物料进厂检验图表
进料检验控制程序

进料检验程序1.目的规范外购、外协材料的检验作业, 确保物料入库合格, 防止不合格品的非预期使用。
2.范围适用于外购、外协生产物料的检验(包括测试)。
3.职责3.1仓库: 负责进料的点收、保管, 不合格品的隔离及记账等工作。
3.2采购: 负责与供应商联络、处理来料异常事项。
3.3检验:负责进料的品质检验/试验, 并做好相应的检验状态标志;负责启动进料不合格品处理作业流程。
4.作业程序4.1供应商交货到厂后, 仓管员将供应商的送货单与实际数量进行核对, 无误后将物料放入收货待检区。
4.2仓管员在规定时间内完成物料数量验收, 并在物料包装明显位置上贴好物料标示卡。
4.3仓管员以《送检单》书面方式通知原材料检验员, 并指明物料所在位置。
若为紧急来料, 仓管员可先电话通知原材料检验员先检而后补《送检单》报检。
4.4原材料检验在收到仓库报检的《送检单》后10分钟内须向仓管员回复检验时间。
若来料为生产急需料或为原材料检验可在30分钟内鉴定的物料, 原材料检验员须在接到《送检单》后10分钟内进行现场检验。
4.5原材料检验员按物料检验标准确定待检物料的检验方案, 准备好相关的图纸资料、样品、检验用具。
如果是客户提供物料或客户指定的特殊来料, 由销售部提供客户物料具体规格及客户品质明确要求, 以便原材料检验员进行检验。
4.6原材料检验员按进料检验规范、全检物料清单、批量产品抽样方案对物料进行抽样或全检, 并对照图纸、样板、BOM等进行检验工作, 并将检验结果记录在原材料检验报告上(要求原材料检验报告必须填写完整、正确、规范)。
4.7送检物料检验合格后不需进行性能测试的, 由原材料检验员在物料包装明显位置贴上绿色合格标签, 填写完整的检验内容(包括物料名称、规格/型号、检验员、日期等内容)。
4.8送检物料若需进行性能测试的, 由原材料检验员按测试标准进行性能测试, 将测试结果记录在检验报告上, 要求当天的测试工作于一个工作日内完成。
内衣厂物料检验标准模板
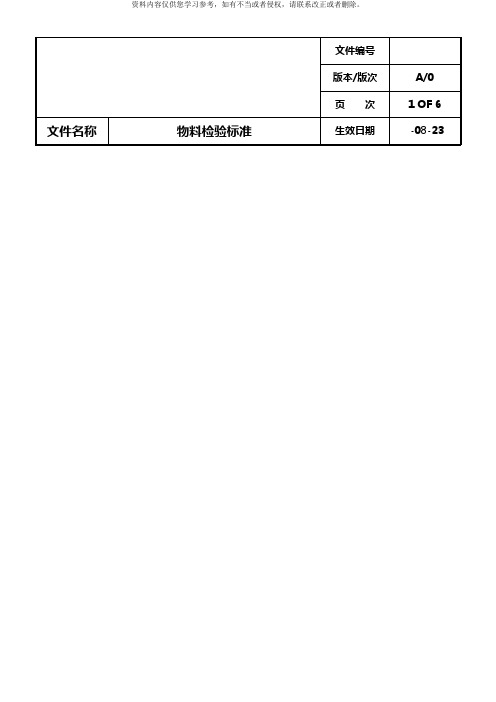
4.2.4计算损耗率
1)按疵点出现的位置折算疵点数, 间距在30CM之内的疵点折算成一个疵点。每个疵点按0.3M损耗计。宽度小于等于2CM的花边要根据所用的部位来确定损耗。( 如用于拉肩带、 内裤脚口的损耗要按照0.5M计算) 。
4.4.3检验操作规程
1)根据送货单清点总箱数, 然后查阅箱子上所贴标签的各项内容。
2)对照尺寸表检查各部位尺寸是否正确。
3)检查模杯的杯型是否符合要求, 经过测量各部位尺寸来判断杯型是否符合要求。( 需要特别注意模杯的杯深度) 。
4)检查模杯的厚度是否符合要求; 手感是否与标准样办一致。
