8D根本原因分析(PPT 64张)
品质工具-8D报告应用培训PPT课件
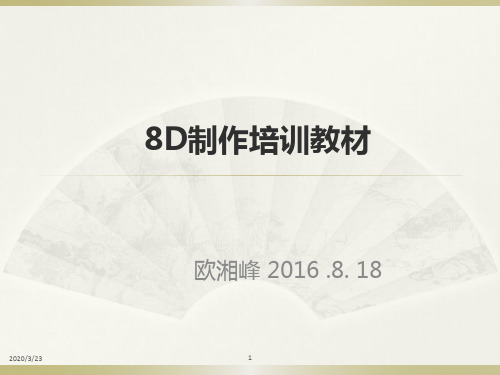
2020/3/23
11
D3.原因分析可选用的质量工具
2020/3/23
12
2020/3/23
13
2020/3/23
14
2020/3/23
15
2020/3/23
16
2020/3/23
17
2020/3/23
18
2020/3/23
19
2020/3/23
20
2020/3/23
21
2020/3/23
8、未建立完善对供应商8D措施稽查落实跟踪闭环
2020/3/23
3
D1、成立改善小组
D2、描述问题原因
2020/3/23
4
8D拟制要求
D1.成立改善小组 D2. 描述问题—1 (5W2H) 问题描述需基于来料检验环节和生产反馈的问题加以分析; 将问题发生的时间、发生问题的内容为何?影响的广度与深度为何?受影 响的料号、批号为何?缺点率等相关问题陈述的内容加以说明,明确说明 真正的问题。
22
2020/3/23
23
2020/3/23
24
2020/3/23
25
8D拟制要求-根因分析
D4. 原因分析及验证真因:
原因分析按产生根因和流出根因两条轴线来进行分析(针对技术性问题建议采用鱼骨图 方式进行分析验证真因、针对其他生产管理类问题采用流程图进行分析验证真因):剖析 问题产生根因、违背什么要求、未遵循什么规则制定或指导书、还是未建立标准等
11 发生 (D2步骤. 描述问题)的真正原因、进行说明分析、方法(有很多种、可以使用QC 品质工具(七大手法工具、5W)
1.层别法(问题分类)
2.检查表 (找问题)
8D培训(8D工具-根本原因分析)

1、为什么根本原因没有被确定和验证? 2、供方将如何计划继续该过程? 3、供方打算完成该过程的时间计划?
一般可通过①趋势图、②排列图、③柏拉图等质量工具找出问题点,或者是内部的异常反馈。
14
D3
实施和验证临时措施
零件表面没有镀银
批量 不良率
10000PCS 39/200=18.5%
8
D1
成立小组
邀请具备产品及过程知识,能支配时间,且拥有职权及技术知识的人士,组成一个小组,解决 提出的问题及采取纠正措施。小组应指定一位组长。适当时,小组可包括分供方和顾客 成员。
常见性错误:
1、所选择的完成8D过程的小组成员没有技术知识。 2、只有一两个人实施该过程。
D3
实施和验证临时措施
确定并执行应先采取的临时对策, 控制外部/内部客户问题事态的扩大,直到执行永久对策,并验证 所采取临时对策的效果。
为保证临时措施的效果,在确定临时措施后,应考虑以下方面的问题: 1、所有可疑地点(供方现场/仓库、分供方现场、顾客现场、下一个顾客现场、其他)的库存是否清查? 2、防堵(拦截)的有效率是多少?是否满意? 3、防堵措施的日期列出了吗? 4、筛选结果列出已筛选数,发现数和缺陷数了吗? 5、筛选的方法提到了吗? 6、筛选的方法是否满意? 7、短期纠正措施列出了吗?
