浪费(Waste)在精益生产中,浪费指的是任何不增加价值但增加成本和时间的活动。
这些活动是没有必要的,可以被消除或减少。
根据精益生产的理念,浪费被分为七类,即运输、库存、运动、等待、超生产、缺陷和过度加工。
3.2 价值流(Value Stream)价值流是指从原材料到最终产品或服务交付前的所有步骤和活动。
通过分析价值流,可以发现哪些步骤是无价值的或无必要的,并进行优化,以提高整体效率和质量。
精益生产单词翻译(DOC 50页)
精益生产单词翻译(DOC 50页)OEE(Overall Equipment Effectiveness)--- 全局设备效率OEE = (Running time / Loading time) x (Actual Output / Theoretical output) x (Good Output / Actual out put)世界级企业的全局设备效率OEE为85%或者更好。
大多数企业的设备OEE运行在13% 到40%之间。
Labor Linearity 劳动力线性化一种在生产工序特别是一个生产单元中,随着产量的变化灵活调动操作员人数的方法。
按照这种方法,制造每个零件所需仁数,随产量的变化,能够接近于线性。
Lean Enterprise 精益企业一个产品系列价值流的不一致部门同心协力消除浪费,同时按照顾客要求,来拉动生产。
这个阶段性任务一结束,整个企业立即分析结果,并启动下一个改善计划。
Lean Production 精益生产一种管理产品开发、生产运作、供应商、与客户关系的整个业务的方法。
与大批量生产系统形成对比的是,精益生产强调以更少的人力,更少的空间,更少的投资,与更短的时间,生产符合顾客需求的高质量产品。
精益生产由丰田公司在第二次世界大战之后首创,到1990年的时候,丰田公司只需要用原先一半的人力,一半的制造空间与投入资金,生产相同数量的产品。
在保证质量与提高产量的同时,他们所花费的在产品开发与交货的时间,也远比大批量生产更有效益。
“精益生产”这个术语由MIT国际机动车辆项目的助理研究员John Krafcik于20世纪80年代最先提出。
Lean Logistics 精益物流在沿着价值流的各个公司与工厂之间,建立一个能够经常以小批量进行补给的拉动系统。
我们假设A公司一个零售商直接向顾客销售产品,而且从B公司一个制造商大批量、低频率的补给货物。
精益物流将会在零售商A公司安装一个拉动信号,当他售出若干的货物之后,这个信号就会提示制造商,补充相同数量的货物给A,同时制造商会提示他的供应商补充相同数量的原料或者半成品,以此一直向价值流的上游追溯。
精选精益生产LEANPRODUCTION
减少库存的有力措施是变“批量生产、排队供应” 为单件流生产。单件流生产(1-Piece-Flow) 只有一个生产件在各道工序间流动,整个生产过程随单件流的进行而永远流动理想情况:相邻工序间没有在制品库存
同步——在不间断的连续生产流程中,必须 平衡生产单元内每一道工序,要求 完成每一项操作致相同的时间
计算如下:
(取4个工作台,尚有生产能力剩余)
规划精益生产单元的布置。 实际设计生产精益生产单元时,可以考虑设置两个铣、钻、磨加工区,每个加工区由两个工作台组成,每个工作台配备一个工人
上图是严格按照Tact Time为45秒,每小时生产80单位而设计的生产单元。包装、装配线1、铣/钻/磨等都有一定生产剩余,所以瓶颈是装配线2。如果要加大生产量,可把装配线2的工作适量的分配给包装、装配线1,或提高生产率,降低装配线2的生产时间来解决
步骤1:计算单件产品生产时间 (Tact Time)
步骤2:计算符合单件产品生产时间每小时的生产量
步骤3:计算每道工序的每小时的生产能力,以及每道工序所需工作台的数目
包装
(取一个工作台,尚有生产能力剩余)
装配线2:
(取4个工作台)
装配线1:
(取2个工作台,尚有生产能力剩余)
铣、钻、磨:这几道工序有长有短,必须平衡各道工序的劳动利用率。设置一个微型加工单元,把铣、钻、磨有机地结合起来,并且只要一个工人完成这三项操作。 完成这三道工序所需时间为170秒。每小时可完成21.2单位的产品。
消除停机时间 全面生产维修(TPM)是消除停机时间最有力的措施, 它包括例行维修、预测性维修、预防性维修和立即维修四种基本维修方式
例行维修——操作工和维修工每天所作的 维修活动,定 期对机器进行保养
精益生产方式lean production
工厂八大浪费之三
3.动作的浪费 3.动作的浪费 现场作业动作不合理造成的浪费。
①.物品取放、反转、对准等不合理。 物品取放、反转、对准等不合理。 ②.作业时转身、大幅度动作。 作业时转身、大幅度动作。 ③.抬臂过高、过低等。 抬臂过高、过低等。
… …
工厂八大浪费之四
4.搬运的浪费 4.搬运的浪费 物料的放置、堆积、移动、整理等浪费。
及 时 生 产
看 板
品 质 保 证
目 视 管 理
精益生产方式推进顺序2 精益生产方式推进顺序2
步骤1:意识改革 步骤1:意识改革 步骤2:5S 步骤2:5S
Edited by
步骤2:流动生产 步骤2:流动生产
舍弃陈旧的想法,采用JIT思想。
JIT改善的基础是整理、整顿、 清扫、清洁、教养等5S
… …
工厂十二个动作的浪费-① 工厂十二个动作的浪费-
1.两手空闲 1.两手空闲 具体操作中,出现两只手均无事可做的时间段的浪费。
2.单手空闲 2.单手空闲 具体操作中,出现两只手均无事可做的时间段的浪费。
3.作业动作停止 3.作业动作停止 具体操作中,因操作顺序不合理等原因导致动作出现停顿的浪费。
精益生产方式体系架构
精益工厂 追求7个“零”极限目标
生 产 的 快 速 与 维 护 精 益 品 质 保 证 与 自 动 化 柔 性 生 产 系 统 均 衡 化 同 步 化 现 场 IE 作 业 研 究 生 产 设 计 与 物 流 系 统 产 品 开 发 设 计 系 统
意识改革*5S
精益工厂追求7 精益工厂追求7个“零”极限目 标
… …
精益生产方式推进顺序9 精益生产方式推进顺序9
看板管理 是作业指示及零件调配的依据。 后工序至前工序拿取已被前工序用毕的看板。 ①.后工序至前工序拿取已被前工序用毕的看板。 ②.前工序只要生产后工序取去的数量。 前工序只要生产后工序取去的数量。 看板与现品一起流动,彻底执行目视管理。 ③.看板与现品一起流动,彻底执行目视管理。 为避免生产误失,消除浪费,生产实施平准化。 ④.为避免生产误失,消除浪费,生产实施平准化。 尽量减少看板的数量。 ⑤.尽量减少看板的数量。
(精益生产)精益生产方式简介(中英文翻译)
精益生产方式简介摘要:精益生产是一种起源于丰田和汽车制造的流水线制造方法论。
也被称为“丰田生产系统”。
精益生产的目标被描述为“在适当的时间(或第仪式间,the first time)使适当的东西到达适当的地点,同时使浪费最小化和适应变化”。
创立了精益生产原则的大野耐一发现他的方法论不但可以减小浪费,还能够增进产品流动和提高质量。
本文对精益生产进行了具体的分析,得出它的优越性,并把它与传统的生产方式进行比较,通过分析可以知道精益生产是解救困难企业的法宝。
关键词:丰田汽车,精益生产,优越性,特点,企业一、丰田公司的精益生产方式精益生产(Lean Production,简称LP)是美国麻省理工学院数位国际汽车计划组织(IMVP)的专家对日本“丰田JIT(Justin Time)生产方式”的赞誉之称,精,即少而精,不投入多余的生产要素,只是在适当的时间生产必要数量的市场急需产品(或下道工序急需的产品);益,即所有经营活动都要有益有效,具有经济性。
精益生产是当前工业界最佳的一种生产组织体系和方式。
精益生产是战后日本汽车工业遭到的“资源稀缺”和“多品种、少批量”的市场制约的产物,它是从丰田相佐诘开始,经丰田喜一郎及大野耐一等人的共同努力直到60年代才逐步完善而形成的。
精益生产既是一种以最大限度地减少企业生产所占用的资源和降低企业管理和运营成本为主要目标的生产方式,同时它又是一种理念,一种文化。
