实验6 筛板精馏塔理论板层数及塔效率的测定
板式精馏塔的操作与效率的测定实验报告

2.全塔效率
(4)
式中,NT、NP分别表示达到同样的分离要求所需的理论塔板数和实际塔板数。理论塔板可用M-T图解法求取。
(1)在储料罐中配制一定浓度的来自精溶液(10%~20%)。(2)待塔全回流操作稳定时,打开进料阀,开启进料泵电源,调节进料量至适当的流量。
(3)启动回流比控制器电源,调节回流比R。
(4)当流量,塔顶及塔内温度读数稳定后即可取样分析。
3.乙醇浓度的测定
(1)比重法。根据天平测定比重的方法,分别测出塔顶、塔底试样的比重。并由酒精组分一比重对照表查得酒精质量分数。测完的样品分别倒回回收瓶中。
(2)气相色谱法。
4.注意事项
(1)塔顶放空阀一定要打开。
(2)料液一定要加到设定液位2/3处方可打加热管电源,否则塔釜液位过低会使电加热丝露出、干烧致坏。
(3)部分回流时,进料泵电源开启前务必先打开进料阀,否则会损害进料泵。
六、实验原始数据记录
取得两组数据:
(1)塔顶:0.810(测量得)
质量比:93.44;体积比:95.75(查表得)
(4)当塔顶温度,回流量和塔釜温度稳定约15~30min后,由塔顶取样管和塔底取样口用取样瓶接取适量试样,取样前应先取少量式样冲洗取样瓶两次。取样后用塞子将取样瓶塞严,并使其冷却到室温。塔板上液体取样注射器从所测定的塔板中缓缓抽出,取1mL左右注入事先洗净烘干的针剂瓶中,各个样品尽可能同时取样。
2.部分回流
79.9
筛板精馏塔的操作及其性能评定

实验六 筛板精馏塔的操作及其性能评定混合物的分离是化工生产中的重要过程,精馏是分离液体混合物的重要单元操作之一,广泛应用于化工、石油等工业部门。
精馏过程在精馏塔内完成。
根据精馏塔内构件不同,可将精馏塔分为板式塔和填料塔两大类;根据塔内气、液接触方式不同,亦可将前者称为级式接触传质设备,后者称为微分式接触传质设备。
精馏是通过加热造成气液两相物系,利用物系中各组分的挥发度不同的特性以实现分离的目的。
例如:苯与甲苯的混合体系、乙醇与水的混合体系等。
一、实验目的1.了解连续精馏装置的构造及基本流程,掌握精馏塔的操作方法。
2.掌握精馏塔全塔效率和部分回流效率的测定方法。
3.理解回流比、蒸汽速度等对精馏塔性能的影响。
4.在部分回流条件下进行连续精馏操作,在规定时间内完成500ml 乙醇产品的生产任务,并要求塔 顶产品中的乙醇体积分数大于0.93,同时塔釜出料中乙醇体积分数小于0.03。
二、实验原理(一)精馏塔的效率及测定塔板是板式精馏塔的主要构件,是气、液两相接触传热、传质的媒介。
通过对塔釜液体的加热,从塔底沸腾汽化的上升蒸汽流和从塔顶冷凝的下降液体流(回流),在塔板液层上进行气液两相的热交换和质交换,依据组分的挥发度不同,轻组分随蒸气流向上,重组分随液体流向下,从而完成液体混合物的分离目的。
1.对于二元物系,已知其气液平衡数据,则根据馏出液组成D x ,原料液组成F x ,残液组成W x ,回流比R 和进料状态,则可求得理论塔板数。
2.精馏塔稳定操作时,在进料条件和工艺分离要求确定后,要严格维持塔内的总物料平衡和组分物料平衡,即要满足总的物料平衡,即W D F +=各组分的物料平衡,即W D F W x Dx Fx +=3.精馏塔的全塔效率E ,是理论塔板数N T 与实际塔板数N P 之比(理论塔板数皆不包括蒸馏釜)。
