【精品】炼钢转炉设计
年产500万吨合格铸坯炼钢厂转炉炼钢系统设计

年产500万吨合格铸坯炼钢厂转炉炼钢系统设计冶金工程冶金06-3班邵志华指导老师:张芳摘要本设计的题目:年产500万吨合格铸坯炼钢厂转炉炼钢系统设计。
本说明书在实习和参考文献的基础上,对所学知识进行综合利用。
讲述了设计一转炉车间的方法和步骤,说明书中对车间主要系统例如铁水供应系统,废钢供应系统,散装料供应系统,铁合金供应系统,除尘系统等进行了充分论证和比较确定出一套最佳设计方案。
并确定了车间的工艺布置,对跨数及相对位置进行设计,简述了其工艺流程,并在此基础上进行设备计算,包括转炉炉型计算,转炉炉衬计算及金属构件计算,氧枪设计,净化系统设备计算,然后进行车间计算和所用设备的规格和数量的设计,在此基础上进行车间尺寸计算,确定各层平台标高。
最后对转炉车间设计得环境和安全要求进行说明。
为了更加详细说明转炉车间设计中的一些工艺及设备结构,本设计穿插了图形,为能够明确、直观的介绍了转炉炼钢车间的工艺布置。
关键词: 转炉;500万吨;设计;设备计算;车间计算Design of Converter Systems of Annual Output 5 Million Tons of Qualified ContinuousCasting SlabAbstractThis design topic of annual 5 million tons' qualified casting steel of converter steelmaking system.This instruction booklet in the practice and in the reference foundation, to studies the knowledge to carry on the comprehensive utilization.Narrated has designed a converter mill the method and the step, in the instruction booklet to the workshop main system for example molten iron supply system, scrap supply system,dispersed feeds the supply system, ferroalloy supply system,dedusting system and so on to carry on the abundant proof and quite is definite a set of best design proposal.And had determined the workshop craft arrangement, carries on the design to the cross number and the relative position, has summarized its technical process, and carries on the equipment computation in this foundation, including the converter stove computation, the converter lining computation and the converter metal components computation the oxygen gun design, the purification system equipment computation, then carries on the workshop computation and uses the equipment the specification and quantity design, carries on the workshop size computation in this foundation, determines each platform