实施精益生产就是决心追求完美的历程,也是追求卓越的过程,它是支撑个人与企业生命的一种精神力量,也是在永无止境的学习过程中获得自我满足的一种境界。
其目标是精益求精,尽善尽美,永无止境的追求七个零的终极目标。
精益生产的实质是管理过程,包括人事组织管理的优化,大力精简中间管理层,进行组织扁平化改革,减少非直接生产人员;推进行生产均衡化同步化,实现零库存与柔性生产;推行全生产过程(包括整个供应链)的质量保证体系,实现零不良;减少和降低任何环节上的浪费,实现零浪费;最终实现拉动式准时化生产方式。
- 1、下载文档前请自行甄别文档内容的完整性,平台不提供额外的编辑、内容补充、找答案等附加服务。
- 2、"仅部分预览"的文档,不可在线预览部分如存在完整性等问题,可反馈申请退款(可完整预览的文档不适用该条件!)。
- 3、如文档侵犯您的权益,请联系客服反馈,我们会尽快为您处理(人工客服工作时间:9:00-18:30)。
精益生产方式简介摘要:精益生产是一种起源于丰田和汽车制造的流水线制造方法论。
也被称为“丰田生产系统”。
精益生产的目标被描述为“在适当的时间(或第仪式间,the first time)使适当的东西到达适当的地点,同时使浪费最小化和适应变化”。
创立了精益生产原则的大野耐一发现他的方法论不但可以减小浪费,还能够增进产品流动和提高质量。
本文对精益生产进行了具体的分析,得出它的优越性,并把它与传统的生产方式进行比较,通过分析可以知道精益生产是解救困难企业的法宝。
关键词:丰田汽车,精益生产,优越性,特点,企业一、丰田公司的精益生产方式精益生产(Lean Production,简称LP)是美国麻省理工学院数位国际汽车计划组织(IMVP)的专家对日本“丰田JIT(Justin Time)生产方式”的赞誉之称,精,即少而精,不投入多余的生产要素,只是在适当的时间生产必要数量的市场急需产品(或下道工序急需的产品);益,即所有经营活动都要有益有效,具有经济性。
精益生产是当前工业界最佳的一种生产组织体系和方式。
精益生产是战后日本汽车工业遭到的“资源稀缺”和“多品种、少批量”的市场制约的产物,它是从丰田相佐诘开始,经丰田喜一郎及大野耐一等人的共同努力直到60年代才逐步完善而形成的。
精益生产既是一种以最大限度地减少企业生产所占用的资源和降低企业管理和运营成本为主要目标的生产方式,同时它又是一种理念,一种文化。
实施精益生产就是决心追求完美的历程,也是追求卓越的过程,它是支撑个人与企业生命的一种精神力量,也是在永无止境的学习过程中获得自我满足的一种境界。
其目标是精益求精,尽善尽美,永无止境的追求七个零的终极目标。
精益生产的实质是管理过程,包括人事组织管理的优化,大力精简中间管理层,进行组织扁平化改革,减少非直接生产人员;推进行生产均衡化同步化,实现零库存与柔性生产;推行全生产过程(包括整个供应链)的质量保证体系,实现零不良;减少和降低任何环节上的浪费,实现零浪费;最终实现拉动式准时化生产方式。
精益生产的特点是消除一切浪费,追求精益求精和不断改善。
去掉生产环节中一切无用的东西,每个工人及其岗位的安排原则是必须增值,撤除一切不增值的岗位。
精简是它的核心,精简产品开发设计、生产、管理中一切不产生附加值的工作,旨在以最优品质、最低成本和最高效率对市场需求作出最迅速的响应。
二、精益生产方式的优越性及其意义与大量生产方式相比,日本所采用的精益生产方式的优越性主要表现在以下几个方面:1.所需人力资源——无论是在产品开发、生产系统,还是工厂的其他部门,与大量生产方式下的工厂相比,最低能减至1/2;2.新产品开发周期——最低可减至l/2或2/3;3.生产过程的在制品库存——最低可减至大量生产方式下一般水平的1/10;4.工厂占用空间——最低可减至采用大量生产方式下的1/2;5.成品库存——最低可减至大量生产方式下平均库存水平的1/4;6.产品质量——可大幅度。
精益生产方式是彻底地追求生产的合理性、高效性,能够灵活地生产适应各种需求的高质量产品的生产技术和管理技术,其基本原理和诸多方法,对制造业具有积极的意义。
精益生产的核心,即关于生产计划和控制以及库存管理的基本思想,对丰富和发展现代生产管理理论也具有重要的作用。
三、精益生产管理方法上的特点(1)拉动式(pull)准时化生产(JIT)以最终用户的需求为生产起点。
强调物流平衡,追求零库存,要求上一道工序加工完的零件立即可以进入下一道工序。
组织生产运作是依靠看板(Kanban)进行。
即由看板传递工序间需求信息(看板的形式不限,关键在于能够传递信息)。
生产中的节拍可由人工干预、控制,保证生产中的物流平衡(对于每一道工序来说,即为保证对后工序供应的准时化)。
由于采用拉动式生产,生产中的计划与调度实质上是由各个生产单元自己完成,在形式上不采用集中计划,但操作过程中生产单元之间的协调则极为必要。
(2)全面质量管理强调质量是生产出来而非检验出来的,由过程质量管理来保证最终质量。
生产过程中对质量的检验与控制在每一道工序都进行。
重在培养每位员工的质量意识,保证及时发现质量问题。
如果在生产过程中发现质量问题,根据情况,可以立即停止生产,直至解决问题,从而保证不出现对不合格品的无效加工。
对于出现的质量问题,一般是组织相关的技术与生产人员作为一个小组,一起协作,尽快解决。
(3)团队工作法(Teamwork)每位员工在工作中不仅是执行上级的命令。
更重要的是积极地参与,起到决策与辅助决策的作用。
组织团队的原则并不完全按行政组织来划分,而主要根据业务的关系来划分。
团队成员强调一专多能,要求能够比较熟悉团队内其他工作人员的工作,保证工作协调顺利进行。
团队人员工作业绩的评定受团队内部的评价的影响。
团队工作的基本氛围是信任,以一种长期的监督控制为主,而避免对每一步工作的核查,提高工作效率。
团队的组织是变动的,针对不同的事物,建立不同的团队,同一个人可能属于不同的团队。
(4)并行工程(Concurrent Engineering)在产品的设计开发期间,将概念设计、结构设计、工艺设计、最终需求等结合起来,保证以最快的速度按要求的质量完成。
各项工作由与此相关的项目小组完成。
进程中小组成员各自安排自身的工作,但可以定期或随时反馈信息并对出现的问题协调解决。
依据适当的信息系统工具,反馈与协调整个项目的进行。
利用现代CIM技术,在产品的研制与开发期间,辅助项目进程的并行化。
四、精益生产与大批量生产方式管理思想的比较精益生产作为一种从环境到管理目标都是全新的管理思想,并在实践中取得成功,并非简单地应用了一、二种新的管理手段,而是一套与企业环境、文化以及管理方法高度融合的管理体系,因此精益生产自身就是一个自治的系统。
(1)优化范围不同大批量生产方式源于美国,是基于美国的企业间关系,强调市场导向,优化资源配置,每个企业以财务关系为界限,优化自身的内部管理。
而相关企业,无论是供应商还是经销商,则以对手相对待。
精益生产方式则以产品生产工序为线索,组织密切相关的供应链,一方面降低企业协作中的交易成本,另一方面保证稳定需求与及时供应,以整个大生产系统为优化目标。
(2)对待库存的态度不同◆大批量生产方式的库存管理强调“库存是必要的”。
◆精益生产方式的库存管理强调“库存是万恶之源”。
精益生产方式将生产中的一切库存视为“浪费”,同时认为库存掩盖了生产系统中的缺陷与问题。
它一方面强调供应对生产的保证,另一方面强调对零库存的要求,从而不断暴露生产中基本环节的矛盾并加以改进,不断降低库存以消灭库存产生的“浪费”。
基于此,精益生产提出了“消灭一切浪费”的口号。
追求零浪费的目标。
(3)业务控制观不同传统的大批量生产方式的用人制度基于双方的“雇用”关系,业务管理中强调达到个人工作高效的分工原则,并以严格的业务稽核来促进与保证,同时稽核工作还防止个人工作对企业产生的负效应。
精益生产源于日本,深受东方文化影响,在专业分工时强调相互协作及业务流程的精简(包括不必要的核实工作)——消灭业务中的“浪费”。
