QC检验规范
QC检验能力考核管理规范
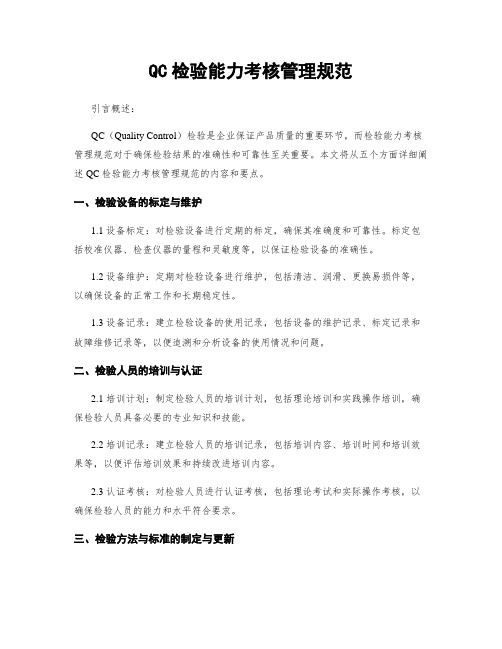
QC检验能力考核管理规范引言概述:QC(Quality Control)检验是企业保证产品质量的重要环节,而检验能力考核管理规范对于确保检验结果的准确性和可靠性至关重要。
本文将从五个方面详细阐述QC检验能力考核管理规范的内容和要点。
一、检验设备的标定与维护1.1 设备标定:对检验设备进行定期的标定,确保其准确度和可靠性。
标定包括校准仪器、检查仪器的量程和灵敏度等,以保证检验设备的准确性。
1.2 设备维护:定期对检验设备进行维护,包括清洁、润滑、更换易损件等,以确保设备的正常工作和长期稳定性。
1.3 设备记录:建立检验设备的使用记录,包括设备的维护记录、标定记录和故障维修记录等,以便追溯和分析设备的使用情况和问题。
二、检验人员的培训与认证2.1 培训计划:制定检验人员的培训计划,包括理论培训和实践操作培训,确保检验人员具备必要的专业知识和技能。
2.2 培训记录:建立检验人员的培训记录,包括培训内容、培训时间和培训效果等,以便评估培训效果和持续改进培训内容。
2.3 认证考核:对检验人员进行认证考核,包括理论考试和实际操作考核,以确保检验人员的能力和水平符合要求。
三、检验方法与标准的制定与更新3.1 方法制定:制定适用于企业产品的检验方法,包括检验步骤、检验要求和判定标准等,以确保检验的一致性和准确性。
3.2 标准更新:定期对检验方法和标准进行更新和修订,以适应产品技术的发展和市场需求的变化,确保检验方法的有效性和可靠性。
3.3 文件管理:建立检验方法和标准的文件管理制度,包括文件的编号、版本控制和变更记录等,以确保检验方法和标准的可追溯性和一致性。
四、检验过程的控制与监督4.1 过程控制:建立检验过程的控制措施,包括样品的管理、检验环境的控制和操作规程的执行等,以确保检验过程的稳定性和可控性。
4.2 过程记录:建立检验过程的记录制度,包括样品的接收记录、检验数据的记录和异常处理记录等,以便追溯和分析检验过程的问题和改进措施。
QC检验能力考核管理规范
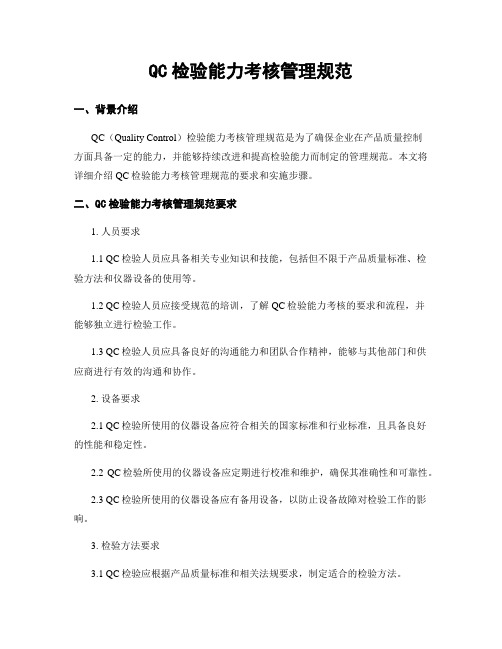
QC检验能力考核管理规范一、背景介绍QC(Quality Control)检验能力考核管理规范是为了确保企业在产品质量控制方面具备一定的能力,并能够持续改进和提高检验能力而制定的管理规范。
本文将详细介绍QC检验能力考核管理规范的要求和实施步骤。
二、QC检验能力考核管理规范要求1. 人员要求1.1 QC检验人员应具备相关专业知识和技能,包括但不限于产品质量标准、检验方法和仪器设备的使用等。
1.2 QC检验人员应接受规范的培训,了解QC检验能力考核的要求和流程,并能够独立进行检验工作。
1.3 QC检验人员应具备良好的沟通能力和团队合作精神,能够与其他部门和供应商进行有效的沟通和协作。
2. 设备要求2.1 QC检验所使用的仪器设备应符合相关的国家标准和行业标准,且具备良好的性能和稳定性。
2.2 QC检验所使用的仪器设备应定期进行校准和维护,确保其准确性和可靠性。
2.3 QC检验所使用的仪器设备应有备用设备,以防止设备故障对检验工作的影响。
3. 检验方法要求3.1 QC检验应根据产品质量标准和相关法规要求,制定适合的检验方法。