elevation. Finally to environmental and safety requirements of the Steel workshop to carry on the explanation.For more detailed description of some of the converter workshop design technology and equipment structure, the design with graphics, which can clear, intuitive introduces converter steelmaking plant process arrangement.Key word: The Converter;5 million tons;design;the converter equipment calculates;the workshop computation第一章文献综述1.1 国内外钢铁产业的发展情况钢铁产业是国民经济的重要支柱产业,涉及面广、产业关联度高、消费拉动大,在经济建设、社会发展、财政税收、国防建设以及稳定就业等方面发挥着重要作用。
120T炼钢转炉设计 (2)
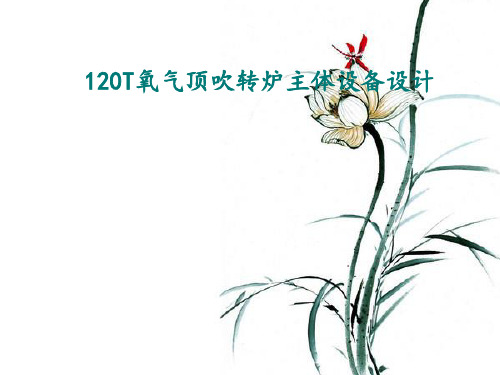
5.造渣制度
石灰加入量的计算公式 : Q=2.2([Si%]铁水+[P%])×R/(CaO%)有效 ×W铁水×1000 式中:Q—石灰加入量(㎏/炉);[Si%]铁水—为铁水硅成分;R—炉渣 碱度; W—铁水量(t);(CaO%)有效—石灰有效CaO含量;(CaO%)有 效=石灰CaO%-R×石灰SiO2%。 终渣碱度要求控制在2.6~3.5,具体数值取决于钢种对终点P、S含量的 要求、入炉铁水处理工艺、装入制度和操作工艺。碱度要求按照《钢种 生产技术操作标准》。 采用分批加入的操作工艺,一般第一批渣料在开吹的同时加入,加入量 为总量的2/3,第二批料在前期渣化好后分批加入,视化渣情况,在4~7 分钟内加完。
钢水
倒炉出钢 前
测温管
插入钢水 400~ 500mm,时 间 5s 均匀
MgO、P2O5、 FeO、TFe等
根据需要
渣
第一次倒 炉出钢前
样勺
CaO、SiO2、 根据需要
钢水
第一次倒 炉出钢前
样勺
稳、准、 快、满、 盖
C、S、P、 Mn
所有非用 副枪取样 的炉次
10.溅渣护炉示意图
溅渣护炉
吹炼前期随第一批料加入轻烧白云石
根据供氧压力、供氧流量、纯吹时间,
8.脱氧合金化
合金加入量(kg)=目
标成分%—钢水残余成 分%/合金成分%×合金 收得率% ×钢水量(㎏/ 炉) 出钢到1/4时开始陆续加 入合金,3/4时应加完 合金应加在钢流上。
脱氧合金示意图
9.测温取样
取样类型 取样时间 取样、测 温方式 取样、测 温要求 分析元素 取样频率
6.温度制度
① ②
炼钢设计基础第二章

炉容比经验公式
V / T 0.75 7.5C 0.12100 Si
1
3
0.15100 P
1
3
B
1
2
0.06
式中:C-铁水含碳量(%) Si-铁水含硅量(%) P-铁水含磷量(%) B-供氧强度,m3/t· min
14
高宽(径)比
转炉的总高度(H总)和炉壳外直径(D壳)的比值(或
3
转炉常用炉型图
筒球形
锥球形
截锥形
4
炉型种类的选择原则
①炉型应能适应炉内钢液、炉渣和炉气的循环运动规律, 使熔池得到激烈而又均匀的搅拌,从而加快炼钢过程的物理 化学反应; ②有利于提高供氧强度(B),缩短冶炼时间,减少喷 溅,降低金属损耗; ③新砌好的炉子的炉型要尽量接近于停炉以后残余炉衬 的轮廓,减少吹炼过程中钢液、炉渣和炉气对炉衬的冲刷侵 蚀及局部侵蚀,提高炉龄,降低耐火材料的消耗; ④炉壳应容易制造,炉衬砖的砌筑和维护要方便,从而 改善工人的劳动条件,缩短修炉时间,提高转炉作业率。 总之应能使转炉炼钢获得较好的经济效益,优质、高产、低 耗。
Q 3 2 D=1.07 n T T
0.1825
m