5)检查模杯切边是否圆顺, 边缘无硬化现象; 左右碗有无厚薄; 有无明显色差; 自然放置后不瘫软。
3)检查丈根规格是否和要求相符( 宽度和厚度) 。
4)取1.5M丈根( 在中间取办) 做测量及批色存办用。丈根需要测试其自然回缩率( 放置24—48小时) 。注: 平面橡筋需要车在面料上面拉尽面料检查边缘起毛现象。
5)记录驳口的数量, 检查同一驳口内的头、 中、 尾处及驳口之问有无明显色差、 有无明显宽度差异。检查同批物料不同箱间是否有色差, 检查深色料拉伸后是否露白, 深色料切口是否露白。
9)用于模杯车间生产棉杯的面料要特别注意整洁, 一点细微的杂色毛毛压出成品棉杯都有可能导致报废, 除了破洞之外的面料上的外观疵点都要剪板给模杯车间压模测试成品后的效果再判定是否能够使用, 每批料要剪取卷差、 缸差提供给模杯车间做高温测试, 经过测试判定大货颜色是否0k。
10)在一匹布的头、 中、 尾各测量一次封度, 并作好记录。
物料检验规范
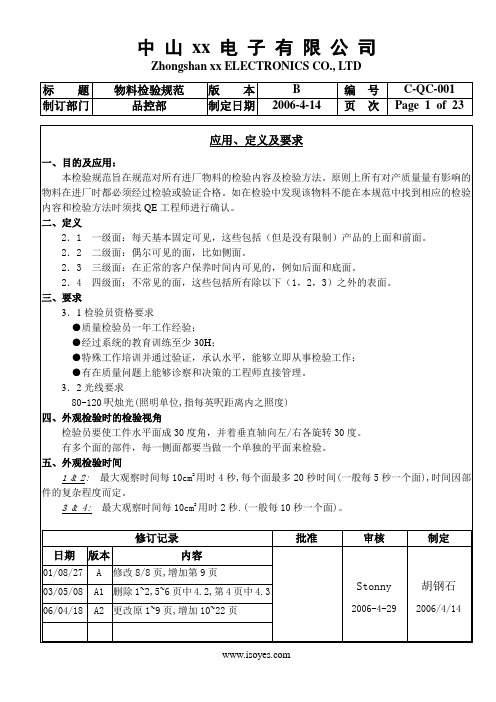
检验方法及要求
检验工具
参考文件
外观检验
颜色、外观、包装
1.来料包装完好无破损,标识清晰;
2.核对样板及图纸,外形,绝缘层材料、颜色及电镀颜色符合要求;
3.目视外观无镀层氧化、镀层脱落、变色、生锈、利边、变形,歪头、裂缝等缺陷;
4.表面不可有油污、水渍及其它脏物。由运输材料引起而且能够被空气吹走的灰尘是可被接收的。
样板,
PANTONE
目视
《零件图纸》
《进料检验抽样方案》
《缺陷分级作业指导书》
《进料抽样检验作业指导书》
《附着力测试作业指导书》
《耐磨擦试验作业指导书》
尺寸结构检验
外形尺寸,配合尺寸及结构检验
4.根据零件图纸测量产品的长度、外径、内径等相关尺寸应符合图纸要求。
5.有装配要求的喷涂件应目视和实配,不允许有变形的现象;
样板;
目视
《工程图纸》
《进料检验抽样方案》
《缺陷分级作业指导书》
《进料抽样检验作业指导书》
尺寸结构检验
外形尺寸,配合尺寸及结构检验
5.根据工程图纸测量产品的长度、外径、内径等相关尺寸。
6.有装配要求的注塑件应目视和实配,不允许有变形现象;螺丝孔用螺丝实配不能有滑牙,锁不到位的现象。
卡尺
螺丝刀
试验
高温起泡
03/05/08
A1
删除1~2,5~6页中4.2,第4页中4.3
06/04/18
A2
更改原1~9页,增加10~22页
物料名称:线材进料检验标准
1、目的
完善公司质量作业标准,规范物料的进料检验方式,确保进料质量满足公司及客户质量要求。
2、适用范围
凡供货商交货进厂之物料需执行检验的工作均适用。
生产部产品质量检验标准表
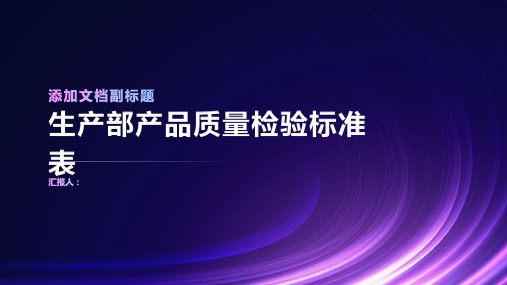