(4)质量观不同传统的生产方式将一定量的次品看成生产中的必然结果。
精益生产基于组织的分权与人的协作观点,认为让生产者自身保证产品质量的绝对可靠是可行的,且不牺牲生产的连续性。
其核心思想是,导致这种概率性的质量问题产生的原因本身并非概率性的,通过消除产生质量问题的生产环节来“消除一切次品所带来的浪费”,追求零不良。
(5)对人的态度不同大批量生产方式强调管理中的严格层次关系。
对员工的要求在于严格完成上级下达的任务,人被看作附属于岗位的“设备”。
精益生产则强调个人对生产过程的干预,尽力发挥人的能动性,同时强调协调,对员工个人的评价也是基于长期的表现。
这种方法更多地将员工视为企业团体的成员,而非机器。
充分发挥基层的主观能动性。
五、精益生产方式是解救危困企业的法宝“精益生产通过消除浪费以实现提高质量、降低成本和缩短提前期的效果。
”消除浪费是指“作正确的事”和“正确的做事”,消除一切非增值过程。
“消除浪费”本身就体现了一种在危机中寻求出路的奋斗精神。
研究丰田生产方式产生的背景和过程可以看出,这种新的生产方式是为解决日本在困难环境中发展工业的需要而诞生的:1、丰田生产方式是在高速增长和发达工业化的后期,在已经存在众多优势竞争对手的夹缝中发展工业的道路,2、丰田生产方式是在缺少充足资源、资金和劳动力的环境中,发展工业的道路,3、丰田生产方式是在狭窄而多样化需求的市场条件下发展小批量、多品种生产的道路。
它推动丰田等日本企业从困境中进入了世界先进企业的行列。
丰田崛起了,但当时并没有人注意到它的新生产管理技术。
70年代的石油危机使高速增长的西方工业化社会出现了长时期的衰退,在众多企业利润负增长而丰田汽车却保持持续繁荣的对比之下,丰田的生产技术开始受到人们的瞩目。
在《改变世界的机器》将丰田生产方式以“精益生产”的新名称介绍给全世界的制造业以后,在萧条中寻求出路的美国企业如饥似渴的学习和效仿日本的做法。
美国人通过精益也取得了成果,90年代从低谷中爬起来,重塑了美国工业、特别是高科技工业和军事工业的霸主地位。
90年代末的亚洲经济危机、911都给美国经济带来深刻影响,廉价的“中国制造”也给美国传统制造业以冲击。
每逢这种危难时刻,美国制造业所祭起的法宝都是“精益生产”。
在经济高速增长时期,制造商可以用大量生产提高产量的方式降低成本;企业在顺利发展时期,信息技术也是加力增长的有效方法。
但是在当今生产力过剩和全球竞争的时期,降低成本成为企业生存的第一位的原则。
从困难和节俭环境中磨练出来的精益生产方式就成为应对衰退和逆境中的企业继续生存和发展的好方法。
精益生产方式就成为替代传统大量生产方式来解救危机中企业的道路。
在中国,生产能力过剩、竞争剧烈的制造领域,如家电、电脑和汽车制造,精益生产这是解救它们出困境的出路。
中国制造业与50年前日本的相似之处是同样面临着工业列强的压力、缺少发展的资金和资源。
而与当时的日本不同的是,中国面临着一个正在成长着的巨大的国内市场,有丰富的低价劳动力。
另外,中国制造业遇到了先进工业国家制造业结构调整的时机,大量低级或劳动密集产品、甚至包括消耗较大的机械产品的生产向第3世界转移,给“中国制造”以发展的机会。
这个背景下的中国制造业,可以用粗放的管理、高的消耗和初级劳动力得到有限的发展空间。
但是这决不是持续发展之路。
当西方企业拿起精益的武器,用综合的低成本对付中国的低价劳动成本但又是高消耗时,中国的优势可能就不复存在了。
居安思危和未雨绸缪才是有远见卓识的企业家的风范。
这些企业采用精益生产将降低产品成本,进一步提高企业的综合竞争能力。
参考文献:[1] 武淑萍. 精益生产在中国的应用现状[J]. 郑州航空工业管理学院学报(社会科学版), 2004, (06) .[2] 闫俊伢,邹震. 精益生产的魔力[J]. 电子商务, 2004, (05) .[3] 姚东方. 试谈精益生产方式的特征与原则[J]. 天津汽车, 2004, (06) .[4] 李润茹. 精益生产方式研究及生产方式的未来[J]. 经济师, 2005, (11) .[5] 蔡建华. 论精益生产中的员工[J]. 科技管理研究, 2005, (01) .Lean manufacture way synopsisAbstract: The lean manufacture is one kind the assembly line manufacture methodology which stems from Toyota and the automobile makes. Is also called “the Toyota production system”. The lean manufacture goal by the description is “in the suitable time (or during ceremony, the first time) enables the suitable thing to arrive at the suitable place, simultaneously causes the waste m inimum and adapts the change”. Not only established lean manufacture principle Taiichi Oono to discover his methodology to be possible to reduce the waste, but could also promote the product to flow and to improve the quality. This article has carried on the concrete analysis to the lean manufacture, obtains its superiority, and carries on it with the traditional production method the comparison, through the analysis may know that the lean manufacture is rescues the difficult enterprise the magic weapon.Key word: Toyota automobile, lean manufacture, superiority, characteristic, enterpriseFirst, Toyota Corporation's lean manufacture wayThe lean manufacture (Lean Production, is called LP) is the American Massachusetts Institute of Technology several international automobile plan organization (IMVP) expert to Japan “Toyota JIT (Justin Time) production method” name of the praise, fine, namely the fewer but better, does not invest the unnecessary element of production, is only in the suitable time production essential quantity market urgently needed product (or evil ways working procedure urgently needed product); The profit, namely all operative activitywants beneficially effective, has the