式中:T-平均出钢量,t; n-喷枪孔数; Q-氧流量,m2/min。 在设计时单孔喷枪每分钟每平方米熔池只能吸收 15.25m3 的氧、 三孔喷 枪吸收 25.9m3 的氧,七孔喷枪吸收 45.7m3 的氧。用上式进行计算得出的熔 池直径和实际熔池直径相差不大。
影响炉容比大小的因素 1)炉子吨位本身的影响(炉子容量) 2)铁水成分 3)铁水比 4)供氧强度 5)冶炼操作方法(如:冷却剂) 6)氧枪孔数
(完整word版)转炉炼钢设计说明书

转炉炼钢设计说明书事故处理一、转炉工艺事故及处理1、低温钢1. 吹炼过程合理控制炉温,避免石灰结坨。
2.吹炼过程加入重型菲钢,过程温度控制应适当偏高些。
3.出钢口修补时不要口径过小,以免出钢时间长,降低钢水温度。
4.吹炼过程若温度过低可采取调温措施。
通常的办法是向炉内加硅铁、锰铁,甚至金属铝,并降低枪位,加速反应提高温度,若出钢后发现温度低,要慎重处理,必要时可组织回炉以减少损失,切不可勉强进行浇注。
若钢水含碳量高,可采取适当补吹进行提温。
2、高温钢吹炼前发现炉温过高,可适当加入炉料冷却熔池,并采取点吹使溶池温度,成分均匀,测温合格后即可出钢。
吹炼过程中发现温度过高,要及时采取降温措施,可向炉内加入氧化铁皮或铁矿石,应分批加入注意用量。
3、化学成分不合格(1)碳不合格控制脱碳时间,或加入冷却剂。
(2)硫不合格吹炼过程注意化好渣,保护炉渣流动性要好,碱度要高,渣量相应大些,炉温适当高些。
同时注意观察了解所用原料含硫量的变化,采用出钢挡渣技术,严禁出钢下渣。
(3)锰不合格a.认真计算合金加入量,坚持验称制度,合金要分类按规定堆放,铁水装入量要准确,准确判断终点碳,注意合金加入顺序及吸收率变化,准确判断余锰量。
B.采用出钢挡渣技术,严禁出钢下渣。
(4)磷不合格a认真修补好出钢口,采用出钢挡渣技术,尽量减少出钢时带渣现象。
控制合理炉渣碱度及终点温度,出钢后投加石灰稠化炉渣。
B.第一次拉碳合格后,若碳高需补吹则要根据温度,碱度等酌情补加石灰,调整好枪位,防止氧化铁还原太多炉渣产生返干,坚持分析终点磷,尽量缩短钢水在包中停留时间。
4、回炉钢水回炉钢水的处理1)与铁水按比例配合再回炉,利用铁水的化学热来进行回炉钢水的冶炼。
2)整炉回炉的钢水一般可分成2〜3次,即每包铁水中兑入1/2或1/3 回炉钢水,以保证有足够的热量。
3)吹炼回炉钢水的炉次一般不加废钢,由于回炉钢水中磷、硫较低,可以适当减少部分渣料。
4)兑有回炉钢水的铁水其碳也较低,纯供氧时间也可相应缩短。
转炉炼钢的总体工艺设计

转炉炼钢的总体工艺设计1、转炉炼钢车间设计应根据产品大纲,确定转炉公称容量、转炉座数和炉外精炼的配置。
2、转炉炼钢车间内转炉座数宜配置2座或3座,不宜大于4座,不应设置备用炉座。
多于3座转炉的车间,转炉宜分组分开布置。
3、转炉的公称容量应为炉役期的平均出钢量,最大出钢量应为公称容量的1.05倍~1.10倍,转炉生产宜采用分阶段定量法操作。
4、转炉吹炼炉座的年生产能力应按下列公式计算:式中:Q——每一吹炼炉座年产合格钢水量(t/a);G——转炉炉役期内每炉平均出钢量(t/炉);T——每炉钢平均冶炼周期(min/炉);N——转炉的年有效作业天数(d/a);n1——年修炉天数(d/a);n2——年日常计划检修天数(d/a);n3——年车间集中检修天数(d/a);n4——年生产耽误天数(d/a)。
5、转炉炼钢车间的组成宜符合下列规定:(1)主要生产系统宜包括主厂房、铁水预处理站、废钢配料间、炉渣间、烟气净化及煤气回收设施、余热蒸汽回收设施;(2)辅助生产系统宜包括铁合金贮运设施、散状原料贮运设施、快速分析室、空压站、车间变配电所、水处理设施、除尘设施、生活福利设施;(3)设计可根据生产规模、原材料供应情况等具体条件确定车间实际组成。
6、铁水中含有可利用的铌、钒、钛等合金元素时,应采用合理的冶炼工艺予以回收。
7、新建转炉的冶炼控制,宜采用以副枪检测系统和(或)炉气成分连续分析系统作为实时信号反馈的动态闭环过程控制。
8、转炉的各种工艺过程和能源介质的工作参数,均应配置检测仪表,所有被检测参数应输入到基础自动化控制系统。
冶炼试样应采用快速分析系统,数据应传输到过程控制计算机系统。
