车身结构与设计论文
先进的车身设计提高行驶稳定性和安全性

先进的车身设计提高行驶稳定性和安全性随着科技的不断进步,车辆的设计和技术也在不断改进。
其中,车身设计的先进性对于行驶稳定性和安全性的提升起着至关重要的作用。
本文将探讨先进的车身设计如何提高行驶稳定性和安全性。
1. 气动力学设计先进的车身设计将注重气动力学原理的运用,以减少空气阻力和提高车辆的稳定性。
通过改善车身的外形和细节设计,例如减少车辆阻力的空气动力学设计、引入有效的风洞实验等,车辆可以更好地与空气流动相适应,降低风阻系数,减少空气阻力对车辆行驶的影响,提高车辆的稳定性和燃油经济性。
2. 车身结构设计车身结构的先进设计可以提供更高的刚度和强度,从而增加车辆的稳定性和安全性。
采用先进的车身材料,如高强度钢材、铝合金等,可以提高车身的刚度和强度,有效抵抗车辆在行驶过程中受到的侧向力和冲击。
同时,合理的车身结构设计还可以提供更好的防护性能,减少碰撞事故对车内乘员的伤害。
3. 悬挂系统设计悬挂系统作为车辆的重要组成部分,对于行驶的稳定性和安全性起着重要的影响。
先进的悬挂系统设计可以保持车辆的轮胎接地面积更大,提供更好的操控性和抓地力,从而增强车辆的稳定性。
例如,采用独立悬挂系统和可调节悬挂系统,可以根据行驶条件和需求进行调整,提高车辆在不同路况下的稳定性和驾驶舒适性。
4. 安全辅助系统设计先进的车身设计不仅关注行驶的稳定性,还注重安全性能的提升。
现代车辆普遍配备了各种安全辅助系统,如防抱死制动系统(ABS)、电子稳定控制系统(ESC)、自适应巡航控制系统(ACC)等。
这些系统通过使用传感器、计算机和执行器等技术,可以实时监测车辆的状态并采取相应的控制措施,提供更好的行驶稳定性和安全性。
5. 先进的驾驶员辅助系统先进的车身设计还包括驾驶员辅助系统的开发和应用。
例如,采用先进的制动辅助系统、车道保持辅助系统等,可以提供更好的驾驶员操作体验和驾驶安全性。
这些系统通过与车辆的传感器和人机交互界面的结合,可以提醒驾驶员注意安全、辅助驾驶员正确操作,并在危险时采取措施进行干预,从而减少驾驶员的疲劳和人为操作错误,提高行驶的稳定性和安全性。
汽车车身结构设计模块刚性和轻量化的平衡
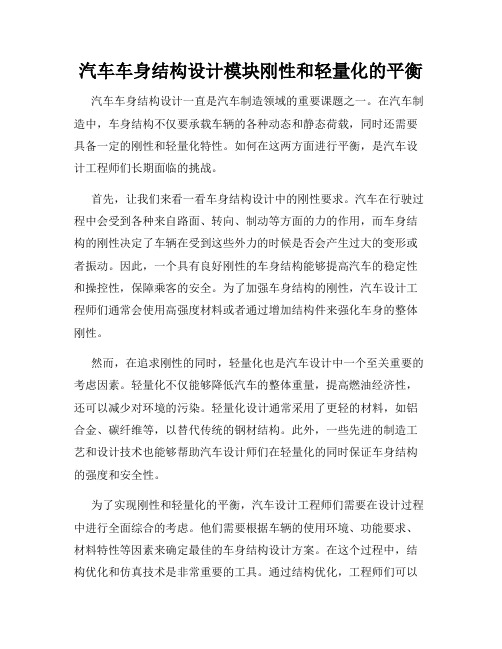
汽车车身结构设计模块刚性和轻量化的平衡汽车车身结构设计一直是汽车制造领域的重要课题之一。
在汽车制造中,车身结构不仅要承载车辆的各种动态和静态荷载,同时还需要具备一定的刚性和轻量化特性。
如何在这两方面进行平衡,是汽车设计工程师们长期面临的挑战。
首先,让我们来看一看车身结构设计中的刚性要求。
汽车在行驶过程中会受到各种来自路面、转向、制动等方面的力的作用,而车身结构的刚性决定了车辆在受到这些外力的时候是否会产生过大的变形或者振动。
因此,一个具有良好刚性的车身结构能够提高汽车的稳定性和操控性,保障乘客的安全。
为了加强车身结构的刚性,汽车设计工程师们通常会使用高强度材料或者通过增加结构件来强化车身的整体刚性。
然而,在追求刚性的同时,轻量化也是汽车设计中一个至关重要的考虑因素。
轻量化不仅能够降低汽车的整体重量,提高燃油经济性,还可以减少对环境的污染。
轻量化设计通常采用了更轻的材料,如铝合金、碳纤维等,以替代传统的钢材结构。
此外,一些先进的制造工艺和设计技术也能够帮助汽车设计师们在轻量化的同时保证车身结构的强度和安全性。
为了实现刚性和轻量化的平衡,汽车设计工程师们需要在设计过程中进行全面综合的考虑。
他们需要根据车辆的使用环境、功能要求、材料特性等因素来确定最佳的车身结构设计方案。
在这个过程中,结构优化和仿真技术是非常重要的工具。
通过结构优化,工程师们可以在不断调整设计方案的过程中找到一个最佳的平衡点。
而通过仿真技术,他们可以对车身结构的性能进行全面的评估,发现潜在的问题并提出改进方案。
此外,汽车制造领域的快速发展也为实现刚性和轻量化的平衡提供了更多的机会。
新材料、新工艺的应用不断推动着汽车设计与制造的技术水平提升。