3.2 QC检验应使用正确的检验方法和仪器设备,确保检验结果的准确性和可靠性。
3.3 QC检验应记录检验方法和结果,以备查证和追溯。
4. 检验标准要求4.1 QC检验应根据产品质量标准和相关法规要求,制定适合的检验标准。
4.2 QC检验应使用正确的检验标准,对产品进行全面和准确的检验。
4.3 QC检验应根据检验结果,及时调整和改进检验标准,以提高检验能力和产品质量。
5. 数据分析和报告要求5.1 QC检验应对检验数据进行分析,发现问题和异常,并及时采取纠正和预防措施。
5.2 QC检验应编制检验报告,将检验结果及时反馈给相关部门和供应商,并提出改进建议。
5.3 QC检验应建立数据统计和分析的体系,以便于监控和评估检验能力的提升。
三、QC检验能力考核管理规范实施步骤1. 制定QC检验能力考核管理规范的计划和目标,明确考核的内容和要求。
QC检验能力考核管理规范

QC检验能力考核管理规范一、背景介绍QC(Quality Control)检验能力考核是企业为了确保产品质量,提高生产效率和满足客户需求而进行的一项重要工作。
通过对QC检验人员的能力进行考核,可以评估其是否具备正确的检验技能和知识,以及是否能够准确判断产品质量。
二、考核目的1. 确保QC检验人员具备正确的检验技能和知识,能够准确判断产品质量。
2. 提高QC检验人员的工作效率和准确性,减少产品质量问题和不合格率。
3. 促使QC检验人员不断学习和提升自己的专业水平,适应市场和技术的变化。
三、考核内容1. 理论知识考核:包括产品的质量标准、检验方法和流程、常见的产品质量问题等方面的知识。
2. 实际操作考核:通过对实际产品进行检验,考察QC检验人员的操作技巧、仪器使用和数据分析能力。
3. 判断能力考核:通过给出一些产品质量问题的案例,考察QC检验人员的判断能力和解决问题的能力。
四、考核流程1. 提前通知:考核前,应提前通知参加考核的QC检验人员,告知考核的时间、地点和考核内容。
2. 考核准备:参加考核的QC检验人员需要提前准备相关的理论知识和实际操作技能。
3. 考核进行:按照考核内容,组织考核人员进行理论知识考核、实际操作考核和判断能力考核。
4. 考核评估:根据考核结果,对参加考核的QC检验人员进行评估,给出合格或不合格的判定。
5. 反馈和改进:对于不合格的QC检验人员,应及时给出具体的不合格原因,并制定相应的改进计划和培训措施。
五、考核结果的应用1. 人员岗位安排:根据考核结果,合格的QC检验人员可以继续担任相关岗位,不合格的人员需要进行培训或调整岗位。
2. 奖惩措施:对于考核结果优秀的QC检验人员,可以给予相应的奖励和激励措施;对于多次不合格的人员,应采取相应的纪律处分措施。
3. 持续改进:根据考核结果,总结经验教训,不断完善和改进QC检验能力考核管理规范,提高考核的科学性和有效性。
六、考核管理的要求1. 公正公平:考核过程中要保证公正公平,不得有任何歧视和偏袒行为。
QC检验能力考核管理规范

QC检验能力考核管理规范一、背景介绍为了确保产品质量和生产流程的稳定性,对于质量控制部门的QC检验人员的能力进行考核是必要的。
本文旨在制定一套QC检验能力考核管理规范,以确保检验人员的能力达到要求,提高产品质量和生产效率。
二、考核目的1. 确保QC检验人员具备必要的技能和知识,能够准确、可靠地进行产品质量检验。
2. 评估QC检验人员的工作表现,发现问题并及时进行改进。