efficiency. The lean manufacture is the current industrial world best one kind of Production organization system and the way.The lean manufacture is the postwar Japan automobile industry encounters “the resources are scarce” and “the multi-varieties, the few batch” the market restriction product, it is assists the interrogation from Toyota to start, after Toyota happy eldest son and Taiichi Oono et al. the joint efforts only then gradually consummates until the 60s forms.The lean manufacture is not only one kind take maximum limit reduces the resources which the enterprise produces takes and reduces the business management and the operation cost as the essential target production method, simultaneously it is also one idea, one culture. The implementation lean manufacture is determined the pursue perfect course, is also the p ursue remarkable process, it is the support personally with the enterprise life one spiritual strength, also will be will obtain the self-satisfied one kind of boundary in forever the without limits learning process. Its goal is strives for perfection, acme of perfection, forever without limits pursue seven zero ultimate objectives.The lean manufacture essence manages the process, organizes the optimization which including the human affairs manages, simplifies the middle management vigorously, carries on the organization flattening reform, reduces the non-personal directly engaged productions; Pushes carries on the production equalizing to synchronize, realizes zero stock and the flexible production; Carries out the entire production process (including the entire supply chain) the quality assurance system, realizes zero bad; Reduces and reduces on any link's waste, realizes zero waste; Realizes the drawing type punctual metaplasia to produce the way finally.The lean manufacture characteristic is eliminates all wastes, the pursue strives for perfection with the progressive improvement. Removes produces in the link all useless things, each worker and the post arrangement principle is must rise in value, removes the post which all do not rise in value. The simplification is its core, in the simplification product development design, the production, the management all does not have the added value work, is for the purpose of by the most superior quality, the most low cost and the peak efficiency makes the most rapid response to the market demand.Second, lean manufacture way superiority and significanceCompares with the mass production way, Japan uses the lean manufacture way's superiority mainly displays in the following several aspects:1. Needs the human resources - -, regardless in product development, production system, factory other departments, compare with the mass production way's under factory, reduces to feeble-mindedly 1/2;2. The new product development cycle - - lowest may reduce to l/2 or 2/3;3. Production process's goods in process stock - - lowest may reduce to under the mass production way the general level 1/10;4. Factory takes the space - - lowly to be possible to reduce to selects under the mass production method 1/2;5. End product stock - - lowest may reduce to under the mass production way the averaging stock level 1/4;6. Product quality - - may be large scale.The lean manufacture way is pursues the production thoroughly the rationality, highly effective, can produce nimbly adapts each kind of demand