例如,3D打印技术可以以更加灵活的方式制造出复杂形状的零部件,从而减少材料浪费,提高结构的刚性和轻量化水平。
此外,智能制造技术的应用也为汽车制造业带来了新的发展机遇,可以更加精确地控制材料的使用和工艺的执行,从而实现更加优化的车身结构设计。
某皮卡车身防腐分析及结构设计
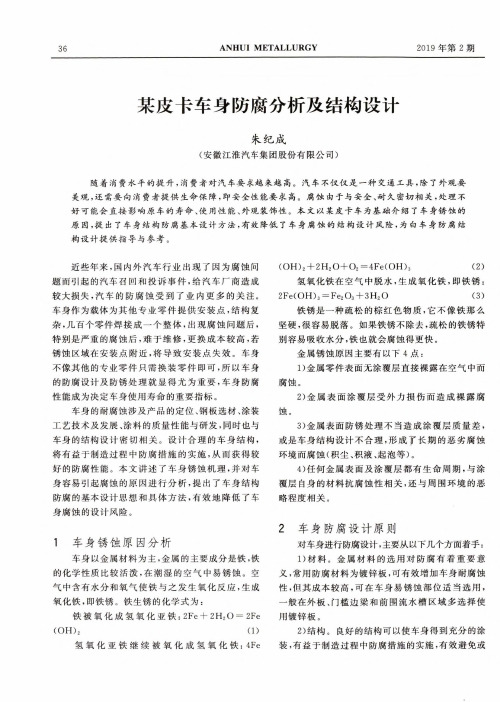
36ANHUI METALLURGY2019年第2期某皮卡车身防腐分析及结构设计朱纪成(安徽江淮汽车集团股份有限公司)随着消费水平的提升,消费者对汽车要求越来越高。
汽车不仅仅是一种交通工具,除了外观要美观,还需要向消费者提供生命保障,即安全性能要求高。
腐蚀由于与安全、耐久密切相关,处理不好可能会直接影响原车的寿命、使用性能、外观装饰性。
本文以某皮卡车为基础介绍了车身锈蚀的原因,提出了车身结构防腐基本设计方法,有效降低了车身腐蚀的结构设计风险,为白车身防腐结构设计提供指导与参考。
近些年来,国内外汽车行业出现了因为腐蚀问题而引起的汽车召回和投诉事件,给汽车厂商造成较大损失,汽车的防腐蚀受到了业内更多的关注。
车身作为载体为其他专业零件提供安装点,结构复杂,几百个零件焊接成一个整体,出现腐蚀问题后,特别是严重的腐蚀后,难于维修,更换成本较高,若锈蚀区域在安装点附近,将导致安装点失效。
车身不像其他的专业零件只需换装零件即可,所以车身的防腐设计及防锈处理就显得尤为重要,车身防腐性能成为决定车身使用寿命的重要指标。
车身的耐腐蚀涉及产品的定位、钢板选材、涂装工艺技术及发展、涂料的质量性能与研发,同时也与车身的结构设计密切相关。
设计合理的车身结构,将有益于制造过程中防腐措施的实施,从而获得较好的防腐性能。
本文讲述了车身锈蚀机理,并对车身容易引起腐蚀的原因进行分析,提出了车身结构防腐的基本设计思想和具体方法,有效地降低了车身腐蚀的设计风险。
1车身锈蚀原因分析车身以金属材料为主,金属的主要成分是铁,铁的化学性质比较活泼,在潮湿的空气中易锈蚀。
空气中含有水分和氧气使铁与之发生氧化反应,生成氧化铁,即铁锈。
铁生锈的化学式为:铁被氧化成氢氧化亚铁:2Fe+2H2O=2Fe (OH)2(1)氢氧化亚铁继续被氧化成氢氧化铁:4Fe (OH)2+2H2O+O2=4Fe(OH)3(2)氢氧化铁在空气中脱水,生成氧化铁,即铁锈:2Fe(OH)3=Fe2O3+3H2O (3)铁锈是一种疏松的棕红色物质,它不像铁那么坚硬,很容易脱落。
车身结构优化设计与性能分析

车身结构优化设计与性能分析一、前言汽车行业经历了长达一个世纪的发展,车身结构也随之不断进化。
从最初的单纯金属制造到现在的多材料结构,每一次的演变都让汽车更加安全与高效。
本文将从车身结构的优化设计入手,探讨如何提高汽车性能。
二、车身结构的优化设计1. 材料选择在过去,车身结构主要是由钢铁等金属材料构成,但现在随着新材料技术的不断发展,更多的新材料被应用于车身结构上。
比如碳纤维,它的强度和刚度比钢铁还高,同时它的重量却要轻很多,可以大大减轻汽车的整体重量,提高汽车的燃油效率和节能性能。
2. 结构设计车身结构设计需要考虑车辆的性能和安全性。
为了达到这些目标,工程师们通常会采用一些设计手段来确保车辆在各种条件下的安全性和性能。
例如,在汽车碰撞时,工程师必须确认车身结构能承受撞击力,并且车内乘客得到足够的保护。
设计车身结构时,还要考虑到气动以及流体力学特性,以确保汽车在高速行驶的过程中能够保持稳定的行驶。
3. 仿真计算与传统的试错方法相比,仿真计算可以更加快速而精确地对车身结构进行评估,减少时间和成本。
使用高效的计算机仿真软件,工程师们可以对施力、载荷、应力、扭矩和应变等因素进行详细的分析和优化。
在此基础上,设计出更加优异的车身结构,缩短研发周期,提高产品质量。
三、车身结构性能分析1. 刚度车身结构的刚度对于汽车牵引、平稳行驶、路面过滤等方面的表现有极大的影响。
由于车身结构的强度和刚度取决于材料和构造,在材料性能相同时,通过合理结构设计和优秀的组装工艺可以极大提高车身的刚度。