3. 为QC检验人员提供个人成长和发展的机会。
三、考核内容1. 理论知识考核:对QC检验人员的理论知识进行考核,包括产品规格、检验标准、检验方法等。
考核方式:书面考试或在线考试。
考核内容:根据产品特点和行业标准制定的考题,包括选择题、判断题、简答题等。
2. 技能操作考核:对QC检验人员的实际操作能力进行考核,包括使用检验设备、操作检验仪器、判断产品合格与否等。
考核方式:实际操作考核。
考核内容:根据产品特点和检验要求,设置一系列的检验项目,要求考核人员独立完成。
3. 问题解决能力考核:对QC检验人员的问题解决能力进行考核,包括发现问题、分析问题原因、提出解决方案等。
考核方式:个人面试或小组讨论。
考核内容:根据实际工作情况,设置一系列的问题场景,要求考核人员进行思考和回答。
四、考核流程1. 考核计划制定:质量控制部门根据实际情况制定年度考核计划,明确考核的时间、内容和参与人员。
2. 考核准备工作:质量控制部门组织相关培训,确保考核人员具备必要的知识和技能。
3. 考核实施:按照考核计划进行考核,分别进行理论知识考核、技能操作考核和问题解决能力考核。
4. 考核结果评估:质量控制部门根据考核结果进行评估,确定考核人员的能力水平。
5. 反馈和改进:质量控制部门将考核结果反馈给考核人员,并提出改进意见和建议。
6. 能力提升计划:根据考核结果,制定个人能力提升计划,为考核人员提供个人成长和发展的机会。
五、考核记录和管理1. 考核记录:质量控制部门对每次考核进行记录,包括考核时间、内容、参与人员和考核结果等。
QC检验能力考核管理规范
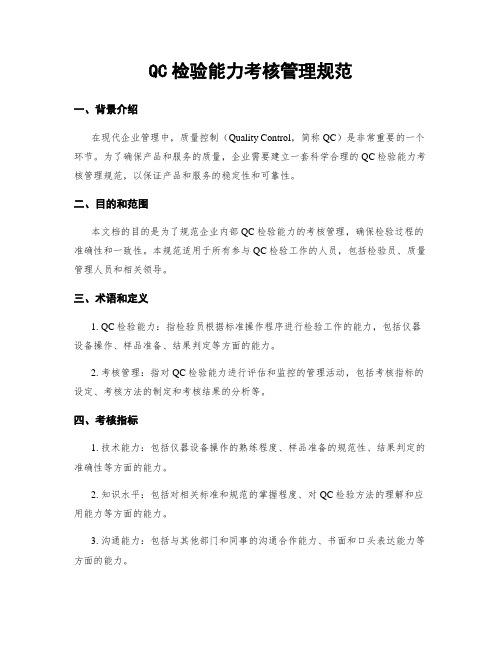
QC检验能力考核管理规范一、背景介绍在现代企业管理中,质量控制(Quality Control,简称QC)是非常重要的一个环节。
为了确保产品和服务的质量,企业需要建立一套科学合理的QC检验能力考核管理规范,以保证产品和服务的稳定性和可靠性。
二、目的和范围本文档的目的是为了规范企业内部QC检验能力的考核管理,确保检验过程的准确性和一致性。
本规范适用于所有参与QC检验工作的人员,包括检验员、质量管理人员和相关领导。
三、术语和定义1. QC检验能力:指检验员根据标准操作程序进行检验工作的能力,包括仪器设备操作、样品准备、结果判定等方面的能力。
2. 考核管理:指对QC检验能力进行评估和监控的管理活动,包括考核指标的设定、考核方法的制定和考核结果的分析等。
四、考核指标1. 技术能力:包括仪器设备操作的熟练程度、样品准备的规范性、结果判定的准确性等方面的能力。
2. 知识水平:包括对相关标准和规范的掌握程度、对QC检验方法的理解和应用能力等方面的能力。
3. 沟通能力:包括与其他部门和同事的沟通合作能力、书面和口头表达能力等方面的能力。
五、考核方法1. 理论考核:通过书面考试的方式,对检验员的知识水平进行评估。
考试内容包括相关标准和规范、QC检验方法和仪器设备的操作等。
2. 实际操作考核:通过对检验员进行实际操作的考核,评估其技术能力和样品处理的规范性。
考核内容包括仪器设备操作、样品准备和结果判定等。
3. 互评考核:通过同行之间的互评,评估检验员的沟通能力和团队合作精神。
互评方式可以是匿名评价或者面对面评价。
六、考核结果与分析1. 考核结果的评定:根据考核指标的设定,对每个考核项目进行评分,综合计算得出总分。