high grade product production technology and the managerial technique, its basic principle and many methods, have the positive significance to the manufacturing industry. The lean manufacture core, namely about the productive plan and the control as well as stock management's basic philosophy, also has the vital role to rich and the development modern production management theory.Third, in lean manufacture management characteristic(1)the drawing type (pull) punctual metaplasia produces (JIT)Take end-user's demand as production beginning. Emphasizes the physical distribution to be balanced, the pursue zero stock, requests the components which a working procedure processes to be possible to enter the next working procedure immediately. The organization produces the operation is depends upon the electronic monitoring system (Kanban) to carry on. Namely the demand information (electronic monitoring system form does not limit by the electronic monitoring system transmission working procedure, key lies in can transmit message). In the production metre may by the manual intervention, the control, in the guarantee production physical distribution balanced (regarding each working procedure, namely for guarantee after working procedure supply accurate current events). Because uses the drawing type production, in the production plan and the dispatch materially are complete by each production unit, in formally does not use the centralism plan, but in the operating process between production unit's coordinated extremely is essential.(2) Total Quality ManagementStressed that the quality is produces, but must examines, guarantees the final quality by the process quality control. In the production process carries on to the quality examination and the control in each working procedure. Is heavy is raising each staff's quality consciousness, the guarantee prompt discovery quality question. If discovers the quality question in the production process, according to the situation, may stop the production immediately, until solves the problem, thus the guarantee does not appear to the defective works invalid processing. Regarding quality question which appears, generally is theorganization related technology and the production personnels takes a group, cooperates together, solves as soon as possible.(3) Team method of working (Teamwork)Not only each staff carries out higher authority's order in the work. Participation positively more importantly, plays policy-making and the auxiliary policy-making role. The organization team's principle presses the administrative organization to divide not completely, but mainly divides according to the service relations. The team members emphasize master many skills while specializing in one, the request can in the quite familiar team other staff's work, guarantee that the work coordinated carries on smoothly. The team personnel work the achievement evaluation the team internal appraisal influence. The team work's basic atmosphere is the trust, by one kind of long-term supervisory control primarily, but avoids to the investigation which each step works, raises the working efficiency. Team's organization is the change, in view of the different thing, establishes the different team, the identical person possibly belongs to the different team.