%100⨯=PTN N E 4. 精馏段操作线方程:D x R x R R y 111+++=提馏段操作线方程:W x WL Wx W L L y -'--''=进料方程(q 线方程):11---=q x x q qy F (二)精馏塔的操作及调节精馏塔操作目标包括质量指标和产量指标。
筛板式精馏塔实验

实验九筛板式精馏塔实验一、实验目的1.了解筛板精溜塔和附属设备的基本结构。
2.掌握精溜过程的基本操作方法。
3.测定塔顶、塔底及塔板上的液相组成,据此求取全回流工况下的理论塔板数全塔效率和单板效率。
4.调节精溜塔的进、出料量和塔釜加热功率,使精溜塔稳定达到所需回流比下的部分回流工况。
5.测定塔顶、塔底液相组成,据此求取回流比下的理论塔板数和全塔效率。
6.调节精流塔使其稳定操作于不同的回流比工况,求取相应的全塔效率。
7.分析实验结果,归纳总结回流比对精流塔分离效率的影响二、基本原理在板式精流塔的精溜过程中,每一层塔板的汽、液相间进行着热、质传递,。
通常用塔的塔板效率表示塔板上传质的完善程度。
最常用的有单板效率和全塔效率。
单板效率直接反映单独一层塔板上传质的优劣,常用于塔板研究中,而全塔效率是反映整个塔的平均传质效果,常用于板式塔的设计中。
1.全回流操作时的单板效率和全塔效率。
1.1 单板效率单板效率指气相(或液相)经过实际塔板的组成变化值与经过理论板所达到的组成变化值之比,单板效率统称由实验测的。
汽相单板效率:Emv=(yn-yn+1)/(yn’-yn+1)液相单板效率:Eml=(xn-1-xn)/(xn-1-xn’)式中:yn,yn+1 ---------离开第块塔板的蒸汽组成,摩尔分数xn-1,xn------离开第块塔板的液体组成,摩尔分数y*n--------与成平衡的气相组成,摩尔分数xxn*------与T成平衡的液相组成,摩尔分数考虑到全回流操作时的操作线方程:则5-1式可以写成:Emv = (xn-1-xn)/(yn*-xn)1.2 全塔效率ET = (NT-1)/NP ×100%式中:NT----一定分离任务所需要的理论塔板数,包括蒸馏釜NP-----完成一定分离任务所需要的实际塔板数,本装置NP=8在精流塔中全回流操作时,操作曲线在图上为对角线,根据塔底的组成在操作线和平衡线见作梯级,即可得到理论塔板数。
板式精馏塔的操作与效率的测定实验报告

2.部分回流
提高回流比R,则能够提高塔顶产品浓度。回流比提高一是靠减小产品量,二是靠增加塔的加热速率和塔顶的冷凝量(增加冷却水量),因而本实验在规定的条件下通过回流比R、塔底出料量W、加热量等几个参数的调节控制,寻找能够达到分离要求的较优的操作条件。
2.全塔效率
(4)
式中,NT、NP分别表示达到同样的分离要求所需的理论塔板数和实际塔板数。理论塔板可用M-T图解法求取。
(1)
(2)
联立以上两式可得:
; (3)
因此,当xF给定时,精馏条件受到上述两式的制约,即若规定了塔顶和塔底的产品浓度(xD和xW),则不能再规定塔顶或塔底的采出率(D/F和W/F),若规定了xD和D/F,就不能再规定xW和W/F了。
在规定的精馏条件下,DxD≤FxF,即D/F≤xF/xD,所以当D/F过分大时,即使该塔有足够的分离能力,也是不能达到预定的产品浓度xD。换句话说,在此情况下,即使进行全回流操作也是无法达到预定塔顶的浓度xD。
化学工程与工艺专业
化工原理实验报告
姓名
学院
专业班级
学号
指导教师
实验日期
评定成绩:
评阅人:
板式精馏塔的操作与效率的测定实验报告
一、实验目的