不合格品处理流程
发现不合格品:在生产过程中发现不合格品
处理不合格品:根据不合格品的类型和严重程度, 采取相应的处理措施,如返工、报废、降级等
分类处理:根据不合格品的类型和严重程度进 行分类处理
反馈不合格品信息:将不合格品的处理结果反 馈给相关部门,以便进行改进和优化
记录不合格品信息:记录不合格品的详细信息, 包括产品名称、规格、数量、不合格原因等
生产部产品质量检验标准 表
目录
单击此处添加文本 产品质量检验标准 检验方法及工具 检验流程及要求 质量记录及报告
产品外观质量标准
颜色:符合产品 标准色卡
形状:符合产品 图纸要求
尺寸:符合产品 图纸要求
表面处理:无划 痕、无锈蚀、无 变形
产品尺寸精度标准
尺寸精度:±0.1mm
测量工具:千分尺、游标卡尺 等
检测工具:包括游标卡尺、千分尺、硬 度计、拉力机等
检测标准:根据产品标准和客户要求制 定
检测流程:制定检测计划、执行检测、 记录检测结果、出具检测报告
检测人员:具备相关专业知识和技能, 经过培训和考核
检测环境:符合产品标准和客户要求, 确保检测结果的准确性
安全性能检验方法及工具
检验方法:包括目测、手感、仪器测量等 工具:包括游标卡尺、千分尺、硬度计等 检验标准:根据产品标准和客户要求制定 检验流程:按照检验标准进行检验,记录检验结果,出具检验报告
质量记录的填写、收集、整理和报送工作由生产部负责,并按规定时间报送质量管理部门。 质量记录应字迹清晰、内容完整、准确可靠,并按照规定的保存期限进行存档。 质量管理部门负责对质量记录进行审核,并对存档的质量记录进行监督检查。 质量记录的报送和存档应符合国家相关法规和标准的要求。来自质量数据分析及应用要求
电子厂来料检验物料验收标准

线路板厂来料检验物料验收标准
1.0目的
确保进料品质满足生产和客户需要特制定本检验标准。
2.0适用范围
本厂所进的原辅材料、工治具、化学药品的检验。
3.0检验工具
刻度尺、刻度显微镜、二次平面测试仪、数显千分尺、剥离强度测试仪、锡炉、非接触性测试仪等
4.0 检验内容
第一部分:基材、铜箔验收标准
第二部分:补强板验收标准
第三部分:保护膜验收标准
第四部分: 模具验收规范
第五部分: 化学药品验收标准
第六部分: 钻咀验收标准
第七部分:纯胶验收标准
第八部分:胶纸验收标准
第九部分:单双面离型膜验收标准。
工厂仓库操作流程图(九个流程)
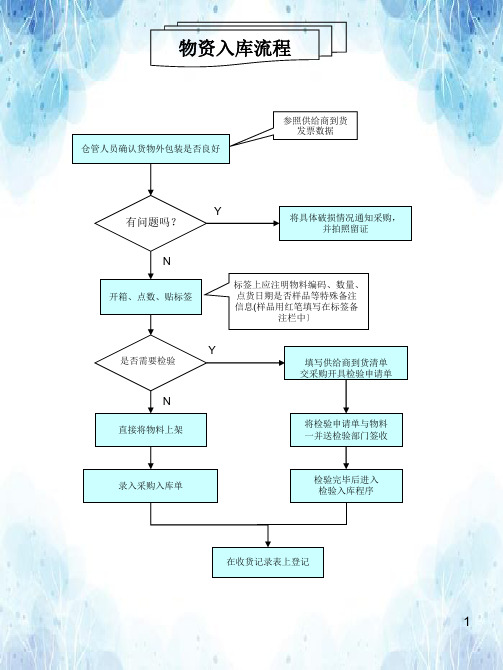
货包装本卷须知
2
产成品入库流程
生产部门开出FINISHED PARTS FOR STOCK IN
到生产部门拿取完工产品
收货时应特别注意标签备注栏上的信息 〔如系列号、发徕卡或其他特别事项等〕
N