9、转炉炼钢使用的气体介质、燃料、冷却水及其管道,应符合下列规定:(1)氧气、氩气、氮气、蒸汽、压缩空气和燃料的供应能力应按设计规定的工作制度配备,并应按吨钢耗量和转炉车间的小时生产率计算;(2)贮气罐容积应满足车间高峰用量,同时能适应用量的波动和当供应源因事故停供时,贮气罐的贮备量至少应能满足一炉钢冶炼的需要;(3)车间分期建设时,各种介质的主管道宜按最终规模一次建成,而相关公用设施可视具体条件,或在总图上预留发展面积,也可在厂房内预留增建机组的条件。
设计一座年产万吨良坯的转炉炼钢车间

设计一座年产万吨良坯的转炉炼钢车间背景介绍转炉炼钢车间是钢铁企业中重要的设施之一,用于将生铁和废钢进行冶炼和炼制,生产出良好品质的钢坯。
本文将介绍如何设计一座年产万吨良坯的转炉炼钢车间,以满足钢铁企业的生产需求。
工艺流程转炉炼钢车间的工艺流程通常包括以下几个步骤:1.废钢预处理:废钢经过分选、压块等工艺处理,以满足后续冶炼的要求;2.转炉冶炼:将生铁和废钢投入转炉中进行冶炼,通过吹氧、搅拌等控制参数,使炉内的成分达到预定要求;3.过程控制:对冶炼过程中的温度、压力、氧气吹入量等参数进行监控和调整,确保炉内的化学反应进行顺利;4.出钢操作:炼钢完成后,将炼钢渣和钢水分离,通过倾吊等工艺操作,将钢水倾入连铸机进行连铸;5.连铸过程:将钢水铸造成连续的坯料,在连铸机上进行拉伸、切割等操作,生产出相应规格的钢坯;6.冷却处理:将连铸坯料进行冷却处理,使其达到适合后续轧制加工的温度。
设备配置为了实现年产万吨良坯的转炉炼钢车间,需要合理配置以下关键设备:•转炉:根据产量要求选择适当规模的转炉,确保能够满足炼钢工艺的要求;•除尘设备:通过布袋除尘器等设备,对炼钢过程中产生的烟尘进行有效处理,减少对环境的影响;•吹氧设备:提供足够的氧气供应,在转炉冶炼过程中,通过吹氧操作促进化学反应的进行;•连铸机:选择合适规格的连铸机,能够实现稳定连铸生产,并保证坯料的质量;•冷却设备:通过冷却设备对连铸坯料进行快速冷却处理,确保其达到后续轧制工艺要求。
设施布局为了实现高效的运行和生产,转炉炼钢车间的设施布局应该合理设计,包括以下几个方面的考虑:1.原料区:合理划分废钢和生铁的存放区域,确保按需调配原料,并提供合适的设备进行前处理;2.转炉区:转炉应位于中心位置,便于对转炉冶炼过程进行监控和操作,同时设备之间的距离要合理,便于人员操作;3.出钢区:炼钢完成后,需要有足够的空间进行钢渣和钢水的分离操作,并能顺利将钢水倾入连铸机;4.连铸区:连铸机应根据产量设定合理数量,并合理布置连铸机的进出坯口位置,便于钢坯的连续生产;5.冷却区:钢坯在连铸后需要进行冷却处理,确保其达到后续轧制加工的要求,冷却区应根据产量和冷却时间合理设置。
转炉基础设计方案
转炉基础设计方案介绍本文档将详细描述转炉的基础设计方案。
转炉是一种重要的冶金设备,用于炼钢过程中的转炉炼钢。
在设计转炉基础时,需要考虑到结构的稳定性、耐火材料的选用以及温度和压力的控制等因素。
设计一个合理的转炉基础能够保证转炉的正常运行,并提高生产效率和产品质量。
结构设计转炉基础的结构设计是确保转炉稳定运行的关键。
基础通常由混凝土浇筑而成,可以根据转炉的尺寸和重量来确定基础的尺寸。
考虑到转炉运行过程中的振动和冲击载荷,基础结构应具有足够的强度和刚度。
为了增加基础的稳定性,可以在基础的周围设置反冲墙或桩基。
基础的设计还包括转炉的支撑方式。
支撑方式可以采用直接支撑或间接支撑。
直接支撑是将转炉直接放置在基础上,采用铸铁座或钢座来支撑。
间接支撑则是通过支承架将转炉悬浮在基础上,可以减小振动影响。
耐火材料的选用在转炉的基础设计中,耐火材料的选择至关重要。
耐火材料主要用于转炉的内衬和底部。
常用的耐火材料有矽砖、高铝砖和镁碳砖等。
在选择耐火材料时,需要考虑其耐温、耐压和耐火碱性的性能。
同时,还需要考虑耐火材料的粘结性和耐久性,以保证其能够在高温和高压环境下长时间稳定运行。
温度和压力控制转炉基础设计中的另一个重要考虑因素是温度和压力控制。
转炉在运行过程中会产生高温和高压的环境,因此需要采取措施来控制温度和压力,以避免设备损坏和生产事故的发生。