(1)了解板式精馏塔的构成和精馏流程;
(2)熟悉精馏塔的操作方法;
(3)掌握精馏塔的效率测定方法。
二、实验基本原理
实验六 板式精馏塔板效率的测定

4.6板式精馏塔板效率的测定(Ⅰ)全回流精馏塔一﹑实验目的1.了解精馏装置的基本流程及筛板精馏塔的结构,熟悉精馏操作方法;2. 测定全回流条件下总板效率(或单板效率)。
二﹑基本原理精馏塔是分离均相混合物的重要设备。
衡量板式精馏塔分离性能,一般用总板效率表示:pTN N E =(4-31) 式中:E —总板效率;N T —理论板层数; N P —实际板层数。
理论板层数N T 的求法可用M-T 图解法。
本实验是使用乙醇-水二元物系在全回流条件下操作,只需测定塔顶流出液组成x D 和釜液组成x w ,即可用图解法求得N T ,实际板层数N p 为已知,所以利用式(4-30)可求得塔效率E .若相邻两块塔板设有液体取样口,则可通过测定液相组成x n-1和x n 求得第n 块板在全回流下的单板效率E mL 。
*11nn nn mL x x x x E --=-- (4-32)而全回流时,y n =x n-1式中:x n-1—离开上块板的液相中易挥发组分摩尔分率; x n ―离开下块板的液相中易挥发组分摩尔分率;y n ―离开下块板的气相中易挥发组分摩尔分率; x n *―与y n 成平衡的液相组成摩尔分率,以x n-1作为气相组成在平衡线上查得。
三、装置与流程实验装置为一小型筛板塔见图4-13。
原料液在蒸馏釜2中被加热汽化进入塔体4,与回流液在塔板上进行热、质交换后进入塔顶冷凝器5,冷凝为饱和液体后,又全部回流到塔内,由取样口7取样分析馏出液组成,从塔釜取样分析釜液组成。
四、操作步骤1. 熟悉精馏装置的流程和结构,以及所需的控制仪器表盘的布置情况,检查蒸馏釜中料液量是否适当,釜内液面高度控制在液面计的2/3左右。
2. 检查电源并接通电源,加热釜液。
用调压器调节加热功率(电流以3~4A 为宜),注意观察塔顶和塔釜的温度变化,塔顶第一块板上开始有回流时,打开冷却水,冷却水用量以能将蒸汽全凝为宜。
3. 打开塔顶放空阀8排出不凝性气体,塔板上鼓泡正常、温度稳定即表明操作稳定,可开始取样。
筛板精馏塔的操作与塔效率的测定
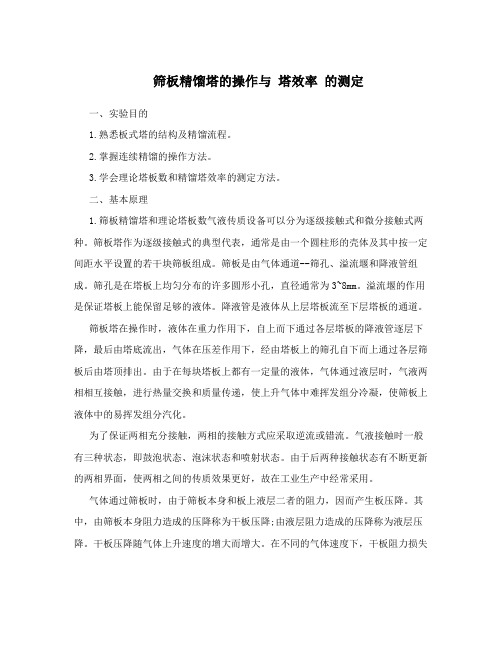
筛板精馏塔的操作与塔效率的测定一、实验目的1.熟悉板式塔的结构及精馏流程。
2.掌握连续精馏的操作方法。
3.学会理论塔板数和精馏塔效率的测定方法。
二、基本原理1.筛板精馏塔和理论塔板数气液传质设备可以分为逐级接触式和微分接触式两种。
筛板塔作为逐级接触式的典型代表,通常是由一个圆柱形的壳体及其中按一定间距水平设置的若干块筛板组成。
筛板是由气体通道--筛孔、溢流堰和降液管组成。
筛孔是在塔板上均匀分布的许多圆形小孔,直径通常为3~8mm。
溢流堰的作用是保证塔板上能保留足够的液体。
降液管是液体从上层塔板流至下层塔板的通道。
筛板塔在操作时,液体在重力作用下,自上而下通过各层塔板的降液管逐层下降,最后由塔底流出,气体在压差作用下,经由塔板上的筛孔自下而上通过各层筛板后由塔顶排出。
由于在每块塔板上都有一定量的液体,气体通过液层时,气液两相相互接触,进行热量交换和质量传递,使上升气体中难挥发组分冷凝,使筛板上液体中的易挥发组分汽化。
为了保证两相充分接触,两相的接触方式应采取逆流或错流。
气液接触时一般有三种状态,即鼓泡状态、泡沫状态和喷射状态。