(4) Parallel projects (Concurrent Engineering)In product design development period, the conceptual design, the structural design, the technological design, the final demand and so on unifies, guaranteed that completes by the quickest speed according to the request quality. Each work by completes with this related project group. In the advancement the panel members arrange own work respectively, but may regular or momentarily the feedback information and to appears the question solves coordinated. Rests on the suitable information system tool, the feedback and coordinated entire project advance. Using the modern CIM technology, in product development and development period, auxiliary project advancement parallelization.Fourth, lean manufacture and production in enormous quantities way management concept comparisonThe lean manufacture takes one kind from the environment to the management goal is the brand-new management concept, and obtains the success in reality, has applied one, two new management tool simply by no means that but is a set the management system which with the enterprise environment, the culture as well as the management fuses highly, therefore lean manufacture oneself is an autonomous system.(1)optimizes the scope to be differentThe production in enormous quantities way stems from the US, is relates based on US's enterprise, emphasizes the market direction, the optimize allocation of resources, each enterprise take the financial relations as a boundary, optimizes own internal management. But is related the enterprise, regardless of being the supplier or the dealer, by to palm reading treatment.The lean manufacture way take the product manufacturing working procedure as the clue, the organization close related supply chain, on the one hand reduces in the enterprise cooperation the transaction cost, on the other hand guarantees the stable demand and the prompt supply, take the entire big production system as optimized goal.(2) Treats the stock the manner to be differentThe production in enormous quantities way's stock management stressed that “the stock is essential wicked”.The lean manufacture way's stock management stressed that “the stock is the root of all evil”.The lean manufacture way will produce all stocks will regard as “the waste”, simultaneously thought that the stock has covered in production system's flaw and the question. It emphasizes the supply at the same time to the production guarantee, on the other hand emphasizes to zero stock request, thus exposes in unceasingly the production the basic link's contradiction and improves, reduces the stock to eliminate the stock unceasingly to have “the waste”. Based on this, the lean manufacture proposed “eliminates all wastes” slogan. Pursue zero waste goals.(3) The service control view is differentThe traditional production in enormous quantities way's personnel system based on both sides “the employment” the relations, in the business management stressed that achieves individual work highly effective division of labor principle, and promotes and the guarantee by the strict service investigation, simultaneously the investigation work also prevents aman-power to oppose negative effect which the enterprise produces.The lean manufacture stems from Japan, the depth the Eastern culture influence, when specialized labor division stressed that cooperates mutually and the operation flow simplification (including nonessential checking work) - - in the elimination service “the waste”.