职位 客服课长
QE RD IE QA组长 组装课长
角色 Leader member member member member member
联络电话 X X X X X X
不通电(虚焊)不良 8D报告ppt课件

在工 品
1700
2.返工后的U5不良PCS,现象为灯不亮,没有不通电 现象,拿20PCS成品给到开发部做高低温试验(高温
60度,低温-20度,各2H-----无不良;
3.不通电异常通过返工维修基本上能把问题改善,将 风险在内部拦截。
顾客 端
不涉及
责任人
4
D6:永久对策的D实4施根及本跟原踪因及验证
不良图片:无
3
D6:(永Im久ple对me策nt的at实ionD施&3及V紧跟al急i踪da对ti策on of PCA )
状态 可疑品数量
处理措施
库存 不涉及
1.对组装车间已经好的400PCS成品安排24小时的老 化试验;----发现4PCS不良(不通电)故要求对 1700PCS全部返工,对芯片做拖锡处理后t的at实ionD施&2及V问跟al题i踪da描ti述on of PCA )
客户
华三
发生时间 213.11.12 地点
菲菱科思
不合格类别归属 □来料 ■制程 □体系□成品 □客验 □客诉□其它: 现场稽核问题
批量
1700
检验数
/
不良数
13
不良描述:11月9号下午初测反馈投 产1700PCS产品,在一小时内发现连 续13PCS不通电。异常发生后立刻要 求产线停线。后经工程分析为U5位置 虚焊导致
2013.11.12
6
D6:永久对策的D实5施永及久跟性踪纠正对策
(Implementation & Validation of PCA )
No. 永久对策
责任人 完成时间
1 受潮物料烘烤上线验证200PCS,无不良。为避免后续在生 产过程中“GD34”/”GD35”两个批次出现焊接问题,烘烤后 上线,烘烤方式采用125°±5°时间48小时。
8D根本原因分析之5WHY与鱼骨图完整版(ppt 64页)

10
2 使用“5WHY”注意事项
2.1 对问题的描述——事实、全面、具体、
要向有关人员清晰陈述所发生的问题和相关信息,做到让所有相关人员都 了解要分析问题是什么,即使是不熟悉该类问题的人员。
8D根本原因分析 —— 5WHY与鱼骨图
2019/8/25
一、8D使用工具简介 二、5Why分析方法培训 三、鱼骨图分析方法培训 四、8D中5WHY与鱼骨图的应用
1、8D使用工具简介
脑力激荡、 (头脑风暴)
因果图 (鱼骨图)
柏拉图
时间线 (甘特图)
流程图
是/不是矩阵 Is/Is not
共性分析
5WHY
5WHY分析法的运用①
5WHY分析法的运用②
异常现象 为什么?
(原因/效果关系)
直接原因 为什么?
真正的解决问题 必须找出问题的 根本原因,而不 是问题本身,根 本原因总是隐藏 在问题的背后。
(原因/效果关系)
原因 为什么?
(原因/效果关系)
原因 为什么?
(原因/效果关系)
为什么?
真正 原因
根本原因
“因此”
测试
CCC
根本原因
2.5 不仅仅是5次
五个为什么 问五次为什么 原则:找到根本原因
5
2.5 5WHY总的指导方针
要天真一些 要绝对的客观 找原因,非找借口、理由 根据数据、事实,而非猜测、假设 做到三现,在现场通过现物掌握现实 不要认为答案是显而易见的 如果你自己不完全熟悉过程,就组建一个多功能的工作组来完成分析 若问题的答案有一个以上的原因,则应找出每个原因的根源。
8D问题分析

Team: 工程/品管/测试中心/铁管/制造的具备问 题解决的人员担当;
D1 第一步骤: 成立小组
§成立小组关键要点:
1,成员资格,是否具备工艺、产品、专业的知识 ; 2,分工是否明确; 3,是否任命小组长; 4,是否有供方或顾客参与.
D2 第二步骤: 描述问题
1.目标型问题(提示) 如成本↓,效率提升;
未来导向型 2.创意型问题(意愿) 如产品设计;
3.新技巧型问题(认识) 如导入自动化,计算机化.
传统的问题解决依据
地位 直觉 经验
问题思考具有五种能力
敏锐力(观察):对问题或环境的敏感度。有些人敏感 度高,任何事物若有疏失或不寻常的地方,很快的会 感觉出来。
(2) 在发现问题的72小时内,提交包 含问题发生原因的初步分析的8D报 告.
8D问题分析报告 :
8D报告
结论:
8D格式用于监控解决问题的过程, 它不是一个详尽的报告或复杂的 分析、描述工具,而是一个包含 了解决问题的每个步骤的集合, 因而可从其中找到经提炼的基本 信息.