2. 强度车身结构的强度代表着汽车在受到外力冲撞时对撞击力的抵抗能力。
因此,提高车身的强度可以保证汽车在各种行业标准测试下的安全性能。
3. 抗拉能力抗拉能力是车身结构性能的一个重要指标,它代表了车身在受到拉力时的能力。
因此,车身结构的材料和结构设计需要具备足够的抗拉能力,以确保车辆在行驶过程中不易损坏。
4. 范德瓦尔斯力分析驾驶车辆时,车身的稳定性对乘客的感觉和安全性都是非常重要的。
轻型汽车车身结构设计与优化

轻型汽车车身结构设计与优化现今,轻型汽车成为人们日常生活中必不可少的交通工具。
而轻型汽车的车身结构设计与优化已经成为汽车制造业的研究热点之一。
轻型汽车车身结构设计的主要目的是为了提升汽车的安全性、驾驶舒适性、能源利用效率和减轻整车重量等方面,而车身结构优化则是为了通过技术手段使得轻型汽车减少整车重量以及提高整车综合性能。
轻型汽车车身结构的设计必须考虑到以下几个方面:1.结构的强度与刚度轻型汽车的车身结构必须保证足够的强度和刚度,以抵御意外碰撞或其他外力的影响。
优秀的车身结构设计要确保车辆在车祸中的碰撞安全,避免人员和物品的损失。
一般来说,此类车型会采用各种合金材料,通过压铸及其他制造方法,减轻车身自重以达到增强强度与刚度的目的。
2.空气动力学设计空气动力学设计是一项重要的设计考虑因素,它可以有效提高轻型汽车的行驶稳定性和车辆油耗。
空气动力学测试可以反映出来车辆行驶中受到的空气阻力和气流,一款脱离空气动力学基础测试的汽车,无法确保驾驶员和乘客在汽车高速移动中的安全。
3.人机工程学设计在轻型汽车设计的全过程中,人机工程学设计也是非常重要的一部分,其目的在于设计出切合人体工程学规律的驾驶舱室空间,让驾驶员在驾驶过程中更加舒适自如。
4.制造成本轻型汽车的制造成本在合理控制之后,其价格也可以降低,对消费者的物质压力也有所缓解。
因此,在车身结构设计中,切合实际的制造成本也是一项非常重要的考虑因素。
对于轻型汽车的结构优化而言,主要包括如下几个方面:1.减少车身自重为了降低轻型汽车的整车重量,在配备安全性能的情况下尽量减少车身自重。
这需要采用各种轻量化材料,如高强度钢材料、碳纤维等。
2.提高车身刚度在自重减少的情况下,也需要保持足够的车身刚度,以确保轻型汽车的驾驶稳定性。
3.改进动力系统轻型汽车的动力系统可以通过改进提高其工作效率,使其能在一定程度上减少车身自重。
总结起来,轻型汽车车身结构设计与优化需要综合考虑诸多因素。
轿车车身结构毕业设计
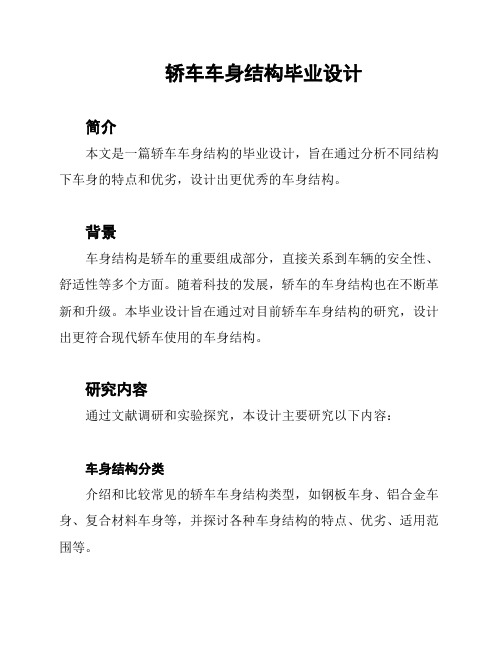
轿车车身结构毕业设计
简介
本文是一篇轿车车身结构的毕业设计,旨在通过分析不同结构下车身的特点和优劣,设计出更优秀的车身结构。
背景
车身结构是轿车的重要组成部分,直接关系到车辆的安全性、舒适性等多个方面。
随着科技的发展,轿车的车身结构也在不断革新和升级。
本毕业设计旨在通过对目前轿车车身结构的研究,设计出更符合现代轿车使用的车身结构。
研究内容
通过文献调研和实验探究,本设计主要研究以下内容:
车身结构分类
介绍和比较常见的轿车车身结构类型,如钢板车身、铝合金车身、复合材料车身等,并探讨各种车身结构的特点、优劣、适用范围等。
车身结构设计
结合轿车车身的实际使用情况和安全性要求,设计出一种更优秀的车身结构,探讨轿车车身结构的未来发展方向和趋势。
结论
通过对文献调研和实验研究,本设计提出了一种更优秀的轿车车身结构设计方案,并探讨了车身结构的未来发展方向和趋势。
有望为轿车车身结构的研究和设计工作提供新的思路和方法。
参考文献
- 张三, 钟南山. (2016). 轿车车身结构研究. 上海交通大学学报, 20(6), 18-23.
- 李四, 王五. (2017). 轿车车身结构的优化设计. 机械设计与制造, 36(3), 52-57.。
客车车身结构及其设计方案
客车车身构造及其设计方案摘要:客车是目前最常见和主要的交通工具之一,随着人们对出行的要求越来越高,从而也对客车提出了更好的要求。