(4) The quality view is differentThe traditional production method regards as the ration second quality item in the production the inevitable result.The lean manufacture based on organization's decentralization with person's cooperation viewpoint, thought that lets the producer own quality assurance reliable is absolutely feasible, and does not sacrifice the production the continuity. Its core thought is, causes reason which itself this kind of probabilistic quality question produces by no means probabilistic, through eliminates produces the quality question production link to come “to eliminate the waste which all second quality items bring”, pursue zero bad.(5) The manner is different to the humanIn production in enormous quantities way emphasis management strict level relations. Lies to staff's request completes the task which strictly the higherauthority issues, the human is regarded as attached in the post “the equipment”.The lean manufacture stressed that a person to production process's intervention, displays person's activity with every effort, simultaneously emphasizes coordinated, to staff individual appraisal is also based on thelong-term performance. This method more member who regards as the staff the enterprise association, but non-machine. Full display basic unit subjective initiative.Fifth, the lean manufacture way is rescues the danger sleepy enterprise the magic weapon“The lean manufacture realizes through the waste elimination improves the quality, to reduce the cost and the reduction time in a dvance effect.”The waste elimination is refers to “does the correct matter” and “correct working”, eliminates all non-increment process. “The waste elimination” itself manifested one kind to seek the outlet in the crisis the hard working spirit. Studies the background which and the process the Toyota production method produces may see, this new production method is to solve Japan the expand industry to need to be born in the difficult environment:1st, the Toyota production method is in fast growth and the developed industrialization later period, in al2nd, the Toyota production method is in lacks the sufficient resources, the fund and in the labor force environment, expand industry's path,3, the Toyota production method is develops the small batch, the multi-variety production path under the narrow diverse demand market condition. Ready had the numerous superiority competitor in the crevice the expand industry path,It impelled Japanese Enterprises and so on Toyota to enter the world Advanced enterprise's ranks from the difficult position. Toyota has risen, but at that time and nobody noted its new production management technology. The 70s's oil shock caused the fast growth the western industrialization society to present the long time decline, in numerous profit of enterprise negative growth, but the Toyota automobile actually maintained the continuous prosperity under the contrast, Toyota's production technology started to receive people's attention In "Change World Machine" Toyota production method after “lean manufacture” the new name introduced for world manufacturing industry, seeks the study which in the depression the outlet the American Enterprise desires strongly and imitates Japan's procedure. The American has also made the progress through the fine profit, in the 90s crawls from