温度控制可以通过给转炉设置冷却设备来实现。
冷却设备可以通过循环水或其他冷却介质来降低转炉的温度。
需要注意的是,在选择冷却方式时,要考虑冷却介质的稳定性和廉价性。
对于压力控制,可以在转炉上设置压力传感器来监测压力变化,并及时采取措施来调节压力。
在设计基础时,还可以考虑设置泄压装置,以防止超压情况的发生。
安全性考虑在转炉基础设计中,安全性是不可忽视的因素。
转炉的运行过程中存在较高的温度和压力,因此需要考虑到操作人员和设备的安全。
为了保证操作人员的安全,可以在转炉周围设置安全栏杆和标识,提供明确的操作指导,以避免意外事故的发生。
300吨转炉炼钢车间设计
=8523-0.8358×(1600+273) =8523-1565 =6959 ㎏/m3 V 池=3×105÷6959=43.11 m3 因此 h
V池 0.046 D 3 0.79 D 2 43.11 0.046 6.213 0.79 6.212
表 3-1 氧气转炉平均冶炼时间 30 50 100-120 150 14~15 15~16 16~18 18~19 28~30 30~33 33~36 36~38
4
间夹有一层石棉板绝热层。 永久层贴紧炉壳(无绝热层时) ,维修时一般不予拆除。其主要作用是保护 炉壳。该层常用镁砖砌筑。 填充层介于永久层与工作层之间, 一般用焦油镁砂捣打而成, 厚度 80~100 ㎜。 其主要功能是减轻炉衬受热膨胀时对炉壳产生挤压和便于拆除工作层。 也有 的转炉不设填充层。本设计取用 100 ㎜。 工作层系指与金属、熔渣和炉气接触的内层炉衬,工作条件极其苛刻。目 前该层多用镁炭砖和焦油白云石砖综合砌筑。 炉帽可用二部煅烧镁砖,也可根据具体条件选用其他材质。 转炉各部位的炉衬厚度设计参考值如下表。 表 2-1 转炉炉衬厚度设计参考值 转炉容量 炉衬各部位名称 <100 100~200 >200 本设计选用 永久层厚度/㎜ 60~115 115~150 115~150 120 炉帽 工作层厚度/㎜ 400~600 500~600 550~650 500 永久层厚度/㎜ 115~150 115~200 115~200 120 炉身(加料侧) 工作层厚度/㎜ 550~700 700~800 750~850 700 永久层厚度/㎜ 115~150 115~200 115~200 120 炉身(出钢侧) 工作层厚度/㎜ 500~650 600~700 650~750 700 永久层厚度/㎜ 300~450 350~450 350~450 400 炉底 工作层厚度/㎜ 550~600 600~650 600~750 600
包钢炼钢厂50吨转炉设计
包钢炼钢厂50吨转炉设计摘要:一、包钢炼钢厂50 吨转炉设计的背景和意义二、50 吨转炉的设计原理和关键技术三、50 吨转炉的设计流程和实施步骤四、50 吨转炉设计的优势和预期效果五、总结正文:一、包钢炼钢厂50 吨转炉设计的背景和意义包钢炼钢厂是我国重要的钢铁生产基地之一,一直以来都在为国家的经济发展和社会进步做出重要贡献。
为了提高生产效率,降低生产成本,提升产品质量,包钢炼钢厂决定设计一款50 吨转炉。
这款转炉的设计,不仅可以满足市场需求,还能推动钢铁行业的技术进步,具有重要的现实意义和深远的历史意义。
二、50 吨转炉的设计原理和关键技术50 吨转炉的设计原理主要是利用高温下的氧化还原反应,将铁矿石还原成纯铁。
在这个过程中,需要对炉内温度、压力、氧气浓度等进行精确控制,以保证钢铁的质量和产量。
关键技术包括高温熔融技术、氧气控制技术、炉内压力控制技术等。
三、50 吨转炉的设计流程和实施步骤设计50 吨转炉的过程可以分为两个阶段,第一阶段是设计阶段,主要包括确定转炉的规模、结构、材料等;第二阶段是实施阶段,主要包括转炉的制造、安装、调试等。
在设计阶段,需要进行详细的设计计算,以确定转炉的各项参数。
在实施阶段,需要严格按照设计要求进行,以保证转炉的正常运行。
四、50 吨转炉设计的优势和预期效果50 吨转炉的设计,可以大幅提高炼钢的效率和质量,降低生产成本。