题分析与解决铭言集
成功的人找方法,失败的人找借口 感觉困难,代表能力不够;感觉麻烦,代表方法不对 问题解决能力=管理能力+专业能力+EQ能力 方法不变,结果不变 问正确的问题是解决问题的第一步 明确的将问题指出,就等于解决问题的一半 精确的陈述问题比解决问题还来得重要 会问问题的人,80%都知道问题的答案是什么 办法总比问题多
D8 第八步骤: 团队激励
•对于努力解决问题之团队予以嘉勉,使其 产生工作上的成就感,并极乐意解决下次 碰到的问题。无论是产发段发现的问题, 或是量产、客诉问题, 若公司每年有近百 项的工程问题依照8D的方式来解决,对工 程人员实力的培养着实可观,成为公司重 要的资产,这也是很多公司将8D制式化的 原因。
8D如何进行根本原因的分析

8D如何进行根本原因的分析?公司里,最大的成本之一是不断地去处理重复发生的问题。
浪费时间、精力和人力,不但伤钱,还伤感情。
同时,相信很多人在问题分析的时候会像玻璃上的窗苍蝇,前途一片光明,却找不到出路,无从下手。
也有很多人分析不到重点,稍微找到一个可能的原因,就如同发现了新大陆,妄下结论,浅尝即止。
殊不知只发现了冰山一角,水下面还有更多的冰。
这两点都源于一个主要的问题,就是问题没有找到根本原因,没有从源头彻底解决。
那具体该如何进行系统性地原因分析呢,没有固定的标准答案,因为不同问题不同对待,但对于多数问题来说,我们还是可以使用一些套路的。
IATF16949标准中10.2.3问题解决的条款要求:▪为了控制不合格,采取遏制措施和临时措施。
比如100%的全检,防止不合格品再次流出。
排查所有区域的不合格品。
▪分析根本原因,采取长期对策。
▪对措施的有效性进行验证。
▪对适当的文件,如PFMEA,控制计划进行更新,防止同类问题重复发生。
▪▪当产品和过程发生偏离,在分析原因之前,必须采取应急措施,如100%的全检。
▪应用适当的方法,如8D、鱼骨图、5WHY方法等进行根本原因的分析。
▪制定纠正措施,验证其有效性。
▪对PFMEA、控制计划进行更新,防止同类问题再发生。
问题只需四步就能分析到根本原因,即确定所有可能的原因、筛选出最可能的原因、验证并确定根本原因和分析根本问题。
1第一步:确定所有可能的原因也就是说找到所有可能产生问题Y的所有X因子。
在根本问题分析时,主要用到的就是头脑风暴、鱼骨图和5why分析。
在解决更为复杂的问题时,可以用Process Map解决整个过程、整套系统的问题,如提高产品合格率,提高生产效率等等。
所以,一般在做六西格玛这种比较大的项目时使用的会更多些。
但总之,目的是找到所有可能产生问题的X因子。
鱼骨图列出的更多是表面上可能导致问题的直接原因,是问题的表象,这个原因在原理原则上是说的通的,但并不是根本原因。
不通电(虚焊)不良 8D报告ppt课件
D1 团队 D2 问题描述 D3 紧急对策 D4 根本原因分析及验证 D5 永久性纠正对策 D6 纠正行动有效性确认 D7 预防再发生 (标准化) D8 感谢团队协作
目录
(撰写人):
日
期:2013.11.112
D6:(永Im久ple对me策nt的at实ionD施&1及V成跟al立i踪da团ti队on of PCA )
2013.11.15 2013.11.15
5 SMT工程优化检测设备和检测手法,AOI人员检验时,发 现同一异常连续发生,无法确定异常问题时,找工程部技 术人员确认,技术员无法确认将问题升级让工程师处理, 确定问题后品质要求停线整改。
2013.11.15
7
D6:永久对策D的6实纠施正及行跟动踪有效性确认
团队成员
组长
品质
(DIP QE)
(SMT QE)
(客服)
工程
(SMT 工程)
生产
(SMT 生产)
开发
/
其他
/
(DIP工程) (组装 生产)
(TE) (DIP生产)
2
D6:(永Im久ple对me策nt的at实ionD施&2及V问跟al题i踪da描ti述on of PCA )
客户