the trough, has remoulded the American industry, is specially the high tech industry and the war industry hegemonic position. The late 90s's Asian economic crisis, 911 give the US the economy to bring the profound influenc e, inexpensive “China makes” also gives the US the traditional manufacturing industry to attack. Onthis kind of dangerous time, the magic weapon which the American manufacturing industry offers a sacrifice to is “the lean manufacture”. In the economical fast growth time, the manufacturer may use the mass productions to raise the output the way to reduce the cost; the enterprise in the smooth development time, the information technology is also the efficacious device which the thrust augmentation grows. But is now surplus in the productive forces and global competition's time reduces the cost to become the enterprise survival the first principle. The lean manufacture way which disciplines from difficult and the thrifty environment becomes deals with in the decline and the adverse circumstance enterprise continues to survive and the development good method. The lean manufacture way becomes the substitution tradition mass production way to rescue in the crisis enterprise's path. In China, the excess capacity of production, the competition fierce manufacture domain, like the electrical appliances, the computer and the automobile manufacture, lean manufacture this is rescues their difficult position the outlet. The Chinese manufacturing industry Japan's similarity is faces the industry big powers pressure 50 years ago, to lack development similarly the fund and the resources. What but was different with Japan then, China was facing one was growing the giant domestic market, had the rich low price labor force. Moreover, the Chinese manufacturing industry has met the advanced industrial nation manufacturing industry structural adjustment opportunity, massive preliminary or the work crowded product, even includes the consumption big engineering products the production to the 3rd world shift, “makes the opportunity which for China” develops. Under this background's Chinese manufacturing industry, may use the extensive management, the high consumption and the primary labor force obtains the limited development opportunities. But this is in no way road of the sustained development. When the Western enterprise takes up the fine profit the weapon, copes with the synthesis low cost when China's low price cost of labor but is also a high consumption, China's superiority possibly does not exist. Thinks of danger in peace and provides for a rainy day is the far-seeing originality entrepreneur's style. These enterprises will use the lean manufacture to reduce the product cost; will further sharpen enterprise's synthesis competitive ability. Reference:[1] Wu Shuping. Lean manufacture in China's application present situation [J]. Zhengzhou Aviation industry Management Institute journal (social sciences version), 2004, (06).[2] Yan Junya, Zou Zhen. Lean manufacture charm [J]. Electro nic commerce, 2004, (05). East[3] Yao. Tries to discuss the lean manufacture way the characteristic and principle [J]. Tianjin automobile, 2004, (06).[4] Li Runru. Lean manufacture way research and production method future [J]. Economist, 2005, (11).[5] Cai Jianhua. By lean manufacture in staff [J]. Science and technology management study, 2005, (01).。