合理的车身构造、更小的能耗、更大的承载量以及更长的使用寿命是客车车身构造及其设计时需要考虑的问题,而随着这些问题的凸显,车身构造设计也越来越受重视,本文从车身构造的分类及其设计方案来探讨客车设计的多样性。
关键字:客车;车身构造设计;客车车身分类1.引言客车的合理设计,是保证其承载量和使用寿命的重要缘由。
优秀的设计,不能仅能够提升效益,降低能耗,还能够从各个方面保障行车与民众安全。
在国际标准中,对客车车身的定义为:长方形,用来装载乘客和行李的车厢。
由于客车种类繁多,车身构造也多种多样,本文针对客车车身构造及其设计,从分类方法、设计思路等多个方面进展阐述,力求为行业查找最优的车身构造设计,为行业的进展供给参考依据。
1.客车车身构造及分类常见的客车车身构造及分类方法如下:1.按用途分类依据客车的使用方式,可以分为城市客车、长途客车、旅游客车和专用客车四个类别。
其用途和优点比照方下:客车身构造设计特点车用途1.城设有乘客站立区域市客车 2.车厢在设计时充分考虑频繁上下客的问题,座椅少、车门多且有扶手,走动空间大,通道宽。
1.长无站立位,每个乘客一个位置的设计。
途客车 2.座椅较为密集,且质量好,这是为了保证长途坐车的舒适性,且此类客车车厢地板高,车厢下有行李舱。
旅其与长途客车的设计原则根本相近,但在游客外观和舒适性等方面比长途客车好,车内设施车及附件设备也更豪华和高档。
专与长途客车设计类似,但无行李箱,一般用客是依据特定要求来设计和制造,常见于校车、车机场摆渡车、采血车等。
〔二〕按承载形式分类按车身承载形式,客车车身构造可分为非承载式、半承载式和承载式三大类。
1、非承载式客车国内的轻型客车,大局部就是非承载式的设计,底盘有车架,靠车架支撑全车。
图 1- 非承载式客车的底盘及车身2、半承载式客车车身半承载式车身就是车身与车架刚性连接,车身局部承载的构造形式。
新能源车辆车身结构轻量化设计研究
新能源车辆车身结构轻量化设计研究随着环保理念的日益普及,新能源车辆已经成为了市场上瞩目的领域。
然而,对于新能源车辆而言,车身结构轻量化的问题是其制造以及续航能力的重要因素。
在本文中,我们将探讨如何通过轻量化设计来提高新能源车辆的性能和实现可持续发展。
一、轻量化设计的概念和意义轻量化设计即是通过减少汽车的重量来提高其性能表现的设计方案。
轻量化设计可以分为两种,一种是材料轻量化,另一种是结构轻量化。
材料轻量化是通过采用新材料、优化材料厚度或者减少材料的使用量来减轻汽车的重量。
而结构轻量化是通过优化汽车的构造设计、减少结构件的数量来减轻汽车的重量。
轻量化设计对于新能源汽车而言至关重要。
因为新能源汽车的基础是电力,而电池的质量和容量决定了其续航能力。
所以,在保证其稳定性和安全性的前提下,轻量化设计可以有效地提高新能源汽车的续航能力,增强其市场竞争力。
二、新能源汽车轻量化设计的研究现状目前,新能源汽车轻量化设计的研究主要集中在车身结构和材料方面。
其中,一些新型的材料,例如碳纤维复合材料、铝合金材料等已经被广泛应用于新能源汽车的制造中。
这些新材料能够实现优异的性能表现和轻质化的效果,带来了良好的市场反响。
另一方面,新能源汽车的车身结构设计也在不断优化中。
例如应用优化设计原理和计算机模拟技术,可以优化车身结构,降低重量。
通过减少车身壳体中的不必要的支撑和加固结构,使得车身结构更加稳固、安全,并且减轻了车身自重。
三、新能源汽车轻量化设计的前景和发展趋势从行业发展的角度来看,新能源汽车的未来发展必将趋势于轻量化。
因为随着人们的环保意识不断加强,节能与低碳成为了社会发展的主旋律。
同时,轻量化设计将成为新能源汽车更为普遍的发展趋势,也是制造商实现可持续发展的重要途径。
在实际生产中,新能源汽车制造商也在不断地进行创新与改进,在材料和结构方面寻求技术的突破。
例如,压铸成形、全铝车身、高强钢材料等均成为了新能源汽车轻量化设计的重要发展方向。
车身结构设计的安全与稳定性