华三
发生时间 213.11.12 地点
60度,低温-20度,各2H-----无不良;
3.不通电异常通过返工维修基本上能把问题改善,将 风险在内部拦截。
顾客 端
不涉及
责任人
4
D6:永久对策的D实4施根及本跟原踪因及验证
(Implementation & Validation of PCA )
No. 根本原因及验证
8D分析报告模板PPT(华为供应链用)
原因分析
05
04
1.升级CNC加工中心操作指导书第五项机器故障处理规定,增加机器故障停开机,品管专检工序。ห้องสมุดไป่ตู้.1.改善前流程:
纠正措施
1.1.改善后流程:
机器故障停开机
品管专检确认
2.出货检验增加全尺寸测量管控。
05
预防措施
1、立即制作孔位检具,制程导入检具作业,机加作业员每小时自检确认一次,检具如下图一(8月8日可完成检具制作)2、立即完成项目要求培训,培训记录见图二。
1、客户端立即派人用卡尺全检,已选出不良批1010PCS退回报废处理;2、厂内库存606PCS确认为不良,标识报废;3、立即安排重新生产,快速完成良品交付。
1.根本原因:夜班CNC 生产机器发生故障,技术员在排障中在X轴0点校正方向时调反了,造成孔偏位不良。 2.流出原因:2.1.调机后没有通知首件确认2.2.出货检验没有做全尺寸检查
图一:孔位检具图
图二:培训记录
06
改善效果验证
改善后第一批出货,增加检具全检来验证改善效果
THANKS
端板5099000081131螺纹孔偏位分析报告
---精信源 2023.8.7
目录 CONTENT
05
05
预防措施
不良问题点
01
8月04日,客诉:端板5099000081131产品,M5螺纹孔机加X轴方向偏位(如下图所示),影响实配。
良品:实测3.35mm
不良品:实测2.47mm
围堵措施
02
8D根本原因分析
一、8D使用工具简介 二、5Why分析方法培训 三、鱼骨图分析方法培训 四、8D中5WHY与鱼骨图的应用
脑力激荡、 (头脑风暴)
因果图 柏拉图 (鱼骨图) 故障树分析 假设检验
时间线 (甘特图)
流程图
是/不是矩阵 Is/Is not共性分析5WHY
回归分析
试验设计
决策矩阵
4.)为什么燕子以喜欢聚集到这里? 是因为建筑物上有它喜欢吃的蜘蛛? 5.)为什么会有蜘蛛? 蜘蛛爱在这里安巢,是因为墙上有大量它爱吃的飞虫 6.)为什么墙上飞虫繁殖得这样快? 因为傍晚时尘埃在从窗外射进来的强光作用下,形成了刺激飞虫生长的温床。 解决问题的结论是:拉上窗帘。 杰弗逊大厦至今完好无损。
简单的说特性就是“工作的结果”,首先,对团队成员讲解会议目的,然 后,认清、阐明需要解决的问题,并就此达成一致意见。
1
特 性
②特性和主骨。 •特性写在右端,用四方框圈起来。
•主骨用粗线画,加箭头标志。
2
1
主 骨
特 性
③大骨和要因。 大骨上分类书写3~6个要因,用四方框圈起来。
3
要点:绘图时,应保证大骨与主骨成60度夹角,中骨与主骨平行。
亲自看实物、接 触实物。
观光缆车的玻璃窗由于水蒸气变得模糊 观光缆车的玻璃窗由于水蒸气变得模糊
里面乘了六个人 观光缆车内外有温差 观光缆车内空气湿度 升高了(水份饱和度)
问题 直接原因 原因 原因 根本原因 原因 原因 根本原因 直接原因 原因 原因 根本原因
异常的发生
为什么? (原因/后果 关系)
治标对策 (暂时)
真因
WHY
改善行动
WHY
真因
真因
品质异常分析8D报告ppt课件
2019/01/10
----责任人:XXX 完成时间
5
四 原因分析
A外箱: 印刷跑位、保证日期印错、
包装
人
机
印稿日期制作错误
模切纸板未放到位
传送带未调试好
摆放错误
机器故障
纸张弯翘 尺寸大小一至
料
设置方法问题 作业方式错误
法
运输
为什么会有 跑位、印错、 混料问题发
保证期印错
4
混料
三 处理对策
紧急应对措施:
A.1:外箱跑位:生产召集会议分析原因,商讨改善方案.