根据总分的高低,将检验员分为优秀、良好、合格和不合格等等级。
2. 考核结果的记录和分析:将每次考核的结果记录在档案中,并进行分析。
分析考核结果的目的是发现问题和改进措施,以提升整体QC检验能力。
七、考核结果的应用1. 奖惩机制:根据考核结果,对表现优秀的检验员给予奖励,如加薪、晋升等;对表现不合格的检验员进行惩罚,如警告、降薪等。
QC检验能力考核管理规范

QC检验能力考核管理规范引言概述:QC(Quality Control)检验能力考核管理规范是指对企业质量控制部门进行检验能力的评估和管理的一套规范。
通过对检验能力的准确评估和有效管理,可以提高产品质量,降低不合格品率,提升企业竞争力。
本文将从四个方面介绍QC检验能力考核管理规范。
一、考核标准的制定1.1 确定考核指标:根据企业的产品特点和质量要求,制定适合的考核指标,如检验项目的准确性、可靠性、稳定性等。
1.2 设定考核等级:根据考核指标的重要性和难易程度,将考核等级划分为不同层次,以便对不同水平的检验员进行评估和管理。
1.3 确定考核周期:根据企业的生产周期和产品特点,确定适宜的考核周期,保证考核的及时性和有效性。
二、考核方法的选择2.1 实地考核:通过对检验员的实际操作进行观察和记录,评估其检验能力的准确性和熟练程度。
2.2 文化考核:通过书面考试或者在线测试等方式,对检验员的理论知识进行考核,评估其对相关标准和规范的掌握程度。
2.3 绩效考核:通过对检验员的工作成果进行评估,如检验报告的准确性和及时性等,评估其工作效率和质量。
三、考核结果的分析与反馈3.1 考核结果的统计分析:对考核结果进行统计和分析,了解不同等级检验员的分布情况,发现问题和不足。
3.2 考核结果的反馈:将考核结果及时反馈给检验员本人,指出其优点和不足,并提出改进意见和建议。
3.3 考核结果的应用:根据考核结果,对不同等级的检验员进行分类管理,提供相应的培训和发展机会,促进其能力的提升和成长。
四、考核管理的持续改进4.1 定期评估和修订:定期对QC检验能力考核管理规范进行评估和修订,根据实际情况进行相应的调整和改进。
4.2 培训和提升计划:根据考核结果和企业的需求,制定相应的培训和提升计划,提高检验员的技能水平和专业素质。
4.3 经验分享和交流:建立检验员之间的经验分享和交流机制,促进彼此之间的学习和进步,提升整个团队的检验能力。
QC检验规范

.:CMOLO- AT-W-0一、目的规范检验员的检验方法,确保产品质量,提高工作效率。
二、适用范围适用于QC检验。
三、定义无四、权责品质部要确保各工序产品品质,杜绝不良品流入下一工序。
五、检验条件要求在天然散射光或烈日下不应低于60W光源环境下,正常视力。
六、检验依据《加工图纸》《国家标准》七、检验指引《QC检验规范》《QC检验标准》《钣金检验标准》《机箱检验标准》八、检测工具1. 是否适用检验2. 是否在有效期即是否在校正日期以内.(校验标签)3. 是否定期保养4. 检验前有无测试其精准度九、测量方法1. 有无按测量工具操作指引进行操作•2. 有无对应图纸技术要求的标注进行测量3. 有无按测量基准.及相关产品详细的《测量方法》进行测量.十、检验步骤1. 半成品、成品检验在检验前应戴好必要的防护用品。