车身结构设计的安全与稳定性在汽车工业的发展中,车身结构的设计是至关重要的。
一个安全与稳定的车身结构不仅能够提供乘车人员的保护,还能够降低事故发生时的伤害程度。
本文将论述车身结构设计的安全与稳定性,并探讨其在汽车工业中的重要性。
一、安全性设计1. 合理的车身布局合理的车身布局是确保车辆安全的基础。
在车身结构设计中,需要考虑乘车人员的位置和乘坐的空间,以便在碰撞时提供最大限度的保护。
同时,车身布局还应考虑到车辆的稳定性和操控性,以确保在各种路况下驾驶的安全性。
2. 强度与刚度的平衡车身结构的强度和刚度对于车辆的安全起着至关重要的作用。
一方面,车身结构应具备足够的强度,以承受发生碰撞时产生的冲击力,避免车辆变形或破裂。
另一方面,车身结构应具备适度的刚度,以确保在高速行驶时车辆的稳定性。
通过平衡强度和刚度,可以提高车辆的安全性能。
3. 防撞设计防撞设计是车身结构设计中的重要环节。
采用吸能材料和各种防撞装置,如防撞梁、气囊等,可以在碰撞时吸收和分散能量,减轻乘车人员的伤害。
同时,防撞设计还应考虑到不同角度和不同速度下的碰撞情况,以全面提高车辆的安全性。
二、稳定性设计1. 重心与平衡车辆的重心位置对于稳定性起着决定性的作用。
合理的重心设计可以降低车辆在高速行驶和弯道驾驶时的倾斜程度,提高车辆的稳定性。
此外,车辆的前后重量平衡也是影响稳定性的重要因素。
通过合理设计车身结构,可以实现重心位置和重量平衡的最佳化。
2. 悬挂系统设计悬挂系统是车辆稳定性设计中的重要组成部分。
合理的悬挂系统可以提高车辆的操控性和稳定性。
通过选用合适的减震器、弹簧和悬挂连接件等,可以减少车辆在行驶过程中的颠簸感,提高车辆的稳定性和舒适性。
3. 气动性设计气动性设计对于车辆的稳定性具有重要影响。
通过减小车辆的气动阻力和提高车辆的空气动力学效应,可以降低车辆在高速行驶时的抗风性能,提高车辆的稳定性。
采用空气动力学模拟和流场分析等技术,可以优化车身外形,提高车辆的气动性能。
英文汽车结构作文
英文汽车结构作文英文:As a car enthusiast, I have always been fascinated by the structure of automobiles. The design and engineering that goes into creating a car is truly remarkable. There are several components that make up a car's structure, including the chassis, body, suspension, and drivetrain.The chassis is the foundation of the car's structure and provides support for all the other components. It is typically made of steel or aluminum and is designed to be strong and rigid. The body of the car is attached to the chassis and is responsible for providing protection for the passengers and cargo. It is typically made of lightweight materials such as aluminum or carbon fiber.The suspension system is responsible for providing a smooth ride and ensuring that the car stays stable while driving. It is made up of several components, including theshocks, struts, and