2019/01/09
----责任人:XXX 完成时间
A.2:外箱印刷错误和混料:调查发生原因,梳理管控流程。 ----责任人:XXX 完成时间 2019/01/10
B.送货单问题:与客户确认后续格式,并协商好异常品补货时间
工 程 : 刘工 程 :张
品 质 : 何品 质 :吴
业 务 : 徐丁业 务 :
计划:韦采购:
玉
云国
小美
远克
峰俊
凤印
雷森
兵梅
玲
XXX XXX XXX XXX XXX
3
二 问题描述
1/9日至客户端现场检讨反馈近期问题如下:
A.外箱: 印刷跑位、保证日期印错、混料(如下图 示) B.送货单: 批号错误
印刷跑位
品质异常分析改善报告
1
一 小组成立 五 改善对策
报
二 问题描述 六 水平展开
告
内
三 处理对策 七 效果确认
容
四 原因分析 八 改善结案
2
一 小组成立
成立原因:客诉问题 成立目的:改善现状 成立时间:2019年1月10日
- 1、下载文档前请自行甄别文档内容的完整性,平台不提供额外的编辑、内容补充、找答案等附加服务。
- 2、"仅部分预览"的文档,不可在线预览部分如存在完整性等问题,可反馈申请退款(可完整预览的文档不适用该条件!)。
- 3、如文档侵犯您的权益,请联系客服反馈,我们会尽快为您处理(人工客服工作时间:9:00-18:30)。
C
C
C
C
为什么?
直接原因
(原因/后果 关系)
C
C
C
C
为什么?
原因x
(原因/后果 关系)
C
C
C
原因xx
为什么? (原因/后果 关系)
C
C
C
原因xxx
为什么? (原因/后果 关系)
C
C
C
根本原因
“因此” 测试
2.5 不仅仅是5次
五个为什么
问五次为什么
原则:找到根本原因
5
2.5 5WHY总的指导方针
10
2 使用“5WHY”注意事项 2.1 对问题的描述——事实、全面、具体、
要向有关人员清晰陈述所发生的问题和相关信息,做到让所有相关人员都 了解要分析问题是什么,即使是不熟悉该类问题的人员。
确认所描述的状态为事实,而非推断、猜测 尽可能分享所有已知的相关信息 可以的话,使用数据进行说明 避免 涉及了对策 假定臆测的原因 模糊
千万别忽视第一步
我们中国古代以来就有“打破沙锅问到底”的习惯;“打破沙锅问到底”是一句俗语, 形象表达了锲而不舍、不断探索的精神,这是人们常挂在嘴边的一句口头禅。 到了日本人手里就整出一个5why出来了,说明日本人还是挺善于系统化总结的,我们用 了讲了这么多年的“打破沙锅问到底”,也没见有人把它总结出来成为一个方法。
观光缆车内外有温差
观光缆车内空气湿度 升高了(水份饱和度)
ቤተ መጻሕፍቲ ባይዱ
两个为什么间必须紧密相关,不要跳步
2.3 找出每个原因的根源
若问题的答案有一个以上的原因,则应找出每 个原因的根源。
问题
直接原因 原因 原因
直接原因 原因
原因
根本原因
原因
根本原因
原因
根本原因
2.4 推导的同时进行验证
异常的发生
为什么? (原因/后果 关系)
真理诞生于一百个问号之后
5
1.2 问题的冰山性
WHY WHY WHY WHY WHY WHY WHY
问题表象
直接原因 (中间原因) 根本原因
1.3 5WHY分析法的要点①
现象
现在
WHY WHY
察觉(异常点、变 化点等) 问题 紧急处 理
一次因 (近因) 治标对策 (暂时)
一种用不断问“为什么”来找 现象的根本原因的方法
为什么?4 原因 为什么?5
基本经由调查 问题发生在哪块? “去看”问题
原 因 调 查
为什么? 为什么? 为什么? 为什么? 为什么?
5WHY 根本原因调查分析
根源 对策
在开始5WHY 先理清问题,掌
评估对策成效
流程标准化/教训
1.5 5WHY分析法的运用
5WHY分析法的运用①
异常现象 为什么?