如:棉手套.手指套.等检验合格后,贴上绿标签,把合格品放置绿色胶框里,并将合格品放到合格品指定区域如检验不合格,贴上红色标签,把不合格品放置不合格区域,将不合格原因在反馈报告上记录,当天要把问题反馈给QA部QC 按《QC佥验规范》《QC佥验标准》《钣金检验标准》将各工序生产或安装时的产品进行随机检查。
如发现工艺上的问题,将检验结果记录并反馈.2. 制程巡检QC 按抽样计划及检验标准,对各工序生产安装半成品进行随机抽检QC 应对重要优先检查.按轻重缓急检验并将检验结果记录于检验报告中.3. 检验内容:材质确认图纸要求材料与实际生产用料是否相符.(钣金类)确认材料经加工后有无沙孔/气孔.麻点.(钢化玻璃件)外观有无裂纹.破损.压痕.刮花.变形.披锋.变形• 如果发现外观有缺陷可参照《QC 检验标准》 《钣金检验标准》 《机箱检验标准》检验时做到小心轻放.注意保护外观.尺寸符合工艺需求符合图纸设计要求可参照《QC 检验标准》配合度检验时如不能保证尺寸能符合安装要求 ,可以试装,试用4. 检验记录《检验反馈报告》记录要做到:记录及时•内容完整•页面清洁•字迹工整.数据准确•5. 品质异常处理流程:说明:反映问题一定要迅速•异常货品要贴上红色标示放在指定区域隔离 1^一、检验结果处理1. 合格品处理 (贴上合格标签,放到合格品区域或进入下一工序)2. 不合格品处理不合格品管制流程Q |K 佥验鉴下道工序若需进一步处理由品质部知会仓管,并执行纠正措施,或选用 /返修/报废。
QC检验能力考核管理规范
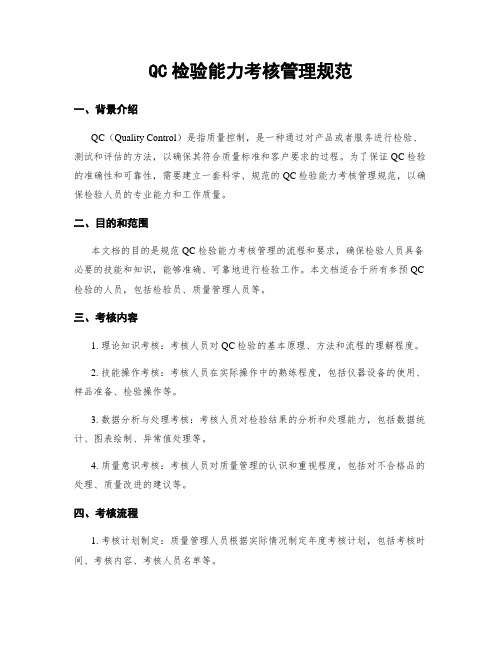
QC检验能力考核管理规范一、背景介绍QC(Quality Control)是指质量控制,是一种通过对产品或者服务进行检验、测试和评估的方法,以确保其符合质量标准和客户要求的过程。
为了保证QC检验的准确性和可靠性,需要建立一套科学、规范的QC检验能力考核管理规范,以确保检验人员的专业能力和工作质量。
二、目的和范围本文档的目的是规范QC检验能力考核管理的流程和要求,确保检验人员具备必要的技能和知识,能够准确、可靠地进行检验工作。
本文档适合于所有参预QC 检验的人员,包括检验员、质量管理人员等。
三、考核内容1. 理论知识考核:考核人员对QC检验的基本原理、方法和流程的理解程度。
2. 技能操作考核:考核人员在实际操作中的熟练程度,包括仪器设备的使用、样品准备、检验操作等。
3. 数据分析与处理考核:考核人员对检验结果的分析和处理能力,包括数据统计、图表绘制、异常值处理等。
4. 质量意识考核:考核人员对质量管理的认识和重视程度,包括对不合格品的处理、质量改进的建议等。
四、考核流程1. 考核计划制定:质量管理人员根据实际情况制定年度考核计划,包括考核时间、考核内容、考核人员名单等。
2. 考核准备:考核人员根据考核计划,自行准备相关资料和器材,并熟悉考核要求和流程。
3. 理论知识考核:采用笔试形式进行,考核人员需回答与QC检验相关的理论知识问题。
4. 技能操作考核:考核人员需在指定的实验室环境下进行操作,根据考核要求完成一系列的检验任务。
5. 数据分析与处理考核:考核人员需根据给定的数据进行分析和处理,并提交相应的报告。
6. 质量意识考核:通过面试的形式进行,考核人员需回答与质量管理相关的问题,并展示自己的质量意识和改进能力。
7. 考核评估:考核结束后,由专业评估人员对考核结果进行评估和打分,并形成评估报告。