springs. The drivetrain is responsible for transferring power from the engine to the wheels. It is made up of several components, including the transmission, driveshaft, and differential.Overall, the structure of a car is a complex andintricate system that requires careful engineering and design. It is truly amazing to see how all of these components work together to create a functional andefficient vehicle.中文:作为一个汽车爱好者,我一直被汽车的结构所吸引。
- 1、下载文档前请自行甄别文档内容的完整性,平台不提供额外的编辑、内容补充、找答案等附加服务。
- 2、"仅部分预览"的文档,不可在线预览部分如存在完整性等问题,可反馈申请退款(可完整预览的文档不适用该条件!)。
- 3、如文档侵犯您的权益,请联系客服反馈,我们会尽快为您处理(人工客服工作时间:9:00-18:30)。
车身结构与设计基于理论分析汽车气动力及力矩【摘要】汽车空气动力性是汽车的重要特性之一,气动力和气动力矩是它的主要内容。
通过运用数学和物理方法,理论分析气动力及气动力矩的相关参数,进而与汽车的动力性及燃油经济性综合在一起进行分析,找到相关的影响因素,通过改变这些因素来改善汽车性能,合理的选择相关参数,为接下来的设计及模拟仿真做好铺垫。
【关键词】空气动力性气动力气动力矩气动阻力动力性燃油经济性前言汽车空气动力性是汽车的重要特性之一,它直接影响汽车的动力性、燃油经济性、操纵性、舒适性及安全性,它是指汽车在流场中所受的以阻力为主的包括升力、侧向力的三个气动力及其相应的力矩的作用而产生的车身外部和内部的气流特性、侧风稳定性、气动噪声特性、泥土及灰尘的附着与上卷、刮水器上浮以及发动机冷却、驾驶室内通风、空气调节等特性。
当一辆汽车以80km/h的速度前进时,有60%的动力用于克服空气阻力。
从世界上首款流线型汽车“气流”诞生开始,迄今为止,国内外对于汽车空气动力学的研究方法大致分为一般采取试验法、试验与理论相结合法及数值模拟仿真研究法。
理论研究方法主要是通过数学工具来建立空气运动规律及相应初始、边界条件的理论模型,以揭示气动力产生机理及作用关系。
而试验及模拟仿真都是在理论研究和计算的基础之上进行的,可见理论研究对于汽车空气动力学来说是不容忽视的。
气动力及气动力矩分析1、气动力及力矩汽车与空气相对运动并相互作用,会在汽车车身上产生一个气动力F,这个力的大小与相对运动速度的平方、汽车的迎风面积及取决于车身形状的无量纲气动系数成正比,可表示为F = qSC F = 0.5ρvSC F (1)式中,F为气动力,S为汽车迎风面积,C F为气动系数。
图1为汽车所受气动力及力矩坐标表示图气动阻力F X=qSC D=1/2ρvSC D气动侧力F Y = qSC L=1/2ρvSC L气动升力F Z = qSC Z=1/2ρvSC Z气动侧倾力矩M X=F Z*Y C-F Y*Z C=ρSlC q气动横摆力矩M Y=F X*Z C-F Z*X C=ρSlC N气动纵倾力矩M Z=F Y*X C-F X*Y C=ρSlC M图1 汽车所受气动力及力矩坐标示意图实际中上述力和力矩都应尽量降低,以保证汽车的机动性和燃油经济性。
而从以上各式分析,车速、车身迎风面积是我们可以改进的地方。
现代高档汽车都力求把车身前端尽量做得扁平,减少稳流,进而减少行驶阻力。
2、气动阻力及侧倾力矩汽车气动阻力由压差阻力F XA、摩擦阻力F XB、诱导阻力F XC、干涉阻力F XD 和内流阻力F XE五部分组成。