核对物料品名、数量 工单编号是否与入库
结果一致
Y
上架时再次确认 标签上是否注明 物料编码、数量、 入库日期、工单 编号等重要信息
仓管根据OTHER STOCK IN 结果 去检验部门领取检验合格的良品
N
与检验部门 负责人再次确认
库管核对物料品名、 数量或OIQC编号是 否与检验结果一致
Y
仓管将物料上架
N
是否需要检验
Y
填写供给商到货清单 交采购开具其他检验申请单
将其他检验申请单与物料 一并送检验部门签收
检验完毕,质量部门开出 OIQC STOCK IN给仓库
仓管清点物料数量
在金蝶系统中录入其他入库单
4
生产任务单物料领用流程
生产部门开STOCK OUT LIST
备料时应在STOCK OUT LIST 上将有IQC编号的物料 记录下来备查。
格式为IQC编号_数量X
仓管人员根据STOCK OUT LIST 按照先进先出原那么将物料从货架中取出
如有766516领用需通知 质量部门IQC编号
因人为原因导致物料损坏 生产部门需要补发物料
进入生产单物料补领流程
5
生产任务单已领用物料更换流程
如果因质量原因生产部门需要更换物料 生产部门各车间负责人在换货登记本上登记
确保登记本上换货时间、成 品编码、工单号、原材料编 码、IQC编号、数量、申请人、
换货原因等重要信息完整
进料检验规范
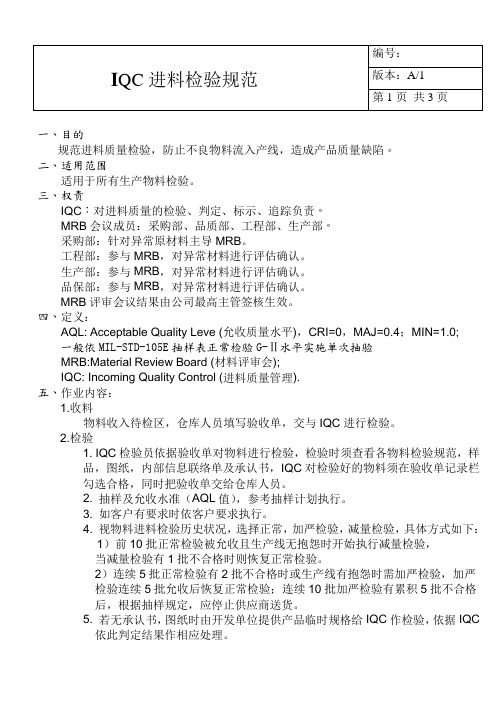
一、目的规范进料质量检验,防止不良物料流入产线,造成产品质量缺陷。
二、适用范围适用于所有生产物料检验。
三、权责IQC:对进料质量的检验、判定、标示、追踪负责。
MRB会议成员:采购部、品质部、工程部、生产部。
采购部:针对异常原材料主导MRB。
工程部:参与MRB,对异常材料进行评估确认。
生产部:参与MRB,对异常材料进行评估确认。
品保部:参与MRB,对异常材料进行评估确认。
MRB评审会议结果由公司最高主管签核生效。
四、定义:AQL: Acceptable Quality Leve (允收质量水平),CRI=0,MAJ=0.4;MIN=1.0;一般依MIL-STD-105E抽样表正常检验G-Ⅱ水平实施单次抽验MRB:Material Review Board (材料评审会);IQC: Incoming Quality Control (进料质量管理).五、作业内容:1.收料物料收入待检区,仓库人员填写验收单,交与IQC进行检验。
2.检验1. IQC检验员依据验收单对物料进行检验,检验时须查看各物料检验规范,样品,图纸,内部信息联络单及承认书,IQC对检验好的物料须在验收单记录栏勾选合格,同时把验收单交给仓库人员。
2. 抽样及允收水准(AQL值),参考抽样计划执行。
3. 如客户有要求时依客户要求执行。