预期效果主要包括提高钢铁产量、降低生产成本、提高产品质量等。
此外,50 吨转炉的设计,还能推动我国钢铁行业的技术进步,提升我国钢铁行业的国际竞争力。
五、总结包钢炼钢厂50 吨转炉的设计,是一项重要的技术创新,对于提高我国钢铁行业的技术水平,推动我国钢铁行业的发展具有重要的作用。
包钢炼钢厂50吨转炉设计
包钢炼钢厂50吨转炉设计
【原创实用版】
目录
一、包钢炼钢厂 50 吨转炉设计的背景和意义
二、转炉设计的主要参数和特点
三、转炉设计的实施过程和难点
四、转炉设计的效果和影响
正文
一、包钢炼钢厂 50 吨转炉设计的背景和意义
包钢炼钢厂是我国重要的钢铁生产基地之一,其 50 吨转炉设计项目旨在提升生产效率,降低生产成本,同时保证钢铁的质量和性能。
在当前的钢铁市场中,提高生产效率和降低成本是企业生存和发展的关键,因此,包钢炼钢厂的 50 吨转炉设计具有重要的现实意义。
二、转炉设计的主要参数和特点
50 吨转炉的设计主要涉及炉体的尺寸、结构、材料、冷却系统、炉内气体流动等方面。
其中,炉体尺寸和结构是设计的基础,直接影响到转炉的产量和效率。
材料选择则关系到炉体的使用寿命和安全性。
冷却系统和炉内气体流动的设计则关系到钢铁的质量和性能。
三、转炉设计的实施过程和难点
转炉设计的实施过程主要包括设计、制造、安装、调试等环节。
其中,设计阶段需要充分考虑生产需求和实际条件,制定合理的设计方案。
制造阶段需要保证炉体材料的质量和加工精度。
安装阶段需要保证炉体的稳定性和安全性。
调试阶段需要确保炉内气体流动和冷却系统的正常运行。
整个过程中,最大的难点在于如何在保证产量和效率的同时,确保钢铁的质量和性能。
这需要设计者具有丰富的经验和专业知识。
四、转炉设计的效果和影响
50 吨转炉的设计成功实施后,包钢炼钢厂的生产效率得到了显著提升,生产成本得到了有效控制,同时钢铁的质量和性能也得到了保证。
- 1、下载文档前请自行甄别文档内容的完整性,平台不提供额外的编辑、内容补充、找答案等附加服务。
- 2、"仅部分预览"的文档,不可在线预览部分如存在完整性等问题,可反馈申请退款(可完整预览的文档不适用该条件!)。
- 3、如文档侵犯您的权益,请联系客服反馈,我们会尽快为您处理(人工客服工作时间:9:00-18:30)。
——任务要求:含C3.9%,Si0.6%,50t复吹转炉炉型专业班级:冶金工程3班学生姓名:李源祥指导教师:杨吉春完成时间:2011年11月25日一、炼钢课程设计目的与内容二、炼钢课程设计的目的炼钢课程设计属于钢铁冶金专业的实践性教学环节,要求学生查阅相关资料,在指导老师的具体指导下,合理选择工艺参数、配料,使物料平衡、热平衡等工艺过程,及其绘图等,使学生经物料平衡计算,了解加入炉内参与炼钢过程的全部物料与产物之间的平衡关系。
经热平衡计算后,了解炼钢过程的全部热量来源与支出之间的平衡关系。
经炉型设计和绘图,掌握炉型对尺寸的计算方法。
对提高学生工程实践及独立分析解决问题的能力,培养创新意识,同时,加深了学生对炼钢原理,炼钢工艺等专业知识的理解,提高专业水平具有重要意义。
三、炼钢课程设计的内容1.转炉炼钢的物料平衡与热平衡计算;2.复吹转炉炉型设计计算及绘图。
3.设计具体要求:铁水含C3.9%,含Si0.6%,50t炉型图。
2.转炉炼钢的物料平衡和热平衡计算2.1物料平衡计算2。
1。
1计算原始数据基本原始数据有:冶炼钢种及成分、铁水和废铁的成分、终点钢水成分;造渣用溶剂及炉衬等原材料成分;脱氧和合金化用铁合金的成分及回收率;其他工艺参数.表2-1钢种、铁水、废钢和终点钢水的成分设定值注:本计算设定的冶炼钢种为Q235A。
[C]和[Si]按实际生产情况选取;[Mn]、[P]和[S]分别按铁水中相应成分含量的30%、10%和60%留在钢水中设定。
表2-2原材料成分注:炉衬配比:(镁碳砖),镁砂:80~85%碳:15~20%碳的有效成分:99.56%,余为挥发分:0。
44%。
表2-3铁合金成分(分子)及其回收率(分母)22.1。
2物料平衡的基本项目收入项有:铁水、废钢、溶剂(石灰、萤石、白云石、矿石)、氧气、炉衬蚀损、铁合金。