气动阻力系数只与汽车外形形状有关,与大小无关。
(1)压差阻力因它的大小取决于物体的形状,尤其是物体的后部形状,故又称为形状阻力。
对汽车而言,约占总气动阻力的50%-65%。
由流体力学及伯努利方程可得静压强系数Cp=P-P∞/(0.5ρv∞)=1-(u/v∞) (2)无粘流时,O点处由(2)式知Cp=1。
当来流流至A时,流速由0增到最大值,Cp 由1降为负压最大值。
当来流至B时,流速由最大值降为0,Cp由负压最大值增至1。
不存在气动阻力。
考虑到粘流,O处Cp仍为1,流向A点时,由于增加了表面粘性阻力的作用,使得流速达到最大值的点提前,负压最大值出现在A点之前。
再流至B时,由于粘性阻力,气流发生分离,增大并迅速扩散,从而在二元圆柱后部产生湍流区,有压力差产生气动阻力a 无粘流绕二元圆柱流动b 有粘流绕二元圆柱流动c 无粘流流动力场d 有粘流流动力场图2 汽车车身压强分布(阴影为正压)图3 粘流有无与气动阻力示意图(2)摩擦阻力摩擦阻力是由于空气的粘性作用使得空气与汽车车身表面产生摩擦所形成的阻力。
对汽车而言,约占总气动阻力的6%-10%。
引入附面层定义,即将u=0.99v∞处距物面的距离定义为附面层厚度δ,在附面层内有较大的速度梯度。
靠近汽车车身表面前部的附面层内,各层气流之间互不干涉、运动有序,称为“层流附面层”;后部附面层内的流动会变得杂乱无章,互相干扰,称为“紊流附面层”。
在进行汽车造型时,尽可能使车身表面的气流为层流附面层,减少紊流附面层和气流分离。
图4附面层(3)诱导阻力由尾涡诱导形成,是气动升力所产生的纵向水平分力,一般约占气动阻力的5%~7%。
CD i=βC L/(3.14λ) (3)CD i为诱导阻力系数,λ为宽长比,β为修正系数,C L为升力系数。
由上式可知诱导阻力与升力直接相关,因而要减小诱导阻力,就要设法减小升力。
(4)干涉阻力是由暴露在汽车外部的各种附件引起气流相互干扰而形成的阻力,对汽车而言,约占总气动阻力的12%-16%。
这些附件包括后视镜、门把手、雨刷、流水槽、前牌照、照明灯、前保险杠图5诱导阻力图示以及天线和装饰物等。
不仅本身存在气动阻力,而且当被装配到汽车车身时,会引起附近区域气流的状况,从而产生一个附加的气动阻力。
这就是空气动力学干涉现象。
(5)内流阻力又称内循环阻力,是由冷却发动机等的气流和车内通风气流而形成的阻力,约占气动阻力的12%~20%。
当气流流经等截面直管时,其粘性效应不仅发生在管壁附近,而且还会扩展至整个内部截面,从而产生阻力。
当气流流经渐放变截面直管时,由于管截面的扩张,静压递增形成阻力,可能发生气流分离,进一步产生阻力。
当气流流经突变截面直管、弯管时气流分离现象更为严重,阻力也更大。
侧倾力矩主要有车身侧面形状决定,流线型好侧倾力矩相对较小;汽车的高度和宽度对侧倾力矩影响很大,一般低而宽的汽车侧倾力矩系数比高而窄的汽车侧倾力矩系数小。
3、气动升力及纵倾力矩一辆汽车在行驶时,会对相对静止的空气造成不可避免的冲击,空气会因此向四周流动,而窜入车底的气流会被暂时困于车底的各个机械部件之中,空气会被行驶的汽车拉动,地面上的纸张或树叶会被卷起。
由于汽车车身上下部气流的流速不同,使其上下部形成压力差,从而产生升力。
依据伯努利方程,作用在汽车上的升力将减小轮胎对地面的压力,使轮胎附着力和侧偏刚度降低,影响汽车的操纵稳定性。
无侧风时,升力系数C L在-0.4和+0.4之间,受到侧风影响时,升力系数可能增到3倍。
目前一些两厢车的后部都安装有扰流板,这是一个类似于飞机机翼的原理,只不过向上凹,上部面积小,流速低,下部大流速高,在压差作用下汽车受到向下的作用力,起阻碍升力的作用。
此外还起到美观的作用。
4、侧向力及横摆力矩侧向力及横摆力矩主要影响汽车的直线行驶性能。
由F Y = qSC L=0.5ρvSC L,M Y=F X*Z C-F Z*X C=ρSlC N 。
分析,车身侧面积、车身长度对侧向力及横摆力矩有很大影响,因而一般长度较小、宽度较大、车身低矮的汽车比较好。