4. 视物料进料检验历史状况,选择正常,加严检验,减量检验,具体方式如下:1)前10批正常检验被允收且生产线无抱怨时开始执行减量检验,当减量检验有1批不合格时则恢复正常检验。
2)连续5批正常检验有2批不合格时或生产线有抱怨时需加严检验,加严检验连续5批允收后恢复正常检验;连续10批加严检验有累积5批不合格后,根据抽样规定,应停止供应商送货。
5. 若无承认书,图纸时由开发单位提供产品临时规格给IQC作检验,依据IQC依此判定结果作相应处理。
6. 当进料检验发现不良时,由IQC检验员在验收单上描述不良现象,达到判退标准时由IQC主管确认后直接判退,并知会采购部,资材部。
进料检验流程
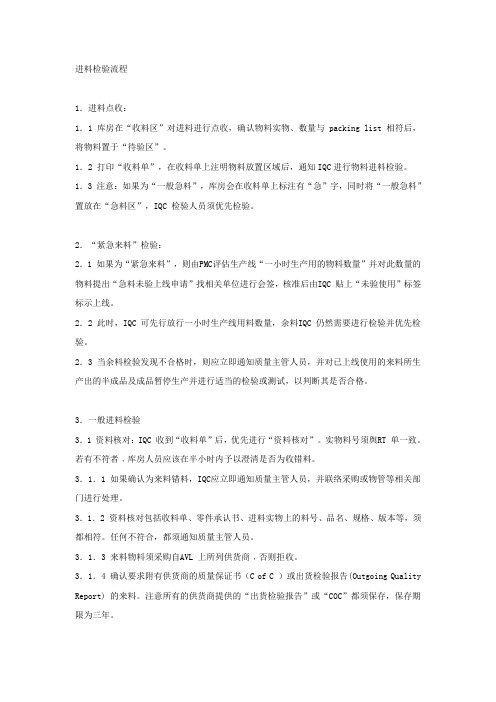
进料检验流程1.进料点收:1.1 库房在“收料区”对进料进行点收,确认物料实物、数量与packing list 相符后,将物料置于“待验区”。
1.2 打印“收料单”,在收料单上注明物料放置区域后,通知IQC进行物料进料检验。
1.3 注意:如果为“一般急料”,库房会在收料单上标注有“急”字,同时将“一般急料”置放在“急料区”,IQC 检验人员须优先检验。
2.“紧急来料”检验:2.1 如果为“紧急来料”,则由PMC评估生产线“一小时生产用的物料数量”并对此数量的物料提出“急料未验上线申请”找相关单位进行会签,核准后由IQC 贴上“未验使用”标签标示上线。
2.2 此时,IQC 可先行放行一小时生产线用料数量,余料IQC 仍然需要进行检验并优先检验。
2.3 当余料检验发现不合格时,则应立即通知质量主管人员,并对已上线使用的来料所生产出的半成品及成品暂停生产并进行适当的检验或测试,以判断其是否合格。
3.一般进料检验3.1 资料核对:IQC 收到“收料单”后,优先进行“资料核对”。
实物料号须舆RT 单一致。
若有不符者﹐库房人员应该在半小时内予以澄清是否为收错料。
3.1.1 如果确认为来料错料,IQC应立即通知质量主管人员,并联络采购或物管等相关部门进行处理。
3.1.2 资料核对包括收料单、零件承认书、进料实物上的料号、品名、规格、版本等,须都相符。
任何不符合,都须通知质量主管人员。
3.1.3 来料物料须采购自AVL 上所列供货商﹐否则拒收。
3.1.4 确认要求附有供货商的质量保证书(C of C )或出货检验报告(Outgoing Quality Report) 的来料。
注意所有的供货商提供的“出货检验报告”或“COC”都须保存,保存期限为三年。
3.2 外观、电性能、尺寸、包装方式等的检验:IQC 进料检验的依据进料检验指导书进行抽样和检验。
依据检验结果,填写“进料检验记录”。
3.3 贴标签:依据检验结果贴上对应的标签。