由于后两种接触状态有不断更新的两相界面,使两相之间的传质效果更好,故在工业生产中经常采用。
气体通过筛板时,由于筛板本身和板上液层二者的阻力,因而产生板压降。
其中,由筛板本身阻力造成的压降称为干板压降;由液层阻力造成的压降称为液层压降。
干板压降随气体上升速度的增大而增大。
在不同的气体速度下,干板阻力损失和液层阻力损失所占比例是不同的。
在低气速条件下,以液层阻力为主;在高气速条件下,干板阻力所占比例相对增大。
在每一块筛板上,由于气液接触的时间有限,因而离开筛板时,气液两相的传质并未达到平衡。
这就是说一块实际的塔板的传质效果同一块理论塔板的传质效果相比,存在一定差距。
通过精馏操作,实现某组分分离目的需要的理论塔板数可在y~x相图上用图解法求出。
对于理想双组分溶液的精馏,在全回流操作的条件下,理论塔板数也可以用芬斯克公式进行计算:(3-5-1)式中:Nmin--全回流时所需要的最少理论塔板数;αm--全塔物料的平均相对挥发度;xA--塔顶馏出液或塔釜液中组分A的摩尔分数;xB--塔顶馏出液或塔釜液中组分B的摩尔分数;d,w--分别代表塔顶馏出液和塔釜液。
筛板式精馏塔的操作以及塔板效率的测定

实验六筛板式精馏塔的操作及塔效率的测定一、实验目的1、了解筛板式精馏塔的结构和精馏流程;2、熟悉筛板式精馏塔的操作方法;3、测定部分回流时的全塔效率,并掌握效率测定的方法。
二、实验任务1、在对约15-20%(V)的水和乙醇混合物的精馏中,在冷液加料的情况下,要求达到塔顶馏出液中的乙醇浓度不低于93%(V),乙醇回收率不低于80%(V)。
2、在部分回流的情况下,测定精馏塔的效率。
三、实验操作原理板式精馏塔中,塔釜产生的蒸汽沿塔逐渐上升,来自冷凝器的回流液从塔顶逐板下降,气液两相在足够的塔板数下层层接触,实现传热、传质过程,而达到分离的目的。
在操作方面,可以根据物料衡算及调节回流比和加热蒸汽用量完成实验任务。
本实验过程的原料液组成是恒定的。
因此可以根据进聊量F,由物料衡算控制产品量D和塔底残液量W。
继续精馏塔的物料衡算F=D+W式中------分别为原料液、塔顶产品和塔釜残液组成。
联立以上二式,可得:W/F=1-D/F由上两式可知,在及乙醇回收率确定的条件下,则W/F、也是确定的。
因此,可以根据进料量F来调节塔顶产品量D和残液量W,以满足分离要求。
另一方面,在确定的塔中,提高回流比R,可以提高塔顶产品浓度。
R=L/D V=L+D因此,可以加大蒸汽量V和减少产品量D来提高回流比,但V受到塔液泛速度和塔顶冷凝传热条件限制,而减少D则减少乙醇的回收率。
全塔效率式中,分别表示达到同样的分离要求,所需理论板数和实际板数。
实验装置,构造及流程图:本实验采用筛板式精馏塔装置,整套装置由塔体、供液系统,产品储槽、回流系统以及仪表控制柜等部件组成。
其流程如下图所示。
1、蒸馏釜:蒸馏釜为不锈钢材制成为立式结构,旁边装有玻璃管液面计,可视釜内液面高低、塔釜内以2支1[KW]的电加热棒进行加热。
其中一支是常家热而另一支通过自耦变压器。
可在0-1[KW]范围内调节。
2、塔身系采用不锈钢管制成。
设有二个加料口供选择,全塔有15块。
筛板精馏塔精馏实验报告

筛板精馏塔精馏实验6.1实验目的1.了解板式塔的结构及精馏流程2.理论联系实际,掌握精馏塔的操作3.掌握精馏塔全塔效率的测定方法。