8. 考核结果反馈:将评估报告反馈给考核人员,包括考核结果、不足之处和改进建议等。
五、考核结果处理1. 合格:考核人员在所有考核项目中均达到或者超过合格标准,被认定为合格人员。
- 1、下载文档前请自行甄别文档内容的完整性,平台不提供额外的编辑、内容补充、找答案等附加服务。
- 2、"仅部分预览"的文档,不可在线预览部分如存在完整性等问题,可反馈申请退款(可完整预览的文档不适用该条件!)。
- 3、如文档侵犯您的权益,请联系客服反馈,我们会尽快为您处理(人工客服工作时间:9:00-18:30)。
Q C检验规范
DOC.NO.:CMOLO-AT-W-0
一、目的
规范检验员的检验方法,确保产品质量,提高工作效率。
二、适用范围
适用于QC检验。
三、定义无
四、权责
品质部要确保各工序产品品质,杜绝不良品流入下一工序。
五、检验条件
要求在天然散射光或烈日下不应低于60W光源环境下,正常视力。
六、检验依据
《加工图纸》《国家标准》
七、检验指引
《QC检验规范》《QC检验标准》《钣金检验标准》《机箱检验标准》
八、检测工具
1.是否适用检验
2.是否在有效期即是否在校正日期以内.(校验标签)
3.是否定期保养
4.检验前有无测试其精准度
九、测量方法
1.有无按测量工具操作指引进行操作.
2.有无对应图纸技术要求的标注进行测量
3.有无按测量基准.及相关产品详细的《测量方法》进行测量.
十、检验步骤
1.半成品、成品检验
1.2检验合格后,贴上绿标签,把合格品放置绿色胶框里,并将合格品放到合格品指定区域
1.3如检验不合格,贴上红色标签,把不合格品放置不合格区域,将不合格原因在反馈报告上记录,当天要
把问题反馈给QA部
1.4QC按《QC检验规范》《QC检验标准》《钣金检验标准》将各工序生产或安装时的产品进行随机检查。
如
发现工艺上的问题,将检验结果记录并反馈.
2.制程巡检
2.1QC按抽样计划及检验标准,对各工序生产安装半成品进行随机抽检.
2.2QC应对重要优先检查.按轻重缓急检验并将检验结果记录于检验报告中.
3.检验内容:
3.1材质
3.11确认图纸要求材料与实际生产用料是否相符.(钣金类)
3.12确认材料经加工后有无沙孔/气孔.麻点.(钢化玻璃件)
3.2外观
3.21有无裂纹.破损.压痕.刮花.变形.披锋.变形.
2.黄色:表示不良品因为交期等不明原因不做处理予以特采的
3.红色:不合格品
备注:填写时一定要写完整.清楚.(品名.图号.检验员.日期.数量原因等) 编制:审核:批准:实施日期:年月日 3.22如果发现外观有缺陷可参照《QC 检验标准》《钣金检验标准》《机箱检验标准》
3.23检验时做到小心轻放.注意保护外观.
3.3尺寸
3.31符合工艺需求
3.32符合图纸设计要求
3.33可参照《QC 检验标准》
3.4配合度
3.41检验时如不能保证尺寸能符合安装要求,可以试装,试用
4.检验记录
4.1《检验反馈报告》
4.2记录要做到:记录及时.内容完整.页面清洁.字迹工整.数据准确.
5.品质异常处理
5.1流程:
5.2
十一、检验结果处理
1.合格品处理(贴上合格标签,放到合格品区域或进入下一工序)
2.不合格品处理
2.1不合格品管制流程
2.11OKOK
2.12NONO
2.2
2.3若需进一步处理由品质部知会仓管,并执行纠正措施,或选用/返修/报废。
2.4挑选,返修后的产品要全检.
十二、标签使用
1.绿色:表示成品检验合格。