有些汽车上在侧方加设侧翼,可以改变侧面气流的旋涡,降低C N,这样就能够在不增大侧向力和升力的条件下,减小横摆力矩。
汽车性能与气动力相关性分析汽车性能主要包括汽车动力性、燃油经济性、操纵稳定性等方面,本文主要从动力性和燃油经济性角度来分析。
动力性汽车的动力性是指汽车在良好的路面上直线行驶时由汽车受到的纵向外力决定的所能达到的平均行驶速度。
最高车速、加速时间和最大爬坡度为其主要评价指标。
(1)最高车速用直接档或超速档在良好的水平路面上行驶时所能达到的最高速度,汽车牵引力只需要克服气动阻力和滚动阻力。
满足的关系式如下F=(G-F Z)f+F X=(G-0.5C Lρv∞S)f+0.5C Dρv∞S (4)式中,F为牵引力,G为汽车重量,F Z为气动升力,f为滚动摩擦系数,F X为气动阻力。
当汽车的牵引力达到最大,即F=F max时,最高车速V max =[2(F max-Gf)/ ρS(C D-C L f) ] (5)由上式可以看出,最高车速与气动阻力和气动升力密切相关,F、G一定时,减小气动阻力系数C D和提高气动升力系数C L均可以提高最高车速,但考虑到行驶稳定性,一般不采用提高气动升力系数的办法。
(2)加速度d v∞/dt=3600ηT [P e-(F X+Gf-F Z f) v∞/3600ηT]/(Gδv∞) (6)由上式分析,减小气动阻力,提高气动升力可以提高汽车加速性能。
目前高档汽车加速到100km/h只需不到10秒,有的如布加迪威龙甚至只需短短的3秒。
对于普通汽车而言,改善加速性能,采用降低气动阻力的方式即可。
(3)最大爬坡度最大爬坡度对应的加速度为0,定义i=tanθ为爬坡度,其中θ为坡度角。
Cosθ近似等于1汽车牵引力只需克服滚动阻力、气动阻力和爬坡阻力。
F=(Gcosθ-F Z)f +0.5C Dρv∞S+ Gsinθ(7)由上式可得最大爬坡度i max=[ F-(G -F Z)f -0.5C Dρv∞S]/ G (8)由上式分析,减小气动阻力可以增加最大爬坡度。
通过以上汽车动力性分析可知,气动力在其中扮演了很重要的角色,尤其是气动升力和气动阻力。
减小气动阻力,适当增大气动升力可以很大程度上改善汽车动力性,未来那些追求速度的汽车公司需要在这两个方面做更多更深远的研究。
燃油经济性燃油经济性在保证动力性的前提下,尽量节省耗油量,主要由百公里燃油消耗量作为标准来衡量。
Q=g e(F f+F D)/(3672ηTγ)=g e[(0.5C Dρv∞S)+(G-0.5C Lρv∞S)f]/( 3672ηTγ)(10)式中,Q为百公里耗油量,g e为燃油消耗率,γ为燃油重度,ηT为效率。
由上式分析,气动阻力和气动升力依然是汽车的百公里油耗的影响因素之一,气动阻力越大、升力越大,燃油经济性越好,同样考虑到行驶安全性,普通车辆只需尽量从减小气动阻力方面来完善即可。
为了减少气动力对汽车性能的影响,现代汽车的设计理念是将汽车设计的更流线更平滑,车身附件更小巧更隐蔽;车轮不宜太宽,车轮室不宜过深;车身底部布局合理;车前部进气格栅设计也应合理。
目前依据汽车空气动力学原理而应用于汽车上的器件主要有阻风板、扰流器、导流罩、底板、裙边、导流板、整流罩、轮辐盖、轮毂罩等,这些应用让汽车外形更美观、性能更优越。
结论汽车理论分析,空气动力学是必不可少的,而气动力、气动力矩又是其中的重中之重。
通过数学工具建立的空气运动规律及相应的初始边界条件的理论模型,揭示了气动力产生的机理及相关参数,它与相对运动速度的平方、汽车的迎风面积、长宽高及车身形状的无量纲气动系数有关,根据相应的公式可以定性和定量的分析一辆汽车所受到的各个气动力及气动力矩,进而定性分析汽车的加速度、耗油量、最高车速等汽车性能参数,并优化它们,以便于进一步分析和设计。
参考文献【1】傅立敏汽车空气动力学机械工业出版社【2】傅立敏汽车空气动力学数值计算北京理工大学出版社【3】谷正气汽车车身现代技术机械工业出版社【4】辛喆汽车发动机原理中国农业大学出版社。