6.2实验内容⑴采用乙醇~水系统测定精馏塔全塔效率、液泛点、漏液点⑵在规定时间内,完成D=500ml、同时达到x D≥93v%、x W≤3v%分离任务6.3实验原理塔釜加热,液体沸腾,在塔内产生上升蒸汽,上升蒸汽与沸腾液体有着不同的组成,这种不同组成来自轻重组份间有不同的挥发度,由此塔顶冷凝,只需要部分回流即可达到塔顶轻组份增浓和塔底重组份提浓的目的。
部分凝液作为轻组份较浓的塔顶产品,部分凝液作为回流,形成塔内下降液流,下降液流的浓度自塔顶而下逐步下降,至塔底浓度合格后,连续或间歇地自塔釜排出部分釜液作为重组份较浓的塔底产品。
在塔中部适当位置加入待分离料液,加料液中轻组份浓度与塔截面下降液流浓度最接近,该处即为加料的适当位置。
因此,加料液中轻组分浓度愈高,加料位置也愈高,加料位置将塔分成上下二个塔段,上段为精馏段,下段为提馏段。
在精馏段中上升蒸汽与回流之间进行物质传递,使上升蒸汽中轻组份不断增浓,至塔顶达到要求浓度。
在提馏段中,下降液流与上升蒸汽间的物质传递使下降液流中的轻组份转入汽相,重组份则转入液相,下降液流中重组份浓度不断增浓,至塔底达到要求浓度。
6.3.1评价精馏的指标—全塔效率η全回流下测全塔效率有二个目的。
一是在尽可能短的时间内在塔内各塔板,至上而下建立浓度分布,从而使未达平衡的不合格产品全部回入塔内直至塔顶塔底产品浓度合格,并维持若干时间后为部分回流提供质量保证。
二是由于全回流下的全塔效率和部分回流下的全塔效率相差不大,在工程处理时,可以用全回流下的全塔效率代替部分回流下的全塔效率,全回流时精馏段和提馏段操作线重合,气液两相间的传质具有最大的推动力,操作变量只有1个,即塔釜加热量,所测定的全塔效率比较准确地反映了该精馏塔的最佳性能,对应的塔顶或塔底浓度即为该塔的极限浓度。
- 1、下载文档前请自行甄别文档内容的完整性,平台不提供额外的编辑、内容补充、找答案等附加服务。
- 2、"仅部分预览"的文档,不可在线预览部分如存在完整性等问题,可反馈申请退款(可完整预览的文档不适用该条件!)。
- 3、如文档侵犯您的权益,请联系客服反馈,我们会尽快为您处理(人工客服工作时间:9:00-18:30)。
根据乙醇体积分数������、质量分数������查表得������������、������������、������������(g/cm3 = kg/L),与相应体积流量之乘积 除以相应平均摩尔质量得摩尔流量:
������
=
������������ ������������ ������������
【实验装置与流程】
实验装置如下图,由
1.;2.;3.;4.;5.;6.;7.;8.;9.;10.;11.;12.;13.;14.;15.;16.;17.;18.;19.;20.
【实验步骤与注意事项】
1. 检查塔釜是否有足够原料液(须恰好浸没加热器),开启加热开关加热塔釜; 2. 观察塔板温度,塔板温度升高变化时开启冷却水阀向冷凝器供水; 3. 令精馏塔保持全回流状态至塔顶温度稳定(约 78~79℃),开始进料,通过流量计调节进料、塔顶 馏出、塔底出料和回流流量,观察塔釜储罐液位不变为止; 4. 待操作条件(塔内压强、塔顶温度)稳定不变后,对原料液、塔顶产品、塔釜液同时取样约150mL,冷 却至室温后用浮力式酒度计测量、读数; 5. 停止加热,关闭进料、塔顶塔釜出料阀,待其余热继续进行全回流一段时间后,关闭冷凝器供水。 ※1. 开始加热前塔釜液必须浸没加热器才可开启加热电源,否则会损坏加热器; 2. 取样时应缓慢开启取样阀,以免流体快速喷出导致烫伤; 3. 测试完的样品应当回收到废料桶里,不得倾倒于下水道.