5WHY分析法的运用②
8D根本原因分析 —— 5WHY与鱼骨图
2019/2/14
一、8D使用工具简介 二、5Why分析方法培训 三、鱼骨图分析方法培训 四、8D中5WHY与鱼骨图的应用
1、8D使用工具简介
脑力激荡、 (头脑风暴)
因果图 柏拉图 (鱼骨图)
时间线 (甘特图)
流程图
是/不是矩阵 Is/Is not
共性分析
十分接近真相的原因 表面原因
看到的现象
为什么?
为什么? 答案:
(原因/效果关系)
原因
(原因/效果关系)
为什么?
真因必须靠更深入地挖掘,询问问 题何以发生。先问第一个“为什么 ”,获得答案后,再问为何会发生 ,依此类推,问5次“为什么”
根本原因
1.6 5WHY分析法的优点
找出问题发生的根源,彻底解决之 重视潜在的系统性问题 为什么-为什么图表会把因果路径简单地呈现出来 易懂、易用、兼容性强
5WHY
故障树分析
假设检验
回归分析
试验设计
决策矩阵
SPC
防错法
控制计划 Control plan
佩恩特图
能力矩阵
5W2H
直方图
趋势图
故障检测分类 FDC
相关分析 风险评估 (散点图) FMEA 7钻石法
样本大小 和功效
层别法
一、8D使用工具简介 二、5Why分析方法培训 三、鱼骨图分析方法培训 四、8D中5WHY与鱼骨图的应用
要天真一些 要绝对的客观 找原因,非找借口、理由 根据数据、事实,而非猜测、假设 做到三现,在现场通过现物掌握现实 不要认为答案是显而易见的 如果你自己不完全熟悉过程,就组建一个多功能的工作组来完成分析 若问题的答案有一个以上的原因,则应找出每个原因的根源。
3 “5WHY”案例说明 3.1 案例1:迟到
真正的解决问题 必须找出问题的 根本原因,而不 是问题本身,根 本原因总是隐藏 在问题的背后。
① W
(原因/效果关系)
问题发生在哪? 其造成问题的根本原因为什么呢?
为什么?
直接原因
根由:
真正原因
② W ③ W ④ W ⑤
为什么? 原因 为什么? 真正 原因
(原因/效果关系)
为什么? 为什么? 为什么?
问题:“今天上班迟到了10分钟 ”
过去
真因
真因
WHY
一种对现象发生的可能原因进行 分析的方法 一种建立在所有事实上寻找根本 原因的分析方法
WH Y
真 因
改善 行动
真因
WHY
一种更进一步的因果分析方法,不 是只找出最具影响的因素
真因
N次因 (远因)
治本对策 (永久)
7
1.4
了解情况 抓住形势
5WHY漏斗
问题鉴别 (大、模糊、复杂的问题) 阐明问题 已定位的原因区 原因点 (POC) 为什么?1 原因 为什么?2 原因 为什么?3 原因
1、5WHY分析法介绍
1.1 由来
5WHY分析又称5问法,最初由丰田公司提出并在丰田公司广泛采用,因此也被称 为丰田5问法。 5WHY报告在日系企业利用的很多,其首创是丰田公司的大野耐一,来源于一次 新闻发布会,有人问,丰田公司的汽车质量怎么会这么好?他回答说:我碰到 问题至少要问5个为什么。 大野耐一总是爱在车间走来走去,停下来向工人发问。他反复地就一个问题, 问“为什么”,直到回答令他满意,被他问到的人也心里明白为止——这就是 后来著名的“五个为什么”。 5问法的关键所在为:鼓励解决问题的人要努力避开主观或自负的假设和逻辑陷 阱,从结果着手,沿着因果关系链条,顺藤摸瓜,穿越不同的抽象层面,直至 找出原有问题的根本原因.
千万别忽视第一步
11
2.2 三个现场要素
眼见为实,耳听为虚
现实
亲自去了解 现实情况。
现场 现物
亲自到现场 。
亲自看实物、 接触实物。
2.3 注意层和层间的相关性素
每个为什么的问题和答案间必须有必然关系。
观光缆车的玻璃窗由于水蒸气变得模糊 观光缆车的玻璃窗由于水蒸气变得模糊 里面乘了六个人