支出项有:钢水、炉渣、烟尘、渣中铁珠、炉气、喷溅。
2。
1。
3计算步骤以100㎏铁水为基础进行计算。
第一步:计算脱氧和合金化前的总渣量及其成分。
总渣量包括铁水中元素氧化,炉衬腐蚀和加入溶剂的成渣量。
其各项成渣量分别列于表2-5~表2-7。
总渣量及成分如表2—8所示。
表2—5铁水中元素的氧化产物及其成渣量①注:由CaO还原出的氧量;消耗CaO量=0.0133×56/32=0.0233㎏.表2—6炉衬腐蚀的成渣量表2-7加入溶剂的成渣量注:①。
石灰加入量:渣中已含CaO=-0.0233+0.004+1.30+0.003=1。
2837kg;渣中已含SiO2=1.286+0.006+0.015+0。
013+0。
021=1.341kg;因设定终渣碱度R=3。
5,故石灰加入量为:[R∑ω(SiO2)-∑ω(CaO)]/[ω(CaO,石灰)-R×ω(SiO2,石灰)]=3.410/(88.0%—3。
5×2.50%)=4。
303㎏②.石灰加入量=(石灰中CaO含量)-(石灰中S→CaS自耗的CaO量)表2—8总渣量及其成分①.总渣量计算如下:表中除(FeO)和(Fe2O3)以外的总渣量为:5。
081+1。
468+0。
932+0。
162+0.155+0。
448+0。
186+0。
039=8.471㎏,矿石成渣量中(FeO)和(Fe2O3)所占比例:(0.280+0。
660)/(8。
471+0.280+0.660)=9。
988%<13.25%,因此总渣量为:(8.471+0.280+0.660)/(1—9.988%)=10.388kg②ω(FeO)=10。
388×8。
25%—0。
28=1。
577㎏③ω(Fe2O3)=10.388—8.471-0.857-0。
660-0.001=0.399㎏第二步:计算氧气消耗量.氧气的实际消耗量系消耗项目与供入项目之差。
见表2-9第三步:计算炉气量及其成分。
炉气中含有CO、CO2、N2、SO2和H2O.其中CO、CO2、SO2和H2O可由表2—5~表2-7查得,O 2和N 2则由炉气总体积来确定。
现计算如下:炉气总体积V Σ:V ∑=g V +0.5%V ∑+6.991(s G 324.22+0。
5%V ∑-x V )所以:V ∑=(99。
6g V +0.7Gs -x V )/99.103=7.275m 3式中Vg-—CO 、CO 2、SO 2和H 2O 各组分总体积,m ³。
本计算中其值为:8.075×22。
4/28+1。
410×22.4/44+0.013×22。
4/64+0。
005×22。
4/18=7.189m 3 Gs ——不计自由氧的氧气消耗量,㎏。
本计算中其值为: 6.645+0。
066+0。
34=7.051㎏Vx ——石灰中的S 和CaO 反应还原出的氧量(其质量为:0。
002㎏)m ³。
0.5%——炉气中自由氧含量。
99——自由氧纯度为99%转换得来。
计算结果列于表2-10表2-10炉气量及其成分注:①.炉气中O 2的体积为7。
275×0.5%=0。
036m ³;质量为0。
036×32/22.4=0.051㎏.②。
炉气中N 2的体积系炉气总体积与其他成分体积之差;质量为0.050×28/22。
4=0。
0625㎏第四步:计算脱氧和合金化前的钢水量。
钢水量Qg =铁水量—铁水中元素的氧化量-烟尘、喷溅和渣中的铁损 =100—5。
348—[1.50×(75%×56/72+20%×112/160)+1+10。
388×6%] =91.944㎏由此可以编制出未加废钢、脱氧与合金化前的物料平衡表2—11表2—11未加废钢时的物料平衡表注:计算误差为(115。
27—115.07)/115.27×100%=0.017%第五步:计算加入废钢的物料平衡。
如同第一步计算铁水中元素氧化量一样,利用表2-1中的数据先确定废钢种元素的氧化量及其消耗量和成渣量(表2-12),再将其与表2-11归类合并,逐得到加入废钢后的物料平衡表2—13和表2-14。
表2—12废钢中元素的氧化产物及其成渣量注:计算误差为(121。
629-121.43)/121.629×100%=0。