������
=
������
+
���������̅ ���������(������������ ������
−
������������ )
,������
=
������������ ������������
+
������������(1
−
������������),���������̅ ���������
������������
=
22.4[(������
+
1)������ + (������ 3600������������0
−
1)������]������0������
以上两式中������(atm)为操作压强,实验中取塔釜气压表的读数;������(K)为气相平均温度,实验中取
塔顶温度与塔釜温度的平均值;������0(atm)、������0(K)为标况下的温度、压强,即������0 = 1.00atm,������0 = 273K。
=
������������������������
������������ ������������ + ������������(1
−
������������ )
������
=
������������ ������������ ������������
=
������������������������
下同)、塔顶产品流量������������、塔釜液流量������������、回流量������������,进料、塔顶、塔釜、回流液、塔板、冷却水 进出口温度(℃),塔釜真空度(kPa)。取得原料液、塔顶产品、塔釜液样品并冷却后用浮力式酒度 计测量,核对样品温度求得20℃时的酒精体积分数������,换算得质量分率������,并求得摩尔分率������������、������������、 ������������:
������������
=
22.4(������ + 1)������������0������ 3600������������0
提馏段上升蒸汽量������′ = ������ + (������ − 1)������ = (������ + 1)������ + (������ − 1)������,单位为kmol/h,换算为������������(m3/s):
89.7)⁄18
=
0.773
������������
=
������������⁄������������
������������⁄������������ + (100 −
������������)⁄������������
=
1.62⁄46
1.62⁄46 + (100 −
1.62)⁄18
=
0.006
������������������������ + ������������(1
−
������������ )
������
=
������������������������ ������������
=
������������������������
������������ ������������ + ������������(1
������������������������ + ������������(1
−
������������ )
=
������������������ (A)������������
+
������������������ (B)(1
−
������������ )
������,������������������为轻组分 A、重组分 B 的汽化潜热和比热容,������������为进料混合物沸点,������������为进料液温度;
【实验数据记录与处理结果】
实验数据记录表
设备编号:18537,塔板数������P =20,内径:∅76, 塔顶温度:79℃,塔釜温度:101℃,回流温度:44℃,进料温度:28℃,塔板温度:95℃,
冷却水出口温度:38℃,冷却水进口温度:28℃,
进料流量������������ =10L/h,回流流量������������ =11L/h,产品流量������������ =2L/h,塔釜流量������������ =8L/h 塔釜真空表读数:0kPa.
������
=
������������������������
������������ ������������ + ������������(1
−
������������ )
=
46
×
0.972 × 10 0.0786 + 18 × (1
−
0.0786)
=
0.481kmol/h
������
=
������������������������
=
17.9⁄46
17.9⁄46 + (100 −
17.9)⁄18
=
0.0786
������������
=
������������⁄������������
������������⁄������������ + (100 −
������������ )⁄������������
=
89.7⁄46
89.7⁄46 + (100 −
【实验目的】
1. 了解精馏装置的基本流程及操作方法; 2. 掌握精馏塔全塔效率的测定方法; 3. 研究回流比、空塔速度等操作参数对精馏塔的影响。
【实验内容】
1. 测定指定条件下的全塔效率; 2. 研究回流比改变后对塔效率的影响; 3. 研究塔釜汽化量改变对塔性能的影响。
【实验原理】
理论板是假想中的塔板,离开该塔板的气液两相互相平衡。现实中装配好的精馏塔具有固定的 实际塔板数,总板效率即为衡量实际塔板在生产中能起多少块理论板的生产能力的标准。理论板数、 实际板数与总板效率关系如下:
4. 根据塔釜液中轻组分的摩尔分率������������,在辅助线������ = ������上取点(������������, ������������),连接该点与 ������线和精馏段 操作线交点,得提馏段操作线;
5. 用在相平衡曲线与操作线之间绘制阶梯,求得理论塔板数������T。 实验中所用装置是编号为 18537 的筛板精馏塔,可检测数据有进料流量���������(��� 体积流量,单位L/h,
������������)⁄������������
回流液组成与塔顶产品相同,轻组分含量为������������,∴回流比������ = ������⁄������ = ������������⁄������������.
除了回流比以外,操作因素的另一部分为塔内空气速度,亦称空塔速度,其定义为无填料无塔
酒精摩尔质量������������ = 46kg/kmol,水摩尔质量������������ = 18kg/kmol, 原料液、塔顶产品、塔釜液平均摩尔质量(kg/kmol)计算: ������������ = ������������������������ + ������������(1 − ������������),������������ = ������������������������ + ������������(1 − ������������),������������ = ������������������������ + ������������(1 − ������������)
������������),在������
=
0上取点(0,
������������ ),连接两点,即为精馏段操作线;
������+1
3. 根据进料的热状况������的值,进料的轻组分摩尔分率������������ ,过辅助线������ = ������上的点(������������, ������������),以斜率 ������⁄(������ − 1)作直线与精馏段操作线相交,即为������线,式中