16%表2-14加入废钢的物料平衡表(以100㎏铁水+废钢为基础)第六步:计算脱氧和合金化后的物料平衡。
现根据钢种成分设定值(表2-1)和铁合金成分及其回收率(表2—3)算出锰铁和硅铁的加入量,在计算其元素的烧损量。
将所有的结果与表2—14合并,及得到炼一炉钢的总物料平衡表。
锰铁加入量W Mn 为:W Mn =回收率Mn 含量Mn 锰铁中][][-×终点钢种Mn w Mn w ×钢水量=%80%80.67%18.0-%55.0××92.38=0。
63kg硅铁加入量W Si 为:W Si =回收率量锰铁含加锰铁后的钢水量终点钢种Si Si ][-)][-][(Fe ××MnSi w Si w Si w=%75%00.73002.0-)55.038.92(%25.0×+×=0。
42kg铁合金中元素烧损量和产物量列于表2—15.脱氧和合金化后的钢水成分如下: w(C )=0。
10%+25.93037.0×100%=0.14% %25.0%10025.93230.0002.0)i (w =×+=S %55.0%10025.93002.0342.0%81.0)(w =×++=Mn%021.0%10025.93001.0%020.0)(w =×+=P %021.0%10025.93001.0%02.0)(w =×+=S可见,含碳量尚未达到设定值。
为此需在钢包内加焦炭增碳。
其加入量W 1为:钢水量)(×=回收率C ×含量C 焦炭中%14.0-18.0W 1㎏)( 0.06193.2575%81.50%14.0-18.0=××=由此可得整个冶炼过程(即脱氧和合金化后)的总物料平衡表2-16。
表2-16总物料平衡表①。
计算误差为(116.13-115。
96)/116。
13×100%=0。
14%2。
2热平衡计算2.2。
1计算所需的原始数据计算所需的基本原始数据有:各种入炉料及产物的温度(表2—17);物料平均热熔(表2—18);反应热效应(表2-19);融入铁水的元素对铁水熔点的影响(表2-20)。
其他工艺参数参照物料平衡选取。
表2—18物料平均热熔表2-19炼钢温度下的反应热效应表2—20融入铁水的元素对铁熔点的降低2.2.2计算步骤以100㎏铁水为基础 第一步:计算热收入S Q 。
热收入项包括:铁水物理热;元素氧化热及成渣热;烟尘氧化热;炉衬中碳的氧化热。
(1)铁水物理热W Q先根据纯铁熔点、铁水成分以及溶入元素对铁熔点的降低值(见表2—17、表2-1和表2—20)计算铁水熔点T t ,然后由铁水温度和生铁热容(见表2-17和表2—18)确定W Q 。
t T =1536-(3。
9×100+0。
6×8+0.3×5+0.10×30+0。
040×25)-6=1129.7(℃)W Q =100×[0.745×(1129.7-25)+218+0。
837×(1250-1129。
7)]=114169。
26(KJ)(2)元素氧化热及成渣热y Q由铁水中元素氧化量和反应热效应(见表2-19)可以算出,其结果列于表2-21.表2-21元素氧化热和成渣热(3)烟尘氧化热C Q由表2—4中给出的烟尘量参数和反应热效应计算可得。
C Q =1.5×(75%×56/72×4250+20%×112/160×6460)=5075。
35kJ(4)炉衬中碳的氧化热1Q =0.3×15%×90%×11639+0。
3×15%×10%×34834=628.13kJ故热收入总量为S Q =W Q +y Q +C Q +1Q =114169。
26+80924.65+5075.35+628。
13=200797.39kJ第二步:计算热支出Z Q 。
热支出项包括:钢水物理热;炉渣物理热;烟尘物理热;炉气物理热;渣中铁珠物理热;喷溅物(金属)物理热;轻烧白云石分解热;热损失;废钢吸热.(1)钢水物理热Q g先按求铁水熔点的方法确定钢水熔点T g ;再根据出钢和镇静时的实际温降(通常前者为40~60℃,后者约为3~5℃/min ,具体时间与盛钢桶大小和浇注条件有关)以及要求的过热度(一般为50~90℃)确定出钢温度T Z ;最后由钢水热容算出物理热。